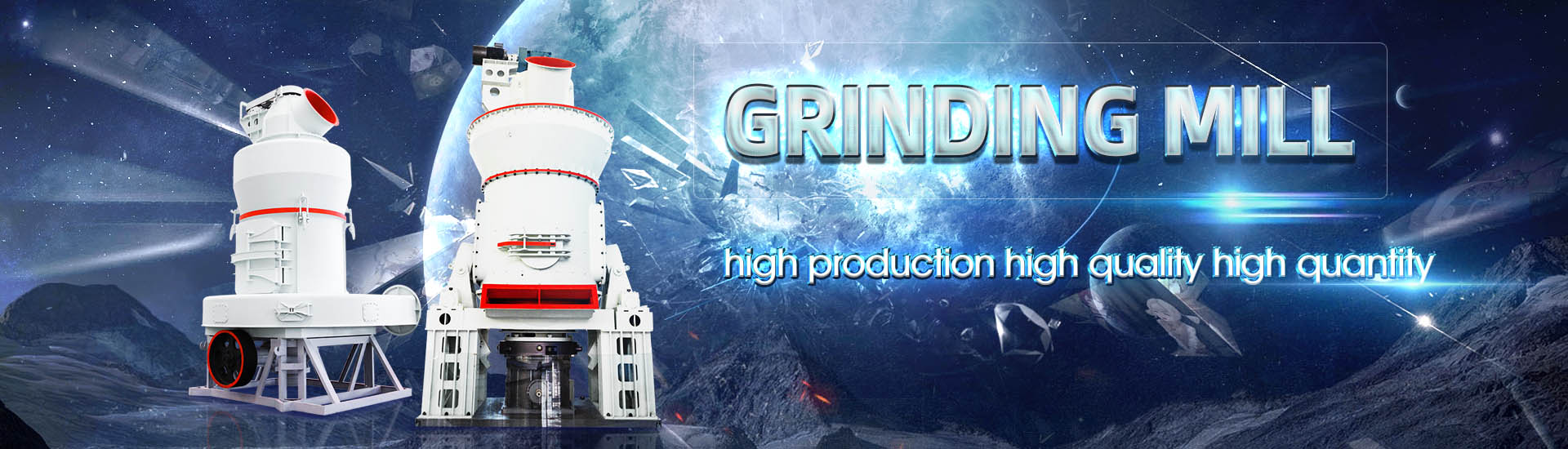
Large coal mill principle
.jpg)
LOESCHEMILLS
The modular structure of larger roller grinding mills enables utilisation of the same components in different mill sizes Module components include grinding rollers, rocker arms, pedestals and spring assemblies The principle behind this structure was patented in 1970 and is employed for coal Mills are mechanical devices used to break different types of solid materials in small pieces by grinding, crushing or cutting In pulverised coalfired power plants, a pulveriser coal mill grinds Coal Mill an overview ScienceDirect Topics2012年5月1日 The paper presents development and validation of a coal mill model to be used for improved mill control, which may lead to a better load following capability of power plants Derivation and validation of a coal mill model for control2015年11月1日 Coal mills are bottleneck in coal–fired power generation process due to difficulty in developing efficient controls and faults occurring inside the mills In this paper, a dynamic A unified thermomechanical model for coal mill operation
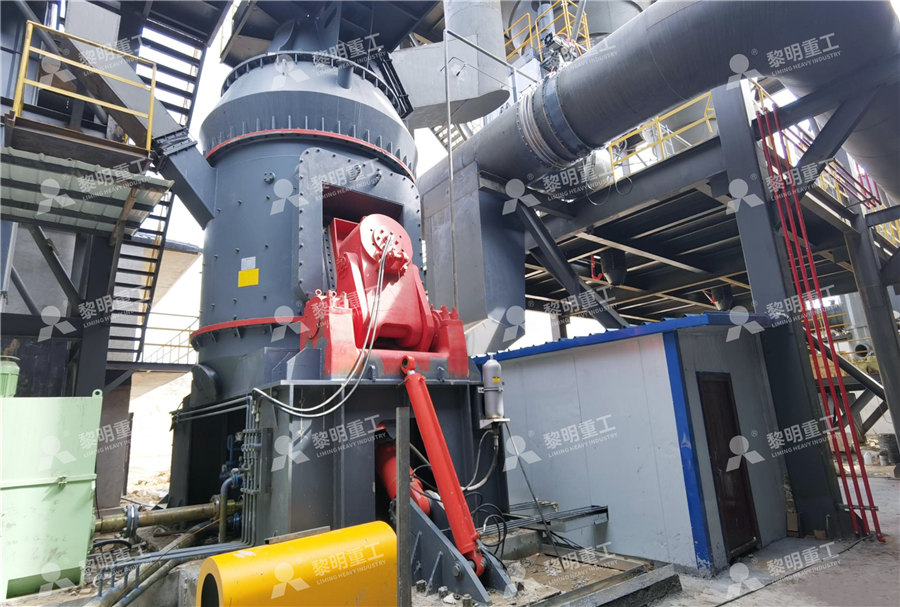
OFTEN Loesche
The modular structure of large roller grinding mills enables the use of the same components in different mill sizes The principle behind this structure was patented in the 1960s and is vertical roller grinding mills for grinding: • Coal • Cement raw material • Clinker / granulated slag • Industrial minerals, and • Ores The core elements of these plants are the Loesche vertical PROCESS OPTIMISATION FOR LOESCHE GRINDING PLANTSspindle coal pulverising mill’s performance to facilitate optimal plant performance Plant design and mill’s acceptance test data was analysed to understand the design and subsequentPerformance optimisation of vertical spindle coal pulverisersPulverized coal (PC) firing is the dominant method used in modem power sta tions So, most of this chapter will focus on coal preparation systems for PC boilers and their design Fluidized Coal Preparation Systems for Boilers Springer
.jpg)
An investigation of performance characteristics and energetic
2020年8月12日 To understand the performance of a vertical roller coal mill, the real operational tests have been performed considering three different coal sources Obtained results indicate Introduction Hot Sale: Drying and grinding are two in one, and can dry while grinding Domestic largescale highend vertical coal mill LM vertical coal mill, also known as mediumspeed coal mill, is lunched by the company for the LM vertical coal millThe mediumspeed coal mill is a crucial largescale equipment in the coaltooil pulverizing system : ec@shyychina consult online leave a message Working Principle The electric motor drives the grinding disc through the MPS ZGM Coal MillGrinding Equipment YingYong 2024年6月17日 Imagine hitting a piece of chalk with a standard hammer Hammer mills work using the same principle, except more hammers hit materials faster and with more force A hammer mill supplies repeated impacts to crush Understanding Hammer Mill Operation Pulva
.jpg)
Modeling and Control of Coal Mill
Abstract: The paper presents development and validation of coal mill model (including the action of classifier) to be used for improved coal mill control The model is developed by using the mass and heat balance equations of the coal mill Genetic Algorithm is used to estimate the unknown parameters that are used in the model validationThe ball mill is used for the grinding of a wide range of materials, including coal, pigments, and felspar for pottery, and it copes with feed up to about 50 mm in size The efficiency of grinding increases with the holdup in the mill, until the voids between the balls are filled Further increase in the quantity then lowers the efficiencyBall Mill an overview ScienceDirect TopicsAt present, the rod mill is widely used, and is widely used in the preparation of coalwater slurry in coal chemical industry, quartz sand, silica sand, sand aeration, tungsten ore, potassium albite, The working principle of the rod mill makes the rod mill suitable for many large industries or production linesThe Working Principle and Advantages of the Rod MillIntroduction This article concerns itself with vertical grinding mills used for coal pulverization only (coal pulverizers), although vertical grinding mills can and are used for other purposes The 3D model in the saVRee database represents a vertical grinding bowl millOther grinding mill types include the ball tube mill, hammer mill, ball and race mill, and , roll and ring millVertical Grinding Mill (Coal Pulverizer) Explained saVRee
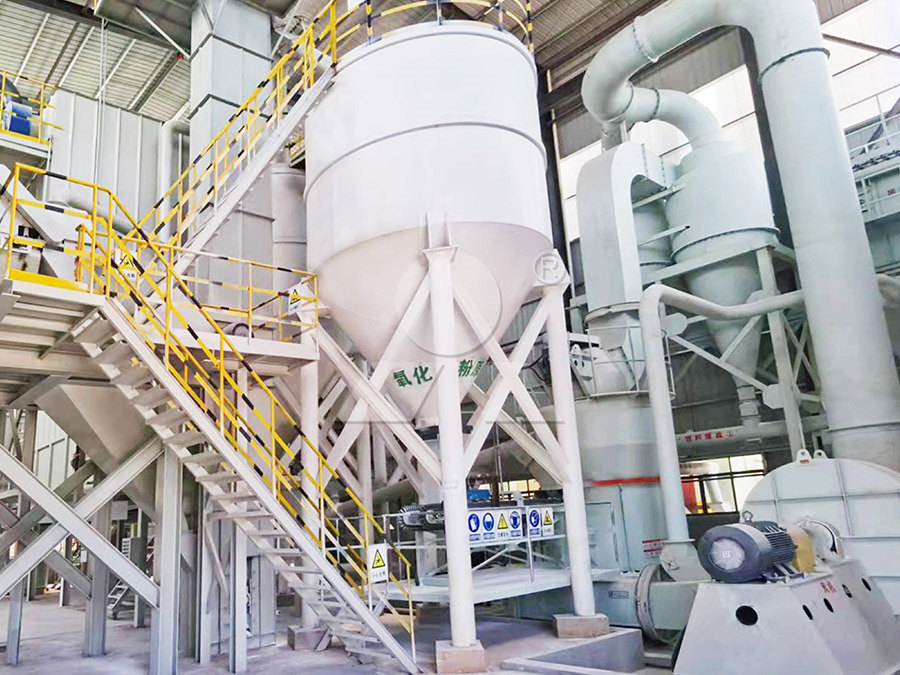
Air Swept Coal Mill Coal Mill In Cement Plant AGICO GROUP
Air Swept Coal Mill Working Principle First, the raw coal is fed into the feed chute by the feeding device Then, the hot air with a temperature of about 300 ℃ enters through the air intake pipe and begins to dry the raw coal while they are falling After The HC series large grinding mill is a large Raymond mill, a large pendulum millThe output is 3040% higher than that of traditional Raymond mill It is a product with the advanced technology, it has obtained several patents, designed by our engineers, it has advantages such as higher efficiency, high output, low consumption and environment friendlyLarge Raymond Mill Large Pendulum Mill Large Grinding MillA control oriented model was then developed by Fan (1994) and Fan and Rees (1994) In 2009, coal flow and outlet temperature of mill were modelled using mass and heat balance equations for startup Sectional view of MBF coal mill Download Scientific Diagram2020年8月12日 This study shows the performance of a currently running vertical roller coal mill (VRM) in an existing coalfired power plant In a power plant, the coal mill is the critical equipment, whose An investigation of performance characteristics and
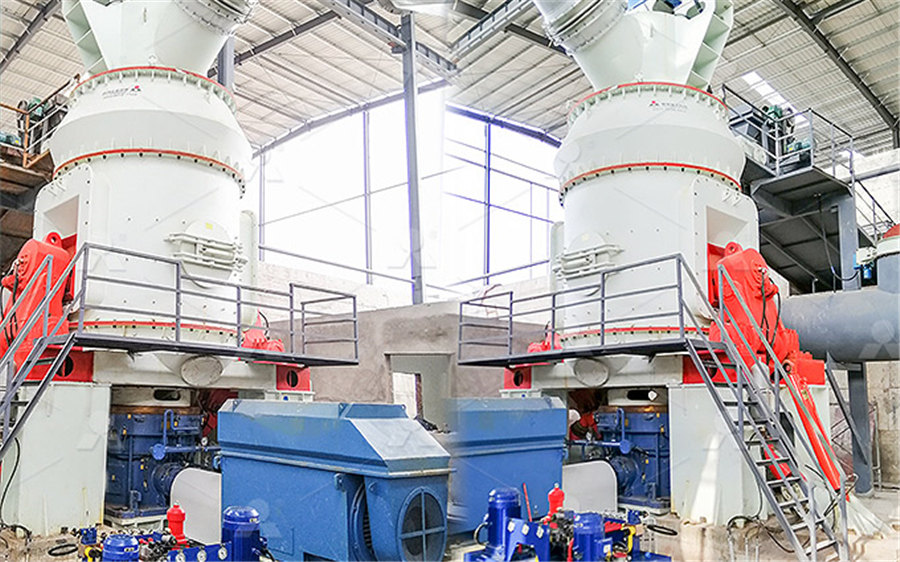
Coal Mill in Cement Plant Vertical Roller Mill Air
The pulverized coal is taken out of the mill by hot air Advantages Compared with the vertical roller mill, the advantages of airswept ball mill are strong adaptability to raw coal quality, simple operation and low investment cost; the Vertical coal grinding mill integrates crushing, drying, grinding, powder selection and conveying; It has simple system and compact structure Vertical coal mill covers an floor area about 50% of the coal ball mill with the same Vertical Coal Mill for Coal Grinding in Cement Plant2020年4月7日 Monitoring and diagnosis of coal mill systems are critical to the security operation of power plants The traditional datadriven fault diagnosis methods often result in low fault recognition rate or even misjudgment due to the imbalance between fault data samples and normal data samples In order to obtain massive fault sample data effectively, based on the Modeling of Coal Mill System Used for Fault Simulation MDPI2022年12月30日 A coal mill works by grinding coal into a fine powder using large metal rollers This process is used to create precise particle sizes as required by the applicationHow does a coal mill work? LinkedIn
.jpg)
Conical Ball Mills Benefits Advantages: Hardinge
2015年3月30日 It was with this idea in mind and with a realization that the machinery in use did not embody this working principle, that the Conical Mill was designed WORKING PRINCIPLE inside the Hardinge BALL MILL In the Hardinge Mills, due to the action of the cones, the coarse material on entering the machine gravitates to the point of largest diameter2012年5月1日 Coal fired power plants are heavily used due to large and long lasting coal resources compared with oil or natural gas An important bottleneck in the operation of this particular kind of plants, however, is the coal pulverization process, which gives rise to slow takeup rates and frequent plant shutdowns (Rees Fan, 2003)In typical coal fired power plants, Derivation and validation of a coal mill model for control2023年7月4日 Working principle: the motor drives and the large particles directly fall on the grinding table for regrinding metal and nonmetallic minerals such as iron ore, manganese ore, cement raw clinker, limestone, blast furnace slag, and coal The highpressure roller mill mainly consists of the feeding system, working rollers Roller Mill SpringerLink1927 First Loesche coal mill delivered for the Klingenberg power station in Berlin 1953 500th coal mill plant sold worldwide 1961 Introduction of hydraulic spring assembly system 1965 Construction of first pressure mill (LM 122 D) 1980 Delivery of first modular coal mill (LM 263 D) 1985 Delivery of first selfinerting coal grinding plant (LM 212 D) for the steel industry (PCI LOESCHEMILLS
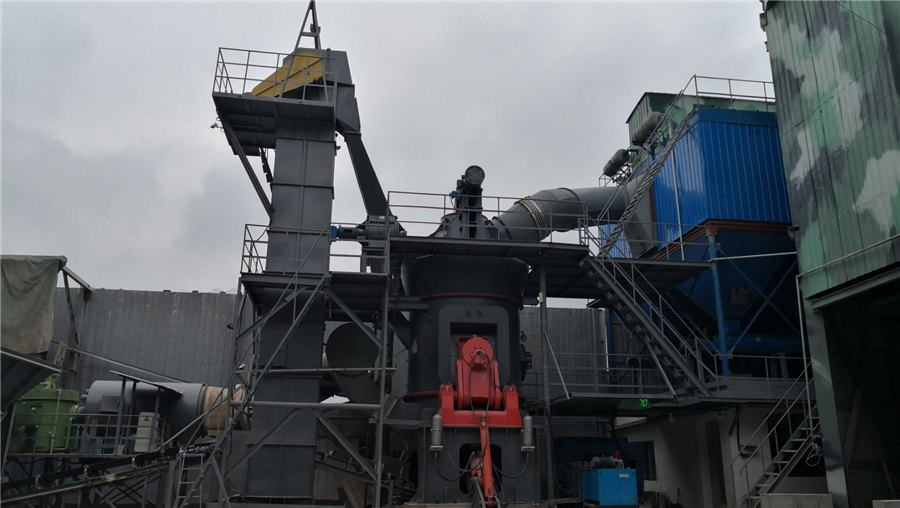
Principle of Vibration Milling and Its Industrial Applications
Vibration milling is a type of mechanical milling that utilizes vibrations to generate an impact force that breaks down particles into smaller sizes This process is commonly used in various industries for material processing and synthesis Vibration milling is a milling process that uses the principles of mechanical vibration and impact to reduce the particle size of various materials2017年2月13日 In all ore dressing and milling Operations, including flotation, cyanidation, gravity concentration, and amalgamation, the Working Principle is to crush and grind, often with rod mill or ball mill, the ore in order to liberate the Ball Mills 911Metallurgist2023年8月5日 High pressure roller mill is a new type of grinding equipment developed on the basis of roller press for cement in recent years Mines increase the specific surface area for fine grinding The high pressure roller mill has the characteristics of high production efficiency, large crushing ratio, low power consumption, significant energy saving and convenient maintenanceWorking principle of high pressure roller millZYmining2024年1月11日 With a vertical roller mill (VRM) VRMs consist of a rotating table or bowl and rollers 1 To grind the coal, feed raw or initially crushed coal into the mill which is then ground between the rotating components; 2 Finally, hot air How to Process Coal into Pulverized Coal in 5 Steps?
.jpg)
The structure principle of common large vertical mill reducer
2023年6月19日 The structure principle of common large vertical mill reducer 19 Jun 2023 Common models of domestic reducers: NGC MLX, MLXSD, MLXSS series; heavytoothed JLP, JLX, JLW series; imported Flender KMPS series; Hangzhou Auto Vertical Coal Mill (VCM) is equipment for grinding and pulverizing coal into micron size Rotary kilns then use the powders as fuel burners The VCM has a housing section equipped with a lining The layout of the coal mill with a rotary classifierOther industries: plastic industry, textile industry, paper industry, coal flotation agents, nanomaterials, and other industries that require environmentallyfriendly production colloid mill principle Colloid mill is a new type of equipment for ultrafine processing, suitable for homogenizing, emulsifying, and pulverizing various types of 4 ways to tell you what is a colloid mill Inox mill: pradeebhamit@gmail, npappa@rediffmail , vasanthi@annauniv Abstract: The paper presents development and validation of coal mill model (including the action of classifier) to be used for improved coal mill control The model is developed by using the mass and heat balance equations of the coal mill(PDF) Modeling and Control of Coal Mill Academia
.jpg)
Schematic diagram of the working principle of MPS medium speed coal
Download scientific diagram Schematic diagram of the working principle of MPS medium speed coal mill [1] from publication: Fault Diagnosis of Coal Mill Based on Kernel Extreme Learning Machine In discussion: Coal Mill Safety At best, coal mill safety is not well understood and, at worst, it is ignored When it comes to coal mill systems, most cement plant operators just presume that the supplier of the equipment knows all of the standards and rules and is 100% capable of making a system that conforms to these and is therefore safeIn discussion: Coal Mill Safety Coal Mill Safety, Explosion and 2014年1月1日 Two mill systems are employed for most coal grinding applications in the cement industry These are, on the one hand, vertical roller mills (VRM) that have achieved a share of almost 90% and, on (PDF) MPS mills for coal grinding ResearchGate2022年7月26日 diagnosis of the major faults in the coal mill system [4] Fan et al, designed a knowledgebased finegrained coal mill operator support/control system for coal plants The system is composed of mathematical coal mill model and expert knowledge database and has the ability of parameter estimation, coal mill performance monitoring, fault diagnosisFault Diagnosis of Coal Mill Based on Kernel Extreme Learning
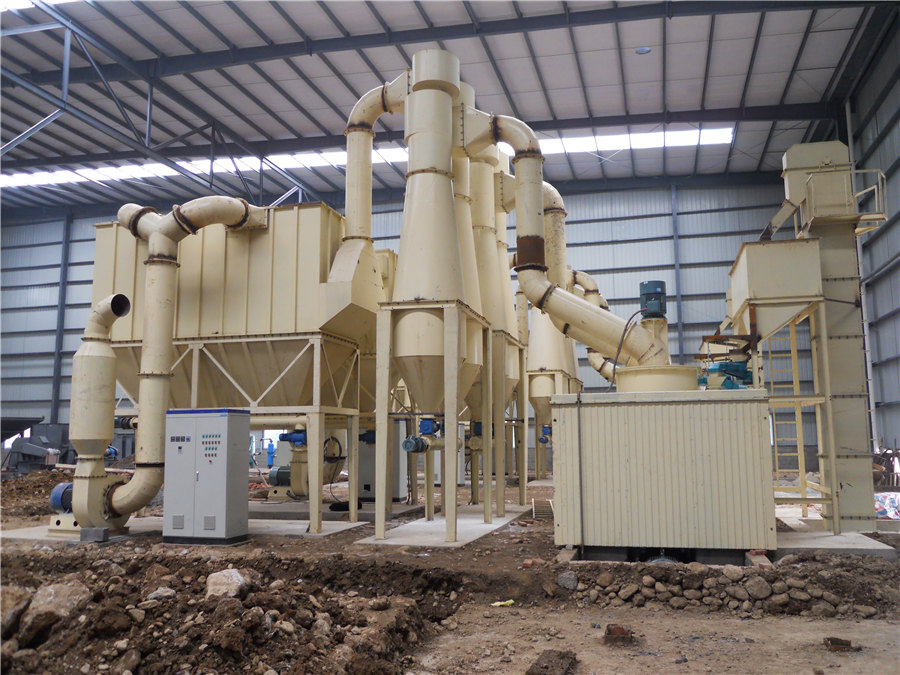
Modelling of Vertical Spindle Mills in Coal Fired Power Plants
A mathematical model of a vertical spindle mill used in coalfired power plant is presented The model is developed based on a mill size mass balance (SMB) and mill global mass and energy balances The model has been validated using data collected from a 660 MW unit during mill modelling field tests The model can be used to perform mill dynamic performance studies, Abstract: The paper presents development and validation of coal mill model (including the action of classifier) to be used for improved coal mill control The model is developed by using the mass and heat balance equations of the coal mill Genetic Algorithm is used to estimate the unknown parameters that are used in the model validationModeling and Control of Coal Mill2009年9月20日 A control oriented model was then developed by Fan (1994) and Fan and Rees (1994) In 2009, coal flow and outlet temperature of mill were modelled using mass and heat balance equations for startup Modeling and Parameter Identification of Coal MillCoal mill has reasonable structure and high grinding efficiency, which is the ideal equipment for coal preparation Coal Mill Working Principle of Coal Mill Coal mill is mainly composed of feeding device, main bearing, rotating part, pulverized coal burner, discharging device, highpressure starting device and lubrication systemCoal Mill with Industrial Solutions Fote Machinery(FTM)
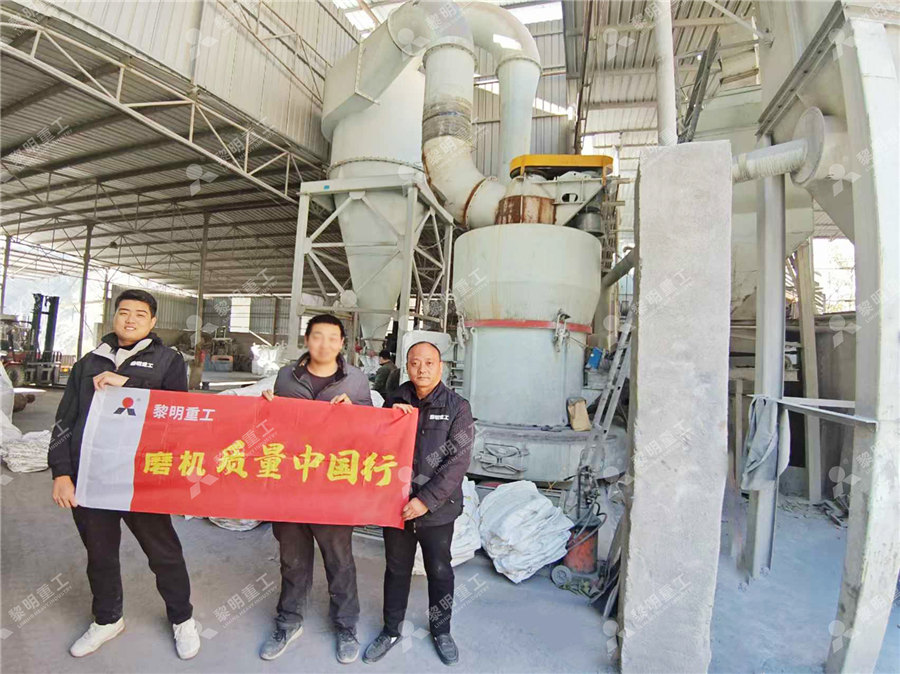
Pulverizer Plant OM Aspects
Stoker large Medium Low Big Pulverized Short High Medium Tiny Cyclone Based on principles of particle size reduction Maximum mill Capacity vs coal moisture at coal HGI 100110 and PF Fineness of 70 % passing through 200 Mesh 3500 3600 3700 3800 3900 4000 4100 4200Principle of Hammer Mill Hammer mills are used in industries such as steel, coal, aluminum, and cement manufacturing They're especially useful in manufacturing where large quantities of materials need to be processed Hammer Mill Principle Construction, Working and AdvantagesVertical roller mills (VRM) have become increasingly popular in recent years, as more cement producers look to increase their use of clinker substitute materials instead of importing clinker to meet localized rises in cement demand The demand for cement has grown rapidly in recent years, creating a need for a more efficient way to grind clinker and other raw materials used in How does Vertical Roller Mill Work? ball mills supplierSemifinishing grinding system: after ground by cement roller press, materials are divided into three parts through an air classifier: coarse, medium and fine, in which the coarse material is returned to the roller press for regrinding, the medium material is put into a ball mill for further grinding, and the fine material is directly discharged as the finished cement productCement Roller Press Roller Press In Cement Plant Roller Press
.jpg)
Optimization control of a pulverizing system on the basis of the
DOI: 101016/JCONENGPRAC201703015 Corpus ID: ; Optimization control of a pulverizing system on the basis of the estimation of the outlet coal powder flow of a coal mill