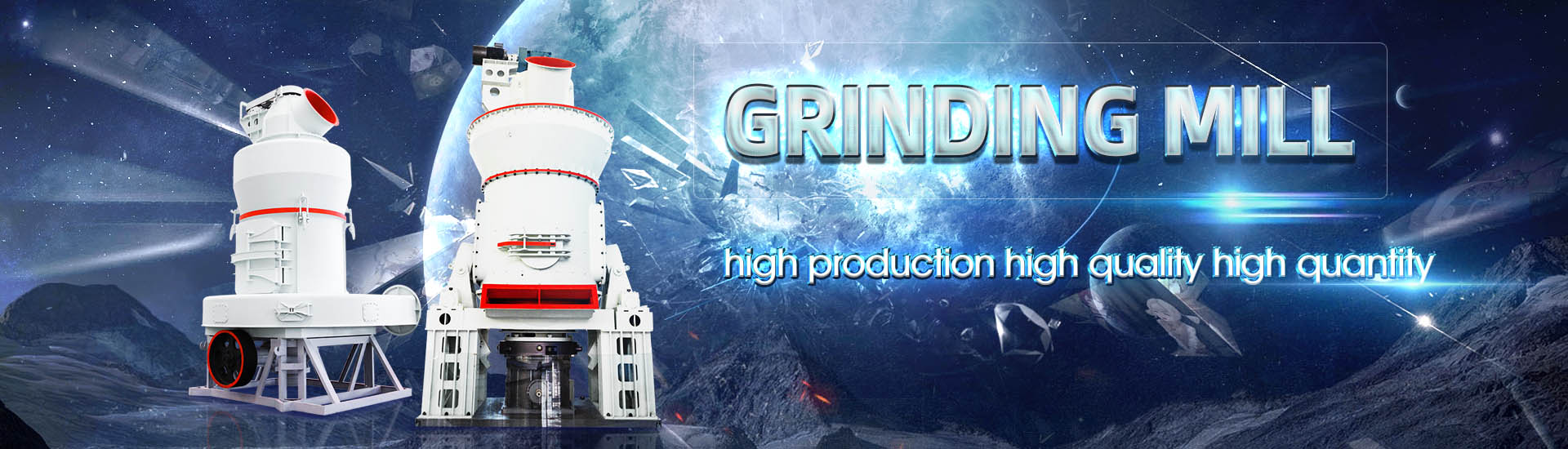
EM coal mill
.jpg)
Coal Mill an overview ScienceDirect Topics
Mills are mechanical devices used to break different types of solid materials in small pieces by grinding, crushing or cutting In pulverised coalfired power plants, a pulveriser coal mill grinds 摘要:结合新型静态分离器的结构特点,利用Fluent软件中湍流模型、离散相模型、随机轨道模型,对EM型磨煤机分离器内部空气流场、固体颗粒的运行轨迹和分级效果进行数值模拟。EM 型磨煤机分离器性能的数值模拟 University of Jinan2012年5月1日 The paper presents development and validation of a coal mill model to be used for improved mill control, which may lead to a better load following capability of power plants Derivation and validation of a coal mill model for controlThe Loesche coal grinding mill range is divided into two serial types: Small twin mills constructed to individual specifications (LM 122 D to LM 202 D), with table diameters from 1,200 to 2,000 LOESCHEMILLS
.jpg)
A unified thermomechanical model for coal mill operation
2015年11月1日 Coal mills are bottleneck in coal–fired power generation process due to difficulty in developing efficient controls and faults occurring inside the mills In this paper, a dynamic Designed without bearings or lubrication points inside the grinding section, the EM mill remains the simplest, most reliable means available for fine grinding coal and a number of other Grinding Claudius Peters, Technik GERMAN TECHNIKThe Claudius Peters EM Mill is the preferred grinding and drying technology for the production of pulverized bulk materials, such as coal and petcoke, metal ores and other materials A semi Grinding Claudius Peters2021年1月28日 Gaussian mixture model (GMM) is first applied to identify the operating modes of the coal mill Subsequently, combined with multioutput relevance vector regression (MRVR), A Novel MultiMode Bayesian Method for the Process
.jpg)
Pulverizer Wikipedia
A pulverizer or grinder or flour mill is a mechanical device for the grinding of many different types of materials For example, a pulverizer mill is used to pulverize coal for combustion in the 碗式中速磨煤机沿高度方向自下而上可分为四部分:驱动装置、碾磨部件、干燥分离空间以及煤粉分离和分配装置。 工作过程为:由电动机驱动,通过减速装置和垂直布置的主轴带动磨盘或 碗式中速磨煤机 百度百科Rejects discharged from coal mills are a mixture of different materials (iron pyrites, rocks, tramp metal, etc) with pulverized coal Magaldi engineered the MRS ® system to ensure their dry removal and mechanical transport from Dry Mill Rejects Handling system MagaldiKey words: Coal mill classifier, Cut size, Nonswirling inlet, Particle image velocimetry, Impeller rotational speed 摘要: The classification performance of model coal mill classifiers with different bottom incoming flow inlets was experimentally and numerically studiedThe flow field adjacent to two neighboring impeller blades was measured using the particle image velocimetry techniqueClassification performance of model coal mill classifiers with cip
.jpg)
Coal Mill an overview ScienceDirect Topics
A simple energy balance model of the coal mill is derived in (Odgaard and Mataji 2006), this model is based on a more detailed model found in (Rees and Fan 2003)In this model the coal mill is seen as one body with the mass m mThe following variables are defined: T(t) is the temperature in the coal dust flow in the mill, ṁ PA (t) is the primary air mass flow, T PA (t) is 3 Precise Control and Automation: Bellian Machinery's coal mills feature advanced control systems that enable precise control over various operational parameters Operators can adjust grinding variables, such as coal flow and mill rotation speed, in realtime to achieve the desired coal fineness and optimize mill performanceCoal Mill in Thermal Power Plant: Enhancing Efficiency and Coal grinding mills LOESCHE coal grinding mills are distinguished by characteristics that improve efficiency, (CG Group) of the advantages of its vertical roller mill technology LOESCHE has managed to gain a new customer in Nepal, namely the cement division of the Chaudhary Group based in KathmanduCoal Mills for Cement Plants LoescheA number of more than 2200 coal mills sold speaks for itself: on the basis of the proven MPS mill technology, The raw coal is dried while being ground in the mill even if feed moisture exceeds 25% The feed size that can be handled is up to 100 mm, making twostep precrushing unnecessary Our products for coal and petcoke preparation Coal mills for all requirements Gebr Pfeiffer
.jpg)
Coal Mill Safety: A Critical Aspect of Power Plant Operations Coal
Proper Ventilation: Ensuring adequate ventilation in the coal mill area helps disperse coal dust and reduce the risk of ignition Ventilation systems must be designed to handle the specific needs of the mill Regular Maintenance: Routine maintenance of coal mills and associated equipment is vital for preventing mechanical failuresAnalysis of Coal Mill Operation Free download as PDF File (pdf), Text File (txt) or read online for free This document analyzes the comilling of coal and wood biomass in a ringball mill It describes tests conducted pulverizing hard coal with additions of 8% and 16% pine sawdust at different moisture contents Key findings include: 1) Biomass has weaker grinding properties Analysis of Coal Mill Operation PDF Mill (Grinding) ScribdIn discussion: Coal Mill Safety At best, coal mill safety is not well understood and, at worst, it is ignored When it comes to coal mill systems, most cement plant operators just presume that the supplier of the equipment knows all of the standards and rules and is 100% capable of making a system that conforms to these and is therefore safeIn discussion: Coal Mill Safety Coal Mill Safety, Explosion and Consultor en Coal Mill Safety Pte Ltd Nº 1011 • Julioagosto de 2022 43 Revista técnica • El espacio que ocupa el sistema es pequeño y no necesita muchas escaleras ni pasillos, y se puede mantener limpio fácilmente • Sólo se instalan en su estructura los equipos queProtección contra incendios Coal Mill Safety, Explosion and Fire
.jpg)
LOESCHEMILLS
1927 First Loesche coal mill delivered for the Klingenberg power station in Berlin 1953 500th coal mill plant sold worldwide 1961 Introduction of hydraulic spring assembly system 1965 Construction of first pressure mill (LM 122 D) 1980 Delivery of first modular coal mill (LM 263 D) 1985 Delivery of first selfinerting coal grinding plant (LM 212 D) for the steel industry (PCI Coal mills, essential components in power generation and various industrial processes, pose significant safety risks if not properly managed These mills, used to grind coal into a fine powder for combustion, present potential hazards such as fire, explosion, and mechanical failures This article outlines best practices and precautions to ensure thBest Practices and Precautions Coal Mill Safety, Explosion and Safe coal handling practices are designed to ensure that the fuel remains intact throughout its journey from the mine until the point at which it is ignited in the boiler Risks of unwanted combustion occur everywhere the coal is handled, processed or stored, including railcars, HE HE COAL MILL COAL MILL Derek Stuart, AMETEK Land, and Todd COAL MILL Land Instruments InternationalThe coal is fed into the coal mill via an inlet pipe so that the coal mill can pulverize the coal into particles Materials:Coal, cement clinker, limestone, calcite, dolomite, talc, etc Product Advantages The use of new wearresistant materials greatly improves the service life of Coal Mill Shanghai Zenith Company
.jpg)
Milling Biomass / Coal AMETEK Land
The coal mill is a key ancillary to any pulverized fuel boiler It grinds the coal to a fine powder so that it can be burned with maximum efficiency Biomass also moves through hammer mills, dryers and pulverizers during the production process Avoiding mill explosions is essential for personnel safety and asset protectionThe simulation models representing several coal mill subcomponents were integrated to investigate the complex interconnectivity between all parts of the combustion system This approach mitigates the risks associated with unrealistic or oversimplified assumptions regarding boundary conditionsDesign optimization makes lower quality coal economically viable coal mill Your contact partners Katalin Leimeter Get in touch Music Fehim Get in touch Get In Touch Company* First name* Last name* * Phone* Message Submit Choose market Wind Power Plants Power Plant Technology Industry Motors Marine Oil Coal Mill For CoalFired Power Plant ELIN MotorsIn November 2011 Loesche GmbH obtained a contract for the first ever 4roller coal mill for the injection of pulverized coal into a blast furnace (PCI technology) The Loesche Mill Type LM 434 D has a capacity of 120 t/h and will be installed in the A coal mill for the injection of pulverized coal

An investigation of performance characteristics and energetic
2020年8月12日 This study shows the performance of a currently running vertical roller coal mill (VRM) in an existing coalfired power plant In a power plant, the coal mill is the critical equipment, whose The air swept coal mill is a coal grinder usually used in the cement production line MFB series air swept coal mills with different capacities and dimensions can be customized by AGICO group Skip to content Blog Contact About Cases Factory CONTACT US info@cementplantequipment CALL US +86 REQUEST A QUOTEAir Swept Coal Mill Coal Mill In Cement Plant AGICO GROUPUsing AMETEK Land’s unique detection system, Millwatch provides continuous, accurate monitoring of CO levels – improving process safety, protecting expensive mill equipment, and preventing costly downtime from unnecessary Millwatch: Coal and Biomass Mills Carbon Monoxide 2020年4月2日 : Fuel and firing system purposely to deliver light fuel oil or coal as one of the primary elements of fuel in an ideal condition for combustion to take place in the boiler combustion chamberAnalysis of the Coal Milling Operations to the Boiler
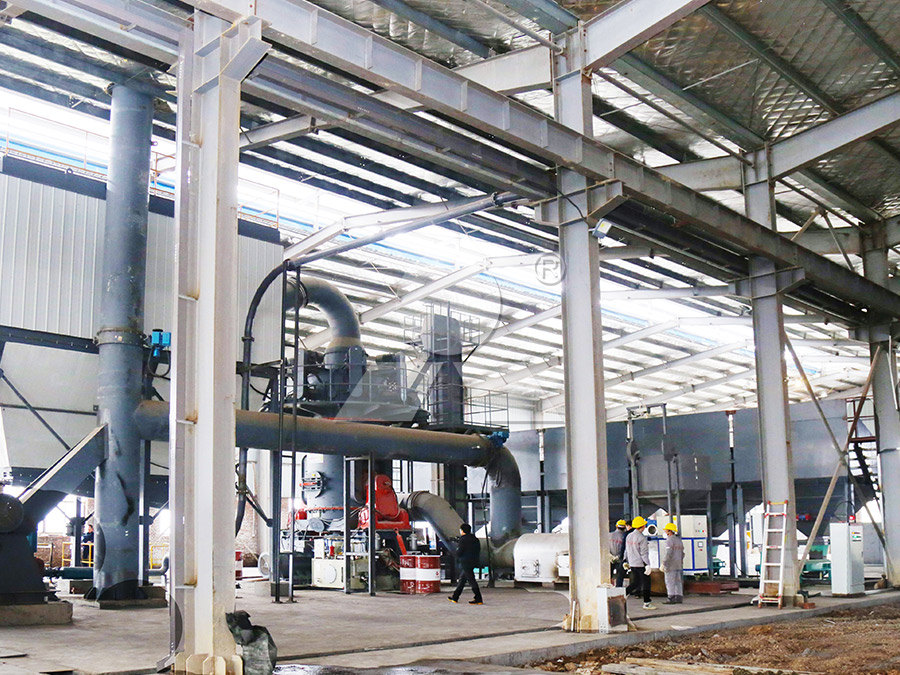
Optimization control of a pulverizing system on the basis of the
Abstract This study aimed to master the operating characteristics of a pulverizing system, improve the output control precision of the system, and reduce the fluctuation amplitude of the main operating parameters of coalfired units A nonlinear dynamic model of a directfired pulverizing system that considers the effect of coal moisture on the energy balance of a coal mill was coal mill Your contact partners Katalin Leimeter Get in touch Music Fehim Get in touch Get In Touch Company* First name* Last name* * Phone* Message Submit Choose market Wind Power Plants Power Plant Technology Industry Motors Marine Oil Coal Mill For CoalFired Power Plant ELIN Motors2012年5月1日 Sensors for coal flow measurement from the mill to the furnace have become available on the market (Blankinship, 2004, Department of Trade and Industry, 2001, Laux et al, 1999)Unfortunately the equipment tends to be expensive and requires frequent calibration; thus it cannot be used directly for control purposes at this time of writingDerivation and validation of a coal mill model for control520 P Niemczyk et al / Control Engineering Practice 20 (2012) 519–530 Nomenclature Dpmill mc mpc mcair mass of unground coal on the table (kg) mass of pulverized coal on the table (kg) mass of pulverized coal carried by primary air (kg) wc wpc wout wret mass mass mass mass flow flow flow flow of of of of the dry raw coal to the mill (kg Derivation and validation of a coal mill model for control
.jpg)
A Fault Early Warning Method for Coal Mills Based on Causality
2024年9月4日 Tao, W, Mao, D: Coal mill fault warning method based on optimized XGBoost In: 2022 4th International Conference on Electrical Engineering and Control Technologies (CEECT), pp 385–390 IEEE, December 2022 Google ScholarThe four most common coal pulverizers types are: BallTube Mills This type of mill consists of a rotating tube filled with cast alloy balls Coal is introduced through two hollow trunnions on each side of the tube As the tube rotates, the balls tumble onto the coal, crushing and pulverizing it Coal Pulverizer – Power Plant Pall CorporationThe ATOX mill will grind and dry coal containing more than 20% moisture in one operation The possibility of customersupplied parts, along with the low civil costs that accompany compact mill installation, add to the excellent economy of the ATOX coal mill Working principles The raw coal enters the mill via a rotary sluice and feed chuteATOX COAL MILL FLSmidth CementSafe operation of coal grinding systems: Raw coal silo protection against fire and explosions Safe operation of coal grinding systems: Raw coal yard management The purchasing process for coal grinding systems needs changes Talk at a virtual seminar, November 2023 Accept the probability that the fire and explosion safety of your coal grinding system is nothing more than a mirageCoal Mill Safety, Explosion and Fire Protection Consultancy
.jpg)
Coal mill motor and large power
YTM / YHP / YMPS Series Documentation YTM series electric motor is matched specially with the tubular shape coal grinder; YHP series is matched with bowl shape coal grinder YMPS series is matched specially with MPS bowl shape 2022年10月24日 We are delighted to announce we will be holding an EM Mill User Group Training Conference next month Time Date: 8am – 5pm 10 November 2022 Venue: Plano Marriott, Legacy Town Center, 7121 Bishop EM Mill User Group Training Conference Claudius A bowl mill for a coal pulverizer with an air mill for primary entry of air, comprising a substantially closed separator body ( 2 ) having a central axis; and a bowllike grinding table ( 3 ) mounted on a shaft ( 4 ) rotatable about said central axis, cooperating with a plurality of grinding rolls ( 6 ) The airmill is provided with multiple entry openings ( 17′, 17″; 18′, 18″; 21, 25 USB2 Bowl mill for a coal pulverizer with an air mill for Coal feeder Coal feeders are used in the power plant industry for mill coaling Usually, the coal feeders are connected to the respective coal bunker via a coal chute The coal is transported in the upper run by direct removal from the material column on the upper run The height of the removed bulk material []Coal feeder HEKO Group EN
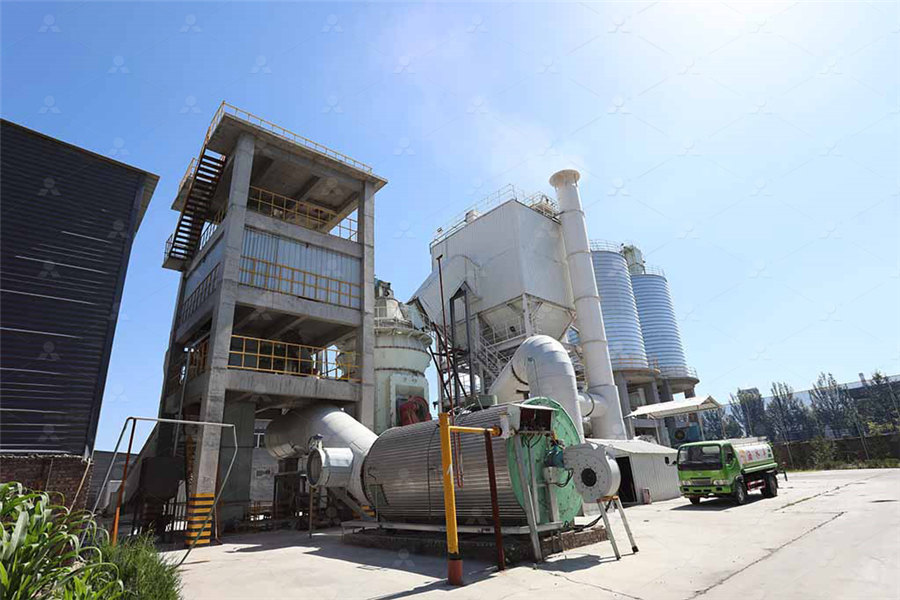
Coal Dust Explosion Protection: Ensuring Safety in industries using
Coal dust explosions are among the severe hazards in industries using coal, posing significant risks to personnel and infrastructure These explosions occur when fine coal particles become airborne and come into contact with a heat source in an enclosed environment, leading to a rapid combustion event Given the catastrophic potential of such incidents, robust measures for coal 2013年3月18日 The screw mill was founded in 1872, the coal mill building originates from approximately 1900 The original twostoreyed edifice of 121 by 175 metre and height of 11 metre was split in 1965 by a Coal Mill by Atelier Hoffman Dezeen2019年4月15日 HP mills produced by SEHPS are widely liked by customers because of its better adaptability for various coals, high operational reliability, easy and low maintenance Until 2019, SEHPS has produced more than 4500 sets of HP mediumspeed coal mill which were installed in almost 300 50MW100MW power generator at home and abroad, and all installed 上海电气上重碾磨特装设备有限公司2012年11月17日 20 131Fineness Fineness is an indicator of the quality of the pulverizer action Specifically, fineness is a measurement of the percentage of a coal sample that passes through a set of test sieves usually designated at 50, 100, and 200 mesh A 70% coal sample passing through a 200 mesh screen indicates optimum mill performance The mill wear and Coal mill pulverizer in thermal power plants PPT SlideShare
.jpg)
Analisa Ekonomis Peralatan Pulverizer untuk Optimalisasi Neliti
2 Salah satu komponen vital mill pulverizer adalah mill termasuk table 3 Perhitungan dengan menggunakan Life Cycle Cost Analysis (LCCA) Dengan LCCA pada komponen pulverizer level 2 terdiri dari feeder, motors and drives, mills, mill coal level controls, coal leak, control system, other pulverizer problems dan inspection 4with the coal mill in Lixhe were checked and certified by the TÜV Rhineland technical inspection authority Plant layout Figure 3 shows the plant process diagram The coal is fed into the MPS 225 BK (2) through a pressure shockresistant, selfpurifying rotary feeder (1)COAL GRINDING IMPS: more than meets the eye Gebr Pfeiffer