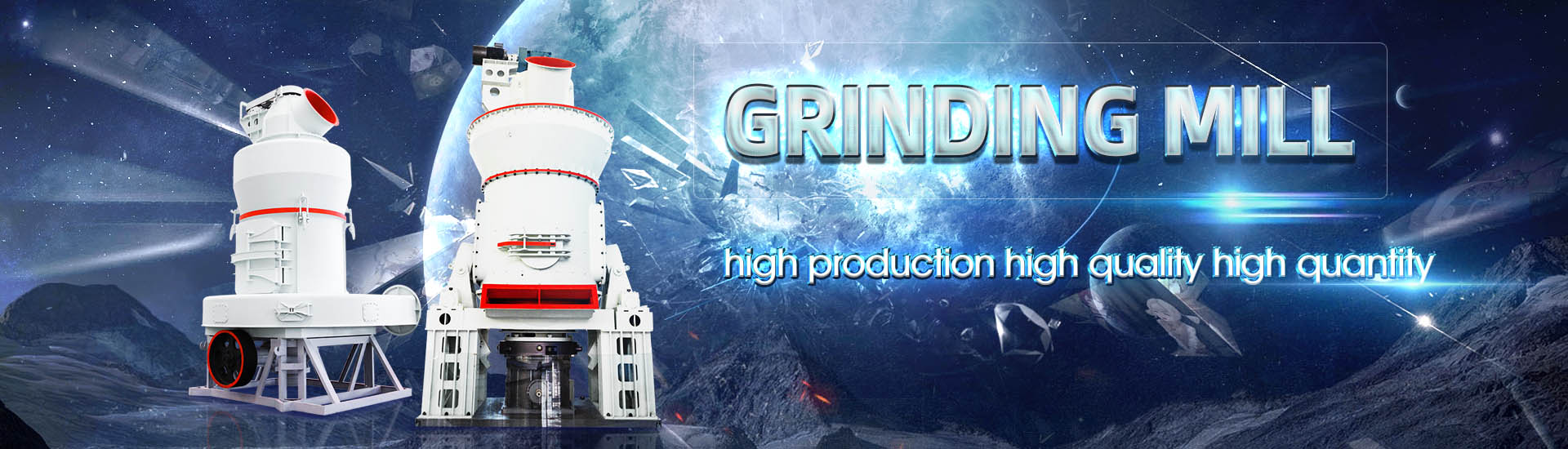
Desulfurization tower ore mill
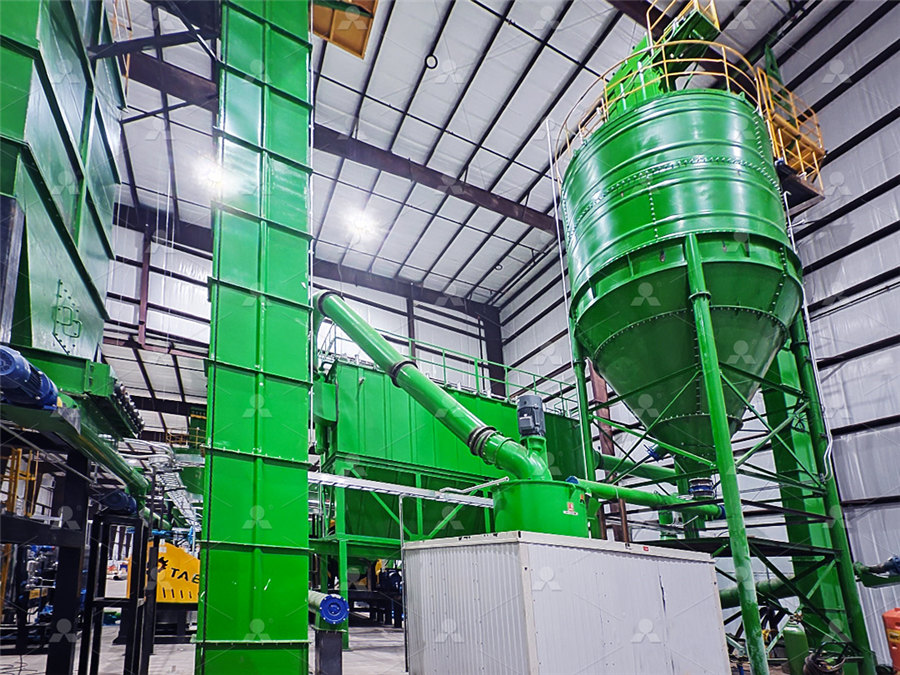
TowerMill industrial material preparation technology,
TowerMill is a vertical agitated media mill developed in Japan in the 1950s Until now, TowerMills have been used in ferrous and nonferrous mines for processes of ore grinding, flue gas desulfurization (FGD), limestone grinding for 2021年12月1日 Environmental desulfurization using nonselective flotation has recently been implemented as an integrated management approach for mine tailings Furthermore, physical Environmental desulfurization of mine wastes using various 2022年1月15日 MC Qin et al studied the gasliquid flow, mass transfer and chemical reaction process of limestone gypsum wet desulfurization in a dualloop spray tower (DLST) through Summary of research progress on industrial flue gas 2024年5月15日 Abstract: Densephasetower desulfurization technology is an emerging semidry fluegas desulfurization ash process, ie, the flue gas is allowed to enter the 1,2,*, Hao Li 3 , Hongzhi Ma 3, 2
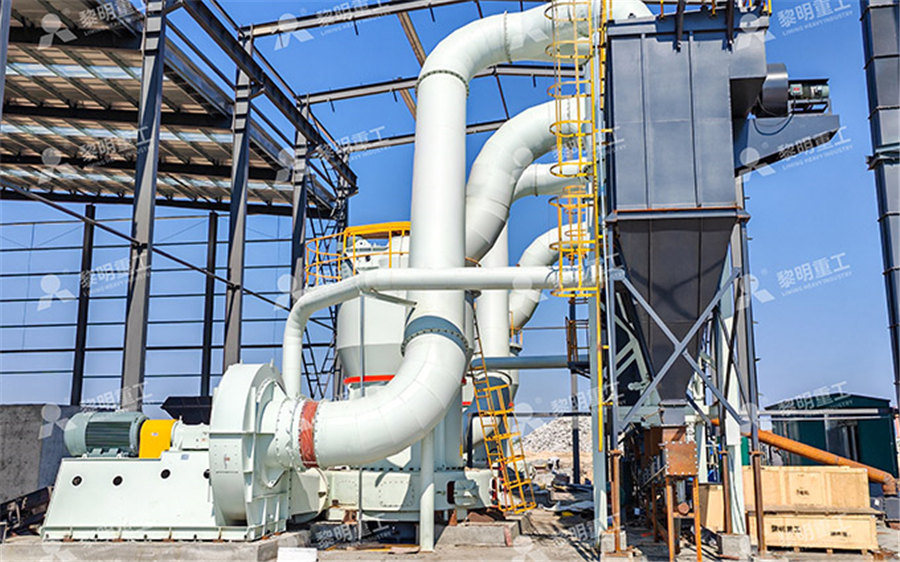
Research on energy saving improvement of ammonia
2018年12月1日 The improved desulfurization tower can ensure the uniform distribution of flue gas inlet, but also can improve the absorption efficiency and increase the recycling of reagents2011年5月15日 Flue gas flows downward along the tower and reacts with active ingredients of desulfurization in an effective reaction zone After desulfurization, the flue gas enters a bag A modeling and experimental study of flue gas desulfurization in a The results show that the desulfurization system can obtain higher desulfurization efficiency under 100% and 50% load conditions The outlet concentration can meet the requirement of ultralow Environmental Science PAPER OPEN ACCESS You may also like 2020年2月22日 The desulfurization tower installation business that broke out in the first half of 2019 broke the original supply and demand Among them, there are many ultralarge oil tankers (VLCC) and ultralarge ore carriers (VLOC) with conversion costs of hundreds of dollars Attempting to implement 1 or 2 retrofit projects, and Desulfurization tower retrofitting: changing the "handson" of
.jpg)
Fluegas desulfurization Wikipedia
Before flue gas desulfurization was installed, the emissions from the Four Corners Generating Station in New Mexico contained a significant amount of sulfur dioxide The G G Allen Steam Station scrubber (North Carolina) Fluegas desulfurization (FGD) is a set of technologies used to remove sulfur dioxide (SO 2) from exhaust flue gases of fossilfuel power plants, and from the 2019年7月27日 Manganese Orebased Wet FlueGas Recent Innovations in Chemical Engineering, 2020, Vol 13, No 0 3 nying the side reaction of Eq 4 to form MnS 2O 6 [28, 36, 42] At the same time, SOManganese Orebased Wet FlueGas Desulfurization: A Review2022年1月15日 The behavior of gasliquid twophase flow in a desulfurization tower, the influence of operating parameters, such as the pH value of the solution and the velocity of flue gas on the desulfurization rate, and the distribution of the gas temperature and velocity field in the evaporation tower have been studied [172], [173], [174] CSummary of research progress on industrial flue gas desulfurization 2016年6月3日 The Tower mill can be installed for a fraction of the cost of an equivalent kilowatt (horsepower) ball mill The Tower mill develops very little dynamic forces Therefore, its foundation can be a concrete floor slab designed for dead load only, whereas a cylindrical ball mill requires a reinforced concrete submat with a minimum of two times the mass of the rotating Tower Mill Operating Work Index 911Metallurgist
.jpg)
Simulation on Evaporation and Motion of Atomized Droplets in
2022年10月17日 The evaporation and motion of atomized droplets have an essential effect on the safe and efficient longterm operation of the desulphurization tower Therefore, the twophase flow model is established and solved by threedimensional steady Reynoldsaveraged NavierStokes equations; the droplets are tracked by EulerianLagrangian method The three factors, 2002年7月1日 Hot metal desulfurization slag is a highmetallic iron content slag produced at a typical steelmaking facility and is currently considered Initially, at a steel mill, iron ore, flux, and fuel (coke) are added into an oxygen blast furnace The materials combine and react to form liquid hot metal, gasses, and blast furnace Pelletizing steel mill desulfurization slag ScienceDirectDesulfurization is a technology used to separate SO 2 from its emitting sources such as exhaust flue gases of fossilfuel power plants, oil refineries, etc The crucial requirement to decrease sulfur loading in fuels to nearly zero content is imposed by mandatory environmental and health protocols as well as the accurate tolerance needed for their use in fuel applicationsDesulfurization an overview ScienceDirect Topics2023年6月19日 When the limestone vertical mill is operational, the internal hot blast stove typically generates hot air Depending on the production conditions, a fuelfired or coalfired hot blast stove can be chosen to ensure continuous evaporation of water from the raw materialsDesulfurization Vertical Mill Production Line of 40 Tons Per Hour
.jpg)
Numerical Simulation of flow field optimization in Flue Gas
of sintered flue gas desulfurization tower using ANSYS CFX software The simulation results showed that the gasliquid contact time was long when the flow field was uniform, and the pressure drop mainly occurred in the absorption zone, which provides a reference for improving the desulfurization efficiency of the desulfurization towerCurrently, desulfurization technologies can be categorized into three main types: wet flue gas desulfurization (FGD) [11], [12], [13], semidry desulfurization [14] and dry desulfurization [15]Wet flue gas desulfurization is widely employed in largescale desulfurization processes due to its high efficiency and low energy consumption [16]However, it poses a significant environmental Recent advances in process and materials for dry desulfurization 2021年6月1日 Taking a 200 MW coalfired power plant in North China with a limestonegypsum wet desulfurization system transformation project as an example, the effect of energysaving transformation of the Technical Transformation and Energy saving Analysis of Desulfurization TowerMill Vertical Agitated Media Mill Agitated Media Mill for wet dry grinding of ores and minerals Nippon EIRICH, Typical applications are the preparation of ore, Lithium ore and slag for high throughputs as well as the preparation of Towermill Vertical Agitated Media Mill
.jpg)
Sulfur dioxide removal: An overview of regenerative flue gas
2020年5月16日 Numerous mitigation techniques have been incorporated to capture or remove SO2 with flue gas desulfurization (FGD) being the most common method Regenerative FGD method is advantageous over other methods due to high desulfurization efficiency, sorbent regenerability, and reduction in waste handling The capital costs of regenerative methods are 2020年2月7日 Wet flue gas desulfurization is widely used in power plants because of its high desulfurization efficiency The reason why it is difficult to predict sulfur dioxide removal efficiency in flue gas is that it is related to many factors In this paper, the SO2 was removed by absorbing with ammonia solution in a packed tower Experimental studies have shown that the operating Prediction of SO2 removal efficiency for ammoniabased wet 2024年5月15日 Abstract: Densephasetower desulfurization technology is an emerging semidry fluegas desulfurization ash process, ie, the flue gas is allowed to enter the desulfurization tower from the bottom up and, at the same time, is sprayed with a desulfurizing agent that undergoes an acid–base reaction with the flue gas in the ascent process1,2,*, Hao Li 3 , Hongzhi Ma 3, 2industrial seawater desulfurization process, more desulfurization tower type has spray absorption empty tower, tray tower, liquid column tower, jet bubbling tower and so on 43 Selection of desulfurization tower In the desulfurization tower , the cost effective flue gas flow rate is 22~30m/s ThroughOptimization design of marine seawater desulfurization technology
.jpg)
The Desulfurization of Magnetite Ore by Flotation with a
2016年7月8日 The Desulfurization of Magnetite Ore by Flotation with a Mixture of Xanthate and Dixanthogen July 2016; sample at 667% solid density was ground in a ball mill to gain an 85 wt % passing size 2020年1月22日 This review summarizes the background information of Mn ore slurry desulfurization, the desulfurization mechanism, the technological process, and the desulfurization devicesManganese orebased wet flue gas desulfurization: A mini review2022年6月1日 Some scholars have studied the multiphase flow and the desulfurization efficiency in the desulfurization tower For example, Wu et al [9] proposed a water evaporation model and a desulfurization model to study the heat transfer and desulfurization reaction in the semidry desulfurization process Zhang et al [10] studied the effect of humidified water on the semidry Numerical simulation study on gassolid flow ScienceDirect2024年3月7日 SO 2 in the flue gas from coal combustion has become the main cause of air pollution Largescale researches are carried out to control SO 2 emissions, of which flue gas desulfurization technology is the most commonly Investigation into the Dissolution Kinetics of Different
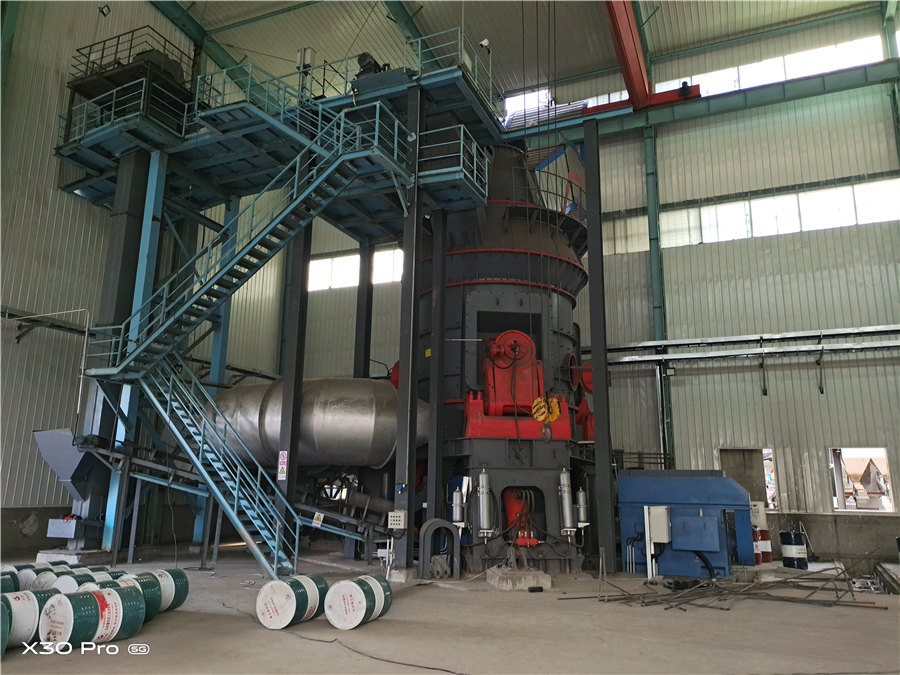
Causes and Control Technology of Slurry Overflow in
In the flue gas ammonia desulfurization process of the coal chemical industry, ammonium sulfate slurry in the desulfurization tower often foams and overflows, which wastes resources and pollutes the environment The solution to this DOI: 102478/pjct20200006 Corpus ID: ; Optimization the operation parameters of SDA desulfurization tower by flow coupling chemical reaction model @article{Mei2020OptimizationTO, title={Optimization the operation parameters of SDA desulfurization tower by flow coupling chemical reaction model}, author={Dan Mei and Junjie Optimization the operation parameters of SDA desulfurization tower EPA600/276281 October 1976 DESULFURIZATION OF STEEL MILL SINTER PLANT GASES by Gary D Brown, Richard T Coleman, James C Dickerman, and Philip S Lowell Radian Corporation PO Box 9948 Austin, Texas 78766 Contract No 68021319, Task 58 ROAPNo 21AQR005 Program Element No 1AB015 EPA Task Officer: Norman Plaks Desulfurization of Steel Mill Sinter Plant GasesAs a manufacturer of sulfur grinding mill machines, HCMilling(Guilin Hongcheng) recommends that you choose a manganese ore vertical mill for the preparation of manganese ore powder desulfurizer Preparation of HLM Vertical Desulfurization Agent grinding mill machine Product Advantages of Manganese Ore Powder Desulfurization Agent 1Which Type Of Desulfurization Agent Grinding Mill Machine
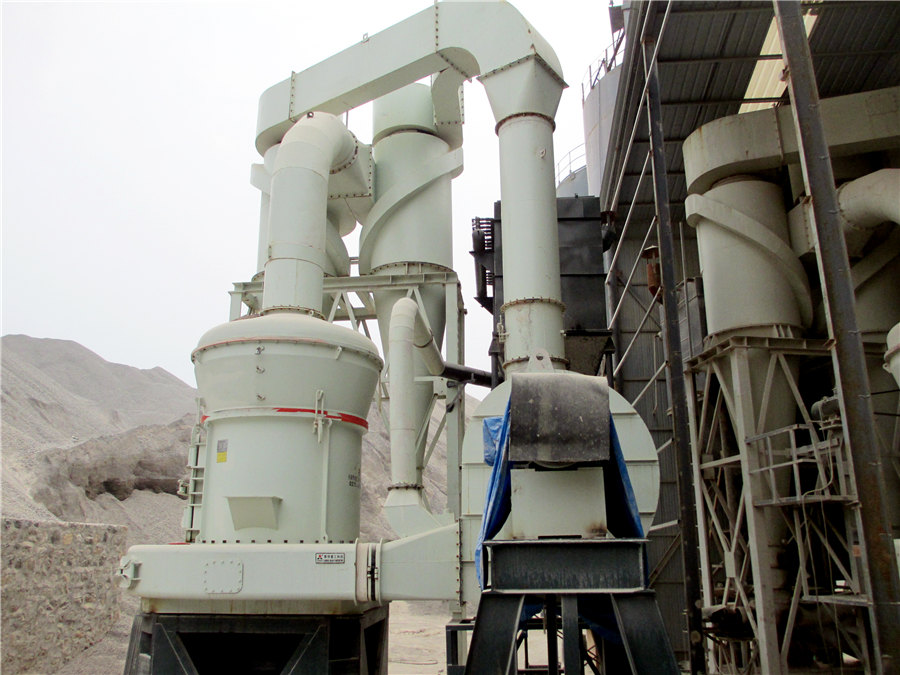
Dry Flue Gas Desulfurisation Technology ScienceDirect
2000年7月31日 Sustainable Built Environment Sustainable Manufacturing J He, J Xu, in Encyclopedia of Sustainable Technologies, 2017 Control Methods of SO x Technologies for SO 2 control are concentrated on both prevention of SO 2 emission and endofpipe treatment of flue gas Fuel cleaning is commonly applied as the SO 2 prevention method, while wet and dry flue 2021年3月17日 The lowtemperature wet oxidation behavior of semidry desulfurization ash from iron ore sintering flue gas in ammonium citrate solution was investigated for efficiently utilizing the lowquality desulfurization ash The effects of the ammonium citrate concentration, oxidation temperature, solid/liquid ratio, and oxidation time on the wet oxidation behavior of Lowtemperature oxidation behavior and mechanism of semi Horizontal spray tower technology is a new flue gas desulfurization system technology that was developed at the University of Science and Technology Beijing, Center for the Environment, overcoming the shortcomings of the vertical spray tower with regard to high desulfurization efficiency, small pressure loss, low operation cost, and easy maintenance, among others Numerical simulation of flue gas desulfurization by horizontal spray towerDownload scientific diagram Grids of SDA desulfurization tower from publication: Optimization the operation parameters of SDA desulfurization tower by flow coupling chemical reaction model Grids of SDA desulfurization tower Download Scientific Diagram
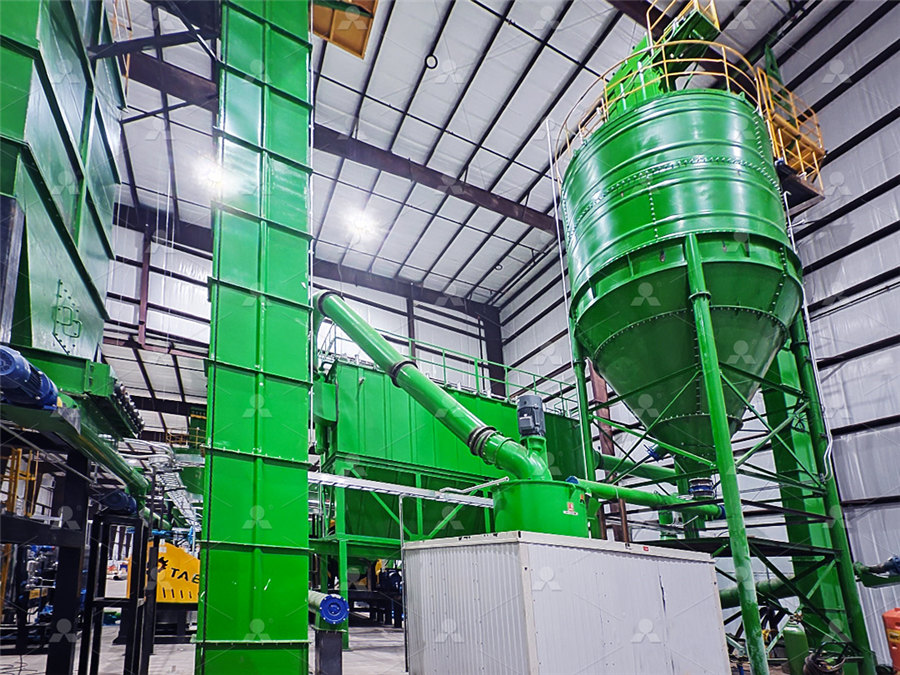
Full article: Modeling and optimization of wet flue gas desulfurization
2019年3月13日 Introduction Sulfur dioxide (SO 2) is one of the major pollutants contributing to frequent hazy weather in ChinaA large amount of SO 2 in the atmosphere comes from coal combustion As the amount of coal for power generation accounts for 45% of the total coal consumption in 2015 (National Bureau of Statistics [NBS] Citation 2017), the Chinese The current industrial method for removal of sulfur from fuels is hydrodesulfurization (HDS), which is a high temperature, high pressure catalytic process This makes HDS a very costly option for deep desulfurization An evaluation of desulfurization technologies for2022年4月26日 Open desulfurization towers use seawater to clean the flue gas Seawater is generally weakly alkaline In the desulfurization tower, the seawater is fully mixed with the flue gas by spraying, and the sulfur oxides are Classification of ship desulfurization towers CYCO Therefore, desulfurization is an essential link in the iron ore pretreatment process Iron Ore Desulfurization Methods The desulphurization of iron ore mainly improves its quality and reduces environmental emissions during subsequent Iron Ore Desulfurization Methods Processes JXSC
.jpg)
Suitable FGD limestone mill, low investment in power plants
2023年2月15日 Faced with increasingly stringent air quality regulations, we will see an increasing need for FGD (flue gas desulfurization) units, efficient devices to remove SO 2 of the flue gas from a coalfired power station That will bring a moderate increase in limestonebased sorbents consumption2023年10月18日 Direct application of highsulfur fuels and ores can cause environmental pollution (such as air pollution and acid rain) and, in serious cases, endanger human health and contribute to property damage In the background of preserving the environment, microbial desulfurization technologies for highsulfur fuels and ores are rapidly developed This paper Mapping the knowledge domain of microbial desulfurization 2024年3月5日 This is achieved through a wet flue gas desulfurization (FGD) system In this process, a slurry of limestone and water, known as absorption slurry, is used Inside the absorption tower, SO2 in the flue gas reacts with calcium carbonate (CaCO3) in the slurry and oxygen to form calcium sulfite (CaSO3) and waterDesulfurization and Absorption Tower Issues in Dust Collector The Desulfurization of Magnetite Ore by Flotation with a Mixture of Xanthate and Dixanthogen Jun Yu, Yingyong Ge * and Xinwei Cai mill discharge was transferred to a 10 dm3 XFDtype laboratory flotation cell The air flow rate was 45 dm3/h and the agitation speed was 1800 rpmThe Desulfurization of Magnetite Ore by Flotation with a Mixture
.jpg)
HighEfficiency Vertical Coal Mill Enhancing Coal Pulverization
Application field: Coal vertical mills are widely used in cement production, calcium carbonate crushing processing, coal powder preparation stations, gypsum powder processing, power plant desulfurization, phosphate rock grinding, metallurgical industry and 2022年3月11日 The flue gas wet desulfurization facility has the following aspects: preparation system (mainly bucket elevator, limestone silo, ball mill, limestone slurry tank, limestone cyclone station, lim estone supply pump), reaction system (mainly absorption tower VWHPRIODUJHFRDO ILUHGSRZHU IOPscienceusing a laboratory ball mill to select the optimum particle size for the experiments Due to the importance of the minimum changes in the current plant circuit, the feasi bility of the desulfurization of the current concentrates of the iron ore industry was performed at d 80 of 82, 72 and 38 µm The tested circuit is shown in Fig 3DESULFURIZATION OF IRON ORE CONCENTRATE USING A