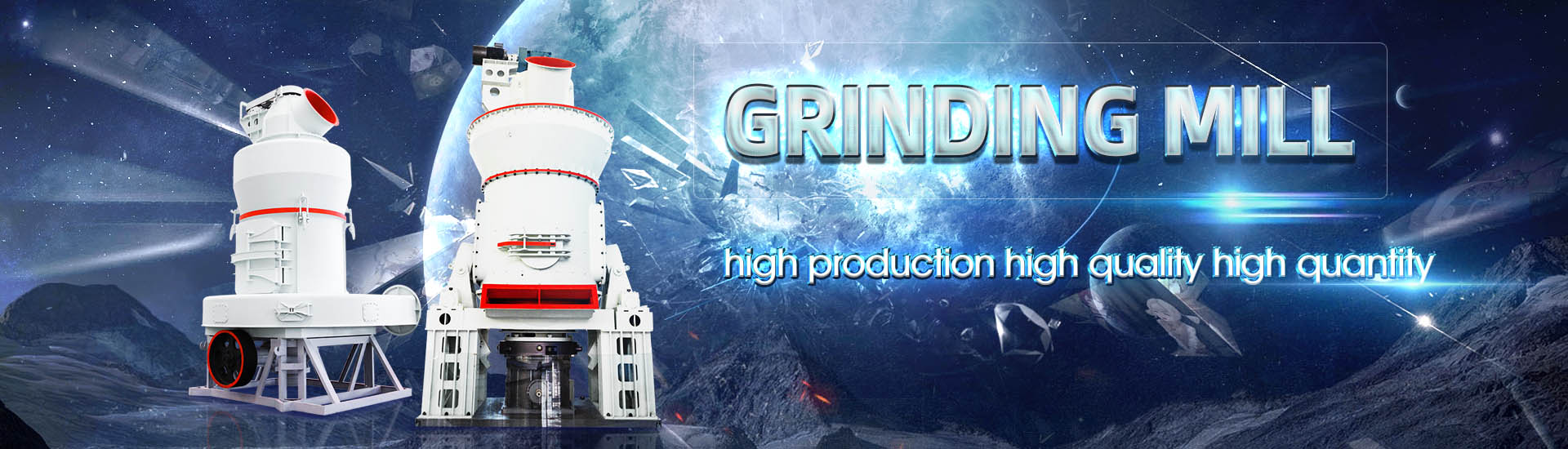
What is the role of crushing in the powder making process
.jpg)
Pulverization 1: Definition and purpose The global standard for
“Pulverization” (comminution, crushing, grinding) is the process of applying an external force to a (solid) material of a certain size to destroy it and reduce it into pieces that are smaller than the original size Pulverization has long been done for many materials, including ore, glass, ceramics, grains, paints, and 展开Comminution is the oldest mechanical operation for the size reduction of solid materials and is an important step in many processes where raw materials are converted into intermediate or final Comminution an overview ScienceDirect TopicsThere are four main processes used in powder production: solidstate reduction, atomization, electrolysis, and chemical In solidstate reduction, selected ore is crushed, typically mixed with carbon, and passed through a continuous furnaceMaking Metal Powder MPIF2015年12月26日 In mineral processing or metallurgy, the first stage of comminution is crushing Depending of the type of rock (geometallurgy) to be crushed, there are 2 largely different techniques at your disposition for Crushing in Mineral Processing 911Metallurgist
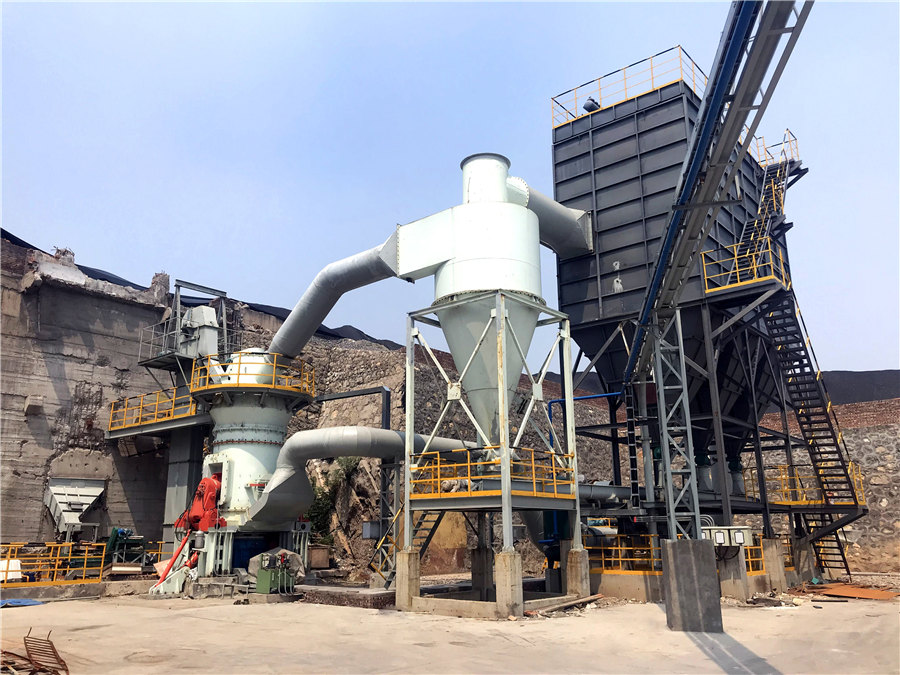
Powder metallurgy – basics applications IIT Guwahati
Crushing => for making ceramic materials such as oxides of metals; Grinding => for reactive metals such as titanium, zirconium, niobium, tantalum R Ganesh Narayanan, IITG2023年2月22日 Metal powder is the raw material of the PM process, produced by grinding, crushing, atomization, or chemical reactions The production method you choose depends on quantity, desired properties, and many other factors Powder Metallurgy Process: Steps, Applications2007年1月1日 Crushing is a size reduction process for particles of brittle materials It is characterized by particle diameters, volumetric equivalent diameters and by force releases on Chapter 4 The Principles of SingleParticle CrushingThe unit operation of the size reduction or comminution of solids by crushers and mills is a very important industrial operation involving many aspects of powder technology It is estimated Size Reduction of Solids Crushing and Grinding Equipment
.jpg)
Primary Crushing SpringerLink
Although a considerable amount of fine grinding is done by dry methods, this book follows usage by reserving the word “crushing” for an operation predominantly dry and “grinding” for work on Powder metallurgy usually refers to powder compression molding The powder metallurgy process involves several stages, such as powder preparation, mixing, pressing, sintering, etc, each contributing to the final production of high What is Powder Metallurgy Process, Materials, and 2019年10月31日 “Pulverization” (comminution, crushing, grinding) is the process of applying an external force to a (solid) (*6) Tsutomu Nakayama: Bead mill for making ultrafine particles and nanoparticles, p2328, p29, p3435 (*7) Powder Pulverization 1: Definition and purpose | THINKY 2024年11月23日 Cement Extraction, Processing, Manufacturing: Raw materials employed in the manufacture of cement are extracted by quarrying in the case of hard rocks such as limestones, slates, and some shales, with the Cement Extraction, Processing, Manufacturing
.jpg)
Powder Process an overview ScienceDirect Topics
Powder Processes Lorraine F Francis, in Materials Processing, 2016 56 Summary Powder processes provide a means to create simple as well as complex shapes from powder starting materials The engineering of powder processing methods requires an understanding of how the characteristics of powders, including size, size distribution and shape, impact the flow and 2020年1月1日 A minimal residual oil content in the meal coming out of the hexane extractor is a clear benefit for a crushing plant; the more oil yield the better revenue for the crusherOverview of the soybean process in the crushing industry2023年10月30日 The selection and design of crushing equipment in the mineral processing industry are influenced by several key factors, all of which are critical for achieving efficient and effective ore processing Chief among these factors is the material's inherent characteristics The hardness, abrasiveness, moisture content, and size distribution of the ore significantly impact The selection and design of Crushing equipment Performance 2015年7月18日 Coarse crushing includes crushing operations discharging at sizes 4 to 6in or coarser; intermediate crushing comprises operations taking feeds 6 or 8in maximum and making products down to 1/2″ or 3/8″ Fine crushing is reduction by crushing to 1/4″ or finer; the distinctions are not sharpRock Crushing Process in Mining 911Metallurgist
.jpg)
Types of Crushers: Choosing the Right One for Each Stage
2024年7月17日 Crushing is a multistage process that includes primary crushing, secondary crushing, and tertiary crushing Different types of crushing equipment are used at each stage to meet various crushing requirements Primary crushing breaks down large raw materials into mediumsized pieces for easier handling in subsequent processes2018年11月19日 PDF The aim of mineral processing is to get the mineral from rock or Ore that has good economic value in the market Generally, the ability of Find, read and cite all the research you need (PDF) Comminution in mineral processing ResearchGateIn the manufacture process of cement, clinkers are formed These cement clinkers are cooled down and added with small amount of gypsum The mixture then sent to final grinding process For ordinary Portland cement it remains between 3 to 4% and in case of Quick setting cement it can be reduced up to 25% Role of Gypsum in CementRole of Gypsum in Cement and its Effects – theconstructor2020年9月10日 The main goal of this work was to demonstrate a broad range of starch applications in ceramic powder synthesis, and to point out that starch and its derivatives can successfully replace polyvinyl derivatives commonly used in Role of starch in the ceramic powder synthesis: a
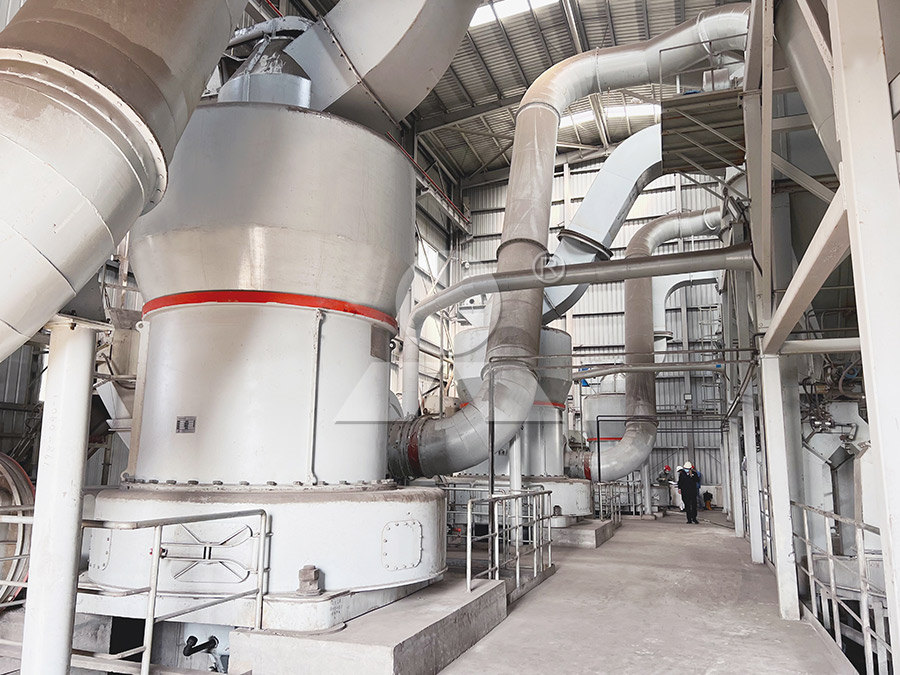
(PDF) The Effects of Blasting on Crushing and Grinding
2003年1月1日 This paper examines the role blasting plays in optimum crushing and grinding with the emphasis on energy reduction The role of different blasting energy input on fragmentation is studied, and mineral processing, art of treating crude ores and mineral products in order to separate the valuable minerals from the waste rock, or gangue It is the first process that most ores undergo after mining in order to provide a more Mineral processing Metallurgy, Crushing Grinding 2023年6月27日 This setup is a barite processing plant configured with a vibrating grizzly feeder, jaw crusher, log washer, spiral sand washer, vibrating screen, and belt conveyors The materials under the grizzly bar of the vibrating feeder go to 2 spiral sand washers through the material guide chute, the material above the grizzly bar feed to the jaw crusherWhat Is The Process Of Barite? Eastman Rock CrusherTertiary crushing is highly valuable in the mineral processing industry The degree to which a material is reduced largely depends on how fine the material’s final size should be More stages of crushing = smallersized products For tertiary crushing you will most likely need a smaller impactor or cone crusherTypes of Crushers: What You Need to Know Machinery Partner
.jpg)
Energy Evolution and Coal Crushing Mechanisms Involved in Coal
2023年12月16日 Coal and gas outburst is a dynamic disaster that poses a significant threat to coal mines Energy analysis is an effective tool for understanding the mechanisms behind such outburst The energy sources and dissipation during outbursts were explored using a multifunctional test system, and the energy transformation relationship was analyzed based on Crushing process All cullet, whether factoryowned or foreign, must be treated before it can be added to the melting process One of the most important parts of this cullet preparation is the crushing process, which is carried out in order to fulfil two major functions Firstly, it serves to reduce the size of the material so that itGlass crushing: The sharp end of cullet recycling Glass 2016年2月29日 Basically the process is supported by two facts, gold is soluble in dilute solutions of cyanide, and second, the pregnant solution can be processed successfully by using zinc powder or activated carbon and electrowinning In other words, the process involves several steps from crushing until obtaining a Dore barGold Extraction Recovery Processes 911Metallurgist2023年8月21日 Fig 5: Conventional Powder metallurgy process In conventional powder metallurgy, the process closely follows the basic steps of powder metallurgy, involving powder mixing, compaction, and sintering, with the incorporation of modern technology Injection Moulding Injection moulding offers the advantage of producing complex shapes in large Powder Metallurgy: Definition, Process, Advantages, Applications
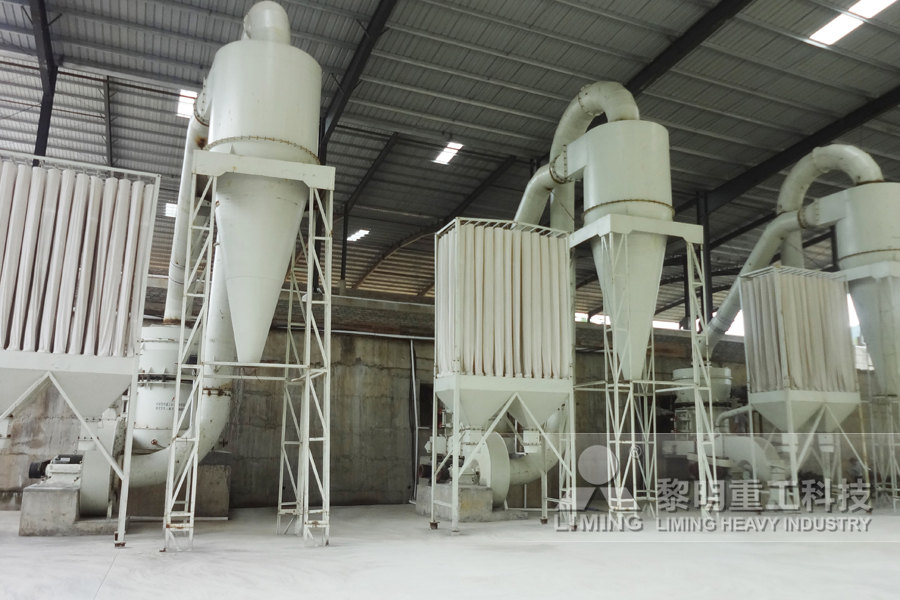
Powder Metallurgy: A Comprehensive Guide for Beginners
2023年9月5日 Powder metallurgy is a manufacturing process that involves using metal powder, or a mixture of metal powder and nonmetal powder, as a raw material The powder is then formed and sintered to produce a range of metal materials, composite materials, and various types of articles2022年9月12日 Because baking powder only requires moisture to react, exposure to ambient air can cause a slow loss of potency over time To test your baking powder, simply place a small amount in a dish and add water What Is Baking Powder? The Spruce Eats2023年11月5日 It is designed to be sturdy and has a wide, flat base to provide stability while grinding and mixing substances The inside of the mortar is roughtextured, which helps in the grinding process by providing better friction What Is A Mortar And Pestle Used For In Science?2023年11月20日 Powdered foods are easy to store and transport, with a longer shelf life that minimizes potential waste, contributing to sustainable development Each food category has a unique composition, responsible for its chemical Powdered Foods: Structure, Processing, and
.jpg)
An overview of advanced cocoa processing machinery
Cocoa processing machines have several applications in the chocolate industry, including: Production of chocolate: The cocoa processing machines are used to produce highquality chocolates of different flavors, shapes, and sizes Production of cocoa Liquor: The cocoa processing machines extract cocoa butter from the cocoa paste, leaving behind the cocoa Table 2: Energy and cost calculations by unit operation with a higher powder factor Operation Feed size Product size Work input Energy cost cm cm kwh/ton $/ton 30 27 119 Explosives ∞ 30 102 135 009 Primary crushing 102 191 428 030 Secondary crushing 191 0053 1355 949 Grinding 1438 1107 Totals In the example, the required work input has decreased by 30%, The Effects of Blasting on Crushing and Grinding Efficiency and 2023年8月24日 Overall, crushing plays a pivotal role in the beneficiation process by preparing the raw material for subsequent processing steps, enhancing mineral liberation, and facilitating the extraction and What is the role of crushing in the beneficiation process?2018年10月24日 Granulation is a sizeenlargement process by which small particles are bonded, by means of various techniques, in coherent and stable masses (granules), in which the original particles are still identifiable In wet granulation processes, the powder particles are aggregated through the use of a liquid phase called binder The main purposes of size Inside the Phenomenological Aspects of Wet Granulation: Role of Process
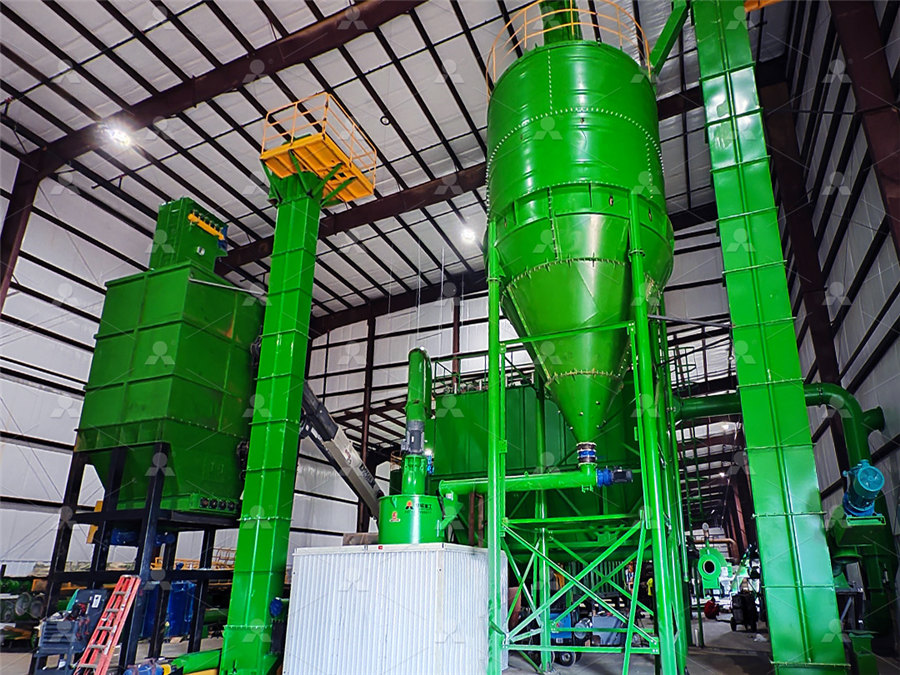
Making Metal Powder MPIF
The first step in the overall powder metallurgy (PM) process is making metal powders There are four main processes used in powder production: solidstate Further processing—washing, drying, reducing, annealing, and crushing—is often required, ultimately yielding highpurity and highdensity powders Copper is the primary metal When most people think of the metalmaking process, they picture a stream of molten metal pouring into a mold it makes a nice visual for films and commercialsBut when you consider making parts with powder metal, it may be a little harder to picture the process or why one would bother with powder metal in the first placeHow Metal Powder Is Made: Step 1 of the Powder Metallurgy2023年2月15日 Talc powder processing: 1 Coarse crushing: First, the talc ore is evenly sent to a jaw crusher through a vibrating feeder for coarse crushing; 2 Drying: Then the crushed ore is sent to a dryer through a bucket elevator for dying; 3 Further crushing: After drying, talc ore is sent to a hammer crusher for medium and fine crushing;How to Process Talc (the Softest Mineral)? FTM Machinery2024年2月29日 While white chocolate landed on the "best chocolate" list of only about 11% of Americans in a 2021 YouGov poll, it still has many fansIt's sometimes considered a "lesser than" type of chocolate The Important Role Of Milk Powder In The Chocolate

SIZE REDUCTION BY CRUSHING METHODS
2017年3月4日 capacity in primary crushing, increasing the total c apacity in the mining crushing process These crushers have a large feed opening and a groov ed mantle, making them suitable for cr ushing largeThe process of enriching flour restores its nutritive value by replacing nutrients lost during milling in amounts similar to those lost Almost 95 percent of the white flour in the United States is enriched with iron and four of the B vitamins: The Milling Process Grain Foods Foundation2024年1月1日 Granulation is a process that is wellknown and widely used in various industries This is primarily used when bulk material in the form of a fine powder is considered difficult to treat and process [1]The process is designed to convert fine powders into granular materials with controlled physical properties, ie a specific shape (granule size) and a specific bulk densityPowder agglomeration processes of bulk materials – A state of the measure of homogeneity can be accomplished with a process that creates large size reduction (crushing) where other samples for other processes will require reduction to fine particles (milling) Smaller particles and homogeneous materials are most often needed for many further laboratory sample preparation techniquesPrinciples of Sample Preparation by Grinding or Comminution
.jpg)
Mineral Processing Equipment for Mining Industry
2024年8月7日 After crushing, grinding refines ore into a fine powder to liberate valuable minerals Key types include Ball Mills, which grind ore using steel balls in a rotating cylinder; Rod Mills, which use long rods for a coarser grind; and SAG Mills, which combine crushing and grinding for efficient processing of large volumes of hard materialsThis paper examines the role blasting plays in optimum crushing and grinding with the emphasis on energy reduction The role of different blasting energy input on fragmentation is studied, and related to needs at the plant The effect of different feed sizes on energy consumption in crushing and grinding is studiedThe Effects of Blasting on Crushing and Grinding Efficiency and They are cohesive and do not flow well Granulation leads to larger more homogenous particles with better flow characteristics, improving the tablet making process Compacted granules occupy less volume/unit weight compared with powder and is easier to store and ship The granulation process can modify or improve the drug release profileThe Mechanism Of Granulation Formation And Methods2023年6月3日 Granulation is the main manufacturing process for the they are passed through roller powder compactors for compaction This results in the formation of slugs Slugs are the rough form of tablets, usually quite large in size Milling or Crushing: The slugs are then milled or crushed until the required granule size Granulation Process in Pharmaceutical Manufacturing
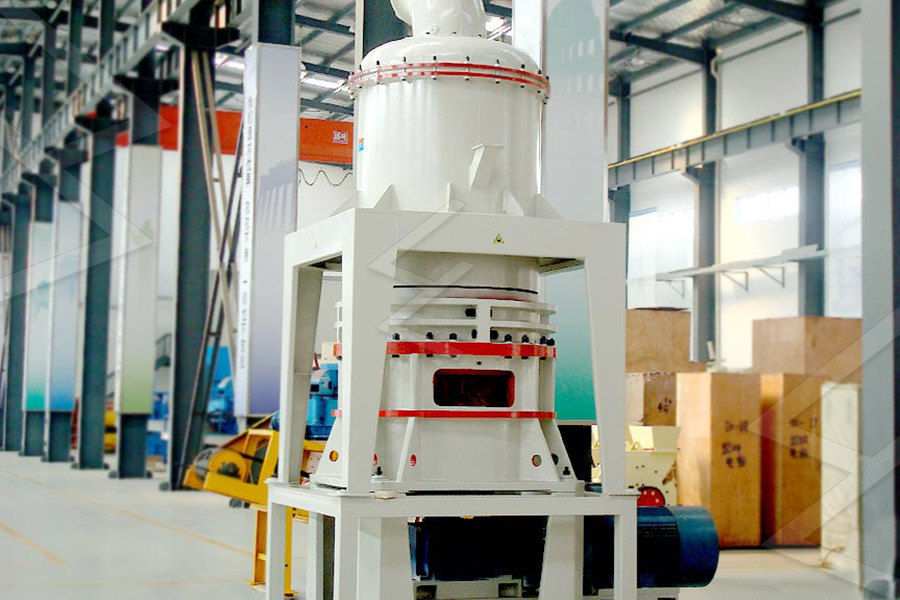
A Review of the Grinding Media in Ball Mills for Mineral Processing
2023年10月27日 The ball mill is a rotating cylindrical vessel with grinding media inside, which is responsible for breaking the ore particles Grinding media play an important role in the comminution of mineral ores in these mills This work reviews the application of balls in mineral processing as a function of the materials used to manufacture them and the mass loss, as