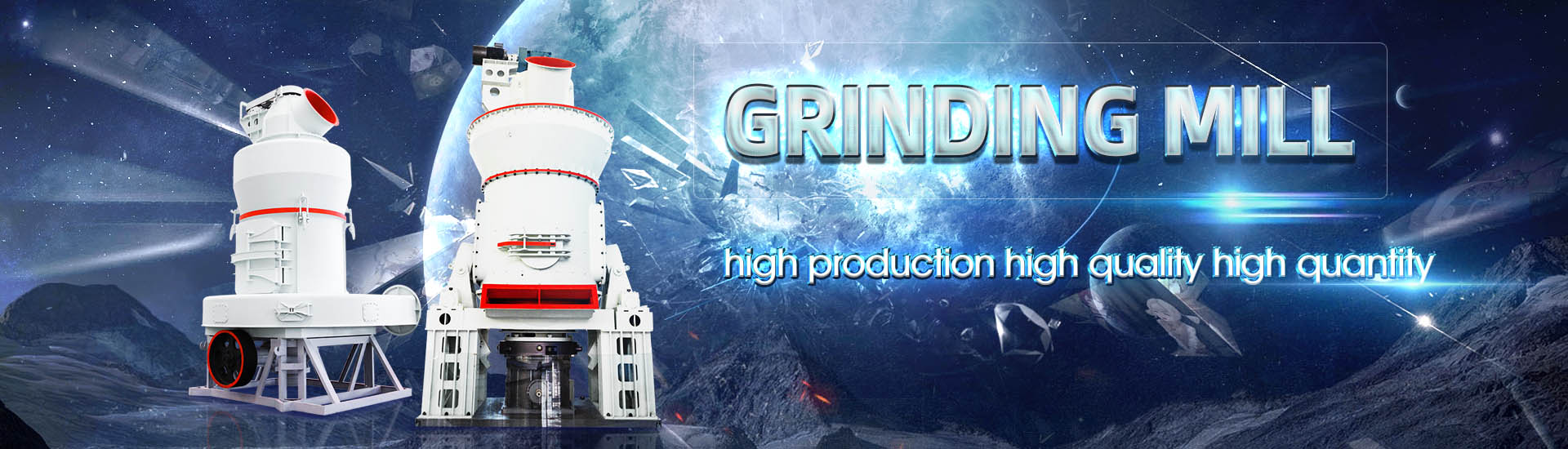
Loesche coal grinding and grinding disc friction coefficient
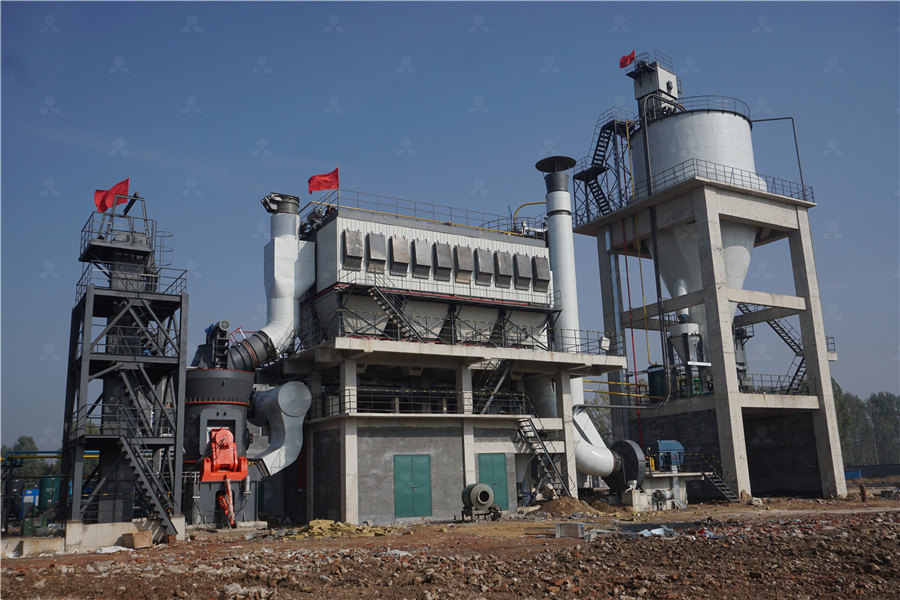
PROCESS OPTIMISATION FOR LOESCHE GRINDING PLANTS
The core elements of these plants are the Loesche vertical mills for drygrinding the abovementioned grinding stock Loesche has developed and built the largest and most efficient grinding plants for its customers Loesche plants are specifically planned for the required process steps Loesche produces grinding mills and classifiers for all solid fuels, with throughputs ranging from 8 to 240 t/h (16,000 to 640,000 lb/h) With a long wear life and easy replacement of worn parts, Loesche Grinding Technology for the Power Industry2002年10月11日 Based on the mechanics of cutting and the experimental data, has derived analytical and empirical relationships to calculate the friction coefficients of different abrasive Study on the friction coefficient in grinding ScienceDirect• Grinding pressure control for expansion of the mill control range from 20 to 100%; • Grinding table speed control with frequency converter Loesche designs, plans and constructs LOESCHEMILLS
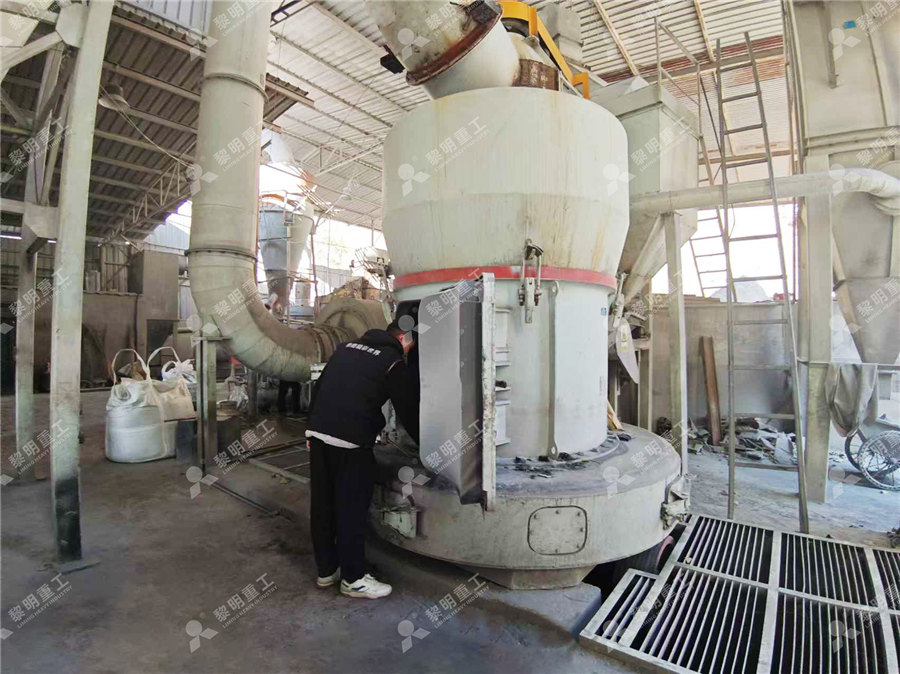
Study on the friction coefficient in grinding ScienceDirect
2002年10月11日 Specific energy, friction coefficient in grinding and Gratio were used as measurands for determining the process efficiency Results show that MQL grinding with Grinding behaviour and wear mechanism of selffabricated rail grinding stones (GS) using zirconia alumina (ZA), white fused alumina (WA) and brown fused alumina (A) were investigated in(a) The friction coefficient during the whole grinding 2012年9月1日 Mills (VRM) installations and summarises the main benefits of the dry compressive Loesche grinding technologies in Airflow and OverflowMode Some of these Latest Installations And Developments Of Loesche Vertical Roller 2016年11月22日 Focusing on the core issues of grinding process, the paper presents some fundamental research findings in relation to grinding material removal mechanisms The grinding efficiency is analysed by considering the Effect of different parameters on grinding efficiency
.jpg)
Loesche vertical roller mills for the comminution of ores and
2001年10月1日 Recent research has shown, that the application of these vertical roller mills in dry grinding of ores and minerals can lead to significantly better recovery rates and higher Loesche mills can be adjusted so that in a few minutes a different product quality is achieved The springloaded roller grinding mill for grinding coal was intro duced by Loesche in the 1920’s 2 µm 5 µm Loesche2022年11月29日 Doubleplane grinding plays an important role in the processing of highprecision flat parts A doubleside autonomous grinding (DSAG) method was proposed and investigated to improve the Modeling and simulation method of trajectory in doubleside Energies 2021, 14, 7300 3 of 15 A = f2(G, B) (2) where G is the coal grindability within the specified system, M means the mechanical properties of the coal, r is the coal porosity, q determines the hard particles mechanical and geometrical characteristics, w is the moisture, T is the temperature, h is the overall efficiency of the grinding system, A is the coal abrasiveness, of Coals in Mineral Processing Systems
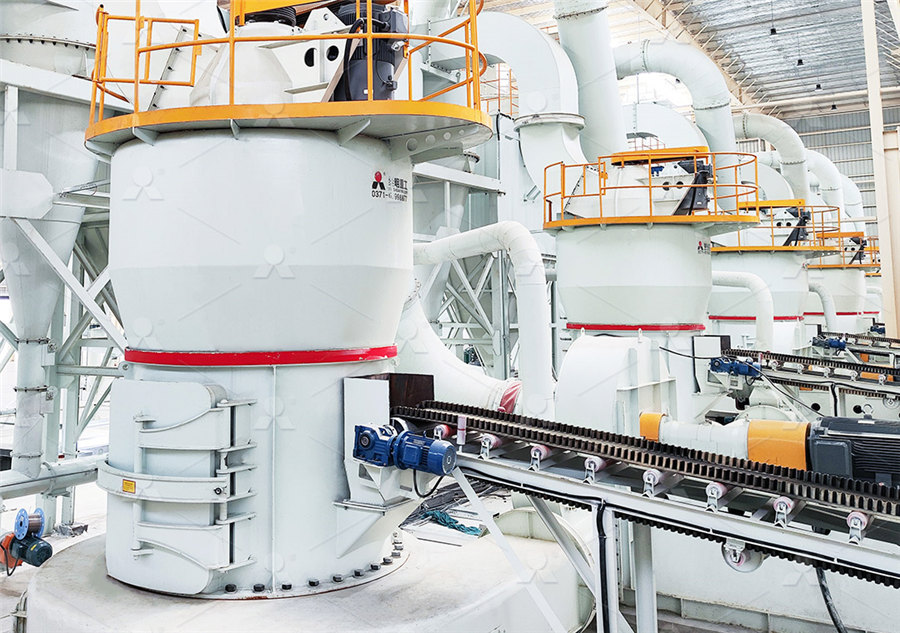
132 Loesche Mills For Solid Fuels Coal Mill E 2016
Loesche has been involved in processing solid fuels since 1925 Some key events include delivering their first coal mill in 1927 and introducing hydraulic systems in 1961 Their mills are distinguished by grinding without metal contact, suitability for combustible dust, and low vibration even at partial load Loesche designs complete grinding plants that operate efficiently and 2020年8月12日 Vertical Coal Mill (VCM) is equipment for grinding and pulverizing coal into micron size Rotary kilns then use the powders as fuel burnersAn investigation of performance characteristics and energetic LOESCHE coal grinding mills are distinguished by characteristics that improve efficiency, safety and environmental protection, from the standard version to topoftherange installations Special versions are available with characteristics that meet special safety regulation or Coal Mills for Cement Plants LoescheAs can be seen from Fig 5(b), the mean grinding force/coefficient of friction presents a negative correlation with porosity, indicating that porous grinding wheels can reduce the energy input and (a) Friction coefficients during grinding and (b) mean value of
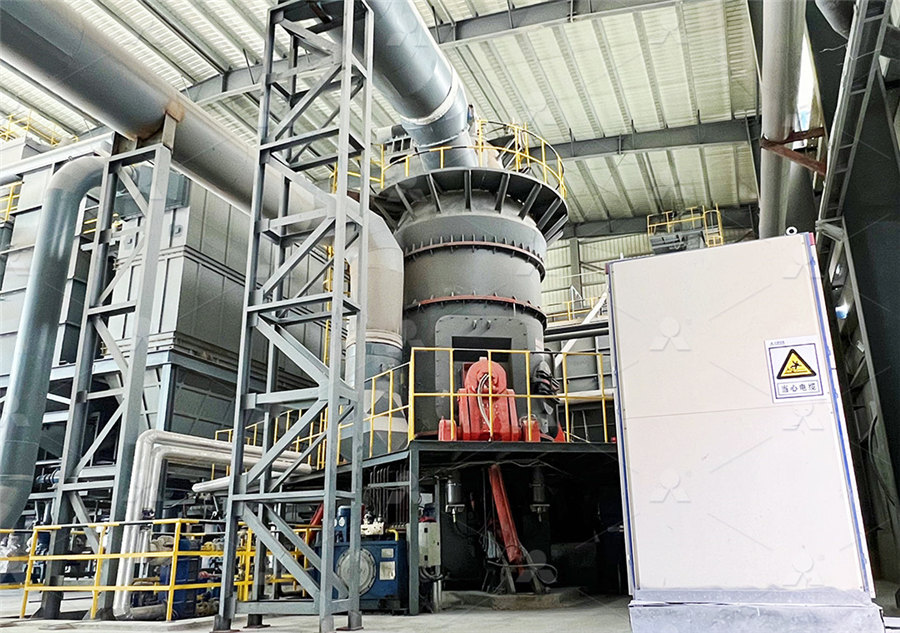
Friction Coefficient of NanoCeramic Polished by Oxide Film on
2013年3月1日 The friction coefficient changes with the feeding rate The Friction Coefficient of ELID Grinding using different specimen materials Fig 3 is the friction coefficient of nanoAl2O3 and nanoZrO2Nowadays, Loesche vertical mills form the core of many plants used to drygrind coal, cement raw materials, granulated slag, industrial minerals and ores Thanks to its grinding plants with throughputs of 2 to 1000 t/h for the cement industry and selfinert, central coalgrinding plants for hard and brown coal power stations, Loesche is the global market leader for vertical mills and About Us Loesche2023年9月29日 Currently, scholars consider the grinding force modeling mainly from the material, grinding process, grinding wheel wear and other aspects Meng et al [3] established the grinding force model of a new type of microstructure grinding wheel based on the topography model, and found that the addition of microstructure reduced the grinding force by 496 % ~ Mechanical behavior and modeling of grinding force: A 2015年1月31日 Request PDF Performance evaluation of Ti6Al4V grinding using chip formation and coefficient of friction under the influence of nanofluids Nanofluid, fluid suspensions of nanometer sized Performance evaluation of Ti6Al4V grinding using chip formation and
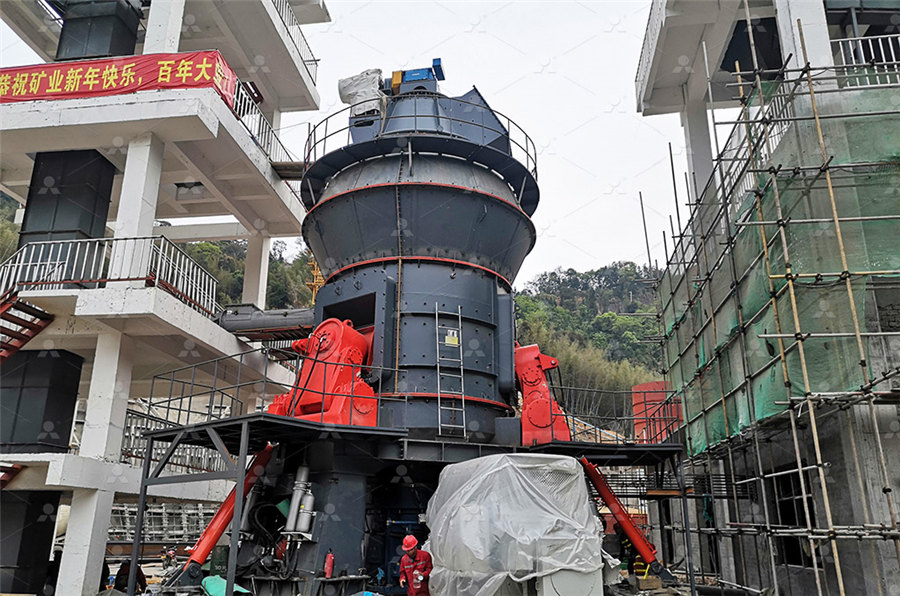
Study on the friction coefficient in grinding ResearchGate
2002年10月1日 Download Citation Study on the friction coefficient in grinding The friction between the abrasive grains and workpiece is a crutial factor determining the main grinding output Few studies Loesche India Private Limited Dry Grinding Plants, Roller Grinding Millls and More Classfiers Manufacturer from Noida, Uttar Pradesh, India IndiaMART Get Best Price Shopping The 2+2, 3+3 roller clinker / slag grinding Mills, 6 Dry Grinding Plants and Roller Grinding Millls and Loesche Coal Mill Free download as PDF File (pdf), Text File (txt) or read online for free 1) Loesche has been involved in processing solid fuels like coal since 1925 and has continued innovating coal grinding technology 2) Loesche Loesche Coal Mill PDF Mill (Grinding) Coke (Fuel)2022年12月23日 In order to study the friction and wear properties of cast iron in free grinding environment under the condition of line contact, this paper presented a new method to calculate the friction coefficient by measuring the friction torque Through the selfdeveloped free abrasive grinding experimental device in line contact condition, this work carried out friction and wear Study on friction and wear properties of cast iron material in line
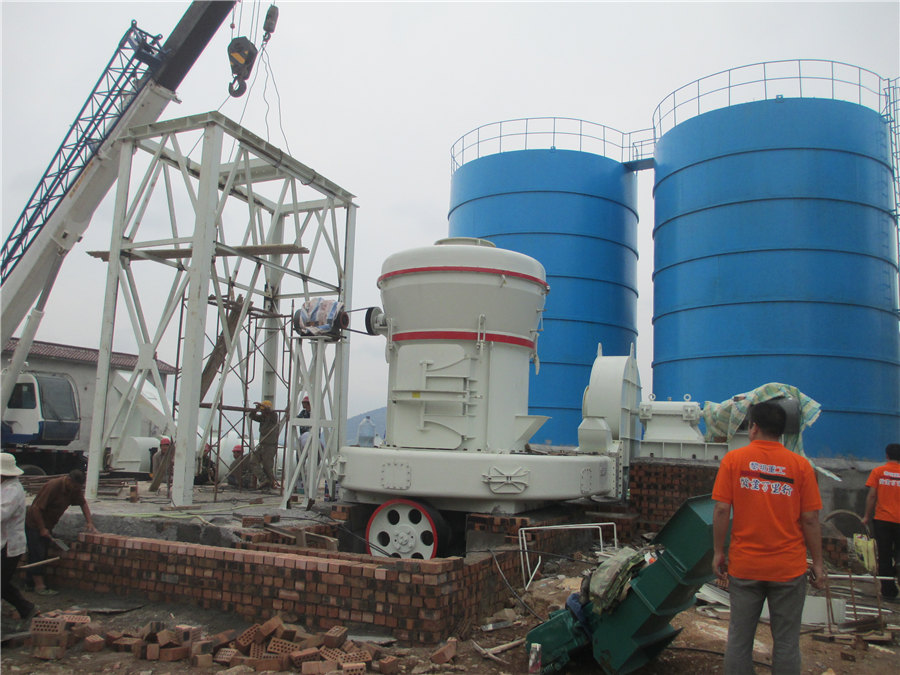
Study of specific energy and friction coefficient in minimum
2012年4月1日 Friction coefficient in grinding (μ) Friction coefficient in grinding is the ratio of tangential grinding force (F t) and normal grinding force (F n) Typical values of μ in grinding lie between 02 and 07 [8] A low value of μ corresponds to welllubricated blunt abrasive grains in contact with the workpiece surface Coefficient of the largest Loesche mill ever built has confirmed the correctness of this development direction The sixroller Loesche mill of type LM 696 has an outside grinding track diameter of 69m The constant demand for higher mill throughput has been the essential challenge for Loesche through its 100+ year history Only tworoller mills wereRAW MATERIAL GRINDING ITadipatri’s big sixer Loesche2022年8月5日 When the load is 40N100N, the friction coefficient increases sharply in the whole grinding process, then decreases gradually, and finally tends to be stable; The fluctuation of friction Study on friction and wear properties of cast iron material in line Loesche Grinding Technology for the Power Industry Created Date: 7/23/2018 11:38:07 AM Loesche Grinding Technology for the Power Industry
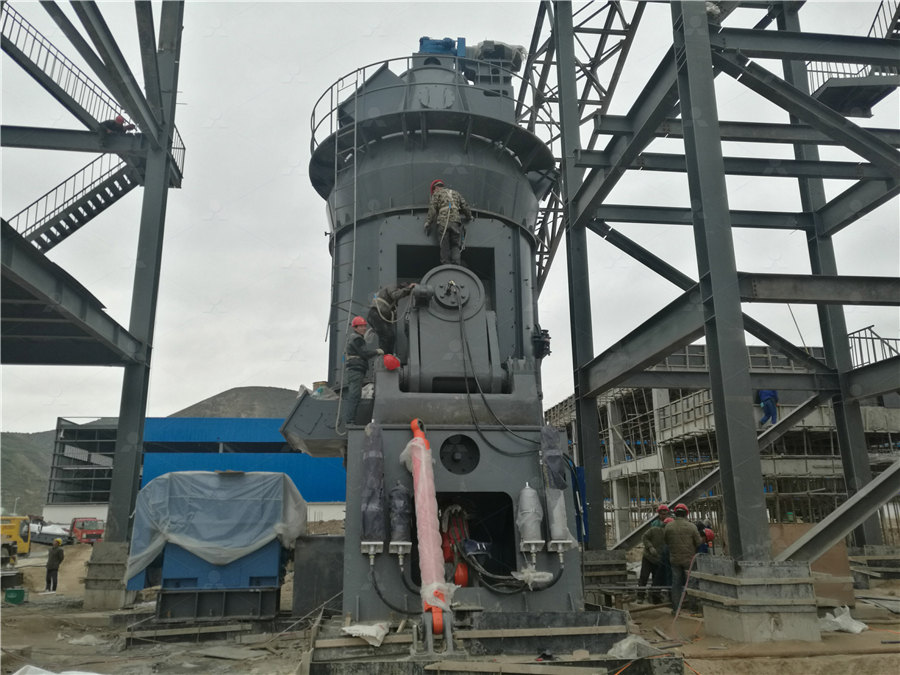
Properties of grinding tool material for doubledisc straight
2021年4月7日 The doubledisc straightgroove (DDSG) grinding method is a new precision machining approach employed for the rolling surface of bearing rollers The friction coefficient and wear resistance of grinding disc materials affect the grinding performance due to the operation on the workpiece However, relevant research on DDSG is rather limited currently Therefore, we 2021年11月4日 The operating costs of breaking coal particles into fine powder, to achieve optimum combustion for the boilers in a power plant, are made up of power input to carry on an energy intensive comminution mechanism and to overcome friction losses within pulverising machines The operating costs also include the cost of the replacement of the processing Technique to Investigate Pulverizing and Abrasive Performance of Coals 2022年10月13日 Experimental equipment: (a) Rtec MFT5000 universal tribometer; (b) diagram of the friction test equipment The grinding ball block remains stationary during the tests, while the rotating module Experimental Investigation into the Friction Loesche builds coal grinding plants for a throughput of 2 t/h to 300 t/h and is the market leader in the sector of selfinert, central coal grinding plants for hard coal and the grinding of brown coal in vertical mills Decades of experience is also the basis for manufacturing containerMobile grinding plant for solid fuels Loesche
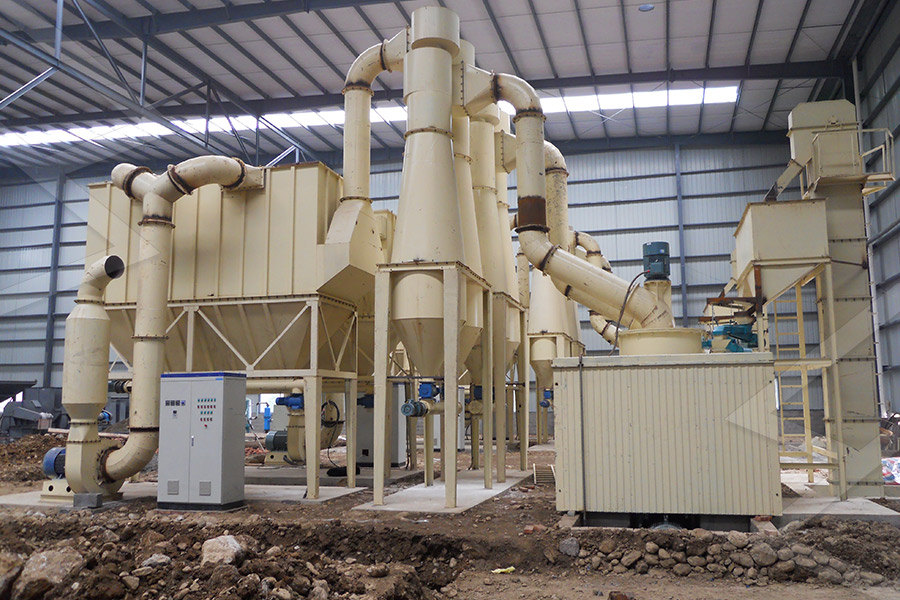
LOESCHEMILLS
1927 First Loesche coal mill delivered for the Klingenberg power station in Berlin 1953 500th coal mill plant sold worldwide 1961 Introduction of hydraulic spring assembly system 1965 Construction of first pressure mill (LM 122 D) 1980 Delivery of first modular coal mill (LM 263 D) 1985 Delivery of first selfinerting coal grinding plant (LM 212 D) for the steel industry (PCI 2014年10月24日 As a technological pioneer LOESCHE is following on from the success of the largest coal mill LM 434 in India and the world's largest raw meal mill LM 696 in Nigeria This latest triumph involves Loesche hands over world’s largest slag mill – LM 633+32023年11月27日 The LOESCHE cement grinding plant for the customer CYCNA, part of the La Cruz Azul group, was successfully commissioned in Tepezalá, Mexico In the summer of 2019, the installation will commence of two more LOESCHE coal grinding plants for petroleum coke grinding in Lagunas and HidalgoPress LoeschematerialStudy on friction and wear properties of cast iron material in line
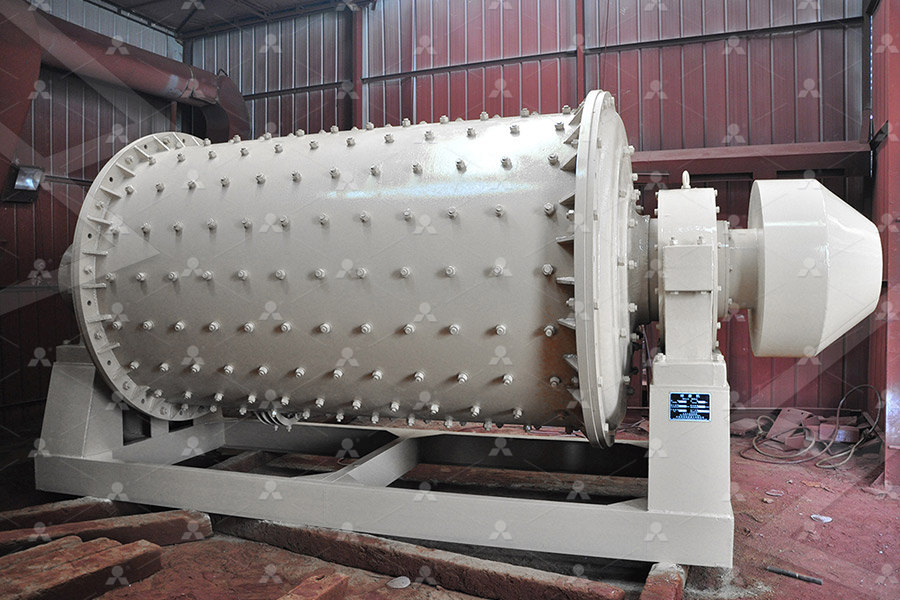
(a) The friction coefficient during the whole grinding process; (b)
Download scientific diagram (a) The friction coefficient during the whole grinding process; (b) the realtime temperature distribution at the contacting zone between rail disc and GS at energies Article Technique to Investigate Pulverizing and Abrasive Performance of Coals in Mineral Processing Systems Wojciech Grzegorzek 1,*, Daniel Adamecki 1, Grzegorz Głuszek 1, Aleksander of Coals in Mineral Processing Systems ResearchGateIn 1990, Loesche GmbH supplied the first coal grinding plant for an IGCC power plant in Buggenum, the Netherlands, with three LM 263 D 4roller Loesche Mill in modular design with LSKS classifier LOE09092OGPrintWorldCoaldd 5Abs1:1 17062009 16:21:10 UhrOFTEN LoescheSuccessful inauguration of the New Steel Pilot Plant with a LOESCHE Ore Grinding Plant (OGPmobile) in Ouro Preto, MG, Brazil Ouro Preto – The company New Steel has developed a revolutionary new process for iron ore concentration for which New Steel has been awarded with the internationally highly esteemed Platts Global Metals Award for Innovation 2015Mills for minerals and ores Loesche
.jpg)
Prediction of Grinding Force by an Electroplated Grinding Wheel
2023年10月12日 The ability to predict a grinding force is important to control, monitor, and optimize the grinding process Few theoretical models were developed to predict grinding forces when a structured wheel was used in a grinding process This paper aimed to establish a singlegrit cutting force model to predict the ploughing, friction and cutting forces in a grinding Energies 2021, 14, 7300 3 of 15 A = f2(G, B) (2) where G is the coal grindability within the specified system, M means the mechanical properties of the coal, r is the coal porosity, q determines the hard particles mechanical and geometrical characteristics, w is the moisture, T is the temperature, h is the overall efficiency of the grinding system, A is the coal abrasiveness, of Coals in Mineral Processing SystemsLoesche – Innovative Engineering For over 100 years the company Loesche has been building vertical roller grinding mills for grinding: • Coal • Cement raw material • Clinker / granulated slag • Industrial minerals, and • Ores The core elements of these plants are the Loesche vertical mills for drygrinding the abovementioned PROCESS OPTIMISATION FOR LOESCHE GRINDING PLANTSDOI: 101016/JJMAPRO201201001 Corpus ID: ; Study of specific energy and friction coefficient in minimum quantity lubrication grinding using oilbased nanolubricantsStudy of specific energy and friction coefficient in minimum
.jpg)
Analysis of grinding mechanics and improved grinding force
2023年7月1日 The establishment and numerical analysis of grinding force prediction models have consistently been a research hotspot Modeling methods are mainly divided into two categories: empirical and theoretical modeling 5 At the early stage, due to randomized grain characteristics on the grinding wheel surface, theoretical research on grinding force has Düsseldorf Clariant Germany approached LOESCHE GmbH, Düsseldorf with an exceptional request it needed a vertical roller mill for grinding bentonite for its facility in Balikesir/Turkey All components of the grinding system must be mobile since a LOESCHE delivers first mobile grinding plantLoesche mills can be adjusted so that in a few minutes a different product quality is achieved The springloaded roller grinding mill for grinding coal was intro duced by Loesche in the 1920’s Since the end of the 1930’s Loesche mills have also been used for grinding cement raw material The biggest breakthrough in this field of application2 µm 5 µm Loesche2019年6月1日 Five rotational speeds of grinding disc, ie, 1600, 1900, 2200, 2500, and 2800 rpm and five feed rates of 03, thus obtaining minimum specific grinding energy and friction coefficient Effect of friction coefficient on chip thickness models in ductile
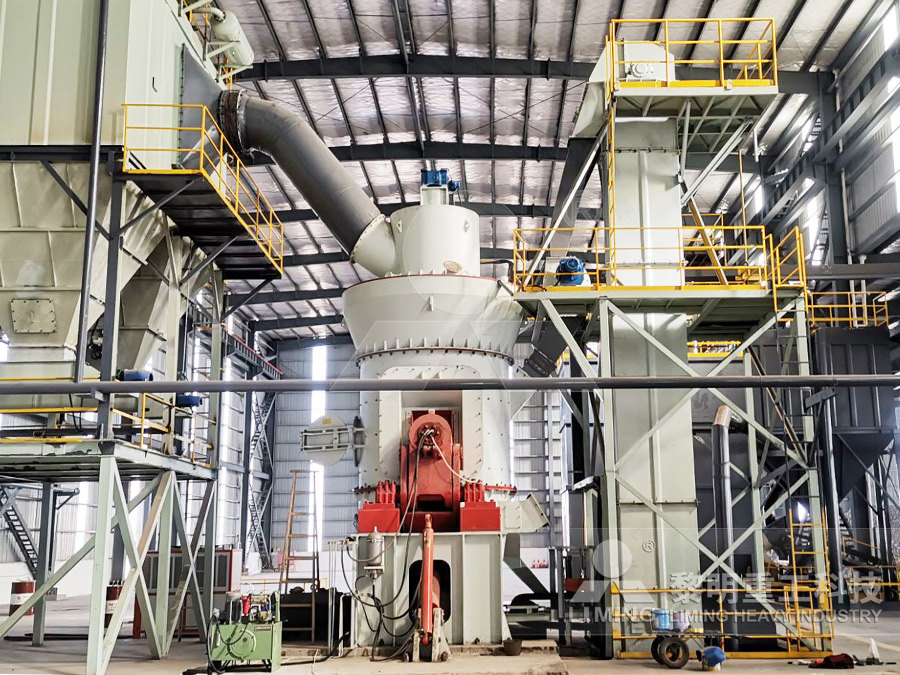
Coal Loesche
This is the second order of a LOESCHE coal mill used in this group Read more With Three Grinding Plants with Proven Vertical Roller Mill Tec By admin on Oct 1st, 2018 Raw Mill LOESCHE Delivers Two Large Grinding Plants to Mexico By admin on May 18th, 2018 Cement Raw Mill Coal 02018年5月31日 We investigated the effect of the friction coefficients of a barrel on the grinding performance of multilayer ceramic capacitors (MLCCs) in a planetary ball mill We formulated the motion equation of the MLCCs, including gravitational force, interactive force due to collisions and the drag force in a planetary ball mill, using the threedimensional discrete element method Effects of the friction coefficient of a barrel on the grinding