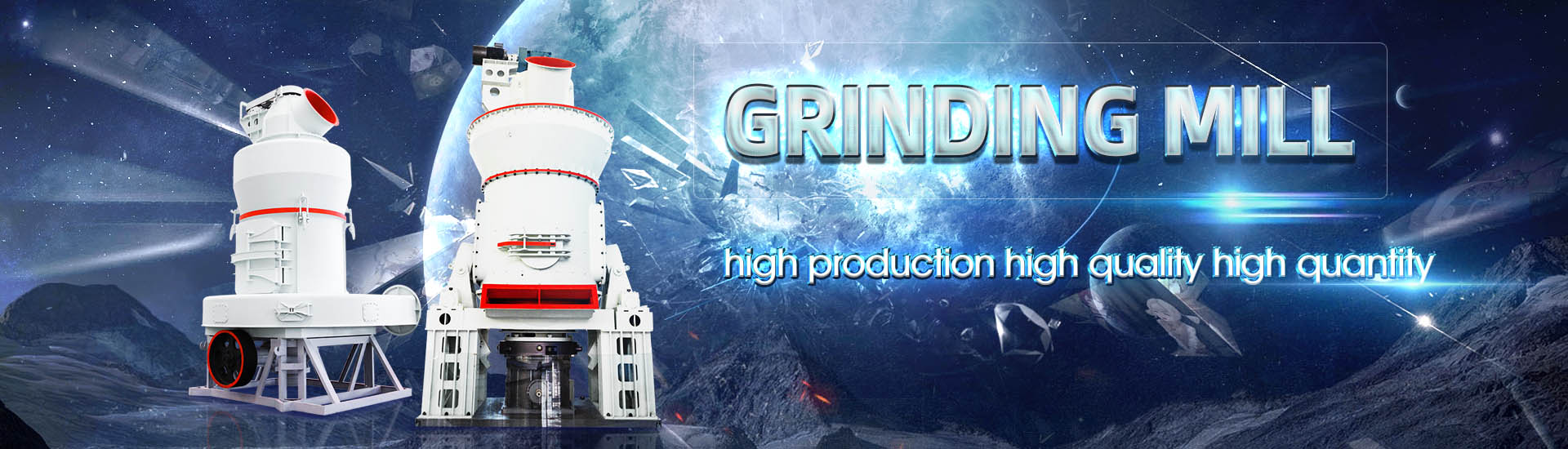
Safety technical operating procedures for coal mills
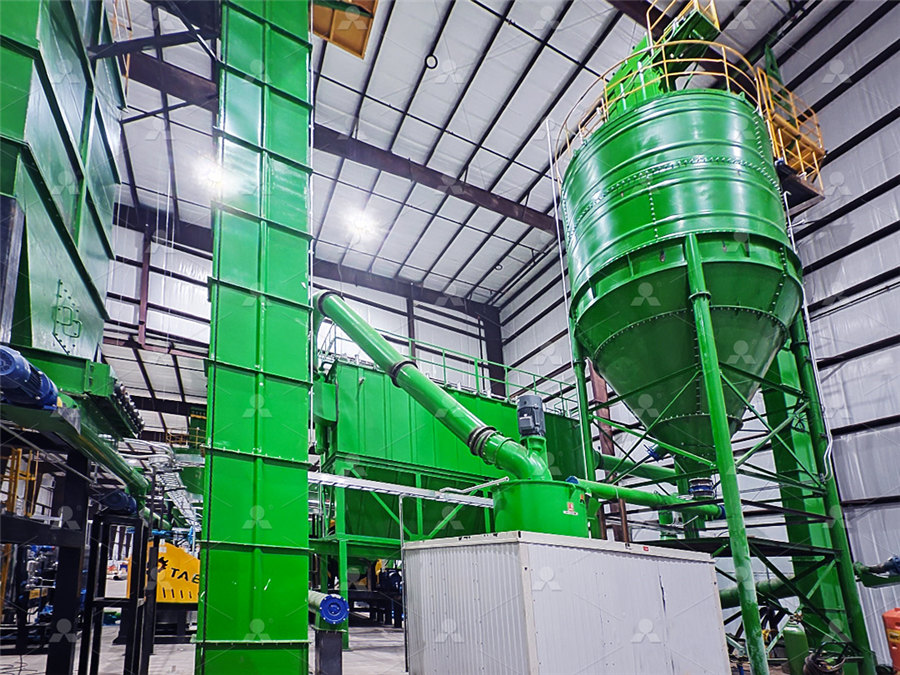
Ensuring Safety in Coal Mills – Best Practices and Precautions
Regular maintenance, effective dust control, comprehensive training, and emergency preparedness are key components in ensuring a safe working environment in coal mill operations Through continuous vigilance and proactive management, hazards can be mitigated or avoidedEnsuring the safe operation of coal mills is crucial for preventing accidents, Coal Mill Safety: A Critical AsEnsuring the safe operation of coal mills is crucial for preventing accidents, maintaining plant efficiency, and safeguarding the health of workers This article explores the key aspects of Coal Mill Safety: A Critical Aspect of Power Plant Operations Coal Coal preparation activities (eg, use of dryers), coal gasification , feeding and ash removal) and coal liquefaction processes may generate pointsource emissions of dust and heavy oils (tars) Environmental, Health and Safety Guidelines for Coal Processing
.jpg)
COAL HANDLING SAFETY Land Instruments International
Safe coal handling practices are designed to ensure that the fuel remains intact throughout its journey from the mine until the point at which it is ignited in the boiler It takes as little as 14 kg Coal grinding operations present significant safety challenges, but with comprehensive safety measures and a proactive approach, these risks can be effectively managed Prioritizing dust Ensuring Safety in Coal Grinding Operations Coal Mill Safety effective occupational health and safety risk management processes in mines It demonstrates how to establish the proper context of a mining operation, and then how to effectively identify, Risk Management Manual Coal ServicesSafe coal handling practices are designed to ensure that the fuel remains intact throughout its journey from the mine until the point at which it is ignited in the boiler Risks of unwanted COAL MILL Land Instruments International
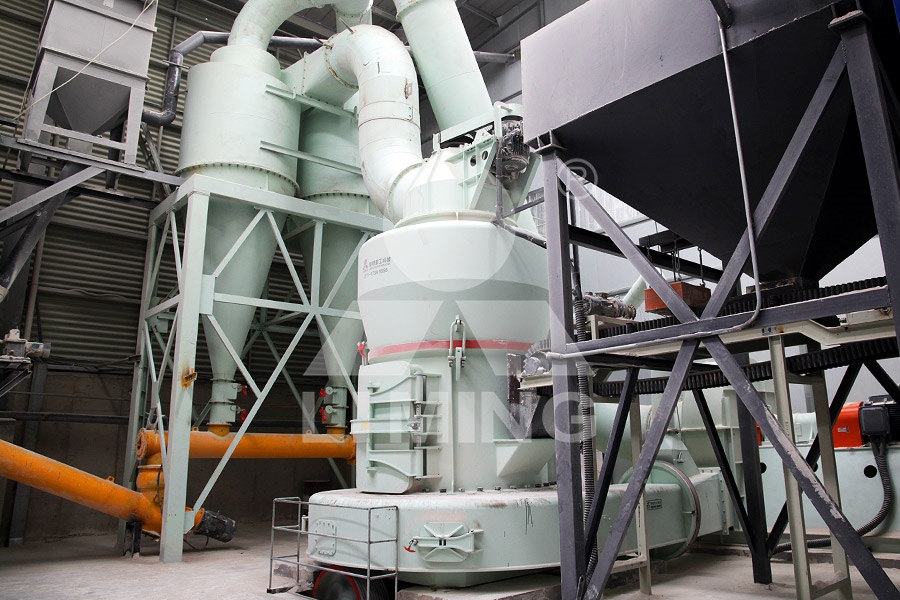
Safety and health in coal mines International Labour Organization
Safety and health in coal mines This code of practice is intended for the use of all those, both in the public and in the private sectors, who have responsibility for safety and health in coal Safety considerations, such as the prevention of fire or explosion are of utmost importance as is the knowledge of how to proceed under normal conditions The training program should COAL GRINDING SYSTEMS SAFETY CONSIDERATIONS PEC 2020年11月25日 This article starts with the analysis of the problems in coal mine safety management, and puts forward strategies to strengthen coal mine safety management to improve the safety of coal mine Safety Management of Coal Mining ProcessIf the pulverized coal undergoes spontaneous heating and the coal mill is restarted with hot embers present, an explosion or fire is possible Although this does not happen often, the chances increase when a coal mill is frequently shut down and then restarted A coal mill system that goes down, particularly under load, must be treated with Coal Grinding Systems Safety Considerations PEC Consulting
]@S0{UDKK%G24F3JGHC.jpg)
Coal Mill Safety PDF Coke (Fuel) Scribd
This document discusses safety aspects of coal mill operations It outlines the general safety rules, ignition process, oxygen concentration limits, protection measures, and safety control systems for coal grinding The key points are: Coal preparation activities (eg, use of dryers), coal gasification , feeding and ash removal) and coal liquefaction processes may generate pointsource emissions of dust and heavy oils (tars) Appropriate technology should be selected to minimize 4 Examples include: API Standard 620: Design and Construction of Large,Environmental, Health and Safety Guidelines for Coal Processing1927 First Loesche coal mill delivered for the Klingenberg power station in Berlin 1953 500th coal mill plant sold worldwide 1961 Introduction of hydraulic spring assembly system 1965 Construction of first pressure mill (LM 122 D) 1980 Delivery of first modular coal mill (LM 263 D) 1985 Delivery of first selfinerting coal grinding plant (LM 212 D) for the steel industry (PCI LOESCHEMILLSIt takes as little as 14 kg (3 lbs) of pulverised coal in 28 m3 (1,000 ft3) of air to form an explosive mixture Since a large boiler burns over 40 kg (88 lbs) or more of coal per second, the safe burning of pulverised coal necessitates strict adherence to planned operating procedures STRENGTHENING PLANT SAFETY IN COALSTRENGTHENING PLANT SAFETY IN COAL GRINDING MILLS
.jpg)
Strengthening safety in mills and silos Power Engineering International
2014年11月17日 Good operating procedures are designed to ensure that coal is used before it has time to selfignite, and many operators use a nitrogen blanket to minimize the scope for oxidation Even with appropriate precautions, silo fires can still occur and appropriate monitoring is needed to prevent oxidation from developing into a silo fireThis document provides the standard operating procedure for the operation and maintenance of ball mills at United Cements Pvt Limited It outlines the responsibilities of department heads and section incharges The procedure describes safe work practices for operating and maintaining ball mills including ensuring proper maintenance and use of personal protective equipment Sop For Om For Ball Mill PDF Personal Protective EquipmentSAFETy IN COAL MINES Coal mining poses several inherent, operational and occupational hazards and associated risks to the work persons Hence, safety Mill Te Per 3 Lac Manshifts Per Mill Te Per 3 Lac Manshifts 197579 157 196 1224 1278 218 044 1424 289 198084 122 143 1018 1065 129 030 975 226SAFETY IN COAL MINESThe safety record and availability history of coal pulverizing systems in the electric utility industry is com mendable The potential for fires and explosions inherent in air and pulverized coal mixtures has been studied for over 60 years Design and operating practices have evolved to a state that allows the safe, practicableFire and Explosion Prevention in Coal Pulverizing Systems
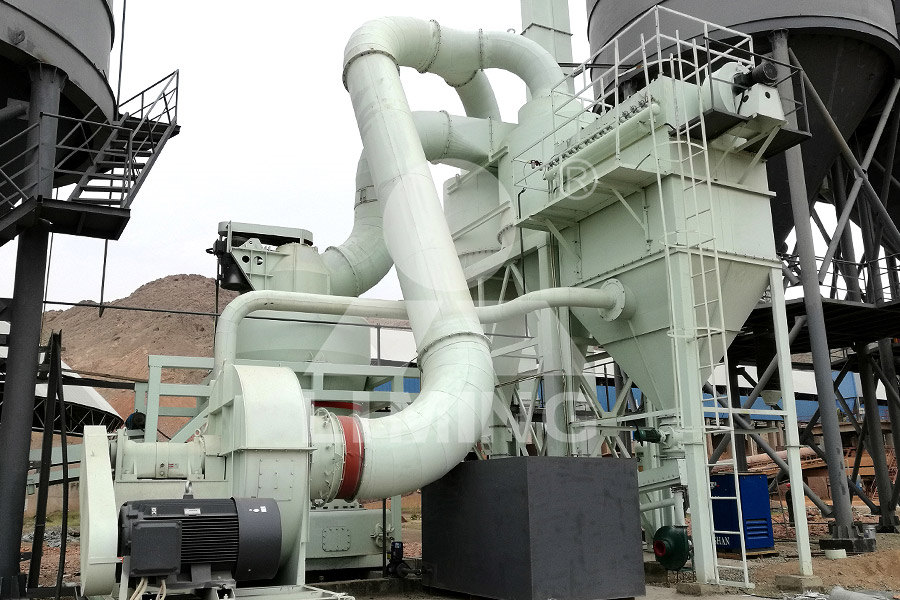
Operating Procedure and Training Curriculum at 55% Minimum Technical
2 STANDARD OPERATING PROCEDURE FOR 55% MINIMUM TECHNICAL LOAD OPERATION 21 Objective To enable coal based thermal Generating Units to run at a Technical Minimum Load of 55% of Rated capacity 22 Scope This document covers the operating procedure for reducing Unit load from peak load to the current Technical Minimum Load ie are, on the one hand, vertical roller mills that have achieved a share of almost 90 per cent and, on the other, ball mills whose share is recorded at just over 10 per cent1 Mill design features and benefits GPSE supplies standalone MPS coal grinding mills as well as complete coal grindingdrying systems Both mill andCOAL GRINDING IMPS: more than meets the eye Gebr PfeifferIt takes as little as 14 kg (3 lbs) of pulverised coal in 28 m3 (1,000 ft3) of air to form an explosive mixture Since a large boiler burns over 40 kg (88 lbs) or more of coal per second, the safe burning of pulverised coal necessitates strict adherence to planned operating procedures STRENGTHENING PLANT SAFETY IN COALCOAL HANDLING SAFETY Land Instruments InternationalObserverBased and Regression ModelBased Detection of Emerging Faults in Coal Mills Peter Fogh Odgaard, Sten Bay Jørgensen, in Fault Detection, Supervision and Safety of Technical Processes 2006, 2007 2 THE COAL MILL The work presented in this paper, is based on a Babcock MPS 212 coal mill used at Elsam’s Nordjyllandsværktet Unit 3 However, the Coal Mill an overview ScienceDirect Topics
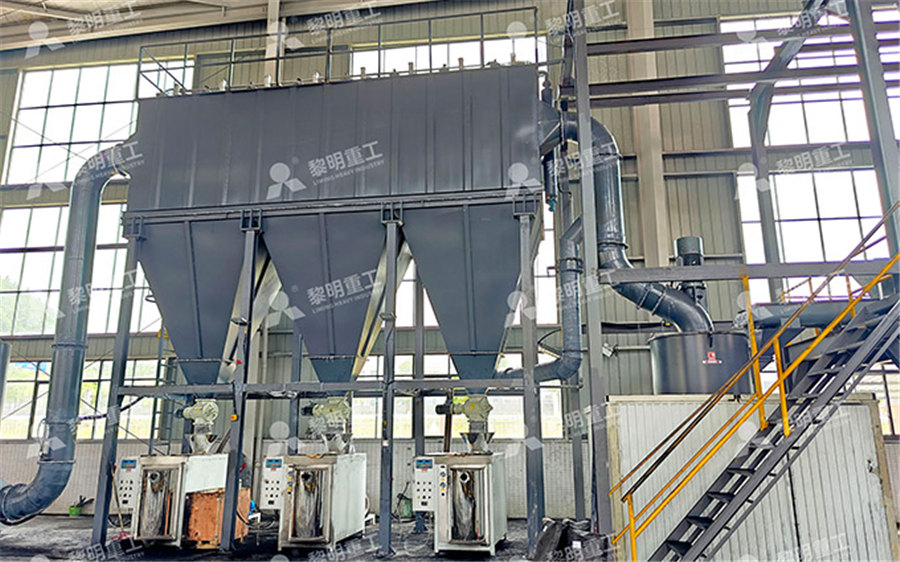
SAFETY CODE FOR IRON STEEL SECTOR MINISTRY OF STEEL,
iv Finishing mill v Cooling bed vi Shearing section/finishing yard vii Dispatch yard Some of criticalEquipments/ facilities in Rerolling mills are as follows: Sl No Area Major equipments 1 Raw material section Conveyors, grinders, hoist/overhead crane etc 2 Reheating furnace section Coal Crushers/Pulveriser (hammer/ Jaw crusher), Pusher,It takes as little as 14 kg (3 lbs) of pulverised coal in 28 m3 (1,000 ft3) of air to form an explosive mixture Since a large boiler burns over 40 kg (88 lbs) or more of coal per second, the safe burning of pulverised coal necessitates strict adherence to planned operating procedures STRENGTHENING PLANT SAFETY IN COALCOAL HANDLING SAFETY Land Instruments InternationalStation capacity determines the quantum of coal to be handled by coal handling plant and thus the capacity of coal unloading system, crushers, coal conveying system etc Generally for unit size of 500 MW and above, one coal handling plant is provided to cater for two units Coal conveying system may cater to maximum three units to limitSTANDARD DESIGN CRITERIA/ GUIDELINES FOR BALANCE OF i ABSTRACT Coal pulverisers’ performance optimisation is an important process in power generation plants Pulveriser operation is costly; reliability and availability is key to power generation andPerformance optimisation of vertical spindle coal pulverisers
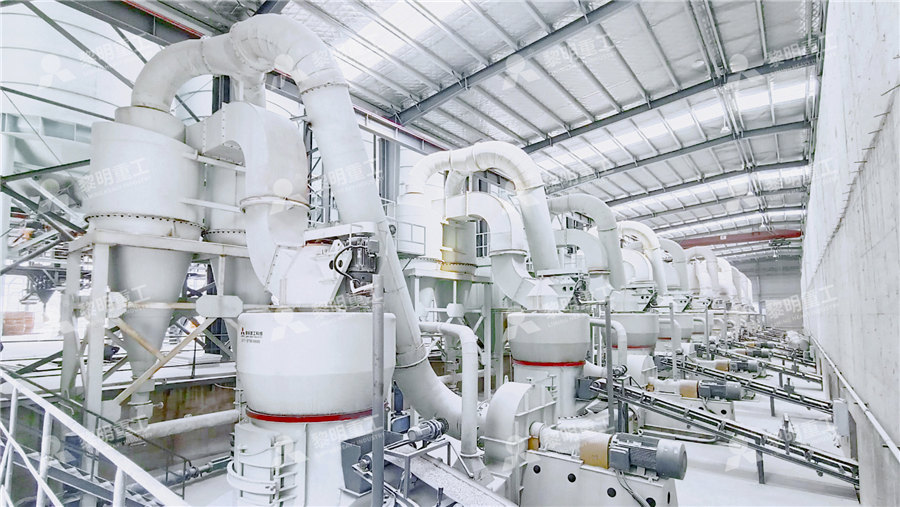
In discussion: Coal Mill Safety Coal Mill Safety, Explosion and
In discussion: Coal Mill Safety At best, coal mill safety is not well understood and, at worst, it is ignored When it comes to coal mill systems, most cement plant operators just presume that the supplier of the equipment knows all of the standards and rules and is 100% capable of making a system that conforms to these and is therefore safe2018年5月2日 Coal mill malfunctions are some of the most common causes of failing to keep the power plant crucial operating parameters or even unplanned power plant shutdowns Therefore, an algorithm has been developed that enable online detection of abnormal conditions and malfunctions of an operating mill Based on calculated diagnostic signals and defined Detection of Malfunctions and Abnormal Working Conditions of a Coal MillDetailed operating procedures and emergency response plans should be in place and regularly reviewed In discussion: Coal Mill Safety Optimisation of coal mill systems, with fire and explosion protection Protección contra incendios y explosiones en Understanding Pulverized Coal: Benefits, Risks, and Safety 2020年7月3日 Coal Mining Safety and Health Regulation 2017 Current as at 3 July 2020 Division 2 Standard operating procedures 109 Giving technical directions to opencut examiner 138 Part 3 Electrical activities, equipment and installationsCoal Mining Safety and Health Regulation 2017 Queensland

02 HIRAJSACoal Mill Operation PDF Safety
1) The document provides a job safety analysis for the task of starting a coal mill It lists the preparation required, including lockout tagout, tool box talks, and checks of equipment 2) The task is broken down into steps, and potential Publications and Interviews Safe operation of coal grinding systems: Raw coal silo protection against fire and explosions Safe operation of coal grinding systems: Raw coal yard management The purchasing process for coal grinding systems needs changes Talk at a virtual seminar, November 2023 Accept the probability that the fire and explosion safety of your coal grinding Industrial Explosion Protection Coal Mill Safety, Explosion and Safe Operating Procedures This SOP should be used in conjunction with relevant machinery manuals and manufacturer recommendations Procedure Reference Version Effective Date Review Date Page Number Date Printed WHS SOP 20 10 28/03/2018 28/03/2021 1 24/04/2018 SOP 20 – Feed Mill / Roller Mill Operation ServicingSafe Operating Procedures SOP 20 Feed Mill / Roller Mill Fuel quality is determined by the properties of the coal and by the design and operating specifications of the pulverising system Title: Coal pulverisers – performance and safety, IEACR/79 Author(s): David Scott Reference: IEACR/79 ISBN: ISBN: 9290292547 Publication Date: 01/06/1995 Pages: 83 Figures: 45Coal pulverisers performance and safety, IEACR/79 ICSC
.jpg)
What are the safe operating procedures for Raymond mills?
HCM Machinery has specialized in the production of new Raymond mills for decades, with good product quality, excellent service and an experienced team For more information on the safety operating procedures of Raymond mill, please feel free to consult, address:hcmkt@hcmillingSafety and health in coal mines This code of practice is intended for the use of all those, both in the public and in the private sectors, who have responsibility for safety and health in coal mines However, its contents may also be applicable to mines other than coal mines The code is not intended to replace national laws orSafety and health in coal mines International Labour Organization3 Fuel conveying – fine coal storage and conveying for an indirect firing system 4 Fuel conveying – fine coal conveying for a direct firing system 5Spillage and unsafe conditions at coal mill Kiln burner (firing system) The purpose of a kiln burner is to optimise the combustion of fuels to release heat in the kilnCOALcoal in its NCTPP, Dadri power plant and further expanded it to other Power plants NTPC has already prepared and implemented the Operating guidelines for Biomass Pellet cofiring in PF Boilers based on its technical and operating experience of cofiring This Standard Operating Procedure for Biomass Pellet cofiring in PF Boilers has been preparedStandard Operating Procedure for Biomass Pellet cofiring in PF
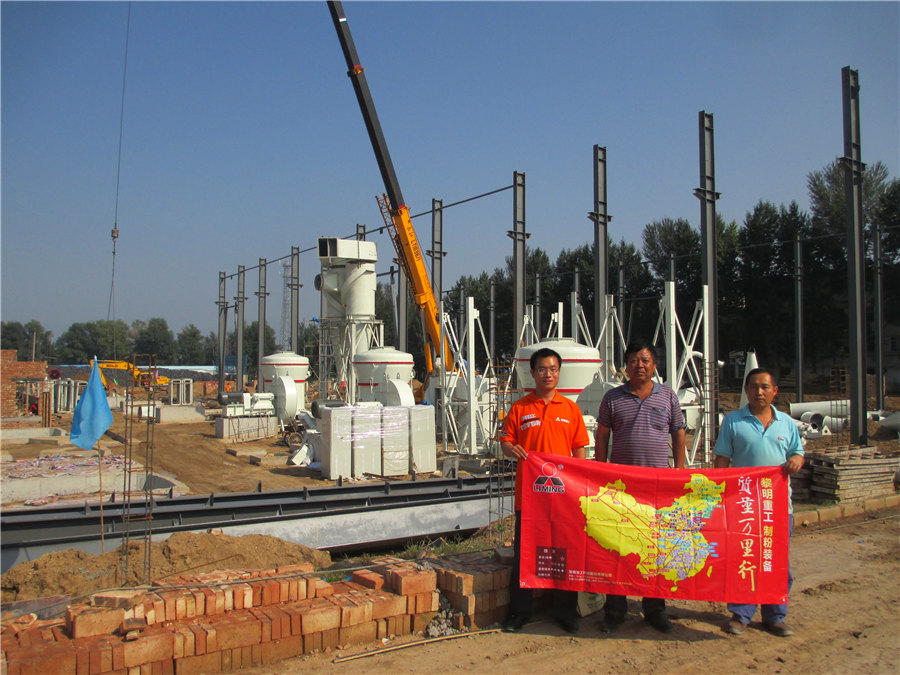
(PDF) MPS mills for coal grinding ResearchGate
2014年1月1日 Two mill systems are employed for most coal grinding applications in the cement industry These are, on the one hand, vertical roller mills (VRM) that have achieved a share of almost 90% and, on 2020年1月5日 The purpose of this SOP is to define the cleaning and operating procedure for Colloid Mill 20 Scope: This Safety Audit Procedure Checklist August 2, 2024 / 0 Comments AlCOA and ALCOA Plus Principles for Data SOP for Operation and Cleaning of Colloid MillCoal grinding is a critical process in various industries, particularly in power generation and cement production However, the process involves significant safety risks due to the combustible nature of coal dust and the mechanical hazards posed by the operation of the mill Ensuring safety during coal grinding is essential to prevent accidents, exAspects of Coal Mill Safety Coal Mill Safety, Explosion and Fire Sop Free download as PDF File (pdf), Text File (txt) or read online for free This document outlines the Standard Operating Procedure (SOP) for effective coal administration in Chhattisgarh as established by the Directorate of Standard Operating Procedure (SOP) For Effective
.jpg)
SAFETY IN COAL MINES Ministry of Coal
2 Statutory Framework for Coal Mine Safety: Coal mining, world over, is a highly regulated industry due to the presence of many inherent, operational and Occupational Hazards Coal Mine Safety Legislation in India is one of the most comprehensive and extensive statutory frameworks for ensuring Occupational Health and Safety (OHS)Overflow ball mills, on the other hand, are suitable for both coarse and fine grinding but require a higher level of maintenance Safety Procedures and Precautions Importance of Safety When Operating a Ball Mill Ball mills can be dangerous if not used properly It is essential to follow safety procedures to avoid accidents and injuriesA Comprehensive Guide to Ball Mill Manual31 CoalBased Thermal Power Plant 18 4BEST PRACTICES 24 41 CoalBased Thermal Power Plant 24 50 SELFASSESSMENT CHECKLIST 34 60 INTERNET OF THINGS (LOT) 40 ACRONYMS ABBREVIATIONS 41 BIBLIOGRAPHY 42 1 ACKNOWLEDGEMENT Auraiya Gas Power Station (AuGPS) (NTPC),Good Practices Manualsteam inerting systems for ball tube mills and coal pulverizers in general can be accomplished This should help in reducing the occurrence of pulverizer system explosions and increase the safety of operating personnel in coalfired steam electric stationsDynamic steam inerting system for a ball tube mill pulverizing
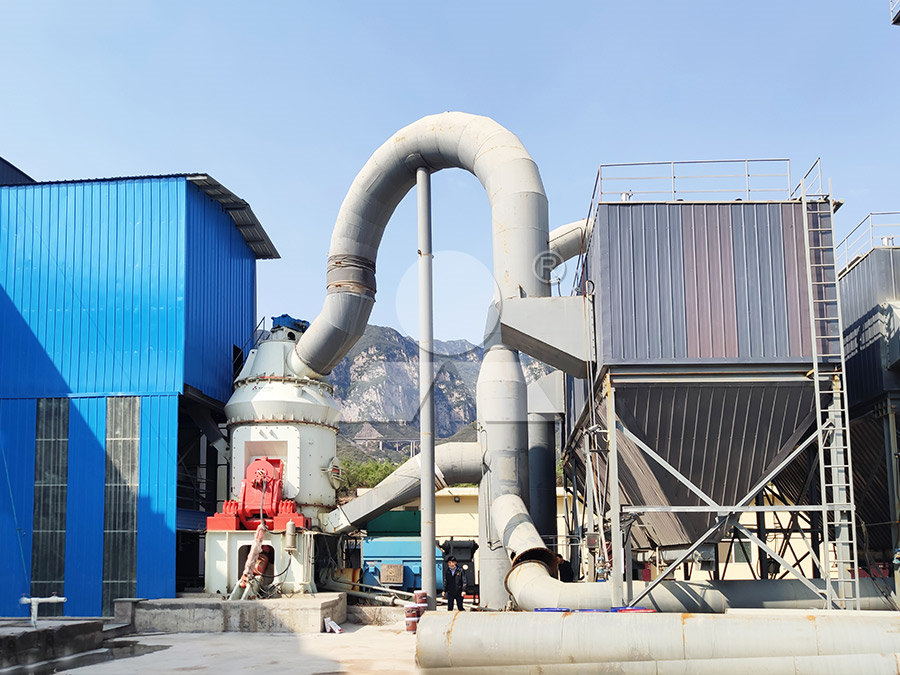
Mill Operators Manual Safety Haas Automation Inc
CAUTION: The sample programs in this manual have been tested for accuracy, but they are for illustrative purposes onlyThe programs do not define tools, offsets, or materials They do not describe workholding or other fixturing If you choose to run a sample program on your machine, do so in Graphics modespringloaded, MB type, vertical spindle mills, each gravimetric belt feeder, seal air fan, 1800 rpm primary air fan, and four mill outlets supplying pulverized coal to one of the three horizontal rows of (4) dualfuel burners When operating at boiler MCR, each mill had a coal throughput of approximately 53,000 #ffirWorldProven Coal Pulverizer Technology Debuts in the US2021年3月12日 Depending on this high feed moisture the mill rating is determined by the drying process whereas for anthracite, hard coal and petcoke the rating of the mill is determined by the grinding process The great variety of solid fuel properties, such as grindability, ash content, volatiles as well as the required product fineness, calls for a wide range of operating statesMPS mills for coal grinding AYS Engineering