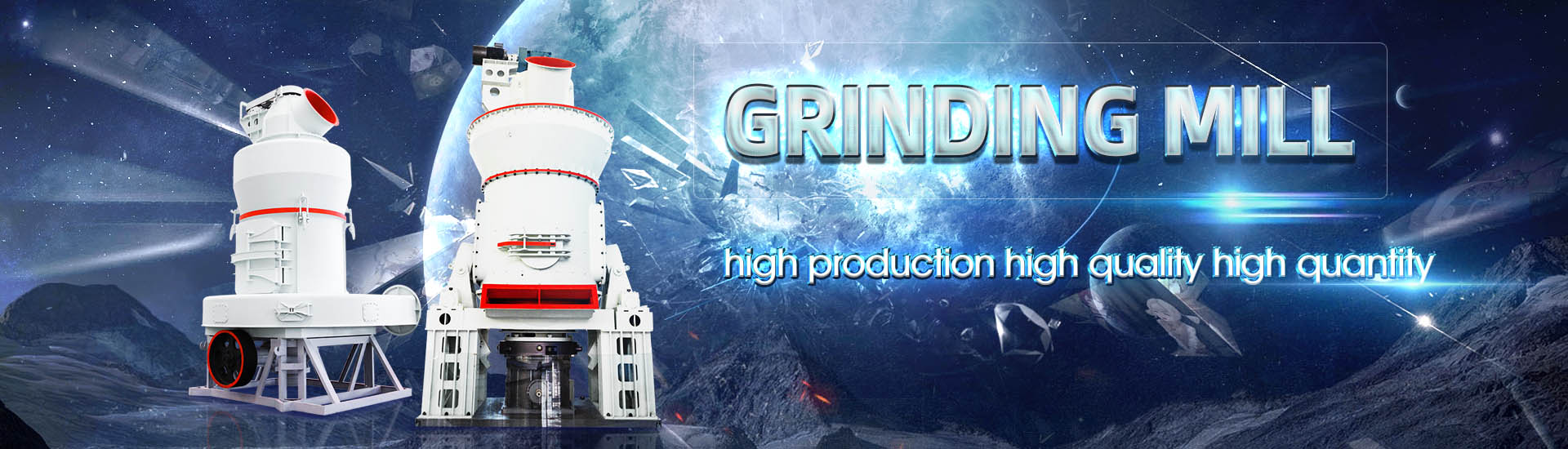
Lime kiln process flow chart
.jpg)
22 Lime Kiln Principles and Operations TAPPI
Lime Kiln Principles And Operations Terry N Adams Technical Consultant Seattle WA Slide 2 Outline • Lime kiln equipment – flames, chains, refractories – product coolers, external mud A new and innovative Parallel Flow Regenerative lime kiln process using 100% blast furnace gas achieves the same performance as a natural gasfired PFR lime kiln; however, with New PFR lime kiln process with blast furnace gas and oxygenGeneral process flow diagram for the manufacturing and processing of lime Source: Midwest Research Institute Emission Factor Documentation for AP42, Section 1115, LimeLime Production: Industry ProfileLime Kiln Maintenance Chain System • Inspect Maintain on Every Major Shutdown – Check for chain thickness missing chain • Chain Check Kit (Drawing, Tape measures, Box end Lime Kiln Principles and Operations TAPPI
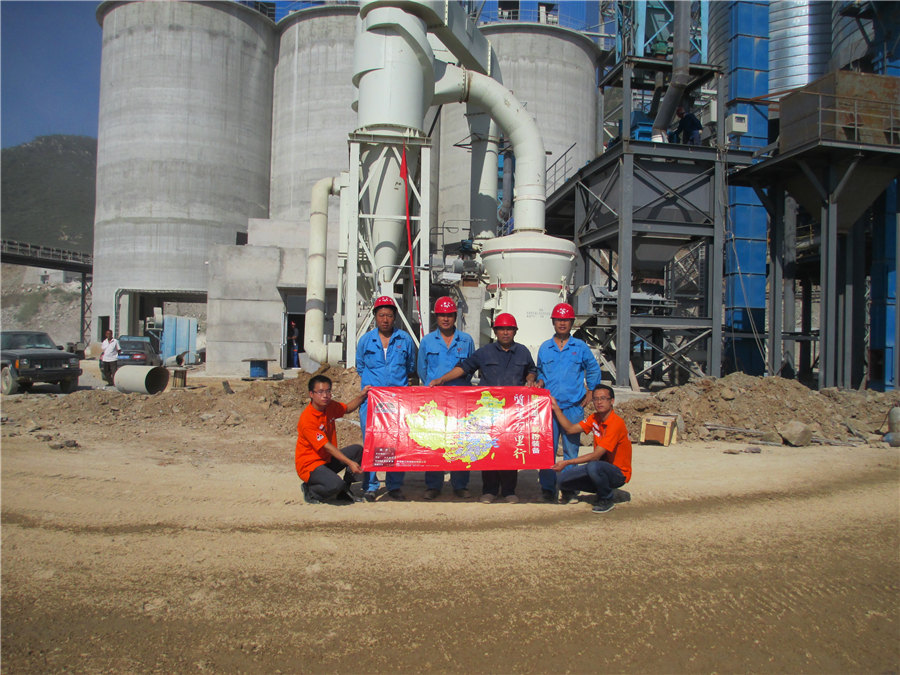
LIME MANUFACTURING Analyse to excel Cimprogetti
process in the shaft kiln The final goal of this collaborative research activity is to design a shaft kiln that takes into account the impacts of raw materials and fuels Cimprogetti’s analytical In some lime plants, the resulting lime is reacted (slaked) with water to form hydrated lime The basic processes in the production of lime are: (1) quarrying raw limestone; (2) preparing 1117 Lime Manufacturing US Environmental Protection AgencyTo meet the demands of lime applications across the markets where it is used, lime is manufactured using natural gas as the kiln fuel using two types of gasfired kiln; vertical shaft Making Limeencourage the flow of material through the chain system, down the kiln In general the typical industry standard for overall quantity of chain in a modern lime kiln is 40 lineal hanging feet of 25 Lime Kiln Equipment Operation and Maintenance TAPPI
.jpg)
Kiln Types European Lime Association
Some shaft kilns can be operated on natural gas, liquid and solid fuels This type of kiln tends to produce medium reactivity quicklime, which can then be used in a number of industrial processes including the manufacture of iron and steel and aerated concrete blocks Quicklime from shaft kilns is also processed into hydrated limeMaerz PFR kiln with its characteristic doubleshaft design and the Maerz HPS single shaft kiln with laterally adjustable liquidcooled burners protrud ing into the material bed at the lower end of the burning zone All Maerz 1 Rectangular Maerz PFR kiln for high reactive lime (left) and Maerz HPS kiln for medium and low reactive lime (right)The Maerz hybrid kiln for variable lime reactivitythe exterior of a modern rotary limereburning kiln Slide 4 shows a schematic of the interior features of a limereburning kiln Rotary lime kilns are large steel tubes that are lined on the inside with refractory bricks They are slightly inclined from the horizontal and are slowly rotated on a set of riding rings Lime mud is introduced at the22 Lime Kiln Principles And Operations TAPPIDownload scientific diagram Stages in cement production flow chart [43] from publication: A review on kiln system modeling The purpose of this study is to evaluate performance cement of Stages in cement production flow chart [43] ResearchGate
.jpg)
Lime Kiln Principles and Operations TAPPI
Lime Kiln Equipment and Maintenance Glenn M Hanson, III Technical Sales Support, Pyro North and Central America Metso Outotec TAPPI Kraft Recovery Course 2 Lime Flow 32 Refractory Damage Can Lead to Kiln Shell Damage Refractory Wastage Refractory Collapse 33Competitive and Efficient Lime Industry Cornerstone for a Sustainable Europe – EXECUTIVE SUMMARY EuLA – The European Lime Association eula Improving the energy efficiency is another important option to reduce energy related emissions Vertical lime kilns, such as the Parallel Flow Regenerative Kiln, are already highlyA Competitive And effiCient Lime industry European Lime A PFR (Parallel Flow Regenerative) kiln has two vertical shafts with a connecting crossoverchannel Both shafts work together: one calcines the product, the other preheats the kiln feed This process works in cycles, switching the functionality of the shafts from “burning shaft” to “regenerative shaft” every 1015 minutesHow the PFR kiln works Maerz Ofenbau AGQuicklime When a calcium limestone or chalk rock, that comprises mainly of calcium carbonate (CaCO 3), is heated in a kiln, it changes by a process called calcination into quicklime also known as 'burnt lime' and chemically is mainly calcium oxide (CaO), and the calcination process releases a gas from the rock which is carbon dioxide (CO 2) Hydrated LimeMaking Lime
.jpg)
Limestone Quarrying and Processing: A LifeCycle Inventory
Nevertheless, the process is relatively simple: locate or create (minimal) breaks in the stone, remove the stone using heavy machinery, secure the stone on a vehicle for transport, and move the material to storage A flow diagram of typical quarrying operations is shown in Figure 1 Figure 1 Process flow diagram for limestone quarrying operations2022年6月24日 The lime industry is a highly energy intensive industry, with a huge presence worldwide To reduce both production costs and pollutants emissions, some lime production plants are introducing more environmentallyfriendly energy sources, such as local agroindustry residues In this paper, a numerical tool is presented, which simulates a largescale Parallel CFD Analysis of Cofiring of Coke and Biomass in a Parallel Flow Production of high reactive lime is now possible with inexpensive blast furnace gas A new and innovative Parallel Flow Regenerative lime kiln process using 100% blast furnace gas achieves the same performance as a natural gasfired New PFR lime kiln process with blast furnace gas and impurities in the makeup lime and refractory bricks used in the kiln, the efficiencies of slakers, causticisers, clarifiers and mud washers, and the burning conditions in the kiln On a dry basis, lime mud typically contains about 95 wt% CaCO 3 and 5 wt% of impurities As lime mud moves through the kiln, theLIME KILNS, HEAT TRANSFER, CONTROL AND COMBUSTION
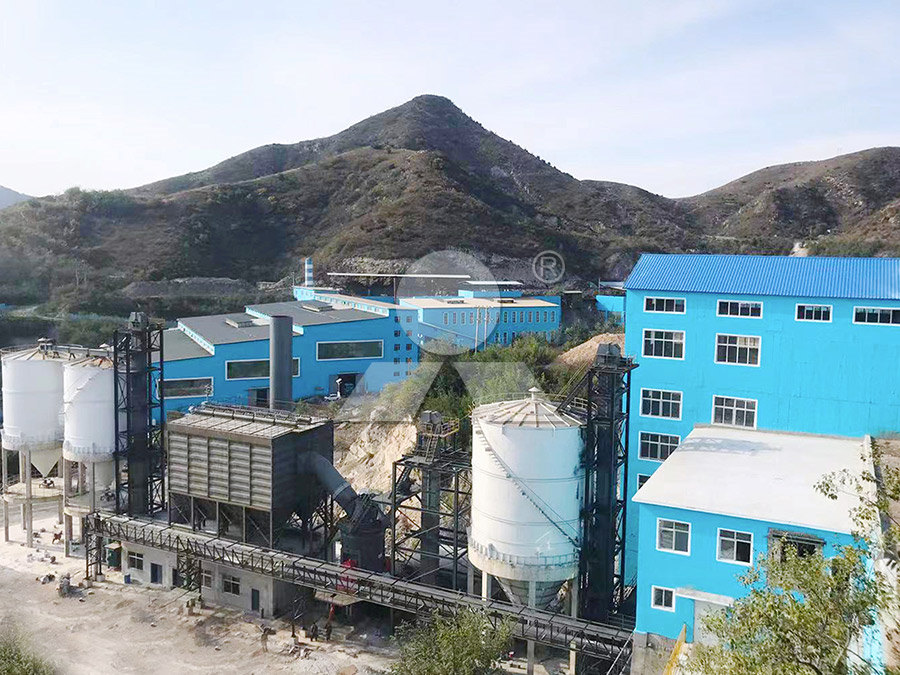
Schematic diagram of a rotary lime kiln ResearchGate
Download scientific diagram Schematic diagram of a rotary lime kiln from publication: Computer Simulation of Heat Transfer in a Rotary Lime Kiln In the present work, a steadystate, finite AMMONIA RECOVERY – PART OF THE SOLVAY PROCESS Ammonia – considered a catalyst as it is not consumed in the reaction and allows the reaction to proceed o Recovered as ammonia is expensive CaO from lime kiln is slaked (reacted with water), forming calcium hydroxide (slaked lime) 𝑪𝒂 (𝒔)+𝐻2 (𝑙)→𝐶𝑎( 𝐻)2 (𝑎𝑞)CHEM 956 THE SOLVAY PROCESS2013年3月16日 The gas based process uses a shaft furnace for the reduction reaction The coal based process uses any one of the four types of reactors for the reduction reaction These reactors are (i) rotary kiln, (ii) shaft furnace, (iii) fluidized bed reactor, and (iv) rotary hearth furnace Rotary kiln is the most popular reactor for the coal based processDirect Reduced Iron and its Production Processes – IspatGuruto total process flow solutions partnership provided brine lime calcium magnesium reducing reactors lithium carbonate reactors eimco® dilution clarifier eimco carbonate clarifier eimco vacuum filter impurities (mg, ca, al, fe) eimco vacuum filter flsmidth rotary dryer pneumatic transport air classifier milling flsmidth ventomatic® bagging Lithium processing technology Complete solutions that FLSmidth
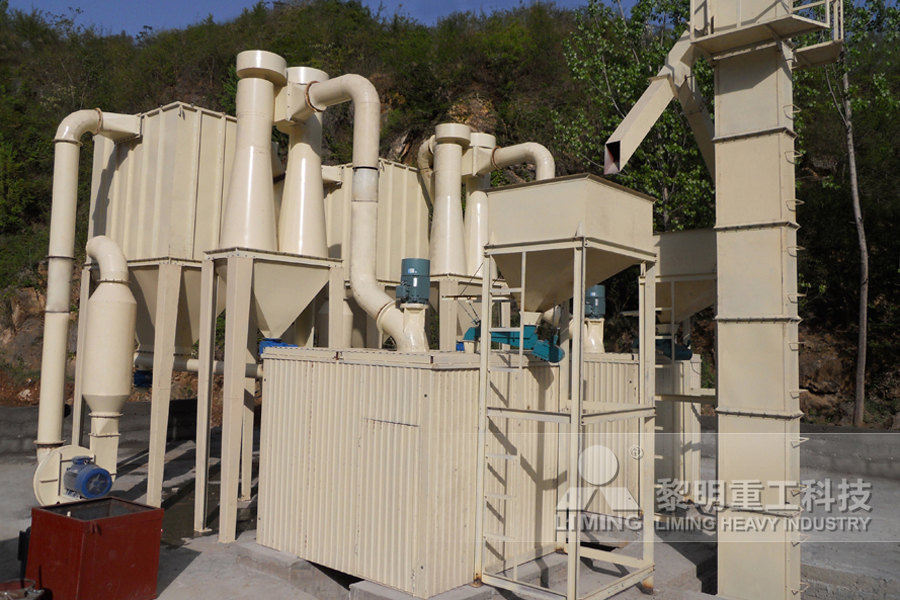
Understanding the process conditions in a parallel flow regenerative kiln
Understanding the process conditions in a parallel flow regenerative kiln TEXT DrIng Thomas Schlegel, DiplIng (ENSCCF) Guilhem Padox, EESAC SAS Duingt/France A lime manufacturer operates a 300 tons per day Parallel Flow Regenerative Kiln (PFRK), fired with natural gas The kiln is fed with 4080 mm limestone, but in order to maximize2013年3月25日 Flow Chart : Chemistry Quick lime is heated with NH 4 Cl to form NH 3 and calcium chloride (by product) Ammonia is used again in this process 2NH 4 Cl + Ca quick lime process flow diagram Mining Quarry Plant2019年11月30日 In India, the wet process has been replaced to a wide extent by the dry process, mainly for fuel and heat economy However, air pollution is reduced in the wet and semidry processes Dry process (modem technology) is now preferred and adopted in most of the cement industries due to the following reasons :Manufacture Of Portland Cement Process Flow chart civil 2014年6月10日 Evolution of the cement Process • Wet process easiest to control chemistry better for moist raw materials • Wet process high fuel requirements fuel needed to evaporate 30+% slurry water • Dry process kilns less fuel requirements • Preheater/Precalciner further enhance fuel efficiency allow for high production ratesCement manufacturing process PPT Free Download SlideShare
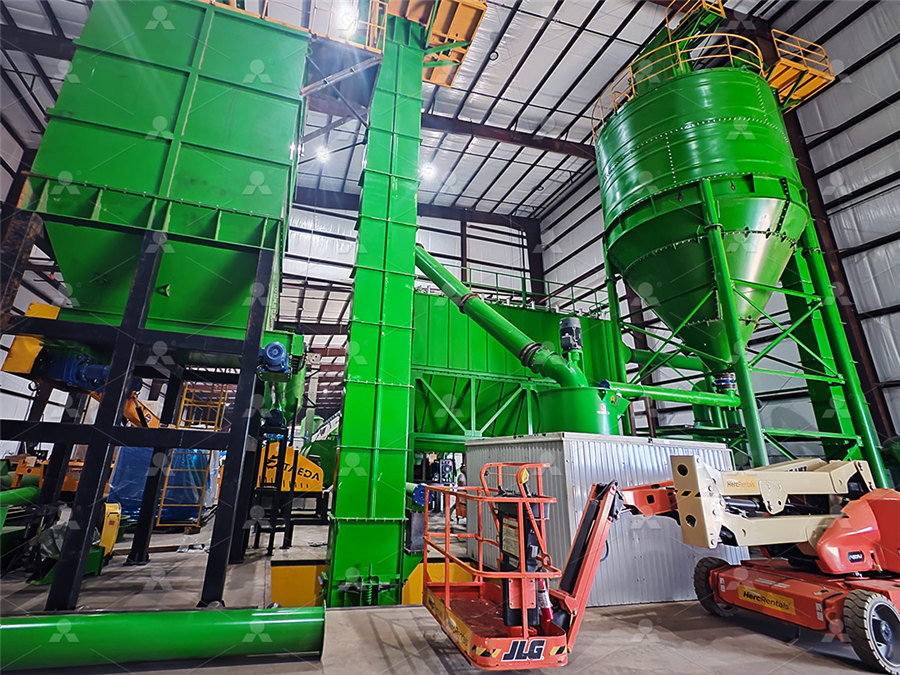
Soda ash manufacturing and process flow diagram
2017年11月19日 It then provides the overall reaction and a process flow diagram depicting the major steps These steps include: 1) ammonia absorption into salt water, 2) production of carbon dioxide from limestone, 3) carbonation encourage the flow of material through the chain system, down the kiln In general the typical industry standard for overall quantity of chain in a modern lime kiln is 40 lineal hanging feet of standard 3/4” x 3” link chain per ton per day of total kiln product or 240 lbs of chain per25 Lime Kiln Equipment Operation and Maintenance TAPPIA lime kiln is around 70100 meters long and around 24 meters in diameter The kiln is typically equipped with product coolers at the discharge end where hot reburned lime meets incoming secondary air in a countercurrent heatexchange process Dusting in a lime kiln occurs when fine material chaotically swirls at the discharge end of the kilnDusting in a lime kiln Chalmers4 天之前 The manufacture of Portland cement is a complex process and done in the following steps: grinding the raw materials, mixing them in certain proportions depending upon their purity and composition, and burning them to sintering in a kiln at a temperature of about 1350 to 1500 ⁰C During this process, these materials partially fuse to form nodular shaped clinker by Manufacturing of Portland Cement – Process and Materials
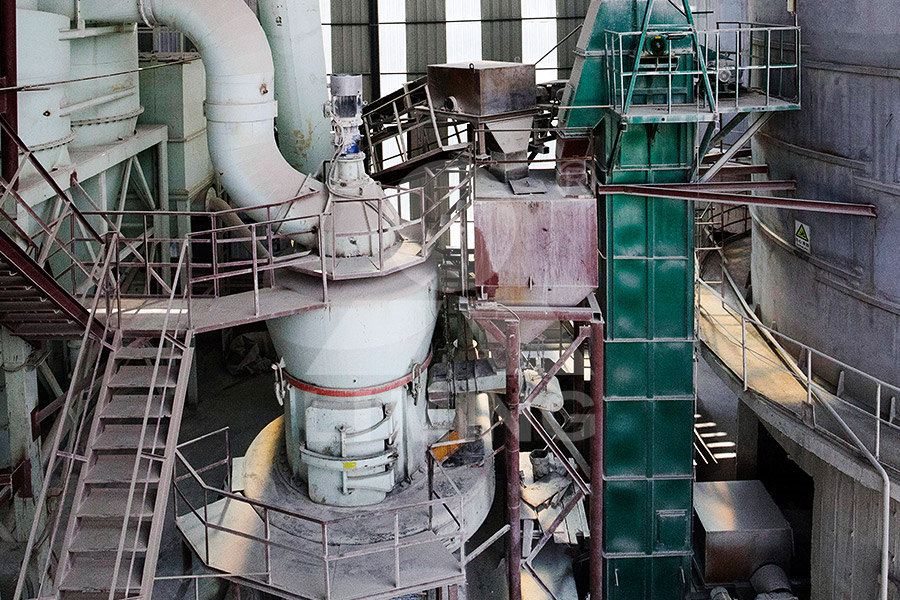
Comparison of lime kiln types Blitzco
32 Parallel flow regenerative kiln This type of lime shaft kiln was developed at the beginning of the 1960ies in a lime factory in Wopfing / Austria The patent was transferred in 1965 to Maerz Ofenbau AG in Zurich / Switzerland which then further developed the kiln process and the kiln design [4] 321 Process DescriptionThe new 200 t/d Maerz PFR lime kiln was com missioned in October 2020 To meet the steadily in creasing market requirements, a new PFR lime kiln with aftercooler and natural gas firing was used This new lime kiln was designed for especially low residual CO 2 content and especially high reactivity of the quicklime Hence it was necessary to New and innovative Maerz PFR lime kiln for Kalkfabrik Netstal in LIME KILN COMBUSTION, HEAT TRANSFER AND OPTIMIZATION Richard Manning Former Director Chief Technology Officer, KFS INTRODUCTION The location of the lime kiln on the Kraft recovery process is shown below COMBUSTION AND HEAT TRANSFER The combustion process involves conversion of fuel to oxidized components releasing energy26 Lime Kiln Combustion, Heat Transfer and Optimization 2019used by the process engineers to calculate the thermodynamic behaviour of the limestone into the kiln, adopting modern mathematical tools combined with other fundamental information, such as the fuel type, rock size and process conditions (see Figure 3) As a rule, the kiln capacity and rock feed size are not the governingLIME MANUFACTURING Analyse to excel Cimprogetti
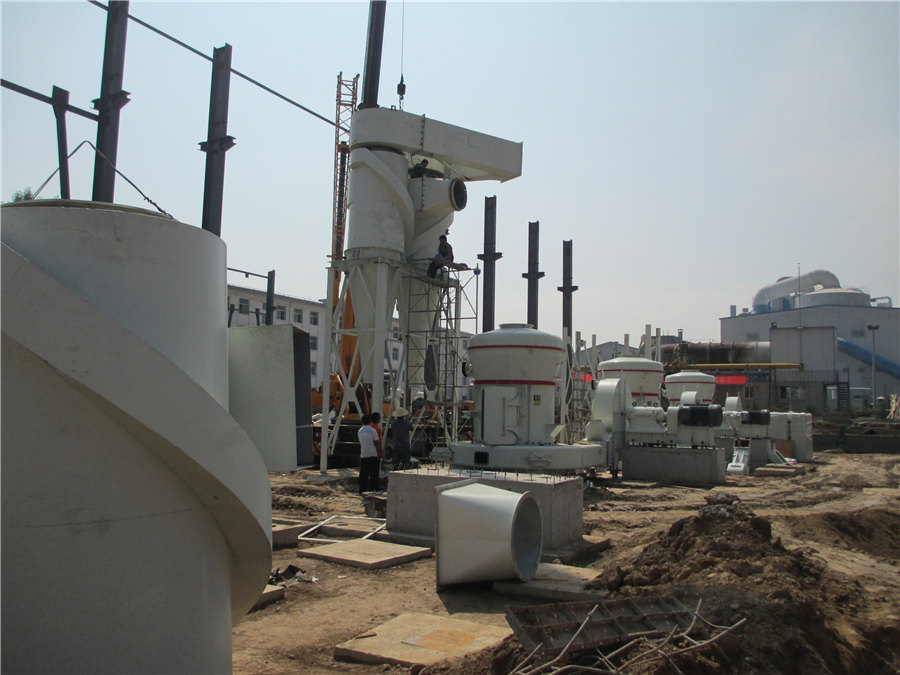
Our PFR kiln is still unbeaten today Maerz Ofenbau AG
The invention of the Maerz PFR kiln process was a big step towards increasing the efficiency of the lime burning process With an efficiency of 85 % of the heat energy used, the PFR process is still unbeaten today We have continuously developed our PFR kilns based on our experience and technical innovations and offer this kiln in two seriesAnother alternative process that is beginning to emerge in the United States is the parallel flow regenerative (PR) lime kiln This process combines 2 advantages First, optimum 1/95 Mineral Products Industry 11171 Figure 11171 Process flow diagram for lime manufacturing4 (SCC = Source Classification Code) 11172 EMISSION FACTORS 1/951117 Lime Manufacturing2023年2月25日 The angle of repose is an intrinsic characteristic of a given material; it depends principally on: particle size, rotational speed of the kiln (Fig 2), and surface condition of the kiln wallMore specifically, this angle characterizes the flow properties of “solid particles” in the kiln; it is often assumed to be constant but may vary along the length of the kiln, in correlation with Rotary kiln process: An overview of physical mechanisms, models Another alternative process that is beginning to emerge in the United States is the parallel flow regenerative (PR) lime kiln This process combines two advantages First, optimum heating conditions for lime calcining are achieved by concurrent flow of the charge material and combustion gases Second,Emission Factor Documentation for AP42 Lime Manufacturing
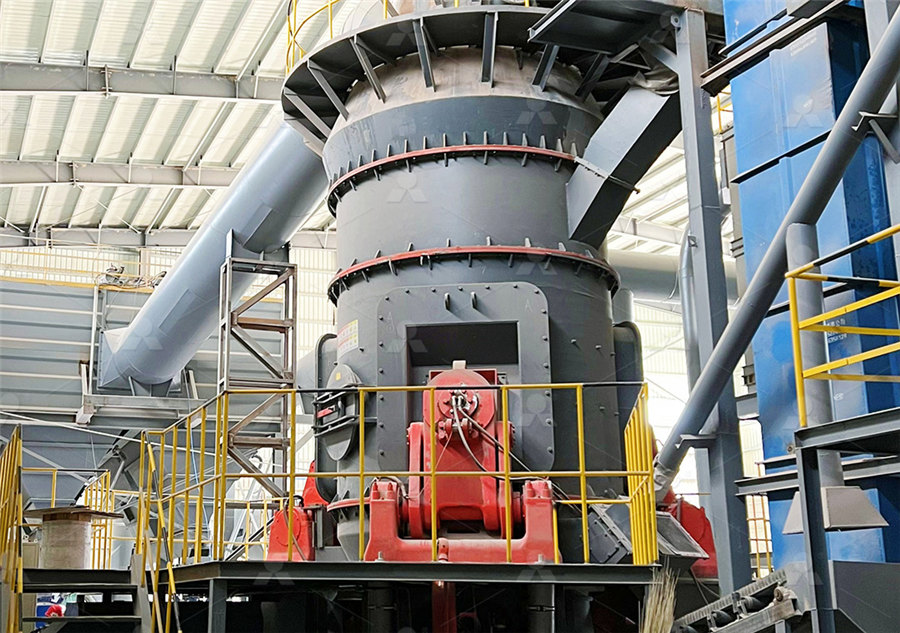
Refractories for Lime Calcination SpringerLink
2020年11月29日 532 Twin Shaft Kiln These are also called Parallel Flow Regenerative (PFR) kiln because the burden and the hot combustion gas flow in the same direction In this process, the peak temperature of calcinations remains low enough not to allow the CaO crystallites to get fused, and the product obtained has high reactivity and suitable for certain applications like an 2021年3月9日 In this study the process flow diagram for the cement production was simulated using Aspen HYSYS 88 software to achieve high energy optimization and optimum cement flow rate by varying the flow rate of calcium oxide and silica in the clinker feed Central composite Design (CCD) of Response Surface Methodology was used to design the ten experiments for Simulation and Optimization of an Integrated Process Flow Sheet Flow in these kilns is cocurrent Major advantages include high temperature, long residence time, and flexibility to process gas, liquid, solid, or A simple heat and mass balance for the kiln section of a limemaking process is shown in Figure 105 Figure 105 Lime kiln heat and material balance Comp = composition; Sen Heat Lime Kiln an overview ScienceDirect TopicsLime Kiln Process Fuel Flow Lime Mud Feed TT AT PT FT DT TT TT FT Hot End Cold End ID Fan Main Drive Mud Filter Lime Product Figure 2 – Sketch of a typical lime kiln unit (simplified)An Integrated Approach to Model Predictive Control of an
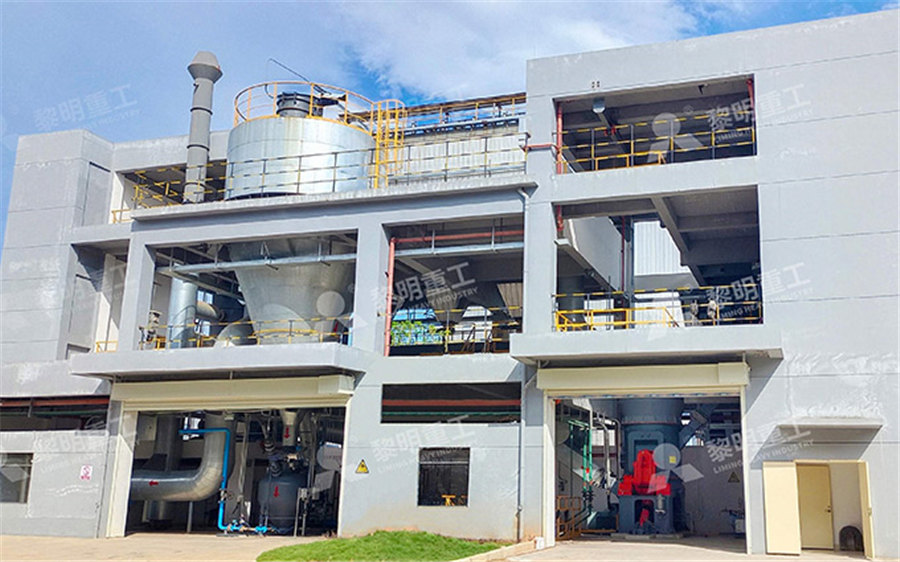
quick lime manufacturing process flow chart Mining Quarry
2013年3月25日 Quick Lime ProductionQuick Lime Production Manufacturers flow chart of dry cement process; russian gold mining resources in malaysia; Email:[ protected] hydrated lime manufacturing process,hydrated lime grinding (lime mud) from the causticizing reaction is washed, and sent to a lime kiln where it is heated to a high temperature to regenerate CaO for reuse Recovery of Heat from Combustion of Organics The organic compounds in black liquor serve as a fuel for the production of steam which is used to generate electricityThe Kraft Recovery Process TAPPI2019年4月23日 Lime kiln process The Architecture of Intelligent Lime Kiln process is shown in Figure 6 It consists of three intelligent controllers (IC) namely IC1, IC2 and IC3 The primary aim of the controller is to produce a lime product of the best quality as soon as the operator changes any of the input parametersDesign of Neural Network Based Expert System for Automated Lime Kiln Burning: In this operation, the slurry is directly fed into a long inclined steel cylinder called a Rotary kilnIn this kiln there are 3 different zones shown in fig below Cement Manufacturing Process Flow Chart (i) Drying Zones: In the wet process, the drying zone is comparatively larger than the dry process It is because the raw material in slurry form is directly fed into the kiln Manufacturing of Cement By Dry and Wet Process Expert Civil