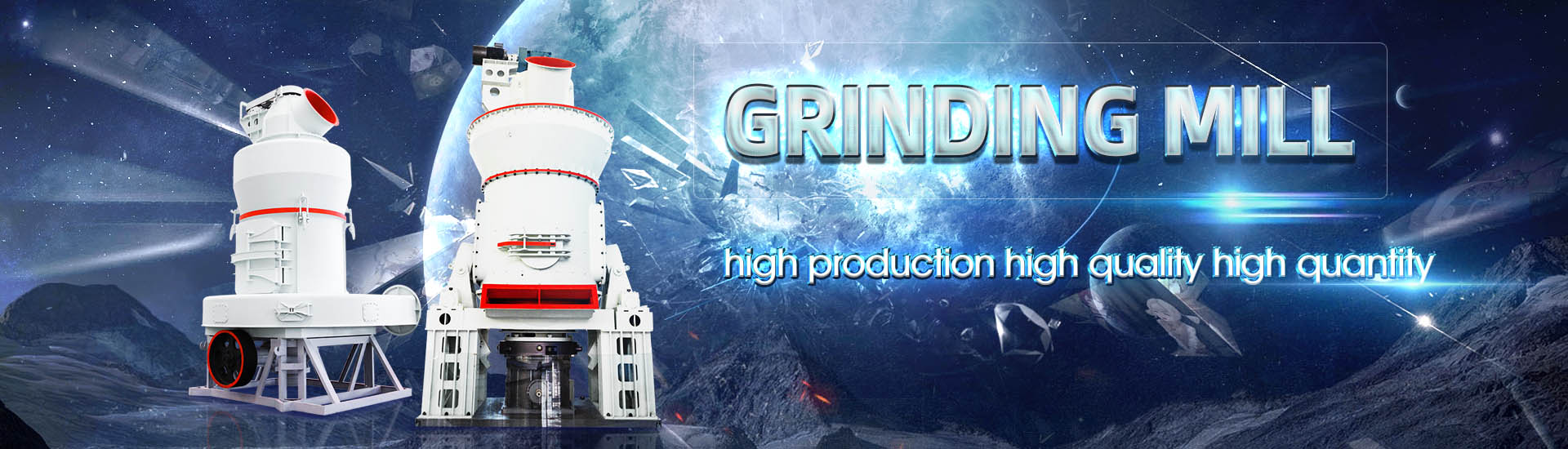
Comparable comprehensive power consumption of cement grinding
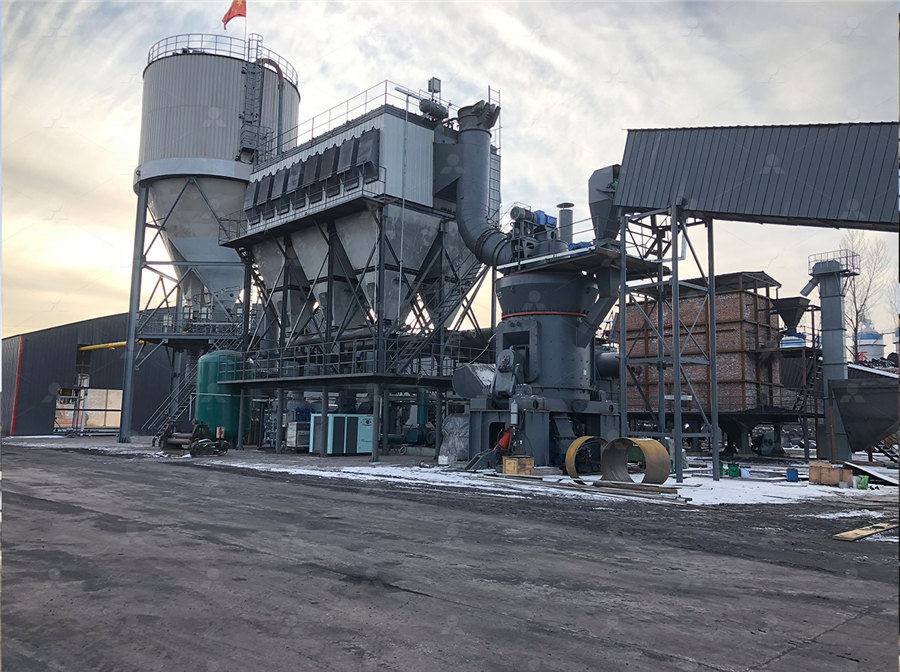
A critical review on energy use and savings in the cement industries
2011年5月1日 Fig 3 shows that grinding (finish and raw grinding) consumes major share (ie 60%) of total energy consumption in a cement manufacturing process This can be targeted to The grinding systems were compared in terms of specific energy consumption and mortar properties of the produced cements The specific energy consumption and the cement setting times increased in the order of combined (PDF) An industrial comparative study of cement Targeting the problems of multiple equivalent optimal solutions and easy to fall into local optimal solutions in Paretobased optimization algorithms, this paper proposes a new optimization DOUDCGAN: Optimization of cement grinding operational The annual energy consumption in 2050 according to the BAT scenario is about 380 PJ Comparing the frozen efficiency scenario and the BAT scenario, the annual saving potential Benchmarking Report for the Cement Sector UNIDO
.jpg)
EnergyEfficient Technologies in Cement Grinding
2016年10月5日 Typical specific energy consumption is 30 kWh/t in grinding of cement Barmactype crushers found application as a pregrinder in cement grinding circuits operating with ball mills to reduce the specific energy 2012年5月1日 The environmental impact of inorganic polymer mortars from nonferrous slag was assessed and compared to ordinary Portland cement (OPC) mortar based on a load An industrial comparative study of cement clinker grinding 2023年5月3日 In this paper, the specific energy consumption (SEC) and related emissions of a real scale cement factory currently running in Türkiye have been decreased by investigating A comprehensive investigation of a grinding unit to reduce energy 2016年10月5日 In this chapter an introduction of widely applied energyefficient grinding technologies in cement grinding and description of the operating principles of the related equip‐ ments and comparisons over each other in EnergyEfficient Technologies in Cement Grinding
.jpg)
Benchmarking of Energy Consumption and CO2 Emissions in
2024年2月2日 The benchmarking analysis quantified the plant’s energy intensity and CO 2 emissions per tonne of cement produced across key process stages including raw material 2016年10月5日 In this chapter an introduction of widely applied energyefficient grinding technologies in cement grinding and description of the operating principles of the related equip‐ ments and comparisons over each other in EnergyEfficient Technologies in Cement GrindingPower Consumption in Cement Manufacturing Plant: The cement industry, as a traditional high power consumption industry, power consumption in the cement grinding process takes a large ratio in the whole production, electric power Power Consumption of Cement Manufacturing Plant2024年2月2日 Key energy and emissions parameters, including thermal and electrical energy intensity, recovered energy and CO 2 intensity, are computed per tonne of cement produced along with capacity utilisation across major process stages including raw material grinding, clinkerisation, and cement grinding Comprehensive data sourced directly from the Benchmarking of Energy Consumption and CO2 Emissions in Cement
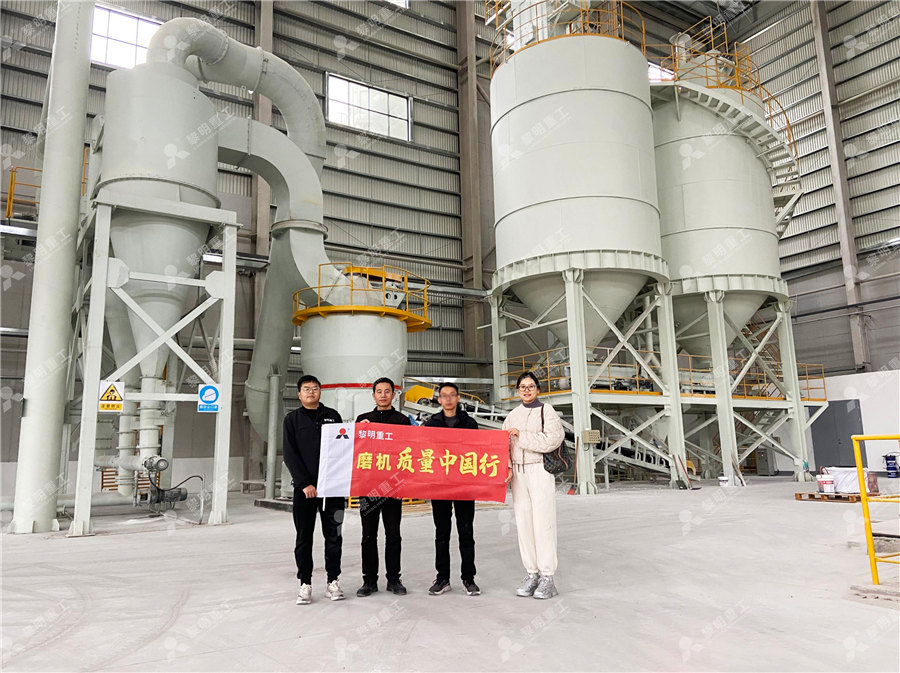
A comprehensive investigation of a grinding unit to reduce
2023年5月3日 A comprehensive investigation of a grinding unit to reduce energy consumption, environmental effects and costs of a cement factory, a case study in Türkiye May 2023 Energy Efficiency 16(5)2018年1月1日 In times of unstable market development due to the energy system transformation and legislative measures concerning the reduction of CO 2 emissions, the manufacturing industry is increasingly aware of the ecological and economical importance of the factor energy A considerable share of industrial energy and resource consumption can be attributed to Energy efficiency of stateoftheart grinding processes2017年1月17日 Excessive mill speeds caused more power consumption but resulted in reduced grinding rate Based on the simulation data, two scaleup models were proposed to predict power draw and grinding rateBreaking down energy consumption in industrial grinding mills2023年1月1日 In this study, the effects of four grinding aids with three different levels on the three important characteristics of the cement, namely the specific surface area, the compressive strength of the (PDF) EFFECTS OF VARIOUS GRINDING AIDS DOSAGE ON
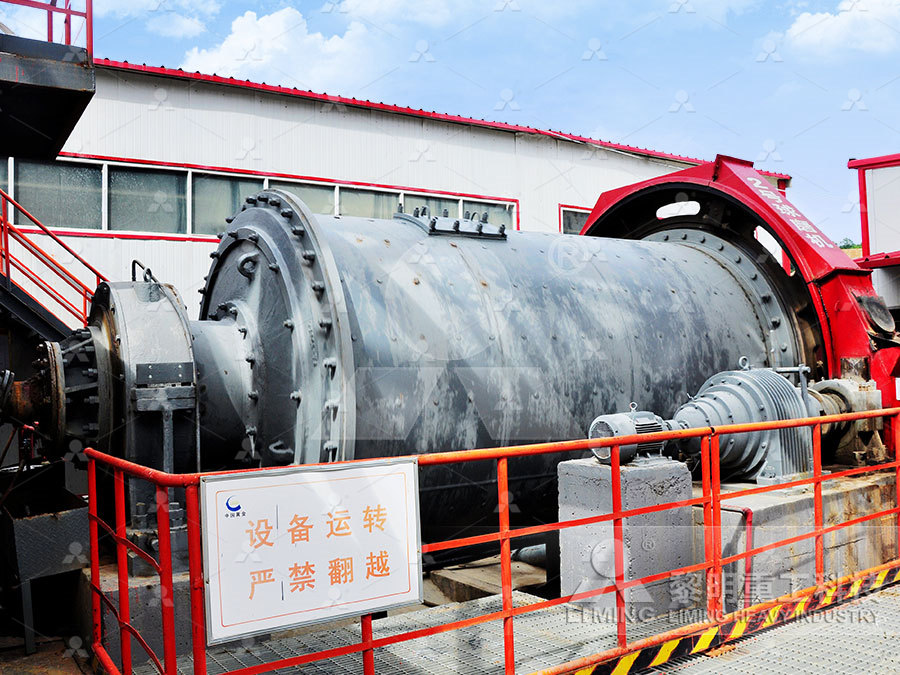
CEMENTS GROUND IN THE VERTICAL ROLLER MILL FULFIL THE
the specific power consumption of a ball mill is higher than that of a vertical roller mill (VRM) carrying out the same oper ations by a factor of between 15 and 2, depending on the2018年7月1日 Among the industries, the nonmetallic industry was reported as the third largest energy user and accounted for about 12% of the global energy use [1]Within this portion, cement industry had the majority of the utilization with 85–12% [1], [2]US Energy Information Administration (EIA) [7] named cement industry as the most energy intensive among the Energy and cement quality optimization of a cement grinding circuit2023年10月19日 Energy Efficiency: Energy consumption during clinker grinding can be significant Therefore, efficient grinding techniques and technologies are employed to minimize energy use and reduce production costs, contributing to the sustainability of the cement industry Types of Clinker Grinding Techniques used in cement manufacturing processClinker Grinding Techniques in Cement Manufacturing JM The final manufacturing stage at a cement plant is the grinding of cement clinker from the kiln, mixed with 45% gypsum and possible additives, into the final product, cement In a modern cement plant the total consumption of electrical energy is about 100 kWh/t The cement grinding process accounts for approx 40% if this energy consumptionCEMENT GRINDING SYSTEMS INFINITY FOR CEMENT EQUIPMENT
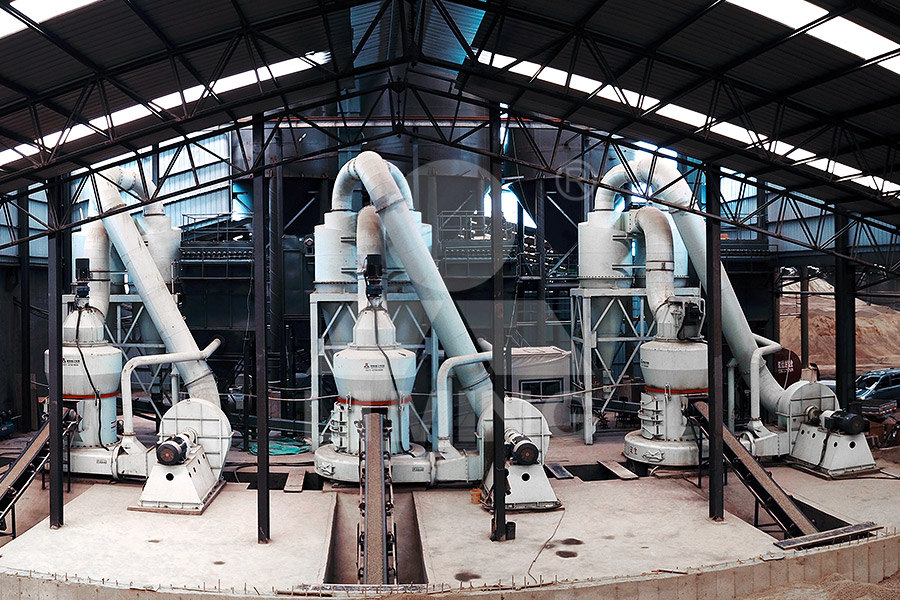
Optimization of Energy Consumption in ElectricPowered Modular Cement
use, reducing waste, and minimizing emissions, the cement industry can move towards a more sustainable future AI Algorithms in Energy Optimization Artificial Intelligence (AI) algorithms have rapidly become indispensable tools in industries seeking to enhance efficiency and reduce energy consumption The cement industry, with its2021年1月22日 In the whole process of cement production, the electricity consumption of a raw material mill accounts for about 24% of the total Based on the statistics of the electricity consumption of the raw A Survey and Analysis on Electricity Consumption of Raw Material 2008年10月22日 A comprehensive research project was undertaken to evaluate the effect of specific energy consumption (Ec) on variations of portland cement fineness measured by the Blaine test and sieve analysis Amine and glycolbased grinding aids (GA) were incorporated at various concentrations of 004, 006, and 008% of the cement weight At Ec values lower than Effect of specific energy consumption on fineness of portland cement 2010年1月1日 A comprehensive research project was undertaken to evaluate the effect of grinding aids (GAs) on the percentage of clinker decrease and reduction of energy needed during the grinding processUse of cement grinding aids to optimise clinker factor
.jpg)
An industrial comparative study of cement clinker grinding
2012年5月1日 This paper is concerned with a comparative analysis of modern cement grinding systems, namely, combined grinding (Comflex®), highpressure roll mill (HPRM) grinding, and horizontal roller mill 2015年8月1日 The results show that approximately 248t, 469t, and 341t of materials are required to produce a ton of the product in raw material preparation, clinker production, and cement grinding stages (PDF) Analysis of material flow and consumption in cement production cement industry reveals prospects to integrate vertical roller mills for cement grinding and use Organic Rankine Cycle (ORC) at the clinkerisation stage Adopting these techniques could reduce the electrical energy intensity of clinkerisation by 51% and cement grinding electrical intensity by 30%, surpassing benchmarks While limited toBenchmarking of Energy Consumption and CO2 Emissions in Cement 2023年11月6日 The influence of the GAs incorporation in cement grinding on properties such as workability and setting times of the placed concrete and/or mortar has been covered in this review(PDF) Review of the Effect of Grinding Aids and Admixtures on the
.jpg)
How to Save Power in Cement Grinding 911Metallurgist
2018年2月14日 For grinding Portland Cement, the power consumption accounts for some 35% of the total consumption of electrical energy for producing cement, counting right 911 Metallurgist is a trusted resource for practical insights, solutions, and support in mineral processing engineering, helping industry professionals succeed with proven expertise How to Save UPGRADATION OF EXISTING CEMENT GRINDING SYSTEMS WITH VRPM FOR CAPACITY ENHANCEMENT AND REDUCTION IN SPECIFIC POWER CONSUMPTION Ms Ankita Fulzele, Mr Yogesh Ghotekar, Mr R K Sharma AMCL Machinery Limited (AMCL) 1 Introduction: The Cement Industry is always looking forward to energy efficient solutions and are ready to upgradeUPGRADATION OF EXISTING CEMENT GRINDING SYSTEMS WITH 2023年3月27日 PDF Cement production is an industry that consumes a lot of electric energy During the period of power shortage in China, the government encouraged Find, read and cite all the research you (PDF) Power consumption characteristics of cement industry and After two hours of grinding, 27 % C02, and after 20 grinding hours 46% C02 was found, although initially no C02 was detectable This indicates a carbonatation of the lime Wear rates of grinding balls Wear rates of grinding balls for wet and Grinding ball data INFINITY FOR CEMENT
.jpg)
Effect of specific energy consumption on fineness of Portland cement
2009年10月1日 A comprehensive research project was undertaken to evaluate the effect of specific energy consumption (Ec) on variations of portland cement fineness measured by the Blaine test and sieve analysis2019年1月3日 Clinker grinding technology is the most energyintensive process in cement manufacturing Traditionally, it was treated as "low on technology" and "high on energy" as grinding circuits use more than 60 per cent of total energy consumed and account for most of the manufacturing cost Since the increasing energy cost started burning the benefits significantly, Clinker grinding technology in cement manufacturing2014年6月1日 Grinding aids are materials that are added to cement mixtures to improve the characteristics of the cement or increase the efficiency of the milling systems or both in the clinker grinding (finish Comprehensive understanding of grinding aids ResearchGateVertical roller mill vs ball mill for cement grinding: Comparison the advantages and disadvantages of these two types of mills TO Download this post and all the books and excel sheets and my personal notes and presentations I collected about cement industry in the last 30 years click the below paypal linkVertical roller mill vs ball mill for cement grinding: Comparison
.jpg)
Energy and exergy analyses for a cement ball mill of a new
2020年2月1日 They showed that the polymerbased grinding aid increases the specific surface, prevents agglomeration and ball coatings, and improves the roundness, fineness and fluidity of the ground cement2019年2月1日 Furthermore, in the cement manufacturing industry, power consumption is predicted by the multiple nonlinear regression algorithm [9] and empirical mode decomposition based hybrid ensemble model Empirical Mode Decomposition Based Hybrid Ensemble Model for In order to realise efficient comminution in limited size ranges with a minimum number of mills, ECRA has developed the concept of “multistage grinding” of cement 2 Multistage grinding: An approach for future comminution 21 The general idea of multistage grinding Separate grinding systems for raw meal and cement are state of the artStudy on the production of cements using a multistage grinding 2016年4月25日 In cement industry about 110 kWh of electrical energy is consumed to produce one ton of cement and about 26% of the total electrical power is used during farine productionDetermination of correlation between specific
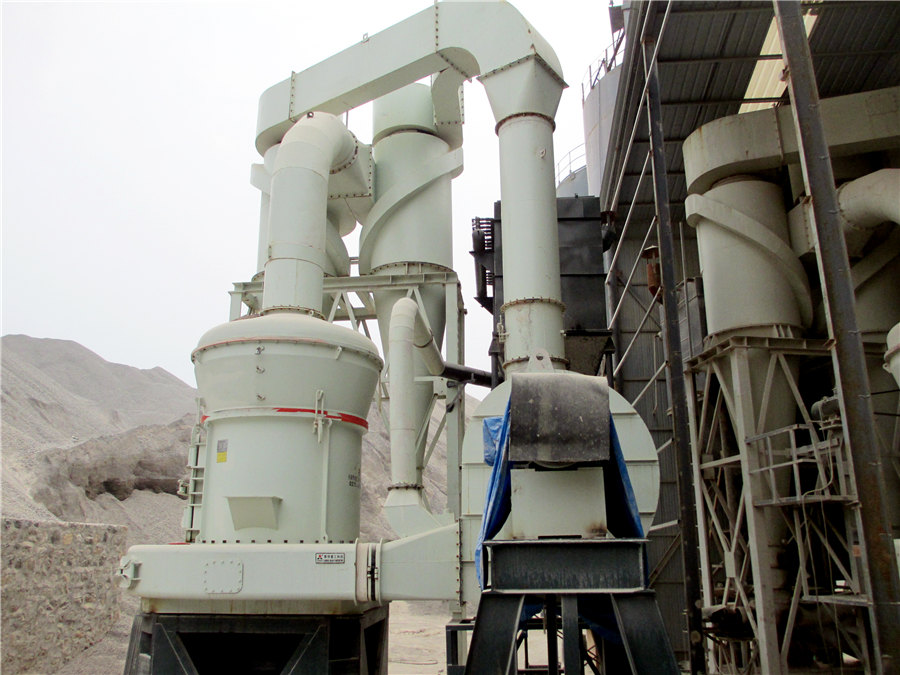
CONVENTIONAL CLINKER GRINDING A NEW APPROACH TO
This power corresponds to: 211 billion tonnes cement x 110 kWh/tonne cement = 2321x10 9 kWh = 0835 x10 9 GJ and it is produced from fossil fuels with thermalProviding a comprehensive guide to the entire cement production process from raw material consumption – 3 Cement mill specific power consumption – 4 Other systems – 5 Debottlenecking Cement milling Finish milling is the grinding together of The Cement Plant Operations Handbook International Cement 2024年8月30日 Different grinding equipment and durations for the same grinding method can result in variations in particle size, water demand, and activity after grinding [26], [27] Therefore, to mitigate the adverse effects of single grinding methods on particles, this study will primarily focus on evaluating the impacts of different grinding methods on both CFBCS particles and the Modification of cementbased circulating fluidized bed Journal of Materials Research and Technology, 2020 Grinding aids (GAs) have been an important advent in the comminution circuits Over the last few decades, in order to address the high energy consumption and scarcity of potable water for mineral processing, chemical additives have become a promising alternativeEffect of specific energy consumption on fineness of portland cement
.jpg)
Effect of grinding aids in the cement industry, Part 2 ResearchGate
2001年1月1日 ASTM C465 Standard Specification for GAs related such changes to cement flowability and mill retention time (MRT) during grinding [17] The MRT can be defined as the average time necessary for the Power saving: comprehensive power consumption of 25kwh/t, more than 30% than the traditional ball grinding system power saving; The system runs stably, with the operation rate as high as 9397%; Process is simple, covers an area of small, the number of mechanical and electrical equipment is small, easy to operate and maintain;Cement Grinding Station Solution Ball Mill and Vertical MillEverything you need to know about clinker/cement Grinding if You read and understand this article , you will be ready to be a cement grinding area manager FEED AND FEED SYSTEM 45% of the total mill power consumption in the first compartment For raw mills it is most common to use a ball charge with the coarse grading Everything you need to know about clinker/cement Grinding2017年8月1日 Benchmarking energy utilization in cement manufacturing processes in Nigeria and estimation of savings opportunitiesBenchmarking energy utilization in cement manufacturing processes
36.jpg)
Effect of specific energy consumption on fineness of portland cement
Effect of specific energy consumption on fineness of portland cement incorporating amine or glycolbased grinding aids Joseph J Assaad Æ Salim E Asseily Æ Jacques Harb Received: 3 June 2008/Accepted: 15 October 2008/Published online: 22 October 2008 RILEM 2008 Abstract A comprehensive research project was