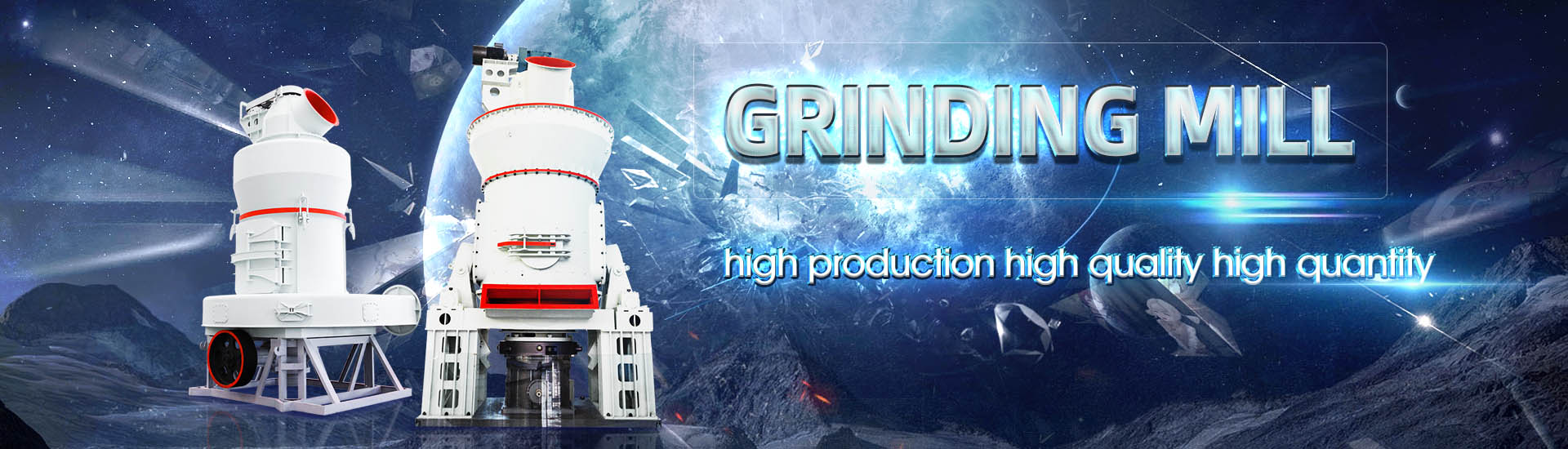
How to improve the output of slag cement mill
.jpg)
OPTIMIZATION OF CEMENT GRINDING OPERATION IN BALL MILLS
Optimization of the Cement Ball Mill Operation Optimization addresses the grinding process, maintenance and product quality The objective is to achieve a more efficient operation and increase the production rate as well as improve the run factor Consistent quality and As grinding accounts for a sizeable share in a cement plant’s power consumption, optimisation of grinding equipment such as ball mills can provide significant cost and CO 2BALL MILLS Ball mill optimisation Holzinger Consultingcement manufacturers import slag The main benefit of slag cement (Type IS) is the effectiveness in mitigating alkalisilica reaction (ASR) by binding alkalis in the concrete hydration reaction1 GRINDING Grinding options for slag and pozzolan PEC 2024年6月1日 Steelmaking slag has promising potential for cement clinker production, boasting high levels of CaO Pretreatment methods enhance slag quality for cement production Slag Utilization of steelmaking slag in cement clinker production: A
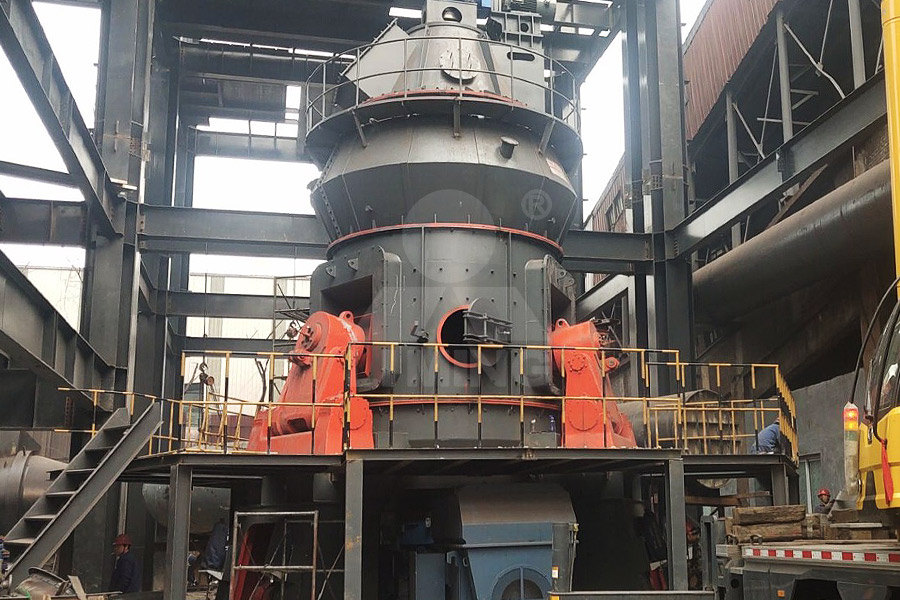
Analysis of the efficiency of the process in closed circuit ball mills
Ball mills for fine grinding cement clinker and additives are widely used around the world To improve the efficiency of a ball grinding the ball mills are transferred in closed circuit with air 2018年7月1日 This study aimed at optimizing both the energy efficiency and the quality of the end product by modifying the existing flowsheet of the cement grinding circuit As a general Energy and cement quality optimization of a cement grinding circuit2008年3月3日 Grinding slag for cement replacement requires only about 25% of the energy needed to manufacture normal Portland cement Without the use of granulated material the Efficient and reliable handling of GBFS and GGBFS at Global Slagthe form of a modified Loesche mill for fine grinding: LM – CS (cement/slag) In this mill preparatory rollers (support rollers) took over preparation of the grinding bed and the grinding 2 µm 5 µm Loesche
.jpg)
SikaGrind® for vertical roller mills
State of the art for Grinding Aids is: ́ Increase the share of coarse particles on the grinding track to obtain high interfriction ́ Improve the properties of the finished cement Concrete producers 2024年8月12日 This study investigates the influence of various types and dosages of sulfatic and alkaline activators on the performance of low emission supersulfated blast furnace slag Blast furnace slag supersulfated cements: composition 2023年5月15日 Steel slag is the main solid waste generated in the steelmaking process, accounting for 15 to 20% of crude steel output [1]China's crude steel output in 2021 was 1035 billion tons [2], more than half of the global crude steel output (19505 billion tons) [3], and the steel slag output exceeded 120 million tonsIn contrast, the comprehensive utilization rate of Comprehensive utilization of steel slag: A review ScienceDirectTips for improve cement kiln working efficiency Improve process level: The output of cement is closely related to its production process The better the production process, the higher the annual output of clinker production line How to Improve Output Of Cement Rotary Kiln
.jpg)
Cement grinding Vertical roller mills VS ball mills
FLSmidth acquired the rights to his patent and started selling an improved version of this mill all over the world For the cement industry the ball mill was really an epochmaking breakthrough as for almost 80 years it was the 2008年3月3日 The use of GGBFS as a partial Portland cement replacement takes advantage of the energy invested in the slagmaking process and its corresponding benefits with respect to the enhanced cementitious properties of the slag Grinding slag for cement replacement requires only about 25% of the energy needed to manufacture normal Portland cementEfficient and reliable handling of GBFS and GGBFS at Global Slag2017年4月23日 It was only rarely that the full strength of Portland cement was fully utilized As a matter of fact, outside of reinforced concrete, the great strength of Portland cement was rarely utilized A cement of much less strength would suffice for most purposes The output of slag cement would depend upon the output of slag from the furnace at NewcastleHow to Make Cement From BlastFurnace Slag 911Metallurgiststrengths of a blended cement with a high slag content All the main cement characteristics are reported as follows: Table 1: Cement production properties Cement type CEM III/B 42,5 N Blaine 4500 cm2/g Recipe Clinker 33%, Gypsum 2%, Slag 65% Mill output 57 t/h Compressive strengths 2days 11 MPa 7days 30 MPa 28 days 43 MPaImprovement of cement performances through the use of
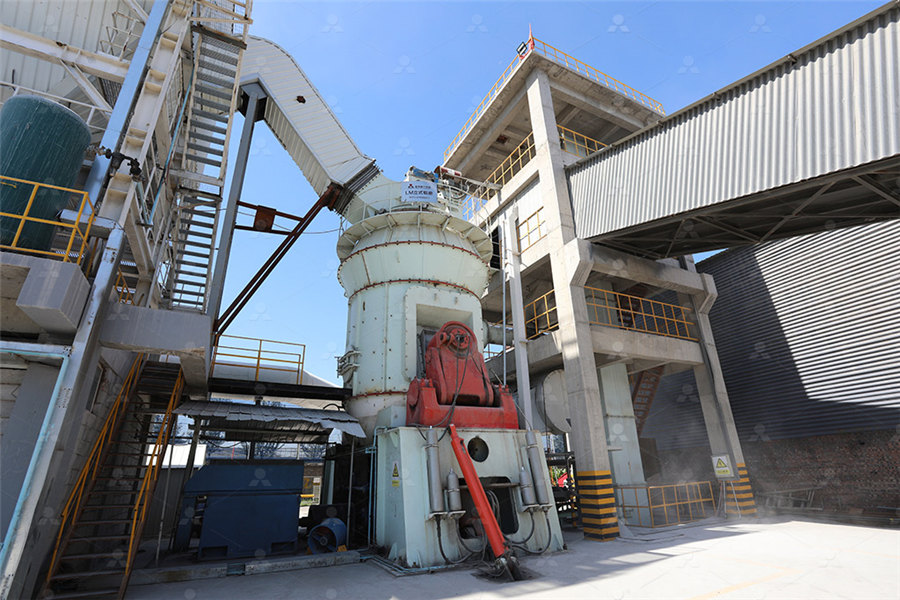
Cement Mill Optimization: Practical Strategies for Enhanced
Optimizing ball mill internals: The internal design of the ball mill, including the diaphragms, liners, and grinding media, can also impact the grinding efficiency Using highquality grinding media, optimizing the diaphragm design to improve ventilation, and regularly inspecting and replacing wornout liners can result in up to 15% reduction 2020年3月19日 The power consumption of raw meal and cement ball mills accounts for about 23% of the power consumption of cement plants and about 13% of the cost of cement Therefore, in order to reduce power consumption, reduce costs, and improve economic efficiency, it is necessary to significantly increase the mill outputHow to improve ball mill output quality and reduce power Many examples prove that CHAENG cement ball mill can run steadily for a long time 2 Novel structure, strong production capacity: CHAENG cement mill adopts the latest and unique streamline design of the world, to reduce the ventilation resistance, increase the effective volume, make discharge easy, and improve the output of the millCement ball mill Xinxiang Great Wall Machinery Co, Ltd PDF In general, the slag powder is processed by the slag grinding plant in advance, and slag powder will be sent into the cement plant for making slag cement, so it is particularly important to select the appropriate slag grinding plant The core equipment of slag grinding plant is vertical cement mill Slag cement manufacturing process can be Slag Cement Production Line Blast Furnace Slag Cement Making
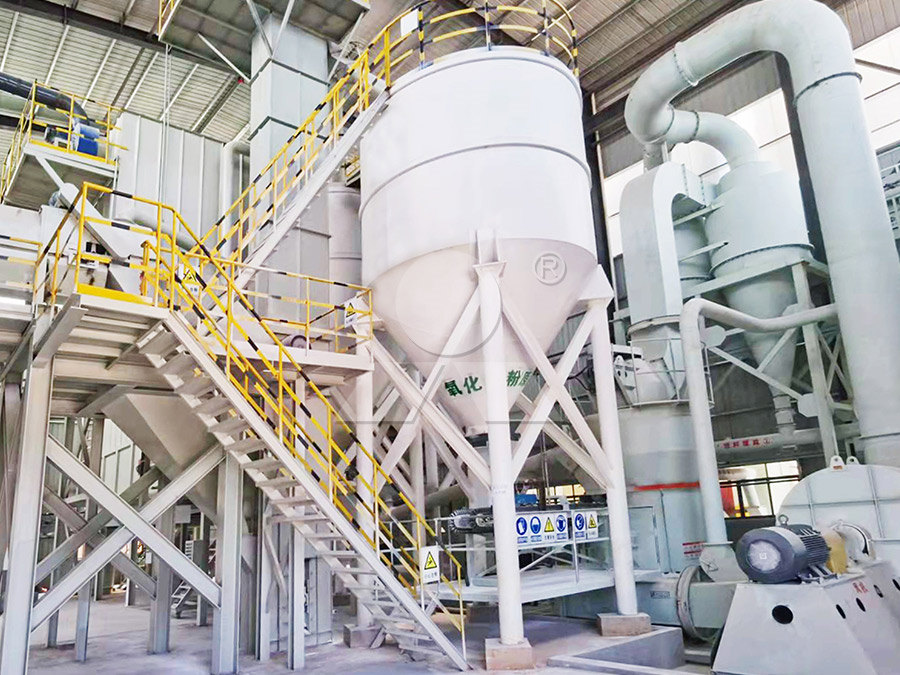
The LCA of portland cement production in China
2014年9月23日 Purpose Cement production is associated with a considerable environmental load, which needs to be fully understood before effective measures can be taken The existing literature did not give detailed life cycle assessment (LCA) study of China and had limited potential for investigating how best available techniques (BATs) would provide a maximum Environmental Benefits of Slag Cement Slag cement is used in nearly all types of concrete construction: pavements; structures and foundations; mass concrete (ie, dams and retaining walls); and prestressed, dry cast and precast Slag Cement Heidelberg Materials2022年7月18日 With respect to the mechanical properties, durability and thermal behavior, groundgranulated blastfurnace slag (GGBS) delineates a rational way to develop sustainable cement and concreteA Comprehensive Review on the Ground Granulated In addition to the vertical slag mill, other types of cement mill that can grind slag powder include: cement ball mill, pregrinding cement roller press, and cement roller press for final grinding For slag grinding plant, ball mill generally causes problems of dust accumulation, low grinding efficiency and high grinding temperatureSlag Mill, Slag Grinding Mill Cement Plant
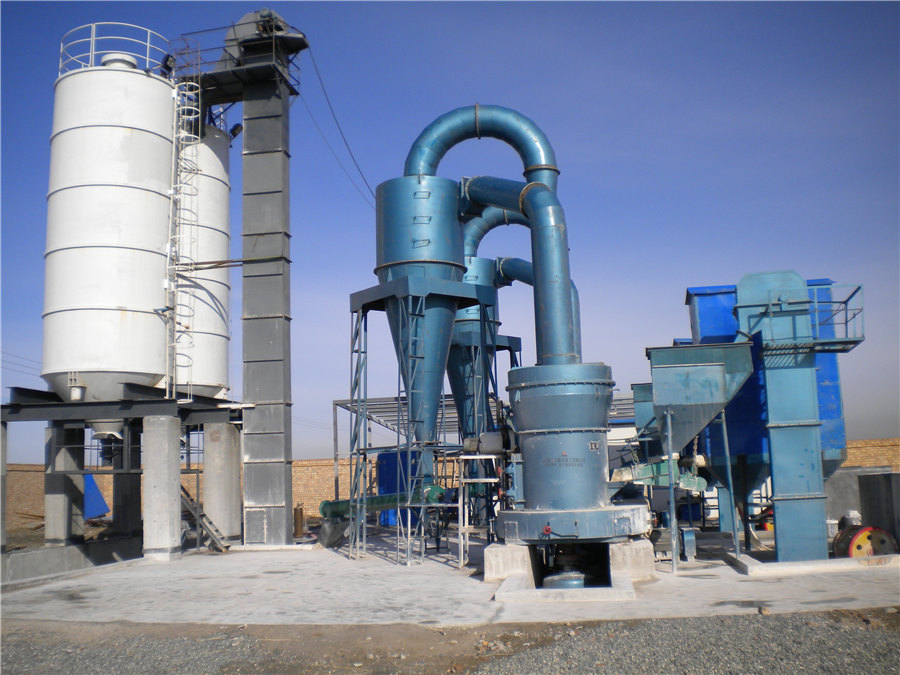
Comprehensive Utilization Technology of Steel Slag
2019年5月23日 The process of making steel slag cement is a simple manufacturing technique with less investment and low cost Meanwhile, steel slag cement has excellent performances such as high longterm strength, low heat of hydration, and wear resistance Thus, steel slag cement is applicable in such aspects as general roads, irrigation, and water conservancy2020年4月1日 Use of BOFS as a cement binder is an established method of reuse, but research is still being conducted regarding: (i) ways to improve the cementitious qualities of the slag, and (ii) ways in which the addition of BOFS changes the properties of cement (Li et al, 2013, Wang, 2016a, Wang, 2016b, Xiang et al, 2016, Zhao et al, 2016, Lu et al, 2018, Basic oxygen furnace slag: Review of current and potential usesHow to improve the output of cement plant is incredibly necessary for rising the operating Grinding Plant potency of cement assembly line and is also the matter that everyone cares most China Great Wall Machinery Manufacturing Co has pay abundant time and energy on rising the yield of cement mill the subsequent six measures rising the yield of cement mill is summarized by How to improve the output of cement mill?It is widely used in clinker grinding production of cement plant and slag grinding plant CHAENG can provide various types of vertical cement mills with productivity of 50250t/h The biggest advantage of CHAENG is to have a large casting base and large machining workshops, which greatly shortens the delivery cycle of cement vertical millThe important role of vertical roller mills in the cement industry
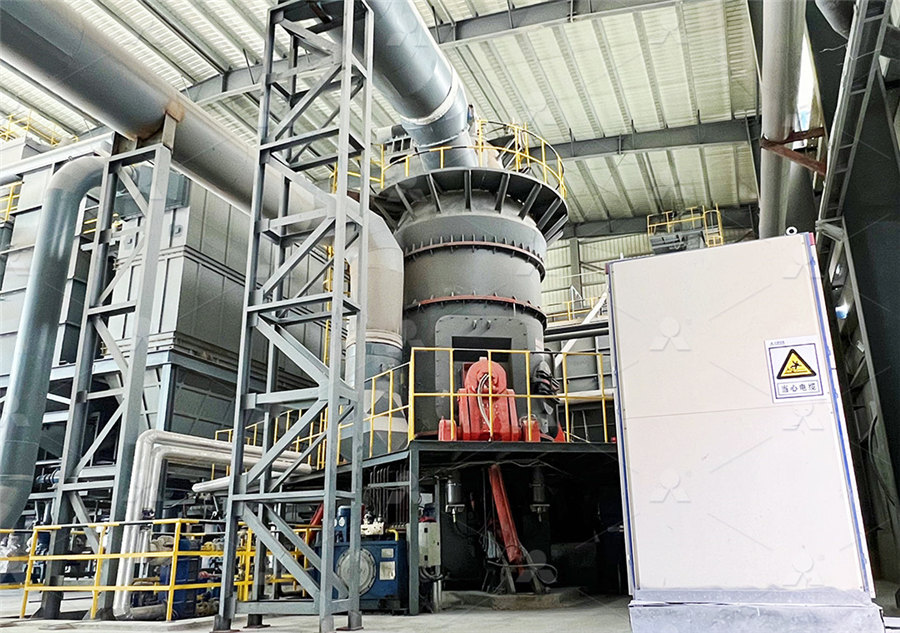
Cement Separator HighEfficiency Cement Mill Separator
High efficiency: AGICO Cement Mill Separator is designed to separate fine materials from coarse materials, which greatly improves the grinding efficiency of the cement mill It can effectively increase the output of the cement mill, reduce energy consumption, and improve the quality of the finished cementIf too much feeding will cause the ball mill to rise, the rising belly will reduce the efficiency of the steel ball inside the ball mill, and the qualified materials can not be discharged, reducing the output Therefore, it should be uniformly fed during the feeding process Improve Material of Liner and Effective Volume of CylinderHow to Improve Working Efficiency of Ball Mill2023年10月25日 With the mass production of coalbased solid waste, coal mine filling can effectively consume it The coal gasification slag is modified and prepared as coal mine filling material to meet the relevant technical requirements, which can realize the recycling of coal mine → coal chemical industry → coal mine In this paper, in order to explore the evolution law of Pore characteristics of sulfateactivated coal gasification slag cement employed for comminution of Blended, Slag and Port Land cement grinding The cement grinding and drying system be dovetail of a large array of obsolete incompetent equipment and was completely replaced by a single VRM, it improves the fineness and diminish the maintenance and power consumption [1, 34, 36] Optimization of cementPROCESS CONTROL FOR CEMENT GRINDING IN VERTICAL ROLLER MILL
.jpg)
OK™ CEMENT MILL
hardest materials The OK™ cement mills are available in all sizes 0 100 200 300 400 500 600 700 800 OK 776 OK 434 OK 484 OK 404 OK 524 OK 716 OK 816 OK 666 OK 614 OK 564 OK ™ cement mill production and slag grinding production (t/h) OK 283 OK 373 OK ™ cement mill and slag grinding Actual capacity depends on product fineness Supplementary cementing materials Daman K Panesar, in Developments in the Formulation and Reinforcement of Concrete (Second Edition), 2019 332 Slag cement Although slag cement has been reported to improve workability, increase cohesiveness, and reduce water demand, the angular and irregular slag cement particles do not benefit as much from the “ballbearing Slag Cement an overview ScienceDirect TopicsThe cement quality control of cement plant is mainly based on specific technological process, which includes the quality control of various raw materials, semifinished products used in the production process, the sampling analysis of materials, to ensure the stability and uniformity of raw material composition The quality control of raw materials requires chemical composition How to improve cement plant process for better cement quality2020年1月11日 Working site of ball mill grinding media refilling In addition to the grinding media proportion and frequency, other factors such as the grinding media material, the shape and so on can improve the ball mill efficiency Consult a professional engineer for details The optimized grinding media can improve the ball mill efficiency by about 30%5 Ways to Improve the Ball Mill Efficiency FTM
.jpg)
PROCESS DIAGNOSTIC STUDIES FOR CEMENT MILL
The mill performance is evaluated and recommendations are formulated based on the past history of the mill operations, inspections, process measurements, feed/product characteristics and grinding performance, in order to improve mill output and reduction in power consumptions in the ball mill system DIAGNOSTIC STUDY History of mill operationsSemifinishing grinding system: after ground by cement roller press, materials are divided into three parts through an air classifier: coarse, medium and fine, in which the coarse material is returned to the roller press for regrinding, the medium material is put into a ball mill for further grinding, and the fine material is directly discharged as the finished cement productCement Roller Press Roller Press In Cement Plant Roller Press hardest materials The OK™ cement mills are available in all sizes 0 100 200 300 400 500 600 700 800 OK 776 OK 434 OK 484 OK 404 OK 524 OK 716 OK 816 OK 666 OK 614 OK 564 OK ™ cement mill production and slag grinding production (t/h) OK 283 OK 373 OK ™ cement mill and slag grinding Actual capacity depends on product fineness OK™ CEMENT MILLThe vertical cement mill is largescale cement grinding machine With advantages of energyefficient and stable quality, vertical roller mill is widely applied to many industries, such as cement, power, metallurgy, chemical and nonmetallic mining industry and etc As a typical type of Cement Mill, vertical cement mill set crushing, drying, grinding, grading transportation in one, it grind Vertical Cement Mill
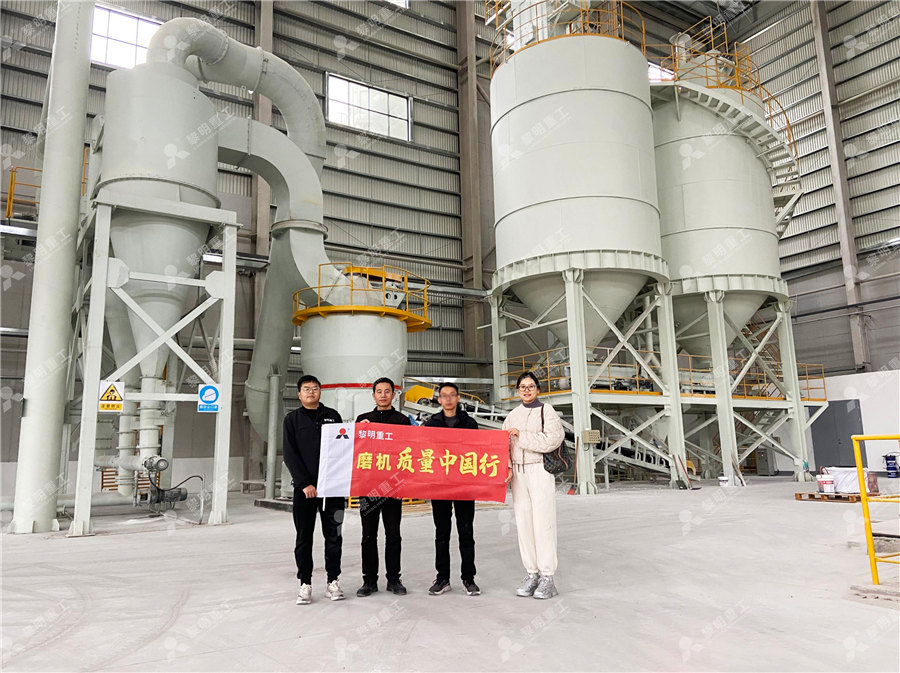
Analysis of the efficiency of the grinding process in closed circuit
Improving inner mill accessory (lining mill partition, the output diaphragm and composition of the grinding media) also allows to improve the process of grinding in a closed circuit ball mill However, the performance of the grinding unit 4×135 m with the implementation of these activities is increasing to 988 to 117 tph while reducing thestrengths of a blended cement with a high slag content All the main cement characteristics are reported as follows: Table 1: Cement production properties Cement type CEM III/B 42,5 N Blaine 4500 cm2/g Recipe Clinker 33%, Gypsum 2%, Slag 65% Mill output 57 t/h Compressive strengths 2days 11 MPa 7days 30 MPa 28 days 43 MPaImprovement of cement performances through the use of Our bestinclass OK™ Mill is a globally successful vertical roller mill solution for grinding raw material, cement and slag Its cuttingedge design features consistently deliver the highest quality products with the greatest efficiency It OK™ Raw and Cement Mill2020年12月29日 6 Methods to Improve the Output of Raymond Mill Dec 29, 2020 As one of the commonly used milling equipment, stone Raymond roller mills are suitable for high fine milling processing of more than 280 kinds of materials in the mining, chemical, and construction industries The output of the Raymond mill grinder machine is directly related to the efficiency 6 Methods to Improve the Output of Raymond Mill
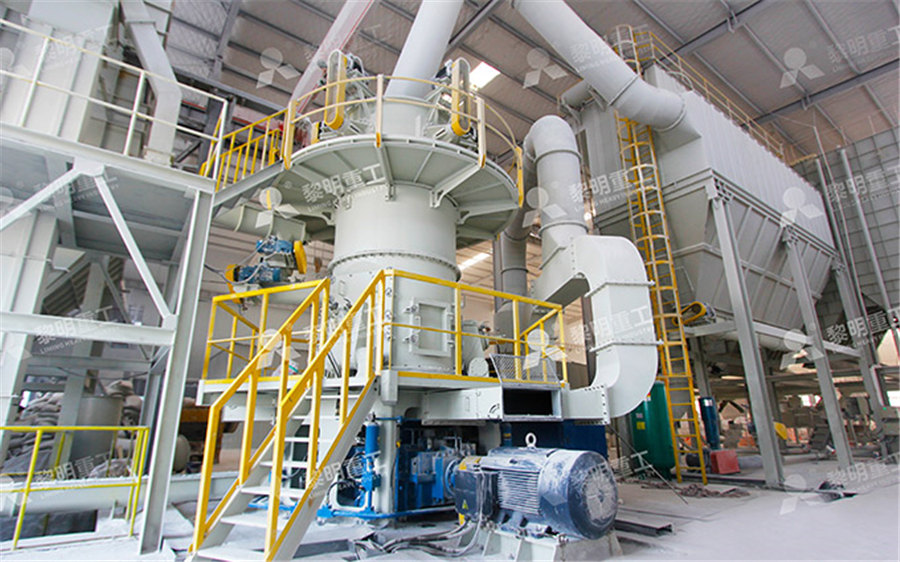
Operational parameters affecting the vertical roller mill
2016年9月1日 Cement production is one of the most energyintensive manufacturing industries, and the milling circuit of cement plants consumes around 4% of a year's global electrical energy productionCement mill open to close circuit The differences between the openflow system and close circuit system: compared with the openflow system, the close circular flow grinding system has less overgrinding in the cement mill, and the output of the cement mill is higher than that of the openflow grinding system of the same specification; the unit power consumption is also low; the Cement Plant Upgrading Modernization AGICO CEMENTSlag Cements are well recognised in many countries with traditional and powerful steel production High chemical resistance, low heat of hydration and sustainability are strong arguments for Slag Cements The main disadvantage of Slag Cement is the slow strength development Slag (ASTM C 989 and EN 15167) or Slag cement (ASTM C 595 and EN 1971 Picture: Loesche GmbH, Germany CEMENT SikaGrind® FOR VERTICAL ROLLER MILL2017年10月25日 It states that the output of new product size material of a ball mill circuit with a given feed size is determined by: a the total mill power draw; b the classification system efficiency, which defines the fraction of the total mill power effectively applied to the grinding of coarse material;How to Improve Ball Mill Performance 911Metallurgist
.jpg)
How To Optimize The Operation Of The Cement Mill
2024年1月23日 The efficient operation of a cement mill is vital for the overall productivity and quality of the cement production process Constant adaptation and optimization are essential in the dynamic environment of cement manufacturing to meet quality standards and 2018年2月5日 Piles of steel slag, a solid waste generated from the iron and steel industry, could be seen due to no utility found for the past century Steel slag has now gained much attention because of its new applications The properties of slag greatly influence its use and thus had got varied applications The chemical composition of steel slag varies as the mineral composition Review on the innovative uses of steel slag for waste minimization