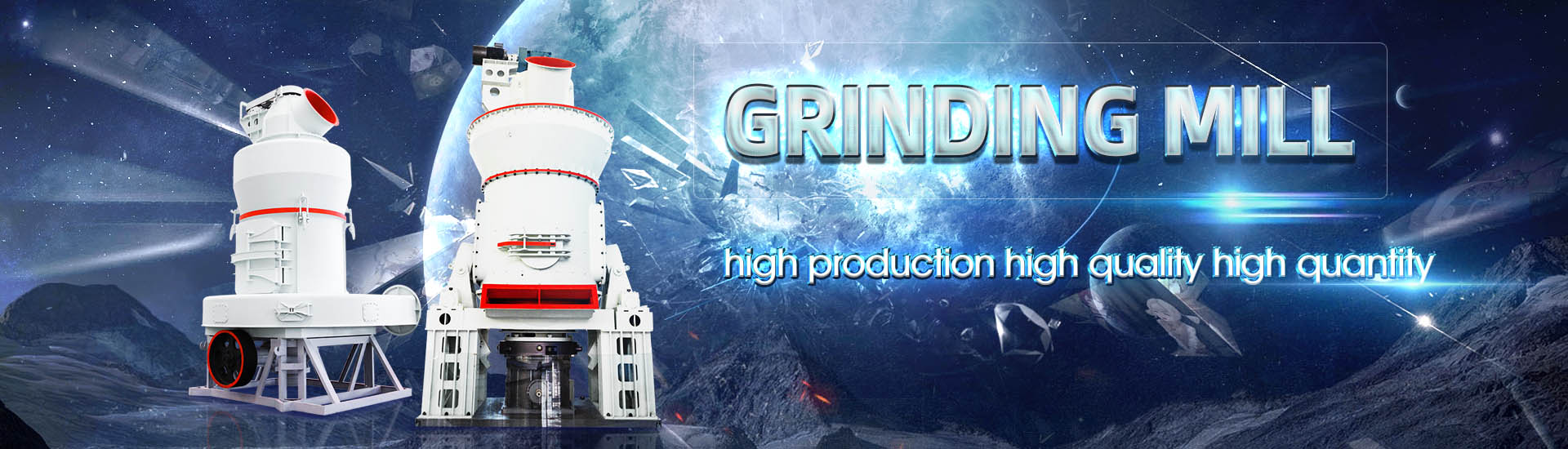
The working principle of nickel concentrate grinding equipment
.jpg)
The Comprehensive Guide to Nickel Processing
2024年1月19日 Nickel ore preparation involves a series of processes to prepare the ore for further processing, including crushing, grinding, and classification These steps help to reduce the ore size, increase the surface area for 2015年8月1日 By far the most common preconcentration process used ahead of commercial hydrometallurgical processing of Ni laterites is the removal of a coarse fraction from the feed Preconcentration strategies in the processing of nickel laterite ores Nickel Refining Various processes are used to refine nickel matte Fluid bed roasting and chlorinehydrogen reduction produce highgrade nickel oxides (more than 95% nickel) Vapor Nickel Smelting and Refining International Finance Corporation2024年10月24日 The nickel concentrate obtained after flotation usually contains a large amount of water, which needs to be reduced by thickening and filtration Commonly used equipment The Guide to Nickel Processing Methods Mining Pedia
.jpg)
Principles of Modern Grinding Technology
2013年1月1日 Principles of Modern Grinding Technology explains the principles that led to rapid improvements in modern grinding technology over recent decades Removal rates and quality2024年1月1日 Fine grinding improves the grade of the copper concentrate and the recovery of nickel to the nickel concentrate by increasing mineral liberation The nickelcobalt rich Nickel and Cobalt ScienceDirect2024年1月1日 Using nickel concentrate or nickelcopper bulk concentrate as raw materials produces intermediateproduct highgrade nickel matte Three process methods are mainly Nickel Metallurgy SpringerLinkMACHINING AND GRINDING NIRESIST AND DUCTILE NIRESIST A PRACTICAL GUIDE TO THE USE OF NICKELCONTAINING ALLOYS NO 242 Originally, this handbook was MACHINING AND GRINDING NIRESIST AND DUCTILE NIRESIST
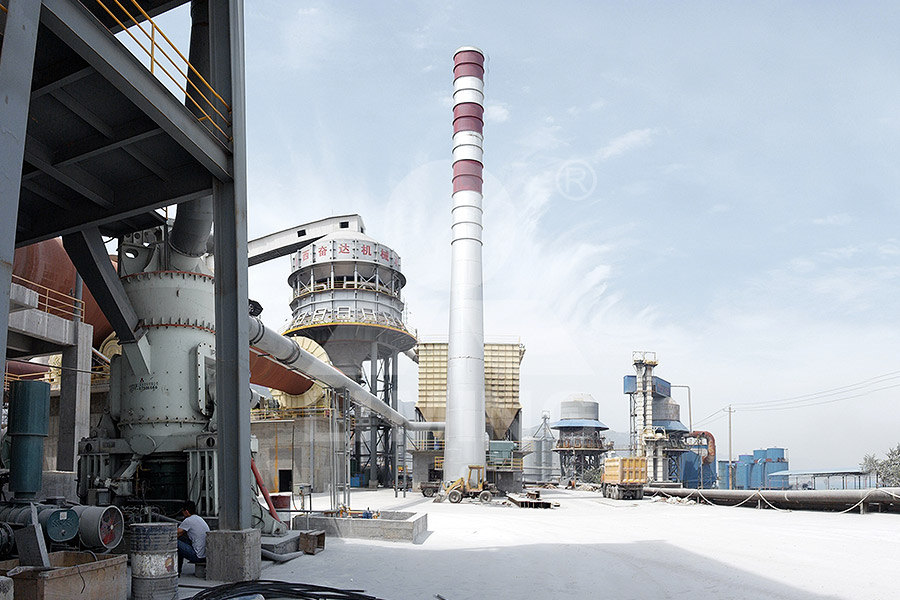
(PDF) A comprehensive review on the grinding process:
2022年6月24日 Grinding is a manufacturing process which significantly contributes in producing high precision and durable components required in numerous applications such as aerospace, nickel powder can also be produced in autoclaves by using hydrogen reduction technology The new Metso Outotec anodeinabag technology for nickel electrowinning offers an Hydrometallurgical nickel and cobalt plants and processes2019年10月17日 1 Working principle 2 Structure Let's dive right in! 1 Working Principle of Rod Mill Rod mill is a common equipment for grinding operation in mineral concentrator, which is mainly suitable for rough grinding operationThe Working Principle and Structure of Rod Mill2016年6月1日 For evaporating moisture from concentrates or other products from plant operations, Rotary Dryers are designed and constructed for high efficiency and economy in fuel consumption Whenever possible to apply heat Rotary Dryer Design Working Principle
]@S0{UDKK%G24F3JGHC.jpg)
A Comprehensive Guide to Lithium Processing
When secondary grinding is required, a wet overflow ball mill can be selected as the grinding equipment for this stage Classification equipment can adopt graded hydrocyclone group According to the ore properties of different lithium ores, 2022年5月16日 The process has not been industrially applied to the processing of nickel sulfide concentrates and information on processing of nickel sulfide concentrates is limited; the original patent by Hourn, Turner, and Holzberger (Citation 1996) only had one application of the Albion Process TM to the processing of a lowgrade nickel concentrate (17% Ni as pentlandite) The Direct Leaching of Nickel Sulfide Flotation Concentrates – A The principle of grinding precision machining: Grinding is an abrasive precision machining method that uses a lapping tool and abrasive to grind off a thin layer of metal from the surface of the workpiece based on fine machining Define grinding: Grinding is a unit operation that reduces solid matter into smaller particles Define grinding process:The Working Principle and Types of Grinding Revealed1988年9月1日 While the vast majority of the world’s nickel is produced using pyrometallurgical techniques, the equipment and processes employed in such production encompass a variety of technologiesA Review of Nickel Pyrometallurgical Operation ResearchGate
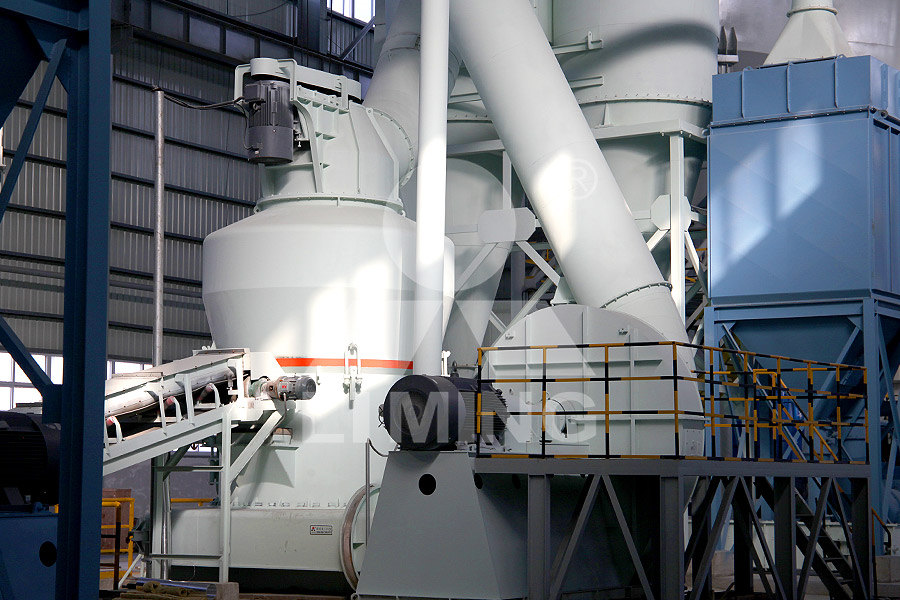
Thickeners — Types, Working Principle Applications
2018年8月8日 Working of a Thickener Let us understand in detail about how thickeners work To start with, it works on the principle of Gravity sedimentation and the most common construction of a thickener 2020年7月6日 The ASARCO (American Smelting and Refining Company) smelter in El Paso, Texas accepts Cu concentrates with a maximum As content of 02% [61] Meanwhile, the Lepanto roaster of the Lepanto (PDF) Processing of Complex Materials in the Copper Industry 2020年5月5日 Nickel is an important strategic metal produced at over 2 million tonnes annually [1]Approximately 60% of all Ni is consumed in the production of stainless steel [2, 3]Currently, Ni is primarily extracted from two types of ores: laterites and sulfides [[4], [5], [6], [7]]Although sulfide ores account for a smaller fraction of global Ni reserves, approximately 60% of global Ni Solid State Extraction of Nickel from Nickel Sulfide Concentrates2017年10月3日 Share with Facebook; Share with Twitter; Share with Google+; Share with LinkedIn; Posted: October 3, 2017 Grinding Mills Types, Working Principle Applications The purpose of this article is to explain the usage of grinding mills in a mineral processing operation and to enable buyers to understand the best suitable grinding mill as per their specific needsGrinding Mill Types, Working Principle Applications Savona Equipment
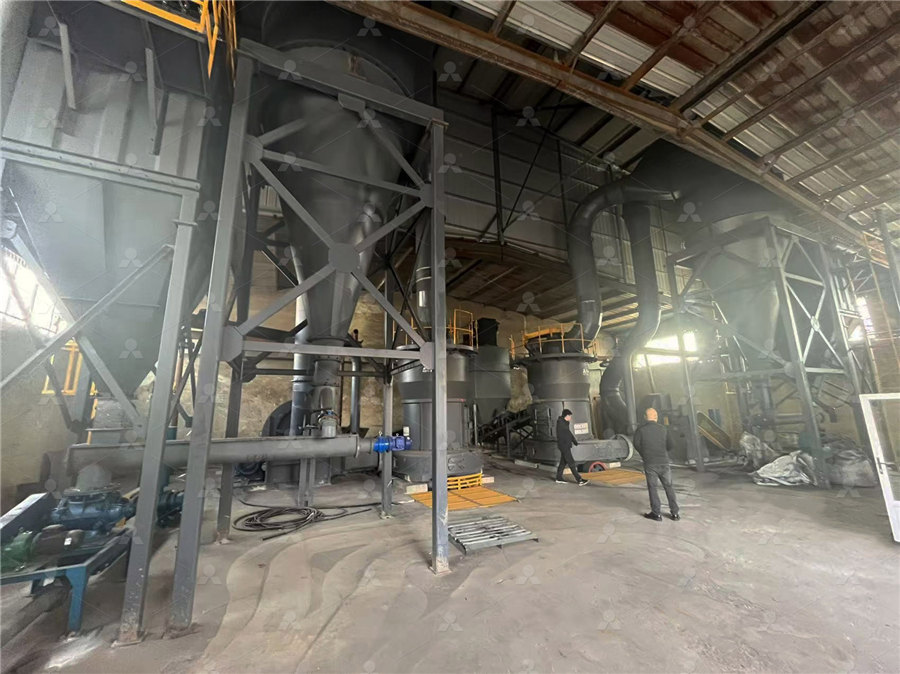
Comminution a Heart of Mineral Processing
2021年7月6日 then grinding with the different major equipment The massive particles are then passed through rigid surfaces (jaws, rollers, etc), where pebbles get hammered, compressed, and squeezed,2023年4月25日 A basic principle in determining the flotation process of coppernickel ore is to prefer copper into nickel concentrates rather than nickel into copper Grinding equipment The semiautogenous grinding ball mill can not 2 Types of Nickel Ore: Processing Methods and associated with working with nickel, nickel compounds and alloys The fourth edition is divided into two modules; Module 1, on the Toxicology and Hazard Classification of Nickel Substances, was updated in 2021 and Module 2, on the Exposure of Workers to Nickel Substances and Health Assessment, is to be updated in 2022 These two modulesnickel workplace Module toxicology hazard classifi cation2024年6月6日 These protruding abrasive particles also remove the unactive layers formed on the work by abrasion to make the surface more receptive It can be seen that the process is similar to conventional grindingIn that, an abrasive grinding wheel is used and the work is fed against the rotating wheel 10% of the work metal is removed by abrasive cutting, and 90% by Electrochemical Grinding: Parts, Working, Application, Advantages
.jpg)
Grinding Machines: Types and Selection Principles Miningpedia
2020年9月22日 Grinding machine has been widely used in gold mines in South Africa since 1905 At that time, the grinding machine used river pebble as the grinding medium, which was essentially a gravel mill Later, in order to improve the production capacity of the mill, cast iron balls were used as the medium, so normal gravel mills were evolved into ball mills and rod mills2019年1月5日 Compared with other conventional machining methods, grinding can satisfy the particular working conditions of nickelbased singlecrystal superalloy because of its good machining quality and high Review on Grinding Technology of Nickelbased ResearchGate2024年2月24日 Grinding is a type of abrasive machining process which uses a grinding wheel or abrasive belt as a cutting tool Grinding is basically a finishing process used for producing close dimensional accuracies and desired smooth surface finishIt is commonly used to remove the material from a workpiece, to produce a smooth finish on the surface of the workpieceWhat is Grinding? Definition, Working Principle, Types, 2023年2月15日 The raw nickel ore is always companied by clay and impurities The washing ore process can remove clay and impurities before crushing and beneficiation operations, which improves operating efficiency and helps to obtain highgrade nickel concentrate The ore washing equipment used in laterite ore mainly is a coarse and fine material screw washerThe Best Mining Equipment for Philippines Nickel Ore You
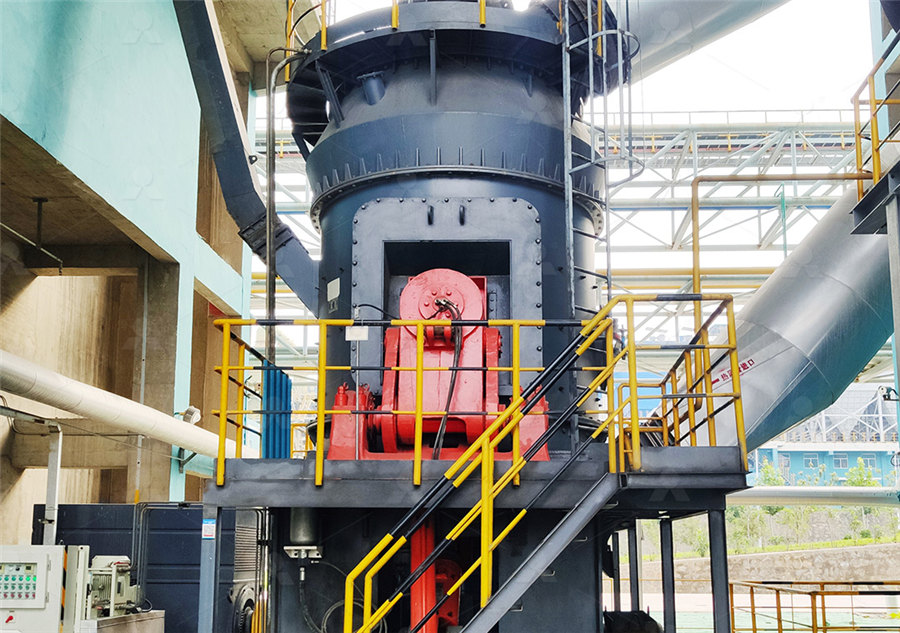
Modelling copper smelting – the flash smelting plant, process and
2020年6月1日 Avarmaa K, Yliaho S, Taskinen P 2018 Recoveries of rare elements Ga, Ge, In and Sn from waste electric and electronic equipment through secondary copper smelting furnace based on the superposition principle Miner Eng 2(4):489 of violaritebased nickel concentrate in simulated suspension smelting 2023年10月27日 The ball mill is a rotating cylindrical vessel with grinding media inside, which is responsible for breaking the ore particles Grinding media play an important role in the comminution of mineral ores in these mills This work reviews the application of balls in mineral processing as a function of the materials used to manufacture them and the mass loss, as A Review of the Grinding Media in Ball Mills for Mineral 2024年10月22日 In cases where sulfide ores have nearly equal quantities of copper and nickel, a second selective flotation step is required to produce both a lownickel copper concentrate and a separate nickel concentrate Nickel concentrates are often subjected to leaching with sulfuric acid or ammoniaNickel Metal: Types, Applications, Benefits, and Production ProcessDownload scientific diagram Working principle of the grinding machine from publication: Development of newly designed combined grinding equipment As acknowledged, biomass has been identified Working principle of the grinding machine
.jpg)
Production of Nickel Concentrates from Sulfide Ores
2011年12月31日 The conventional smelting and refining of Ni sulfide concentrates is an effective strategy for extracting Ni from sulfide ores However, during the smelting process, sulfur is oxidized to sulfur One distinction between crushing and grinding equipment is that the working surfaces of crushing equipment do not make contact with each other during size reduction CrushabililY may be defined as the ease of crushing a sample under standard conditions Various test ing procedures may be used to measure crushability" (Horst 1985, p 3A5)CHAPTER 5 GENERAL PRINCIPLES OF MINERAL PROCESSING 2016年3月26日 The gravity spiral circuit is designed to extract and concentrate "coarse gold' from the recirculating load in the mill grinding circuit and hence prevent a 911 Metallurgist is a trusted resource for practical insights, solutions, and support in mineral processing engineering, helping industry professionals succeed with proven expertise Gravity Spiral Concentrator Gravity Spiral Concentrator Working Principle 911Metallurgist2021年8月27日 The working principle of electrochemical grinding is When a metal surface is acted upon with an electrolyte under a high current, the metal surface gets oxidized to form an oxide layer (corrosive layer) This layer is removed with the action of a flowing electrolyte and rotating grinding wheelElectrochemical Grinding: Definition, Parts or Construction, Working
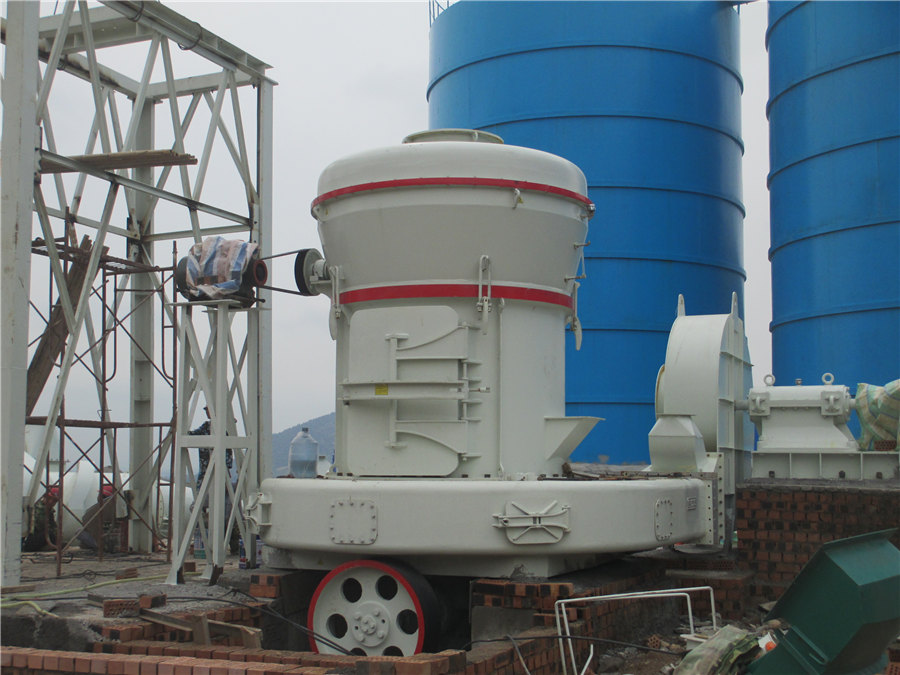
working and principle of grinding machine
2023年8月15日 In conclusion, the working principle of a grinding machine involves rotating the grinding wheel at high speed, which causes the material to be cut or removed from the workpiece This process is achieved by the abrasive particles present in Comminution in the mineral processing plant is carried out in a sequential manner using crushers and screens followed by grinding mills and classifiers The various types of comminution equipment including their general application are described in detail below 321 Crushing Equipment Primary Crushers – Jaw and GyratoryIntroduction to Mineral Processing or Beneficiation2005年12月15日 Scavenger concentrate from each module was recycled to a junction box in the rougher of the same module and rougher concentrates were combined for two stages of cleaning Cleaner tailing was split and half returned to each of the roughers Details of the equipment selection for this flowsheet can be found in George (1996)Development and implementation of a new flowsheet for the There are many types of grinding: “precision” and “rough,” internal, external, surface, centerless; using wheels or belts; and conventional or “super” abrasives “Principles of Grinding” 5 Part Series in Machinery Magazine, new York, NY, 1971 Google ScholarPrinciples of Grinding SpringerLink
[GYQ0R)ZQ]ESS4NJ.jpg)
THE APPLICATION OF THE PLATSOL™ PROCESS TO COPPER NICKEL
nickel and copper concentrates for toll treatment With prevailing smelter payment terms (and associated smelting and refining charges), the economics were never attractiveJune 2022; ARCHIVE Proceedings of the Institution of Mechanical Engineers Part C Journal of Mechanical Engineering Science 19891996 (vols 203210) 236(2):1107(PDF) A comprehensive review on the grinding process: 2022年1月1日 In recent years many developments are there in the direction of cooling and lubrication The new developments to replace the traditional cutting fluids are in the direction of using the technologies like, minimum quantity lubrication, dry cutting by designing the cutting tool geometry properly, air cooling, cryogenic cooling, solid lubricants, nano fluids, gaseous fluids, Effects of minimum quantity lubrication (MQL) in grinding: Principle 2005年7月1日 Since 2014, fine grinding / atmospheric leaching of nickel concentrate in mixed sulphatechloride solution with Cl 2 (g) has been the first step of Vale's Long Harbour Processing facility in The Activox (R) process: Growing significance in the nickel industry
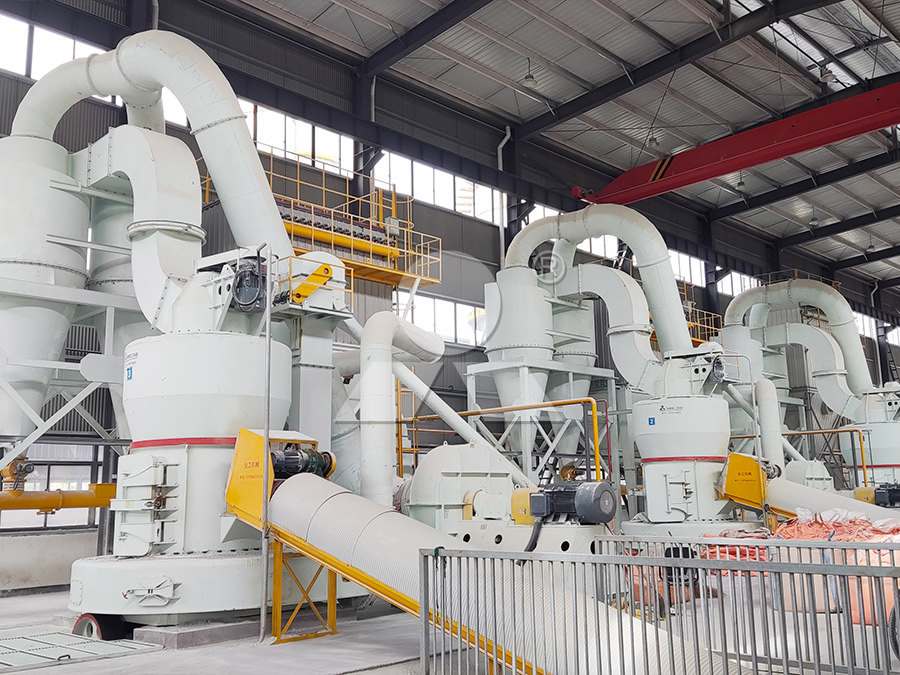
Plastic deformation mechanism of grinding subsurface of nickel
2023年9月4日 In the formula, v s is the wheel speed, v w is the feed rate, a p is the grinding depth, d eq is the diameter of the grinding wheel, and λ s is the perimeter of the grinding wheel 22 Plastic mechanism of subsurface During the grinding process, the workpiece is subject to the tangential force exerted by the abrasive particles, often resulting in subsurface crystal slips High recovery rate – recover 05% to 30% concentrate, increasing recovery rate 3 Wide feed and particle size recovery – feed size up to 30mm, which reduces the step of prescreening the feed Improve the potential for gravity recovery and avoid excessive grinding 4 High efficiency – It occupies a small area and is simple and convenient Mineral Jig Separator Jig Concentrator JXSC Machinerythe annealed condition; hardenable only by cold working Alloy 212 970 Mn 20, C 005 which provides the best condition for machining Alloy 222 995 Mg 0075 Alloy 400 N04400 665 315 Nickelcopper and nickeliron alloys for sulfuric acid and Alloy 401 N04401 425 555 03 Mn 16A GUIDE TO THE USE OF NICKELCONTAINING ALLOYS NO 天之前 High pressure grinding rolls or HPGR is such a kind of equipment that uses this principle for crushing operations HPGR has been widely used in fine crushing of metal ore beneficiation plants, crushing in cement industry, granulation in chemical industry and fine grinding of pellets to increase specific surface areaHigh pressure grinding rolls HPGR for iron ore, cement MAXTON
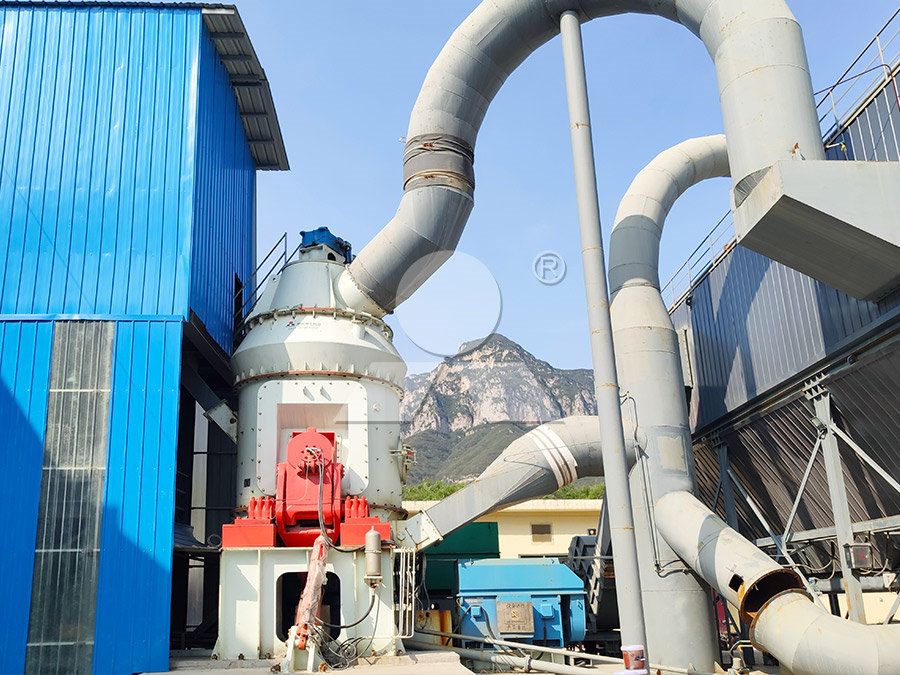
Safe use of nickel in the workplace
Nickel excretion by rats following a single treatment in Proceedings of the Western Pharmacology Society 1973 WESTERN PHARMACOL SOC INC UCLA SCHOOL MEDICINE DEPT PHARMACOLOGY, LOS Tedeschi, RE and FW Sunderman, Nickel poisoning V The metabolism of nickel under normal conditions and after exposure to nickel carbonyl2019年12月12日 The production of ferronickel concentrate from lowgrade nickel laterite ore containing 131% nickel (Ni) was studied by the nonmelting reduction magnetic separation process(PDF) Production of Ferronickel Concentrate from LowGrade Nickel