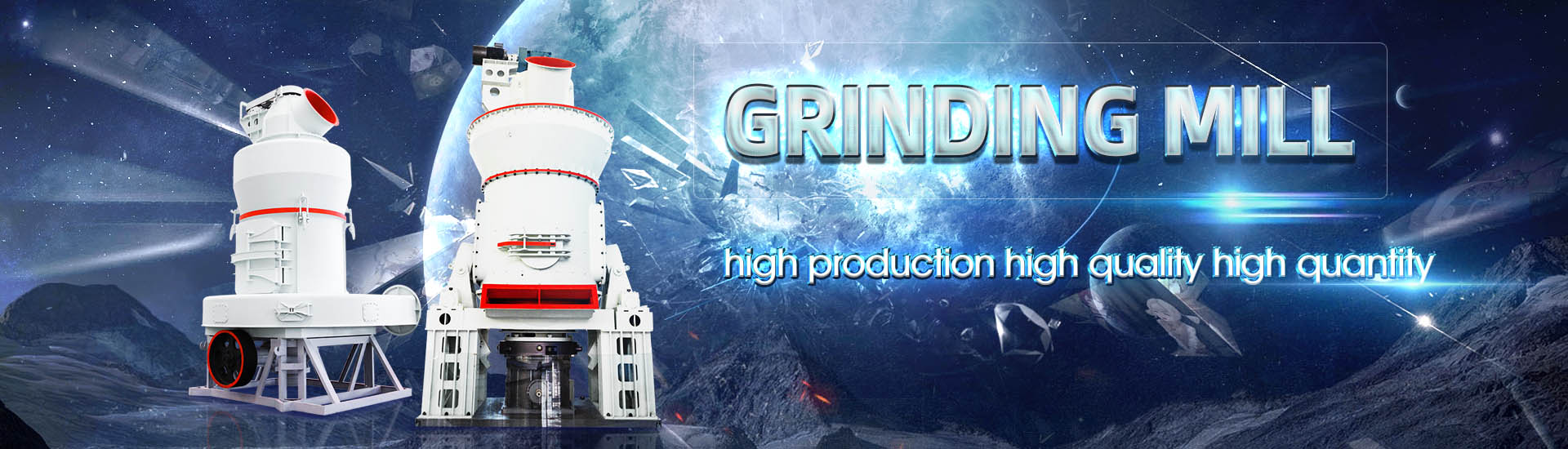
Highefficiency, highfine and antiblocking ore grinding machine
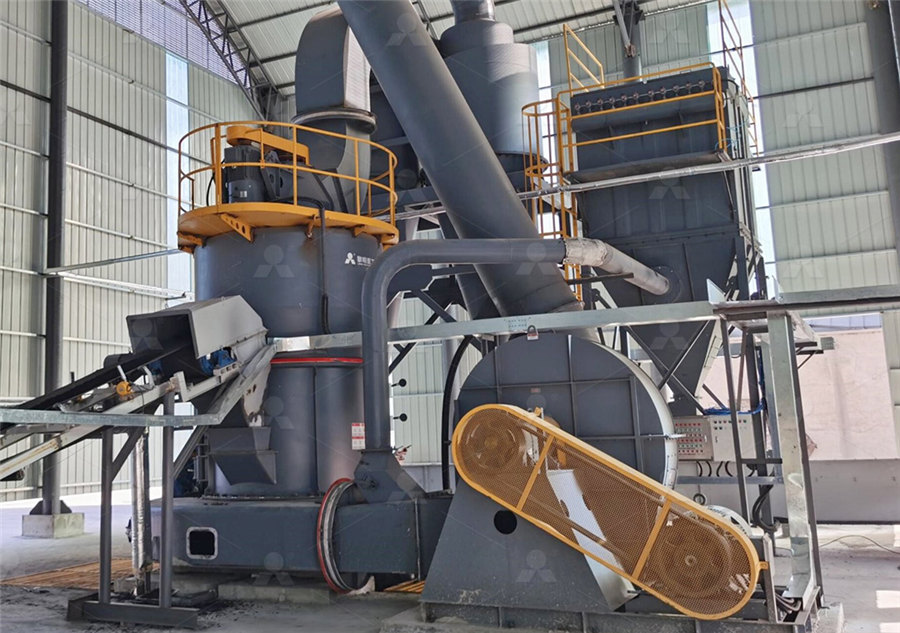
Investigating the benefits of replacing hydrocyclones with high
2020年3月15日 Lower bypass and sharper separation provided by highfrequency screens are the major factors affecting the capacity of the circuit and the results showed that 13% more throughput is achieved with 15% less grinding energy when hydrocyclones are replaced by The high precision, strong antiinterference capability, and high speed of these factors guarantee the separation efficiency of intelligent ore sorting equipment Color ore sorter, Xray ore A review of intelligent ore sorting technology and equipment • Very high intensity attrition grinding mechanism, suited to fines grinding • Small media size, essential to increase grinding efficiency for fines • The use of inert grinding media This can Fine Grinding as Enabling Technology – The IsaMillEnduron® high pressure grinding rolls (HPGR) can handle a wide variety of ores and particle sizes from fine pellet feed all the way up to coarse grinding of 75mm magnetite iron oreOur Dynamic HPGR Technology for Mineral Grinding
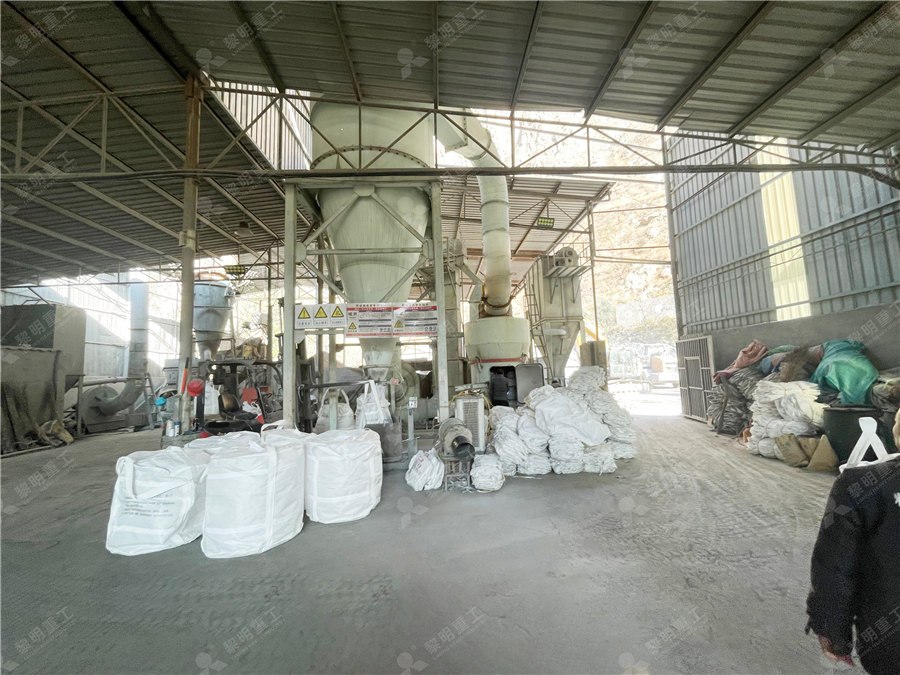
High Pressure Grinding Rolls for Minerals AusIMM
The characteristics of high pressure grinding rolls are : energy efficiency high and steady throughputs low space requirement, compact design lower capital operating costs than 2023年7月20日 According to the different grinding medium, the grinding mill is divided into three types: (1) ball mill – it is used widely, and almost all materials can be triturated by ball mill; (2) Ore Grinding SpringerLink2022年1月7日 As an efficient and environmentally friendly method, flotation is now widely used to separate and purify pyrite, chalcopyrite, sulfide ore, rare earth ore and other minerals The study on the effect of flotation purification on the The following article will demonstrate the importance of modern screening technology in the mining sector and show how processing plants can be simplified and improved when the Advances in screening technology in the mining sector
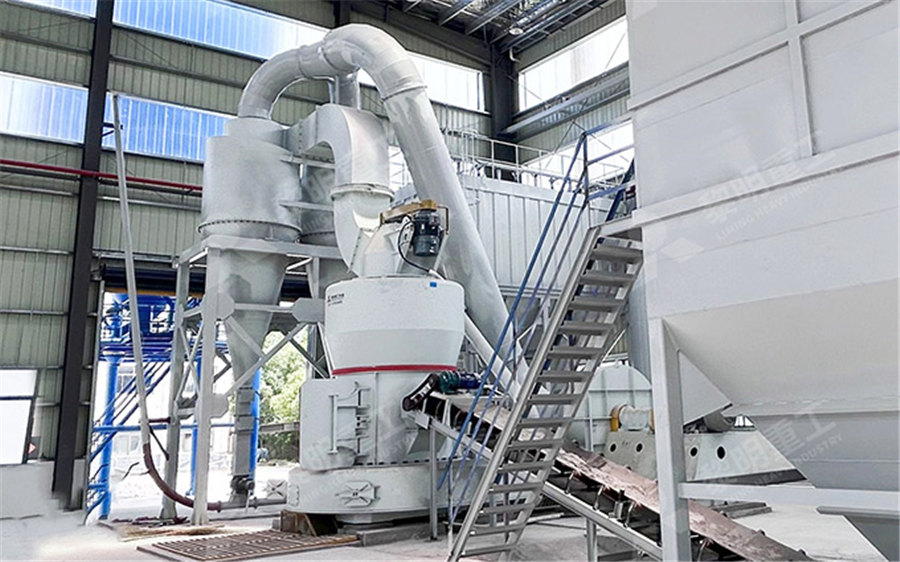
Ultra Fine Grinding A Practical Alternative to Oxidative Treatment
This paper details the operation of the ultra fine grinding process at KCGM as a non oxidative treatment for the extraction of gold from a refractory ores The refractory nature of gold ores is 2024年5月14日 Predictability, precision and speed: Robotics ensure consistent, optimal liner exchange so operators can maximise mill availability and grinding efficiency throughout the Higher performing liners + fast relining = higher throughput4 天之前 The screening efficiency of the fixed screen is low, it is easy to block when the viscous water content is high, and the labor intensity is high during operation However, because of its simple structure, easy manufacture, no power, and low Screening Machines Comparison JXSC Machinery2022年1月1日 A pilotscale grinding technology of ceramic medium stirred mill was proposed in this study Based on the specific productivity and grinding efficiency, the appropriate grinding parameters were ascertained as follows: material ball ratio of 07, ceramic ball medium size ratio (10 mm: 15 mm: 20 mm = 3:2:5), stirring speed of 110 rpm, grinding concentration of 50%, Highefficiency and energyconservation grinding technology using

Ultra Fine Grinding Mill SBM Ultrafine Powder
Brief Introduction HGM Ultra fine grinding mill (also called micro powder mill, superfine powder grinding mill, ultra fine powder grinder) is designed by SBM RD department on the basis of multiple innovations and testing It has been 2022年8月31日 Therefore, any research effort that has the potential to reduce energy consumption while maximizing grinding efficiency is of great importance This Special Issue welcomes papers that highlight innovations and future trends in modeling grinding and technological ways to improve the grinding efficiency in ore/raw material beneficiationGrinding Modeling and Energy Efficiency in Ore/Raw Material Grinding Machine Parts The parts of this machine are easily understood with the image shared below as a reference Though we will be discussing the various types of this grinding machines, there are certain common parts present in all types Let us learn more Fig 1: Grinding Machine Parts Base or Bed Cast iron makes up the base of the bedGrinding Machine: Learn its working, types, and applicationsThis high efficiency air classifier was developed for ultrafine, sharp separation, and is often used in conjunction with grinding plants The optimized classifier wheel geometry produces the finest cut points and high yields that have not been possible with production scale conventional air classifiers with only one classifier wheelCFS/HDS Highefficiency Fine Classifier Grinding Dispersing
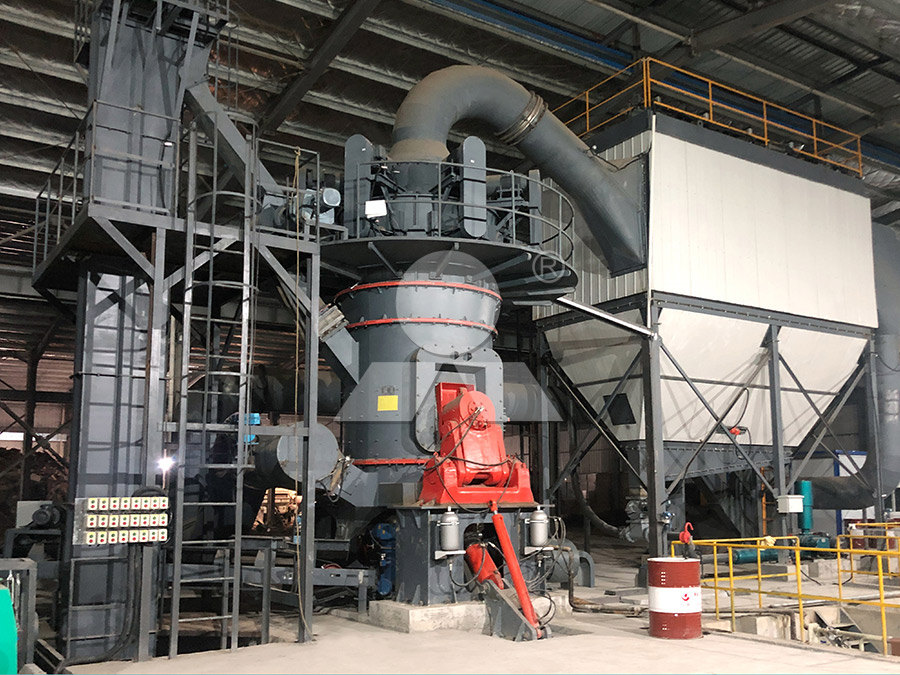
(PDF) A comprehensive review on the grinding process:
June 2022; ARCHIVE Proceedings of the Institution of Mechanical Engineers Part C Journal of Mechanical Engineering Science 19891996 (vols 203210) 236(2):年2月26日 Oxidised pellets have become an indispensable highquality charge for blast furnaces Nevertheless, highquality pellet feeds are becoming scarcer and scarcer To broaden the range of sources of pellet feeds and reduce the production cost of pellets, more steel mills are predicted to use coarse iron ore fines with a relatively low iron grade and low impurities for the Grinding of Australian and Brazilian Iron Ore Fines for Low What is ore washing: Mineral ore washing is the process of scrubbing the ore which is cemented or contains more mud with water or mechanical force, crushing the ore, washing the fine mud on the surface of the ore and separating it Sand, gold, platinum, tungsten, tin and other minerals such as lead, copper, iron and manganese which are deeply oxidized and weathered, usually Ore washing plant for sale, high efficiency ore washer LZZG2018年9月1日 After comminution and dry grinding of the eudialyte ore by a vertical roller mill, an eudialyte concentrate was recovered using WHIMS with a magnetic field intensity of 112 TStudy on the Characterisation and Processing of Iron Ore after Grinding
.jpg)
High Efficiency Precision Grinding of Microstructured SiC
2019年3月7日 Here, b s is set as 200 μm according to the average measurement value of conditioned diamond wheel with D213 μm abrasive size, θ is set as 353° in view of the abrasive grain shape [], C is the grain density on wheel surface and is 1093/mm 2 for D213 μm wheel based on the experimental measurement The calculated maximum undeformed chip 2021年11月1日 Semantic Scholar extracted view of "Highefficiency and energyconservation grinding technology Ceramic Grinding Kinetics of Fine Magnetite Ores in the Batch Ball Mill Chengfang Minerals 2023; Aiming to reveal the kinetic characteristics of ceramic ball grinding of fine magnetite comprehensively, two types of ceramic balls Highefficiency and energyconservation grinding technology investigated on a magnetic fluid support grinding machine by grinding Si 3 N 4 balls with fine diamond grinding wheels SD16000 of both bronze bond and cast iron bond in two types of grinding fluid: tap water and CG7 solution The experimental results showed that increasing the dressing current increased the grinding efficiencyHigh Efficiency Ultraprecision Grinding of Ceramic BallsSBM has focused on the field of ultrafine powder grinding for many years, CLUM vertical mills are suitable for largescale and highvolume nonmetallic ore grinding production lines and the single product qualification rate can reach 90% The grinding efficiency is high, the energy consumption is low, SBM Ore Ultrafine Grinding Mill

Grinding in Ball Mills: Modeling and Process Control
2012年6月1日 As the cylinder starts to rotate, the grinding balls inside the cylinder crush and grind the feed material, generating mechanical energy that aids in breaking bonds, activating the catalyst, and 1993年1月1日 High Efficiency Deep Grinding has been developed from a combination of high speed and creep feed grinding technique It can be characterised by its ability to achieve high stock removal rates and (PDF) High Efficiency Deep Grinding ResearchGate2015年1月1日 As grinding machines belong to the class of machines for the material removal with geometrically nondefined cutting edges, those machines can be classified in correlation to the classification of the different process technologies with geometrically nondefined cutting edges as it is given in DIN 8589, parts 11, 12, and 13 (DIN 858911 2003; DIN 858912 2003; Grinding Machines SpringerLink2013年1月1日 The efficiency of grinding and flotation process in coppermolybdenum processing circuit, largely affected by performance of thickeners and hydrocyclones devices(PDF) THE BENEFITS OF HIGH CLASSIFICATION EFFICIENCY IN CLOSED BALL
.jpg)
Optimization of grinding process for hard and brittle materials
2024年3月1日 The main influencing factors for grinding damage include abrasive grit size, grinding depth, workpiece feed speed, and wheel speed According to the research of Sabia et al [13], the grinding subsurface damage depth (SSD) of glass ceramics is proportional to 5 times the average abrasive grit sizeMa et al [14] found that the SSD of fused silica is 4–6 times the 2015年11月7日 The recently emerged High Efficiency Deep Grinding Temperature measurement in High Efficiency Deep Grinding, International journal of machine tools and manufacture, 45, 11, 12311245, 2005 Article Google Scholar Download references Author information Authors and Affiliations AMTReL, The High Efficiency Deep Grinding, an Application with conventional wheels2019年6月20日 Most dry iron ore grinding installations utilizing the standard type rod or ball mill are grinding highgrade natural ores that do not require beneficiation Most of these ores occur in the weathered state which results in Fine Dry Grinding of Iron Ore for PelletizingAutonomous grinding algorithms with future prospect towards SMART manufacturing: A comparative survey Md Riaz Pervez, Paolo Dario, in Journal of Manufacturing Systems, 2022 21 Grinding operation Grinding is a metal removal process with the help of bonded, coated or free abrasive grain tools Apart from all other machining operations, the ‘Grinding’ is the last Fine Grinding an overview ScienceDirect Topics
.jpg)
Study on the model of high efficiency and low carbon for grinding
2016年11月20日 Therefore, experts and scholars have done a lot of researches on the carbon emissions during manufacturing Jeswiet and Kara (2008) has introduced a simple way of finding the carbon emitted for a part by using Carbon Emission Signature (CES™), and developed a method connecting the electrical energy consumed in manufacturing directly to the carbon 2017年1月1日 This imposes strong requirements on grindingmachine technology and on the understanding of this finalising process While grinding has unique capabilities it is nevertheless in competition with other machining processes The evolution of grinding machines is driven by process requirements like accuracy, MRR, and subsurface integrityRecent developments in grinding machines ScienceDirect2016年7月14日 Thus, some of the finish grinding work is handled by the highpressure grinding roll The throughput of the existing grinding system can be increased by 50 to 70%, while power consumption can be cut by 20 to 30% Additional options for highpressure grinding roll use in gold ore comminution circuits are illustrated in Figure 11HPGR 911MetallurgistUltra Fine Grinding UFG mills overcome these limitations by the use of rotating stirrers inside a stationary mill shell Ultra fine grinding mills have been in use for many years in a large number of every day applications such as pharmaceuticals, dyes, clays, paint and pigments before being used in the mineral processing industryUltra Fine Grinding A Practical Alternative to Oxidative
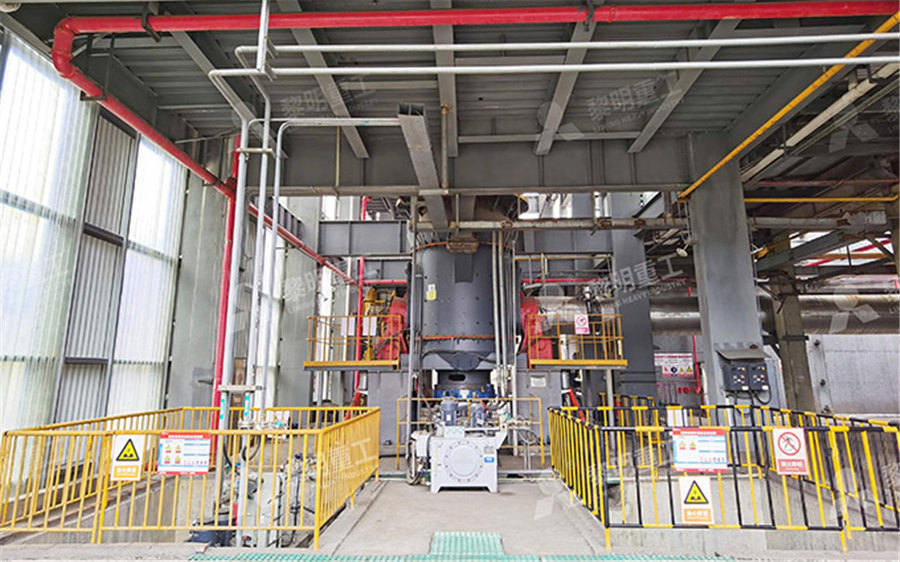
Energy Use of Fine Grinding in Mineral Processing
2013年12月18日 Fine grinding, to P80 sizes as low as 7 μm, is becoming increasingly important as mines treat ores with smaller liberation sizes This grinding is typically done using stirred mills such as the Isamill or Stirred Media Detritor While fine grinding consumes less energy than primary grinding, it can still account for a substantial part of a mill’s energy budget Overall 2016年2月29日 Cyanide acts too slowly on coarse gold, but readily dissolves fine gold Flotation concentration is not effective on coarse gold The small miners who wish to treat a small tonnage of high grade ore and want a quick return rather than for recoveries near to 100%, probably still find the amalgamation process the best available recovery methodGold Extraction Recovery Processes 911Metallurgist2020年6月21日 In the past century, many research studies have investigated the stressing conditions in stirred media mills Researchers developed a broader and better understanding of breakage mechanisms and breakage energy used in stirred media mills [3,4,5,6]Since the process optimization is a timeconsuming process due to several experiments that have to be Dynamic Process Models for Fine Grinding and Dispersing2008年4月1日 Download Citation High efficiency ball mill grinding The test material studied here is a gold ore ground in a closed ball mill circuit with hydrocyclone classificationHigh efficiency ball mill grinding ResearchGate
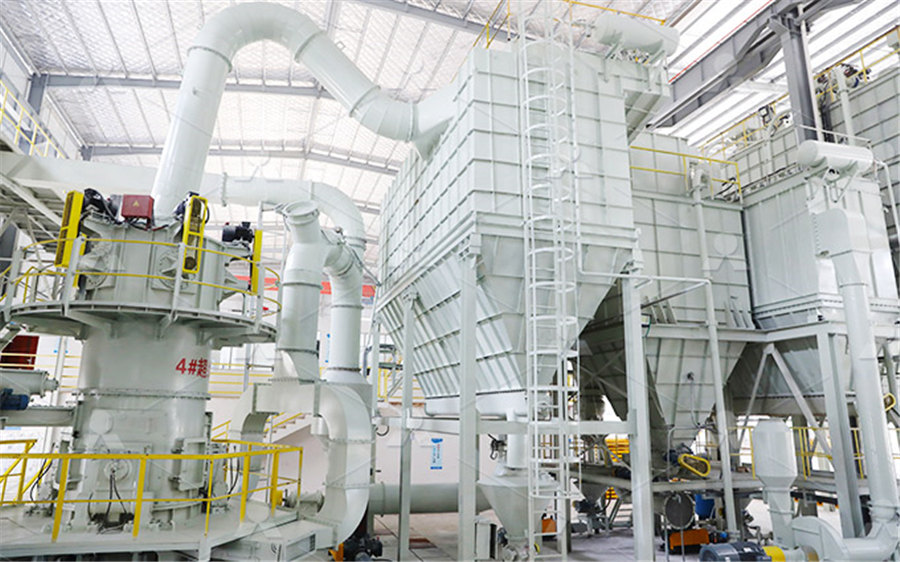
Analysis of process of grinding efficiency in ball and rod mills
2018年9月26日 Moreover, the corrosion test showed an enhancement of corrosion resistance with increased subzero treatment time as grinding devices [2]One of the most popular milling machines is the cement High Pressure Grinding Rolls have been used for the grinding of diamond and iron ores since about 1988 There are now about 40 machines operating worldwide in these industries This number is still small in comparison to the > 450 machines employed in High Pressure Grinding Rolls for Minerals AusIMMEnduron® high pressure grinding rolls (HPGR) can handle a wide variety of ores and particle sizes from fine pellet feed all the way up to coarse grinding of 75mm magnetite iron ore When it comes to feed material characteristics, the Our Dynamic HPGR Technology for Mineral Grinding2024年5月15日 Complexcurved parts made of superalloy, advanced ceramics, and other difficulttomachine materials are frequently used in the aerospace field The harsh environmental conditions place very high demands on their surface quality Precision machining of the complexshaped parts is facing great challenge Furthermore, it is impossible to accurately control the A highshear and lowpressure intelligent precision grinding
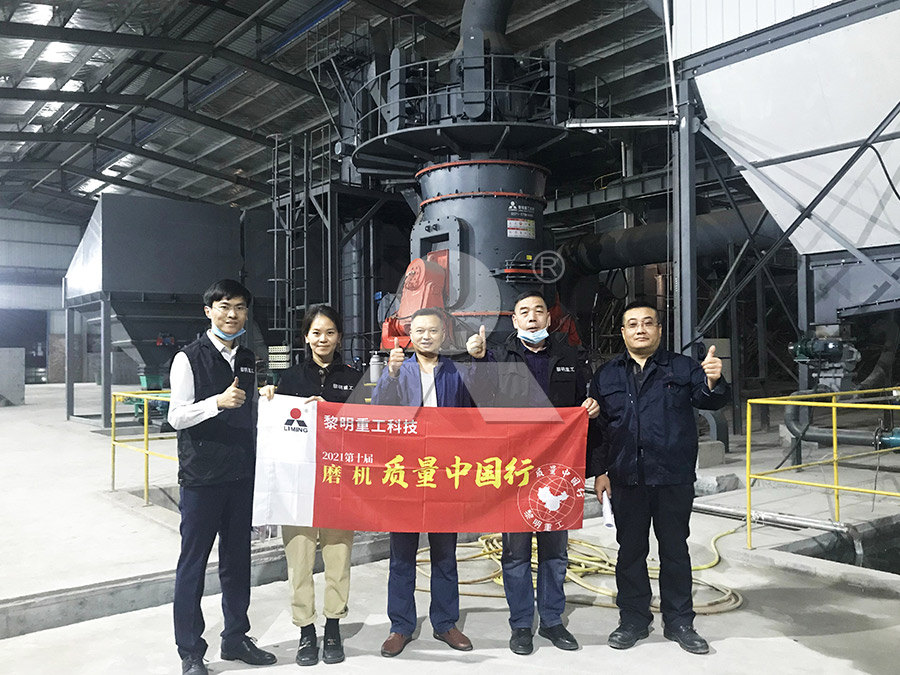
Ultraprecision grinding and polishing processing technology
2023年4月25日 Under the opportunity of 'Made in China 2025', in the field of ultraprecision, China has broken through many key bottleneck technologies, achieved many remarkable scientific research results, built a number of highlevel ultraprecision processing technology innovation platforms, talent growth platforms and application demonstration bases, and 2012年12月28日 A comparative study was carried out to investigate the effect of highpressure grinding rolls (HPGR) comminution on agitation leaching of gold ore in comparison with the conventional jaw crusher Optimizing the performance of highpressure grinding roll based ore 2022年3月16日 21 Experimental Design The experimental planning with selected key factor like operating gap (X 1), applied load (X 2) and roll speed (X 3) was designed by CCD method to obtain the optimum conditions for grinding the BHQ iron ore in HPGRA full secondorder polynomial model was obtained by regression analysis for three factors by using the Design Potential of HighPressure Grinding Roll (HPGR) for Size 2020年6月29日 Grinding, or abrasive machining, once performed on conventional milling machines, lathes and shapers, are now performed on various types of grinding machines Grinding machines have advanced in design, construction, rigidity and application far more in the last decade than any other standard machine tool in the manufacturing industry Grinding Chapter 17: Grinding Methods and Machines American Machinist
.jpg)
Vertical Grinding Machine・Horizontal Grinding Machine Engis
The horizontal grinding machine EHG series is equipped with a soft touch panel, enabling highprecision grinding with simple operation Closedloop control is performed by combining a grinding wheel axis equipped with a highprecision spindle, a work axis and an oscillating motion with an optical linear scale to achieve higher feed accuracy and sizing accuracy