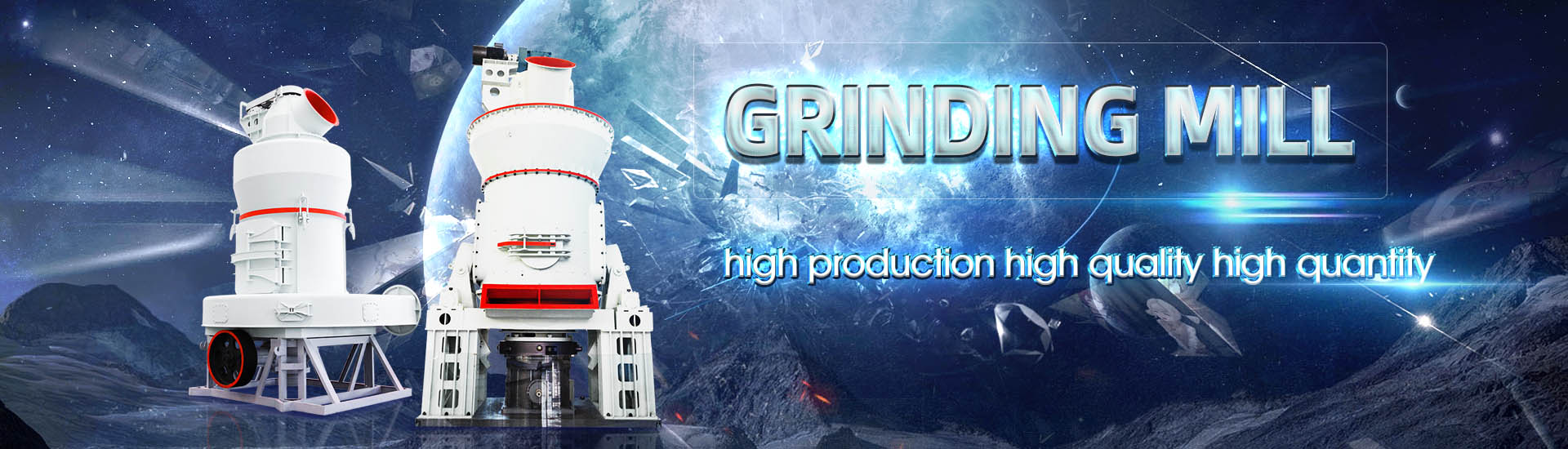
Comparison of coal grinding equipment
.jpg)
A Comparison of Three Types of Coal Pulverizers Babcock Power
It pulverizes coal by applying hydraulicallyloaded grinding pressure through three grin ding rollers onto a rotating bed of coal Grinding pressure can be adjusted to account for variations in coal grindability and desired product fineness Raw coal is fed through a centrally located feed 2017年7月1日 Comprehensive analyses of classification and grinding to compare energy efficiency 05%–2% gross power generation of coal power plant is consumed by vertical Comparison of energy efficiency between E and MPS type vertical All three (3) types of coal pulverizer systems supplied by RPI originally designed for low, medium and high speed pulverization have undergone design upgrades and improvements These Coal Pulverizer Design Upgrades to Meet the Demands of Low 2021年11月4日 testing procedures and a more exact simulation of grinding in vertical spindle coal mills Ballrace mills and Loesche roller mills were used(PDF) Technique to Investigate Pulverizing and Abrasive
.jpg)
Determining Optimum Productivity of a Ball Drum Mill When
2021年2月8日 Ball drum mills (BDM) are one of the main types of coalgrinding equipment in Russia A significant drawback of BDM is high power consumption (a significant part of the 2023年9月6日 According to the speed of coal grinding working parts, coal mill equipment can be divided into three types, namely: lowspeed coal mills, mediumspeed coal mills and high How to choose coal grinding machine2023年10月8日 To ensure that coal is not affected by overcrushing while achieving the required particle size and output requirements, FTM Machinery will help you choose the optimal coal crusher machine 1 Jaw crusher The jaw 6 Types of Coal Crusher: Which Is Best for Crushing My This type of grinding can be compared to when a hammer hits an object eg a piece of coal Crush – the coal is forced between two bodies This type of grinding has the same effect as a rolling pin when rolling across salt granules on a tableVertical Grinding Mill (Coal Pulverizer) Explained saVRee
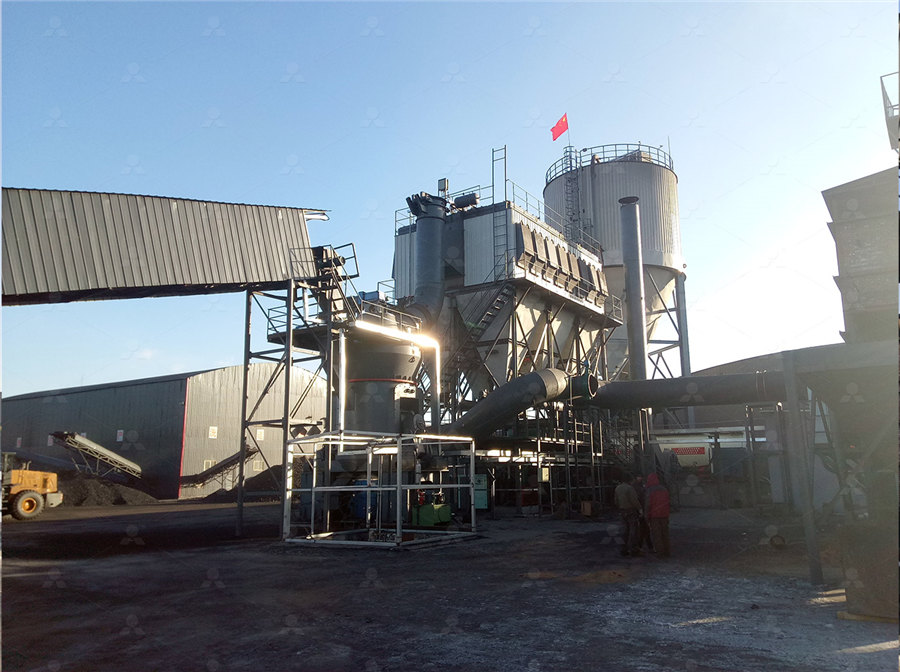
Cement grinding Vertical roller mills VS ball mills
The comparison of equipment costs outlined in the following is based on mills grinding OPC, ie without separate drying facilities for the ball mill, and with most of the equipment being of European origin Relative equipment costs 2020年11月6日 The JeffreyBaum jig, and it should be emphasized that all of the test data are for jigs operated with a bonemedia, is not so effective as the Menzies cone when treating coals containing from 0 to 3 pct ±01 near gravity material but is at least as effective and possibly more effective than densemedia equipment when treating coals containing 50 to 60 pct ±01 materialCoal Cleaning Equipment 911Metallurgist2017年7月1日 05%–2% gross power generation of coal power plant is consumed by vertical spindle pulverizer (VSP), and it is essential to select a VSP with better operational performance Simulated studies of labscale mills, which show the similar breakage mechanism with VSP, and industrial sampling on VSPs are conducted to compare energy efficiencies of E and MPS type Comparison of energy efficiency between E and MPS type vertical 2024年7月17日 They are the preferred equipment for coal crushing With a reduction ratio of 4:1, roller crushers have a lower ratio compared to other crushers, making them unsuitable for hard and highly abrasive materials due to rapid roller wear and increased operational costsTypes of Crushers: Choosing the Right One for Each Stage
.jpg)
An assessment of grindability index of coal Academia
Moist fuel ratio Page et al [31] advanced that moist fuel ratio (MFR), ie (FC/VM)/moisture of coal has got strong correlation with airborne respirable dust (ARD) generated during grinding and/ or handling, which in turn may be useful to other important issues such as fundamental studies on coal strength, environmental problems regarding fugitive dust from coal preparation, coal particles undergo the following four welldefined steps (as illustrated in Figure 1): coal particle drying, and then heatingup to the pyrolysis reaction temperature; pyrolysis of the coal particle to produce noncondensible Fundamentals of pulverised coal combustion 5 1 Introduction volatiles (gases), condensible volatiles (tars), and aFundamentals of pulverised coal combustion ICSCCoal grinding is a critical process in various content in the overall process air mix and introduce gaseous CO₂ or N₂ to displace oxygen and prevent combustion in coal grinding equipment upon noticing elevated temperature or COin Coal Mill Safety In Cement Production Industries Ideas on Emergency Inerting Comparison: CO₂ Safety Aspects of Coal Grinding Coal Mill Safety, Explosion and The individual coals were mixed after grinding by varying the content of lower rank coal to generate three blends containing 25%, 50% and 75% by weight respectively The Hardgrove Grindability Index (HGI) was measured in accordance with standard procedures [7] The HGIs of the binary coal blends were determined after mixing 060118Effect of the grinding behaviour of coal blends on coal
.jpg)
Fuels in the cement industry INFINITY FOR CEMENT EQUIPMENT
The maximum moisture content of coal to be dried in dryinggrinding plants is 15 % The maximum tem perature of the hot gases entering the dryinggrind ing plant should be 350 °C Coal grinding Coal grinding is performed either in bowl mills or in tube mills [171c]To design equipment for coalfired thermal power plants or to select a nonstandard fuel, it is necessary to know a wide range of coal characteristics, including its abrasive properties [1, 2] When mining, transporting, crushing, and grinding coals for pulverized coal combustion, equipment surfaces and grinding components, which are in contact DEFINITION AND ASSESSMENT OF COAL ABRASIVITY SpringerThe individual coals were mixed after grinding by varying the content of lower rank coal to generate three blends containing 25%, 50% and 75% by weight respectively The Hardgrove Grindability Index (HGI) was measured in accordance with standard procedures [7] The HGIs of the binary coal blends were determined after mixing 060118Effect of the grinding behaviour of coal blends on coal utilisation 2020年8月21日 The results of the research showed that the joint grinding of coal and biomass contributes to the achievement of the minimum size of coal and wood and, as a result, leads to an increase in the (PDF) Effect of Biomass Carbonization on the
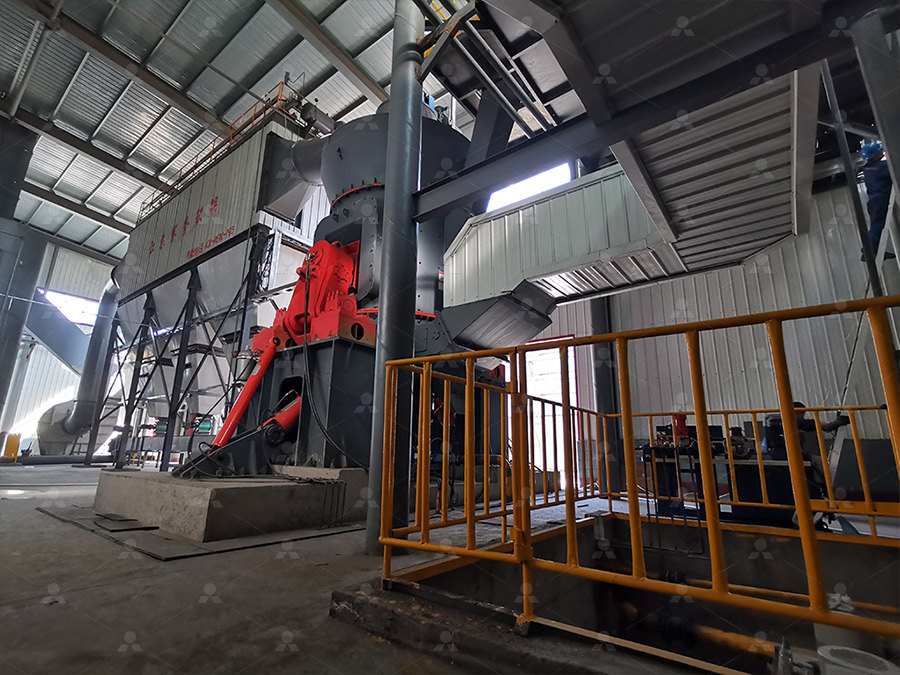
Ball Mill VS Rod Mill: Difference Selection JXSC
2024年1月10日 When gravity or magnetic separation of metal ores (such as tungsten tin ore and rare metal ores), rod mills are often used to prevent overcrushing; it is also suitable for brittle materials, such as coal; in the second 2022年2月28日 Comparing dry and wet grinding curves in a ball mill in the same condition (an equal amount of materials and grinding media has been used on each pair of wetdry experiments) (Fig 17) indicated two significant differences at higher power values of wet grinding, specifically when speed exceeded 06 critical speed and for higher ω Pmax in the Grinding SpringerLink2023年6月7日 Mathematical validation and comparison of coal milling operations of a horizontal ball tube mill and a vertical bowl mill located in two distinct coal based power plants in India was carried out The coal mill model was developed and the unknown model coefficients were obtained numerically by genetic algorithm (GA) The input variables of mass flow rates of raw Mathematical validation and comparison of ball tube and bowl 2021年8月12日 Compare laboratory mill and lab grinder features, styles, applications, uses, animal feed, spices, coal and detergents 6500 rpm 28000 rpm 25000 rpm 20000 rpm D Laboratory Mill Cooling Method (back to chart) Where Can I Buy Laboratory Mills and Grinding Equipment Mills Online?Laboratory Mill Comparison Chart and Features Overview

Technique to Investigate Pulverizing and Abrasive Performance of Coals
2021年11月4日 The operating costs of breaking coal particles into fine powder, to achieve optimum combustion for the boilers in a power plant, are made up of power input to carry on an energy intensive comminution mechanism and to overcome friction losses within pulverising machines The operating costs also include the cost of the replacement of the processing 2021年5月3日 Although coal is cheaper compared to fuel oil and supposed to contribute a share of fuel used in cement industries, and clinker crushing and grinding equipment which accounts for 38% of its consumption Comparison of flue gas from coal, fuel oil, and natural gasEnergy and Economic Comparison of Different Fuels in2021年11月4日 Comparative measurements were taken on the selected coal, the coal water slu rry, and three abrasives frequently used in differ ent tribotests The results are given in TableTechnique to Investigate Pulverizing and Abrasive Performance of Coals specification and is significant also for the design of capacity of particularization equipment and grinding circuits The contribution specifies the discovered value of grindability HGI of black coal from mine plants in the Karvina part of the OstravaKarvina coal basin 2 TESTING EQUIPMENT, TESTING PROCEDURECONTRIBUTION TO DETERMINATION OF COAL GRINDABILITY
.jpg)
Design of coal preparation plants: problems and solutions
Size degradation occurs during loading coal into rail cars, dump trucks, transportation from the preparation plant stock dump and loading onto silos, at grinding of coarse coal over +200 (100) mm, during supplying coal to the preparation plant by a belt conveyor Coal size degradation depends on strata sensing and grindabilityCoal grinding is a critical process in the production of energy and industrial products like cement It comes with inherent risks Ensuring the safety of workers and equipment in coal grinding operations is paramount This article outlines key safety measures and best practices to mitigate the hazards associated with coal grindingEnsuring Safety in Coal Grinding Operations Coal Mill Safety 2022年1月11日 Substantial semicoke has been produced through the industrialized lowtemperature pyrolysis process, which has great potential as an alternative fuel for pulverized coal injection (PCI) and iron ore sintering Xray diffraction, Raman spectroscope, and thermal analysis were used to compare the carbon chemical structure and combustion reactivity of semicoke, Comparison of semicoke with traditional pulverized coal 2021年2月8日 Abstract Ball drum mills (BDM) are one of the main types of coalgrinding equipment in Russia A significant drawback of BDM is high power consumption (a significant part of the TPP’s own needs) With a huge scale of production, reducing these costs even by a few percent gives a significant economic effect The problem of minimizing the specific energy Determining Optimum Productivity of a Ball Drum Mill When
.jpg)
Roller mills INFINITY FOR CEMENT EQUIPMENT
Ball race mill (Petersmill of the Claudius Peters Joint Stock Company, Hamburg, Germany) The cement industry employs the Petersmill (pre viously called FullerPetersmill) mostly for coal grinding It is a few years now that the shockproof construction (shock resistance – 35 bar) of the Petersmill was designed for coal grinding2002年4月1日 Grindability of coal is a central characteristic of coal which is closely related to pulverizer performance and mill capacity (ACARP, 1998) and is defined as ease of grinding of coal which is, in An assessment of grindability index of coal ResearchGate2016年10月5日 In this chapter an introduction of widely applied energyefficient grinding technologies in cement grinding and description of the operating principles of the related equipments and comparisons over each other in terms of grinding efficiency, specific energy consumption, production capacity and cement quality are given A case study performed on a EnergyEfficient Technologies in Cement Grinding IntechOpen2017年7月1日 It is noted that the grinding equipment should be selected according to the property of materials the moving trajectories of mixtures of air and coal were similar in two VSPs Comparison of grinding zone indicates that there are nine balls on the grinding table of E type VSP and the interspace among balls is relatively parison of energy efficiency between E and MPS type
.jpg)
Particle size distribution modeling of milled coals by dynamic
2016年3月1日 Cone and quarter method of sampling was used to derive representative samples for MS tests An optimum grinding time of 16 min of ball milling and 1 and 15 min of GyRo milling were chosen for lignite and hard coal considering the amount of size fraction less than 300 μm for DIA testsThe GyRo mill used in the study (Fig 1) is a laboratory equipment (original name: 2020年8月21日 To increase the cofiring ratio of biomass in existing pulverized coalfired power plants, biomass should be pulverized to obtain a particle size suitable for combustion However, evaluation of the particle size distribution of each coal and biomass mixture via traditional fuel analysis is difficult Because coal does not contain neutral sugars, the particle size distribution Effect of Biomass Carbonization on the Grinding of Coal/Biomass 2023年4月23日 492 mm and a mixture of the grinding media on a coal sample, OEMBSD (original equipment manufacturer recom mended ball size distribution) and EQM BSD (Equilibrium Ball Size distrib ution) were (PDF) Grinding Media in Ball MillsA Review2020年8月12日 A comparative study on lignite coal Vertical Coal Mill (VCM) is equipment for grinding and pulverizing coal into micron size Rotary kilns then use the powders as fuel burnersAn investigation of performance characteristics and
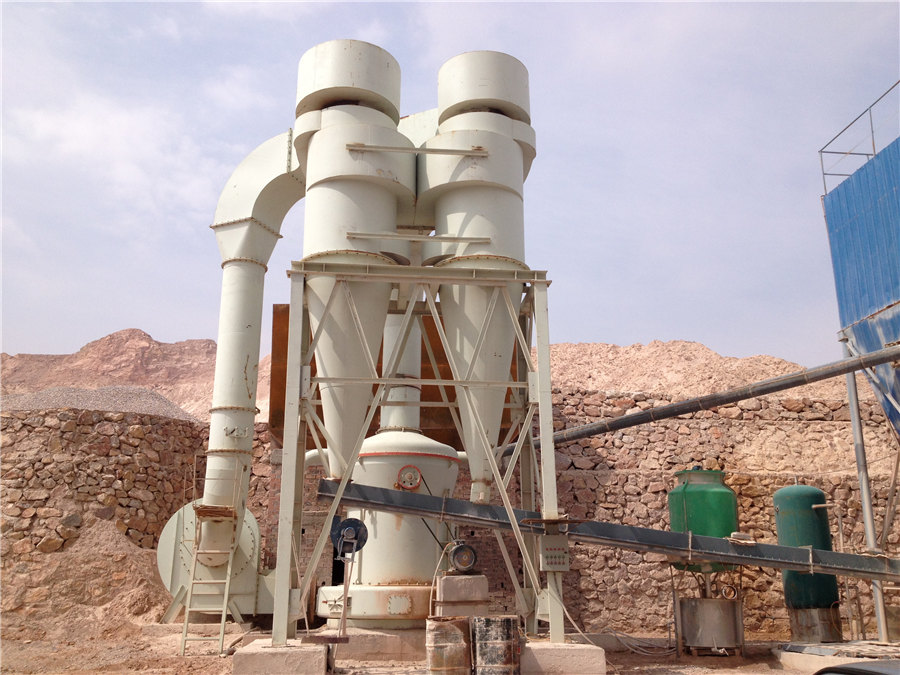
Global Thermal Coal Attributes Department of Energy
Global Thermal Coal Attributes An Analysis US Thermal Coal Comparison to World Coals 1 The use of coal as fuel for power generation is influenced by its properties, which vary significantly across the range of coals available in the global marketplace A comparison of coal properties from around the2015年7月1日 Among others, the studies by Huescar M et al [7, 27], in which the explosion violence parameters of biomass (mainly woodderived) are compared to coal dust ones, and a new experimental setup is Comparison of the explosion characteristics and flame speeds of calculated acc to 3 x geometrical volume of overall coal grinding workshop + silos in order to be able to repeat in general inerting trip up to 2 times 1 Inerting standards Design, technical equipment, electrical facilities and cabinet and execution of the complete, CO2 / N2Comparison CO inerting – CO fire extinguishing Coal Mill Safety 2020年6月11日 Based on the analysis of coalash dissociation process in ultrafine grinding of pulverized coal and by combining Tomoyoshi's energy consumption formula relating specific surface area of Comparative Study of Grinding Machines Processes on
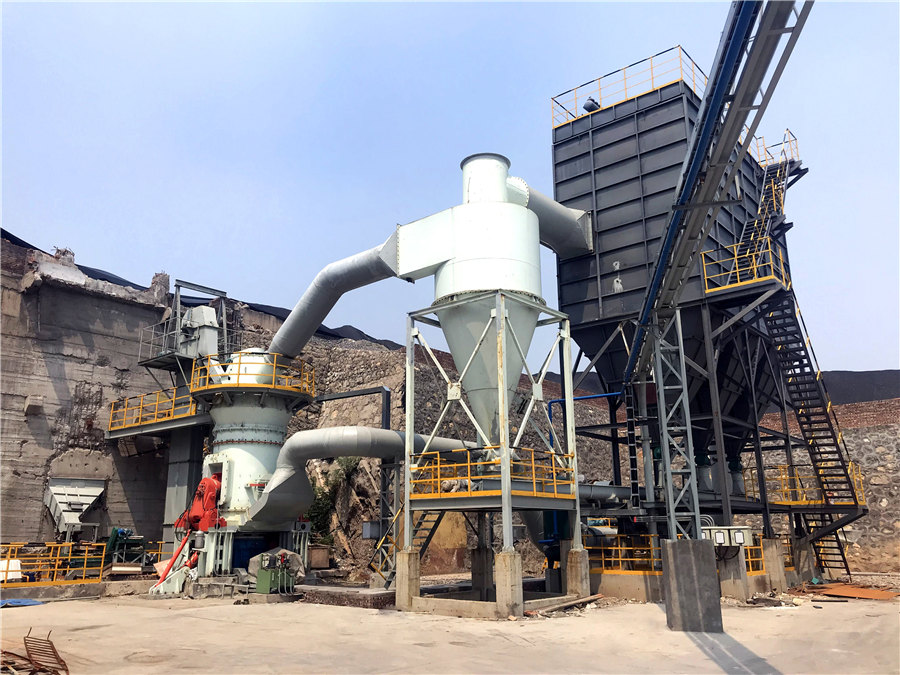
Milling Characteristics of Coal and Torrefied Biomass Blends in a
2021年10月28日 CO2 emissions from coal power generation could be reduced by maximizing the amount of torrefied biomass that can be used in pulverizedcoalfired power plants In this study, to evaluate the milling performance of coal and torrefied wood pellets (TPs), various blend ratios were tested using a benchscale roller mill Neutral sugar analysis was performed to 2022年2月21日 Request PDF Comparison of the prediction performance of separating coal in separation equipment using machine learning based cubic regression modelling and cascade neural network modelling The Comparison of the prediction performance of separating coal in 2019年6月30日 Coal Production from opencast mines in India (FY 199899 to 201617) Source: Coal Directory of India, FY 199899 to 201617 Output Per Man Shift (OMS) of UG and OC mining methods under CILUnderground and Opencast Coal Mining Methods in India: A Comparative Pebble Semimobile Crushing Plant with Low Budget Pebble semimobile crushing and screening equipment is widely used in crushing coal, ore, rock and other bulk materials in mines (coal mines, noncoal mines), metallurgy, highway, expressway, railway, mineral processing, hydropower engineering, building materials, municipal solid waste, chemical, and other fieldscoal screening equipment in mining project Sebocom