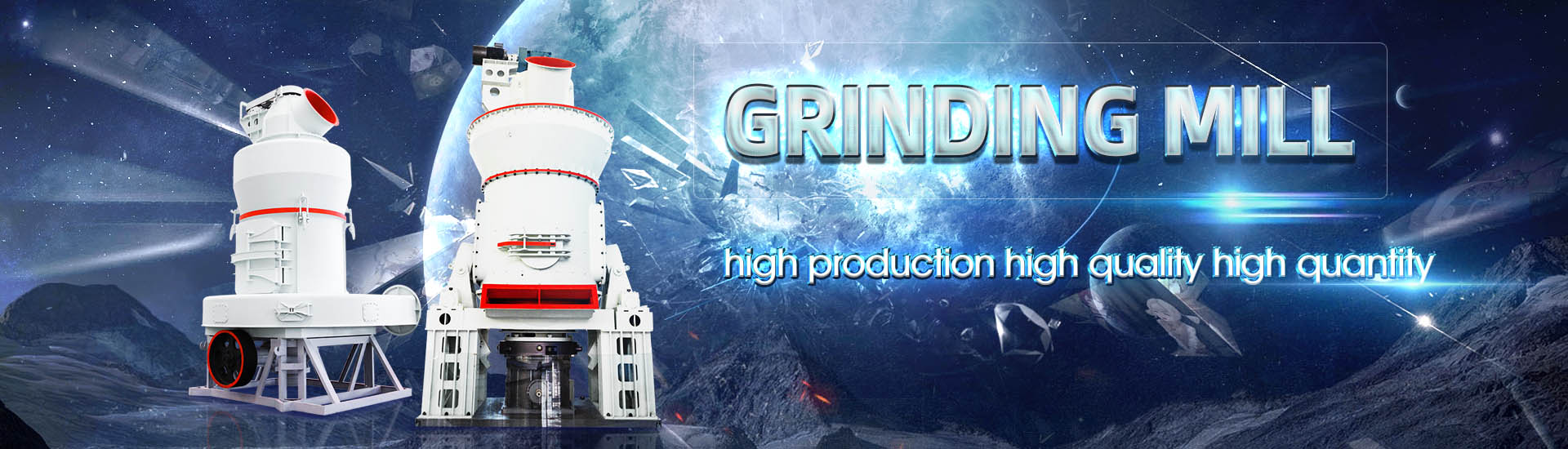
Aluminum ash, overhaul slag, aluminum electrolyte dry grinding equipment
.jpg)
Research Progress of Electrolytic Aluminum Overhaul Slag Disposal
2023年4月25日 This article analyzes and summarizes the composition and hazards of the overhaul slag and the current development status of domestic and international electrolytic Coal gangue is a byproduct of the production of coalassociated minerals, Review of Research on the Pr2023年8月1日 The dissolution behaviors of overhaul slag were fitted by a mass transfer model to obtain the dissolution parameters including dissolution capacity and dissolution rate This work Dissolution behavior of overhaul slag from aluminum reduction 2024年2月1日 The electrolytic aluminum industry generates a large amount lithium (Li)containing electrolytic aluminum slag (EAS) annually, and this can result in severe Efficient lithium recovery from electrolytic aluminum slag via an
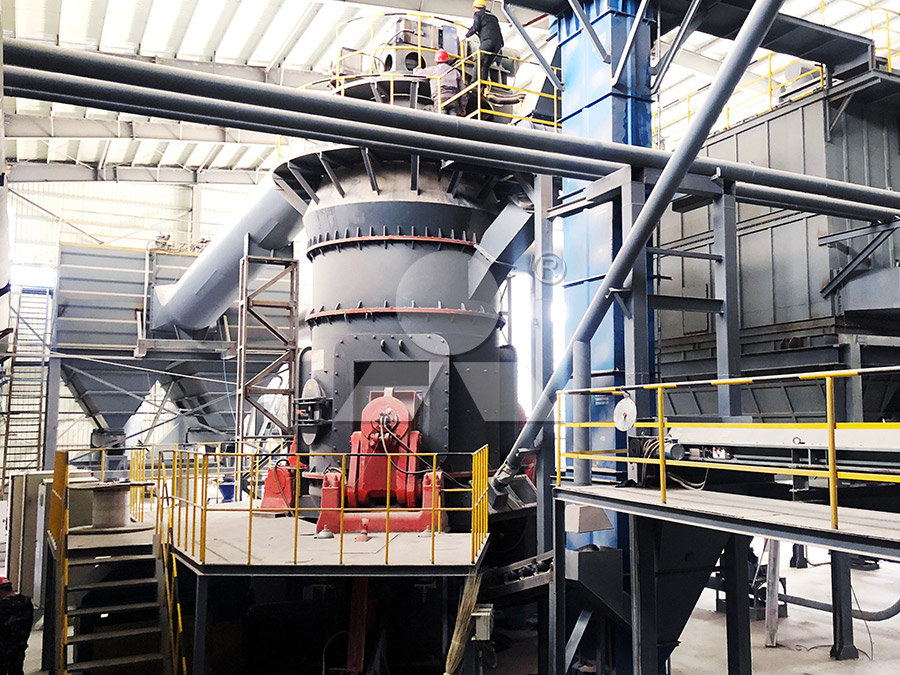
Recycling and Utilization of the Electrolytic Aluminium Ash and Slag
Aluminium ash and slag are produced from molten slag cooling in the electrolytic aluminium production process,the recycling and utilization of the electrolytic aluminium ash and slag is 2024年2月1日 In this paper, an innovative process of sulfuric acid roasting and water leaching is proposed, which can efficiently and environmentally recover F, Al and Li from overhaul slag A novel approach for extracting lithium from overhaul slag by low 2023年9月1日 This study employed hydrometallurgical processes to selectively leach lithium from Licontaining aluminum electrolyte slag, using sodium carbonate solution as the leaching Clean Process for Selective Recovery of Lithium Carbonate from 2024年5月23日 Here, we review carbonrich solid wastes with focus on sources and hazards, detoxification, separation, recovery, recycling and disposal Treatment techniques include The recycling of carbonrich solid wastes from aluminum
.jpg)
Cleaner Process for the Selective Extraction of Lithium from Spent
2024年7月24日 The lithium was selectively recovered and enriched from spent aluminum electrolyte slag by using calcium salt roasting transformation followed by HBL121solvent 2023年4月25日 This article analyzes and summarizes the composition and hazards of the overhaul slag and the current development status of domestic and international electrolytic 电解铝大修渣处置研究进展With the rapid development of aluminium smelting industry in China, millions of tons of hazardous wastes such as carbon slag, overhaul slag and aluminum ash are generated every yearPresent situation of production, utilization and disposal of 2023年10月1日 The main components of waste aluminum cryolite electrolyte are cryolite (Na 3 AlF 6), potassium cryolite (K 2 NaAlF 6), lithium cryolite (Na 2 LiAlF 6), fluorite (CaF 2), and approximately 2% carbon black (Wang et al, 2019)The main treatment methods of waste aluminum cryolite electrolyte can be divided into two categories: combined thermalwet Efficient extraction and recovery of lithium from waste aluminum
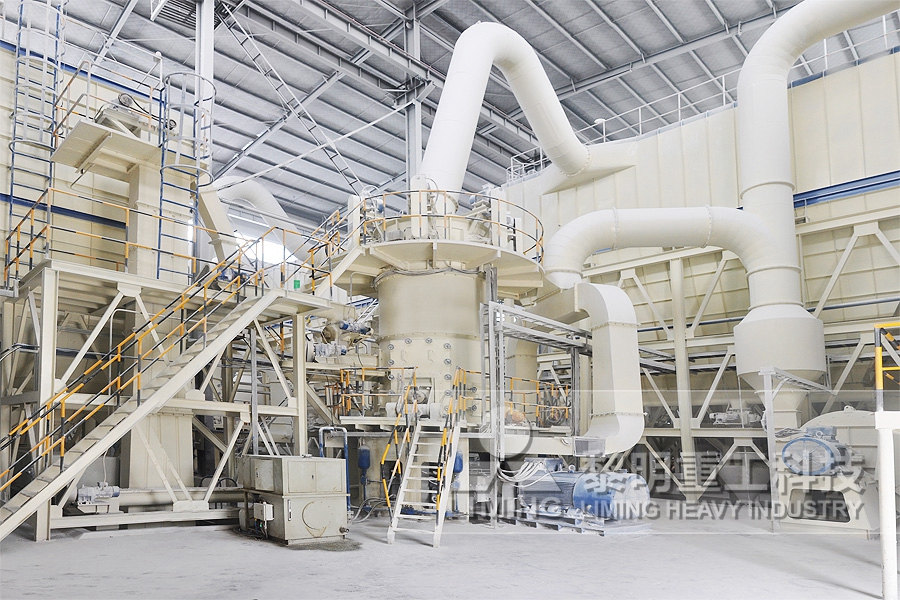
Stepwise extraction of lithium and potassium and recovery of
2024年6月29日 Aluminum electrolyte is a necessity for aluminum reduction cells; however, its stock is rising every year due to several factors, resulting in the accumulation of solid waste Currently, it has become a favorable material for the resources of lithium, potassium, and fluoride In this study, the calcification roasting–twostage leaching process was introduced to extract The main components of aluminum ash include single aluminum, aluminum oxide (Al 2 O 3), aluminum nitride (AlN), aluminum carbide (Al 4 C 3), fluoride and chlorinated salts, silicon, iron and other oxide (Kang et al 2022) Aluminum ash slag can be divided into primary aluminum ash and secondary aluminum ash accordingAssessing Environmental Impact of Aluminum Ash Disposal in 2021年6月16日 Aluminum and aluminum alloys are among the most used metals in fabrication,construction, and in the creation of good all around you It is such a useful and versatile metal, but there are some special considerations you need to make when working with it We have put together this expert guide to fabricating, grinding, and finishing aluminum to Ultimate Guide – Aluminum Fabrication, Grinding, and Finishing 2023年9月1日 Lithium (Li)bearing aluminum electrolyte slag is an inevitable byproduct of the aluminum industry, and improper disposal or stacking it may lead to potential environmental hazards This study employed hydrometallurgical processes to selectively leach lithium from Licontaining aluminum electrolyte slag, using sodium carbonate solution as the leaching agent Clean Process for Selective Recovery of Lithium Carbonate from
.jpg)
A novel approach for lithium recovery from waste lithium
2021年10月1日 To recover valuable elements such as lithium from waste aluminum electrolyte, Wu et al (2021) mixed Na 2 CO 3 with waste aluminum electrolyte and roasted them at 650 • C for 25 h, and Na 2 Coal fly ash (CFA), an industrial byproduct of hightemperature combustion of coal in coalfired power plants, is one of the most complex and largest amounts of industrial solid wastes generated in China It is widely recognized that CFA should be considered as a potential alumina resource to substitute bauxite In this review, the features of highalumina fly ash and aluminum recovery Aluminum extraction technologies from high aluminum fly ash De GruyterDownload Citation On Aug 1, 2023, Jianping Yang and others published Dissolution behavior of overhaul slag from aluminum reduction cell in a cryolitebased molten salt system Find, read and Dissolution behavior of overhaul slag from aluminum reduction 2018年10月1日 In the secondary aluminum industry (aluminum scrap recovery), about 200 kg of aluminum is produced per each ton of secondary aluminum (Seng et al, 2006) By 2020, annual global demand for aluminum will reach to about 97 million tons and almost 32% of which that equals to 31 million tons is expected to be supplied from scrap recycling ( Tsakiridis et al, 2013 )Hazardous aluminum dross characterization and recycling
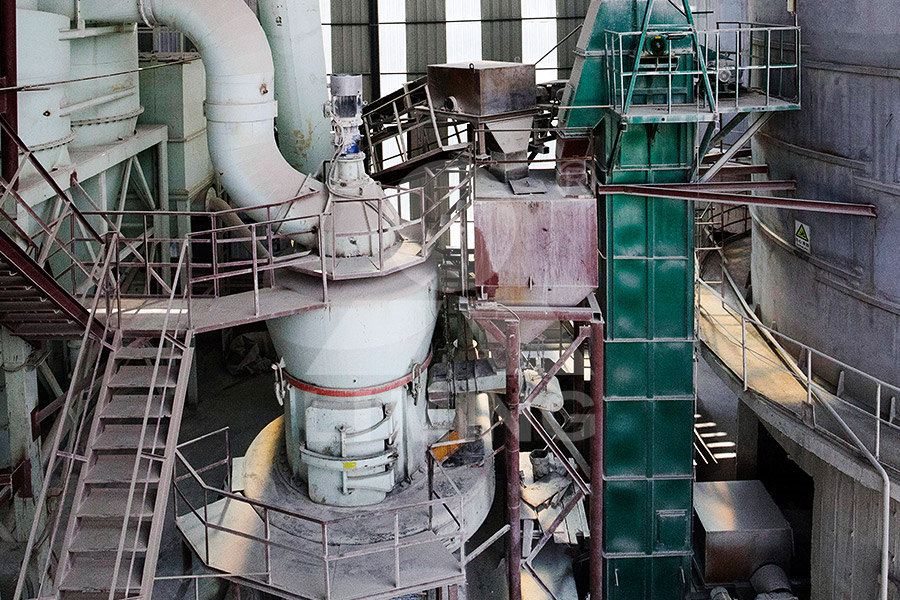
A novel approach for ultrasonic assisted organic acid leaching of
2023年10月1日 Currently, the green resource utilization in the aluminum electrolysis industry mainly focuses on the solid waste treatment of aluminum electrolysis tank overhaul slag, the resource utilization of waste cathodes, and the recovery of electrolytic tank waste heat There are few reports on lithium recovery from waste aluminum electrolytes [16,17]2024年6月4日 The main components of aluminum ash include single aluminum, aluminum oxide (Al 2 O 3), aluminum nitride (AlN), aluminum carbide (Al 4 C 3), fluoride and chlorinated salts, silicon, iron and other oxide (Kang et al 2022) Aluminum ash slag can be divided into primary aluminum ash and secondary aluminum ash according to the different degrees of Assessing Environmental Impact of Aluminum Ash Disposal in Ash Frying Machine, Hot Aluminum Ash Separator 7001300, Metal Aluminum Slag Separation Equipment, Ash Rubbing Machine, US $ 11500 16500 / Set, Guangdong, China, Lvyuan, NewSource from Foshan Lvyuan Innovation Trade Co, Ltd on AlibabaAsh Frying Machine, Hot Aluminum Ash Separator 7001300, Metal Aluminum 2024年2月1日 Overhaul slag, as one of the main hazardous solid wastes generated in the electrolytic aluminum, has high research value [12]The electrolytic cell lining is eroded by continuous chemical corrosion of hightemperature molten metal and salt, resulting in expansion and peeling off, leading to low production efficiency and degradation of performance [13]A novel approach for extracting lithium from overhaul slag by low
.jpg)
Efficient lithium recovery from electrolytic aluminum slag via an
2024年1月1日 Semantic Scholar extracted view of "Efficient lithium recovery from electrolytic aluminum slag via an environmentally friendly process: Leaching behavior and Green and efficient separation of fluorine from spent aluminum electrolyte by aluminum sulfate solution: Leaching behavior and mechanism Lingqi Meng Tianxiang Hao +5 2020年8月1日 1 Introduction Nowadays, coal combustion can meet more than 70% of the total energy demand in China Even by 2050, coal combustion can still meet about 50% of the total energy demand [1]Zhundong coalfield, located in Xinjiang province, is the largest integrated coalfield with a coal reserve of 390Gt [2]This coalfield can be utilized for more than 100 years Evaluation of aluminum ash in alleviating the ash deposition of 2021年11月1日 Bahan baku pembuatan paving block yaitu semen, pasir, batu, dan air Semen portland adalah semen yang terbuat dari dari 60 % kapur, 25 % silika, dan 10 % aluminaThe Influence of Aluminum Slag Ash for Paving Block Production2022年1月10日 Selective comminution and grinding mechanisms of spent carbon anode from aluminum electrolysis using ball and rod mills January 2022 Physicochemical Problems of Mineral Processing 58(3):Selective comminution and grinding mechanisms of spent carbon
.jpg)
Novel process for the extraction of lithium carbonate from spent
2020年12月1日 The rapid development of the electrolytic aluminum industry in China and the increasing demand for aluminum products have led to the development of many lowgrade bauxite mines with an average Li 2 O content of at least 058% (Wang et al, 2013)Due to the use of this lowgrade bauxite in the electrolytic aluminum process, the content of lithium in the 2023年3月12日 Recovery of Carbon and Cryolite from Spent Carbon Anode Slag Using a Grinding Flotation Process Based on Mineralogical Characteristics(PDF) Recovery of Carbon and Cryolite from Spent Carbon Anode Slag 2023年3月12日 Aluminum has a variety of uses in the building, transportation, electric power, packaging, national security, and hightech industries due to its unique chemical and physical properties []Cryolitealumina molten salt electrolysis is mainly applied in modern industrial aluminum production [2,3]As the aluminum production process continues, a large amount of Recovery of Carbon and Cryolite from Spent Carbon Anode Slagaluminum, heat treatment or cold treatment processes are generally used to recover the 10% to 30% of metallic aluminum contained in the aluminum slag The secondary aluminum dross is accounting for approximately 70% to 90% of the aluminum slag, which the metal aluminum content remained is generally less than 5%Technical Report International Aluminium
.jpg)
Comprehensive performance study of aluminum ash and calcium
2022年12月12日 Based on the research on bulk solid waste contact molding technology by our team [49], the comprehensive performance of pressed bricks with different ratios of aluminum ash and calcium carbide slag was investigated, the ratios of aluminum ash and calcium carbide slag are 9:1 ∼ 1:9 and pure aluminum ash and calcium carbide slag, the pressing pressure is 300 2024年5月23日 16 Million metric tons of spent carbon electrodes modify carbonrich solid wastes from aluminum electrolysis are produced annually, threatening ecosystems by cyanide and fluoride pollution Here, we review carbonrich solid wastes with focus on sources and hazards, detoxification, separation, recovery, recycling and disposal Treatment techniques The recycling of carbonrich solid wastes from aluminum The process is to first remove iron from the secondary aluminum ash, and then transport it to the feeding port of the crushing, grinding and screening machine through the automatic conveyor, screen out the granular aluminum and fine ash, and automatically transport the fine ash to the silo on the top of the 10T high temperature calciner for use, and the granular aluminum enters the What Equipment Is Used To Process 120 Meshes Of Secondary Aluminum Ash 2020年2月14日 Download Citation Aluminum extraction technologies from high aluminum fly ash Coal fly ash (CFA), an industrial byproduct of hightemperature combustion of coal in coalfired power plants, is Aluminum extraction technologies from high aluminum fly ash
.jpg)
Cleaner Process for the Selective Extraction of Lithium from Spent
2024年7月24日 Spent aluminum electrolyte slag is a byproduct produced during the electrolysis of aluminum and contains elements such as F, Al, Na, and Li It is a toxic and harmful substance with a stable and complex structure As a consequence of fluorine pollution and low lithium recovery efficiency in the traditional hydro metallurgy process, a novel cleaner production 2023年4月25日 甘肃冶金, 2017, 39(4):8689 LIANG W Q Disposal and reuse plan of aluminum ash, carbon slag and overhaul slag[J] Gansu Metallurgy, 2017, 39 废旧阴极中的碳和电解质[J] 轻金属, 2013(5):2327 LI N, LI R X, XIE G, et al Separation of carbon and electrolyte in waste cathodes of aluminum electrolysis by 电解铝大修渣处置研究进展2023年10月1日 Crush and grind the waste aluminum electrolyte fine Fig 1 (b) shows the particle size analysis, and the results show that the average particle size of the treated aluminum electrolyte powder is 4528 μm Fig 1 (c) shows the XRD diagram, which shows that the waste aluminum electrolyte mainly comprises Na 3 AlF 6, CaF 2, LiF, K 2 NaAlF 6, and A novel approach for ultrasonic assisted organic acid leaching of Harmless aluminum ash hazardous waste disposal program: through acid leaching, alkaline leaching, washing, etc, the nitride, fluoride, salt and other impurities in the secondary aluminum ash are removed to obtain harmless aluminum ash before safe filling Buried Recycling process: After removing toxic and harmful substances, the secondary aluminum ash is processed by Aluminum Ash Processing Aluminum Ash Recovery Aluminum Ash
.jpg)
Efficient lithium recovery from electrolytic aluminum slag via an
2024年2月1日 Aluminum metal was produced using the cryolitealumina molten salt electrolysis method (Ishak et al, 2017) A large amount electrolytic aluminum slag (EAS) is generated during the electrolysis process, as the falling of carbon particles on the anode into the electrolysis cells and the accumulation of lithium fluorine result in energy consumption and electrolyte scrapping On August 2nd, China Nonferrous Metals Industry Association organized an expert meeting on scientific and technological achievements in Kunming, Yunnan Province, and completed the "electrolytic aluminum overhaul slag" jointly Electrolytic aluminum overhaul slag harmless 2021年7月30日 Sintering Aluminum dross and coal fly ash were used to prepare mullitebased ceramics through sintering and acid leaching methods At a sintering temperature of 1500 C, high mulliteA Review of Secondary Aluminum Production and 2021年7月30日 The aluminum metal and molten salt flux are tapped after the process, where the cooled flux along with the mixture of nonmetallic components is called salt slag or salt cake54 Salt slag contains 5–7 wt% residual aluminum metal, 15–30 wt% aluminum oxide, 30–55 wt% sodium chloride, and 15–30 wt% potassium chloride and, depending upon the A Review of Secondary Aluminum Production and Its Byproducts
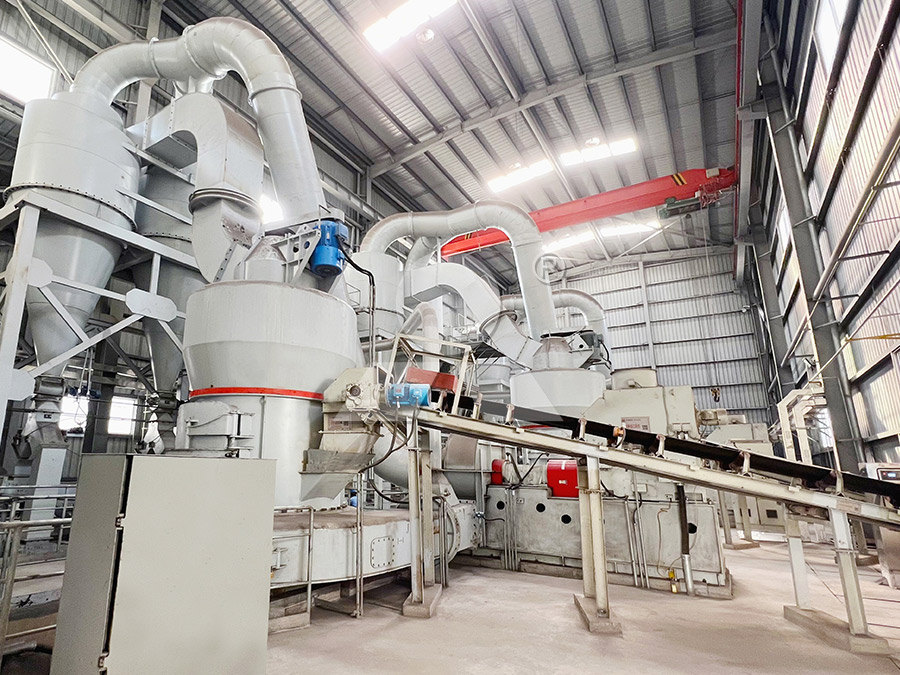
(PDF) The Effect of Secondary Aluminum Ash on the Properties of
2023年7月27日 The addition of secondary aluminum ash can decrease the flexural and compressive strengths of RPC cured for 1 day by the decreasing rates of 0~187% and 0~193%2019年2月26日 Aluminum ash is an industrial waste residue produced during alumina electrolysis and aluminum processing and casting In the experiment, alumina powder with a purity of 9897% was prepared by (PDF) Preparation of Alumina from Aluminum Ash byAluminum electrolytic capacitors are made of two aluminum foils and a paper soaked in electrolyte The anode aluminum foil is anodized to form a very thin oxide layer on one side and the unanodized aluminum acts as cathode; the anode and cathode are separated by paper soaked in electrolyte, as shown in Fig 810A and BThe oxide layer serves as a dielectric and Aluminum Electrolytic Capacitor ScienceDirect Topics2022年10月10日 Grinding flotation performance is significantly affected by grinding parameters such as wet or dry conditions, grinding time, and grinding devices Compared to dryground particles, wetground particles had more irregular shape factors and smoother surfaces, resulting in shorter induction times and higher floatation recovery rates ( Bu et al, 2019 )Recovery of carbon and cryolite from spent carbon anode slag of
.jpg)
A novel approach for lithium recovery from waste lithium
2021年10月1日 A novel approach for lithium recovery from waste lithiumcontaining aluminum electrolyte by a roastingleaching process Author links open overlay panel Shaohua Wu a, Wenju Tao a The experimental results show that the best ratio of aluminum ash and calcium carbide slag is 1:9, the best pressure is 300mpa, the best curing time 2016年10月28日 The grinding efficiency of steel slag was obviously increased and the particle characteristics were improved after using grinding aids (GA), especially the particle proportions of 332 Mm were (PDF) Comparison of Grinding Characteristics of Converter Steel Slag 2020年12月1日 A hydrometallurgical process was developed to extract lithium from a spent lithiumcontaining aluminum electrolyte, reduce the stacking of spent aluminum electrolyte, and recover the valuable elements In this study, we extracted lithium from an electrolyte using the following three steps: 1) leaching with HNO 3 − Al(NO 3) 3, 2) neutralizing the leachate Novel process for the extraction of lithium carbonate from spent