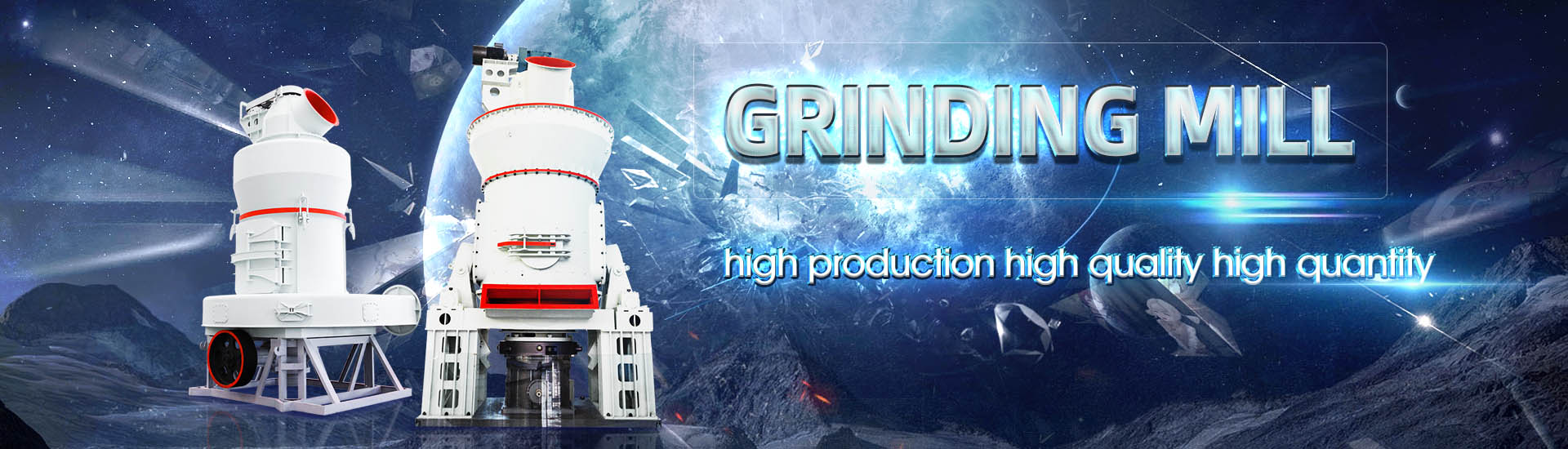
HOME→How to control moisture in cement plant coal mill How to control moisture in cement plant coal mill How to control moisture in cement plant coal mill
How to control moisture in cement plant coal mill How to control moisture in cement plant coal mill How to control moisture in cement plant coal mill
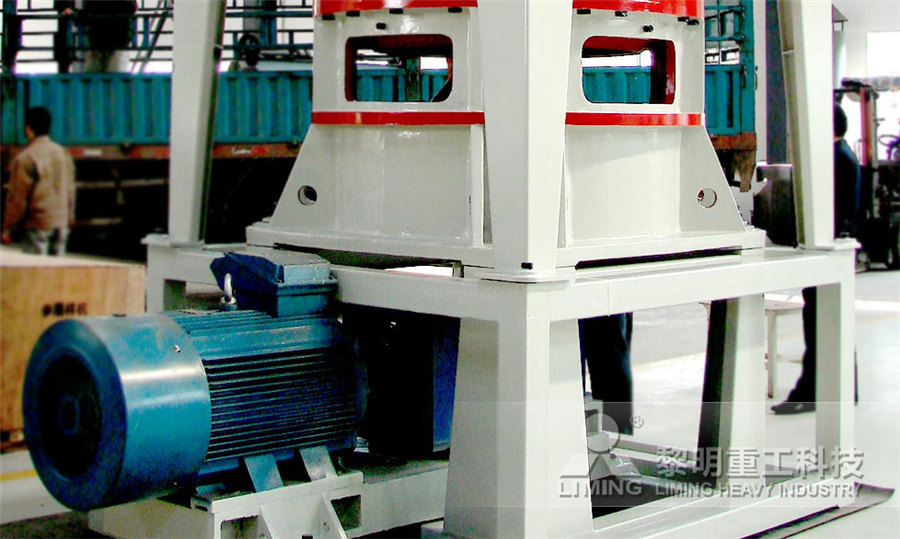
Coal Grinding Cement Plant Optimization
To achieve good combustion and satisfactory flame formation, coal needs to be dried and ground to a proper degree of dryness and fineness Drying of moisture in coal is achieved normally by ducting part of the kiln exhaust gas through the mill with inlet temperatures of up to 300°C2022年5月14日 This video is for learning about the cement production process, especially about the clinker production process in the kiln system We made this video using the Simulex simulator program made byKiln and Coal Mill Operation In Cement Plant English Adjusting operational parameters in the raw mill can help control moisture levels and enhance grinding efficiency Key adjustments include: Mill air flow: Increasing the air flow rate through the mill can enhance drying efficiency by carrying Raw Mill Moisture Content Management: A Inertization of coal mill circuit and fine coal bins with CO2, N2 or CO2+N2 to replace O2 which promotes spontaneous ignition of fine coal Vertical roller mills can typically handle an Raw Material DryingGrinding Cement Plant Optimization
.jpg)
ESTIMATION OF MOISTURE CONTENT IN COAL IN COAL MILLS
2006年1月1日 In this paper a method for estimating the moisture content of the coal is proposed based on a simple dynamic energy model of a coal mill, which pulverizes and dries the coal The temperature controller is often required to keep temperature constant at 100 °C in order to evaporate the moisture content in the coal A coal mill is a harsh environment in which it is Coal Mill an overview ScienceDirect TopicsThe key features of a coal grinding plant in a cement works are: • special layout of the plant to avoid coal dust deposits • pressure shockresistant design of mill and classifier housing, filter COAL GRINDING IMPS: more than meets the eye Gebr PfeifferIn the cement plant, the new dry process cement manufacturing requires the moisture content of coal powder to be 05% ~ 15%, while that of raw coal is 15% ~ 40% Therefore, the ball mill Coal Mill in Cement Plant Vertical Roller Mill AirSwept Ball Mill

The Cement Plant Operations Handbook International Cement
Materials such as granulated blastfurnace slag (GBS) with a high moisture content may require drying, preferably using waste heat High freelime clinker must be blended into mill feed with 2023年1月1日 Moisture content—The mill system is a complex one in which one of the key tasks is drying the moisture from the coal Higher moisture coals can lead to a reduction in mill Coal utilization in the cement and concrete industries2021年1月1日 Coal Grinding: Grinding Mill Vertical Roller Mill or Ball Mill: Coal is ground in Coal mill, which is a fuel for use in Kiln firing: 5: Pyro Section, Clikerization: In line calciner six stage preheater Kiln: Cement clinker is made by pyro processing of kiln feed into the preheaterkiln system: 6: Clinker Cooling: Cooler with roller crusherReview on vertical roller mill in cement industry its 2021年8月28日 This paper is a case study of a Portland cement plant in Romania, the experimental determinations presented mainly focusing on dust emissions in an important sector of the plant (cement mill and related facilities), with dust extraction from two chimneys in working areas (cement mill filtration system and grinder component separator filtration system), as well Dust Emission Monitoring in Cement Plant Mills: A Case Study in
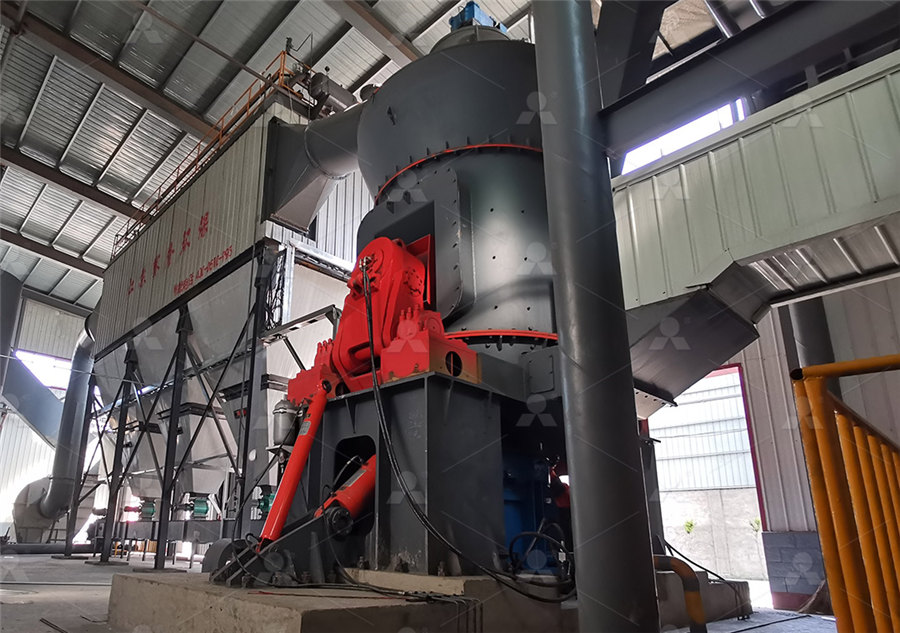
Vertical Roller Mill Operation in Cement Plant
The vertical roller mill (VRM) is a type of grinding machine for raw material processing and cement grinding in the cement manufacturing processIn recent years, the VRM cement mill has been equipped in more and more cement to control the process variable available in VRM are discussed Keywords: vertical roller mill, model predictive control, proportional integral and derivative control, artificial neural networks, fuzzy logic 1 INTRODUCTION The VRM is a type of grinding mill integrated with multi functions such as grinding, drying and separation, used for PROCESS CONTROL FOR CEMENT GRINDING IN VERTICAL ROLLER MILL Inertization of coal mill circuit and fine coal bins with CO2, N2 or CO2+N2 to replace O2 which promotes spontaneous ignition of fine coal Vertical roller mills can typically handle an aggregate moisture of up to 20% in raw materials and consumes about 30% less power in grindingRaw Material DryingGrinding Cement Plant Optimization2024年2月23日 The operation of the cement raw mill is a critical step in cement production By grinding the raw materials into a fine powder, these powders can be more easily mixed with other cement ingredients and burn more evenly during the cement clinker process Therefore, the efficient operation of the cement raw mill directly impacts the production efficiency and quality How Does a Raw Mill Work in a Cement Industry
.jpg)
(PDF) Effect of moisture in coal on station heat rate and fuel cost
PDF On Dec 1, 2015, M Siddhartha Bhatt published Effect of moisture in coal on station heat rate and fuel cost of Indian thermal power plants Find, read and cite all the research you need on Coal grinding mills LOESCHE coal grinding mills are distinguished by characteristics that improve efficiency, safety and environmental protection, from the standard version to topoftherange installations Special versions are available with characteristics that meet special safety regulation or output control requirementsCoal Mills for Cement Plants Loesche2013年1月1日 As of 2009, world cement output was estimated at 304 billion tonnes (metric tons) 6 China represents 561% of the world’s output while the USA represents 20% 7 Fuel used by the US cement industry is 60% coal, 13% petroleum coke, and 3%, natural gas 8 According to the US Energy Information Administration (EIA), the manufacture of cement Coal utilisation in the cement and concrete industriesFor a cement mill: intermediate or outlet diaphragm For the case of; cement mills with a drying chamber see raw mills Mill working conditions: ventilation air speed through the mill Bigger or smaller than 12 [m/s] Material abrasivity The [%] of slag or pouzzolana content on the fresh mill feed for cement grindingEverything you need to know about clinker/cement Grinding
.jpg)
Cement Conveyor Belt Conveyor In Cement Plant
Cement conveyor refers to a belt conveyor in cement plant, which is necessary accessory equipment in the cement production line A belt conveyor is a kind of material handling equipment with strong adaptability, applied for conveying AGICO Cement Vertical Mill AGICO Cement Ball Mill Cement Vertical Mill Grinding System Cement vertical mill, also called roller mill, is another raw mill commonly used in cement pared with the cement ball mill, it has a Raw Mill – Raw Mill In Cement Plant AGICO Cement 2016年3月1日 Next, in November 2014, Titan Cement ordered a Gebr Pfeiffer SE type MPS 2800 BK vertical roller mill for coal grinding, to be set up at line 1 at its Beni Suef plant In January 2015, Suez Cement, Italcementi’s Egyptian arm, said that it would spend US$84m during the year to convert its Helwan and Tourah 2 cement plants to use coalCoal for cement: Present and future trends2024年3月16日 A vertical coal mill is a type of industrial milling equipment used to crush and grind coal into powder for use in thermal power plants and the cement industry, 85tph Cement Ball Mill In Indian Cement Plant; Ore Dressing Line; How Does a Vertical Coal Mill Work Coal Grinding Mill In Cement Plant
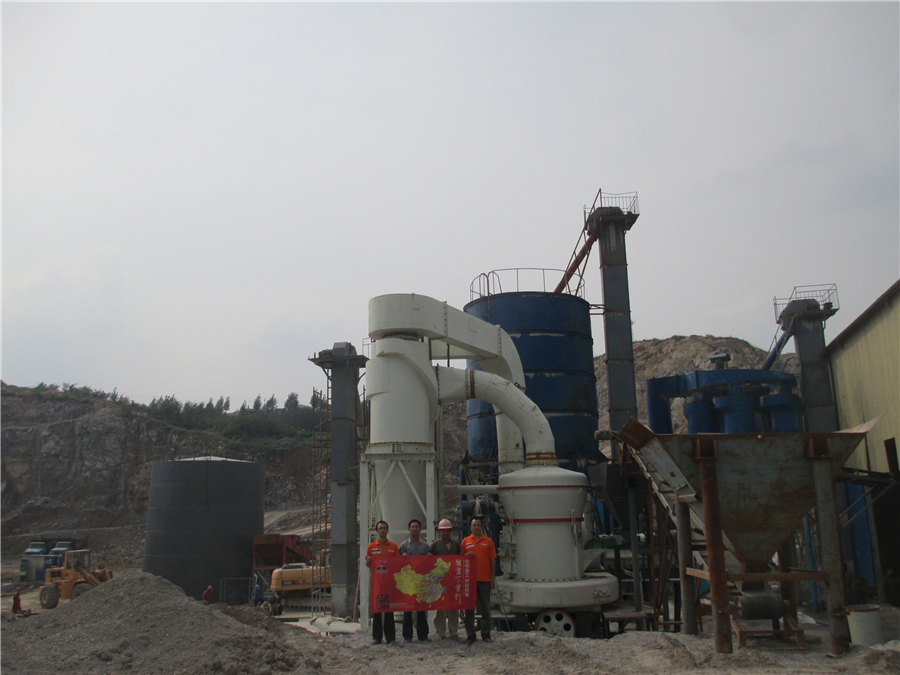
How To Optimize The Operation Of The Cement Mill
2024年1月23日 Air Swept Coal Mill ; Batch Ball Mill ; Cement Ball Mills ; Cement Raw Mill; Ceramic Ball Mill; Coal Ball Mill ; 85tph Cement Ball Mill In Indian Cement Plant; Ore Dressing Line; Proper control of the mill speed is critical for achieving the desired fineness of the cementThe vertical cement mill is largescale cement grinding machine With advantages of energyefficient and stable quality, vertical roller mill is widely applied to many industries, such as cement, power, metallurgy, chemical and nonmetallic mining industry and etc As a typical type of Cement Mill, vertical cement mill set crushing, drying, grinding, grading transportation in one, it grind Vertical Cement MillDust is the main pollutant from the cement industry Many links in the cement production process, such as raw material crushing, raw meal grinding, clinker calcination, cement grinding, etc, have different degrees of dust spilloverAmong them, the clinker calcination stage has the most serious dust emission degree, accounting for more than 70% of the total dust emission of the cement Cement Dust Collectors Selection Dust Control System in Cement PlantWith the increase of cement mill specifications and the requirement of energy saving, high yield, and high quality of cement grinding plant, the closedcircuit grinding is an inevitable trend of cement grinding unitThe essential equipment of a closedcircuit grinding system is a cement classifier, also known as a cement separatorThe function of the cement classifier is to select How To Measure Your Cement Mill And Cement Classifier? AGICO CEMENT
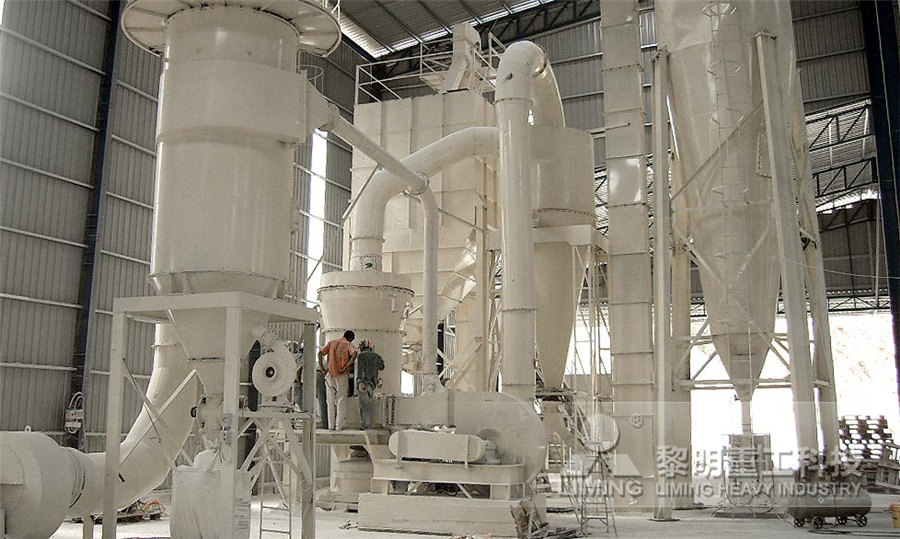
Cement mill Wikipedia
A cement mill (or finish mill in North American usage [1]) is the equipment used to grind the hard, nodular clinker from the cement kiln into the fine grey powder that is cement Most cement is currently ground in ball mills and also vertical roller mills which are more effective than ball millsused to calculate the particle size distributions and flowrates of each stream Statistical adjustment of the raw data was made by reconciliation procedurePerformance Evaluation of Vertical Roller Mill in Cement Ball mill liners are essential components in the operation of a ball mill They play a critical role in the following ways: Protecting the Mill: Ball mill liners protect the mill from wear and tear, reducing the need for repairs and prolonging the lifespan Ball Mill Liner: What is it and How it Works AGICO 2020年8月12日 This study shows the performance of a currently running vertical roller coal mill (VRM) in an existing coalfired power plant In a power plant, the coal mill is the critical equipment, whose An investigation of performance characteristics and
.jpg)
COAL GRINDING IMPS: more than meets the eye Gebr Pfeiffer
The MPS coal grinding mill with a high drying capacity is very suitable for grinding lignites with feed moistures of as much as 45 per cent Depending on this high feed moisture, the mill rating is determined by drying whereas for anthracite, hard coal and petcoke the rating of the mill is determined by grinding The great2023年5月25日 Home » News » How to Choose the Right Ball Mill Trunnion for Your Cement Mill, Autogenous Mill, or Coal Mill How to Choose the Right Ball Mill Trunnion for Your Quality control measures and certifications are indicators of a supplier’s commitment to 85tph Cement Ball Mill Put Into Operation In Indian Cement Plant Read MoreHow to Choose Ball Mill Trunnion for Cement Mill, Autogenous Mill, Coal As a trusted cement plant manufacturer of China, AGICO Cement can provide highquality cement mill and other kinds of cement equipment at competitive prices Wide product range: For meeting various requirements from different clients, our cement mill range from cement ball mill, vertical cement mill, Raymond mill, coal mill in cement plant, etcCement Mill Cement Ball Mill Vertical Cement Mill Factory 2012年6月1日 • when signals and actuators fail, control as much of the plant as possible Mill – Cement and Concrete Research, V ol 33, 2003, 439445 16 D i n g, B C Modern Predictive ControlGrinding in Ball Mills: Modeling and Process Control
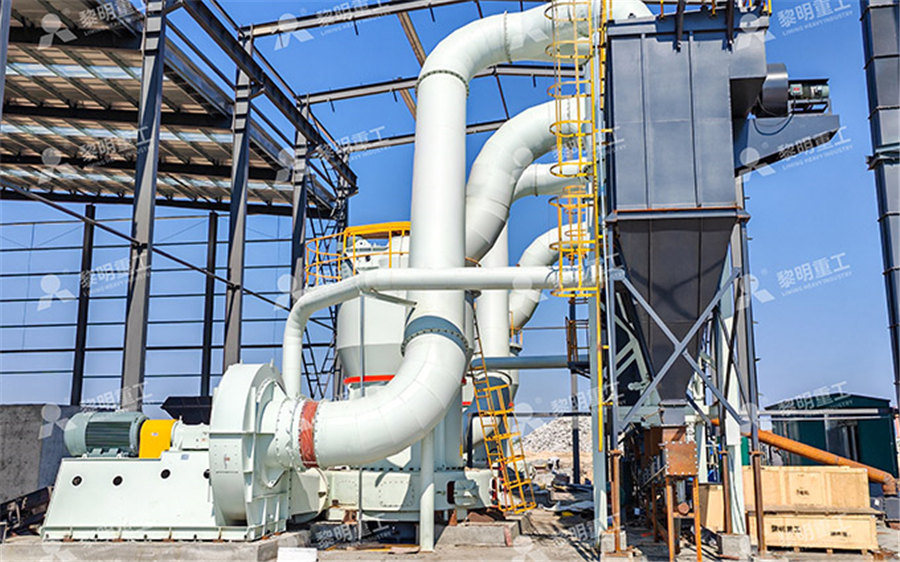
Heat Mass Balance in Cement Plant PPT Free Download
2021年11月27日 Heat Mass Balance in Cement Plant NOx emission control is not so much effective by using low NOx Burner Indian Industry Importance of Dew point Gas temperature always greater than dew point by 20 degree C To avoid moisture inside the RABH and Coal mill bag house the gas temperature should be greater than 2021年8月28日 Distribution of dust emissions at bag filters in the cement mill section no1 (mill filterpoint A and separator filterpoint B, Figure 1) of the analyzed cement plant(PDF) Dust Emission Monitoring in Cement Plant Mills: ABag Filters AGICO Operation Effect Economic Benefit The dust removal efficiency of the blowback bag filter and pulse jet bag filter can reach more than 99%, the air leakage rate is less than 3%, and their dust emission concentration is far below the emission limit of 150 mg/ m 3 Compared with the cyclone dust collector, settling chamber, and electrostatic precipitator, the Bag Filter In Cement Plant Pulse Jet Bag Filter Cement 2016年1月20日 In the surveyed cement plant, three balances are established between input and output material in the raw mill, clinker production, and cement grinding system 248 t, 469 t, and 341 t of materials are required to produce a ton of the product in raw material preparation, clinker production, and cement grinding stages; waste gases account for the largest proportion of the Analysis of material flow and consumption in cement
.jpg)
EnergyEfficient Technologies in Cement Grinding
2016年10月5日 1 Introduction Cement is an energyintensive industry in which the grinding circuits use more than 60 % of the total electrical energy consumed and account for most of the manufacturing cost []The requirements for the 2017年9月11日 In this study, an extensive sampling study was carried out at vertical roller mill of ESCH Cement Plant in Luxemburg Samples were collected from mill inside and around the circuit to evaluate the (PDF) Performance Evaluation of Vertical Roller Mill Of course, even if we set a more appropriate cement fineness, it is difficult to change the current situation that the flow velocity in the opencircuit ball mill is only 1/21/3 of that in the closedcircuit ball mill with the same specification, Ball Mill In Cement Plant Cement Ball Mill AGICO Raw mill is generally called cement raw mill, raw mill in cement plant, it refers to a common type of cement equipment in the cement plantIn the cement manufacturing process, raw mill in cement plant grind cement raw materials into the raw mix, and the raw mix is sent to the cement kiln to make cement clinker, next, clinker and other admixtures will be ground into finished cement by Raw mill Cement Plant
.jpg)
BALL MILLS Ball mill optimisation Holzinger Consulting
and cement Roller presses are used mainly in combination with a ball mill for cement grinding applications and as finished product grinding units, as well as raw ingredient grinding equipment in mineral applications This paper will focus on the ball mill grinding process, its tools and optimisation possibilities (see Figure 1) The ball millVertical raw mill is one kind of raw mill, generally used to grind bulk, granular, and powder raw materials into required cement raw meal in the cement manufacturing plantVertical raw mill is an ideal grinding mill that crushing, drying, grinding, grading transfer set in one It can be widely used in cement, electric power, metallurgy, chemical industry, nonmetallic ore, and other industriesVertical raw mill Cement PlantAGICO is one of the leading cement plant and cement equipment suppliers in China We provide highquality rotary kiln, crushing mills, grinding mills, dust collector, etc We also offer cement plant design service, equipment installation and commissioning service and aftersales serviceCement Clinker Calcination in Cement Production Process AGICO Cement 3 Factors affecting ball mill performance 4 Ball mill improvements case examples 5 Conclusions question time Introduction Cement manufacture is energy intensive o Cement manufacture consumes typically 3,100 – 3,400 MJ of fuel/t clinker 90 130 kWh / t cement in a modern plant, more for older or less efficient plants;Improvements in New Existing Cement Grinding Mills by Tim
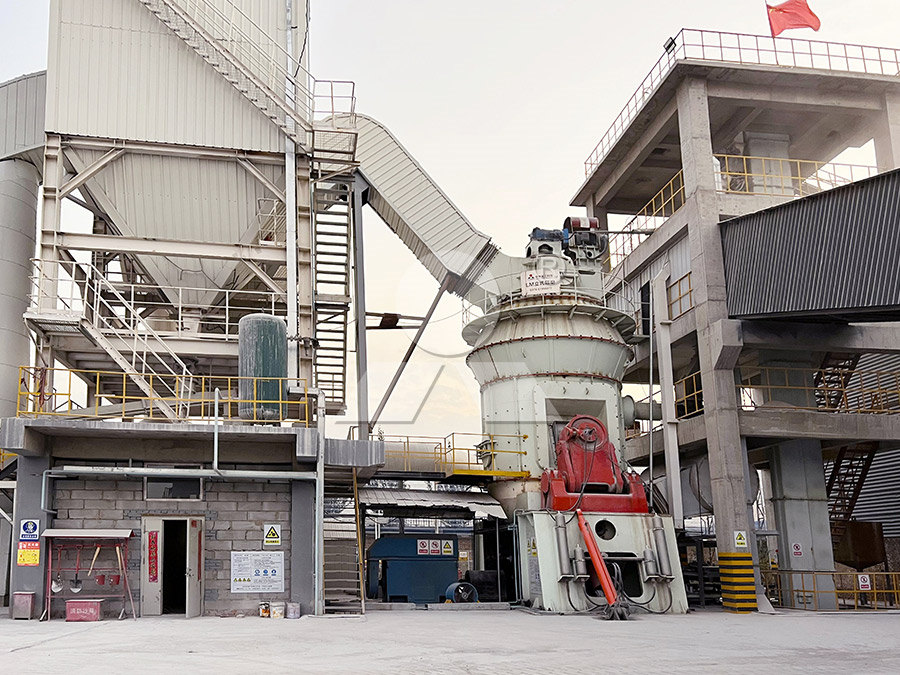
Air Pollution Control in Cement: Solutions Impact
2023年9月22日 Techflow’s Air Pollution Control Products for Cement Plants 1 Electrostatic Precipitator (ESP) for Cement Industry Electrostatic Precipitators (ESPs) are formidable weapons in the battle against air pollution ESP are used in Raw Material Crusher, Cement Mill, Coal Mill, Rotary Kiln in Cyclone Preheater Tower