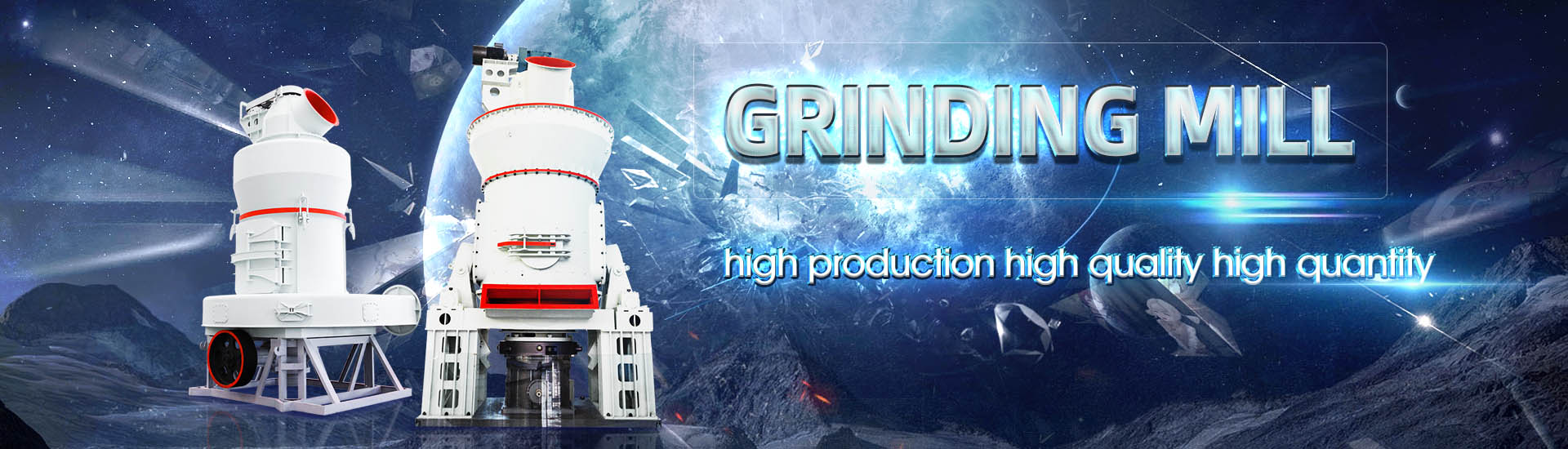
Installation method of coal bunker top ore mill

010Method Statement of Coal Mill Instattalation PDF
This document provides a method statement for installing a coal mill at a project site It outlines the general components and purpose of the coal mill It then describes the responsibilities of personnel overseeing the installationOne method is to provide the facility itself with a coalhandling system in order to lay indigenous and imported coal in alternate layers on the belts while conveying coal to the bunkers; then, Coal Bunker an overview ScienceDirect TopicsFigure 5 shows the installation of a vertical roller mill in a typical pulverized fuel system These mills are designed for pressurized operation since primary air fans are located upstream of the A Comparison of Three Types of Coal Pulverizers Babcock PowerBunkers are loaded with granular or powdery material which exerts pressure on the walls of the bunker The main objective of the study is to evaluate the linear static performance of the Bunker ISSN 23951621 IERJournal
.jpg)
Improving Coal Pulverizer Performance and Reliability Pall
Pulverization is currently the favored method of preparing coal for burning Mechanically pulverizing coal into a fine powder enables it to be burned like a gas, thus allowing more 2012年11月17日 The document discusses coal mill/pulverizers used in thermal power plants It describes how pulverized coal is dried, ground, circulated, and classified within the mill to produce a fine powder that is then transported to Coal mill pulverizer in thermal power plants PPTCoalfired plants are the most widely used power plant today They involve the combustion of coal producing high pressure (typically 2400–3500 psig, ~165–240 bar) and high temperature Instrumentation and control in coalfired power plant ICSCCoal mills or pulverizers play a very essential part in the coalfired power production system Coal mills grind the coal into fine powder, and the primary air entering the mill dries and drives the Coal Mill an overview ScienceDirect Topics
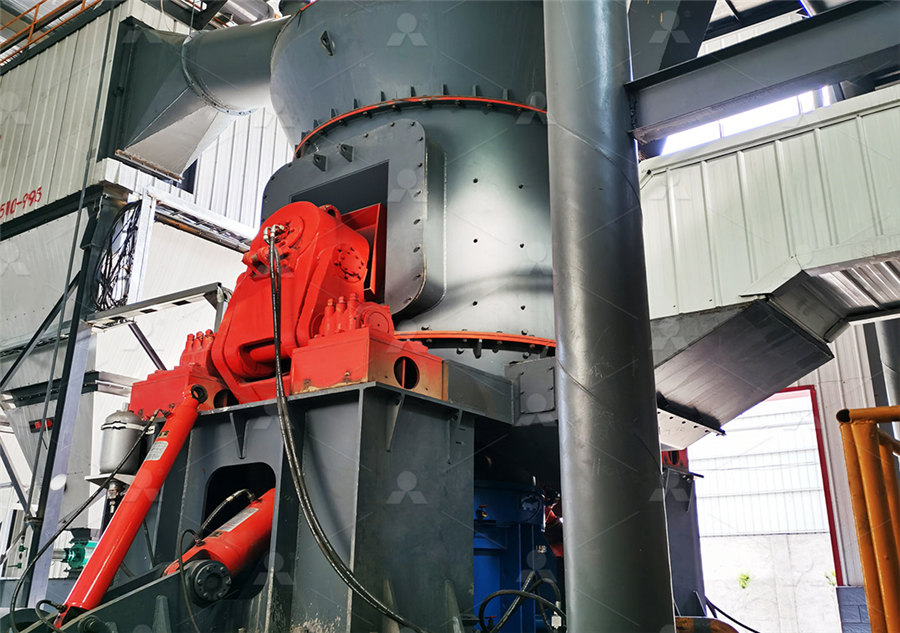
Coal Preparation Systems for Boilers Springer
Coal can be burned in a number of ways Depending on the characteristics of the coal and the particular boiler application, the designer may chose pulverized coal (PC) firing, cyclone firing, 2021年5月21日 To assess the deformation of a coal bunker and propose effective preventative measures for such, a realtime monitoring system was designed Moreover, methods were Multifactor dynamic analysis of the deformation of a coal bunker 2020年4月2日 Each mill bunker has one Coal mill motor power (kW) 0 4171 4548 439 The need to operate a boiler efficiently in today's environment is at the top of many plant owners and Analysis of the Coal Milling Operations to the Boiler The invention discloses a method and a system for preventing the coal blockage of a raw coal bunker In the operating process of a coal feeder, water is filled into the raw coal bunker, and a water film is formed on the inner wall of the raw coal bunker in order to prevent pulverized coal from being agglomerated on the inner wall of the raw coal bunkerMethod and system for preventing coal blockage of raw coal bunker
.jpg)
Improving Coal Pulverizer Performance and Reliability Pall
Bunker To Boiler Furnace Raw Coal Feeder Exhauster Hot Air Motor Coal Pulverizer Figure 1: Simplified diagram detailing a directfired coal burning system 1 EPRI study on large coal fired utility boilers (greater than 600MW) using pulverizers with capacities greater than 50 tons per hour Combustion Engineering 783RP BowlMill Coal Pulverizer2020年4月7日 Monitoring and diagnosis of coal mill systems are critical to the security operation of power plants The traditional datadriven fault diagnosis methods often result in low fault recognition rate or even misjudgment due to the imbalance between fault data samples and normal data samples In order to obtain massive fault sample data effectively, based on the Modeling of Coal Mill System Used for Fault Simulation MDPIA simple energy balance model of the coal mill is derived in (Odgaard and Mataji 2006), this model is based on a more detailed model found in (Rees and Fan 2003)In this model the coal mill is seen as one body with the mass m mThe following variables are defined: T(t) is the temperature in the coal dust flow in the mill, ṁ PA (t) is the primary air mass flow, T PA (t) is Coal Mill an overview ScienceDirect Topics2021年5月21日 To assess the deformation of a coal bunker and propose effective preventative measures for such, a realtime monitoring system was designed Moreover, methods were proposed for monitoring the coalbunker inclination, settlement, groundwater level, temperature, and material level By using a vector autoregression model and timeseries data for the coal Multifactor dynamic analysis of the deformation of a coal bunker
43.jpg)
(PDF) INSTALLATION OF HIGH CAPACITY BELT CONVEYOR
2023年10月12日 The present Indian annual demand of 120 Mt is expected to go up to 310 Mt by the end of this century Although the major share of this is expected to come from opencast mines, underground coal 2022年3月23日 The foundation of the coal bunker is the maintenance structure of bored piles + anchor rods + concrete columns, coal retaining walls, and brick walls, and the elevation of the bearing surface is 43m The upper part of the coal bunker is a space frame + purlin + highstrength pressure steel plate structureSpace frame installation technology of a large barrel closed coal bunkerThis is the calculated coal pressure which will try to cause the deflection of bunker walls Figure 4 Wind Load Application Figure 3 Coal Load Applications The maximum pressure is found at the hopper section of the bunker It increases from top to bottom of the bunker D Wind Load Application Wind load is applied on the bunker face according Bunker ISSN 23951621 IERJournal2016年8月5日 Power; Generation; Thermal; Managing Coal Fired Thermal Power Plants Efficiently This article identifies areas where installation of instrumentation and controls can bring about energy efficiency, safety and Managing Coal Fired Thermal Power Plants Efficiently
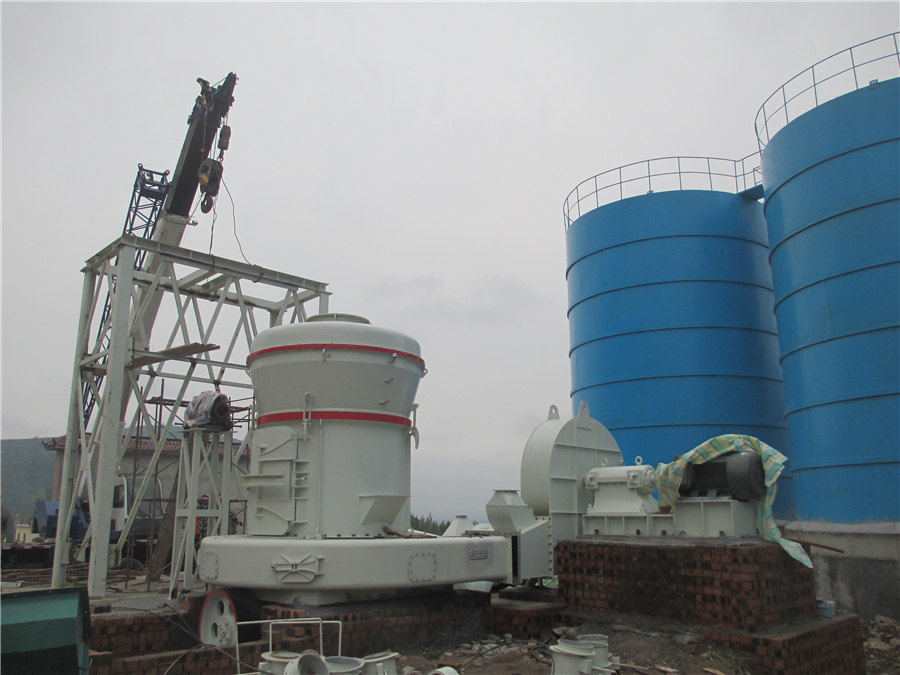
Coal SiloBunker Firefighting Procedures
followed as required Coal bunker, coal silo, and coal feeder fires shall be extinguished using an approximate 1 percent or greater concentration of F500 encapsulator agent and a Piercing Rod Kit This method and concentration are recommended In the PRB Coal Users Group Best Guidelines Practices for Bunker Silo Fires2016年2月14日 A coal mine in the central district of Botswana is experiencing premature failure of conical picks which mine 150350 tons of coal/ pick rather than 400 tons/pick specification(PDF) COAL MINING METHODS ResearchGate2021年10月1日 To assess the deformation of a coal bunker and propose effective preventative measures for such, a realtime monitoring system was designed Moreover, methods were proposed for monitoring the coal Multifactor dynamic analysis of the deformation of a coal bunker 2022年8月15日 Combined with the characteristics of the project and site conditions, in order to speed up the installation efficiency and improve the installation accuracy, the coal bunker space frame of the project adopts a combination of the overall jacking process, the strip and block top hanging process and the highaltitude bulk process for installation, and the construction is Case analysis of space frame installation technology for strip
R)8OC`6F[ZIB.jpg)
Ball Mill Maintenance Installation Procedure 911Metallurgist
2016年10月20日 On Mill Installation and Maintenance Before starting the erection of the mill, adequate handling facilities should be provided or made available, bearing in mind the weights and proportions of the various parts and subassemblies This information can be ascertained from the drawings and shipping papers2020年7月7日 The process of filling bunkers at PT PJB UBJ OM PLTU 1 east java Pacitan is very dependent on coal handling system In the existing system is still dependent on human resources as an operator, of Design of Coal Handling System for Filling Bungker using PID Method coal chain, with virtually all transport systems and most coal producers and consumers making use of stockpiles Stockpiling is carried out at coal mines, coal preparation plants, transhipment facilities (including export/import facilities) and end user sites such as power plants, coking plants and cement works With mounting pressure toManagement of coal stockpiles ICSC• Coal characteristics profoundly influence risk – Lower rank coals are generally more easily ignited inside the coal mill – High volatile matter and highly reactive coals encourage preignition inside the mill – Higher moisture content requires temperature extremes inside the millMill Inerting and Pulverizer/Mill Explosion Mitigation
.jpg)
(PDF) Operation and Maintenance of Coal Handling System in
2011年12月31日 Then, the safe operation of coal handling system and the proper method of the equipment maintenance are summed up Belt Conveyor Dual drums head actuations Fig3[1] Ball mill is an important part of the combustion system, and the coal pulverizing and treating process is shown in Fig 1 The coal falling into coal feeder from coal bunker is grinded up in ball mill coal pulverized system, and the hot air is generally used as a dry atmosphere The mixture of pulverized coal and air with dryCorrelation Analysis of Boiler Operation Parameters Based on Mill 2024年4月26日 The final stage in iron ore processing is ironmaking, where the iron ore is transformed into molten iron through a process called reduction The most common method of ironmaking is the blast furnace route In a blast Iron Ore Processing: From Extraction to ManufacturingFrom the coal yard, the coal is transfer to the mill bunkers through conveyor belt The bunkers are sized for an effective capacity of twelve (12) hours at BMCR with design coal Each mill bunker has one hopper, connected to the feeders Mills operate when the bunker coal gate valves are opened, coal is allowed to flow to the gravimetric feedersAnalysis of the Coal Milling Operations to the Boiler Parameters
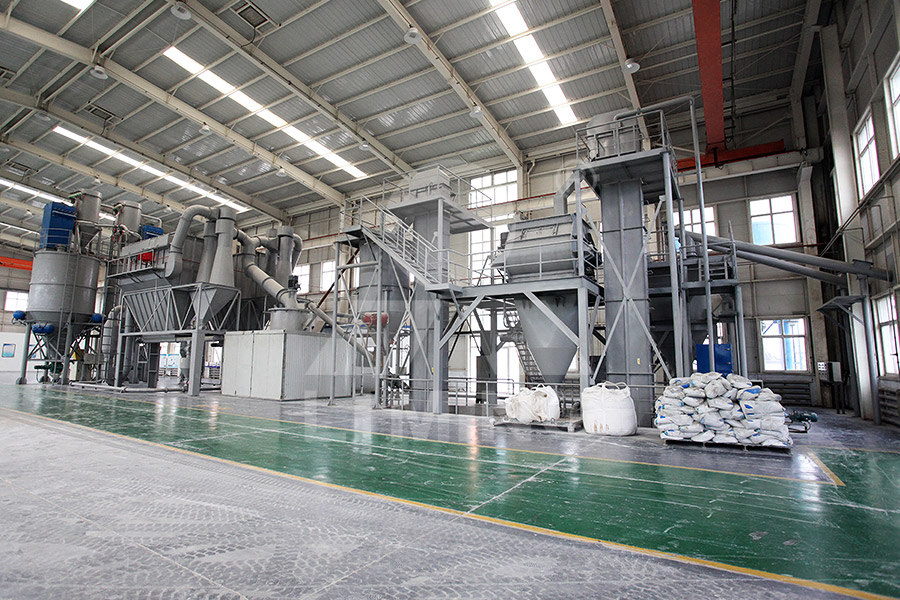
Bunker specification Installation instructions CapillaryFlow
At the lowest point of the bunker sub grade, a 2” x 2” wood frame at least 2 feet long and 2 feet must be placed prior to installing the Capillary Material, If the bunker floor is large and flat, several frames must be placed to ensure that any point of the bunker floor which is less than 6 inches above the lowest point is located no more than 6 feet away from a frame which will create the 2019年11月7日 Comprehensive treatment,we should have a test on the 300 MV unit steel ball coal mill pulverizing systemAt the same time,analyze the main operating parameters before modificationTransform the Optimization and transformation of 300MV units steel ball coal mill Dip: Angle of inclination of a deposit measured from the horizontal Strike: Horizontal bearing of a tabular deposit at its surface intersection Country Rock/Host Rock: Rocks lying in adjacent to the mineral depositIf such rock is lying under the deposit, it is termed as footwall If the rock is lying above the ore deposit, it is termed as hangingwallOverview of Underground Metalliferous Mining SpringerLinkAn introduction to the nature of coal J Groppo, in Coal Combustion Products (CCP's), 2017 14 Coal pulverizing In general, coal is transported and stored as fuel for use at as coarse a size as possible in order to minimize losses during handling and transport, moisture absorption, and spontaneous combustion, among other considerationsCoal Pulverizers an overview ScienceDirect Topics
.jpg)
coal feeders and coal mill Capabuild
Bowl mills are used for pulverizing coal in pulverized coal fired boilers The coal to the mill is fed by a coal feeder from the coal bunker There are many type of feeders used for coal feeding like the belt feeder which can be in volumetric or gravimetric mode, the chain link feeder, the drag feeder, etc Row coal from the yard is sized in crushers and stored in coal bunkersTerminal boxes on bunker top for terminating the reject conveying pipes Mill reject bunker(s) along with structure and manually operated bunker discharge gate at bunker outlet and bag filter, level sensors on the top of bunker Conveying air compressors with drive motor, local control panel and other accessoriesCoal Mill Rejects Handling Coal Mill Reject Handling SystemDenseveyor is installed below the Pyrite Hopper for conveying coal mill rejects to Rejects Bunker through independent material conveying pipeline On top of the Bunker, a bag filter is provided to vent out clean air Bunker is also equipped with a manually operated sector gate for discharge of rejects into the trucks MILL REJECTS HANDLING SYSTEM:Case Study – Coal Mill Rejects Handling System for PF BoilerWhen dealing with less hard ores, the 1925mm ore be ground to 610mm, the configuration of the rod mill and the sieve in a closed circuit is simple and the cost is low Besides, the dust removal in the crushing workshop can be simplifiedThe Working Principle and Advantages of the Rod Mill
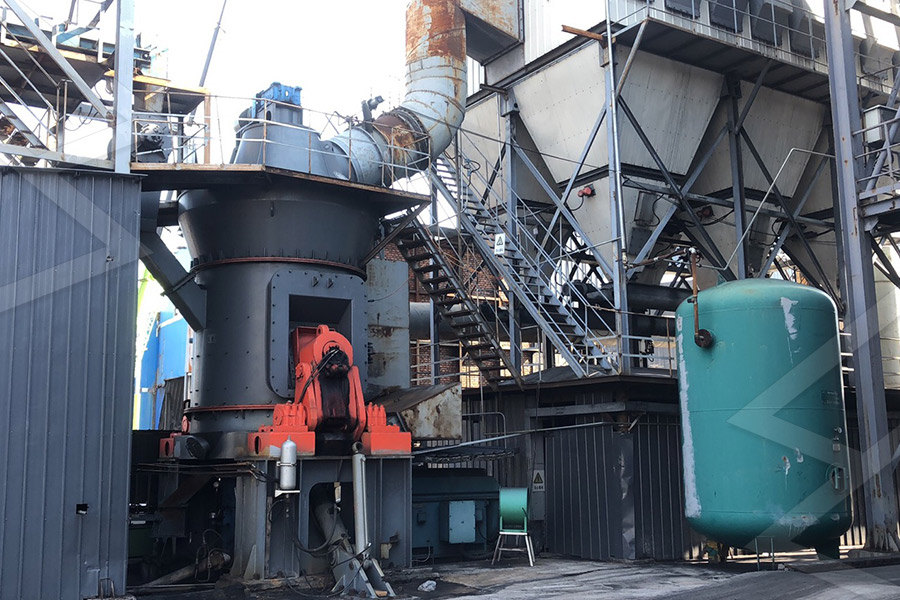
Precautions For Installing Coal Bunker Liner Board
2020年1月3日 2 When using coal bunker lining products, the number of bolts per square meter should not be less than 10; 3 The gap between the lining plates should not exceed 05cm The installation should be appropriately adjusted And in order to control the combustion correct amount of coal need to feed into the boiler to keep the process under control As you see in the diagram feeder lies between the bunker and the crusher or coal mill The coal is usually stored in Coal Feeder Instrumentation basicsVRM has been widely researched in processing of cement (Ito et al 1997;Jorgensen 2005;Wang et al 2009, Ghalandari et al 2021), coal (Tontu 2020), iron ore (Reichert et al 2015), zinc ore (van The layout of the coal mill with a rotary classifier6 Construction and Maintenance of Belt Conveyors for Coal and Bulk Material Handling Plants practicalmaintenance also oscillating horizontally This phenomenon results in internal agitation to the material on belt and therefore the material’s external faces assume inclination at surcharge angleConstruction and Maintenance of Belt Conveyors for Coal and
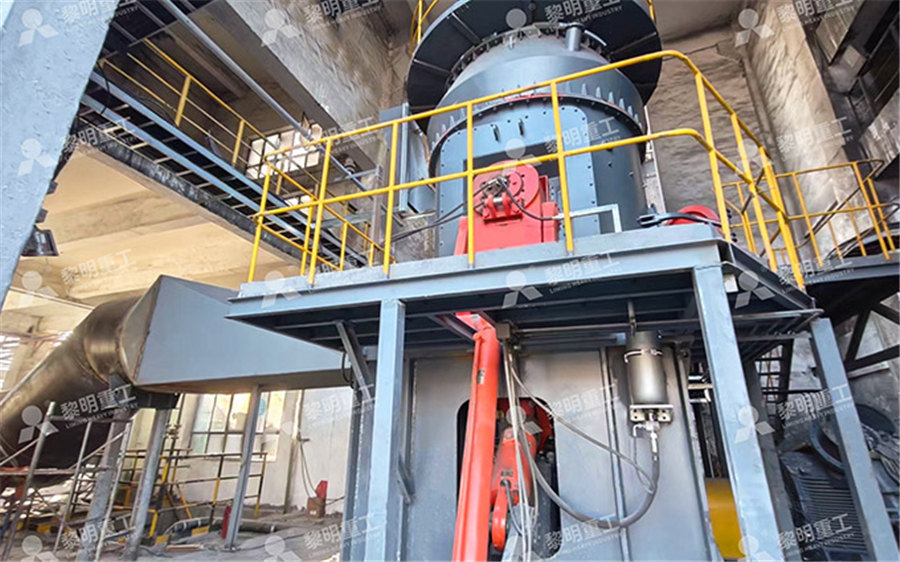
Structural Design of Bunkers with Procedure and Design Considerations
The main structural elements that constitutes a bunker are shown in figure2 They comprise of Vertical walls; Hopper Bottom; Edge Beam (At the top level) Supporting Columns; Fig2: Structural Elements of a bunker The design Procedure can be explained in following steps: Step 1: Design of Vertical Wallsof the coal level in the bunker was very week Our research studies have demonstrated that instead of developing an explicit recurrent dependency may use rescaling of the signals 2 Bull Pol Ac: Tech 69(1) 2021 The identification method of the coal mill motor power model Table 1 The description of the selected control signals and process The identification method of the coal mill motor power model 2022年5月1日 The measures for coal dust explosion comprise water spray, scrubber, canopy air curtain method for minimising coal dust generation; inertisation with stone dust, airodust, hygroscopic salt for prevention of coal dust ignition; water mist, fire retardants, inhibitors and extinguishing agent, closed vacuum chamber for suppression of coal dust generationReview of preventive and constructive measures for coal mine Download scientific diagram Airflue gas cycle of coalfired power plant from publication: An investigation of performance characteristics and energetic efficiency of vertical roller coal mill Airflue gas cycle of coalfired power plant ResearchGate
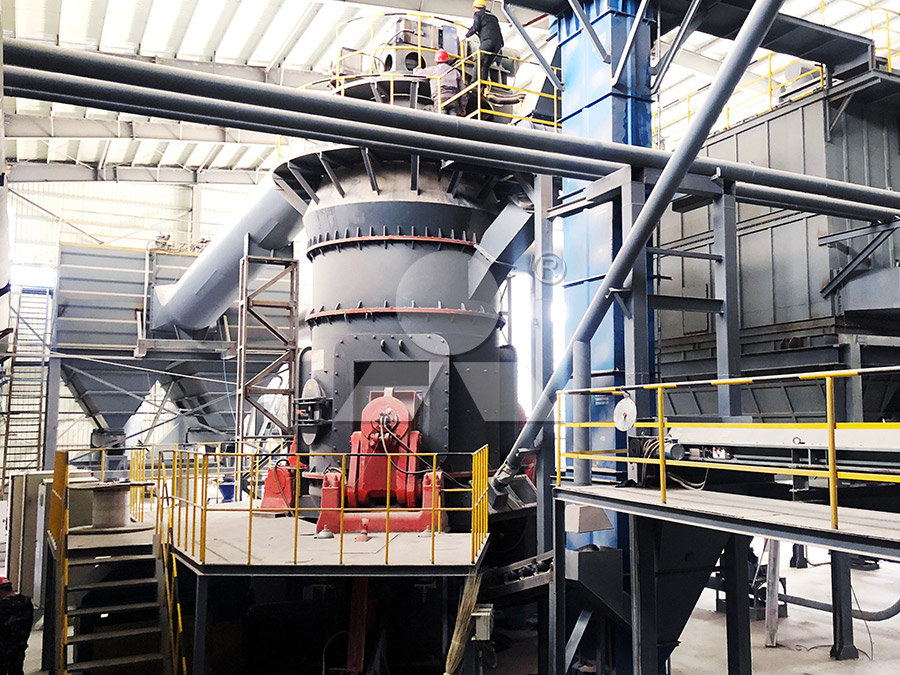
Fire and Explosion Prevention in Coal Pulverizing Systems
Explosions consistently occur when the coal air mixture is leaner than normal, either when initating coal feed on mill startup, stopping coal feed on shutdown, or when equip ment problems cause inadvertent loss of feed Upon loss of feed to a pulverizer, the coal/ air mixture in the system becomes leaner and the coal dust will