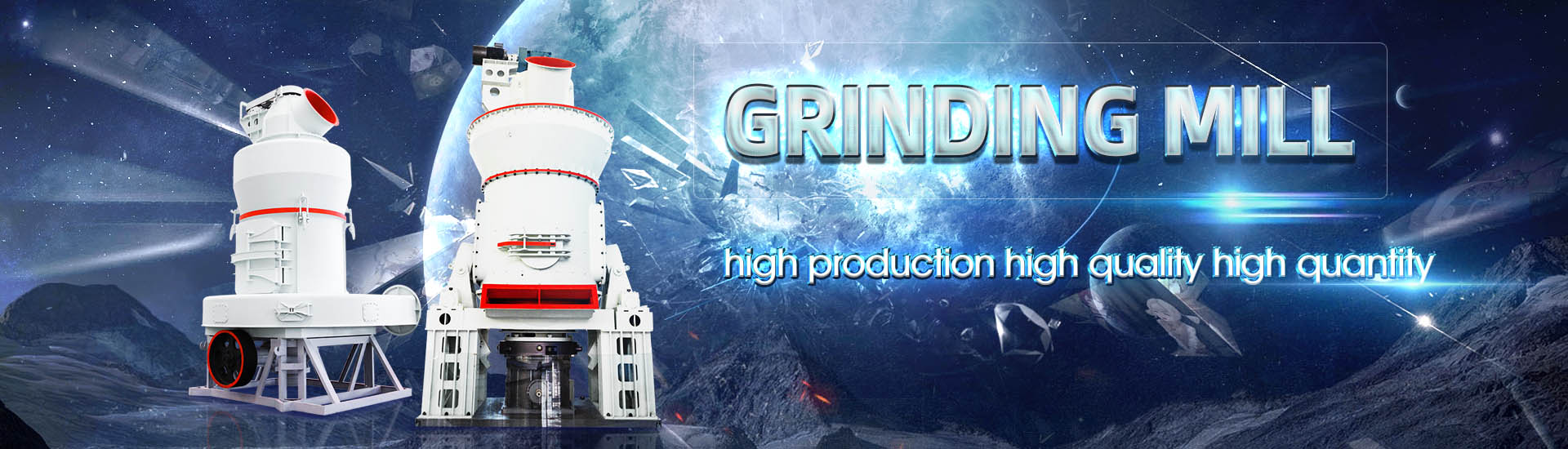
Pig iron unit consumption metallurgical coke iron oxide
.jpg)
Physical and chemical properties of metallurgical coke and its
2024年6月15日 High sulfur content can raise the sulfur level in pig iron, reducing its quality or increasing slag alkalinity, adversely affecting BF operation indices Elevated volatile content Increasing the amount of pigiron produced in blast furnaces led to the mining metallurgical sector increasing efforts to cover ore and coke needsFUEL AND ENERGY CONSUMPTION DECREASE IN ORDER TO In terms of obtaining the pig iron of iron ore and metallurgical coke, through traditional flow, there are high costs of the finished product (pigiron for steelmaking or iron foundry) due in particular FUEL AND ENERGY CONSUMPTION DECREASE IN ORDER TO Equation 44 CO2 emissions from iron and steel production (Tier 1)421 Equation 45 CO2 emissions from production of pig iron not processed into steel (Tier 1) 421CHAPTER 4 METAL INDUSTRY EMISSIONS IGES
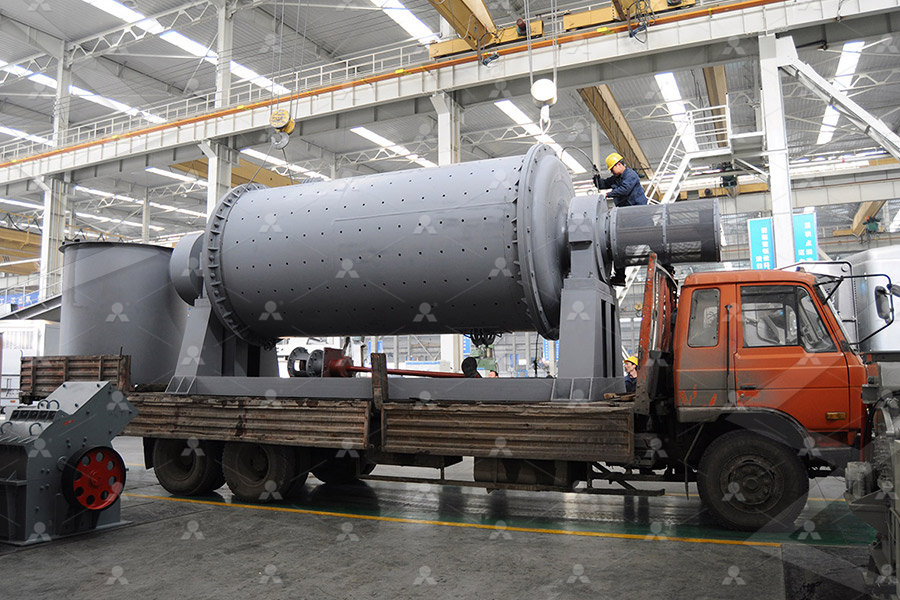
Using biomass for pig iron production: a technical, environmental
The plant considered produces pig iron from iron ores, mainly made of iron oxides, using a socalled “first fusion” route based on three main processes: the coking unit, the sintering unit and 2023年10月13日 Various approaches have been applied to produce pig iron from BR, for example, magnetic separation, pyrometallurgical recovery, and hydrometallurgical recovery Life cycle assessment of pig iron production from bauxite residue: pig iron production and reduced fuel consumption, mainly metallurgical coke The reactions between carbon and gas molecular (CO 2, H 2O) is key in coke gasification process22,23) Negatively Catalyzed Gasification Characteristics of Metallurgical 2013年3月6日 Large carbon dioxide (CO 2) emissions in iron and steel industry are caused by the use of nonrenewable and fossil fuel derived reducing agents Currently coal, metallurgical Production of pig iron by utilizing biomass as a reducing agent
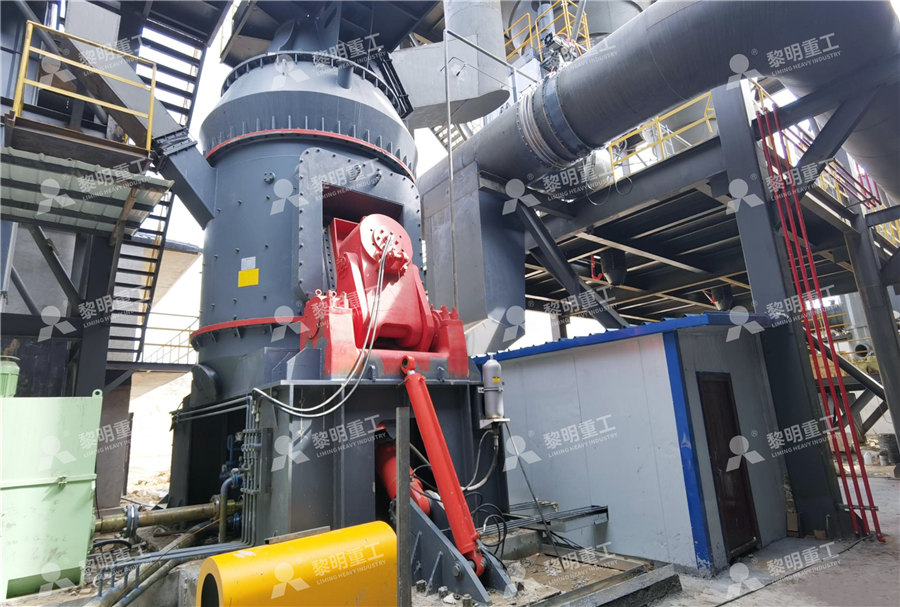
Preparation of Iron Oxide Feed Stock for Pig Iron/Sponge Iron
Direct Reduced Iron (DRI) or sponge iron industry is all set to take a firm root in India as one important solution to the problems of shortage of metallurgical coal and ferrous scrap and high 2017年3月20日 In his discussion of electricfurnace production of pig iron and pig steel before the Engineers’ Society of Western Pennsylvania, Dr J W Richards defines pig steel as “a metal with 22 per cent, or less of carbon, a Pig Iron Manufacturing Process 911Metallurgist2023年4月5日 Recent Trends in the Technologies of the Direct Reduction and Smelting Process of Iron Ore/Iron Oxide in the Extraction of Iron and Steelmaking April 2023 DOI: 105772/intechopen(PDF) Recent Trends in the Technologies of the Direct2020年3月3日 Additional coke is consumed for final reduction of iron oxide, and carbon dissolves in the hot metal, The coke consumed for a unit is termed as coke consumption rate or simply coke rate in kg per thm World’s pig iron production is shown in Table Blast Furnace Reactions SpringerLink
.jpg)
The Use of Foundry Pig Iron in Grey Iron Castings Metallics
metallics IIMA Fact Sheet #7 (2017) info@metallics The Use of Foundry Pig Iron in Grey Iron Castings • Pig iron is produced mainly by the smelting of iron ore in blast furnaces with coke or charcoal as reductant It is a high Fe, low residual metallic material and should not beMetallurgical Coke Metallurgical coke, also referred to as "met coke" or "blast furnace coke," is a vital carbonaceous material produced by heating bituminous coal without oxygen, a process known as carbonization or coking This method drives off volatile components, leaving a solid, porous mass consisting primarily of carbon Met coke plays a pivotal role inMetallurgical Coke Anupam FuelsCoke also serves as a structural material to support the deep bed of coke/iron oxide/limestone that makes Low Ash Metallurgical Coke is required for metallurgical and chemical industries and is (2580 mm) , we are producing the Nut Coke (1030/40 mm) size also which is being used in Captive consumption of Ferro Alloy unit of Jindal Jindal Coke LimitedTo reduce the amount of metallurgical coke to be burned to reach fusion of the impurities, metallurgists adjust the composition of the impurities by adding a fluxing agent to match the composition of the eutectic mix melting at 1260 °C The other eutectic, richer in silica, gives pig iron that contains too much silicaIron Oxide Pellet an overview ScienceDirect Topics
.jpg)
(PDF) Sustainable Iron Making Processes ResearchGate
2014年1月1日 Total CO 2 emission of US and from Iron and Steel Industry and metallurgical coke production in MMT (Million Metric Ton) (EPA, 2013; Worldsteel, 2012)Also amount of fixed carbon, volatile materials and ash in metallurgical coke were analyzed According to Xray diffraction results (XRD, P ANalytical PW3040/60), raw ore contains mainly quartz, magnetite, hematite and magnesium chromium oxide phases and slightly nickel iron oxide XRD pattern of the ore can be seen in figure 1FERRONICKEL PRODUCTION AND OPERATION2014年2月1日 Preparation of coke for blastfurnace smelting based on its fractional composition and the addition of nut coke to the furnace charge in amounts of up to 30 kg/ton pig iron at the EMZ and Donetskstal have reduced the combined consumption of skip coke and nut coke by 4–8 kg/ton pig iron and decreased the amount of coke lost in the form of screenings by 67–13 kg Effect of Introducing Different Sizes of Nut Coke Into the Ore 2011年11月1日 A comparative analysis is made of greenhousegas emissions by alternative cokeless metallurgical processes for making pig iron, metallized pellets, and parative ecological and greenhouse analysis of

(PDF) Recent Trends in the Technologies of the Direct
These reducing agents include metallurgical coke, noncoking coals, charcoal, agric wastes, biomass sawdust, reducer gases (H2, CO/CO2, CH4), etc 26 Iron ore reductionsmelting process using noncoking coals/charcoal as reductants 2023年4月5日 The blast furnace and direct reduction processes have been the major iron production routes for various iron ores (ie goethite, hematite, magnetite, maghemite, siderite, etc) in the past few decades, but the Recent Trends in the Technologies of the Direct 2018年4月1日 One process is that ironbearing substances are added to blended coals and then carbonized in a conventional coke oven [19] The other process is that ironbearing materials and blended coals are Effects of coal and iron ore blending on metallurgical properties does result in increased CO gas and more coal consumption The prereduction degree is the degree to which the iron oxides can be reduced in the prereduction shaft The heat transfer efficiency is the ratio of the heat transferred from hot gases to the bath of molten iron and slag component to the heat generated by the postcombustion unitAn Overview of the ReductionSmelting Process of Iron Oxides in

Overview of the Steel Production Process Springer
Iron ore consists of various oxides of iron (occurring as ironcontaining minerals) mixed with oxides of other metals (such as Al and Si) In the traditional route to produce steel, the ore is first ground and most of the noniron oxide minerals are removed through various means, a process referred to as beneficiationThe beneficiated ore is then made into various forms of prepared 2024年11月4日 At the high temperatures in the furnace, more coke reacts with carbon dioxide forming carbon monoxide Carbon dioxide has been reduced to carbon monoxide carbon + carbon dioxide → carbon monoxide Zone 3 Carbon monoxide reduces the iron(III) oxide in the iron ore to form ironExtraction of iron IGCSE Chemistry Revision Notes Save My 2021年3月8日 These processes operate with different feedstocks The BFBOF pathway converts raw iron ore to pig iron and then to steel HM – while EAF converts both steel scrap and sponge iron to steel HM DRI converts raw iron ore to sponge iron, a porous, permeable, and highly reactive product that requires treatment with EAF before selling to marketLowCarbon Production of Iron Steel: Technology Options, 2024年8月18日 The two categories of metallurgical coal are coal for coking and pulverized coal for injection in blast furnaces The most significant characteristics of coking coal are those determined by technical analysis (yield of volatiles, ash content, etc) and the metallurgical properties determining the quality of blast furnace coke For pulverized coal, the important Global Market for Metallurgical Coal Coke and Chemistry
.jpg)
Characteristics of CalciumAluminate Slags and Pig Iron
2018年7月25日 Pig iron and slag are the products of the smeltingreduction treatment For the targeted slag compositions, the CaO/Al 2 O 3 (C/A) mass ratios were in the range of 065 to 075 This C/A ratio range is appropriate to obtain slag phases that has good leaching properties, as was reported in the literature[11,12] The amounts of coke in the current study are 15 times 2016年3月30日 In book: Encyclopedia of Iron, Steel, and Their Alloys (pppp 10821108) Chapter: i) Direct Reduced Iron: Production; Publisher: CRC Press, Taylor and Francis Group, New York(PDF) i) Direct Reduced Iron: Production2024年2月6日 Based on the stoichiometric method and the free energy minimization method, an ideal model for the reduction of iron oxides by carbon and hydrogen under blast furnace conditions was established, and the reduction efficiency and theoretical energy consumption of the allcarbon blast furnace and the hydrogenrich blast furnace were compared The results Physicochemical principles of hydrogen metallurgy in blast furnace2017年10月10日 Ironmaking Blast Furnace Iron is made by reacting iron ore (iron oxide and impurities), coke (a reductant) and limestone (CaCO 3) in a blast furnace Iron ores with lower iron content such as taconite are first processed Ironmaking 101 – From Ore to Iron with Blast Furnaces
.jpg)
Comparative ecological and greenhouse analysis of alternative coke
2011年11月17日 A comparative analysis is made of greenhousegas emissions by alternative cokeless metallurgical processes for making pig iron, metallized pellets, and steel The concept of technological greenhouse number is used in the analysis Specific data obtained as part of an environmentalenergy analysis of the given processes show that DAV technology (direct 2023年10月13日 With an average iron oxide content of 40%, the overall 7 Mt could translate to an equivalent of 34 Mt of iron ore available in Europe Lime, an essential input to slag production in metal processing, drives the large water consumption in BRpig iron process per functional unit 1 ton pig iron (b) Life cycle assessment of pig iron production from bauxite residue: Effect of waste plastics addition on the reduction of iron oxide by metallurgical coke Reaction products were analysed using an IR gas analyser and a gas chromatography unit Journal of Iron and steel Institute of Japan International, 43: 15021511 Jones, J (2007) “Utilisation of pig iron in the electric arc furnace” An Effect of waste plastics addition on the reduction of iron oxide by 2023年10月13日 With an average iron oxide content of 40%, the overall 7 Mt could translate to an equivalent of 34 Mt of iron ore available in Europe Lime, an essential input to slag production in metal processing, drives the large water consumption in BRpig iron process per functional unit 1 ton pig iron (b) Life cycle assessment of pig iron production from bauxite residue:
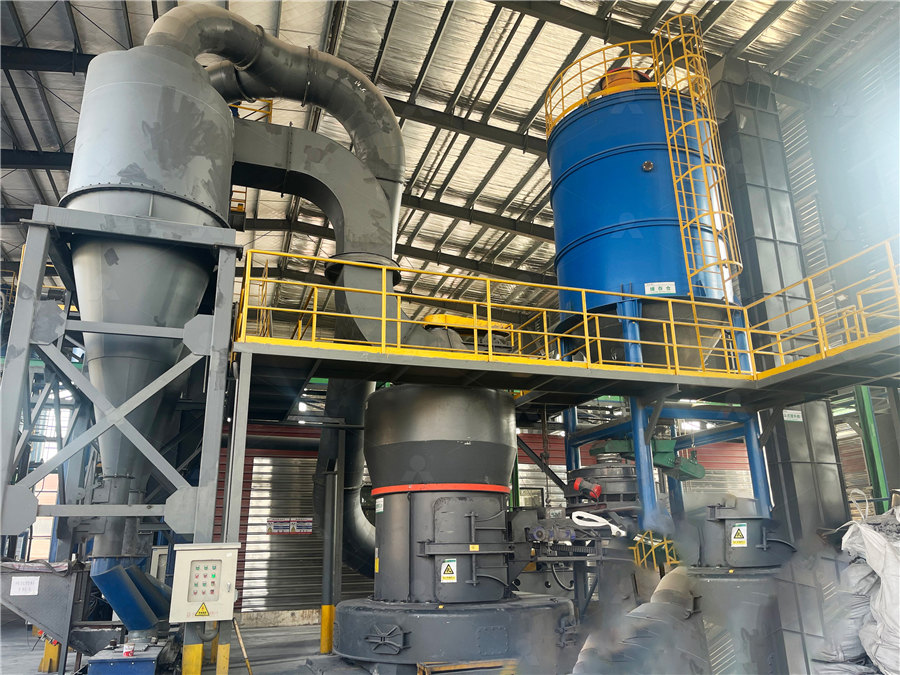
Production of pig iron by utilizing biomass as a reducing agent
2013年3月1日 As a novel application, biomass has demonstrated to be an effective reducing agent for iron oxides reduction in ironmaking processes Raw biomass [10, 11], biomassderived char [12], syngas [9 2024年6月17日 Keywords: iron making, direct reduction of iron ore, natural gas, coal, coke, MIDREX, green steel production, sponge iron Reduction and carburization reactions those are important for DRI generation(PDF) Industrial Project Report on Metallurgical Review: 2017年2月16日 Sintering is a thermal agglomeration process that is applied to a mixture of iron ore fines, recycled ironmaking products, fluxes, slagforming agents and solid fuel (coke)(PDF) Iron Ore Sintering: Process ResearchGate2022年8月23日 The results showed that an iron recovery rate of 90 78% and an iron content of 92 53% of iron concentrate could be obtained by such a technique The optimized roast temperature is 1200 °C and (PDF) An Overview of the ReductionSmelting Process
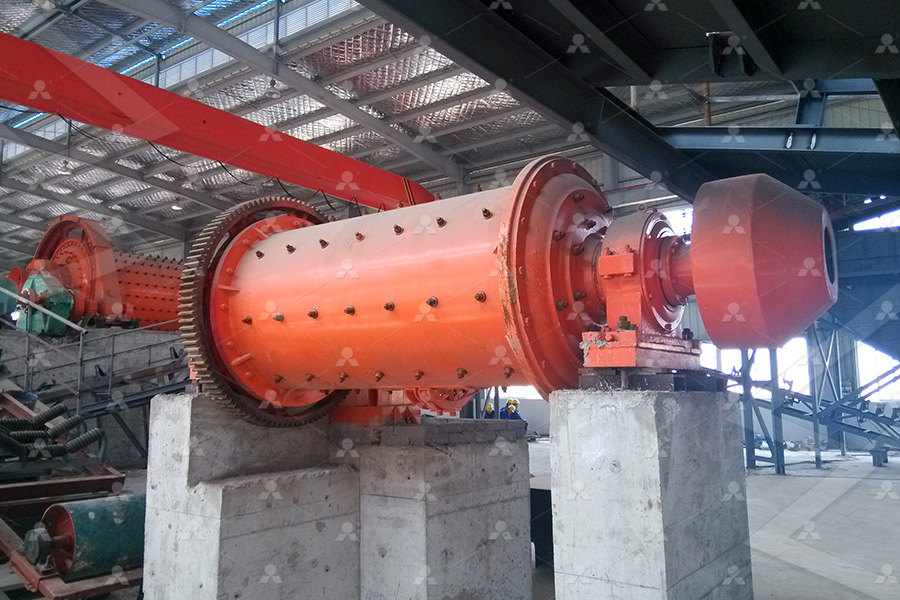
233: Metallurgy of Iron and Steel Chemistry
Originally, the iron was collected in pools called pigs, which is the origin of the name pig iron Figure \(\PageIndex{1}\): A Blast Furnace for Converting Iron Oxides to Iron Metal (a) The furnace is charged with alternating layers of iron The Pig Iron unit commenced commercial operations in 1994 with initial rated capacity of 120,000 tpa for manufacture of Pig Iron with 3 MW captive cogeneration power facility The facility was modernized and expanded in 2004 to a rated capacity of 210,000 tpa of Pig Iron and 1143 MW captive cogeneration of power involving capital outlay of INR 450 millionManufacturing Facilities Satavahana Ispat Limited2020年6月10日 224 Direct Reduction of Iron Oxide by Solid Carbon The direct reduction process of iron oxide by solid carbon is highly endothermic in nature and occurs when the molten slag flows over incandescent coke in the bosh region at a temperature above 1000 °C Therefore, the corresponding reaction can be written as follows:Iron and SteelMaking Process SpringerLink2016年11月1日 The pig iron produced from this process contained of 9362%Fe, 35%C, 155%Si, 087%Mn, 005%P, and 0087%SWith this result, the pig iron produced already fulfill the metallurgical specification (PDF) The production of pig iron from crushing plant waste using hot
.jpg)
Industrial and High Capacity Granulation of Pig Iron
The GRANSHOT® unit can be designed for hot metal from torpedo or • Ideal metallurgical properties; homogeneous, low oxide content, fast dissolution and melting • Totally inert and ideal for automatic handling • Granules with a deformed spherical shape Granulated Pig Iron, GPI, has ideal metallurgical and logistical properties for use 2013年12月12日 I ron making is the pyrometallurgical process of turning solid iron ore materials into liquid hot metal called pig iron typically saturated with carbon (≈5 wt pct) The process uses injection of air and metallurgical coke in a countercurrent flow reactor called a blast furnace (BF) This is probably one of the metallurgical processes that has captivated the most attention of Process Simulation and Control Optimization of a Blast Furnace 2023年7月1日 The iron and steel industry demands 8 % of the energy [8] and emits 7 % of the greenhouse gases (GHG) globally [2, 9]The blast furnace followed by the basic oxygen furnace (BOF) route remains the most efficient and costeffective pathway to crude steel production, of which the blast furnace is the most intensive stage in energy use and GHG emission in the Rigorous environmental and energy life cycle assessment of blast Raw material: Contains: Function: Iron ore (haematite) Iron(III) oxide (Fe 2 O 3): A compound that the iron is extracted from: Coke: Carbon (C) Used as a fuel and reacts to form carbon monoxide Redox, extraction of iron and transition metals Extracting iron
.jpg)
(PDF) Properties and features of direct reduced iron
2007年1月31日 Iron oxide feed stocks Pellets, lump, and fine ore Pellets, lump, and fine ore, green balls, iron oxide waste materials Reduction temperatures ( C) 850–950 C 950–1050 C