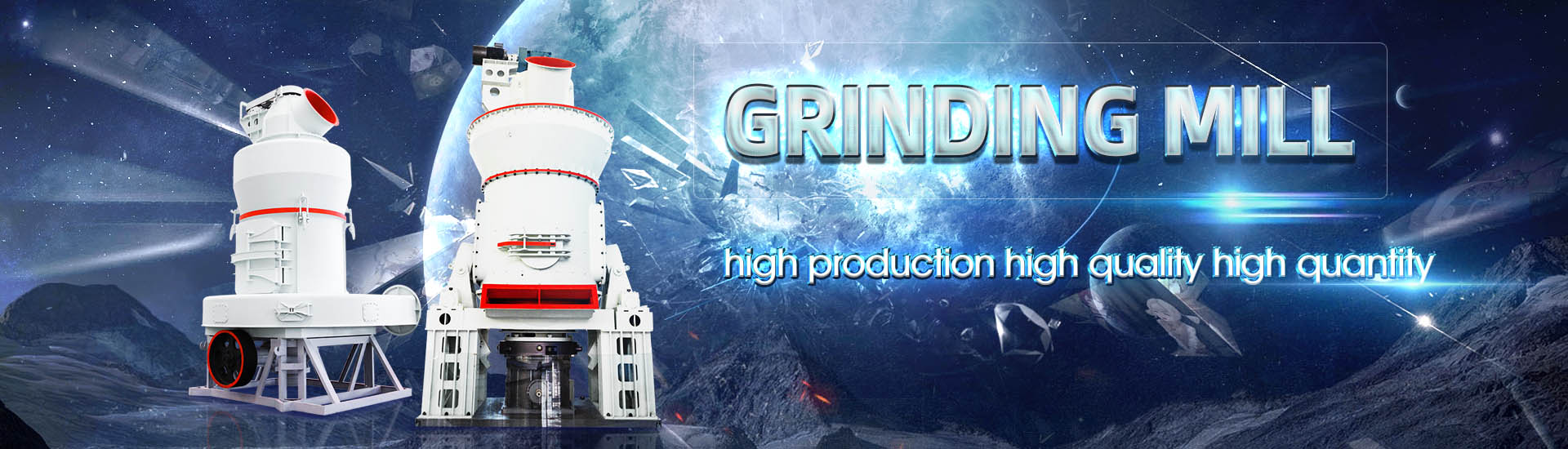
Cement clinker plant
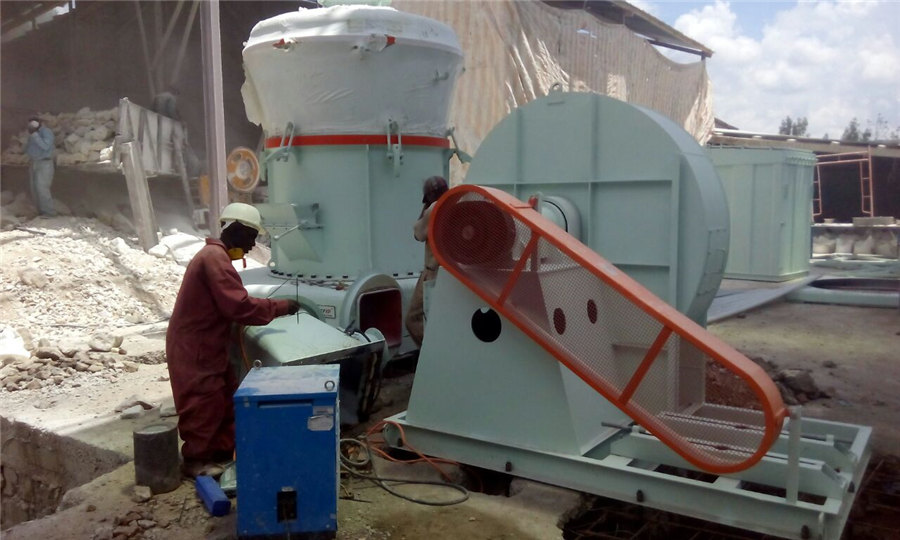
Cement clinker Wikipedia
Cement clinker is a solid material produced in the manufacture of portland cement as an intermediary product Clinker occurs as lumps or nodules, usually 3 millimetres (012 in) to 25 millimetres (098 in) in diameter It is produced by sintering (fusing together without melting to the point of liquefaction) 展开Emissions from manufacturing clinker – the main component of cement – result from chemical reactions and fuel combustion in the process Measures to reduce emissions include reduction of the clinkertocement ratio through the adoption Cement IEA International Energy AgencyClinker free lime (CaO f) should be as high as possible to avoid hard burning of clinker, but safely below value, inviting mortar expansion; normally, between Clinkerization Cement Plant OptimizationBased on reports from various studies, the reuse of sewage sludge as raw material for cement clinker production is feasibleCement Clinker Production an overview ScienceDirect Topics
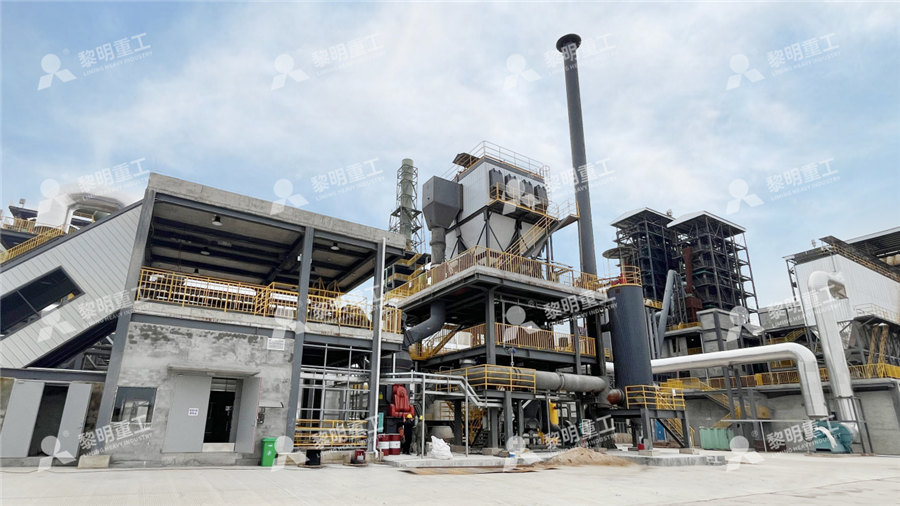
The Environmental Profile of Clinker, Cement, and
2022年3月6日 The systems studied for clinker and cement accounted for 628% of the cement used in Ecuador in 2019 The clinker, cement, and concrete systems have cradletogate approaches Technical system boundaries for What is clinker and why is the cement industry trying to use less clinker? Clinker is the main constituent of cement It is essentially a mix of limestone and other minerals thatCLINKER SUBSTITUTION IN THE CEMENT INDUSTRY CEMBUREAUNew ratebased model was developed and used to validate fullscale CAP simulations for cement plants Upcoming work: CAP optimization CEMCAP framework document: ready for use! Process characteristics of clinker and cement production SINTEFCement grinding is, therefore, a flexible and generally intermittent operation, with mills that have sufficient capacity to grind the clinker considerably faster than kilns produce This allows them to meet the maximum demands when necessary: An Introduction to Clinker Grinding and Cement Storage
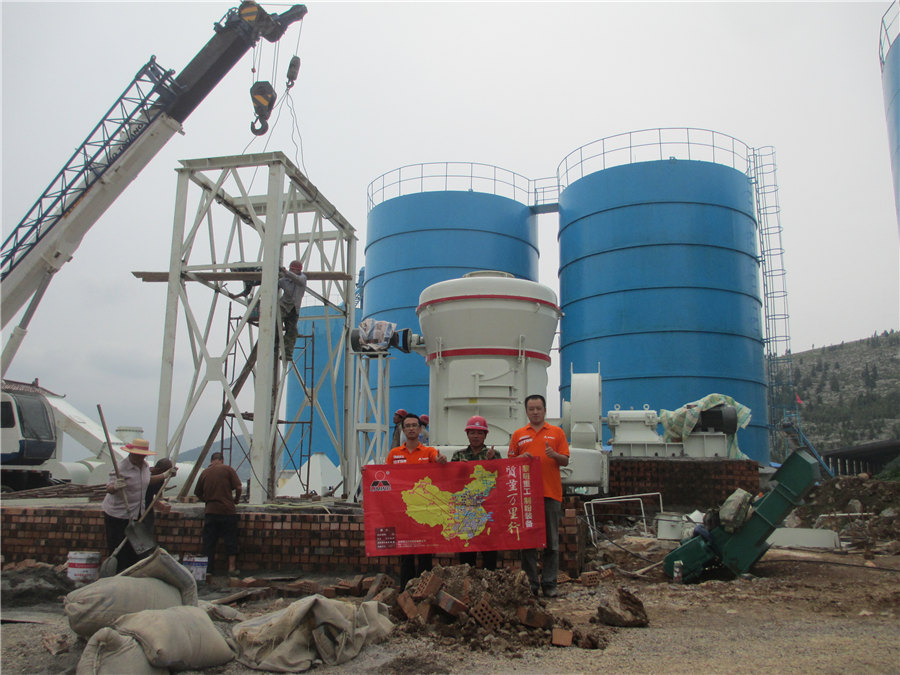
Cement Clinker Calcination in Cement Production
The cement clinker calcination is an important step in the cement production crushing mills, grinding mills, dust collector, etc We also offer cement plant design service, equipment installation and commissioning service and after Initially a part of Reliance Cement Company Pvt Ltd, the Mihar plant in Madhya Pradesh was acquired by MP Cement in 2016 It is one of the largest plants when it comes to manufacturing clinker and its fully automated robotic lab ensures List of MP Birla Cement Plants in IndiaClinker Grinding The cement clinker is ground as finished cement, in a vertical roller mill for cement or in ball mills similar to those normally used for grinding hard raw materials in dry and semidry processes However, the cement An Introduction to Clinker Grinding and Cement StorageProducing traditional cement clinker is an extremely energy and CO 2 intensive process In the EU, 90% of clinker is now made via the more energy efficient dry cement plant or used as a tailend technology; (iv) and direct separation technology, applied in combination with a zeroCO 2 Deep decarbonisation of industry: The cement sector Europa
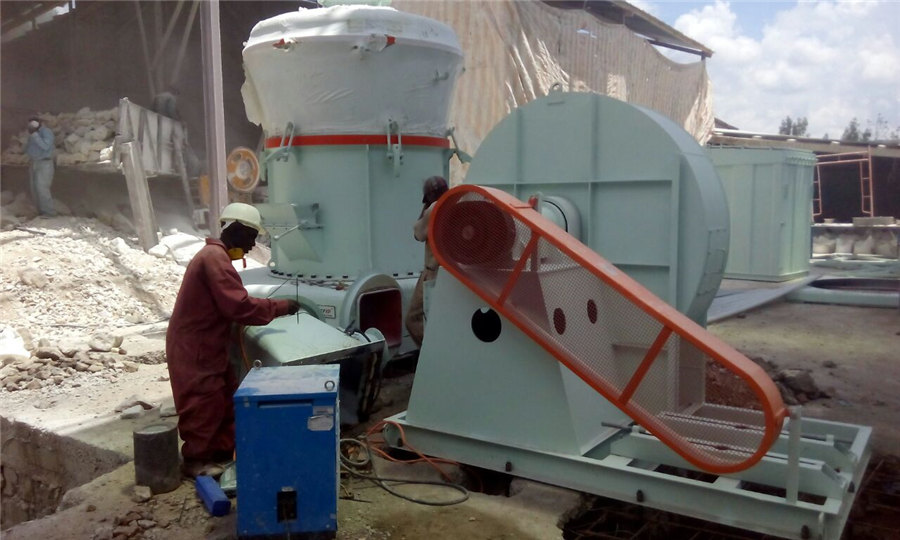
Cement IEA International Energy Agency
The global clinkertocement ratio 1 has increased at an annual average of 11% since 2015, from 066 increasing to 071 in 2022 This number hides significantly different regional trends China, despite having one of the lowest clinkertocement ratios globally, saw an increase from 057 in 2015 to 065 in 2022Cement Kiln In Cement Plant AGICO offers different types of cement kilns from 105000t/d with steady running, high efficiency and large output We adopt the most advanced calcination technology so that the production investment of clinker is small and the income is highClinker Production Clinker Manufacturing Cement Everything you need to know about clinker/cement Grinding if You read and understand this article , you will be ready to be a cement grinding area manager FEED AND FEED SYSTEM Feed Temperature Plants with satellite coolers have high clinker temperatures: eg Cumarebo, Oujda Exit satellite cooler 200250°C Exit grate cooler 100150°CEverything you need to know about clinker/cement GrindingThe grate cooler is a quenching type cement cooler apply for clinker production in the cement manufacturing plant AGICO CEMENT offers highefficiency grate cooler and other types of clinker cooler as you need, send inquiry now! Skip to Grate Cooler In Cement Plant Clinker Cooler, Cement Cooler
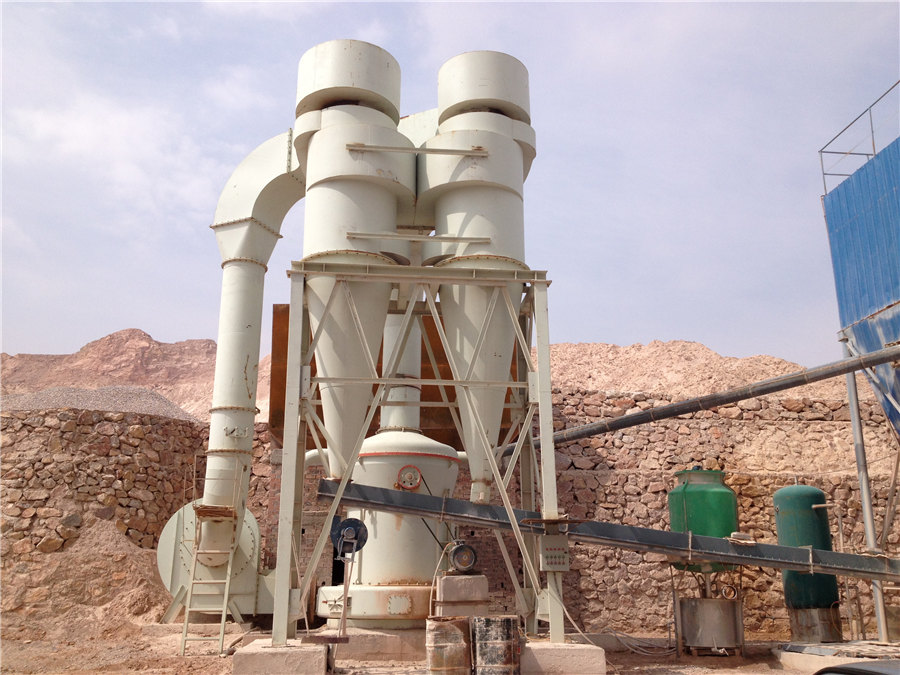
Cement Extraction, Processing, Manufacturing Britannica
2024年11月23日 Raw materials employed in the manufacture of cement are extracted by quarrying in the case of hard rocks such as limestones, slates, and some shales, with the aid of blasting when necessary Some deposits are mined by underground methods Softer rocks such as chalk and clay can be dug directly by excavators The excavated materials are transported AGICO CEMENT supplier rotary drum cooler in cement plant, grate cooler, and other clinker coolers for cement manufacturing High cooling performance and factory price, get your FREE quotation now! Skip to content +86 s about blog contact EN ES Menu Menu Home;Rotary Cooler Clinker Cooler In Cement Plant AGICO CEMENTCement grinding unit is also called the cement grinding plant dust collector, belt conveyor, bucket elevator, cement silo, powder concentrator, etc AGICO provides highquality clinker grinders and advanced cement grinding Cement Grinding Unit Clinker Grinder AGICO Cement2021年5月24日 Large clinker nodules (Figure 2) are difficult to cool, transport and grind into cement Clinker should ideally have a smaller average nodule size and a narrow nodule size range More uniformly sized clinker is more evenly distributed into the cooler and has more consistent bed porosity, which enables more stable cooler and kiln operationBetter and cheaper cement: Optimising the right clinker properties
.jpg)
Clinker Grinding Techniques in Cement Manufacturing
2023年10月19日 Clinker grinders are an important part of the cement manufacturing process They are used to grind clinker into a fine powder and are typically located at the end of the cooler in a cement plant Clinker is a nodular KOTA KINABALU, Feb 14 — A RM2 billion integrated clinker and cement plant in the interior district of Nabawan, the largest in the state, is expected to begin operations by the end of the year Borneo Cement Sabah Sdn Bhd general manager Michael Kinsuan said construction will begin after the Environmental Impact Study Sabah’s largest cement and clinker plant to be operational by AGICO CEMENT is a trusted cement plant manufacturer supplies precalciner, cement calciner as you need, high quality and EPC project, get your quote now! Skip to content +86 Precalciner, Calciner In Cement Plant, Cement Calciner AGICO CEMENTIt is sometimes misunderstood for an integrated cement plant which also manufactures the clinker The integrated plant process involves very high temperatures and the emission of high volumes of particulates and gaseous effluent This is not the case for a straightforward CGP as in the present proposed projectEVERYTHING YOU NEED TO KNOW ABOUT ESTABLISHING CEMENT GRINDING PLANT
.jpg)
The Cement Manufacturing Process Thermo Fisher Scientific
2023年12月20日 The result is called clinker, which are rounded nodules between 1mm and 25mm across The clinker is ground to a fine powder in a cement mill and mixed with gypsum to create cement The powdered cement is then mixed with water and aggregates to form concrete that is used in constructionThermal efficiency Cement kilns have become highly energy efficient as older plants are being upgraded or replacedThe energy intensity of cement manufacturing is influenced by regional characteristics such as raw material moisture content and burnability, fuel types, plant size distribution, and cement standardsClinker CembureauAs the cost of refractories is a major expense in operating a cement plant, kiln stoppages are avoided as far as possible As the meal passes through the burning zone, it is beneficial to minimise clinker temperature as it enters the cement mill The milling process generates heat and excessive mill temperatures are undesirableManufacturing the cement kiln Understanding Cementis inadvisable to habitually run clinker silos down to the steel cone as abrasion will eventually cause failure Loading of hot (>150˚C) clinker to concrete silos should be avoided, as spalling and delamination will progressively weaken the walls Flames and fuels 47 The Cement Plant Operations Handbook – Seventh Edition 46The Cement Plant Operations Handbook International Cement
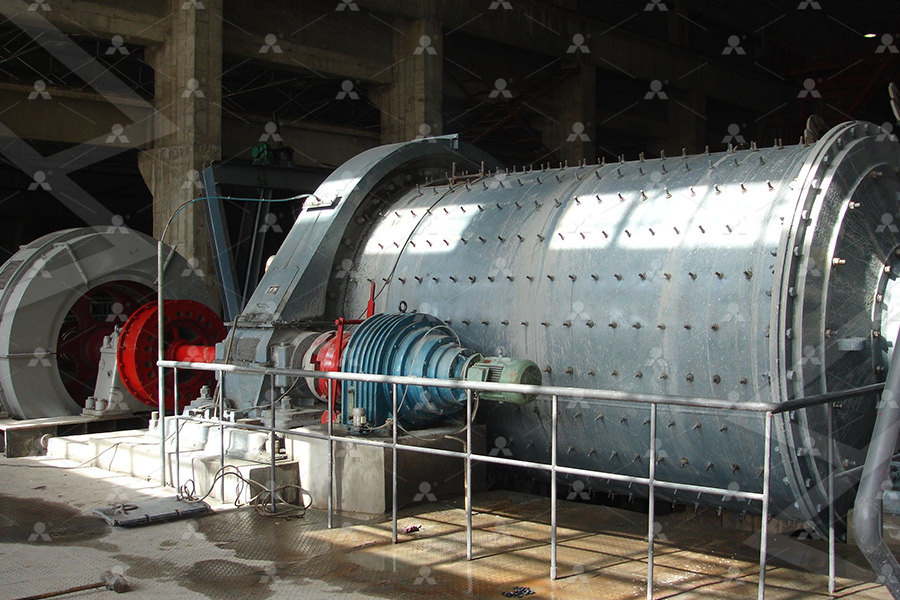
Reactions in the cement kiln clinkering
A number of phases are formed in the clinker feed before the burning zone proper is reached These intermediate phases dissociate in the burning zone and are not therefore found in clinker but assist in forming the final clinker minerals The clinker cooler, also known as grate cooler or cement cooler, it is a necessary equipment of cement clinker productionThe clinker cooler is mainly used to cool and transport the cement clinker At the same time, cement cooler also Clinker Cooler Cement PlantBhushan (2010) stated that lowering the clinker ratio can help in reducing the total emissions per ton of cement since both fuel consumption and specific process emissions depend on the clinkercement ratio From plantlevel data, Gao et al (2016) found out that 469 tons of materials are necessary to produce a ton of product in clinker Clinker Production an overview ScienceDirect TopicsSulfate Resistant Clinker – The composition of this type of clinker is alite 76%, belite 5%, tricalcium aluminate 2%, tetra calcium aluminoferrite 16%, and free calcium oxide 1% In recent years the production of this type of clinker has diminished as it is now possible to get sulfate resistance by making use of granulated blast furnace slag in cement manufacturingWhat is Cement Clinker? Composition, Types Uses
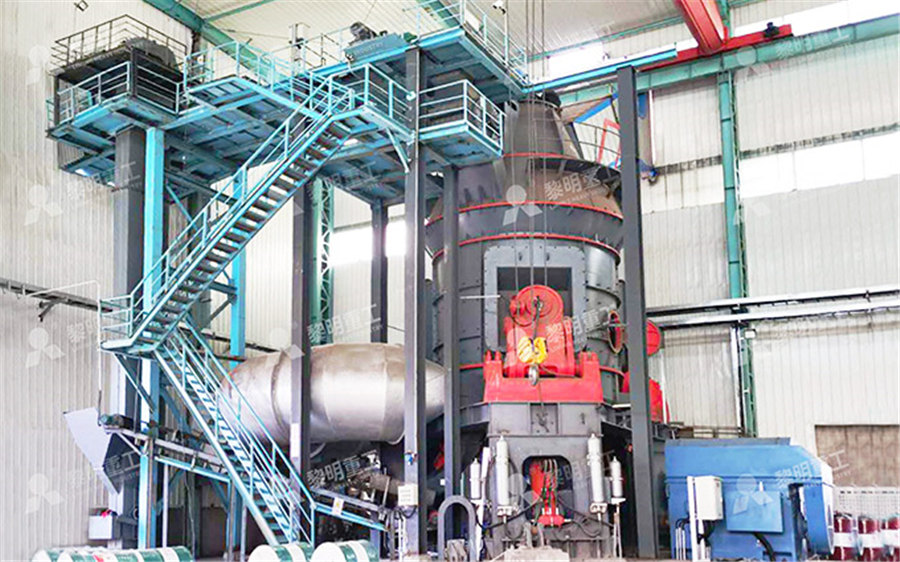
The cement plant of tomorrow ScienceDirect
2023年11月1日 Cement plants of tomorrow will have to implement all CO 2 abatement and saving measures to the best extent possible Reducing the clinker factor, optimising the reactivity of the clinker, substituting fossil fuels by alternative fuels and using alternative raw materials are pathways which will still play a growing role in future cement productionThe cyclone preheating system Phase IV: Calcination The calcination is the core phase of the cement making dry process The calcination of the preheated raw meal takes place in the rotary kiln of the cement plant The rotary kiln is a huge rotating furnace in which the raw meal is heated up to 1450 ⁰C and turned to clinkerHow Is Cement Produced in Cement Plants Cement Making What Is Rotary Cooler? The rotary cooler is also called the clinker cooler, which is the important support equipment for cement rotary kilnIt is mainly used to cool the hightemperature clinker(10001200℃)discharged from the rotary kiln to Rotary Cooler Cement Cooler AGICO Cooler In Cement Plant2023年1月16日 Dr SB Hegde, Professor, Jain University, Bangalore, talks about pyroprocessing and the role of preheater, rotary kiln and clinker cooler in the cement manufacturing process In the concluding part of the twopart series, we will learn more about the various factors aiding pyroprocessing False Air in Pyro ProcessingIndia is the second largest cement producer in []Pyroprocessing and Kiln Operation Indian Cement Review
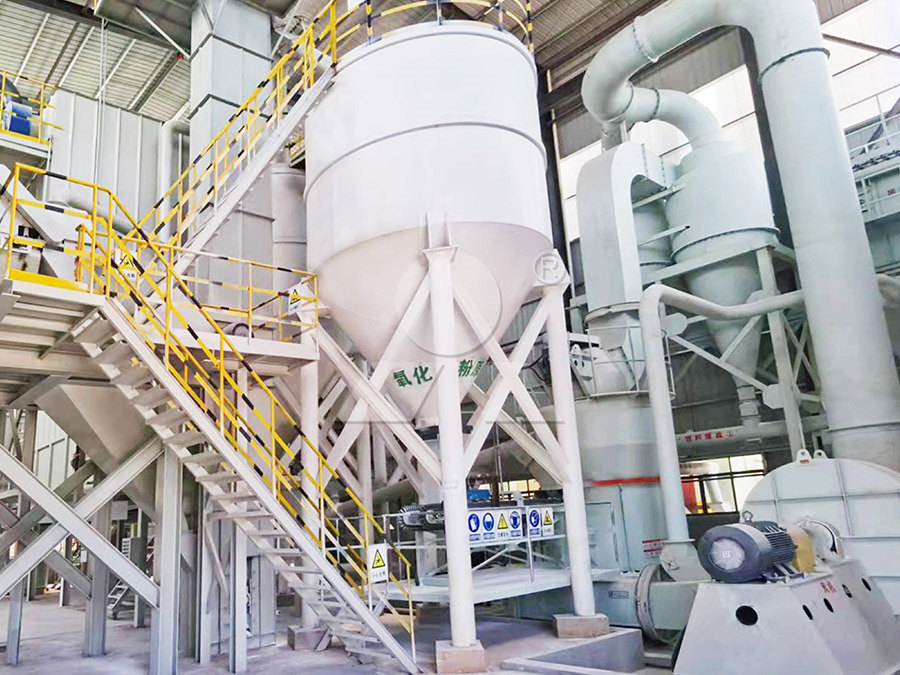
CEMENT CHEMISTRY AND CLINKER MICROSCOPY
2024年10月14日 A 4week modular course designed to give the course attendee a solid understanding of the cement chemistry and clinker microscopy Cement microscopy is a valuable technique for examining clinker, cement, raw materials, raw feed, and coal Every stage of the cement manufacturing process can be improved through the use of a microscopeReducing cement plant GHG emissions and product carbon intensity are important goals for both the cement industry and its customers To assist the US cement industry in evaluating its efforts to decarbonize, EPA calculated the 2019 carbon intensities for the intermediate and final products of cement plants: clinker and cementUS Cement Industry Carbon Intensities (2019) USbetter access to clinker substitutes; or a plant located next to the North Sea may opt for carbon capture due to the proximity of CO2 storage sites Does using a lower clinker cement imply a lower CO2 concrete or a lower CO2 construction? Not necessarily, and for several reasons:CLINKER SUBSTITUTION IN THE CEMENT INDUSTRY CEMBUREAUContinuous high temperature process in the cement industry: Calcination and cement clinker burning Calcination of raw material CaCO 3 => CaO + CO 2 Process emissions of raw material: = 054 t CO 2 /t clinker Endotherm reaction at 950 °C ca 1700 MJ/t clinker ≈ 50% of energy Cement clinker burning at 1450 °C formation of hydraulicProcess characteristics of clinker and cement production SINTEF
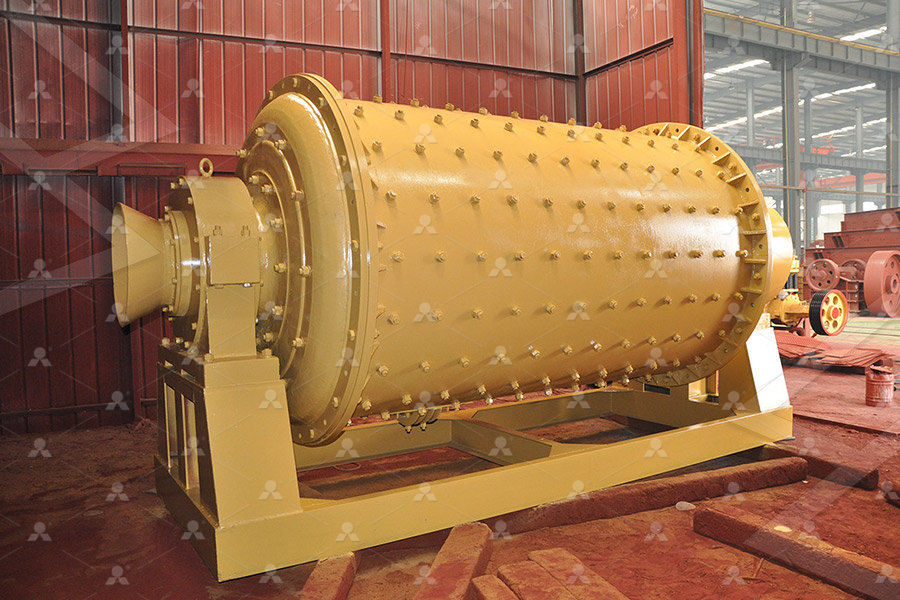
About us Cement Manufacturer Suppliers in India
It has one of the largest single location cement plants in India Equipped with multifuel technology this fully integrated plant includes captive facilities viz a Thermal Capexil Award for recognition for outstanding performance in Electrostatic precipitator (ESP), also known as high voltage electrostatic precipitator, electrostatic dust collector, is a dust collector using electric powerIt is one of the commonly used environmental protection equipment for dust gas purification It is widely used in electric power, metallurgy, building materials, chemical industry, and other industriesESP Electrostatic Precipitator Cement PlantAGICO Cement supplies cement preheater, preheater in cement plant as you need! Skip to content +86 s about blog contact EN ES Menu Menu Home; Cement Equipment and prepare for the clinker production Why cement preheater is necessary for rotary kiln cement plant Cyclone Preheater Cement PlantKINGMAN Provides Cement Plant,Clinker Plant,Lime Kiln,Cement Silo,Rotary Dryer,Vertical Cement Mill and Spare Parts Skip to content info@cementplantparts +86 FREE QUOTATION NOW HOME ABOUT US CEMENT EQUIPMENT Close CEMENT EQUIPMENT Open CEMENT EQUIPMENT; SPARE PARTS Close SPARE PARTS Open Cement Plant,Clinker Plant,Lime Kiln,Cement Silo AGICO CEMENT
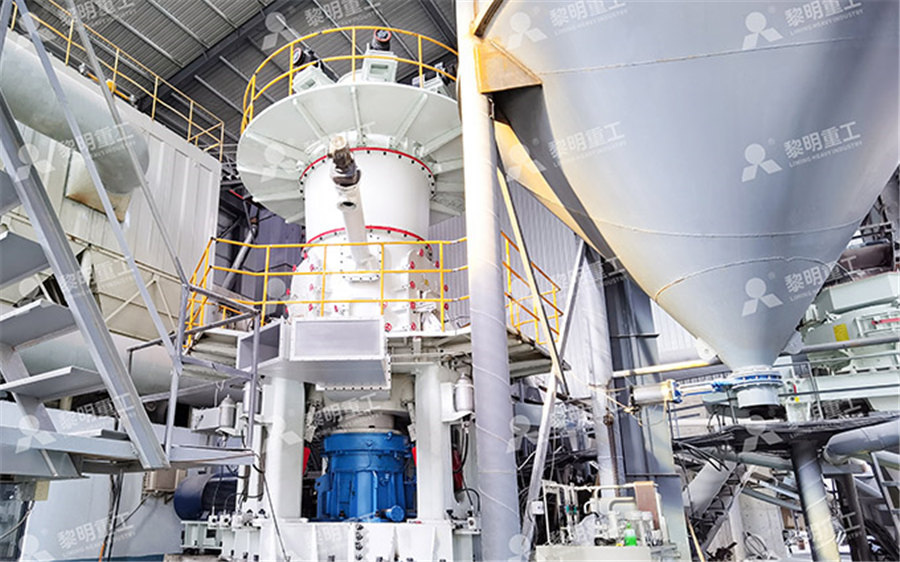
Cement mill Wikipedia
The cement mills on a cement plant are usually sized for a clinker consumption considerably greater than the output of the plant's kilns This is for two reasons: The mills are sized to cope with peaks in market demand for cement In temperate countries, the summer demand for cement is usually much higher than that in winterTanzania Operations Dangote Cement in Tanzania Our 30Mta plant in Mtwara – about 400km from Dar es Salaam – was commissioned in December 2015 and is the largest cement factory in Tanzania With about 500 million tonnes of limestone reserves, enough for 149 years, the plant is capable of producing large amounts of highquality 325 and 425 grade []Tanzania Welcome to Dangote Cement PlcProducción de clinker Conozca la máquina de fabricación de cemento simple para la producción de clinker El clinker de cemento es un producto semiacabado que se obtiene mediante la combustión parcial o total de materias primas y materiales de refrigeración ¿Cómo se fabrica el clinker? El precalentamiento y la precalcinación parcial de la materia prima []Producción de clinker AGICO CEMENT2022年2月2日 CEMEX, SAB de CV (“CEMEX”) and Synhelion announced today the successful production of the world’s first solar clinker, the key component of cement, a significant step towards developing fully solardriven cement plants Clinker is produced by fusing together limestone, clay, and other materials in a rotary kiln at temperatures CEMEX and Synhelion achieve breakthrough in cement