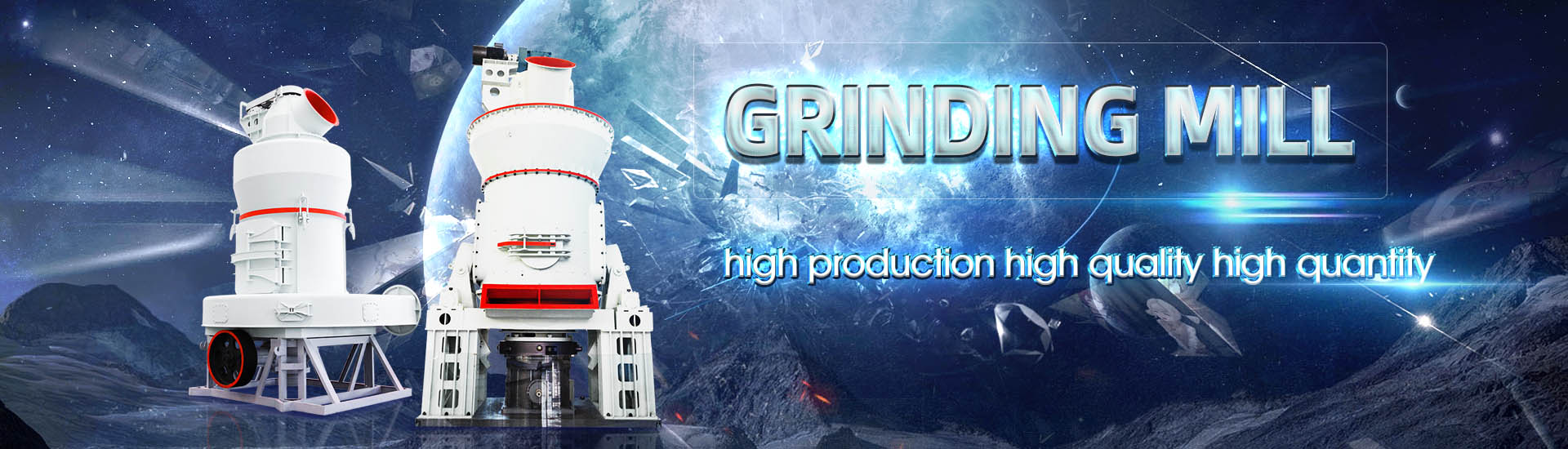
HOME→There are several calcite silica grinding mills and electrolytic aluminum waste residue grinding mills.
There are several calcite silica grinding mills and electrolytic aluminum waste residue grinding mills.

Efficient extraction and recovery of lithium from waste aluminum
2023年10月1日 According to the chemical analysis method of cryolite (YS/T 2733–2020) and lithium fluoride (GB/T 22,660–2008), the content of Al and F in the waste aluminum electrolyte, calcine, leaching residue and LiF sample was determined by the EDTA and Thorium nitrate Cryolitealumina (Na 3 AlF 6Al 2 O 3) molten salt electrolysis is the only Efficient extraction and recov2024年5月23日 Here, we review carbonrich solid wastes with focus on sources and hazards, detoxification, separation, recovery, recycling and disposal Treatment techniques include The recycling of carbonrich solid wastes from aluminum Our analysis reviews the accomplishments in ewaste recycling and assesses the principles of recycling, separation, and the parameters of different technologies, by looking at both Recovery of metals and valuable chemicals from waste electric and
.jpg)
Activation of silicon in the electrolytic manganese residue by
2018年8月10日 In this study, we investigated the effects of mechanical grinding and an activation method coupling roasting by studying several parameters ie, (balling time, ratio of 2022年3月1日 Influences of different grinding aids on dry fine grinding of calcite using a laboratorytype ball mill were investigated Tested grinding aids had affected the flowability Analysis of grinding aid performance effects on dry fine milling of 2023年4月13日 Aluminium is produced by electrolysis using alumina (Al 2 O 3) as raw material and cryolite (Na 3 AlF 6) as electrolyte In this Hall–Héroult process, the energy consumption A comprehensive review of aluminium electrolysis and the waste 2022年4月13日 Here we propose a solidstate electrolysis (SSE) process using molten salts for upcycling aluminium scrap The SSE produces aluminium with a purity comparable to that of A solidstate electrolysis process for upcycling aluminium scrap
.jpg)
Selective comminution and grinding mechanisms of spent carbon
2022年1月10日 In this study, grinding characteristics of spent carbon anode from aluminum electrolysis in both ball mill and rod mill were analyzed, and compared based on the utilization 2021年4月21日 In this study, the performance of batch type vertically/horizontally orientable stirred mills was compared on the basis of stress intensity analysis obtained from a series of The Influence of Stirred Mill Orientation on Calcite Grinding2023年4月8日 Here, we review manganese recycling with focus on ore reserves, electrolytic production, residue stockpiling and environmental impact, reducing the amount of residue and Recyling manganeserich electrolytic residues: a review2023年4月8日 Huge amounts of manganeserich solid residues are yearly produced worldwide by industrial electrolysis, calling for advanced methods of recycling in the context of the circular economy Here, we review manganese recycling with focus on ore reserves, electrolytic production, residue stockpiling and environmental impact, reducing the amount of residue and Recyling manganeserich electrolytic residues: a review
.jpg)
(PDF) A comprehensive review on the grinding process:
June 2022; ARCHIVE Proceedings of the Institution of Mechanical Engineers Part C Journal of Mechanical Engineering Science 19891996 (vols 203210) 236(2):1107In Fig 41, the numbers 150200250 on the graphs of equilibrium relate to caustic soda concentrations in Na 2 CO 3A/C denotes aluminate ion concentration as Al 2 O 3 (A)/caustic soda concentration as Na 2 CO 3 (C) A typical Bayer process cycle with low temperature digestion is also shown Virtually each bauxite contains more or less amount of clay minerals, Chemical Processing of Bauxite: Alumina and Silica 2007年12月31日 The size reduction of particulate materials below 10 μm by highenergy milling is known as ultrafine grinding The ultrafine grinding occurs in different types of high energy mills, which the most Chapter 10 Selection of Fine Grinding Mills ResearchGateThe comprehensive recovery and utilization of electrolytic aluminum spent carbon anode slag (Hereinafter simpli fied as “carbon anode slag”) are therefore necessary OPEN ACCESSRecovery of carbon and cryolite from spent carbon anode slag of
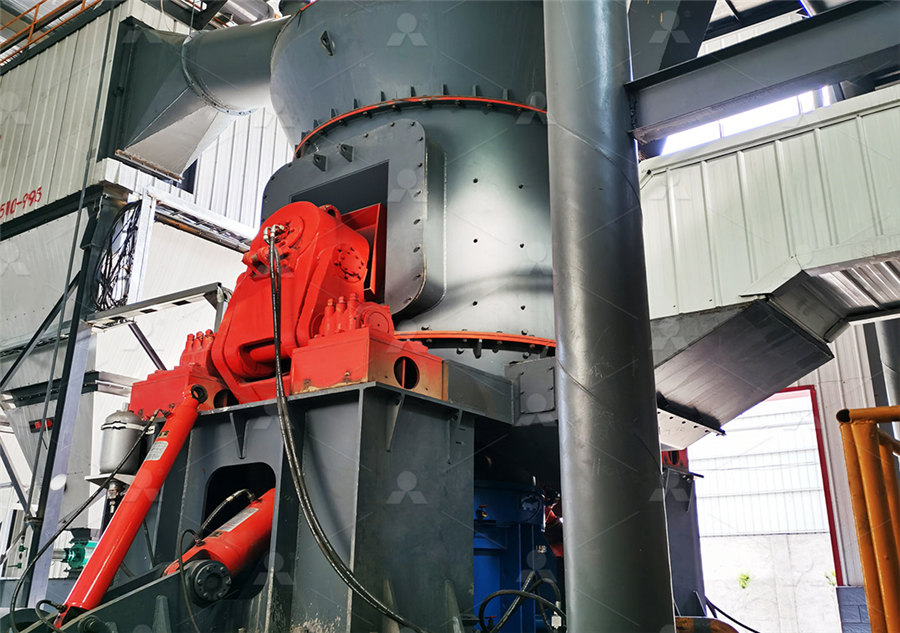
Ductile and Brittle Mode Grinding of Fused Silica ResearchGate
2010年9月1日 There is a demand for highefficiency and high surface integrity grinding of fused silica Ductile grinding is an ideal method for producing a mirror finished surface on hard and brittle materials 2023年4月23日 A comparison of the grinding media is given together with the knowledge gaps that still need to be bridged to improve the quality and performance of grinding media used in ball mills(PDF) Grinding Media in Ball MillsA Review ResearchGate2022年6月24日 Another unascertained problem is the management of grinding swarf, which is being attended to by recycling it to fabricate composites which is expected to be another prominent domain of research Further, the advancements taking place exhibit the potential of the grinding process, suggesting that its future is bright and evergrowingA comprehensive review on the grinding process: Advancements 2024年2月1日 Aluminum metal was produced using the cryolitealumina molten salt electrolysis method (Ishak et al, 2017)A large amount electrolytic aluminum slag (EAS) is generated during the electrolysis process, as the falling of carbon particles on the anode into the electrolysis cells and the accumulation of lithium fluorine result in energy consumption and electrolyte scrapping Efficient lithium recovery from electrolytic aluminum slag via an
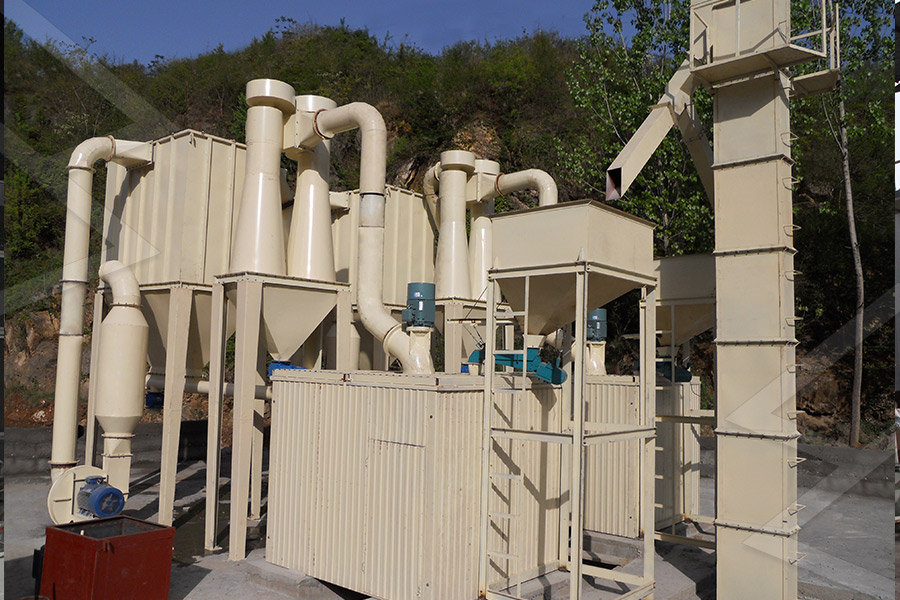
Harmless recovery and utilization of electrolytic aluminum spent
2023年12月1日 However, the amount of solid waste generated in electrolysis process continues to accumulate due to the confinements of the process With the growth of solid waste emissions, environmental and ecological issues have ended up one of the major bottlenecks limiting the sustainable development of aluminum enterprises (Liao et al, 2018; Ishak et al, 2017)Learn how to improve the quality and speed of your metallographic grinding and polishing – from selecting the best method to choosing the right consumables – with expertise, tips and insight from Struers, the world’s leading Metallographic grinding and polishing insightA mill is a device, often a structure, machine or kitchen appliance, that breaks solid materials into smaller pieces by grinding, crushing, or cutting Such comminution is an important unit operation in many processesThere are Mill (grinding) WikipediaDownload Citation On May 1, 2024, Liang Tang and others published Hydration characteristics and pollutant solidification mechanism of full solid waste electrolytic manganese residue super Hydration characteristics and pollutant solidification mechanism of
.jpg)
Selective recovery of manganese from electrolytic manganese residue
2021年3月1日 Electrolytic manganese residue (EMR), a byproduct of the electrolytic manganese metal production process, contains several hazardous components such as ammonia nitrogen (NH3N), soluble manganese Grinding mills and pulverizers transform course materials into finer shards or granules Mills and pulverizers move materials through various devices that use pressure and blades to grind it Types of Grinding Mills and Pulverizers There are several types of grinding mills and pulverizers available to industrial buyers These types include,Grinding Mills and Pulverizers Information GlobalSpec2018年8月17日 Further, the grinding mills can be categorized into three major types — rod mills, ball mills, and SAG mills So, which one is for you? Well, the answer essentially lies in the feed size and the Grinding Mills — Types, Working Principle Applicationsfor electrolytic aluminum waste is proposed This mode is to pulverize the electrolytic aluminum waste, and then mix the crushed electrolytic aluminum waste with the raw coal of the circulating fluidized bed boiler [6], then send it to the circulating fluidized bed boiler for combustion In this study, a mixed combustion experiment ofResearch on the Coprocessing of Mixed Electrolytic Aluminum Waste

(PDF) Electrochemical grinding process, current state and future
2014年1月1日 Electrochemical grinding is one of the widely used nonconventional grinding processes to grind electrically conductive materials and difficulttomachine alloys (such as stainless steel 2003年4月1日 comes economical and there are several base metal concentrators today that grind as low as 10 l m (Underle et al, 1997; Burgess et al, 2001; Ellis and Gao, 2002)Variables Affecting the Fine Grinding of Minerals Using Stirred Mills2023年7月10日 The present literature review explores the energyefficient ultrafine grinding of particles using stirred mills The review provides an overview of the different techniques for size reduction and the impact of energy requirements on the choice of stirred mills It also discusses the factors, including the design, operating parameters, and feed material properties, EnergyEfficient Advanced Ultrafine Grinding of Particles Using2023年2月1日 Aluminum electrolytic technology tends to be more and more reliable 130 AEC consists of two aluminum electrodes, a film oxide layer There are several steps to build an AEC: 230(PDF) Electrolytic capacitor: Properties and operation
.jpg)
Grinding aids for dry fine grinding processes ScienceDirect
2020年9月20日 The history of grinding aids in dry fine grinding processes starts in the late 1930s with the application of the first commercial grinding aids in the cement industry [1]Since that time, the importance of grinding aids in industrial dry fine grinding processes has strongly increased; so did the number of scientific papers dealing with this topicMetso Select™ horizontal grinding mills are a preengineered range of classleading horizontal grinding mills, designed from industry leading experience and expertise The preengineered package eliminates time and costs usually Grinding mills for mining and minerals processing2024年6月1日 Waste Chromite ore processing residue: chromium, aluminum, iron: The leachability of iron, aluminum, and chromium reached 948,751 and 76% respectively under the optimum conditions of ballmilling duration of 2 h,60% of w/w% H 2 SO 4,L/S of 8 mL/g,130 °C leaching temperature, and leaching time of 6 h: Copper Smelting Flue Dust: arsenic, germaniumA review on complex utilization of mine tailings: Recovery of rare 2021年11月15日 Figure 314 Amorphous sillica particles in colloidal silica (TEM, 300,000X) Colloidal silica was first used for polishing wafers of single crystal silicon where all of the damage on the wafer surface must be eliminated before a device can be grown on it The silica is amorphous and the solution has a basic pH of about ~10Grinding and Polishing Guide Buehler Metallography
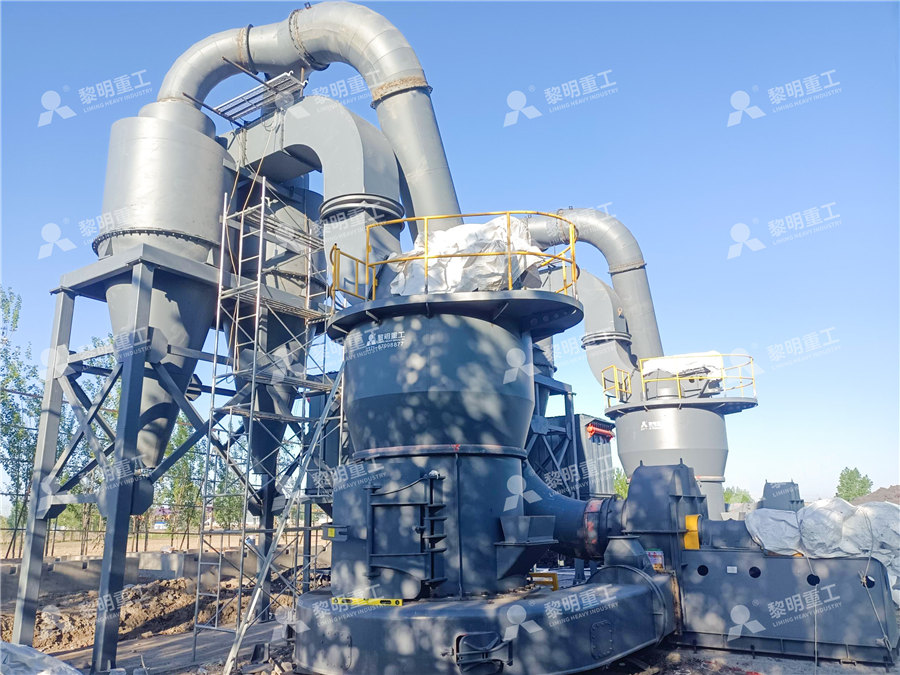
How it Works: Crushers, Grinding Mills and Pulverizers
2017年6月2日 Grinding Mills and Pulverizers Grinding mills and pulverizers are the second level of material reduction equipment after crushers Mills and pulverizers transform materials through pressure or blades to grind, cut or crush it As there is with crushers, there are many different types of grinding mills and pulverizers available2012年12月31日 During the treatment of spent cathode carbon from electrolytic aluminum, a large amount of fluoride containing wastewater is generated By adding different sodium source and aluminum source Study on Harmless and Resources Recovery Treatment Technology of Waste 2023年12月4日 There is a large agreement in declaring that electrochemistry is one of the most difficult curricular domains to teach and learn Applied or Industrial Electrochemistry is even less frequently found in Chemical Engineering curricula The extremely few textbooks on Applied Electrochemistry put most of the effort in developing theoretical content while leaving for later Electrolytic production of aluminium as a case study for linking 2017年3月4日 ball mills, grinding (steel) balls or pebbles are often added to stirred mills to help grind ore, howev er these mills contain a large screw mounted ver tically to lift and grind material In tow SIZE REDUCTION BY GRINDING METHODS ResearchGate
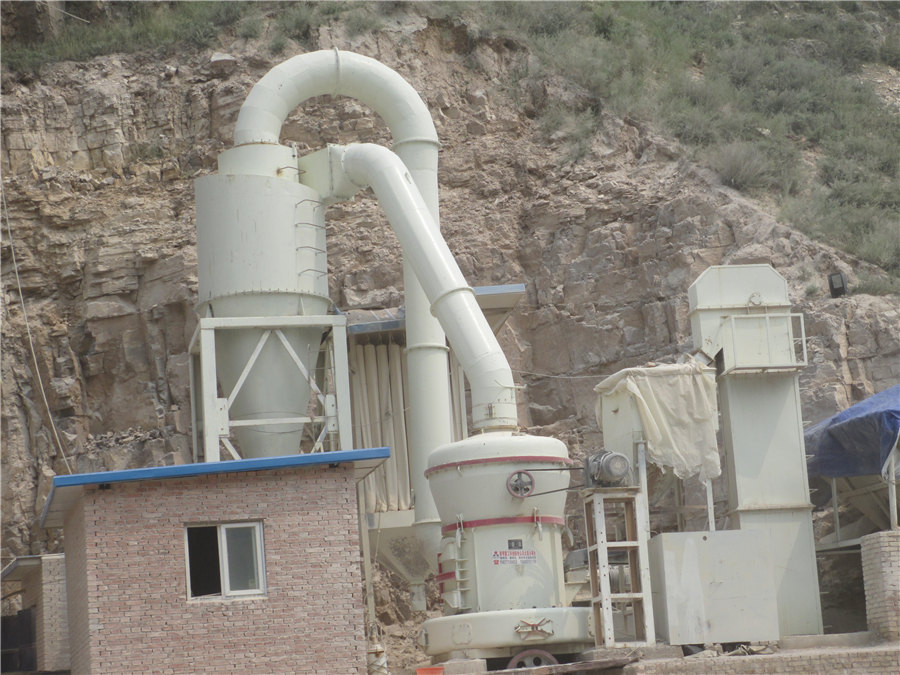
Architectures and mechanisms Water mills for cereal grinding
2013年1月1日 In Villa Tordinia there are two cereal grinding mills and a mechanism for copper processing This was realised after an expansion of the building occurred around in the m idnineteenth century2017年1月17日 AgnicoEagle Goldex Division, Mine Canadian Malartic, and New Gold New Afton Mine participated in the study by providing operating data for 3 semiautogenous grinding (SAG) mills and 4 ball millsBreaking down energy consumption in industrial 2016年9月2日 Depending on the form of the grinding media there are ball mills, rod mills, pebble mills and autogenous grinding mills Grinding media – iron and steel balls with diameter of 15120 mm, steel or cast iron cylpebs dimensions Grinding Mill Types, Construction, and Usage2020年7月1日 And also, olive waste water contains a high percentage of water Some studies in the literature have demonstrated that water used as a grinding aid in dry systems clearly affects the grinding Grinding aids for dry fine grinding processes – Part I: Mechanism
.jpg)
Physical Bauxite Processing: Crushing and Grinding of Bauxite
2022年1月23日 There are a full range of bauxite grinding options available an each has its advantages and disadvantages The final choice of which option best suits the application is influenced by several variables These can be broadly categorized into the feed characteristics and the target product requirements Some of the feed variables are2023年11月1日 Electrolytic manganese residue (EMR) is a hazardous solid waste produced during manganese hydrometallurgy The accumulation of EMR not only occupies significant land resources, but also pollutes water resources and even endangers the safety of human life and property Therefore, there is an urgent need to develop more efficient EMR treatment Remediation treatment and resource utilization trends of electrolytic impregnated with liquid electrolyte There is another type of aluminum electrolytic capacitor, which is the "solid" that uses solid electrolyte containing electrolyte (Apparent Cathode) Electrolyte (Real Cathode) Cathode Aluminum electrode Electrolytic paper Oxide film Anode aluminum electrode Fig 11 1 General Description of Aluminum 1 General Description of Aluminum Electrolytic CapacitorsGrinding is a machining process that used grinding wheels as the cutting tool The heat generation in grinding is significant high as there are a lot of small cutting edges on the grinding wheel Each of them produces the friction when in contact with the workpiece It is recommended to use flood coolants for such an applicationGrinding (Machining) an overview ScienceDirect Topics
.jpg)
Grinding Mills 911Metallurgist
Grinding Mills: Ball Mill Rod Mill Design PartsCommon types of grinding mills include Ball Mills and Rod Mills This includes all rotating mills with heavy grinding media loads This article focuses on ball and rod mills excluding SAG and AG mills Although their concepts are very similar, they are not discussed herePhotographs of a glass ended laboratory ball mill show 2015年3月1日 The electrolytic aluminium industry is a typical energyintensive industry, and one of the six largest energyconsuming industries in China The energy consumption of China’s electrolytic aluminium industry (CEAI) in 2011 accounted for 091% of China’s total energy consumption and 227% of the total energy consumption of the nonferrous metal industryEnergy conservation of electrolytic aluminum industry in China2024年2月1日 The pyrometallurgical process for AD is the subject of extensive research interest The pyrometallurgical process was used to recycle up to 90% of the valuable material from waste aluminum dross (Verma et al, 2021)A study stated that recycling scrap can produce sustainable aluminum (Raabe et al, 2022)Promising methods for managing aluminum dross have been Thermal utilization techniques and strategies for secondary aluminum