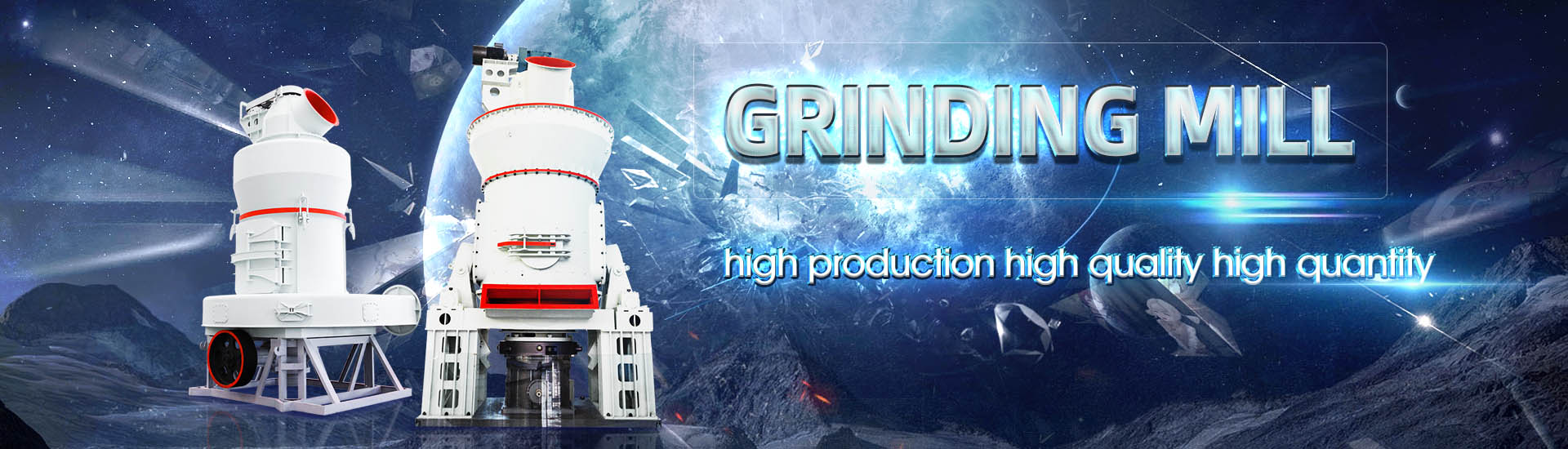
Cement grinding fineness running coarse
.jpg)
Cement Grinding Cement Plant Optimization
Closed circuit ball mill with two compartments for coarse and fine grinding are generally found in cement plants for cement grinding Compartments (filled with grinding media) are divided by a double diaphragm with flow control to utilize maximum mill length for effective grindingClosedcircuit grinding is used to remove fines from the milling system, so that the mill can function with a feed that is optimally coarse for its grinding action In early grinding, both for cement and rawmix, sieves were originally used as the Cement Kilns: Size Reduction and GrindingThe cement industry uses a wide range of different systems in raw material, coal, and cement grinding While new plants mainly focus on highly energy‑efficient systems, using roller Thomas Holzinger, Holzinger Consulting, grinding system In all cases, the best clinker is the one that has a vintage's fineness close to 1315% for the refusal of 100 µm This latter gives a wellformed clinker nodules, well homogenized phases Study Of The Clinker Characteristics And Grindability During
.jpg)
OPTIMIZATION OF CEMENT GRINDING OPERATION IN BALL MILLS
Cement ball mills typically have two grinding chambers The first chamber is filled with larger diameter grinding media andlined with lifting liners The first chamber coarsegrinds the feed 2021年2月3日 This study aims to leverage recent advances in deep learning techniques to propose an FCDNN model to predict the upcoming coarse return in a cement grinding process In the next section, we describe a realworld Coarse Return Prediction in a Cement Industry’s Closed In this study, the performance of cements prepared by blending a coarse ASTM C150 type I/II and a fine type III cement obtained from the same clinker in three different proportions is examinedBlending different fineness cements to engineer the properties of 2015年7月7日 Contents 51 Cement milling 52 Fineness of cement Selected references Further readingGrinding and fineness of cement Portland Cement
.jpg)
Resistance to Grinding and Cement Paste Performance of Blends
2021年4月19日 Estimating resistance to grinding of cement blends from the mixture’s composition would aid in developing optimization models to reduce energy consumption for 2017年5月19日 Grinding is an essential operation in cement production given that it permits to obtain fine powder which reacts quickly with water, sets in few hours and hardens over a period of weeks i Overview of cement grinding: fundamentals, Ball race mill (Petersmill of the Claudius Peters Joint Stock Company, Hamburg, Germany) The cement industry employs the Petersmill (pre viously called FullerPetersmill) mostly for coal grinding It is a few years now that the shockproof Roller mills INFINITY FOR CEMENT EQUIPMENTFine grinding lessens this effect, and early cements had to be stored for several months to give the calcium oxide time to hydrate before it was fit for sale From 1885 onward, the development of specialized steel led to the development of new forms of grinding equipment, and from this point onward, the typical fineness of cement began a steady Cement mill Wikipedia
.jpg)
Intensifying the cement grinding process e3sconferences
The data obtained from a study of cement clinker grinding kinetics shows the dependence of cement specific surface area on grinding time (Table 1) Table 1 Cement clinker grinding characteristics № Material Specific surface area, cm2/g Grinding time, min 40 50 60 70 1 Clinker (1) 2447 2834 3070 3200vii NOMENCLATURE ASTM American Society for Testing and Materials B Flow rate of a material stream, mass per time unit Blaine Specific surface area value as per ASTM C 204, m2/kg or cm2/g C Matrix of classificationIMPROVED CEMENT QUALITY AND GRINDING EFFICIENCY BY would be a length of 135 m and a diameter of 25 m, with a speed of approximately 20 revolutions per minute Such a mill would normally have a load of approximately 90 tons of grinding media, graduated from 90 mm to 60 mm in the first chamber, 50 mm to 15 mm in the second chamber and 15 mm down in the final chamberAn Introduction to Clinker Grinding and Cement StorageFineness Modulus of Cement Result: The standard value of the fineness of cement should have a fineness of less than 10 % or fineness of cement should not be more than 10% as per IS Recommendations You Might Also Like Consistency Test Of Cement Test, Calculation Result; Initial And Final Setting Time Of Cement Test, Procedure ResultFineness of Cement: Definition, Importance, and How to Test It
.jpg)
Fineness Test of Cement by Sieve Analysis IS: 4031 Part1
2020年3月27日 This post is written for civil engineering students and laboratory engineers The reference IS 4031 (Part1): 1996 is used in this post This post covers the definitions, apparatus list, IS code, test procedure, observation table, calculation sheet, formula and expression of result of fineness test of cement by sieve analysis as per IS 4031 Part1 (1996)2022年8月10日 Grinding might be an individual step in the cement production line but it is a crucial one, given the energy consumption and impact on the quality of output that it gives ICR explores how grinding methods have evolved with the help of technology and with the use of modernage grinding aids Grinding in the cement []Grinding: Smarter Solutions Indian Cement Review2023年8月21日 Tushar Khandhadia, General Manager – Production, Udaipur Cement Works, discusses the role of grinding in ensuring optimised cement production and a high quality end product How does the grinding process contribute to the production of highquality cement?The quality of cement depends on its reactive properties and particle size grinding helps to reduce Grinding process is a critical stage in cement production2024年1月15日 The fineness of cement is defined as the particle size distribution of the cement particlesLearn all about Fineness of cement and the significance and measurement The efficiency and control of the grinding Fineness of CementDefinition, Significance,
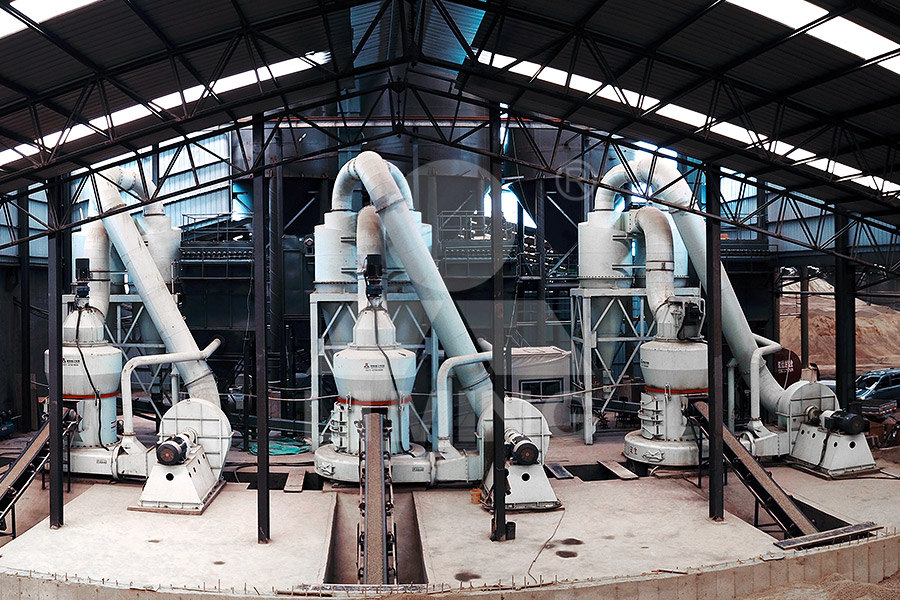
BALL MILL FLSmidth Cement
FLS Cement flsmidthcement 3 Ball mill for cement grinding Cement grinding is a crucial stage of the flow sheet, where both cement quality and process efficiency are decided Achieving the required fineness with maximum efficiency is down to the design of the ball mill and how well it runs An inefficient systemGrinding takes place mainly because of the impact forces Cataract movement is used for coarse grinding in the (poor cement setting, decrease of performance, rough running), it is recommendable in such cases to keep the grinding aids Process Training Ball Mill INFINITY FOR CEMENT 2020年9月15日 Predictive Controller Design for a Cement Ball Mill Grinding Process under Larger Heterogeneities in Clinker Using StateSpace Models September 2020 DOI: 103390/designsPredictive Controller Design for a Cement Ball Mill Grinding 2022年9月24日 In this study, the effect of cement fineness and its grain size distribution on compressive strength and waterreducing admixture demand for providing target flow value was investigated(PDF) EFFECT OF CEMENT FINENESS AND GRAIN SIZE
.jpg)
Study on the production of cements using a multistage grinding
Ultrafine grinding here refers to a material fineness beyond ~8000 cm²/g according to Blaine (mainly finer than 5 to 8 µm [1]) and will become more and more important due to rising demand for cements with very high fineness Each grinding step features at least one mill but can be equipped with various mills in order to meet the required High grinding efficiency For the structure, of the cement mill, we adopt the advanced obstructing equipment for internal powder, add the activated device to the fine grinding chamber, and there is the special grate plate at the end of the cement mill, which can reduce the size of the grinding medium, greatly improve the grinding efficiency, and achieve the purpose of high output and cement grinding Unitblended cements and fineness values have increased (the amount of coarse material retained on sieve increased) at constant grinding times Compressive strength values of mortarsPortland Limestone Cement Part I Preparation of Cementscoarse particles High pressure grinding rolls – main features • First application 1984 • Today worldwide more than 600 mills in operation • Throughput rates up to 1 300 t/h Slag grinding • Max cement fineness 4 800 cm²/g • Energy consumption 60 % compared to a ball millInnovation and optimisation in cement grinding
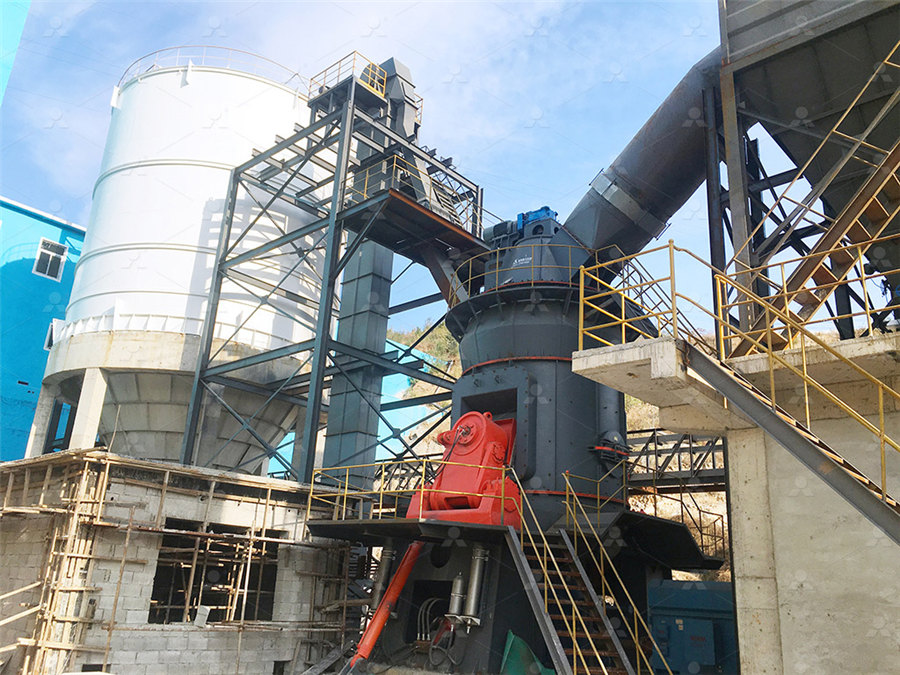
Everything you need to know about Crushers in Cement industry
This crushed product is further reduced by grinding to fineness below about 02 mm size, in which condition it is called raw meal and is ready for feeding to the kiln The capacity of the crusher, reduction ratio, hardness, fragment size, moisture content, plasticity and abrasiveness of the material are important factors affecting the choice of the size reduction machines and methods o Finished grinding may consume 25 – 50 kWh/t cement, depending on the feed material grindability, additives used, plant design especially the required cement fineness Cement grinding is the single biggest consumer of electricity Improvements in New Existing Cement Grinding 2021年7月1日 Stability in operation: Feeding material like fly ash, GGBS are fine in nature and they show a fineness below 3 mm hence where other grinding systems like vertical roller mills required water spray to form a grinding bed but in roller press when a premixing of fines with coarse material is made properly it can efficiently grind up to higher fineness [below 5 per cent Roller press:Efficient grinding solutions Indian Cement ReviewConcretes are designed to fulfil specific engineering requirements, commonly exemplified by slump, unit weight and compressive strength One source of untapped potential for varying engineering properties of hardened concrete is the variation of the cement particle size distribution In this study, the performance of cements prepared by blending a coarse ASTM Blending different fineness cements to engineer the properties of
.jpg)
Coarse Return Prediction in a Cement Industry’s Closed Grinding
2021年2月3日 In the cement grinding process, coarse return is one of the main parameters of the van Zyl, TL Predicting Particle Fineness in a Cement Mill In Proceedings of the 2020 IEEE 23rd InternationalFineness of cement describe about how much cement have fine and coarse particles,as above explanation rapid hardening cement and Portland pozzolana cement have more fine particle than ordinary Portland cement Fineness test for cement, its Test procedure, appartus,results importance Fineness of cement define as is property of cement that indicate particle size of Fineness test for cement, its Procedure ApparatusThis article examines the influence of cement fineness on the properties of cement paste and mortar Cement powder was obtained by grinding cement clinker from a cement plant in Saraburi province, Thailand and sieving it through a specified sieve mesh Gypsum was then added in a ratio of 5% by weight The resulting mixture was used toInfluence of cement fineness on the performance of cement mortar• The measurement and control of fineness and the different measures applied on cement factories • Separation theory • The concept of grindability and the effects of intergrinding materials of different grindability • Drying and evaporative cooling • The segmentation of grinding and milling systems Module 2 – Ball millsGrinding Milling Systems Course International Cement Review
.jpg)
Predictive Control of a Closed Grinding Circuit System in Cement
2017年10月12日 Cement industry is considered as a strategic industry all over the world (Shen et al, 2017) The operational cost of implementing manufacturing processes in this industry is so high that a few 2020年4月7日 However, the sieve test gives no information on the size of grains smaller than 45 μm (No 325 ASTM) sieve, and it is the finer particles that play the greatest part in the early hydration; For this reason, modern standards prescribe a test for fineness by determination of the specific surface of cement expressed as the total surface area in square metres per kilogramFineness of Cement Construction How2021年2月3日 In the cement grinding process, coarse return is one of the main parameters of the process, representing the product quality output fuzzy inference and adaptive neuro fuzzy inference techniques for online monitoring of cement Coarse Return Prediction in a Cement Industry’s Closed Grinding 2003年10月1日 The introduction of grinding aids (GA) started more than fifty years ago; it has as its ultimate objective decreasing the energy consumption to obtain a given fineness or flow of cementInfluence of grinding aids on cement hydration
.jpg)
The Cement Plant Operations Handbook International Cement
1 The basics of cement manufacture – 2 History of cement manufacture – 3 Portland cement in today’s world 2 Raw materials management system – 22 Concrete problems 16 1 Raw materials – 2 Raw mix – 3 Reserves – 4 Crushing – 5 Drying – 6 Preblending – 7 Storage and handling 3 Raw milling and blending 3Ball mills and grinding tools Cement ball mills are typically twochamber mills (Figure 2), where the first chamber has larger media with lifting liners installed, providing the coarse grinding stage, whereas, in the second chamber, medium and fine can then measure the material fineness evolution of nominated grain sizes, starting from BALL MILLS Ball mill optimisation Holzinger ConsultingFor fine grinding in open circuit, the F L Smidth Co, developed a grinding system consisting of two tube mills The principle of this grinding system, also called Minipebssystem, is shown in Fig 124 Pregrinding to a fineness of 2500 3000 Blaine is per formed in the coarse grinding millGrinding in closed circuit INFINITY FOR CEMENT EQUIPMENTcement and a coarse Type I/II cement obtained from the same clinker Practically, this would require that the readymix plant maintain two silos of cement, one for each finenessBlending Different Fineness Cements to Engineer the Properties
.jpg)
Blended Cement Grinding: Energy Intake and Fineness
2022年8月11日 Finished grinding may consume 2550 kWh/t cement, depending on the feed material grindability, additives used, plant design and especially the required cement fineness The grinding process absorbs more energy due to the losses attributable to heat generated during grinding, friction wear, sound noise and vibration2023年10月19日 Therefore, efficient grinding techniques and technologies are employed to minimize energy use and reduce production costs, contributing to the sustainability of the cement industry Types of Clinker Grinding Techniques used in cement manufacturing process Clinker grinders are an important part of the cement manufacturing processClinker Grinding Techniques in Cement Manufacturing JM Download scientific diagram Changes in the Blaine fineness of cements from the 1950s to the present day Regression lines are provided for the Type I survey and CCRL Type I or I/II data sets onlyChanges in the Blaine fineness of cements from the 1950s to the However, we can also take help from higher fineness of cement FINENESS OF CEMENT VERSUS COMPACTING FACTOR R2 = 09523 085 087 089 091 093 095 097 099 1000 1500 2000 2500 3000 3500 4000 FINENESS (cm2/g) COMPACTING FACTOR Figure 2 Fineness of Cement versus 3days Compressive Strength 3500 4000 4500 5000 5500 1000 2000 3000 Variation in Fineness of Portland Cement and its Effects on
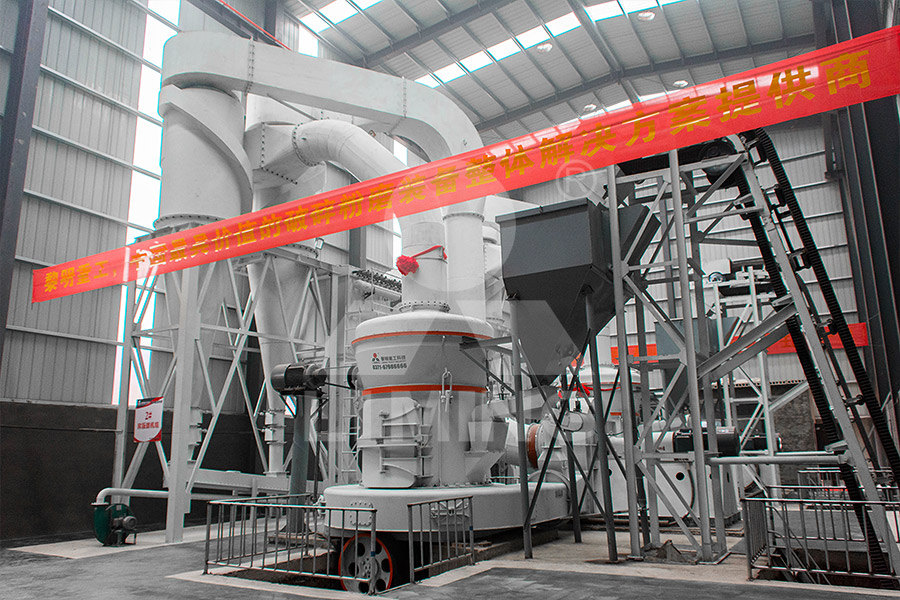
The influence of surfactants upon grinding and hardening of cement
2013年6月15日 The additive was dosed in three different ratios (0,03%, 005% and 01%), reported at the weight of cement subject to grinding Grinding fineness of the cements, expressed through Blaine specific