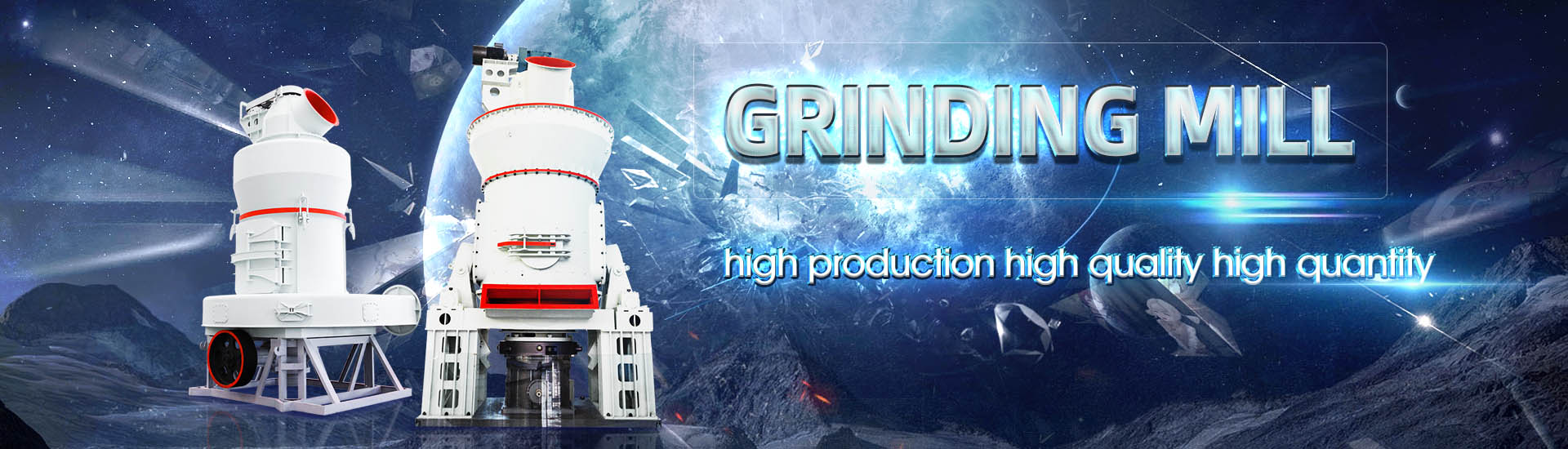
Which brand of cement grinding mill is good
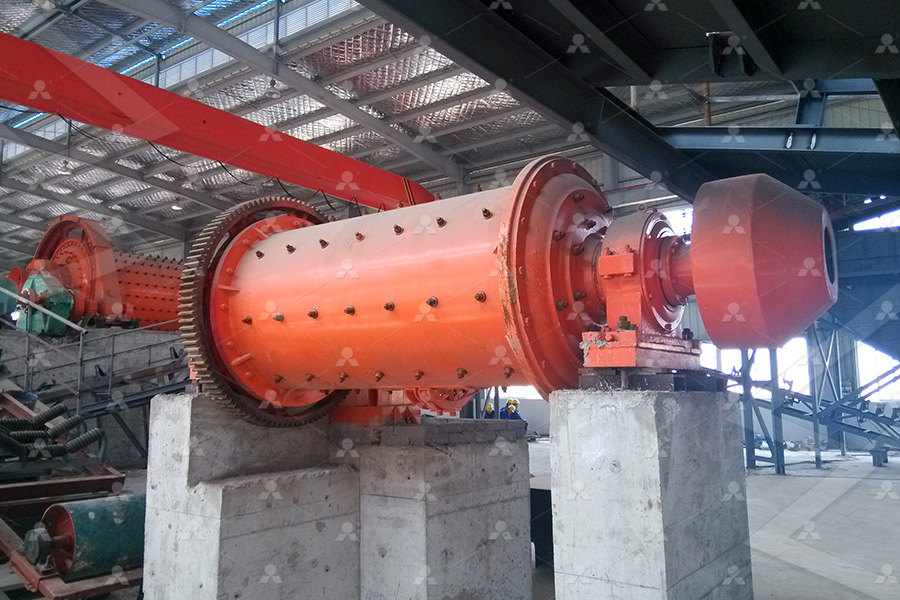
Vertical roller mill vs ball mill for cement grinding: Comparison the
In the cement industry, the choice between a vertical roller mill (VRM) and a ball mill for cement grinding is a crucial decision These two types of mills have unique advantages and disadvantages that can significantly impact the efficiency, energy consumption, and overall Grinding aids also serve to reduce coating problems in cement storage and enhances cement strengths GRINDING MILLS Mills will be selected according to type most suitable for Cement Grinding Cement Plant OptimizationBall mills are factory made and transported to the plant site of the buyer while VRM is built on the site of the cement plant This helps to reduce cost and complicated logistics issues The equipment cost is, however, higher for a Ball Mills Or Vertical Roller Mills: Which Is Better For Greener cement production with Fives' advanced grinding technology The FCB Horomill® is our groundbreaking innovation in sustainable grinding Its bedcompression grinding solution enables cement producers to vastly improve Fives Sustainable grinding with FCB Horomill®
.jpg)
Review on vertical roller mill in cement industry its performance
2021年1月1日 With the grinding capacity of a vertical roller mill and the ability to dry, grind and sort in a single unit, the vertical roller mill offers a definite advantage over the ball mill system Vertical cement mill is a large cement grinding equipment Tongli has successfully developed various models such as ZJTL vertical ultrafine powder roller mill in the field of cement and slag Vertical roller mill CEMENTL2021年8月13日 This article will outline the basic types of concrete grinders on the market and address the positive (and negative) aspects of the most common machines MOST COMMON TYPES OF MACHINES Single head machines Concrete Grinders Polishers What types are there?2022年2月18日 Depending on the specific customer needs, the cement grinding plant installation comprising a highpressure grinding roll polycom ® or a vertical roller mill quadropol ® in conjunction with a sepol ® separator technology World Cement Grinding Milling QA
.jpg)
CEMENT GRINDING SYSTEMS INFINITY FOR CEMENT EQUIPMENT
All grinding work is done in the tube mill and the setup is: Tube Mill with Pregrinding Unit Part of the grinding work is done in a pregrinding unit, which can be: Depending on the selected 2016年10月5日 In this chapter an introduction of widely applied energyefficient grinding technologies in cement grinding and description of the operating principles of the related equipments and comparisons over each other in EnergyEfficient Technologies in Cement Grinding2024年4月16日 We have mentioned a list of top cement brands that are renowned for their superior performance and commitment to building a stronger and more sustainable future for India Here is the list of the top 10 cement 10 Best Cement in India – Types of Cement Latest Grinding Mills: Ball Mill Rod Mill Design PartsCommon types of grinding mills include Ball Mills and Rod Mills This includes all rotating mills with heavy grinding media loads This article focuses on ball and rod mills excluding SAG and AG Grinding Mills 911Metallurgist
.jpg)
Cement Ball Mill Cost Effective Cement Grinding Mill from AGICO
The installation of liners Length Diameter Ratio The lengthdiameter ratio of the cement ball mill is relatively large For mills of opencircuit grinding system, the lengthdiameter ratio is usually between 35 and 6 to ensure that the product fineness is qualified through single grinding; For ball mills in closedcircuit grind system, in order to increase the material flow rate, the length while cement used was of normal fineness as found in market Then, fresh clinker having uniform chemical composition was collected from cement factory of same brand which was used in mix design Clinker was ground in laboratory in a ball mill along with 4% gypsum Six samples with fineness ranging from 1525 to 3741 cm2/g, each weighing 15 Kg, wereVariation in Fineness of Portland Cement and its Effects on Learning outcomes An emphasis on the understanding of the milling technology system: Gas flow, advantage and disadvantage in the Raw mill and Cement mill installations – Grindability concept and the effects of intergrinding materials of different grindability – Ball mill grinding equations and dimensioning – Describe working principles for a separator – Grinding aids and other tools CEMENT GRINDING COURSE The Cement InstituteFosrocCemaxBrochure Free download as PDF File (pdf), Text File (txt) or read online for free Fosroc produces grinding aids and performance enhancers under the Cemax brand to improve cement production efficiency and cement quality Cemax products work to reduce agglomeration during cement grinding, increase mill output, and improve cement flowability and strengthFosroc Grinding Aids Performance Enhancers: CEMAX Technology
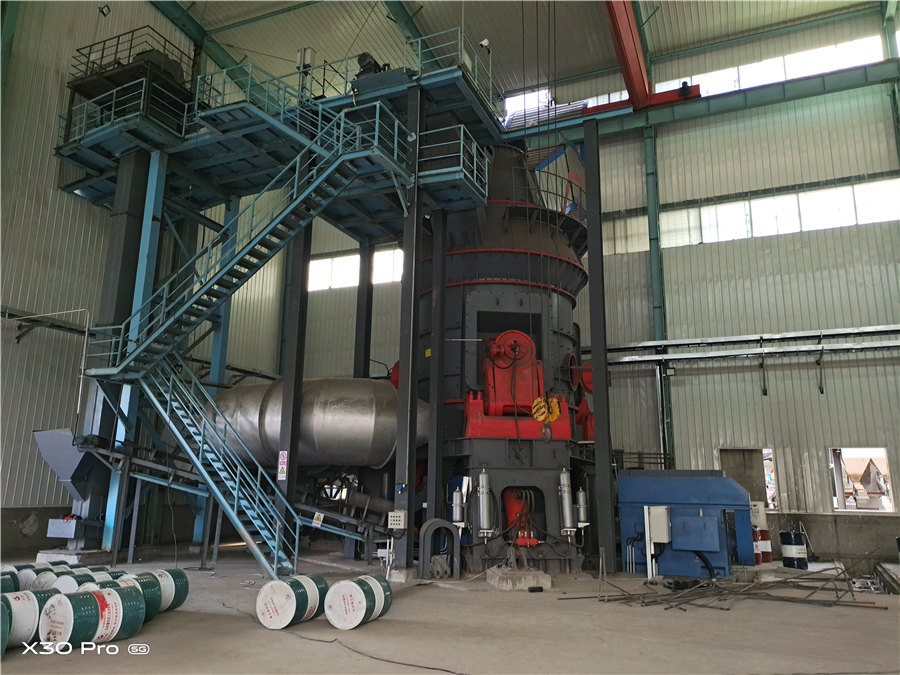
CEMENT GRINDING SYSTEMS INFINITY FOR CEMENT EQUIPMENT
The final manufacturing stage at a cement plant is the grinding of cement clinker from the kiln, mixed with 45% gypsum and possible additives, into the final product, cement In a modern cement plant the total consumption of electrical energy is about 100 kWh/t The cement grinding process accounts for approx 40% if this energy consumption2023年10月19日 Ball Mill: In some cement plants, a ball mill is used to grind clinker into a fine powder It relies on the use of steel balls to crush and grind the clinker Ball mills are often used for grinding cement clinker into a fine powder before it is Clinker Grinding Techniques in Cement Manufacturing JM The choice between a vertical roller mill and a ball mill for cement grinding ultimately depends on the specific needs and constraints of the cement plant VRMs offer significant energy savings, finer product control, and reduced maintenance costs, making them an attractive option for modern cement plants focused on efficiency and sustainabilityVertical roller mill vs ball mill for cement grinding: Comparison Keywords: Vertical roller mill, cement grinding, performance evaluation calculated data set are good in agreement This situation corresponds to an accurate sampling FIGURE 10Performance Evaluation of Vertical Roller Mill in Cement Grinding
.jpg)
Improvements in New Existing Cement Grinding
o Finished grinding may consume 25 – 50 kWh/t cement, depending on the feed material grindability, additives used, plant design especially the required cement fineness Cement grinding is the single biggest consumer of electricity Guangdong Cement Project Luofu mountain cement group of guangdong 12 million ton output cement grinding station, Equipment List the HFCG180160 rolling machine (output 930 ~ 1 050 t/h, main motor power of 600 kW * 2) 1 + Cement plant projects of pregrinding equipment Comparison of cement grinding systems for ordinary portland cement at 3500 Blaine, 4% limestone Ball mill Combi grinding system Finish grinding Ball mill with cage rotor separator Roller press in semifinish mode and ball mill VRM Roller press Specel Energy consumption mill motors kWh/t 30 25 17 17 % at mill motor (ball mill 100%) % 100 83 57 57Thomas Holzinger, Holzinger Consulting, grinding system 2018年12月1日 This may offer another possibility to choose MgSO 4 ⋅7H 2 O as the retarder of Portland cement clinker in place of gypsum MgSO 4 ⋅7H 2 O is soluble to form sulfate solution directly used to Effects of grinding aids on model parameters of a cement ball mill
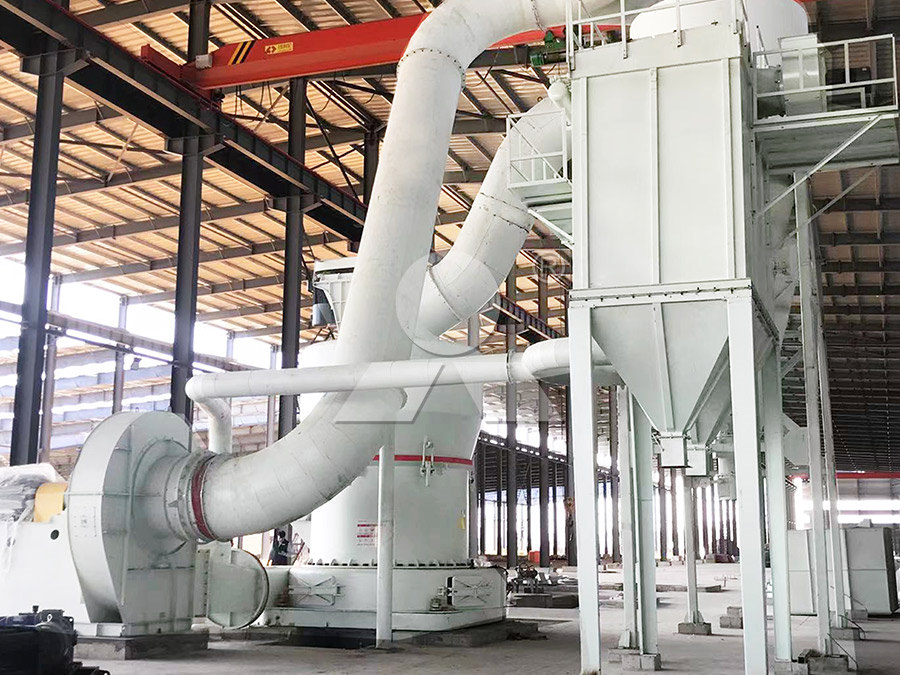
The Effect on the Performance of Cement Grinding Aid Components
Keywords: Cement grinding aid, Fineness, Compressive strength, Size distribution Abstract In this paper, By choosing four kinds of grinding aids better onecomponent, The grinding aid of cement grinding aids is determined by orthogonal optimization By adding different inorganic reinforcing components, Developed a cement grinding2019年1月3日 Clinker grinding technology is the most energyintensive process in cement manufacturing Traditionally, it was treated as "low on technology" and "high on energy" as grinding circuits use more than 60 per cent of total energy consumed and account for most of the manufacturing cost Since the increasing energy cost started burning the benefits significantly, Clinker grinding technology in cement manufacturingThe grinding systems consisting of roller press and ball mill include a pregrinding system, combined grinding system, semifinishing grinding system, and finish grinding system Pregrinding system: after the material is pulverized by the roller press, all or part of it with a good extrusion effect will enter the subsequent ball mill for further grindingCement Roller Press Roller Press In Cement Plant Roller Press 2009年5月1日 When grinding the clinker powder in the ball mill, the cement grinding efficiency decreases due to cohesion between the particles, and it also negatively affects the strength of the cement [1] [2 Characterization of Various Cement Grinding Aids and their
.jpg)
Cement Grinding 911Metallurgist
2016年10月23日 Exact proportioning is dependent upon their chemical properties before and after calcining to cement clinker For good kiln practice the grind required is 8892% – 200 mesh for standard cement, 99%200 mesh for high early Uniform kiln feed size helps reduce tendency to form kiln rings WET VS DRY Grinding of Cement Wet grinding is generally 2023年8月23日 A cement mill is a fundamental component of the cement manufacturing process, playing a vital role in breaking down and grinding cement clinker into fine powder This finely ground powder, when mixed with other What Are the Parts of a Cement Mills? Cement Ball would be a length of 135 m and a diameter of 25 m, with a speed of approximately 20 revolutions per minute Such a mill would normally have a load of approximately 90 tons of grinding media, graduated from 90 mm to 60 mm An Introduction to Clinker Grinding and Cement StorageThe first modern Loesche Mill for cement and slag grinding, a mill with the designation LM 462+2, was sold to Taiwan’s Lucky Cement Corp in 1993 and commissioned in 1994, forCEMENTS GROUND IN THE VERTICAL ROLLER MILL FULFIL THE
.jpg)
Top 9+ Best Cement Brands to Use for Home Construction 2024
2024年9月24日 Shree Cement is another best cement for construction in 2024 This cement company currently has about ten cement plants in the Eastern and northern parts of India Shree Cement currently provides more than 379 million tons of cement annually, which is quite enough to explain its reliabilityOpen and closed circuit dry grinding of cement mill rejects in a pilot scale vertical stirred mill CC Pilevneli*, S Kızgut, I˙ Torog˘lu, D C uhadarog˘lu, E Yig˘itOpen and closed circuit dry grinding of cement mill rejects in a 2018年7月1日 Among the industries, the nonmetallic industry was reported as the third largest energy user and accounted for about 12% of the global energy use [1]Within this portion, cement industry had the majority of the utilization with 85–12% [1], [2]US Energy Information Administration (EIA) [7] named cement industry as the most energy intensive among the Energy and cement quality optimization of a cement grinding circuit2018年11月11日 Fig 1 Illustration of the cement mill Z1 in kufa cement plant 22 The principle of grinding process The idea of grinding clinker and turning it into cement with a certain specific surface is basedIMPROVING PRODUCTIVITY BASED ON THE MOVEMENT OF
.jpg)
Modeling and Control of Cement Grinding Processes
2003年10月1日 Several intelligent controllers designed based on fuzzy logic [13][14][15][16] for the cement ball mill grinding process were able to track the setpoint and reject the disturbance better than the Cement Grinding Optimization Free download as Word Doc (doc / docx), PDF File (pdf), Text File (txt) or read online for free 1 The document discusses optimizing cement grinding circuits It presents tools like the Bond method and population balance models that can be used to analyze and optimize cement grinding 2 It provides details on the typical cement production process Cement Grinding Optimization PDF Mill (Grinding) CementClinker is extracted from our clinker tank and transported to the cement mill hopper by belt conveyors A measured quantity of clinker and gypsum is fed into our closedcircuit ball mill which incorporates with a highefficiency separator OPC is produced by the intergrinding and blending of 95% clinker with 5% gypsum to a fineness of 280 m 2 /kgCement Grinding Cement manufacturing process Priya Cement2024年2月12日 It is not as powerful as other brands at only 10 amps It is designed for grinding concrete but can be used for smoothing pavement and cleaning concrete surfaces The ball bearings are doublesealed to prevent 8 Best Concrete Grinders of 2024 – Top Picks Reviews
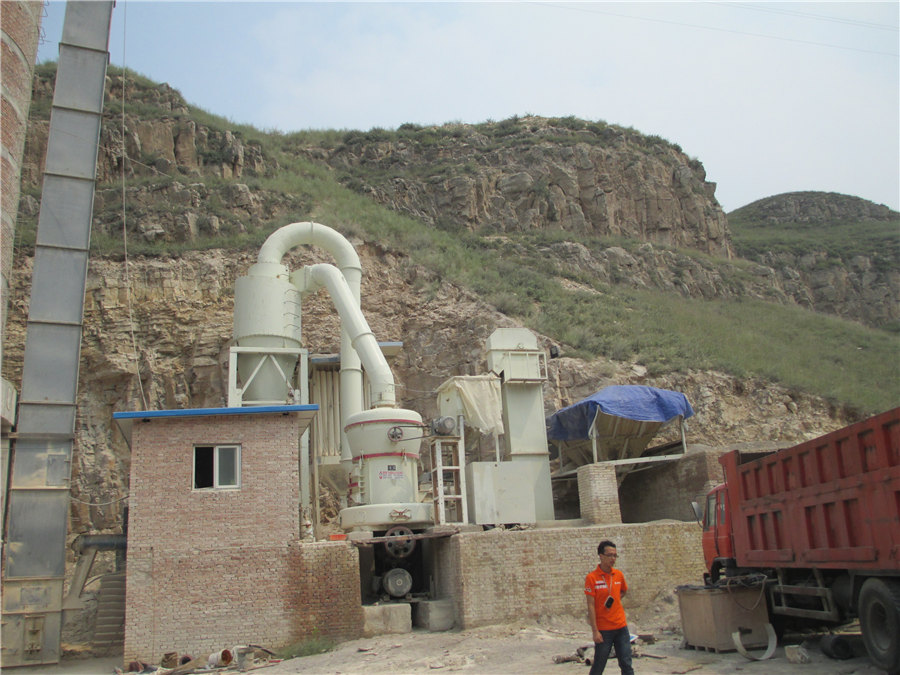
Cement grinding a comparison between vertical roller mill and ball mill
this mill all over the worldFor the cement industry the ball mill was really an epochmaking breakthrough as for almost 80 years it was the predominant mill for grinding raw materials and coal, and still today it is the mill most used for cement grinding Over the last three decades the vertical roller mill hasCement Grinding plant The cement grinding unit manufactured by our company combines drying, grinding, powder classification, dust collection and cement packing It can grind cement clinker and process cement mixtures such as Cement Grinding Plant Manufacturers NT EngitechAGICO VRM Grinding Roller After decades of continuous improvement and improvement, the vertical roller mill has been widely used in the field of cement raw meal, coal powder, and slag grinding The grinding roll is a key component in the vertical roller mill, and it is also the most worn in the daily operation of the millVertical Roller Mill Grinding Roller AGICO Cement Plantpower consumption [1, 34, 36] Optimization of cement grinding using standard bond grinding calculations based on population balance models is successfully applied [4, 38] Various grinding laws, energy relationships, control factors and controller design for cement grinding are discussed in [37] Figure1 Vertical roller mill for cement PROCESS CONTROL FOR CEMENT GRINDING IN VERTICAL ROLLER MILL
.jpg)
Ball Mill In Cement Plant Cement Ball Mill AGICO Cement
Compared with open circuit ball mill, the closedcircuit ball mill has high efficiency, high output, low cement temperature, and good comprehensive benefit It is the best choice for a cement plant Skip to materials mixed in a certain proportion will firstly enter the cement ball mill for grinding and then be sent to the powder Incorporated in 1892 as the first cement manufacturer in South Africa, we have extended our reach across subSaharan Africa over the years as a resilient organization adapting and responding to changes in various operating environments Cement capacity replacement value R36,0 billion at US$230 per annual tonsTop Cement Companies in South Africa2020年11月5日 As you all know, the process of a cement manufacturing plant can be divided into several steps, including crushing, raw milling, clinker calcining, cement milling (or cement grinding), packing and etc In the complete cement production line, the cement mill process plays a very important role The design of cement milling and cement mill process will produce a 3 Necessary Cement Milling Comparison Ball Mill, Vertical Roller MillFTM Cement mill is a kind of ball mill which is designed for the cement industryIt mainly used as the thirdstage grinding Environmental design, long service life of quickwear part;The cement grinding machine is equipped with dust removal system and brand cooperation CONTACT US 0086371; sales@sinofote; High Cement Mill FTM Mining Machine
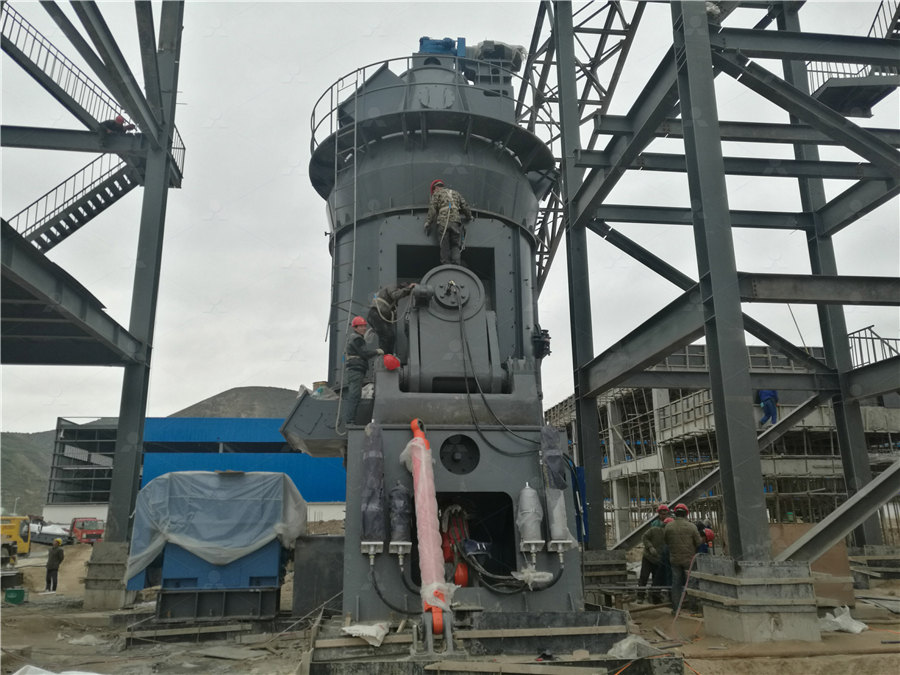
EnergyEfficient Technologies in Cement Grinding
2016年10月5日 In this chapter an introduction of widely applied energyefficient grinding technologies in cement grinding and description of the operating principles of the related equip‐ ments and comparisons over each other in terms of grinding efficiency, specific energy consumption, production capacity and cement quality are given A case study per‐ formed on a