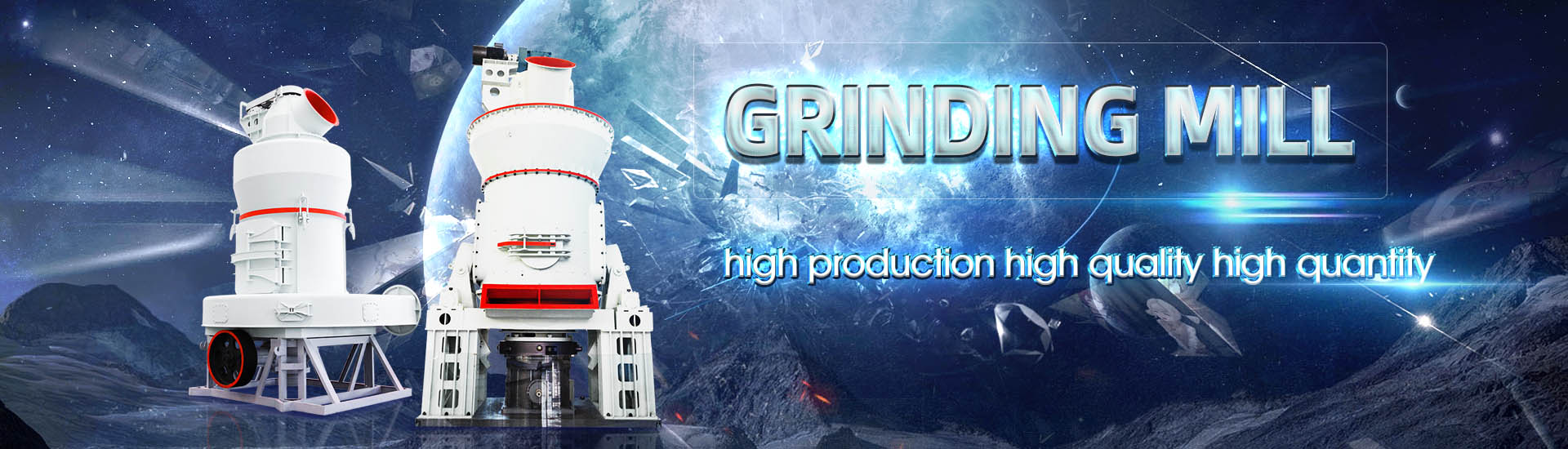
Quick lime coal pulverizer system
.jpg)
Quicklime preparation Gebr Pfeiffer
Quicklime reacts with water, generating a great amount of heat We distinguish softburnt lime, mediumburnt lime, and hardburnt lime In the construction industry, quicklime is added to mortar It can also be used as a drying or Today's coalfired utility boiler operation needs pulverizer designs to supply pulverized coal with required throughput and coal fineness, and also perform with lower specific power Coal Pulverizer Design Upgrades to Meet the Demands of Low The ATRITA pulverizer is a highspeed, compactly designed machine which reduces raw coal to pulverized coal by the combination of crushing, impact and attrition The AT RITA has A Comparison of Three Types of Coal Pulverizers Babcock PowerAs specialists in the design, manufacture, and commissioning of pulverizing systems for fine and semifine grinding, Bradley Pulverizer has equipment Materials Industries Bradley Pulverizer Company
.jpg)
Reliable Coal Pulverizers and Mills » Babcock Wilcox
From our original E/EL ballandrace type pulverizers for lower capacity applications, to the latest BW Roll Wheel™ pulverizer capable of grinding up to 230,000 pounds of coal per hour (104,300 kg/hr), we set the standard for high A verticaltype pulverizer bites into coal between a rotating table and roller to pulverize the coal through the action of crushing and grinding Mitsubishi Power offers a varied lineup from small to high capacity through two types of Pulverizers Mitsubishi PowerPulverization of coal is currently the favored method of preparing coal for burning Mechanically pulverizing coal into a fine powder enables it to be burned like a gas, thus allowing more Coal Pulverizer – Power Plant Pall CorporationKey pulverizing elements are faced with wearresistant materials allowing coal fineness to be maintained over long periods of operation without the need for periodic adjustmentsRILEY POWER’S ATRITA COAL PULVERIZERS RELIABLE COST
.jpg)
Coal Pulverizer Manufacturer Pulverizing System
Williams Vertical Roller Mill Pulverizers are perfect for coal and pet coke applications requiring fine to ultrafine particle sizes for direct firing into boilers and kilns This type of coal pulverizer uses centrifugal force to grind solid fuels Particulate contamination in the lube system can result in rapid damage to critical components In order to protect the coal pulverizer lube system components, Pall recommends maintaining a fluid cleanliness level of ISO 16/13 or better This can be accomplished through the use of Ultipleat® SRT AS grade (ß12(c)≥ 1000) or finer filtersCoal PulverizerFigure I shows the application of a ball mill in a typical directfired coal system These systems can be design ed with or without crusher/ dryers depending on the coal characteristics of an ATRITA pulverizer system is shown in Figure 3 AT RITA pulverizers can be designed for either pressurized or nonpressurized (suction) operationA Comparison of Three Types of Coal Pulverizers Babcock Power• Size of pulverizer coal particles leaving the pulverizer (Fineness) • System resistance of each individual fuel conduit • Total airflow through the pulverizer which is controlled on a ratio of weight of air to fuel • Velocity of air/coal mixture passing through each burner line • Maintenance of critical components such as theOptimum Operation and Maintenance of EL Pulverizers
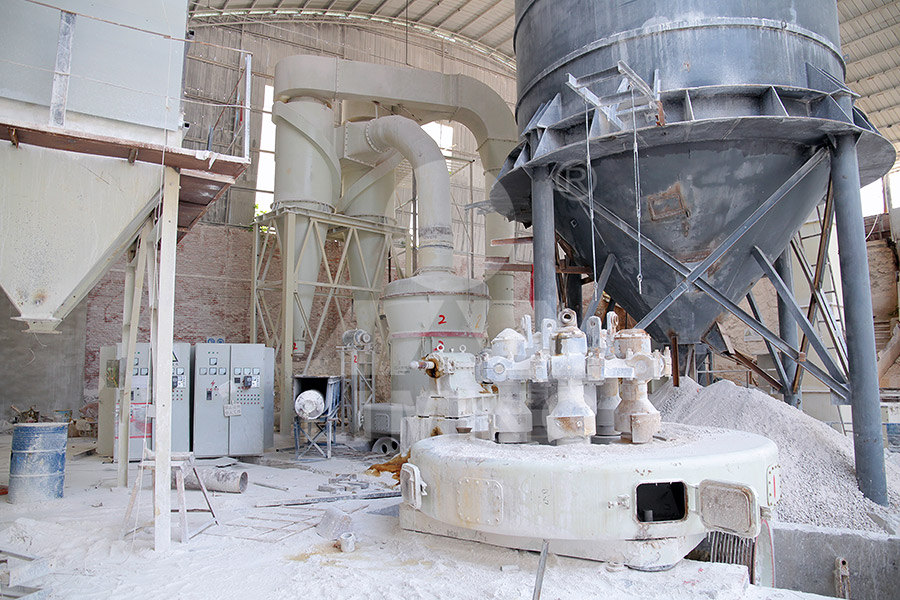
Coal Pulverizer Manufacturer Pulverizing System Williams
Design features of our coal pulverizer emphasize improved system reliability, constant product size control, and reduced energy requirements Vertical Roller Mill Coal Pulverizer Williams Vertical Roller Mill Pulverizers are perfect for coal and pet coke applications requiring fine to ultrafine particle sizes for direct firing into boilers and kilnsThe design “capacity” of the same pulverizer will grind 135,000 pounds per hour with fuel that is 55 HGI (Hardgrove Grindability Index) coal, ¾” raw coal top size, 7% moisture and produces pulverized coal that is 70% passing 200 mesh fineness (red line) This is pretty standardThe Storm Approach to Coal Pulverizer Optimizationthan normal, either when initating coal feed on mill startup, stopping coal feed on shutdown, or when equip ment problems cause inadvertent loss of feed Upon loss of feed to a pulverizer, the coal/ air mixture in the system becomes leaner and the coal dust will be ground to a more uniformly fine size and dried to a greater extentFire and Explosion Prevention in Coal Pulverizing SystemsParticulate contamination in the lube system can result in rapid damage to critical components In order to protect the coal pulverizer lube system components, Pall recommends maintaining a fluid cleanliness level of ISO 16/13 or better This can be accomplished through the use of Ultipleat® SRT AS grade (ß12(c)≥ 1000) or finer filtersCoal Pulverizer – Power Plant Pall Corporation
.jpg)
Vibration control of the coal pulverizer geared drive system using
2011年2月22日 Vibration control of the coal pulverizer geared drive system using linear actuators with the magnetorheological fluid February 2011 Conference: 9th Int Conf on Vibrations in Rotating Machines SIRM 2011 – 9th International Conference on Vibrations in Rotating Machines, Darmstadt, Germany, 21 – 23 February 2011 Vibration control of the coal pulverizer geared drive system using linear actuators with the magnetorheological fluid Tomasz Szolc 1, Łukasz Jankowski 2, Andrzej Pochanke 3, Maciej Michajłow 4 1,2,4 3 Institute of Fundamental Technological Vibration control of the coal pulverizer geared drive system • Size of pulverizer coal particles leaving the pulverizer (Fineness) • System resistance of each individual fuel conduit • Total airflow through the pulverizer that is controlled on a ratio of weight of air to fuel • Velocity of air/coal mixture passing through each burner line • Maintenance of critical components such asInnovative Combustion Technologies, IncPulverized Coal Pipe Testing and Balancing By Richard F (Dick) Storm, PE The first step in optimizing combustion system performance is balancing the air and fuel flowing through each of the plant's coal pipes—the pipes that convey the air/fuel mix from the pulverizers to the individual burners in the furnace wallPulverized Coal Pipe Testing and Balancing Storm Technologies,
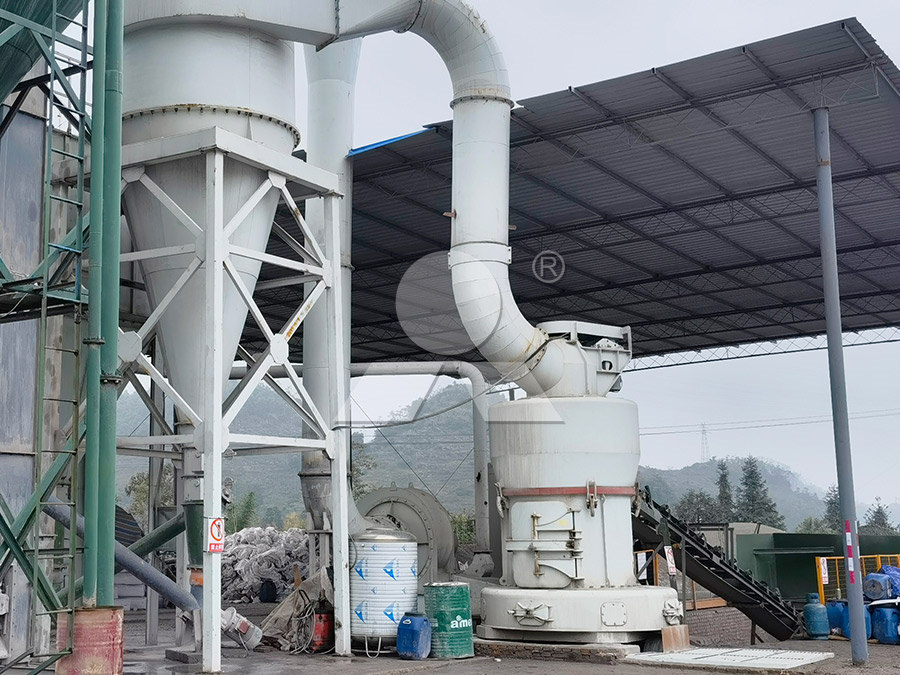
Fire Detection Methods for Coal Pulverizer Systems Babcock
coal pulverizer or mill systems The studies showed that there is an emergence of low rank, high reactive coals as a base fuel for power plants which is resulting in an increase in pulverizer system fires Also, the EPRI study concluded that reducing the frequency of fires would reduce the risk of coal dust explosions Unfor2023年5月8日 They function to supply coal fuel in the furnace; thus, they determine the quality of perfect combustion The PLTU Rembang has an installed capacity of two units of 315 MW in which each unit has one boiler with two coal pulverizer mills The coal pulverizer mills often experience disturbances that cause unit derating or trips during operationCoal pulverizer mill system modeling for failure simulationFirst, the pulverizer system is reviewed for its ability to grind the coal and deliver balanced fuel to each burner at suffi cient fi neness Investigated areas include: Coal analysis and its affect on mill performance Mill heat balance to determine required air/coal ratio and thermal head needed Coal pipe, burner and mill throat velocity15572 Riley POP Pulverizer Services Combustion Optimization ProgramCoal Pulverizer is a dynamic, visuallyengaging, online 3D animated course offered by Technical Training Professionals (TTP) Welcome to our website! Take a look Circulating Water System (Conventional Plant) View Course Power Generation Major Equipment 12 Coal Pulverizer Technical Training Professionals (TTP)
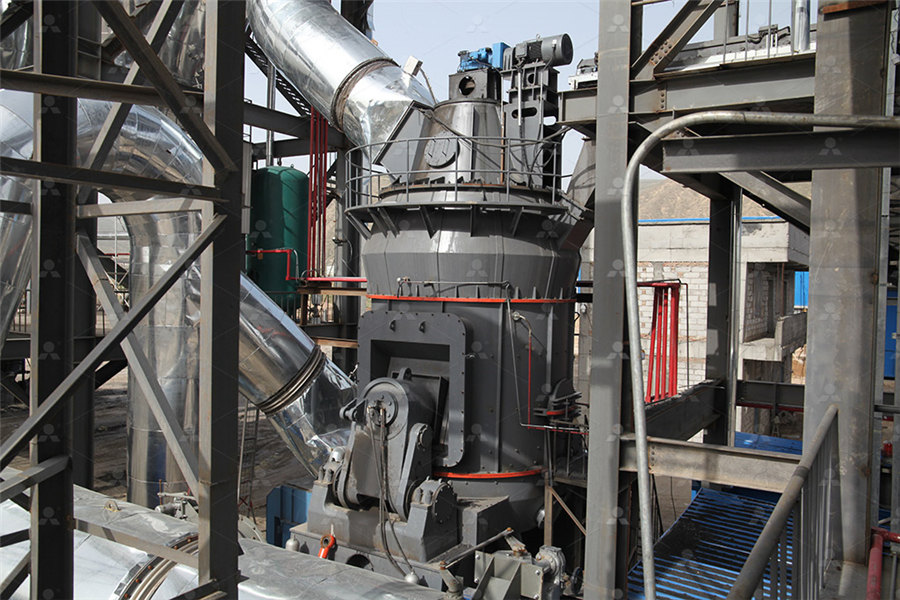
Experimental Results of Pulverized Coal System Fire and Explosion
In each test, a similar subbituminous coal mass was placed in a metal basket 10 inches in diameter by 3 inches deep, ignited, and allowed to come to full burn before being inserted in the simulated pulverizer Various types and amounts of extinguishing agents were applied to the fire through nozzles mounted at the top of the pulverizerTo efficiently combust coal, it needs to be pulverized into fine particles (100μm) before being placed in a boiler A pulverizer (coal pulverizer) is installed for this purpose, and pulverizes pieces of coal several centimeters in diameter down to fine particles The pulverizer includes pulverization, drying and classification functionsPulverizers Mitsubishi PowerThe coal blocks are crushed and ground into powder in this chamber While grinding the coal, the pulverized coal is taken out of the coal mill from the discharge device by a special induced draft fan The coarser coal granules will return to the grinding chamber through the return screw of the discharge device for regrindingHow To Maintain a Coal Pulverizer? (All You Need To Know)2020年1月1日 The coalpulverizer is an important unit, which preprocesses coalfuel fed to the boiler in coalbased thermal power plants It is extremely important to comprehend the operational behavior of (PDF) Modelling and multiloop selective control of industrial coal
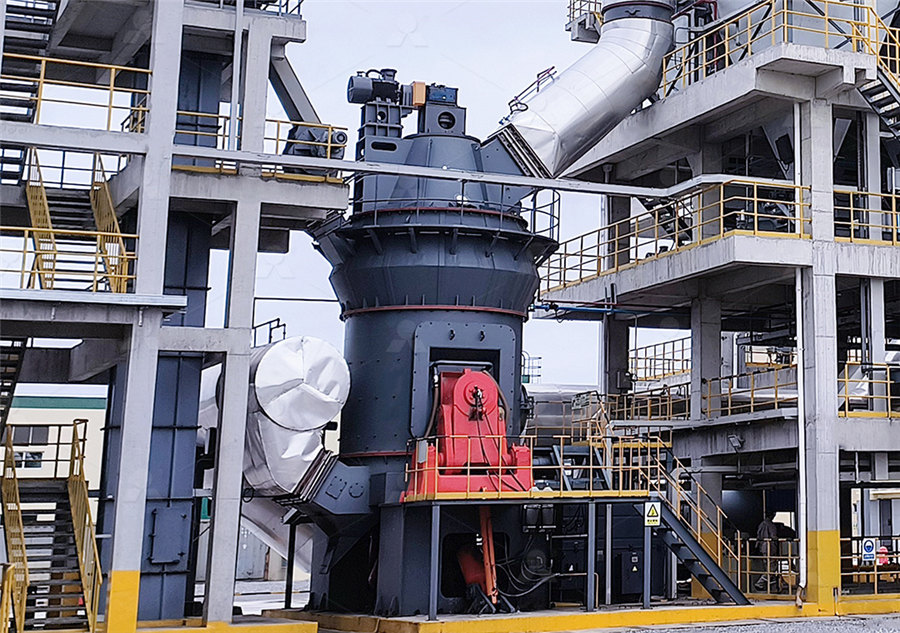
Coal Pulverizers an overview ScienceDirect Topics
In the same way with conventional coal firing boiler, raw coal fed from coal bunker is dried and grinded in the coal pulverizer However, in the case of IGCC, part of the flue gas from the GT is extracted from the HRSG as the drying gas at the pulverizer Pulverized and dried coal is fed to the gasifier by a pulverized coal feeding system1998年10月1日 A Dynamic Analysis System Based on Component Displacement can be Useful in Improving Pulverizer operation and reducing maintenance costs Such a system has been applied on coal pulverizers at a Dynamic Analysis Pinpoints Pulverizer ProblemsFuel preparation for a pc boiler occurs in a mill, where coal is typically reduced to 70% through a 200mesh (74μm) screen Figure 2 shows a particlesize distribution from a bowlmill grinder typically used in power plants A typical utility specification for particle size distribution of the coal is that 70% of the mass should pass through a 200mesh screen, which is equivalent to 70% Pulverized Coal Boiler an overview ScienceDirect Topicsin Coal Conveying Line: • Direct determining of relative flow rate value in coal conveying line • Gives relative values [mA] • Requires second level weighing system for turning relative values [mA] into absolute values [kg/s] • Quicker response Pulverized Coal Injection Paul Wurth
.jpg)
Extending Gear Life in a Coal Pulverizer Gearbox Power Engineering
2007年8月1日 Finally, personnel put the pulverizer gearbox into service along with the filtration system Following three hours of run time, the particle count was reduced to 21/19/11Coal Crusher Raw Coal Bunker To Boiler Furnace Raw Coal Feeder Exhauster Hot Air Motor Coal Pulverizer Figure 1: Simplified diagram detailing a directfired coal burning system 1 EPRI study on large coal fired utility boilers (greater than 600MW) using pulverizers with capacities greater than 50 tons per hour Combustion Engineering 783RP Bowl Improving Coal Pulverizer Performance and Reliability Pall • Coal characteristics profoundly influence risk – Lower rank coals are generally more easily ignited inside the coal mill – High volatile matter and highly reactive coals encourage preignition inside the mill – Higher moisture content requires temperature extremes inside the millMill Inerting and Pulverizer/Mill Explosion MitigationAmerican Pulverizer Company offers numerous solutions to handle lime material Lime can be efficiently processed using our hammermills, impactors, double and singleroll crushers, and our FCC Series Frozen Crackers Every American Pulverizer machine is designed for high production with minimal maintenanceLime Processing Equipment Shredders, Crushers, Impactors,
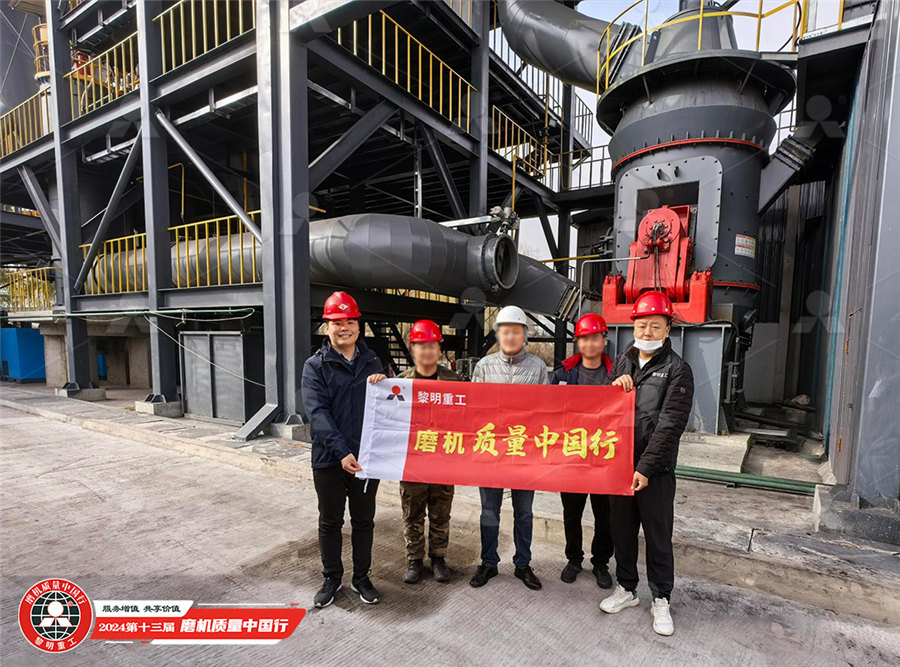
Pulverized Coal Production Line
Pulverized coal production line is widely used in power plants, steel works, industrial boilers, textiles, heating centers, steam power grading and conveying, the system is simple, the layout is compact, the floor space is about 50% of the ball mill system, and it can be arranged in the open air, so the investment cost can be greatly Babcock Power Inc company, has been developing improved coal pulverizer technology during the past several years to meet these challenging demands All three (3) types of coal pulverizer systems supplied by RPI originally designed for low, medium and highspeed pulverization have undergone design upgrades and improvementsThese machinesCOAL PULVERIZER DESIGN UPGRADES TO MEET THE DEMANDS The design “capacity” of the same pulverizer will grind 135,000 pounds per hour with fuel that is 55 HGI (Hardgrove Grindability Index) coal, ¾” raw coal top size, 7% moisture and produces pulverized coal that is 70% passing 200 mesh fineness (red line) This is pretty standardThe Storm Approach to Coal Pulverizer OptimizationFlow and temperature of primary air are automatically adjusted to match coal feed rate and coal moisture Potential for pulverizer fires significantly reduced Integral fan purges the pulverizer of coal dust after the coal feed is stopped As raw coal and primary air RILEY POWER’S ATRITA COAL PULVERIZERS RELIABLE COSTEFFECTIVE
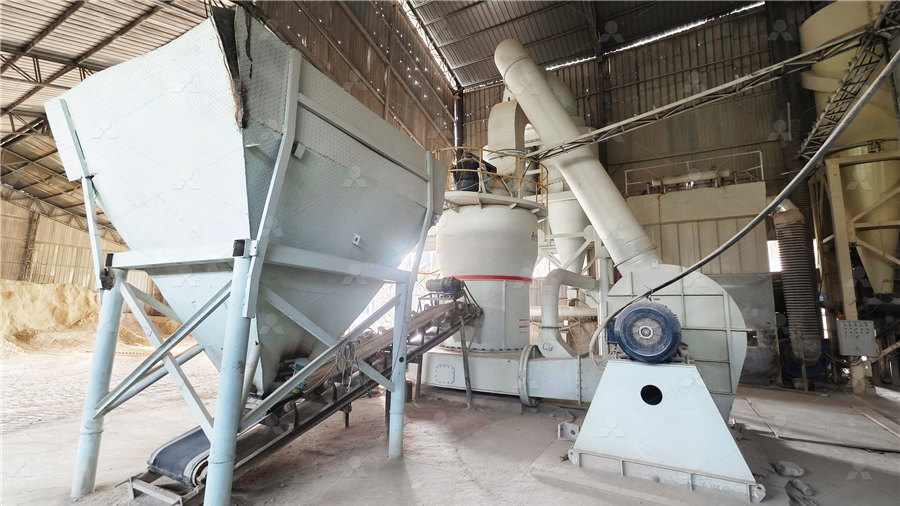
Performance optimisation of vertical spindle coal pulverisers
to evaluate the mill drying capacity constraint Coal analysis was done on hard grove grind ability, abrasive indices and calorific value of coal The effect of low calorific value coal was observed on mill’s response to match the boiler energy requirementsTable 1 details potential life extension of components as fluid cleanliness is improved A review of how ISO codes are determined as provided Step 3 – Install HyPro high efficiency glass media or desiccant breathers on all gearbox vent ports Any coal mill gearboxes have no breather protection which allows coal dust to enter the unit after the oil has begun being filteredUltraSupercritical Coal Fired Power Plant Coal Mill Pulverizer 2015年2月1日 The pulverizing system serves an important function in the safe and efficient operation of thermal power units The effect of coal moisture and pulverized coal moisture on the pulverizing system Modelling and control of pulverizing system considering coal moistureFuel quality is determined by the properties of the coal and by the design and operating specifications of the pulverising system The term `coal' covers a wide range of materials and coals of similar elementary analysis may have markedly different micro structures Studies of coal petrology, maceral Coal pulverisers performance and safety, IEACR/79 ICSC
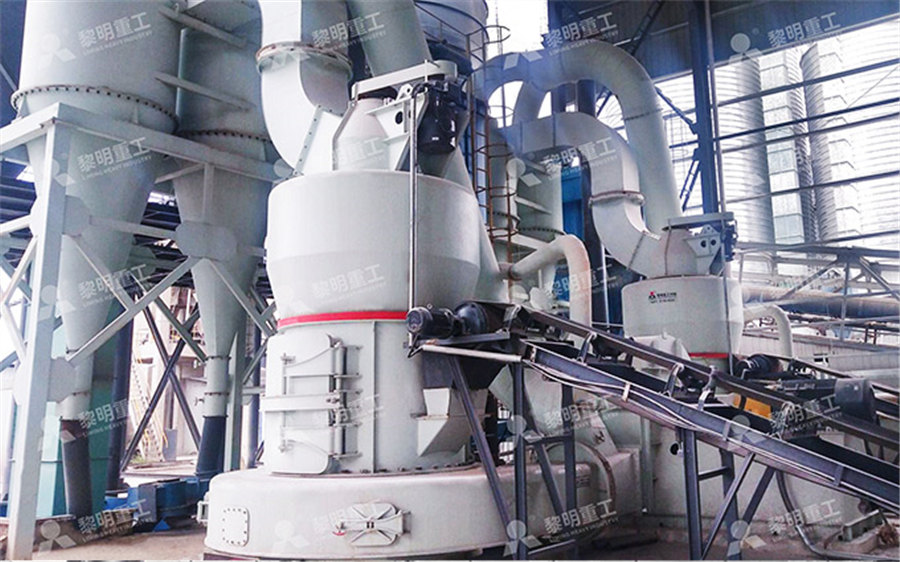
Pulverizers 101: Part I POWER Magazine
2011年8月1日 Now suppose this same pulverizer must grind sufficient coal flow to produce full load on the boiler with fuel that is 40 HGI, still 3/4inch maximum size with 7% moisture, but with an increased A pulverized coalfired boiler is an industrial or utility boiler that generates thermal energy by burning pulverized coal (also known as powdered coal or coal dust since it is as fine as face powder in cosmetic makeup) that is blown into the firebox The basic idea of a firing system using pulverised fuel is to use the whole volume of the furnace for the combustion of solid fuelsPulverized coalfired boiler Wikipedia%PDF16 %âãÏÓ 578 0 obj > endobj 601 0 obj >/Filter/FlateDecode/ID[3B1A95957EC903EF9975C4E56>]/Index[578 41]/Info 577 0 R/Length 103/Prev /Root 579 BW ROLL WHEEL PULVERIZERSQuicklime lumps are ground and classified in Pfeiffer MPS vertical roller mills The fineness of the white fine limes can be set within wide limits (006 to 01 mm) In downstream Pfeiffer lime hydrators, water is added to quicklime, thus transforming it into lime hydrateQuicklime preparation Gebr Pfeiffer