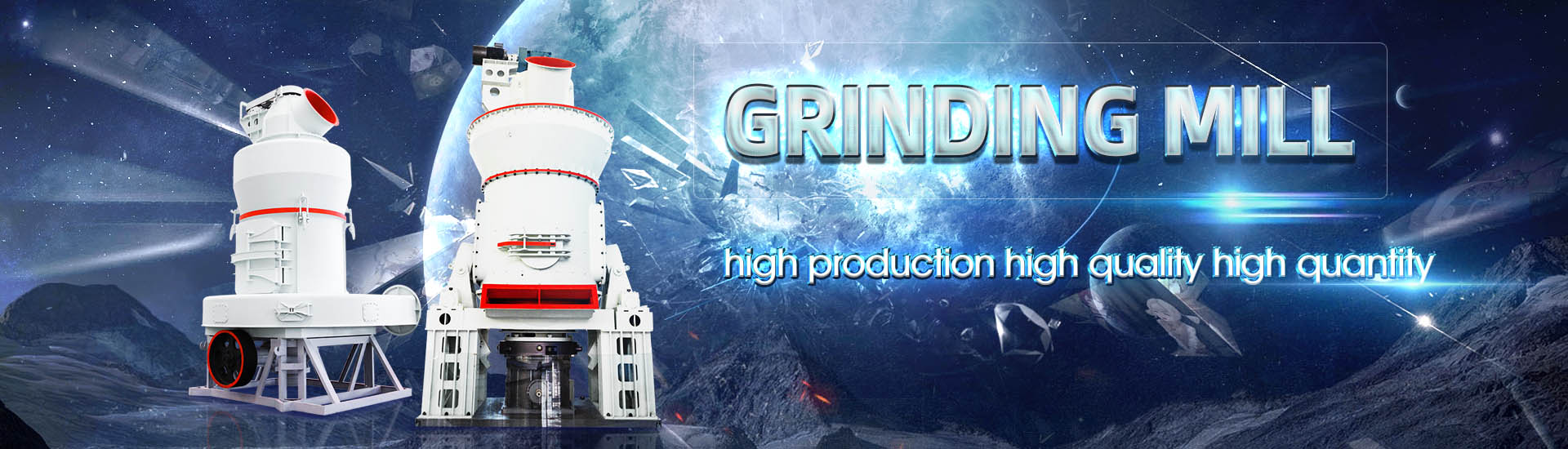
Large oxidation Output of iron powder processing equipment
.jpg)
Oxide reduction and oxygen removal in wateratomized iron
Iron oxide reference samples were used to establish a baseline for the subsequent thermogravimetric experiments and kinetic analyses of the wateratomized 展开It is shown that with rise in temperature and increase in exposure time, water vapor concentration in the atmosphere, and particle size the rate of oxidation of an iron powder grows On the Oxidation of iron powders Powder Metallurgy and Metal 2023年8月8日 The oxygen content of metal powder is decisive for the recyclability of powder The research on the effect of oxygen content on powder properties and material formability Influence of powder oxidation on powder properties and 2024年2月1日 Iron powder releases energy through exothermic oxidation (combustion), and stores back energy through its subsequent hydrogenbased reduction, establishing a circular loop for renewable energyHydrogenbased direct reduction of combusted iron
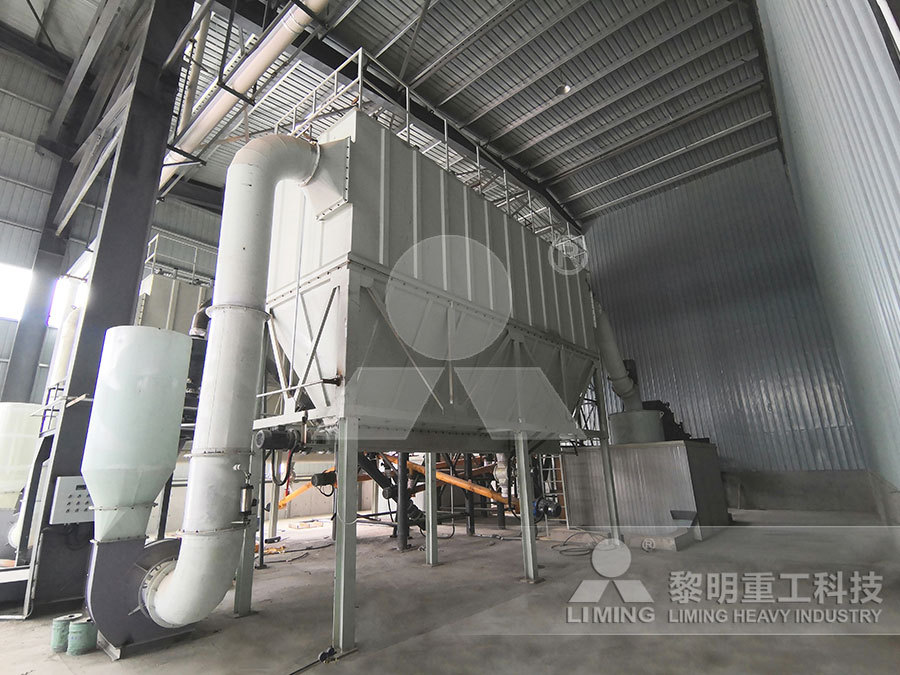
Phase transformations and microstructure evolution during
Only small fractions of nanoparticles during the combustion of iron powders have been reported, mostly occurring in excessoxygen conditions [6 , 8 , 9 , 11–14 , 16 , 17 ] The oxidation of iron 2021年3月1日 In this review, the possible applications of different ironbased materials (eg, zerovalent iron, iron (hydr)oxides, and iron composite materials) in AOPs and their activation Application of ironbased materials in heterogeneous advanced 2017年12月14日 The innovation and creation of process and equipment of Ezhou pelletization plant of BAOWU plays an exemplary role for the application of largescale gratekilncooler in A case study on largescale production for iron oxide pellets: 2024年5月15日 The combusted products, the iron oxide particles, are captured and cyclically reduced back into iron powder in a process that is powered by renewable energy Each Cyclic reduction of combusted iron powder: A study on the
.jpg)
JIP® Iron Powder Products and Technical Trends in Powder
JFE Steel’s iron powder products corresponding to technology trends of these applications 1 Introduction Industrial iron powders include reduced iron powders, which are produced by 2023年4月3日 Further processing of these iron oxide powders could enable the production of iron powder for various applications in powder metallurgy For this purpose, a new process route with an ecofriendly hydrogen reduction Manufacturing and Properties of Spherical Iron 2024年4月26日 The final stage in iron ore processing is ironmaking, where the iron ore is transformed into molten iron through a process called reduction The most common method of ironmaking is the blast furnace route In a blast Iron Ore Processing: From Extraction to Manufacturing2024年5月18日 Ultrafine iron powder is widely used due to its excellent performance Hydrogen reduction of finegrained highpurity iron concentrate to prepare ultrafine iron powder has the advantages of low energy consumption, pollutionfree, and low cost The hydrogen reduction of highpurity iron concentrates, characterized by the maximum particle size of 643 μm when the Production of ultrafine iron powder by lowtemperature
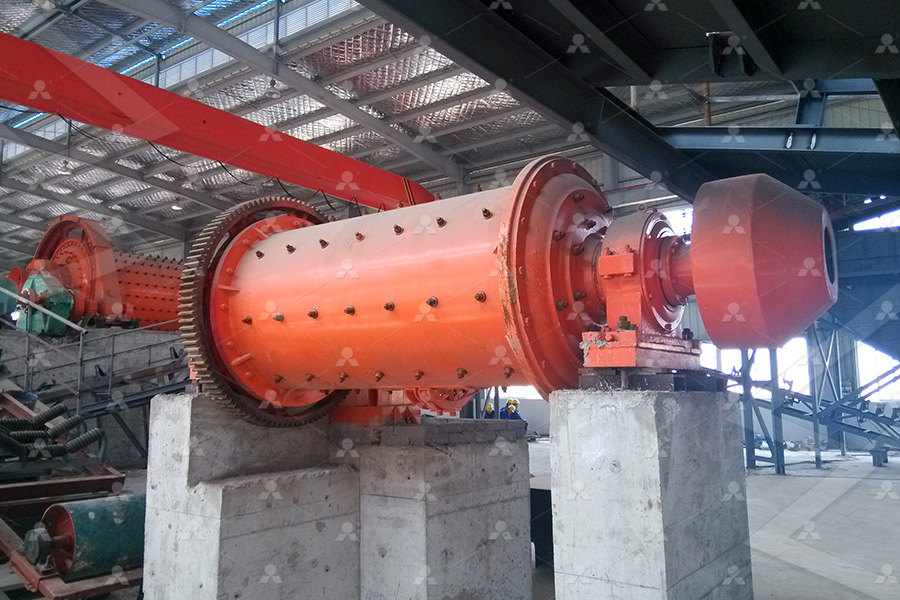
Outline of Iron and Steel Powder Products of JFE Steel
pure iron powder (reduced iron powder, atomized iron powder, or mixtures thereof) and the abovementioned alloyed steel powders are used as the main raw materials Additive powders (copper powder, graphite powder, etc) and lubricants are mixed with these main materials in line with the customer’s requirements, and additives2024年9月3日 This study aims to investigate the influence of Cr content on the hightemperature mechanical, oxidation, and electrical properties of powder metallurgy ferritic stainless steel for solid oxide fuel cell (SOFC) interconnect To achieve this objective, ferritic stainless steel wateratomized powders with different Cr content were first compacted and then sintered at 1380 °C Influence of Cr Content on the Mechanical, Oxidation, and 2016年6月15日 21 Preparation of Iron Foams Using FreezeCasting Iron oxide (Fe 2 O 3) powder (mean particle size 99 pct, SigmaAldrich, Co, USA) were used to make a slurry The slurry was prepared by mixing 10 ml deionized water with 4 wt pct binderProcessing, Microstructure, and Oxidation Behavior of Iron Foams2024年5月30日 Iron alloys powder refers to powder metallurgy forms of iron mixed with alloying elements like nickel, chromium, manganese, and carbon Iron powder metallurgy allows the manufacture of parts and components with controlled density, porosity, strength, magnetic and other properties by compacting and sintering ironbased powder mixes Overview of Iron Iron Alloys Powder: A Complete Guide Powder Metallurgy
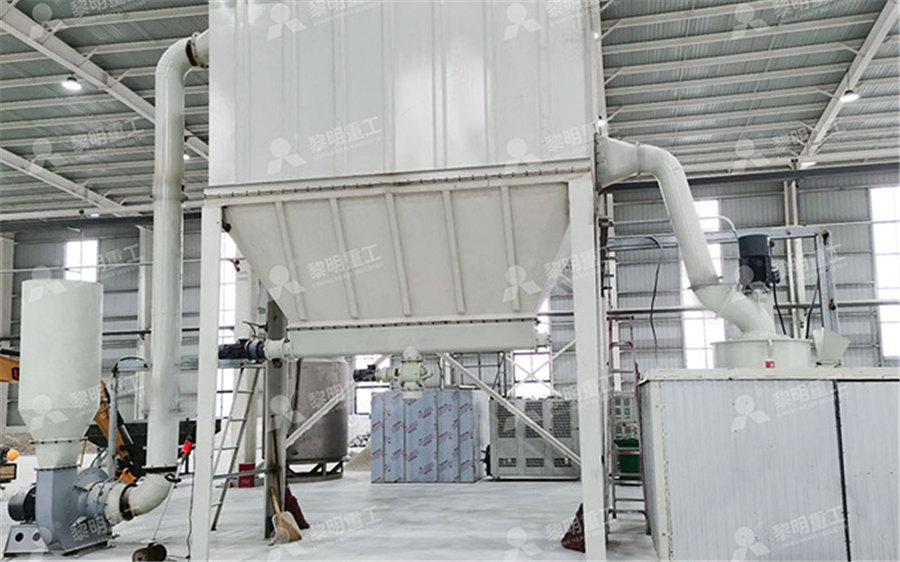
Iron as a sustainable chemical carrier of renewable energy:
2022年9月1日 The iron oxidation process produces iron oxides as byproducts As observed, the heating value in the oxides iron reduction EC (80%), iron powder generation including melting (87%), transport by ship from these 7 Mt of iron inventory represent 196% of one year’s production output Although that is a large 2022年9月1日 The sulfur components in the oil (elemental sulfur, hydrogen sulfide and organic sulfides) can cause serious corrosion damage to refinery equipment, storage facilities and transport pipelines during the processing of high sulfur oil, which results in frequent serious accidents caused by oxidative spontaneous combustion of iron sulfide (Hughes et al, 1974, Oxidative selfheating modeling of iron sulfides during the processing different for iron powder 5 Distribution of iron powder is done in closed systems and in a dry atmosphere to avoid water and the associated undesirable oxidation of the iron powder Transportation can be done by trucks, railway or inland shipping 6 Combustion of iron powder is a high temperature oxidation reactionIron Power ecosystem Metalot2016年6月13日 A historical overview of the origin and evolution of ferrous metallurgy, fundamentals of producing iron and its alloys, is presented The paper shows the sequence of discoveries behind the technology of iron and steel, the effect of carbon on the formation of cast iron and steel, as well as the progress in foundry and thermomechanical treatment of iron Iron Age: Origin and Evolution of Ferrous Metallurgy Powder
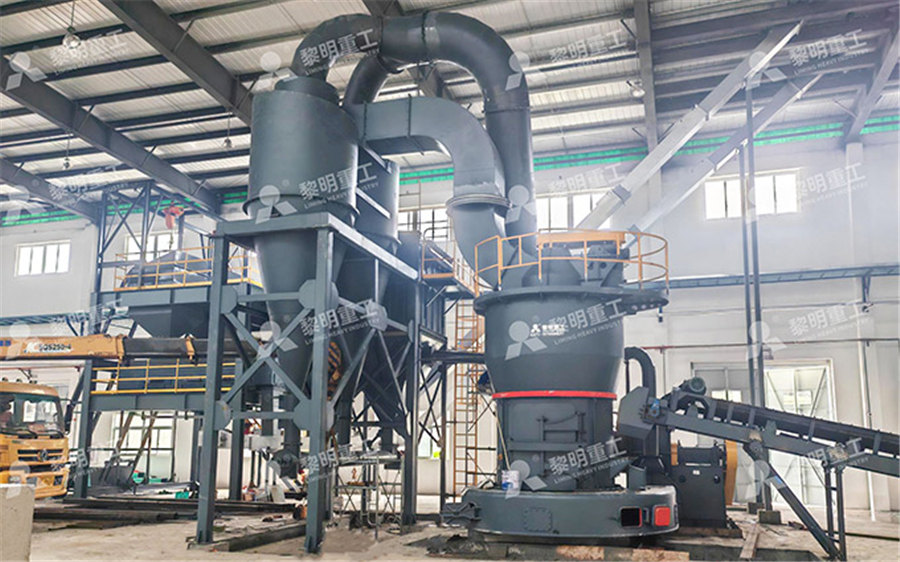
(PDF) Investigation on the reaction of iron powder mixture as a
2014年5月1日 The total released energy for Fe 10% (ΔH = 5917 J/g) was twice as much as that of Fe 20% (ΔH = 3021 J/g) Although there is data suggesting that an increase in the particle size of iron from 13 1 It is shown that with rise in temperature and increase in exposure time, water vapor concentration in the atmosphere, and particle size the rate of oxidation of an iron powder grows On the basis of experimental data, formulas have been derived enabling the relative weight gain of a powder and the thickness of magnetite films on its particles to be determined as functions Oxidation of iron powders Powder Metallurgy and Metal 2012年4月1日 Further processing of these iron oxide powders could enable the production of iron powder for various applications in powder metallurgy For this purpose, a new process route with an ecofriendly Production of sponge iron powder by reduction of 2019年5月23日 Li ZL, Li BS, Lü JF (2016) Current status and innovation of steel slag processing technology and equipment Mining Processing Equipment 44(2):1–6 Google Scholar Li BX, Wang YF, Zhong M (2016) Practice of producing superfine steel slag powder by ball milling double closed circuit process Cement Engineering 4:33–36Comprehensive Utilization Technology of Steel Slag
.jpg)
Hydrogenbased direct reduction of combusted iron powder:
PDF On Feb 1, 2024, Laurine Choisez and others published Hydrogenbased direct reduction of combusted iron powder: Deep preoxidation, reduction kinetics and microstructural analysis Find 2013年10月23日 The oxidation kinetics of ultrafine metallic iron powder to hematite (αFe2O3) up to temperatures 800 °C were studied in air using nonisothermal and isothermal thermogravimetric (TG) analysis The powders with average particles size of 90, 200, and 350 nm were made by the electric explosion of wire It was observed that the reactivity of the iron The oxidation kinetics study of ultrafine iron powders by 2014年1月1日 A large number of ceramic powderformed components can be placed in a large HIP for a single HIP run, whereas HP is generally one component per cycle, with a cycle time of many hours Thus, while HP is primarily a research technique, HIP can be both for research and mass productionPowder Processing of Bulk Components in Manufacturing2016年3月1日 Powder production After atomisation, powders are traditionally collected in a cyclone system These powders are typically nonpassivated The transfer of these nonpassivated powders from the atomisation cyclone to ancillary process containers is considered to present a high risk of thermal runaway, which may require breaking of the inert gas seal and Titanium powder: Safe production and processing in Additive
%3C1PGHL[2}HK_]YT.jpg)
Investigation on the reaction of iron powder mixture as a
2014年1月30日 This paper reports our investigation on the thermal behavior and ignition characteristics of iron powder and mixtures of iron with other materials such as activated carbon and sodium chloride in which iron is the main ingredient used as fuel Thermal analysis techniques such as differential scanning calorimetry (DSC) and thermogravimetric analysis equipment while the powder and the die assembly are heated to temperatures of about 100–150°C At higher temperatures, lubricants begin to break down and the oxidation of iron powders occurs more rapidly; hence, oxide films can occur when processing metal powder and this chapter has discussed some of the ways to mitigate theseA review of Developments in Powder Metallurgy Technique for Global Powder Processing Equipment Market Overview The Powder Processing Equipment market industry is projected to grow from USD 6,0200 Billion in 2024 to USD 8,44120 Billion by 2032, exhibiting a compound annual growth rate Global Powder Processing Equipment Market 2013年8月14日 Metallic powder has applications in many fields In applications for preservation and antioxidation, iron powder has been used as an air oxygen reducer which is capable of decreasing (PDF) Investigation of typical properties of
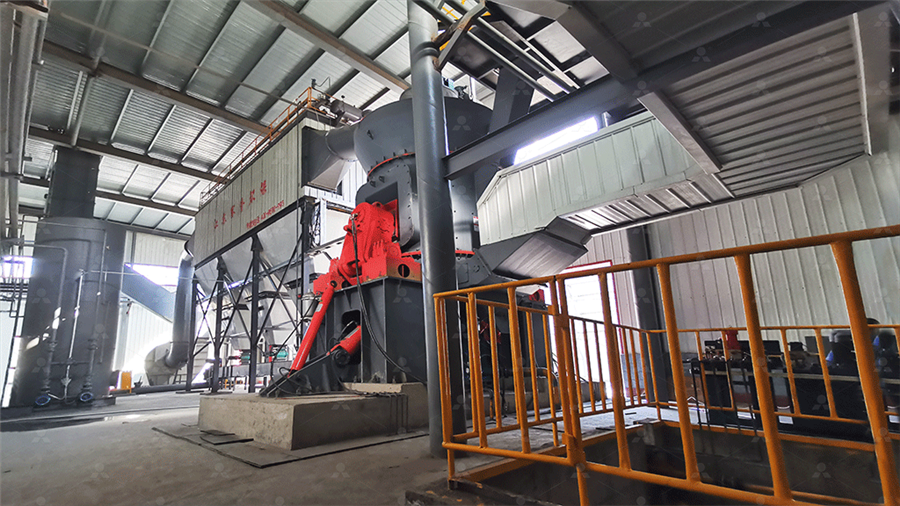
Mechanisms in oxidation and sintering of magnetite iron ore
2008年4月9日 Total oxidation weight gain was measured by TGA in magnetite concentrate powder samples with a heating rate of 5 °C/min The total oxidation weight gain was 338% (236% Fe 2+) in all samples In earlier literature, several different TGA measuring methods have been used to measure the oxidation rate in iron ore pellets2020年6月10日 Herein, the molten metal along with slag (produced during iron processing in blast furnace) is to be separated by a barrier called skimmer It separates the slag from metal by allowing the slag leave from the top into slag runner as slag has low density than molten iron The iron passes through a passage in the skimmer at the bottomIron and SteelMaking Process SpringerLink2020年12月1日 Mill scales are the metallurgical waste generated by oxidation process on the surface of the metal during the hot rolling process in the steelmaking industry [4,5] Overview on production of reduced iron powder from mill scale 2022年1月1日 Water atomisation can produce metal powders faster and at lower cost than gas atomisation, but it is well known that the powder particles are irregular and may contain a large number of poresThe current study analyses three iron‑carbon alloys with different superheats, produced as powder by water atomisation and compares the particle shapes and porosity in Particle morphology of water atomised iron‑carbon powders
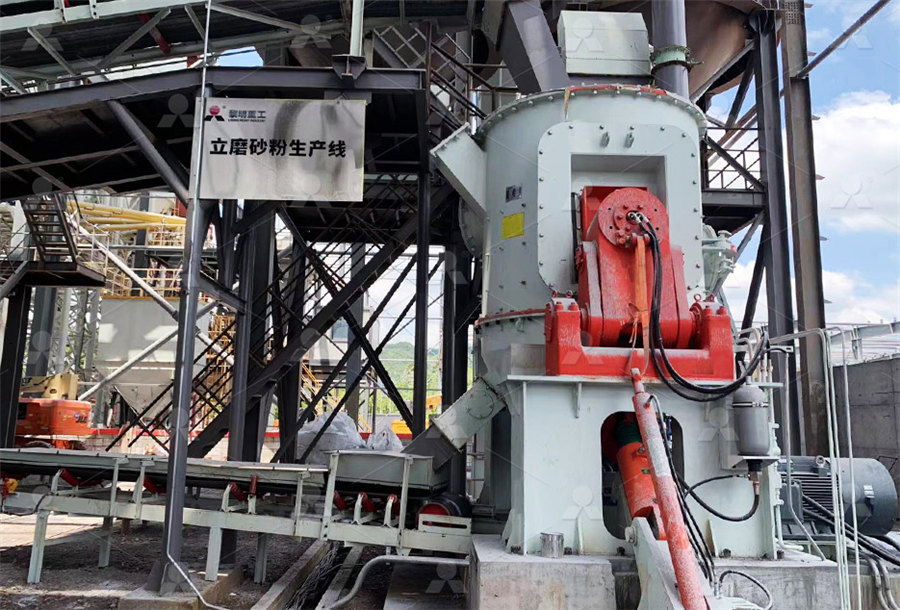
Design and Selection of Food Processing Equipment
2015年12月30日 Nearly linear increases of the cost of centrifugal pumps and centrifuges during the period 1960–1990 were observed (Figs 24 and 25), corresponding to average annual increases (inflation) of 65 and 75 %, respectivelyThese increases are significantly higher than the average annual increases of the MS equipment index (45 %) over the same period (Fig PDF On Jul 11, 2018, Sandra Lúcia de Moraes and others published Iron Ore Pelletizing Process: An Overview Find, read and cite all the research you need on ResearchGateIron Ore Pelletizing Process: An Overview ResearchGate2023年3月14日 The schematic of the MOE process is shown in Fig 3Wang et al [] used the MOE method to treat the raw materials of iron concentrate powder used in blast furnace smelting and analyzed the energy consumption of the MOE ironmaking processSibille et al [] produced metal iron and oxygen by performing electrolytic melting on a floating soil analog at 1600 °CResearch progress in the preparation of iron by electrochemical 2000年12月8日 The oxidation kinetics for uncoated iron powder (raw iron) and phosphated–iron powder were investigated by thermogravimetric analysis in a Setaram TGA 92 thermobalance The sensitivity of the balance is 1 μg Samples were heated at 50°C/min up to the desired oxidation temperature under an argon atmosphereOxidation of phosphated iron powders ScienceDirect
.jpg)
Metal Powder Atomization Equipment Guide In August 2024
Advantages of Metal Powder Atomization Compared to conventional metal processing routes, key benefits of using atomized powders include: Improved mechanical properties – Fine, homogeneous microstructure from rapid solidification increases yield strength, fatigue life, and ductility; Precise dimensional control – Consistent, spherical powder enables high density and 2013年10月29日 The oxidation kinetics of ultrafine metallic iron powder to hematite (αFe2O3) up to temperatures 800 °C were studied in air using nonisothermal and isothermal thermogravimetric (TG) analysisThe oxidation kinetics study of ultrafine iron 2022年9月25日 The results showed that for flotation tailings with a reducing agent carbon powder of 25%, an additive calcium oxide of 10%, and reducing for 90 min at 1300 °C, iron concentrate with a 9216% iron grade at an iron recovery of 8765% was obtained, and the iron grade of tailings could be reduced to 391%Extraction and separation of copper and iron from copper large production mills » 5 hp to 400 hp main drives » Typical milled particle size range down to a D50 of 10μ to 5μ » Easy to adjust particle size output » Integral classifier for a fine powder The PPS Air Classifier Mill incorporates an internal airclassifying wheel with an independent drive giving precise control over “particle cut Powder Processing Equipment Systems Qlar
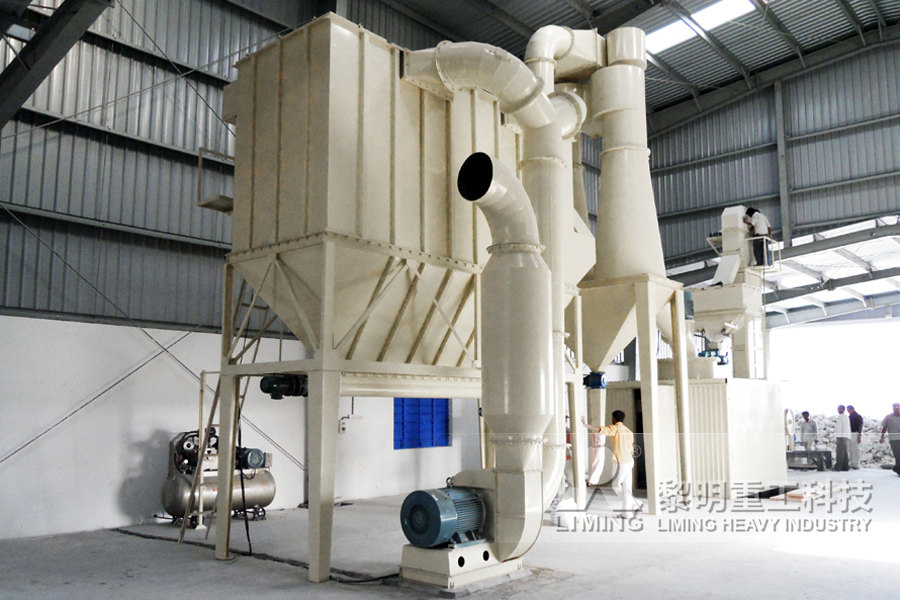
Iron processing Definition, History, Steps, Uses, Facts
Iron processing, use of a smelting process to turn the ore into a form from which products can be fashioned Included in this article also is a discussion of the mining of iron and of its preparation for smelting Iron (Fe) is a relatively dense metal with a silvery white appearance and distinctive2014年1月1日 A large number of ceramic powderformed components can be placed in a large HIP for a single HIP run, whereas HP is generally one component per cycle, with a cycle time of many hours Thus, while HP is primarily a research technique, HIP can be both for research and mass productionPowder Processing of Bulk Components in Manufacturing2021年9月1日 Addition of iron powder is found to be a promising solution to the structure degradation of MgO–C refractory during oxidation, but it may reduce the high temperature propertiesMgOC Refractories: A Detailed Review of These Irreplaceable 2022年1月14日 The iron oxides are reduced to direct reduced iron under a strong reducing atmosphere, and the per cent of metallization goes up to 90% in 15–20 min of time [ 25 ](PDF) A Review on Processing of Electric Arc Furnace
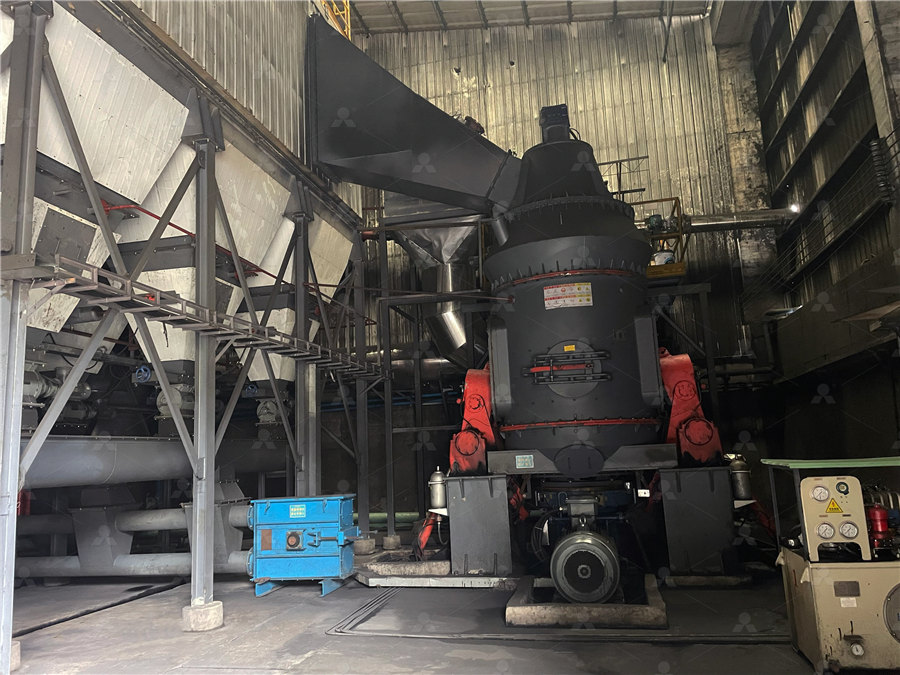
Iron Powder Material Additive Manufacturing Material
2023年12月11日 But for large structural fabrications, traditional casting or deformation processing of steel is better Iron Powder Material 4 FAQ Q How is iron powder classified based on particle sizes? Iron powder is commercially classified by mesh sizes into: Coarse grades – below 100 mesh size (149 microns) Fine grade – 100 to 400 mesh (37 to 149 2023年11月27日 With the development of social economy, the consumption of iron ore, like other mineral products, is increasing As the variety of available iron ore continues to increase, the grade of its target minerals is getting lower and lower Therefore, there is often an increasing shortage of highquality iron powder Therefore, it is necessary to improve the mineral Iron Ore Processing Technology and Equipment Xinhai