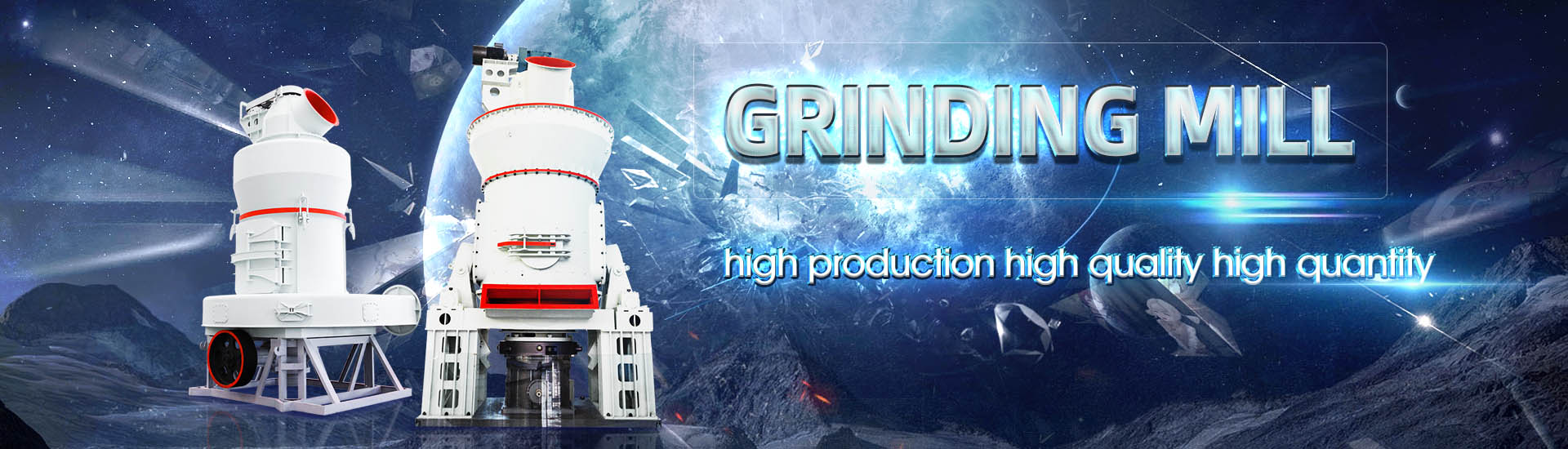
Qiqilime ball mill equipment design and installation unit
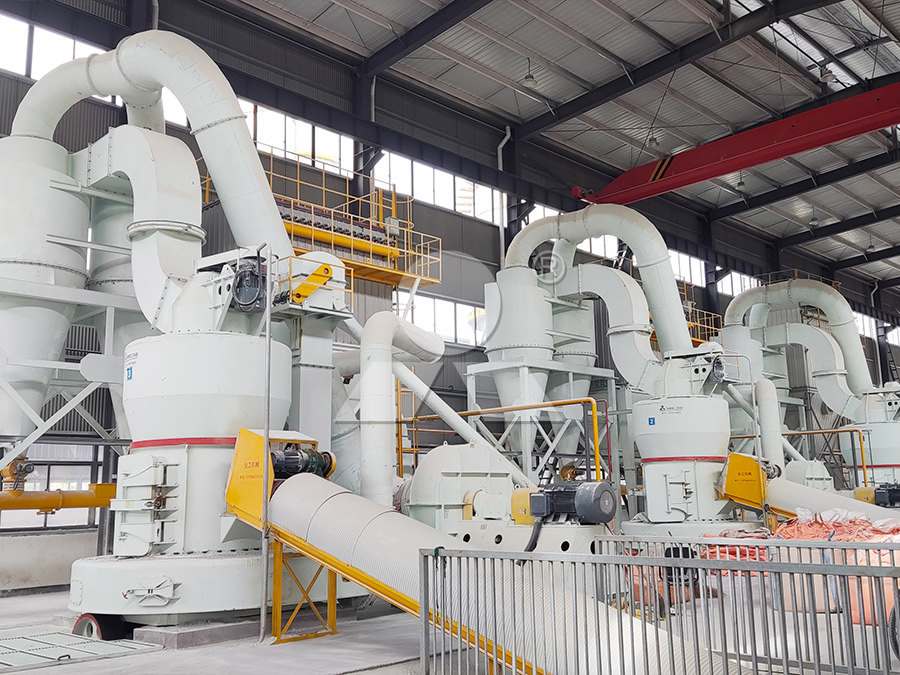
BALL MILLS Ball mill optimisation Holzinger Consulting
type of installation: ball mills, combined in circuit with an air classification system of varying generations and sophistications Depending on the local market situation and product portfolio, 2015年6月19日 Use this online calculators for Motor Sizing and Mill sizing as well as mill capacity determinators In extracting from Nordberg Process Machinery Reference Manual I Ball Mill Design/Power Calculation 911Metallurgist2013年7月15日 This paper discusses the differences between ball mill circuits closed with cyclones and with screens A methodology is described for equipment sizing and selection for (PDF) Energy Efficient Ball Mill Circuit – Equipment Sizing The Wet Ball Mill system consists of Wet Ball Mill, Wet Ball Mill Lubrication system, Mill circuit tank with an agitator, Mill circuit Pump, Mill Hydro cyclone, 3way distributor and accessories TECHNICAL SPECIFICATION OF WET BALL MILL EQUIPMENT
.jpg)
MODULE #5: FUNCTIONAL PERFOMANCE OF BALL MILLING
In this module, you will learn how to characterize the performance of ball mill circuits Specifically, after completing this module, you will be able to: List and describe the four elements of the Explain the role of ball mill in mineral industry and why it is extensively used Describe different types of ball mill design Describe the components of ball mill Explain their understanding of AMIT 135: Lesson 7 Ball Mills Circuits – Mining Mill Operator 1997年12月1日 Computer simulation of ball mill cicuits has been found to be very valuable for optimisation where existing plant data can be used to calibrate the mathematical models used Using modelling and simulation for the design of full scale ball mill The BAM ball mill for industrial minerals is designed to be particularly efficient thanks to our process knowhow This is because the efficiency of a mill depends on its internals All parts of BAM for industrial minerals Christian Pfeiffer
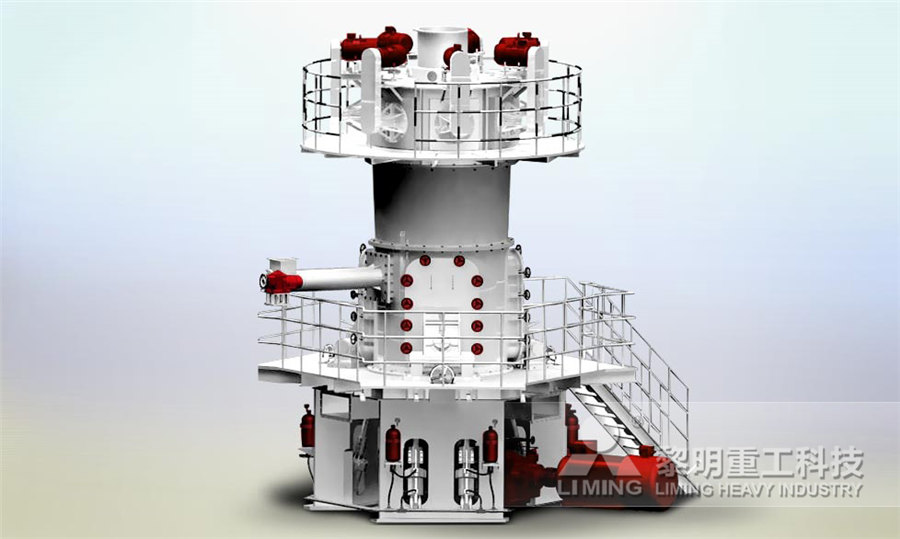
Metso QdX4 Mill Drive system
• Installation procedure is very similar to the alignment of a dual pinion drive • Trained onsite personnel can maintain drive system Standardization Allows for single line application with Optimised liner design can be used to strike the best economic balance between liner life and mill grinding performance, thus enhancing the profitability of a mining operation Protection of the The Selection and Design of Mill Liners 911 Metallurgistin combination with a ball mill for cement grinding applications and as finished product grinding units, as well as raw ingredient grinding equipment in mineral applications This paper will focus on the ball mill grinding process, its tools and optimisation possibilities (see Figure 1) The ball mill comminution process has a high electricalBALL MILLS Ball mill optimisation Holzinger Consulting2016年4月25日 With a view to developing a sound basis for the design and scaleup of ball mills, a large amount of data available in the literature were analyzed for variation of the two key mill performance Design and Fabrication of Mini Ball Mill (edited)
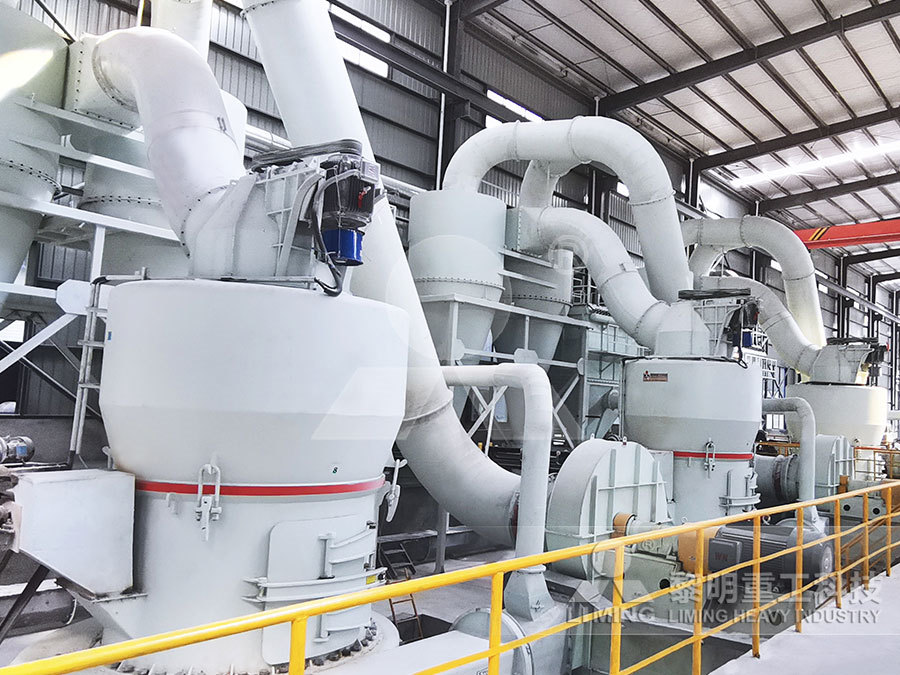
Ball Mills in the Mineral Processing Industry
2024年5月27日 Ball mills’ efficiency and performance can be optimised through proper design, maintenance, and advanced technologies like MechProTech’s TITAN Ball Mill and TITAN Automatic Ball Charger Investing in cuttingedge 2016年1月1日 For open circuit grinding [34,35], there is no disagreement with the calculation of the circulating load and classification efficiency, both of which 2 can be characterized relatively accuratelyAnalysis of the efficiency of the grinding process in closed circuit Ball mill pinion details Installation of Ball Mill Pinion 1 Before installing the pinion, carefully check the bearing pedestal, bearing cover, rolling bearing, pinion, shaft, and other parts, remove the burrs on the gear surface, and thoroughly clean them before installation 2Ball Mill Pinion for Sale Gears and Pinions for Ball Mill AGICOBALL MILL INSPECTION PROCEDURE source : thecementgrindingoffice Introduction This document is intended to help the staff of the cement plants On a process point of view, a mill inspection is only representative if the grinding mill circuit is in a steady working condition with a representative cement productCement Ball Mill Maintenance INFINITY FOR CEMENT EQUIPMENT
.jpg)
(PDF) Design of Threechamber Ball Mill ResearchGate
2021年1月1日 Comchambered with the design of Φ 35 × 13m threechamber ball mill, the design process of ball mill is described in detail General arrangement of the mill Filling rate of grinding body in each This cylinder rotates around its axis and transmits the rotating effect to the balls The material fed through the mill is crushed by the impact and ground as a result of the friction between the balls The drive system can either consist of a central drive (central gear unit: helical gear unit or planetary gear unit) or a girth gear unit with Industrial gear unit drive solution for ball mills SEWEURODRIVE2015年11月30日 If the rate of feed increased, coarser product will be obtained and if speed of rotation is increased the fineness for a given capacity is increases During grinding, the balls themselves wear and are continuously replaced by new ones so that mill contains balls of various ages Ball mill produces 1 to 50 ton/hr of powder and energy requirement of the ball mill is Ball Mill PPT SlideShareVertical roller mills and ball mills represent two clearly distinct technologies However, with proper adjustments to the operational parameters of the vertical roller mill almost identical cement properties can be achieved by the two mills that satisfy the cement user’s demandsNevertheless, the two types of mills have their distinctive meritsCement grinding Vertical roller mills VS ball mills
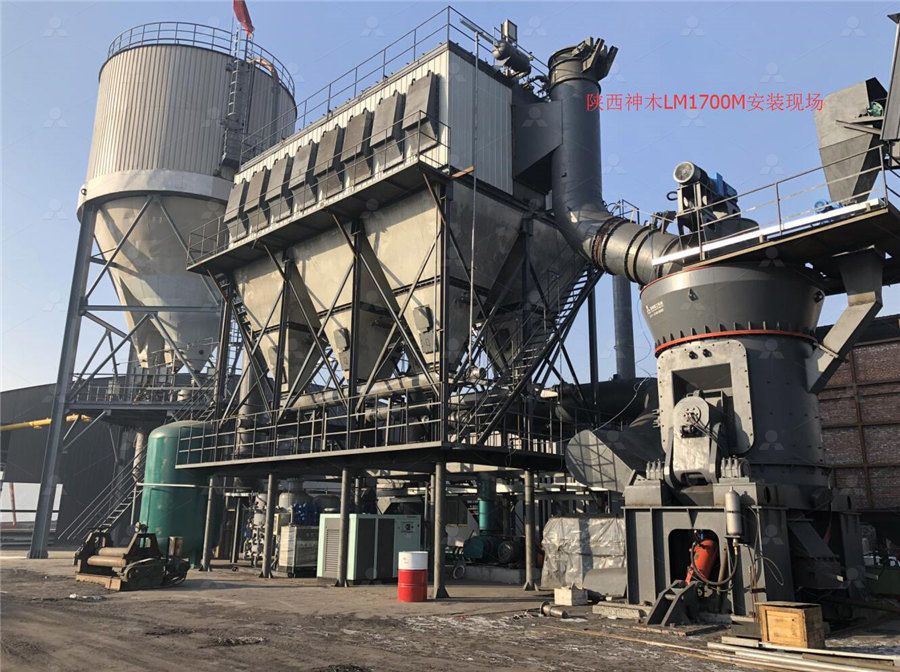
SAG Mill Design and Benchmarking Using Trends in the JKTech
Figure 3(a)—Pilot SAG mill Ecs vs Ball Load, Reproduced from Morrell (2006a); (b) SAG Mill Ecs vs Ball Load for ‘OpenCircuit’ SAG Mills in JKTech Database 0 2 4 6 8 10 12 14 16 18 20 0 2 4 6 8 10 12 14 SAG mill Ecs (kWh/t) Ball load (%) 0 5 10 15 20 SAG mill Ecs (kWh/t) Ball load (%) Coarse feed, uncrushed pebbles Very soft ores, Axb >80Based on the MPT TITAN™ design, the Mills are girth gear dual pinion driven with selfaligned flanged motors, running on hydrodynamic oil lubricated bearings The TITAN design enables you to run full process load 40% Ball charge at Ball Mills – MechProTech MPT2017年2月20日 Grinding Mill Specifications Data According to formula 423/√d, where d is equal to internal shell diameter within new liners In this case the thickness used was 60 mm for small mill sizes up to and including 2940 and 80 mm for larger millsGrinding Mill Design Ball Mill Manufacturer 911Metallurgistsince the first unit was installed in an operating plant at Hilton Concentrator, the units have increased their capacity 13 fold from 205 kW to 26 MW and their volume has increased 20 times Further to this, and the focus on this section of the paper, the design, fabrication, installation and commissioning of the project for the capacityCollaborative Technology Development – Design And Operation
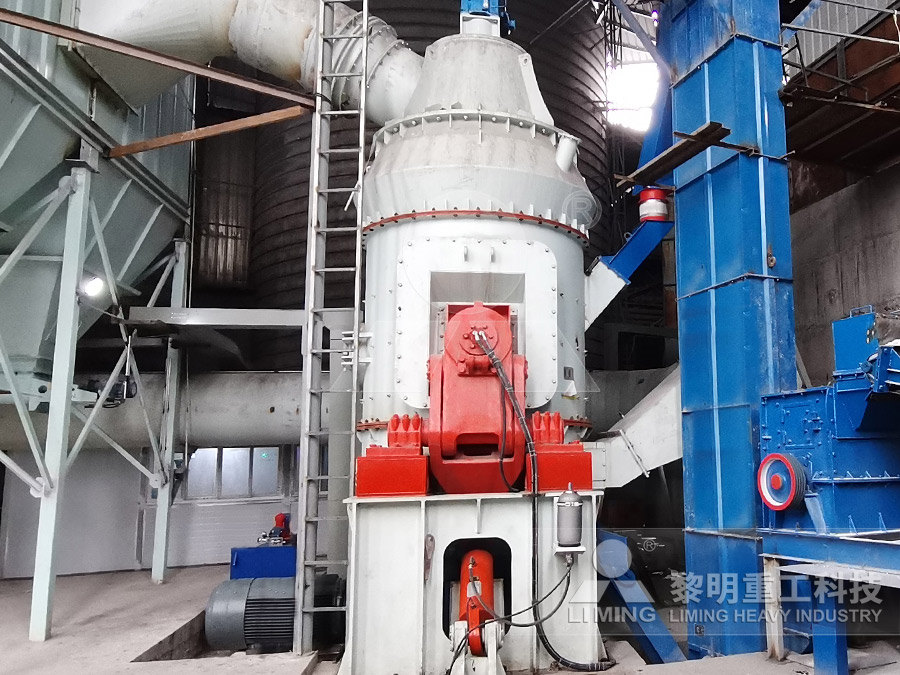
DESIGN AND FABRICATION OF MINI BALL MILL ResearchGate
2016年5月30日 This project is to design and fabricate a mini ball mill that can grind the solid state of raw materials into fine powder Ball mill is a cylindrical device that used to grind and blend raw Figure 5 High–low wave ball mill liner Materials The selection of the material of construction is a function of the application, abrasivity of ore, size of mill, corrosion environment, size of balls, mill speed, etc liner design and material of construction are integral and cannot be The Selection and Design of Mill Liners 911 Metallurgist2016年6月6日 Good Mill Liner Alloys And Design Installation and Prudent Operational Practices Prior to finalization of mill design the owner/operator or his appointee should meet with the mill designer/vendor, contracting/plant design engineer and foundry source to thoroughly review and consider such key factors (1) as: The milling application (See Table I)SAG Mill Liner Design 911Metallurgist2023年9月18日 The traditional Bond work index proposed by FC Bond over 60 years ago is still today a useful tool for characterizing material crushability and grindability in the minerals industryBond´s work index estimation using nonstandard ball mills

Ball Mill Liner Design 911Metallurgist
2016年1月5日 In rod mill work the design is such that they will easily pass through the large ball open end discharge trunnion Where cast liners are used, and especially in rod mill applications, we furnish rubber shell liner backing to help cushion the impact effect of the media within the mill and prevent pulp racing2018年4月8日 Unlock the principles of ball mill design with 911 Metallurgist This guide offers detailed calculations and practical tips to ensure your mill is optimized for performance, efficiency, and effective mineral processingBall Mill Design Calculations How to 911Metallurgist2016年5月26日 The larger mills are custom built according to your requirements Whatever these are there is a C I W Ball Mill built to meet your particular problem at the right price Ball Mill Capacity Table Small Muleback Small Ball Mills 911Metallurgist2024年5月8日 CIC has its own installation and commissioning team, which avoids the trouble incurred by the equipment production lineowner finding the installation and commissioning engineering team byBall Mill Installation And Kiln Installation by
.jpg)
Taurus Ball Mill NETZSCH Grinding Dispersing
NETZSCH Taurus Ball Mill, the pinnacle of fine and ultrafine grinding technology Achieve precise particle sizes with durable, lowmaintenance equipment NETZSCH Taurus Ball Mill, High volume capacities due to its advanced PDF On May 28, 2019, Girisha Lakhman Naik and others published Design and Performance of Ball Milling for Powder Metallurgy Composites Find, read and cite all the research you need on ResearchGate(PDF) Design and Performance of Ball Milling for Powder 2020年1月1日 The laboratory test work program was carried out on SAG belt cut and geounit samples of two BC copperporphyry orebodies yielding an exponent of056 across the range of typical ball mill (PDF) A SIMPLE METHOD OF ASSESSING BALL MILL HEALTH> Engineering approaches have highlighted mill performance with mill modelling and the use of improved materials > Liner design ,with the advent of large diameter SAG mills, the issues of design, selection, monitoring and evaluation of mill performance is critical > Mill trajectory modelling can be used to great effect in improving liner designThe Selection Design and Application of Mill Liners for Large Wet
.jpg)
Everything you need to know about cement Materials Preparation
In recent years, the use of ball mills and, more particularly, of airswept ball mill systems, is being overtaken by vertical roller mills This is essentially due to the fact that with increasing diameter and capacity of ball mills there is a decrease in their specific gas volume, when the permissible gas velocity in the mills is maintained (Figure 2320)Cement grinding unit is also called the cement grinding plant It consists of cement ball mill, dust collector, belt conveyor, bucket elevator, cement silo, powder concentrator, etc AGICO provides highquality clinker grinders and advanced cement grinding technologyCement Grinding Unit Clinker Grinder AGICO Cement2016年4月25日 This project is to design and fabricate the mini ball mill that can grind the solid state of various type of materials into nanopowder The cylindrical jar is used as a mill that would rotate the DESIGN AND FABRICATION OF MINI BALL MILL METHODOLOGY SMALL MULEBACK BALL MILL Small (Muleback Type) Ball Mill is built for “muleback” transportation in 30″ and 3′ diameters (inside liners) A 4′ (Muleback Type) Ball Mill is of special design and will be carefully considered upon request Mankind’s search for valuable minerals often leads him far away from modern transportation 05 TO 15 TPH SMALL SCALE MINER’S BALL MILL
.jpg)
Pilot chocolate ball mill FoodTechProcess
Steel balls for grinding chocolate are essential components used in ball/bead mills These 6 mm diameter balls are made out of hardened steel and are considered as consumables required for operating the BALL MILL 5 Spherical Paul O Abbé Equipment Company is a manufacturer New Steel Ball Mills and Milling Equipment Call 8005242188 or request a quote to get started About Section 179; Ball milling is one of the few unit operations that actual Steel Ball Mills and Milling Equipment Paul O AbbéBall mills are very effective for grinding smooth, aqueous, or oily dispersions by wet grinding since it gives particles of 10 microns or less Construction of Ball Mill: The basic parts of the ball mill are a shell, balls, and motor Fig2 A ball mill is Ball Mill Principle, Construction, Working, and MoreThere are different equipment that is used to make an efficient highenergy ball mill because the equipment involved is rich in its characteristics and enables a better working environment There are different application areas as well which have massively increased over time owing to the excellent growth that the high energy ball mills have provided to the industries that they High Energy Ball Mill Equipment and Its Application Areas
.jpg)
The selection and design of mill liners Academia
The Selection and Design of Mill Liners Malcolm Powell*, Ian Smit#, Peter Radziszewski§, Paul Cleary†, Bruce Rattray+, KlasGoran Eriksson‡ and Leon Schaeffer٭ *Mineral Processing Research Unit, University of Cape Town, Cape Town, South Africa, Anglo Research, Johannesburg, South Africa § Department of Mechanical Engineering, McGill A ball mill is a traditional grinding machine that has been used in the cement industry for decades It consists of a rotating cylinder filled with steel balls that crush and grind the material as the cylinder rotates Ball mills are known for their reliability and ability to grind materials to a fine consistency Advantages of Ball Mills:Vertical roller mill vs ball mill for cement grinding: Comparison mesh (17 mm) ensuring that the ball mill will work efficiently Coarser screens than 10 mm will cause serious losses in ball mill efficiency Ball mill feed must never exceed 80% passing 3 mm if reasonable ball mill efficiency is expected The practice of using ½ inch screens (trommels) is an encroachment on this limit and is perhaps the mostDesign SAG mill production when you need it most: In day 1 and 2010年3月10日 This project is to design and fabricate the mini ball mill that can grind the solid state of various type of materials into nanopowder The cylindrical jar is used as a mill that would rotate the (PDF) Optimization of mill performance by using online ball
.jpg)
(PDF) Effects of Ball Size Distribution and Mill Speed and Their
2020年7月2日 A comprehensive investigation was conducted to delineate the effect of ball size distribution, mill speed, and their interactions on power draw, charge motion, and balls segregation in a 2024年10月28日 A 4week modular course is designed to give the course attendee a solid understanding of the Ball Mill maintenance system and its auxiliary equipment The Ball Mill Maintenance course is designed to engage in the effective use of handson learning methodology as a unique combination of theory and practical work section applied to the ball mill BALL MILL MAINTENANCE The Cement Institute