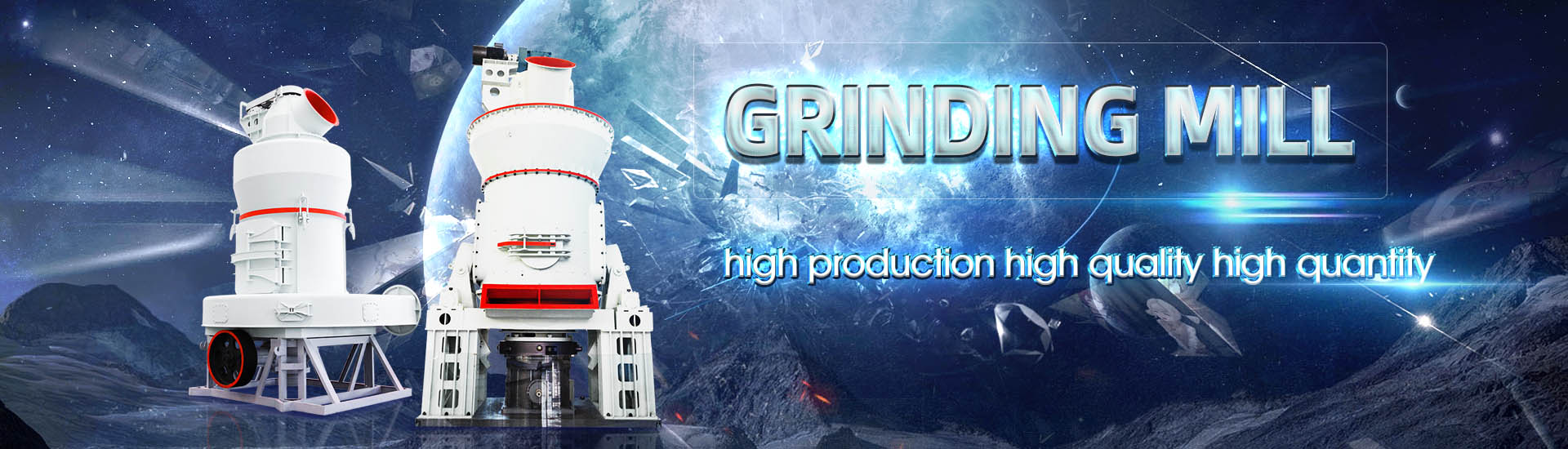
How to improve the highpressure grinding mill
.jpg)
BALL MILLS Ball mill optimisation Holzinger Consulting
o grind raw materials and cement Roller presses are used mainly in combi ion possibilities (see Figure 1) The ball mill comminution process has a high electrical energy consumption, 2022年3月1日 High Pressure Grinding Rolls (HPGR) circuits have the potential to reduce the Mining Industry’s CO2 emissions by up to 345 megatonnes/year, or 435% when compared to the established AutogenousHelping to reduce mining industry carbon emissions: A 2010年8月1日 High pressure grinding roll (“HPGR”) technology is very rapidly gaining a wide acceptance within the mineral processing industry Benefits, including a superior energy Flowsheet considerations for optimal use of high pressure 2023年1月1日 Scaling up HPGRtower mill comminution circuit should consider size reduction ratio This paper presents the commercial implementation of a novel comminution circuit with Evaluating the performance of an industrialscale high pressure
.jpg)
Modelling of HPGR Edge recycling with progressive grinding data
However, it is still possible to increase the HPGR advantages by applying the right flowsheet Concepts like screen recycling versus edge recycling and progressive grinding are options for 2022年3月16日 HPGR has been found to be efficient size reduction equipment compared to conventional size reduction equipments due to its potential processing benefits in terms of Potential of HighPressure Grinding Roll (HPGR) for Size Reduction Wear increases with pressure, thus reducing operating pressure would lead to a longer roll surface wear life Pilot testing determines how product size is affected by operating pressure, HIGH PRESSURE GRINDING MOVING AHEAD IN COPPER, IRON, 2024年5月31日 In order to solve the existing problems of long process flow and high grinding energy consumption in Gongchangling beneficiation plant, this paper proposes the addition of High Pressure Grinding Roll and Magnetic Separation for Energy
.jpg)
Potential of HighPressure Grinding Roll (HPGR) for Size Reduction
In comminution, the primary objective of grinding is to reduce the particle size to an optimum mesh of grind so that the valuable minerals are physically liberated from the gangue minerals This expansion was accomplished via the installation of secondary and high pressure grinding rolls (HPGR) crushing of the ore, with the semiautogenous grinding (SAG) mill receiving a combination of primary, secondary and HPGR crushed feed This design, criteria and rationale for selection was presented at the SAG Conference 2011Cadia Expansion The Impact of Installing High Pressure Grinding Rolls Enduron® high pressure grinding rolls (HPGR) can handle a wide variety of ores and particle sizes from fine pellet feed all the way up to coarse grinding of 75mm magnetite iron ore When it comes to feed material characteristics, the Our Dynamic HPGR Technology for Mineral Grinding2017年10月25日 The energy specific grinding rate of the coarse material in the ball mill can then be defined as follows: The mill specific grinding rate reflects both the efficiency of the mill environment in breaking the coarse particles, as well as the grindability characteristic of the ore over the particular size reduction rangeHow to Improve Ball Mill Performance 911Metallurgist
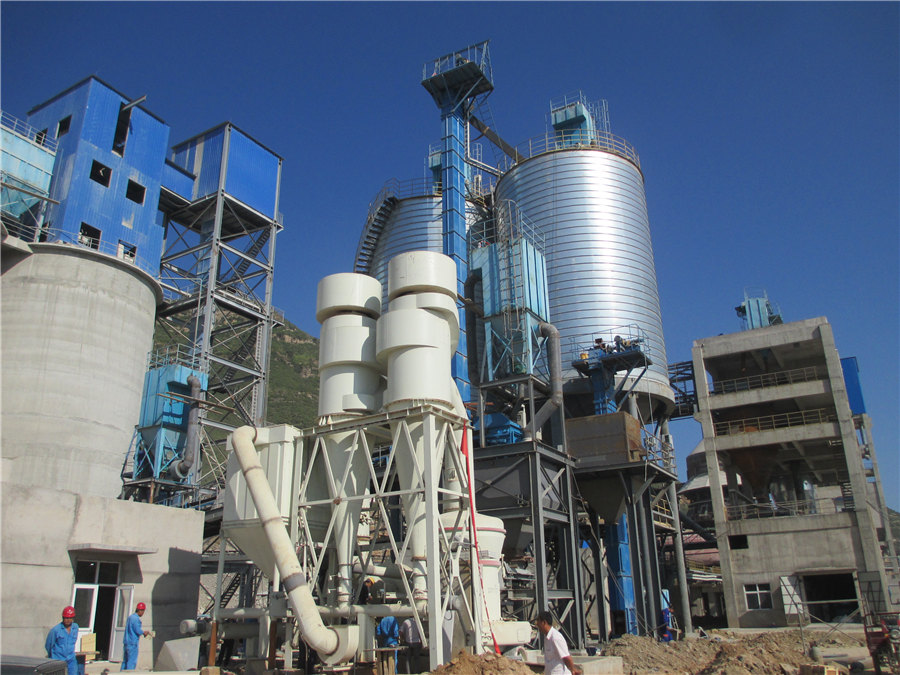
Potential of HighPressure Grinding Roll (HPGR) for Size
2022年3月16日 Abstract HPGR has been found to be efficient size reduction equipment compared to conventional size reduction equipments due to its potential processing benefits in terms of energy savings, improved exposure or liberation and particle weakening The objective of the current work is to study the optimization of different process parameters during grinding The amount of feed in the mill can be tested by 3 methods: Grinding roller limit device clearance; The power of the mill (ie the main motor current); Metering of belt scales; If the layer is too thick, the following phenomena will occur: The mill pressure difference increases; Grinding machine vibration increases; Mill current increases;How to Improve Grinding Efficiency of Vertical Roller MillDownload scientific diagram Relationship between SAG mill power draw, bearing pressure and feed rate from publication: Supervisory Fuzzy Expert Controller for SAG Mill Grinding Circuits: Sungun Relationship between SAG mill power draw, bearing pressure and Köppern – Specialists in HighPressure Comminution 7 Improved CostEfficiency Highpressure grinding roll presses (HPGRs) are emerging as an important comminution technology in the minerals processing industry The technology has found its key application in the liberation of diamonds and also in primary comminutionHighPressure Grinding
.jpg)
Why gold mines are adopting HPGRs to increase production and improve
2021年2月2日 How HPGR improves gold recovery There are two main ways mines recover gold ore from the gangue, and HPGRs can assist with each process One of them is heap leaching and for mines using this process, we’ve found that the most efficient setup is to have a HPGR perform tertiary grinding immediately prior to recovery, completely avoiding the use of a 2015年3月10日 In the present study, size reduction experiments were performed on HighPressure Grinding Rolls (HPGR), ball mill and stirred mill of PGE bearing chromite ore The performance of HPGR was evaluated in two stages of size Effect of operational parameters and recycling load on the high 4 天之前 The problem of high temperatures in ball mills is a prevalent problem that needs to be addressed to improve their performance and efficiency By implementing the solutions discussed in this article, such as proper lubrication, regular maintenance, and the use of cooling devices, the temperature of a ball mill can be effectively controlledFour Ways To Improve The High Temperature Problem Of Ball MillYGM Series High Pressure Suspension Grinding Mill can produce powder from various nonflammable and nonexplosive mineral materials with Mohs hardness below 93 and humidity below 6%, there are mainly applied in the industries YGM Series High Pressure Suspension Grinding Mill
.jpg)
How to Improve Cement Ball Mill Performance
High Pressure Grinding Roll; Cement Ball Mill; Vertical Roller Mill; Cement Mill Separator; Cement Mill; Others Menu Toggle Conveying System; Overland Conveyor; Vibrating Grizzly increase the impact times of balls on materials, 2017年10月26日 The following are factors that have been investigated and applied in conventional ball milling in order to maximize grinding efficiency: a) Mill Geometry and Speed – Bond (1954) observed grinding efficiency to be a Factors Affecting Ball Mill Grinding Efficiency2024年5月31日 This paper presents an industrial verification test, adding a high pressure grinding roll and magnetic separation operation after the thirdstage fine crushing operation to reduce the particle size of ball mill feed and improve the processing capacity of grinding operation The optimal process parameters of high pressure grinding roll and magnetic separation were High Pressure Grinding Roll and Magnetic Separation for Energy 2017年9月17日 Functional performance analysis of ball milling has been described previously by Mclvor “Coarse” versus “fine” or product particle cutoff size is first selected, usually equal to some benchmark passing size of the circuit product (eg, 80%)How to Improve Ball Mill Grinding 911Metallurgist
.jpg)
(PDF) Optimization and performance of grinding circuits: the
2020年1月16日 The analysis of survey data revealed inefficient grinding operation characterized by ball mill product (x P 80 > 400 µm) coarser than designed and higher hydrocyclone cut sizes (x T > 200 µm), too2010年1月1日 High Pressure Grinding Rolls ('HPGRs') presently are seen as a standard technology to be considered in feasibility studies, as an alternative to be compared with more conventional crushing and High pressure grinding rolls scaleup and experiencesHigh Pressure Grinding Rolls have been used for the grinding of diamond and iron ores since about 1988 There are now about 40 machines operating worldwide in these industries This number is still small in comparison to the > 450 machines employed in High Pressure Grinding Rolls for Minerals AusIMM2 Enduron® High Pressure Grinding Rolls 3 Proven for over 30 years HPGR benefits This cuts operating expenditure and improves stability of the floatation/leaching circuit settings, tramp material, such as SAG mill balls, will occasionally make its way into the HPGR feedEnduron High Pressure Grinding Rolls Weir Group
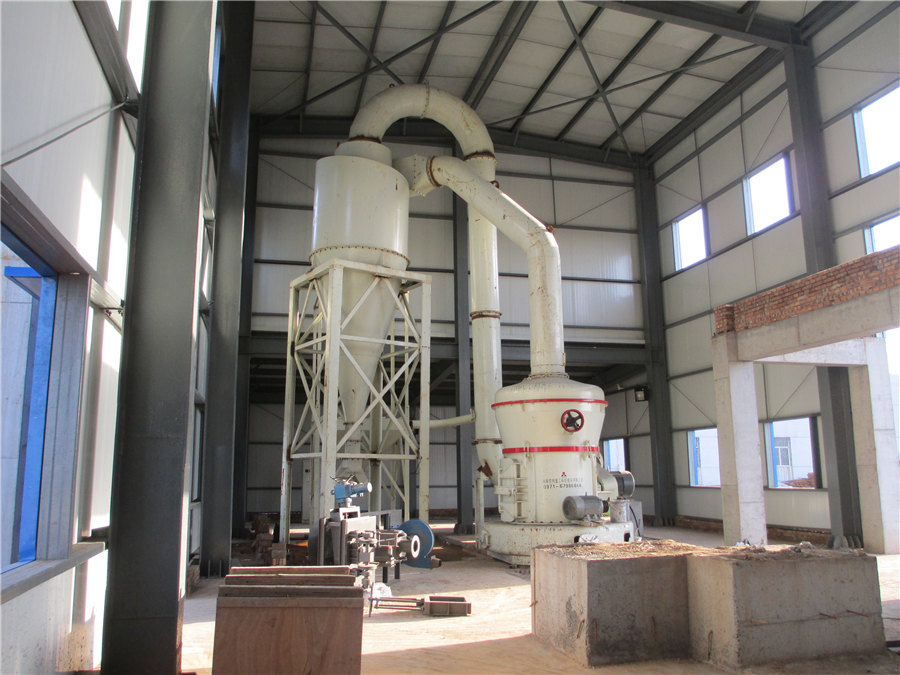
10 Ways to Improve the Grinding Efficiency of Your Ball Mill
Here are the 10 ways for your to improve the ball mill performance: Step#1 Change the original grindability Step#2 More crushing and less grinding to reduce the feed size into mill Step#3 High grinding density, the material is easy to stick around the steel ball, High Pressure Grinding Mill is a mill with more advanced technology, more reliable performance and more efficient output than Raymond mill The machine adopts a number of patented technologies of pulverizers such as flexible connection and roller linkage pressurization, and improves the Shatter effect 1High Pressure Mill, High Pressure Roller Mill, High Pressure Grinding High pressure grinding mill, also known as high pressure roller mill, can grind nonflammable and explosive materials into fine powder +17 [ protected] The grinding force of each grinding roller assembly can be YGM High Pressure Grinding Mill2006年2月1日 Request PDF High pressure grinding rolls These improvements will allow the cement to be milled with less electricity and also improves the capacity of the cement millHigh pressure grinding rolls (HPGR) applications in the cement industry
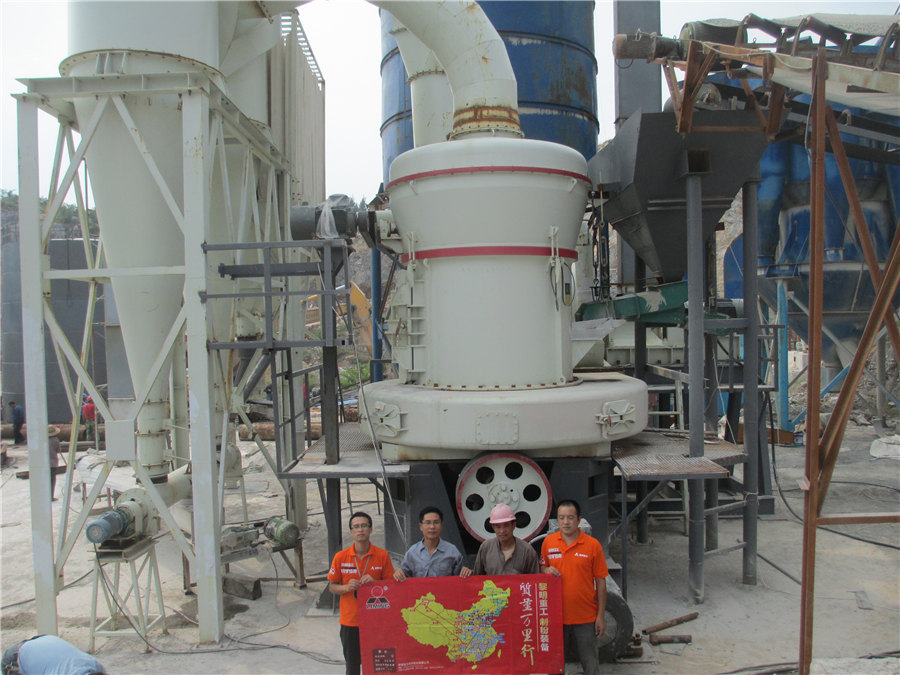
HPGR – High pressure grinding rolls/rollers
The HPGR (high pressure grinding rolls/rollers) is the core equipment of the high pressure grinding process The machine reduces particles by compressing and crushing the feed between two counter rotating, parallel rollers with a small gap between them This forces the rocks against each other and compresses the feed’s density to 80% of its solid []2016年10月5日 In this chapter an introduction of widely applied energyefficient grinding technologies in cement grinding and description of the operating principles of the related equipments and comparisons over each other in terms of grinding efficiency, specific energy consumption, production capacity and cement quality are given A case study performed on a EnergyEfficient Technologies in Cement Grinding IntechOpenHRCtrade; Series high pressure grinding rolls (HPGR) are most often utilized when the processed material is hard rock However, they can also refine softer materials like industrial minerals The smaller models of the are particularly productive in producing manufactured sand for asphalt and concrete Highpressure mill HRC™ Metso Corporation roller / 2009年5月1日 High Pressure Grinding Rolls (HPGR) circuits have the potential to reduce these emissions by up to 328 Megatonnes/year, or 443% when compared to the Semiautogenous/ball mill circuit alternativesPredicting the overall specific energy requirement of crushing, high
.jpg)
Use of drilling performance to improve rockbreakage
2020年3月1日 This characteristic caused an inconsistent phase of the grinding speed in the tumbling mill The particle size quickly reduced to 100–200 μm, but additional grinding at finer sizes produced almost no change due to the high hardness of the silicate Therefore, it was difficult to achieve a steady state for calculating GprCondition in one of the grinding chambers of the mill Results of Optimization The graphical analysis presented in Figure 2 represents progress of grinding along the length of the mill after optimizing the grinding process rogress of grinding is clearly visible in Desired p the graphs Figure 2: Analysis of longitudinal samplesOPTIMIZATION OF CEMENT GRINDING OPERATION IN BALL MILLS2015年4月9日 High pressure grinding rolls The high pressure grinding rolls, often referred to as HPGRs or roller press, consists out of two rollers with the same dimensions, which are rotating against each other with the same circumferential speed The special feeding of bulk material through a hopper leads to a material bed between the two rollersGrinding Mills and Their Types – IspatGuru2023年7月4日 The basic structure of the roller mill includes the grinding roller, the grinding body, the force generation and transmission mechanism, airflow, and the device for easy replacement It can be divided into vertical roller mill, horizontal cylinder roller mill, high pressure roller mill, Raymond mill, and column millRoller Mill SpringerLink
.jpg)
The effect of rolls speed and rolls surface pattern on high pressure
1997年4月1日 An important aspect in the performance of the high pressure grinding rolls (HPGR) is its throughput The HPGR throughput can be changed by varying the speed of the rolls, but, it is important to determine the effects of changes in the rolls speed together with other variations such as grinding force and feed size, on the overall performance of the HPGRexperience high collisional energies, as they are ejected from the bed and impact on return effect of grinding pressure and hold[3] Therefore, particle size reduction is the result of both chipping and fragmentation in the mill [4] Grinding conditions in the spiral jet mill have beenAnalysis of holdup and grinding pressure in a spiral jet mill comminution product in grinding and milling High and rising energy prices can make a real dent in your profitability Bring down energy consumption and increase your overall efficiency with the HPGR Pro, our latest generation high pressure grinding roll HPGR Expertise 35+ years of experience supplying HPGR’s to mining customersHPGR / HPGR Pro The next level in grinding FLSmidth2023年12月7日 The pressure is on for mine operators to increase efficiency and improve overall recovery despite falling ore qualities With this in mind, grinding is well known to be the main engine of any concentrator Grinding is the essential first step in reducing the material for downstream processes, such as flotation and separationCase study: Industry 40 – Advanced mill optimisation AusIMM
.jpg)
Full article: Review of HighPressure Technology in Terms of
2024年10月1日 HPGR operation in the closed circuit also improves the overall energy efficiency while maintaining the same level of final product fineness Comparing economic model predictive control to basic and advanced regulatory control on a simulated highpressure grinding rolls, ball mill, and flotation circuit2021年2月2日 How HPGR improves gold recovery There are two main ways mines recover gold ore from the gangue, and HPGRs can assist with each process One of them is heap leaching and for mines using this process, we’ve found that the most efficient setup is to have a HPGR perform tertiary grinding immediately prior to recovery, completely avoiding the use of a Why gold mines are adopting HPGRs to increase production and improve 2020年9月8日 How to solve these problems? Here are some methods to improve the yield and production efficiency of Raymond mill 1 Reasonable selection of engine speed and improvement of grinding force Because the grinding force mainly comes from the centrifugal force of the grinding roller, the rotation speed of the main engine directly affects the Six Methods to Improve the Efficiency of Raymond Mill