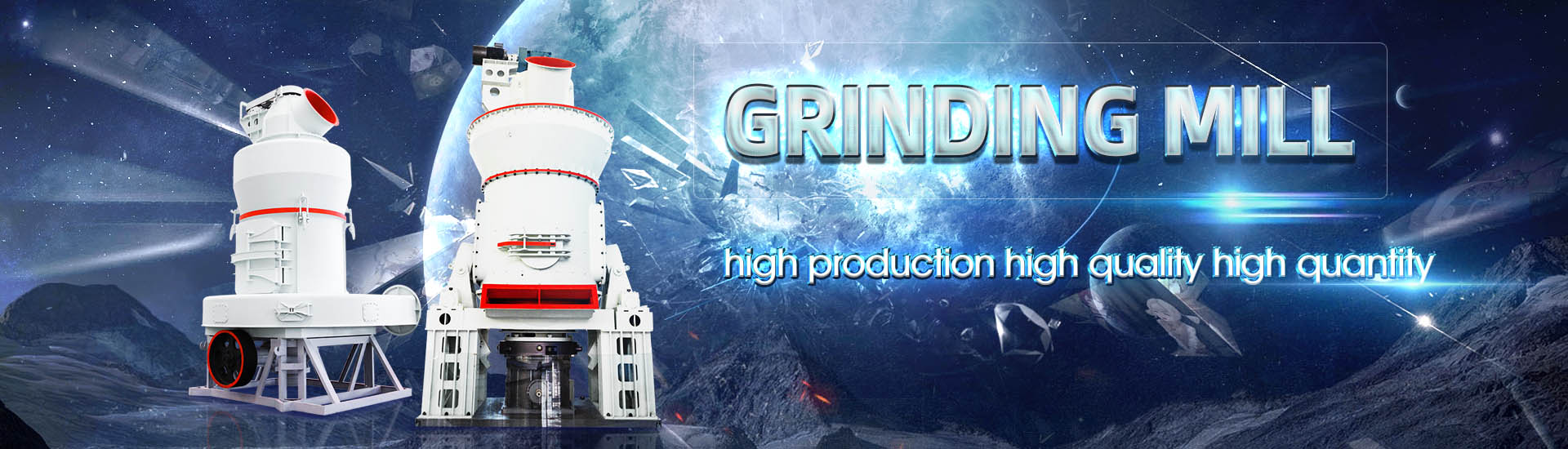
Electrolytic Aluminum Waste Slag Mill Ore Mill Sample
.jpg)
Research Progress of Electrolytic Aluminum Overhaul Slag Disposal
2023年4月25日 This article analyzes and summarizes the composition and hazards of the overhaul slag and the current development status of domestic and international electrolytic Coal gangue is a byproduct of the production of coalassociated minerals, Review of Research on the Pr2024年5月23日 16 Million metric tons of spent carbon electrodes modify carbonrich solid wastes from aluminum electrolysis are produced annually, threatening ecosystems by cyanide The recycling of carbonrich solid wastes from aluminum 2020年8月1日 Here, we discuss the influence of different processing parameters on electrolytic refining of aluminum alloy and investigate the mechanism of extracting Al from coarse AlSi Recovery of aluminum from waste aluminum alloy by low
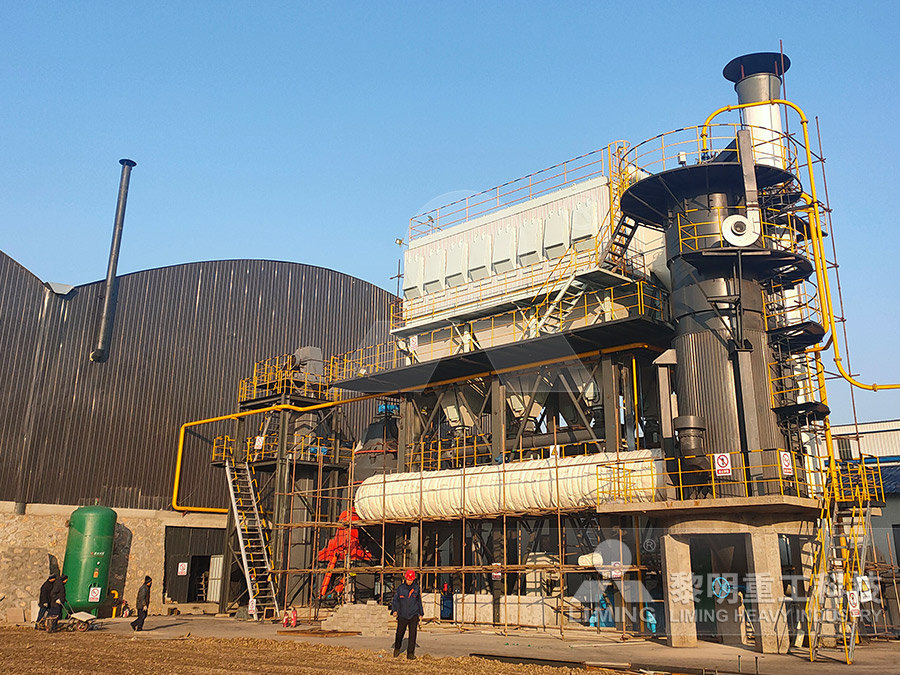
Efficient lithium recovery from electrolytic aluminum slag via an
2024年2月1日 The electrolytic aluminum industry generates a large amount lithium (Li)containing electrolytic aluminum slag (EAS) annually, and this can result in severe This study collected electrolytic aluminum waste cathodes, anodes, limestone and other materials After grinding the materials with an electric mill, 50 grams of electrolytic aluminum waste Research on the Coprocessing of Mixed Electrolytic Aluminum 2022年1月10日 In this study, grinding characteristics of spent carbon anode from aluminum electrolysis in both ball mill and rod mill were analyzed, and compared based on the utilization of the selectiveSelective comminution and grinding mechanisms of 2024年2月1日 This process is easy to operate and highly controllable, achieving efficient separation and recovery of lithium, aluminum, and fluorine in the overhaul slag The research A novel approach for extracting lithium from overhaul slag by low
.jpg)
A comprehensive review of aluminium electrolysis and the waste
2023年4月13日 The process of aluminium electrolysis and the ways to improve the current efficiency of aluminium electrolysis cells and reduce their energy consumption are outlined 2023年4月13日 Aluminium is produced by electrolysis using alumina (Al2O3) as raw material and cryolite (Na3AlF6) as electrolyte In this HallHéroult process, the energy consumption is A comprehensive review of aluminium electrolysis and the waste 2024年2月2日 Calcium carbide slag is a difficult industrial waste to treat Millions of tons of calcium carbide slag are piled up in China yearly, occupying a large amount of land and easily causing secondary pollution []The main component of calcium carbide slag is Ca(OH) 2, with 71–95% content []Therefore, the current recycling methods of calcium carbide slag mainly Research on Using Carbide Slag to Mineralize the Carbon Dioxide 2024年6月29日 Aluminum electrolyte is a necessity for aluminum reduction cells; however, its stock is rising every year due to several factors, resulting in the accumulation of solid waste Currently, it has become a favorable material for the resources of lithium, potassium, and fluoride In this study, the calcification roasting–twostage leaching process was introduced to extract Stepwise extraction of lithium and potassium and recovery of
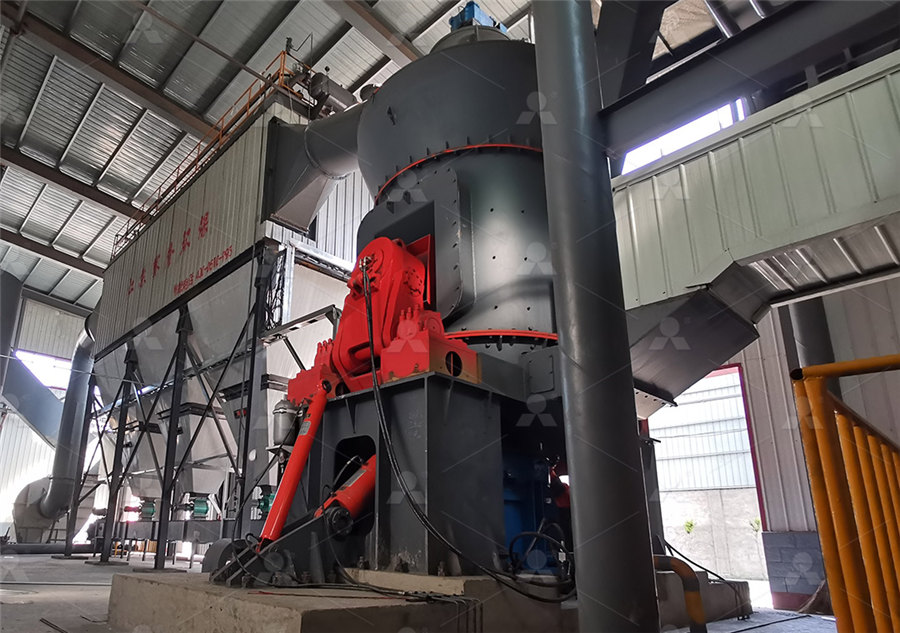
The use of aluminum slag waste in the preparation of roof tiles
2021年12月1日 Abtract Aluminum slag waste generated from the smelting process of bauxite was used to prepare roof tiles samples Clay was substituted by slag waste in percentages reaching 40% in the basic mix 2022年10月10日 The comprehensive recovery and utilization of electrolytic aluminum spent carbon anode slag (Hereinafter simplified as “carbon anode slag”) are therefore necessary Flotation is a physical separation method used to separate particles by using the difference in surface property of particles ( Chen et al, 2022 ; Ni et al, 2022 )Recovery of carbon and cryolite from spent carbon anode slag of 2022年9月1日 A study of the solidification and stability mechanisms of heavy metals in electrolytic manganese slagbased glassceramics(PDF) A study of the solidification and stability mechanisms of 2022年2月19日 Recycling waste containing rare earth has always been a research hotspot The molten salt electrolysis process of rareearth metals and alloys generates a large amount of waste slag, which contains high rareearth content and, thus, has very considerable recovery value However, the high content of fluorine in rareearth molten salt slag brings challenges to the Recovery of RareEarth Elements from Molten Salt Electrolytic Slag
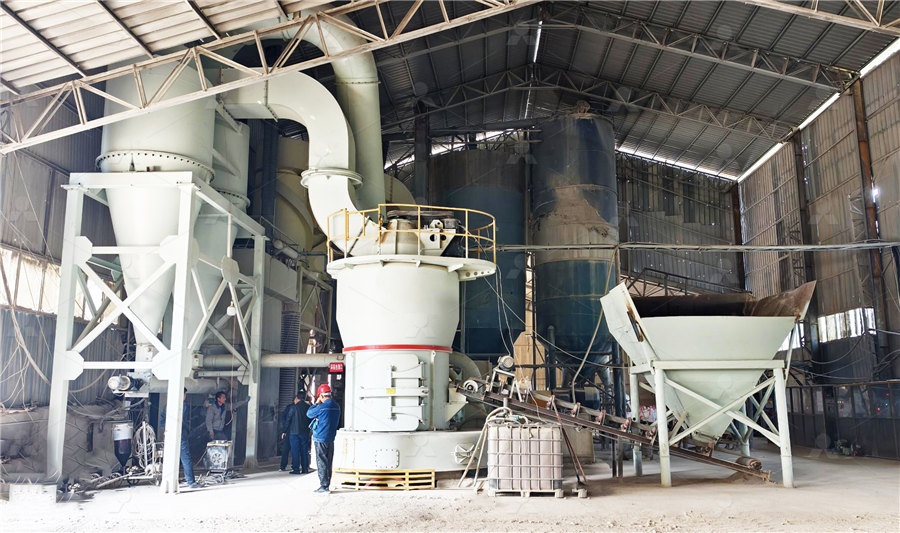
Synthesis of Electrolytic Manganese Slag Solid WasteBased
Materials 2024, 17, 1431 3 of 16 the preparation of geopolymers Sodium hydroxide (NaOH) particles were purchased from Sinopharm Reagent (Shanghai, China), and sodium silicate (Na2SiO3) powder with a modulus of 314 was purchased from 2023年6月1日 0duction process, only 719% of manganese from raw materials is converted into the final product, while the rest enters the anode slag, known as electrolytic manganese anode slag (EMAS) [3]For every 1 ton of electrolytic manganese produced, 50–150 kg of anode slag is generated [4]In China, the annual output of electrolytic manganese is approximately 15 Kinetics and mechanism of manganese reductive leaching from 2012年12月31日 The paper provides a brief introduction in the physical and chemical properties of waste aluminum cathodes, and its harmless treatment technology and resource comprehensive utilization technologyStudy on Harmless and Resources Recovery Treatment Technology of Waste 2020年12月1日 The rapid development of the electrolytic aluminum industry in China and the increasing demand for aluminum products have led to the development of many lowgrade bauxite mines with an average Li 2 O content of at least 058% (Wang et al, 2013)Due to the use of this lowgrade bauxite in the electrolytic aluminum process, the content of lithium in the Novel process for the extraction of lithium carbonate from spent
.jpg)
Utilisation of lead–zinc mill tailings and slag as
2020年8月14日 Paste backfilling is an incipient underground mine backfill technology in India It facilitates maximum use of mill tailings with enhanced stability of the underground workings and minimises rehandling of water, as 2009年8月1日 Mill scale is an iron oxide waste generated during steelmaking, casting and rolling Total generation of mill scale at JSWSL is around 150 t/day and contains 60–70%FeO and 30–35%Fe2O3Recycling of steel plant mill scale via iron ore ResearchGate2023年3月12日 The aluminum electrolysis industry continually and unavoidably produces hazardous solid waste in the form of carbon anode slag Carbon anode slag poses a serious environmental pollution risk, and it must be disposed of Recovery of Carbon and Cryolite from Spent Carbon 2017年3月5日 PDF Nowadays, iron and steel industries are moving toward environmental sustainability through careful control of greenhouse gas emissions and Find, read and cite all the research you need (PDF) Iron and Steel Slags ResearchGate
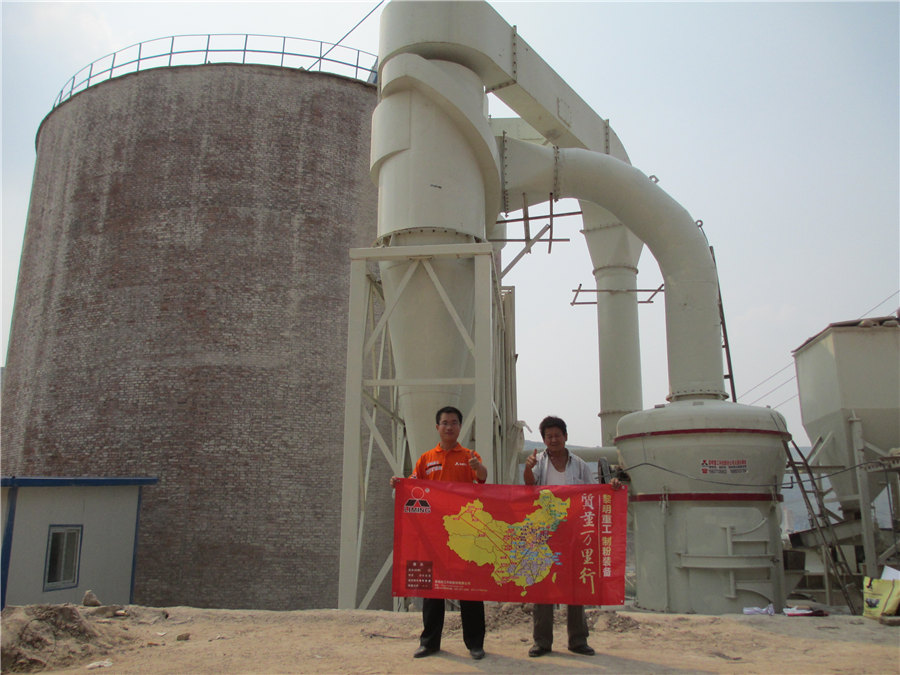
Aluminium salt slag characterization and utilization – A review
2012年5月30日 Aluminium salt slag is toxic/hazardous waste (production: 200–500 kg/Al tonne) Chemical and mineralogical characteristics are presented Various processes for Al metal recovery and recycling of KCl/NaCl to smelting process are reported Preparation of value added products from the final NMR is discussed2016年5月16日 Reduce, reuse, and recycle are important techniques for waste management These become significant for improving environmental and economic condition of industries Integrated steel industries are generating huge amounts of steel slag as waste through the blast furnace and Linz–Donawitz (LD) process Presently, these wastes are disposed by dumping in Sustainable Approaches for LD Slag Waste Management in Steel The aluminum electrolyte waste used in this work was sourced from an electrolytic aluminum plant in Sichuan, China The quantitative analysis and characterization were carried out for the aluminum electrolyte sample before the experiments The result of XRD (see Fig 1a) indicates that the aluminum electrolyte consisted mainly of cryolite Na(3 Stepwise extraction of lithium and potassium and recovery of 2024年3月21日 manganese slag–solid wastebased geopolymer (SWGP) was evaluated by analyzing the mineral phase, morphology , and leaching concentration of the geopolymer 2Synthesis of Electrolytic Manganese Slag–Solid WasteBased
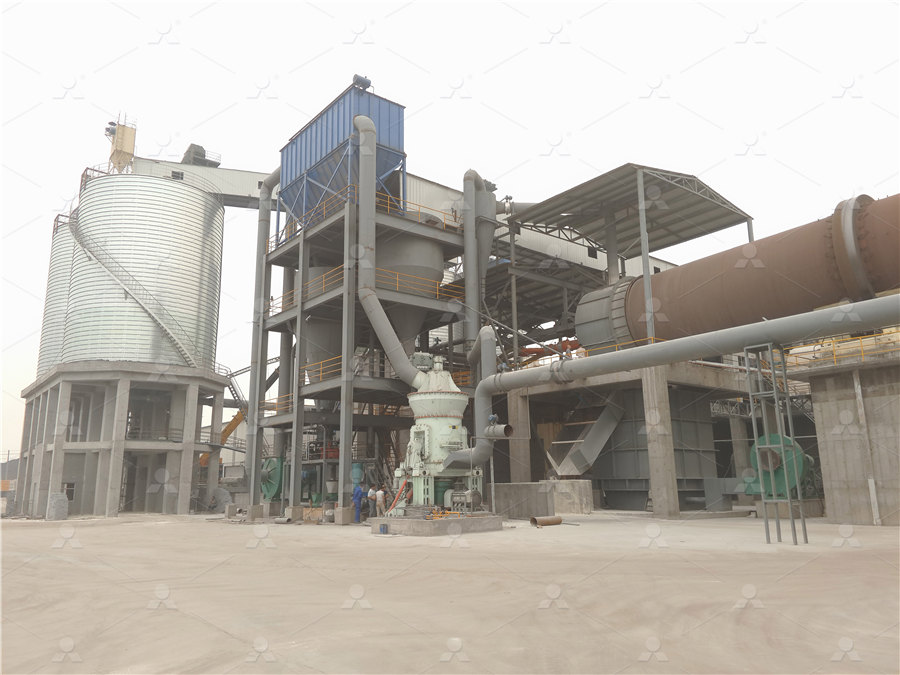
Synthesis of Electrolytic Manganese Slag Solid WasteBased
Mn]+ + +]]))]]]))] + 2023年4月13日 This paper proposes a technical viewpoint for the recovery of waste heat in aluminum electrolysis The idea of combining heatgenerating electrolysis process and the heatconsuming alumina tube A comprehensive review of aluminium electrolysis and the waste 2024年9月23日 This critical review systematically explores the innovative utilization of ground granulated blastfurnace slag (GGBS), steel slag (SS), and other steel waste in concrete, addressing a crucial research gap in predicting concrete properties with these materials By analyzing 97 publications, this review offers a comprehensive understanding of how these Enhancing concrete properties with steel waste: a comprehensive 2013年6月1日 In this research, the electrolytic manganese residue (EMR) based beliteye'elimiteferrite (EBYF) clinker composed of 516 % belite, 256 % iron phase, 158 % ye'elimite and 65 % overburned Preparation of electrolytic manganese residue–ground
.jpg)
(PDF) Production of Reduced Iron from Mill Scale Waste Using
2023年1月1日 Suppression of CO2 discharged from iron and steel making companies is an example of the biggest issues for the protection of global environment and sustainable growth of steelmaking industry2020年8月1日 Many researchers have studied the refining of aluminum by low temperature aluminium bath system Ali and Yassen (2018) used a different type of dissolvent to recover aluminum from industrial wastes This method was capable of obtaining aluminum of 99% purity by electrorefining of impure aluminum through the use of anhydrous AlCl 3 and NaCl as ionic Recovery of aluminum from waste aluminum alloy by low There are three ways for extracting Aluminum, primary source from aluminum ores (bauxite ore), XRD analysis shows the same profile for both samples of aluminum saline slag, milling the original waste in a ball mill for 3 h with alumina 10 mm balls and a single extraction with NaOH 2 mol/dm3 for 1 hEfficient recovery of aluminum from saline slag wastes2021年12月10日 Lately, the content of metals in ores has been decreasing, due to the intensive extraction and processing of various ores rich in metals At the same time, the annual amount of industrial waste containing both precious metals and other useful compounds is increasing []Waste in dumps contains heavy nonferrous metals, compounds of silicon, calcium, Processing of NonFerrous Metallurgy Waste Slag for its
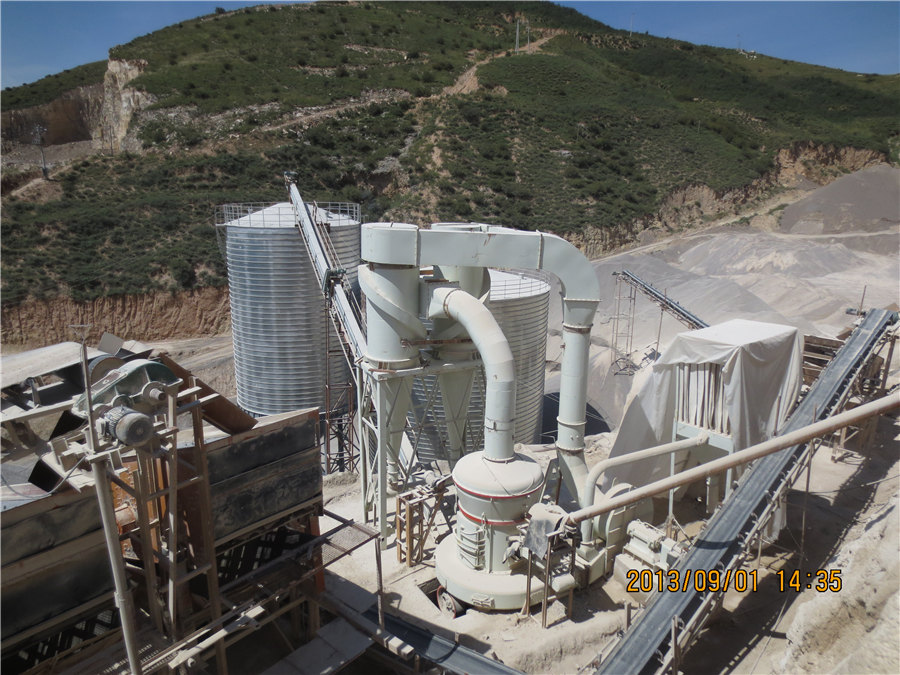
Recycling of steel plant mill scale via iron ore sintering plant
2012年4月1日 Adding mill scale as an ingredient into the iron ore sintering or pelletizing process is the main utilization approach for mill scale because of its high iron content and positional advantages [10 2023年12月1日 Tong et al (2023) mixed aluminum sulfate and calcium oxide to treat the rare earth molten salt electrolytic slag and achieved the expected effect, indicating that the reaction with fluoride in rare earth molten salt electrolytic slag after mixed roasting is feasible, which is consistent with the thermodynamic calculation results of the reaction of coroasting aluminum Review of efficient recycling and resource utilization for rare earth 2021年1月23日 Aluminum dross is a hazardous solid waste produced in the process of electrolytic aluminum or cast aluminum production, with annual emission of more than 3 million tonsProcess for stabilizing fluorine in electrolytic aluminum spent pot 2023年8月1日 The overhaul slag from the aluminum reduction cell is a hazardous waste The annual production of overhaul slag is above one million tons in China [1]The overhaul slag mainly consists of spent impervious materials and refractory bricks [2], [3]A large number of hazardous substances, such as fluorides and cyanides, are included in the overhaul slag [4]Dissolution behavior of overhaul slag from aluminum reduction
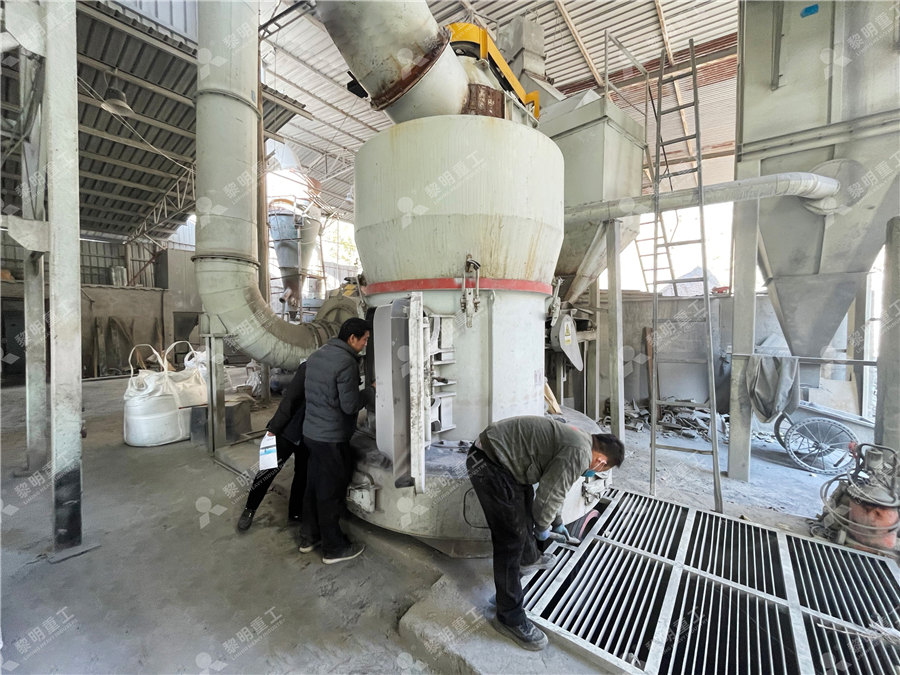
Efficient extraction and recovery of lithium from waste aluminum
2023年10月1日 Cryolitealumina (Na 3 AlF 6Al 2 O 3) molten salt electrolysis is the only modern method for the industrial production of metallic aluminum (Ishak et al, 2017)Under the influence of direct current, Al 2 O 3 dissolved in the molten salt is reduced to monolithic aluminum at the cathode (Haraldsson and Johansson, 2020)As the blood of the electrolytic cell, the electrolyte 2024年9月1日 REO's proportion of the moltensalt electrolytic slag sample (wt%/TREO) Element Nd 2 O 3 Pr 6 O 11 Sm 2 O 3 Other; An investigation on the kinetics of chromium dissolution from Philippine chromite ore at high oxygen pressure in KOH sub Recovering rare earths and aluminum from waste BaMgAl 10 O 17:Eu 2+ and CeMgAl 11 O 19:Tb Recovering rare earths, lithium and fluorine from rare earth molten 2014年10月16日 Mill scale is an industrial waste, produced in rolling mills during hot rolling process Mill scale constitutes iron (60 to 70 %) in elemental form as well as in form of oxides as Wusite (FeO Direct Reduction of Mill Scale By Low Grade Coal: An 2024年11月1日 The utilization rate of SS exceeds that of LFS due to its lower basicity, although it remains considerably lower than the rates observed in developed countries in Europe and the United States, standing at approximately 30 % [4]Currently, the internal recycling of SS predominantly takes place within the smelting production process, serving purposes such as Recent research progress on recycling metallurgical waste slag
.jpg)
Selective comminution and grinding mechanisms of spent carbon
2022年1月10日 The recovery of spent carbon anode (SCA) materials plays important roles in environment protection and resources recycling, while this cannot be efficiently achieved without liberation2021年1月12日 At present, the treatment methods of carbon anode slag from electrolytic aluminum mainly include flotation [8, 9], vacuum smelting [10], physical activation, roasting, alkali fusion, bubbling (PDF) The Study of Carbon Recovery from Electrolysis Aluminum Carbon 2024年2月1日 Aluminum metal was produced using the cryolitealumina molten salt electrolysis method (Ishak et al, 2017) A large amount electrolytic aluminum slag (EAS) is generated during the electrolysis process, as the falling of carbon particles on the anode into the electrolysis cells and the accumulation of lithium fluorine result in energy consumption and electrolyte scrapping Efficient lithium recovery from electrolytic aluminum slag via an Maytham Mahmood Ali AlKhwarizmi Engineering Journal, Vol 14, No 3, PP 81 91 (2018) 82 reasons Comparison with extraction ofRecovery of Aluminum from Industrial Waste (Slag) by Melting
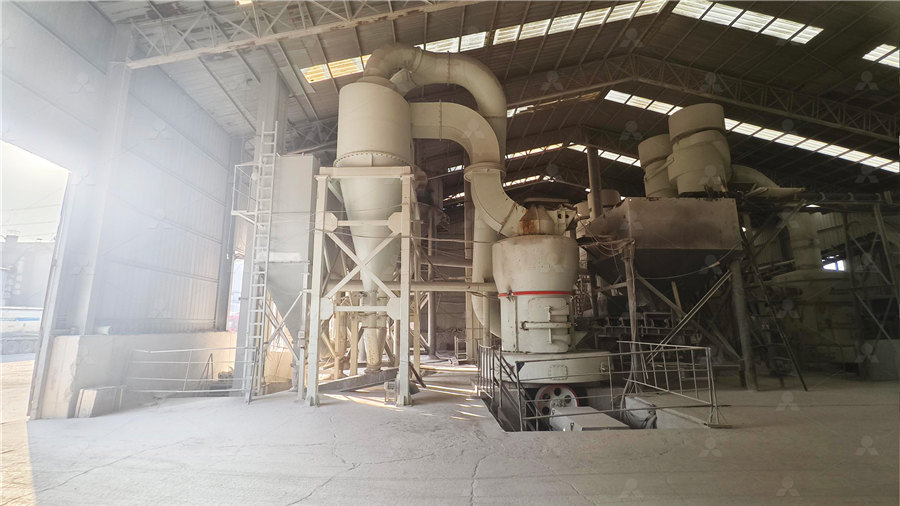
Clean Process for Selective Recovery of Lithium Carbonate from Waste
2023年9月1日 Lithium (Li)bearing aluminum electrolyte slag is an inevitable byproduct of the aluminum industry, and improper disposal or stacking it may lead to potential environmental hazards This study employed hydrometallurgical processes to selectively leach lithium from Licontaining aluminum electrolyte slag, using sodium carbonate solution as the leaching agent 2018年9月3日 Values and average of melting percentage of Aluminum with and without using flux at different temperature at (TOA) L9 Recovery of Aluminum from Industrial Waste (Slag) by Melting