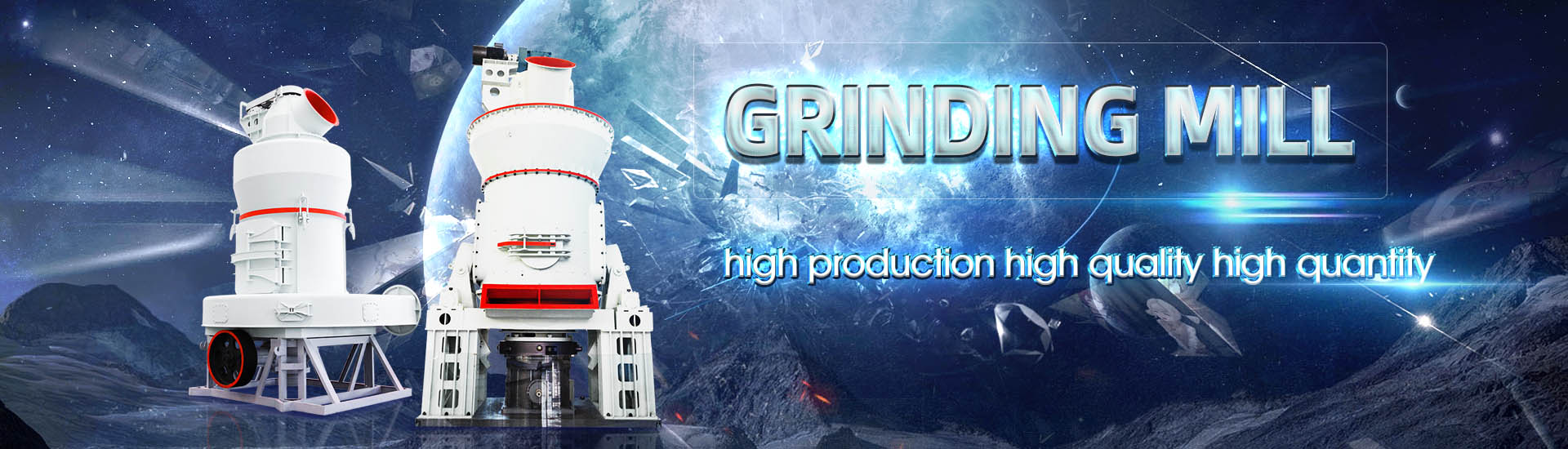
Introduction to anthracite lignite grinding mill
.jpg)
Reprint from ZKG 3 Gebr Pfeiffer
Depending on this high feed moisture the mill rating is determined by the drying process whereas for anthracite, hard coal and petcoke the rating of the mill is determined by the grinding processVertical roller mills are not only used for grinding cement raw materials but also find an application in grinding a wide variety of coal types in cement and power plants Gebr Pfeiffer SE (GPSE) COAL GRINDING IMPS: more than meets the eye Gebr Pfeiffer2014年1月1日 Two mill systems are employed for most coal grinding applications in the cement industry These are, on the one hand, vertical roller mills (VRM) that have achieved a share of almost 90% and,(PDF) MPS mills for coal grinding ResearchGateIndividual grinding mill design with a proven track record, encompassing 2, 3 and 4 rollers for fuel throughput rates up to and in excess of 200 t/h Pressure shock resistance up to 35 bar LOESCHEMILLS

Grinding Mill an overview ScienceDirect Topics
Grinding can be achieved by several mechanisms, including: impact or compression due to sudden forces applied almost normally to the particle surface; chipping or attrition due to The MPS mill also grinds, dries, calcines, and classifies gypsum without any problem, all in a single machine, for any fineness requested and considering individual requirements The MPS Coal mill, gypsum mill, clay mill, etc Pfeiffer MPS mills2022年12月1日 Introduction Coal grinding mills are part of thermal power plants and are used to prepare solid fuel in the form of peat, lignite, hard coal and anthracite for combustion [1], [2], The wear mechanism of mill beaters for coal grinding madeup 2020年3月15日 This paper focuses on the energysize reduction and energy split factor of components during the heterogeneous grinding of anthracite and coking coal in a Hardgrove Energysize reduction of mixtures of anthracite and coking coal in
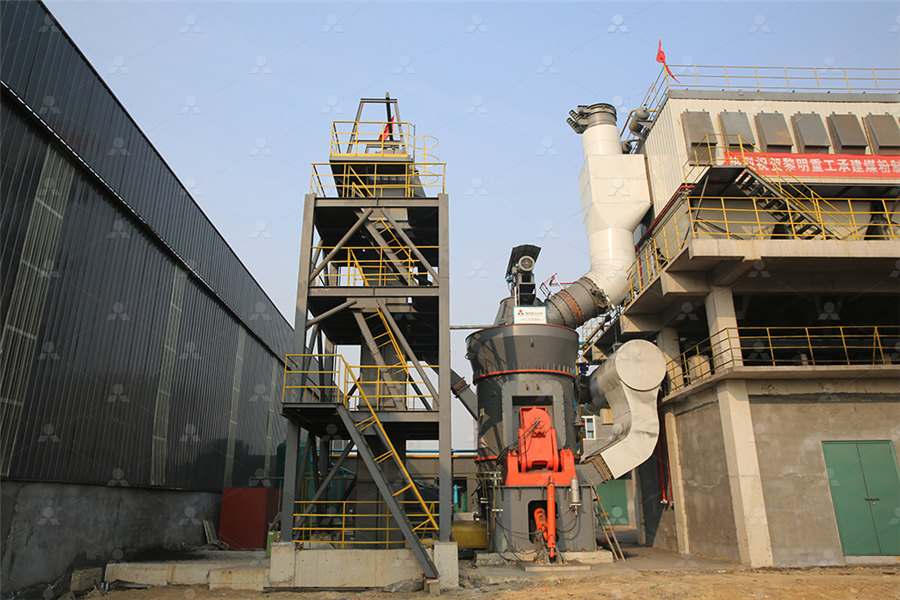
Vertical mill for coal pulverizing in power plant
It could be used to grind bituminite, meagre coal, and anthracite lignite with high moisture under some conditions Vertical mill adopts low speed, big roller diameter, high loading force design It has the widest adaptability to coal types 2022年7月4日 Milling Machine Definition: The milling machine is a type of machine which removes the material from the workpiece by feeding the work past a rotating multipoint cutterThe metal removal rate is higher very high as the Milling Machine: Definition, Parts, Operation, 1 Introduction Update on lignite firing 5 Coal plays a significant role in meeting global energy demand Coal is the world’s most abundant fossil fuel and coal deposits exist in nearly every region of the worldUpdate on lignite firing2020年3月15日 This paper selects anthracite coal and coking coal as experimental materials to conduct heterogeneous grinding in the Hardgrove mill Energy consumption and product t 10 of single coal and mixtures at various grinding time are measured, and effects of mixed ratio on energysize reduction process are discussed T 10 values of component after the mixture Energysize reduction of mixtures of anthracite and coking
.jpg)
The Effects of BallMill Grinding Parameters on Lignite Morphology
2023年9月9日 The average roughness (Ra) values of particles increased from 609 nm to 1079 nm upon increasing the grinding time from 2 min to 16 min Due to these findings, it can be suggested that lignite This document discusses beater wheel mills used in lignitefired boilers It includes: 1 An overview of beater wheel mills, including their components, typical sizes and capacities, and the comminution process within the mill 2 Diagrams of beater wheel mills with different configurations, such as with or without a separating classifier or with a precrusher 3 Photos of Beater Wheel Mill PDF Lignite Mill (Grinding)Cement production involves quarrying limestone and clay, grinding and blending the materials, burning them at high temperatures to form clinker, and finely grinding the clinker to produce cement powder The key steps are: 1) Quarrying limestone and clay and grinding them to powder; 2) Blending the powders in precise proportions; 3) Burning the blend at high heat to form Chapter 1 Introduction To Cement Production PDF Mill (Grinding 2023年1月1日 Generally, a value of 55 represents an average grinding coal When switching to lower HGI coal, the capacity of the coal mill system should be assessed A key element in understanding a mill’s ability to handle lower HGI coals is Coal utilization in the cement and concrete industries
.jpg)
An investigation of performance characteristics and energetic
2020年8月12日 As one of the three major forces of coal mills, the grinding force exerts a significant impact on the working process of coal mills and parameters like mill current and outlet temperatureThe slow speed and medium speed mills are selected for coals ranging from subbituminous to anthracite The highspeed mills are used mainly for lignite Operation Of Bowl Mill Pulveriser In bowl mill pulveriser raw coal coming from feeder gets ground between the grinding rolls and bull ring segments installed on the revolving BowlPulveriser in Thermal Power Plant Bowl Mill Ball Mill2024年8月8日 Introduction In the intricate dance of ball milling, where raw materials are transformed into finely milled particles, the choice of grinding media emerges as a pivotal performance lever This seemingly minor selection can Ball Mill Success: A StepbyStep Guide to Choosing Anthracite – Wikipedia, the free encyclopedia and appearance, like bituminous coal and often anthracite as well, as opposed to lignite peat 1; lignite; subbituminous coal; bituminous coal; anthracite; » Free Online Chat What is the difference in peat bituminous lignite and anthracite Peat lignite and anthracite are forms of what?distinction between peat, lignite, bituminous and anthracite coal
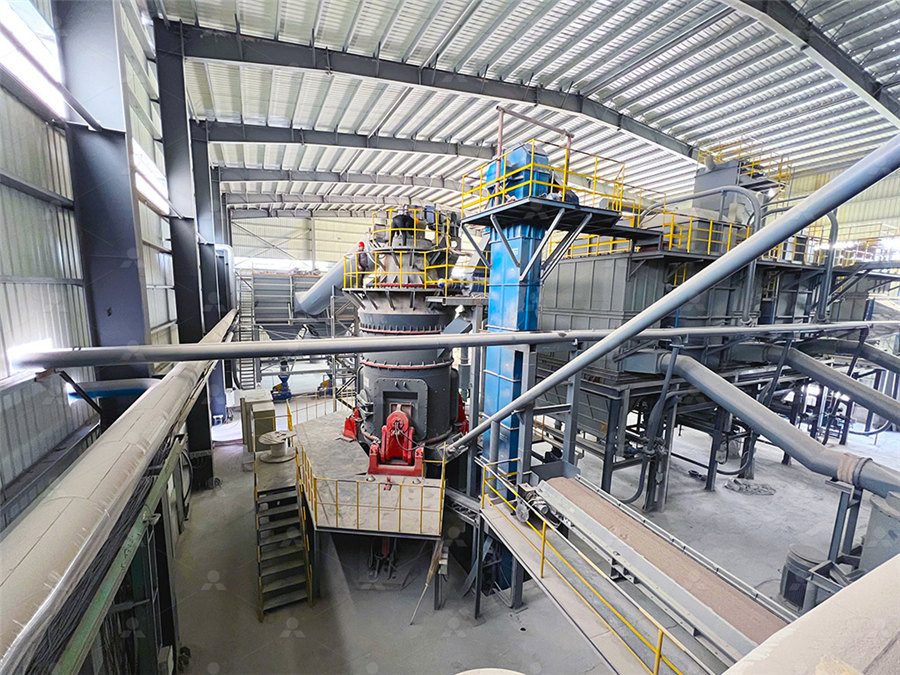
An introduction to the nature of coal ScienceDirect
2017年1月1日 Several different systems are used to classify peat, using characteristics such as geology, botanical content, or physiochemical properties (Fuchsman, 1980, Boron et al, 1987)Table 11 shows an increase in carbon content and a decrease in oxygen content as the level of humification increases As decomposition proceeds, readily degraded components, 2012年6月1日 As the cylinder starts to rotate, the grinding balls inside the cylinder crush and grind the feed material, generating mechanical energy that aids in breaking bonds, activating the catalyst, and Grinding in Ball Mills: Modeling and Process ControlThe European mill is designed and developed absorbing newest grinding technologies and ideas and has a number of independent intellectual property rights The mill adopts bevel gear integral transmission, inside thin oil lubrication system and curve air duct which has advanced technical level and advantages of small occupation area, low consumption, high yield, good appearance MTW European grinding mill – toreksminingmachineryas centre of excellence for coal and biomass mill application in the power utility industry 2002 Coal grinding plant (LM 232 D) for grinding wood pellets for power stations 1992 Central coal grinding plant (LM 263 D) for the production of lignite (brown) coal dust 1985 Delivery of first selfinerting coal grinding plantLoesche Grinding Technology for the Power Industry
.jpg)
Adding Metal Nitrates to Intensify Lignite and Anthracite
2023年8月27日 The influence of metal nitrates—KNO3, NaNO3, and Ca(NO3)2—as activating additives on the oxidation and combustion of lignite and anthracite is investigated The additives (5 wt %) are introduced in the samples by impregnation, according to the moisture capacity By thermal analysis and highspeed video recording of combustion, it is established that the This makes them suitable for processes such as wet grinding, dry grinding, and solventbased reactions 3 Factors to Consider when Selecting a Ball Mill: When choosing a ball mill, several factors should be taken into account to ensure optimal performance and efficiency:Introduction to ball mills: Versatile tools for grinding and mixing2015年4月9日 Grinding Mills and Their Types satyendra; April 9, 2015; 12 Comments ; autogenous grinding, ball mill, grinding mills, hammer mill, rod mill, roller mill, SAG,; Grinding Mills and Their Types In various fields of the process industry, reduction of size of different materials is a basic unit operationGrinding Mills and Their Types – IspatGuruIntroduction This project is mainly equipped with MTW175 European grinding mill and other ancillary equipment The processing material is lignite for humic acid use The material enters the MTW175 for grinding through the regulated silo, anLignite Processing SiteLIMING HEAVY INDUSTRY CO, LTD
.jpg)
An investigation of performance characteristics and energetic
The mill combines crushing, grinding, classification and if necessary drying operations in one unit and enables to decrease the number of equipment needed in grinding circuits (Altun et al 2017)2023年1月16日 The objective of this research is to design and construct a hammer mill for grinding leonardite charcoal (Lignite, class J) The conditions for the design and construction of the grinder are Optimum Design of Hammer Mill for Grinding LeonarditeIntroduction to unit operations and processes 2 Dimensional analysis and similarity 3 In the mill the grinding chamber is an oval loop of pipe 25 to 200 mm in diameter and 12 to 24 m high Feed enters through a venturi injector Size Reduction1: Grinding – Unit Operations in Food 2 Introduction to Mineral Processing Free download as Powerpoint Presentation (ppt / pptx), PDF File (pdf), Text File (txt) or view presentation slides online The document provides an overview of mineral processing techniques used to extract valuable minerals from ore It discusses various comminution methods like crushing and grinding to reduce the particle size 2 Introduction To Mineral Processing PDF Mill (Grinding
.jpg)
(PDF) Grinding Media in Ball MillsA Review ResearchGate
2023年4月23日 Introduction According to data analysis by NapierMunn [1] High mill filling reduces the grinding rate because the collision zone would be saturated Deniz [71] 2023年9月9日 The average roughness (Ra) values of particles increased from 609 nm to 1079 nm upon increasing the grinding time from 2 min to 16 min Due to these findings, it can be suggested that lignite samples became rounder with increasing grinding times, and roughness analyses made in a 10 × 10 μm surface area with an Atomic Force Microscope (AFM) The Effects of BallMill Grinding Parameters on Lignite 2002年6月1日 The kinetics of batch dry and wet grindings of calcite, barite, quartz, lignite and anthracite from feeds of sieve size 425+300 μm has been determined using a laboratory scale ceramic ball millKinetics of wet versus dry grinding of lignite by a porcelain millCOAL MILLppt Free download as Powerpoint Presentation (ppt), PDF File (pdf), Text File (txt) or view presentation slides online The document discusses coal mill equipment, including the names, functions, and working principles of different types of equipment It focuses on vertical roller mills (VRM), describing the three main sections of VRM separation, drying, and grindingCoal Mill PDF Coal Lignite
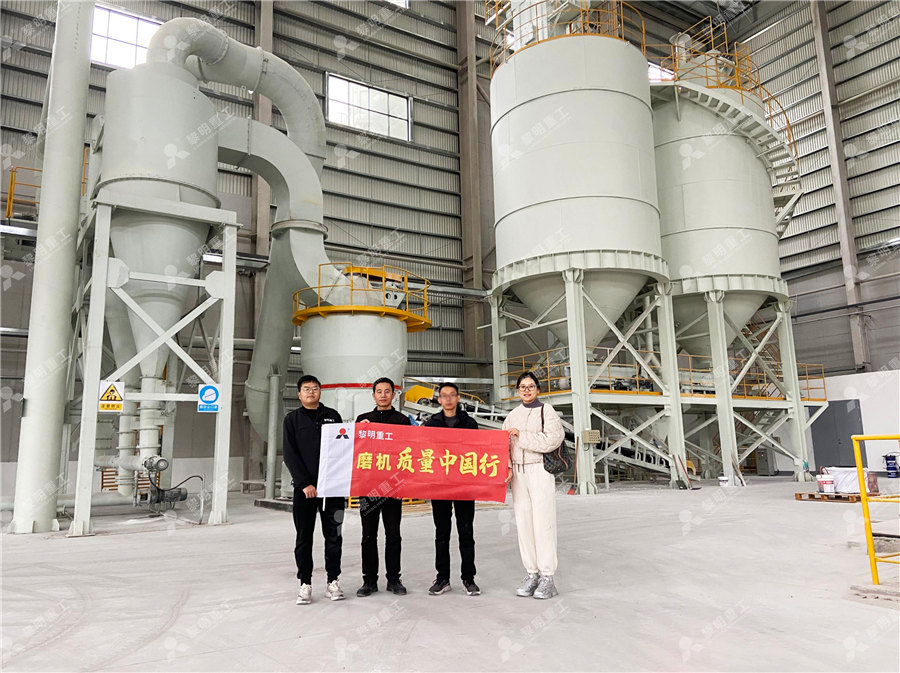
Practical 1 : Ball Milling TF Lab 1
2013年12月23日 Practical 1: Title: Ball Milling Objective: To grind the coarse salt to a smaller size by using a ball mill and to obtain the particle size distribution of the initial and the sieved final mixture Introduction: 'Ball milling is a method used to break down the solids to smaller sizes or into a powder A2013年5月15日 The objective of this study was to analyze dry grinding kinetics of three different solid fuels in terms of selection and breakage distribution functions values using a batch laboratory ball parisons of Dry Grinding Kinetics of Lignite, Bituminous 2017年10月26日 The following are factors that have been investigated and applied in conventional ball milling in order to maximize grinding efficiency: a) Mill Geometry and Speed – Bond (1954) observed grinding efficiency to be a Factors Affecting Ball Mill Grinding Efficiency2023年8月2日 The milling process has evolved over time, employing various techniques to produce flour with different particle sizes and applications This paper discusses the advancements in the wheat flour The Latest Innovations in Wheat Flour Milling: A Review
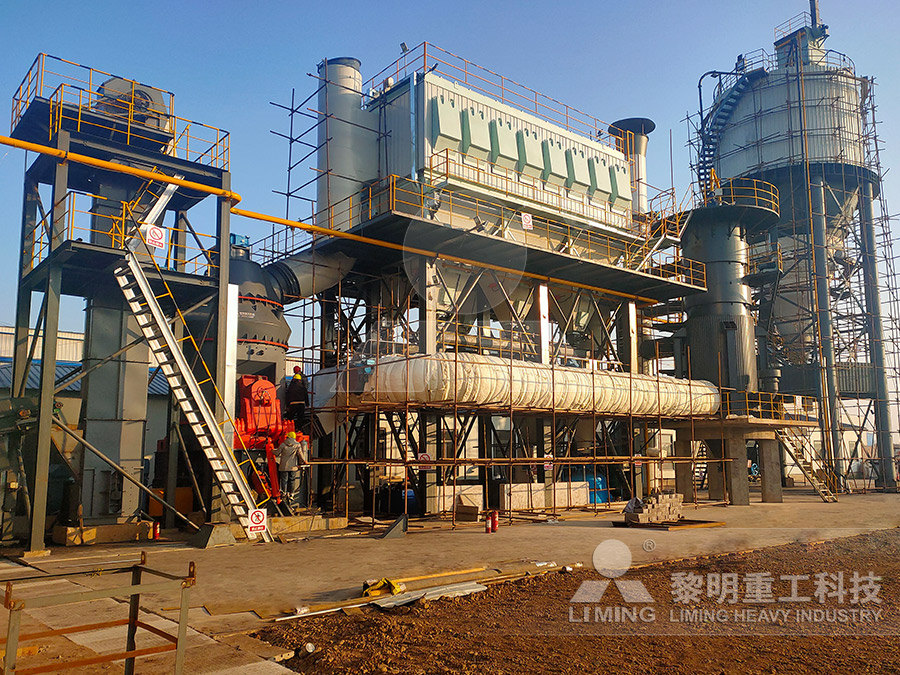
Effect of the grinding behaviour of coal blends on coal utilisation
Ball Mill The coal sample was dry ground in a 305x305 mm laboratory ball mill Total weight of steel ball charge was 316 kg, which occupy 50% of the mill volume and comprising three ball sizes: 38 cm diameter (248 kg), 51 cm diameter (61 kg) and 09 cm diameter (07 kg) The material was ground for 10 minutes and then sieved on a 212 μm A crushing plant delivered ore to a wet grinding mill for further size reduction The size of crushed ore (F 80) was 40 mm and the SG 28 t/m 3 The work index of the ore was determined as 122 kWh/t A wet ball mill 1 m × 1 m was chosen to grind the ore down to 200 micronsGrinding Mill an overview ScienceDirect Topics2011年2月1日 1 Introduction Grinding is one of the most widely used unit operations but the most inefficient process Most studies on grinding aim to determine the relation between energy and size reduction and the possibility to consume the least amount of energy to achieve the most convenient size [1]It has been reported that in the US, 15% of all electricity generated is used A comparison of the results obtained from grinding in a stirred When grinding two surfaces that are perpendicular to each other, the side of the wheel may be engaged at the same time as the face This may be done to produce features such as a shoulder, slot, or groove 1122 Abrasive Grinding wheels: left is fine, center is medium, right is extra fineChapter 11: Surface Grinders – Introduction to Machining
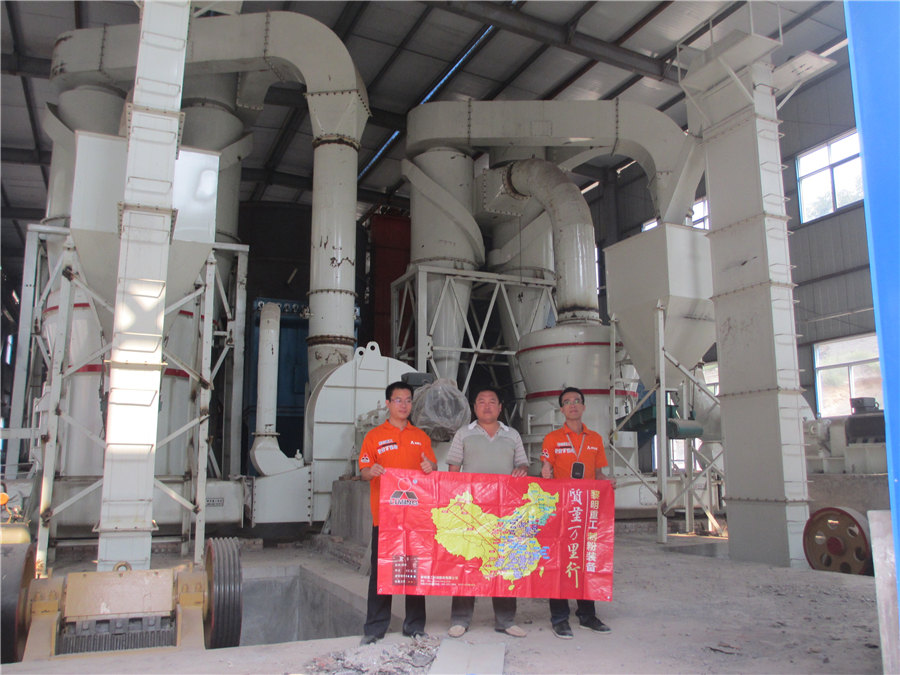
Ball Mill Ball Mill Machine AGICO
Ball mill can be divided into dry type and wet type; According to different mine discharge types, it can be divided into lattice type and overflow type; According to the shape of cylinder, it can be classified into short tube ball mill, long tube ball mill, tube mill and cone mill; Other types are rod ball mill, cement ball mill, ultrafine laminating mill, hand ball mill, horizontal ball mill – For lignite 35% looks possible to operate with 3 mills in service through air supply and mill adjustments and additional means LEFT Vattenfall’s lignitefired Schwarze Pumpe plant, where firing down to 37% has been demonstrated Firing systems – lignite RIGHT RWE’s WTA lignite drying plant at Niederaussem – Studies show lignite Increasing the flexibility of coalfired power plants ICSCCoal and Ash R Keith Mobley, in Plant Engineer's Handbook, 2001 Lignite Lignites are brown and have a laminar structure in which the remnants of woody fibers may be quite apparent The word lignite comes from the Latin word lignum meaning wood Their origin is mostly from plants rich in resin, so they are high in volatile matter Freshly mined, lignite is tough, although not Lignite an overview ScienceDirect TopicsCoal Mill Safety Pte Ltd introduction(11) The following is an analysis after many years of work in the cement industry and with technology suppliers, in which the typical faults in the engineering of coal/petcoke/lignite grinding systems have been observedAccept the probability that the fire and explosion safety of your