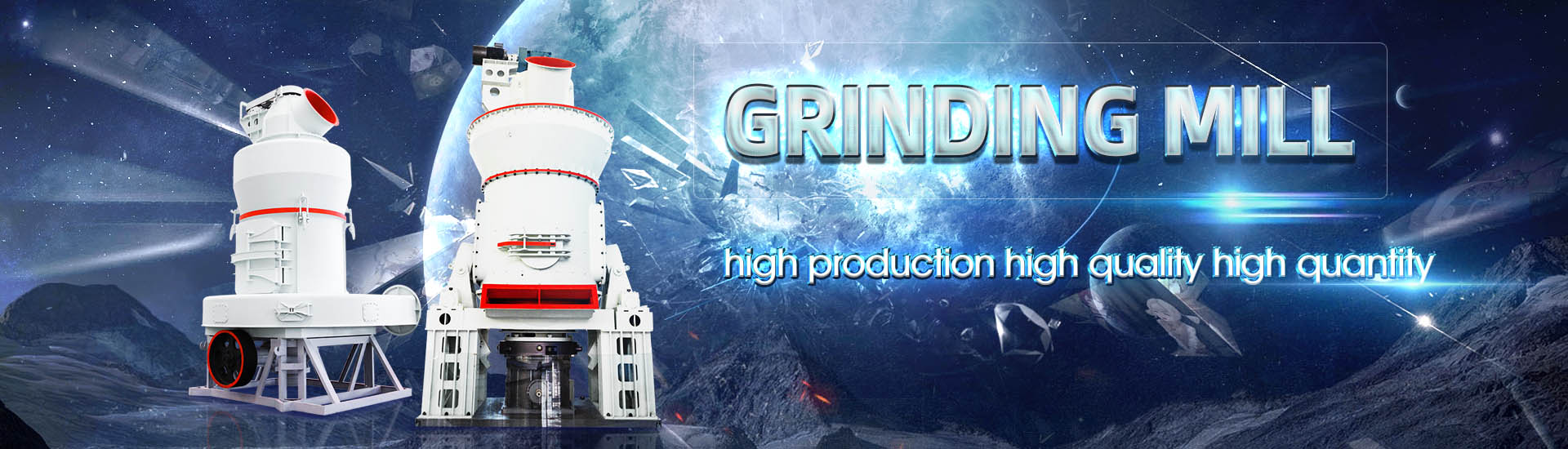
How does the coal mill ensure the fineness of coal powder
.jpg)
Coal Mill an overview ScienceDirect Topics
Coal mills grind the coal into fine powder, and the primary air entering the mill dries and drives the coal into the power plant furnace for combustion Mills can be a bottleneck for the power generation processThe first is that the CO 2 concentration in the flue gas is noticeably higher in a Cement Plant2017年11月15日 A method for choosing the optimum fineness of coal in pulverisedfuel boilers is presented This method is based on economic criteria and takes into account variations of Optimisation of coal fineness in pulverisedfuel boilers2021年6月1日 Pulverized coal fineness (PCF) is a key parameter in coalfired power plants, demanding accurate and online monitoring This study presents online measurement of PCF Online measurement of pulverized coal fineness on a 300 MWe
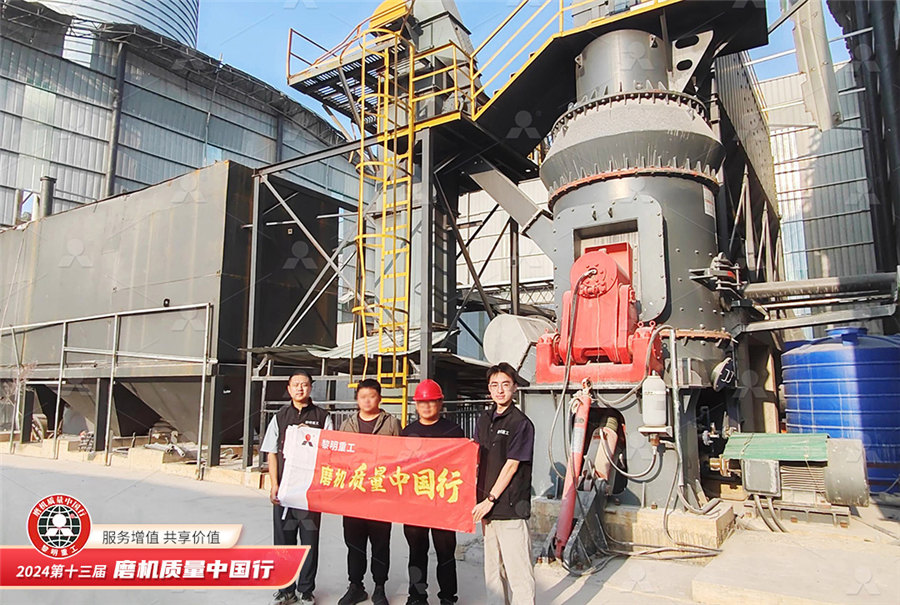
Pulveriser Mill Performance Analysis Optimisation in Super
Coal Pulveriser Mill Function and Operation details Pulverizer as shown in fig1 is used in power plant to reduce the size of the incoming raw coal to a fineness thatare four major mechanisms that happen during the coal crushing in the mills viz, size reduction in the coa coal, transport of the crushe coal and the classification of coal in terms of its A Study on 500 MW Coal Fired Boiler Unit’s Bowl Mill Performance 2017年8月1日 Particle size distribution (PSD) of coal powder, socalled pulverized coal fineness (PCF) [2], is a crucial parameter in coalfired power plants, with a significant effect on Optimisation of coal fineness in pulverisedfuel boilersspindle coal pulverising mill’s performance to facilitate optimal plant performance Plant design and mill’s acceptance test data was analysed to understand the design and subsequent Performance optimisation of vertical spindle coal pulverisers
.jpg)
CPRI Online Coal Flow Balancing and Fineness Adjustment
ABSTRACT: The paper describes the beneficial application of online coal flow measurement and control and online coal fineness measurement for optimization of the combustion process Computational fluid dynamics (CFD) modelling and validation with experimental coal fineness test in real plant are made The optimum range of air flow rate and coal particle flow rate in Computational Study of Coal Particle Distribution in Coal 2012年11月17日 The document discusses coal mill/pulverizers used in thermal power plants It describes how pulverized coal is dried, ground, circulated, and classified within the mill to produce a fine powder that is then transported to Coal mill pulverizer in thermal power plants PPT2010年10月7日 Ensure Fuel Line Fineness and Distribution Testing by Air/Fuel Ratio Sampling and Ensure That an Optimum Fineness Level Is Achieved Accurate weighing and sieving of the coal samples through four Pulverized Coal Pipe Testing and Balancing
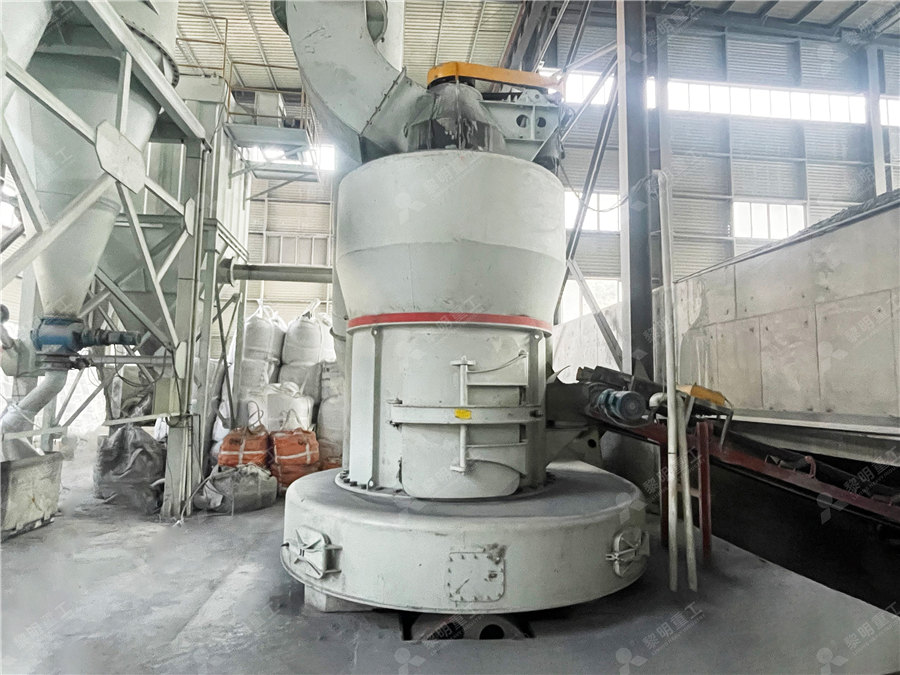
Coal mill pulverizer in thermal power plants PPT
2012年11月17日 20 131Fineness Fineness is an indicator of the quality of the pulverizer action Specifically, fineness is a measurement of the percentage of a coal sample that passes through a set of test sieves usually designated at 50, 2023年6月3日 Superfine powder A powder of which not less than 90 percent by the number of the particles are less than 10 micron size When the fineness of the powder is described by means of a number, it is intended that all the particles of the powder shall pass through a sieve of which the nominal mesh aperture, in /lill, is equal to that numberPowder Fineness (Types of Powder) PharmaguidelineSection of coal bowl mill Table 1 Guaranteed coal conditions for mill performance evaluation Coal Moisture % 20 Coal HGI 55 Mill Outlet Temperarure °C 80 Mill Air Flow T/hr 102 Coal Fineness (% passing trough 200 mesh) 70% passing through 200 mesh and 90% passing through 50 mesh Differental Pressure 300 mmwc Coal Output from Mill 609 t/hrA Study on 500 MW Coal Fired Boiler Unit’s Bowl Mill 2019年11月7日 Comprehensive treatment,we should have a test on the 300 MV unit steel ball coal mill pulverizing systemAt the same time,analyze the main operating parameters before modificationTransform the Optimization and transformation of 300MV units steel ball coal mill
.jpg)
Coal Mill in Thermal Power Plant: Enhancing Efficiency and
3 Precise Control and Automation: Bellian Machinery's coal mills feature advanced control systems that enable precise control over various operational parameters Operators can adjust grinding variables, such as coal flow and mill rotation speed, in realtime to achieve the desired coal fineness and optimize mill performanceThe equipment involved is a ball mill, which is used to grind the pellet feed into extremely fine powder for use in pelletizing process Metallurgical components of this mill, such as screws, shell and mill head, are analyzed in a milling system simulation using iron ore slurry in order to correlate the components loss weight with running timeOptimisation of coal fineness in pulverisedfuel boilers2017年8月1日 Particle size distribution (PSD) of coal powder, socalled pulverized coal fineness (PCF) [2], is a crucial parameter in coalfired power plants, with a significant effect on combustion efficiency Optimisation of coal fineness in pulverisedfuel boilersCoal mill is suitable for types of coal with various hardness and humidity Coal ball mill is mainly used in coal power plant or mineral calcining system A highquality coal mill can effectively solve the fineness problem of coal powder and ensure uniform grinding of raw coalCoal Ball Mill Grinding for Different Kinds of Pulverized Coal
.jpg)
Pulverizer Capacity is not simply “tons throughput per hour!”
feed rate, HGI variations, spring pressures, coal fineness, mechanical alignment of the grinding elements, bearing condition, optimum or reduced air/fuel ratios, etc Our experience proves that monitoring mill HP/ton consumption for a given fuel HGI and/or mill fineness can serve as a performance indicator to ensure the preservation2021年3月31日 24 mill performance monitoring using non iso kinetic technique • dirty pitot testing to be carried out before and after mill overhaul • non iso kinetic sampling to be used for routine checking of fineness • pf fineness data to be Effect of Coal Quality and Performance of Coal Pulverized coal combustion systems offer a viable solution to all these problems, wherein coal is reduced to a fine powder in grinding mills and projected into the combustion chamber through a hot primary air current To ensure complete combustion, supplementary air (known as secondary air) is delivered separately to the combustion chamberPulverised Coal Combustion an overview ScienceDirect TopicsNot only does the VARB ensure even mass flow distribution of PF down each splitter outlet, its mixing effect also ensures the PF particle size distribution is also consistent down each pipe leg The PfMaster Coal Flow OnLine Monitoring System Optimizing PF Distribution and Velocity Enhancing Performance Coal Flow Measurement, Balancing, and Boiler Optimization
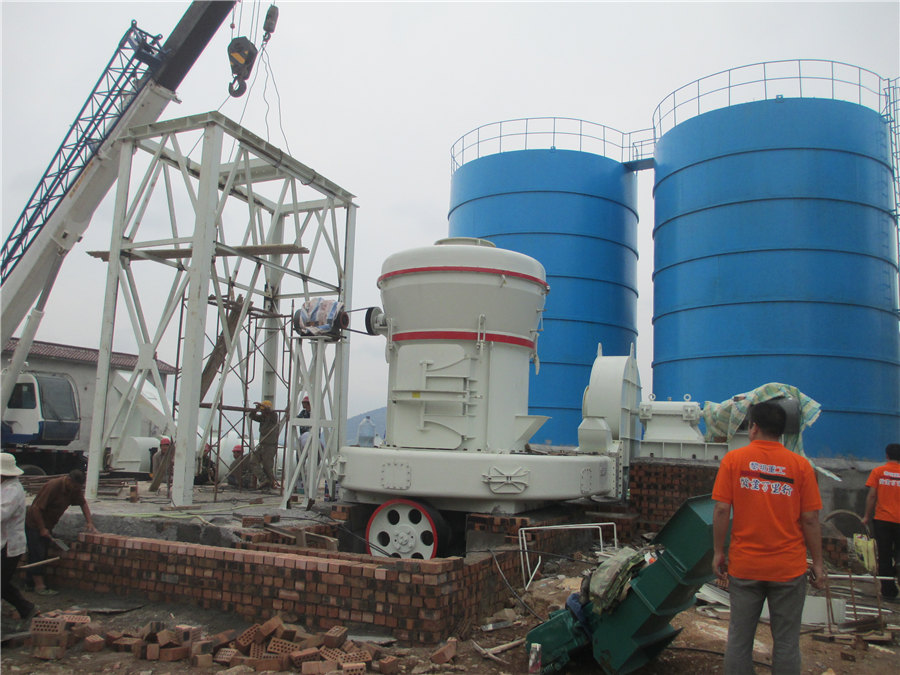
Vertical Grinding Mill (Coal Pulverizer) Explained saVRee
Introduction This article concerns itself with vertical grinding mills used for coal pulverization only (coal pulverizers), although vertical grinding mills can and are used for other purposes The 3D model in the saVRee database represents a vertical grinding bowl millOther grinding mill types include the ball tube mill, hammer mill, ball and race mill, and , roll and ring mill2017年4月11日 The fineness of the coal powder and the uniformity of the coal flow sent to the burners are crucial parameters to achieve an effective combustion in coalfired power plantsPreliminary investigation on the effects of primary airflow to coal conducted This should include isokinetic coal sampling and dirty airflow measurements through each fuel line to determine air fuel balance and coal fineness Primary airflow “HotK” calibrations of the primary airflow measuring element should also be conducted Only after the mill is thoroughly checked out should it be released to The Storm Approach to Coal Pulverizer Optimization2024年3月16日 This sustainable approach not only ensures the efficient utilization of resources but also underscores a commitment to environmental responsibility and circular economy principles A vertical coal mill functions by introducing coal into a rotating table, where it undergoes pulverization through a combination of compression and grinding forcesHow Does a Vertical Coal Mill Work
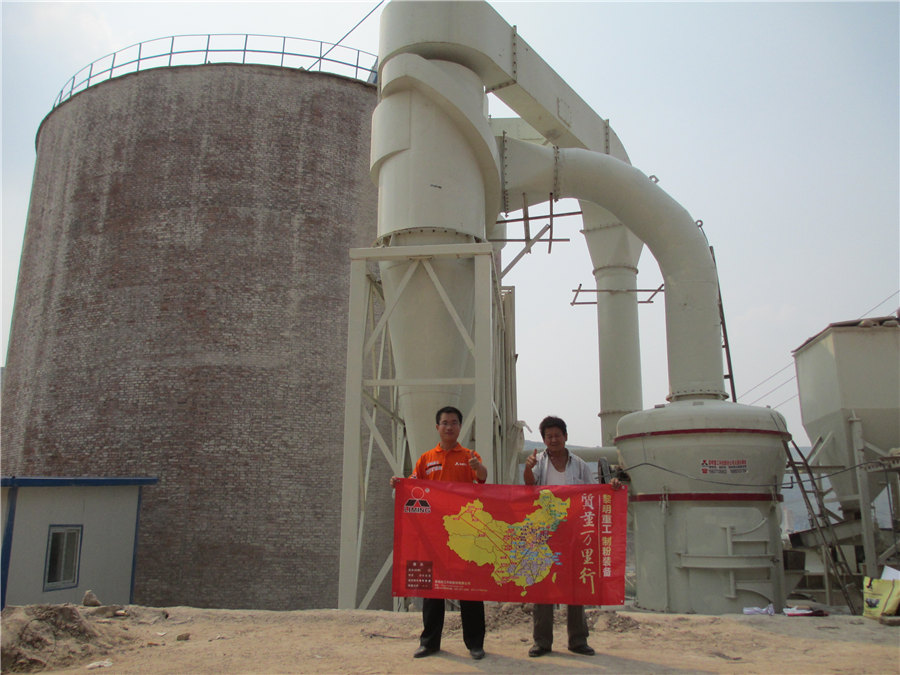
How to Process Coal into Pulverized Coal in 5 Steps?
2024年1月11日 With a ball mill 1 To pulverize crushed coals in a ball mill, you start by feeding the mill with crushed coal Then the grinding media crushes and grinds the coal in the rotating chamber 2 Airflow carries the pulverized coal out of the ball mill 3 Next, you'll need to use the mill classifier to separate the fine coal particles from the airflow2018年10月21日 Fig 1 Pulverized coal combustion and gas composition in raceway The extent of combustion (combustion efficiency), and hence the amount of unburnt material transported out of the raceway, depends on several parameters which include (i) properties of the coal, such as the VM content, particle size and density, and (ii) operating conditions, for example, blast gas Understanding Pulverized Coal Injection in Blast Furnace2015年11月1日 The coal mill grinds the raw coal into fine powder and hot air entering the mill dries and carries the pulverized coal to the burners of the furnace Maffezzoni (1986 ) emphasized that coal mills are the primary cause of slow load following capability and regular plant shutdownsA unified thermomechanical model for coal mill operation2021年9月30日 Henderson (2016) Coalfired power plants—flexibility options and challenge Presented at UNECE/WCA workshop on the sustainability credentials of coal and its role in the UN, Geneva, 26 October 2016 Google Scholar Hilleman D (2018) Coal plants: American experience, modifying coal plants for generation flexibilityFlexible Operation of High Efficiency Coal Power Plants to Ensure
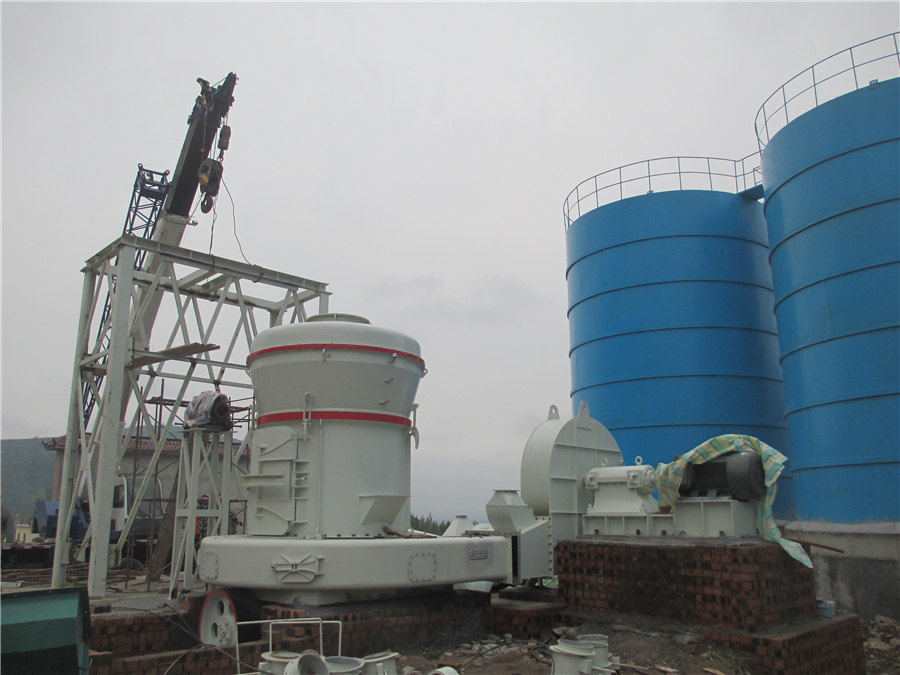
Online measurement of pulverized coal fineness on a 300
2021年6月1日 This was mainly due to the sparseness of coarse coal powder, leading to a low probability of coal powder larger than 200 μm to be captured by the measurement system Although the obvious difference of PCF for mill D and B can be revealed with SAD directly, R 90 results and distribution curves were still with deviations comparing to the sieving methodThe adverse effects are compounded because burners having more coal will likely be of lower fineness making it even more difficult to achieve complete combustion in the burner belt zone Importance of Fineness Poor Coal Fineness often yields poor distribution as large coal particles air mix to form a (2) phase mixture which will not homogenizePulverizer FinenessThe BTM is a lowspeed mill that primarily grinds coal by impact and attrition The VRM is a medium speed mill that grinds coal by compression and, because of the low coal inventory in the mill and flat grinding surfaces, develops shearing action as well For both mills a constant centrifugal force is maintained The speedA Comparison of Three Types of Coal Pulverizers Babcock Power2015年12月1日 Acceptable standards for best lowNO x burner performance are coal fineness of 75% passing a 200mesh sieve and less than 01% remaining on a 50mesh sieve Fuel balance should be within the range Coal Pulverizer Maintenance Improves Boiler Combustion
}@~3SRDG`IA1KP_ICWAA.jpg)
HighEfficiency Vertical Coal Mill Enhancing Coal Pulverization
The coal vertical mill, also referred to as the vertical roller coal mill, is an advanced equipment developed by our company It combines modern technology with our extensive experience in powder manufacturing This coal pulverizer efficiently integrates coal grinding and drying, providing highperformance and energysaving features2023年5月30日 The produced coal fines were found to have greater minerals content than the primary coal fine samples The organic composition of the coal fines was dominated by vitrinite (5158–6700%) followed by inertinite (10–3474%) and inorganic minerals (421–28%) The coal fines samples were dominated by clay minerals, pyrite, and quartzCharacterization of Coal Fines and their Production Springer2020年11月25日 Dried coal of BRXL lignite emits a smaller amt of NOx than that of BRXL lignite However, the dried degree of BRXL lignite is closely related to R90 fineness Dried coal with optimal moisture content yields least NOx emissions When deep or middle staged combustion was adopted, the application of multistaged combustion is conducive to NOx rednA Control Strategy of the Air Flow Rate of CoalFired Utility Boilers Our Boiler Mill and Coal Pulverizer Service Solutions help you make the most of your mill’s operational efficiency Up to 20% improved coal fineness GE’s PVPRO mill upgrade system uses a patented process for better control of coal fineness and reduced pulverizer wear for extended operationsBoiler Mill and Coal Pulverizer Performance GE Steam Power
.jpg)
HOW ELECTRICITY IS PRODUCED AT A COALFIRED POWER
The purpose of the coal stockyard is to ensure that there is sufficient coal reserves available to keep the power station in operation should the mine experience production problems Inside the power station, the coal is pulverised to a fine powder in giant grinding mills This is because pulverised coal burns quickly, like gasHot air flow is induced through the mill in order to dry the coal and remove the fines from the pulverizing zone If the rate of feed is increased, coarser product will be obtained and if the speed of rotation is increased the fineness for given Pulveriser in Thermal Power Plant Bowl Mill Ball Millspindle coal pulverising mill’s performance to facilitate optimal plant performance Plant design and mill’s acceptance test data was analysed to understand the design and subsequent changes over the years of the mill’s operation The mill outputs, pulverised coal fineness andPerformance optimisation of vertical spindle coal pulverisersers and satisfactory coal fineness Adequate fineness for both west7 Optimum design Ensure optimum arrangement of the mill throat and the coal flow path to improve mill performance Source: Storm Technologies Inc Grinding surface Finer particles and air to rise to classifier Recommended 7,000 FPM at throat free annular jet velocity at“Blueprint” Your Pulverizer for Improved Performance
.jpg)
AN EXPERIMENT ANALYSIS OF COAL PULVERIZER ON
Keywords Fuel Fineness, Unburned Carbon, Isokinetic Coal Sampling I INTRODUCTION A coal fired boiler utilize pulverized coal firing system These systems utilize pulverizer or mill to grind the coal to a desired fineness and subsequently transport the coal particles to the burners using primary air as a transport medium [1]This paper was brief, but hopefully has shown the importance of one aspect, mill performance, on many coal quality related issues At first glance one might not consider the influence mill fineness has on mill capacity, slagging and opacity; this paper has shown that it does indeed, and mill performance is only one of many areas of considerationCoping With Coal Quality Impacts on Power Plant Coal in some cases the recommended dust fineness does not satisfy its dependence on the content of volatiles in the fuel For example, for the 3B brown coal of the Bogoslovskoe deposit having Vdaf = 480% and Ad = 47, 9% the recommended value of R 90 is 45% The same value of R 90 is recommended for the 1B brown coal of the Aleksandriiskoe deposit Choice of Fineness of Pulverized Coal SpringerSemantic Scholar extracted view of "The Laws Governing the Fineness of Powdered Coal" by P Rosin This paper presents the results of the characterization of alumina ball size distribution in the mill of a crushing and grinding plant The mill was The Laws Governing the Fineness of Powdered Coal