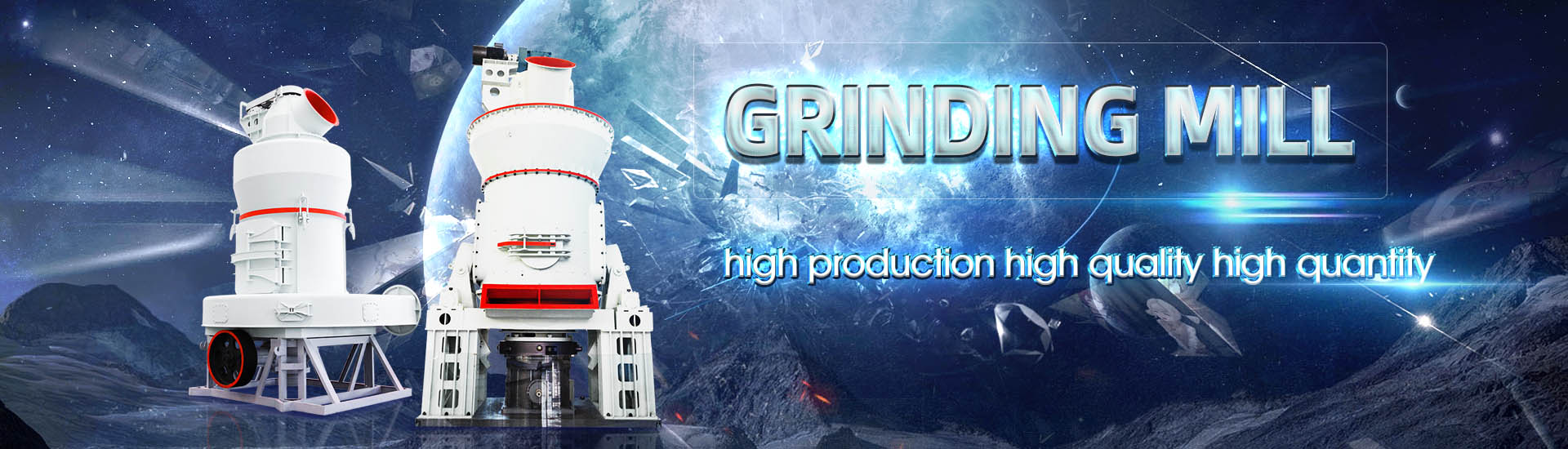
Cement plant waste heat power generation QC
.jpg)
Potential savings in the cement industry using waste heat recovery
2023年9月15日 A simultaneous power generation and heat recovery application using a heat pipeassisted thermoelectric generator were depicted in [130] Modelling results showed that 2013年4月1日 This study aims at the identification of a best practice example for energy utilization in an existing commercial cement production plant with a waste heat recovery system as a new(PDF) Waste Heat Recovery Power Generation Systems Waste Heat Recovery for the Cement Sector 1 Waste Heat recovery (WHr) is a proven technology, but until now WHr uptake has been limited except in China As early as the 1980s, Waste Heat Recovery for the Cement Sector2018年3月1日 In this paper, we propose a global optimization method based on thermal resistances analyses for a waste heat power generation system in a cement plant The system Optimization design of waste heat power generation systems for
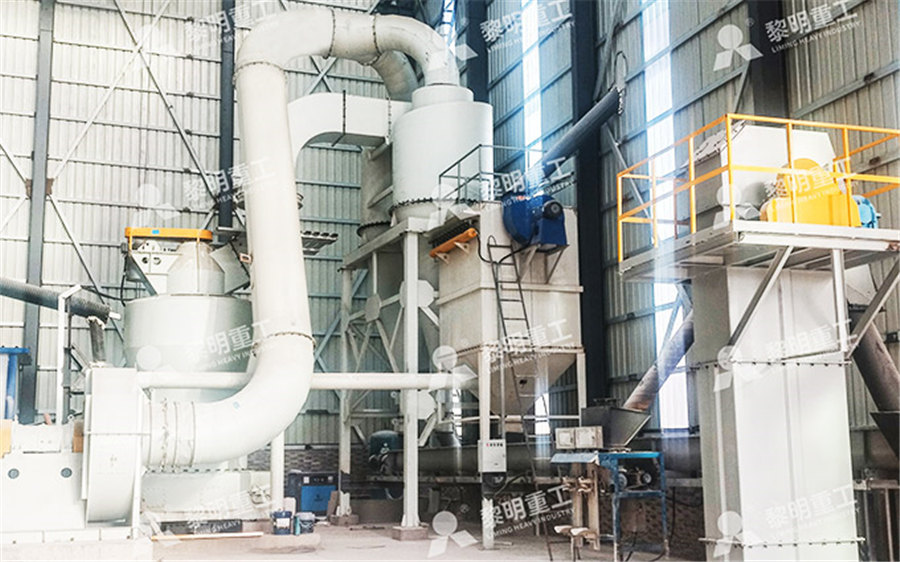
Power generation in white cement plants from waste
2021年10月1日 The waste heat from three waste streams from a white cement plant is to be recovered using both steam Rankine cycle (SRC) and steamorganic combined Rankine cycle (S ORC)2024年11月3日 A novel cycle: partial evaporating cycle with ejector is proposed to recover waste heat from cement flue gas for power generation Pinch point analysis is done to characterize Performance Analysis of Cement Plant Waste‐Heat Recovery for 2014年8月13日 This paper is an introduction to waste heat recovery generation systems and their operations and feasibility for the cement production process and is also a review of the Waste Heat Recovery Power Generation Systems for Cement In this study, a waste heat recovery (WHR) captive power plant will be installed to effectively utilize the low temperature waste heat of the exit gases from Suspension Preheater (SP) and Waste heat recovery and power generation in cement works
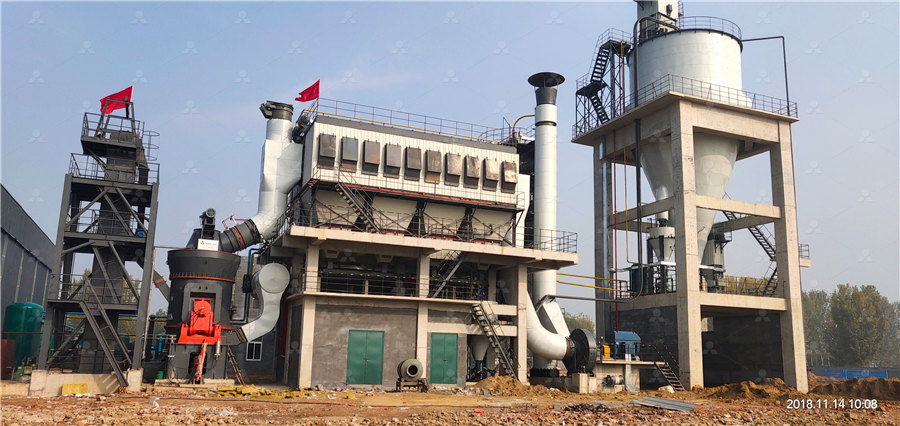
Power Generation by Waste Heat Recovery in Cement Industry
heat recovery (WHR) system to generate electricity Criterion 2 WHR system consists of a Suspension Preheater boiler (SP boiler) and/or Air Quenching Cooler boiler (AQC boiler), Waste Heat Recovery in Cement Plants The waste heat recovery power generation technology in cement plants is usually applied to the preheater to fully absorb the heat energy of waste heat and waste gas and improve the Waste Heat Power Generation in Cement Plant2023年7月26日 That’s a lot of heat yet in many cement plants, much of it still disappears via flue gases and surface dissipation – as much as 40%45% of what’s put in This is where waste heat recovery (WHR) comes in The waste Harnessing waste heat to decarbonise cement and steelwaste heat recovery but has limited power generation due to certain factors like pinch points, working fluid decomposition 9781467344517/12/$3100 ©2012 IEEEPower Generation by Different Waste heat recovery Methodologies
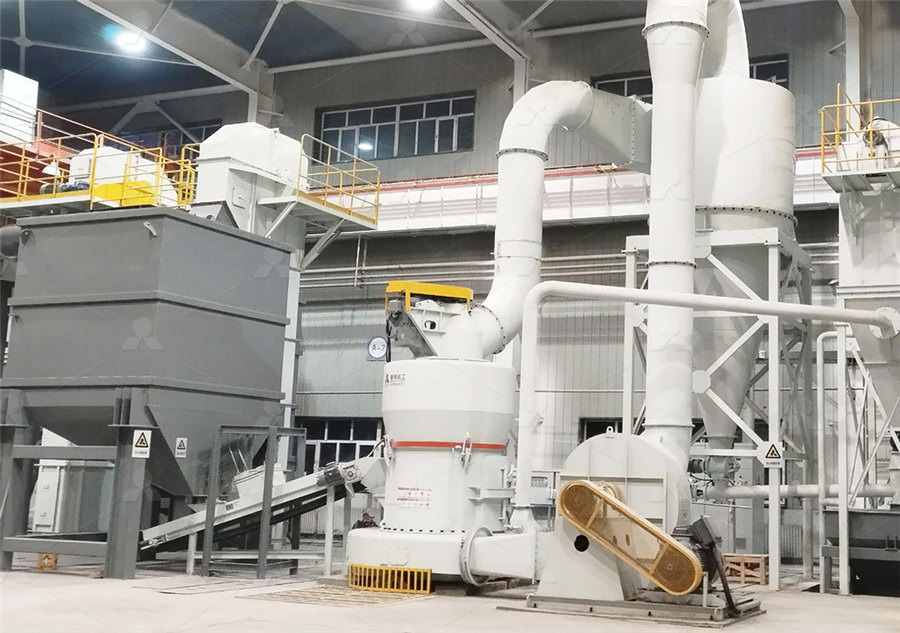
On the rise: Building and waste heat recovery at Najran Cement
2012年8月7日 Table 1: Capacities and suppliers of major equipment to be installed on Najran Cement's Line 3 at Sultana in the south of KSA Waste Heat Recovery (WHR) power project In addition to the Line 3 cement project and CPP, NCC intends to play a pivotal role in KSA by reducing CO 2 emissions, optimising cement plant operation to improve energy efficiency and 2013年4月1日 of cement plant waste heat power generation reached 40 billion KWh per year until December of 1980 in the United States The technology of WHRPG is generating electricity by(PDF) Waste Heat Recovery Power Generation Systems for Cement 2015年1月1日 of cement plant waste heat power generation reached 40 billion KWh per year until December of 1980 in the United States The technology of WHRPG is generating electricity by(PDF) Waste Heat Recovery Power Generation Systems for Cement The document discusses waste heat recovery power generation (WHRPG) technology for cement plants It provides an overview of WHRPG, its diffusion in cement plants, Kawasaki's WHRPG technology, and operational reliability WHRPG can generate electricity by capturing waste heat from cement production processes like preheaters and clinker coolers It has been Kawasaki Waste Heat Recovery Cement Plant PDF
.jpg)
Potential savings in the cement industry using waste heat
2023年9月15日 There are different technologies available for the recovery of waste heat, and many industrial facilities have been improved by using waste heat to enhance their energy efficiency [8]These systems can offer significant energy savings and substantial reductions in greenhouse gas emissions (GHGs) [9]Wasteheat recovery systems include recuperative and 2020年9月7日 Global energy consumption trend during the last 140 years The energy sources that have been taken into account are coal, crude oil, natural gas, hydroelectricity, nuclear electricity, and (PDF) Waste Heat to Power: Technologies, Current Applications Evaluating Recoverable Waste Heat and Power Generation Potential provide up to 30 percent of a cement plant’s overall electricity needs Besides, it offers several other benefits, including reduced greenhouse gas emissions and less dependency on external power suppliersWaste Heat Recovery in Turkish Cement Industry World Bank942 Optimization of Organic Rankine Cycle Waste Heat Recovery for Power Generation in a Cement Plant via Response Surface Methodology Table 3 Design of experiment level code Code Level 1682 1 0 +1 +1682 p HPT (bar) 966 1000 1050 1100 1134OPTIMIZATION OF ORGANIC RANKINE CYCLE WASTE HEAT RECOVERY FOR POWER
.jpg)
Cement burning plant waste heat power generation system
In a cement burning plant waste heat power generation system, an AQC boiler comprises an economizer, an evaporator and a superheater, and a PH boiler comprises a first evaporator and a superheater A part of hot water heated by the economizer of the AQC boiler is fed through a flasher to the low pressure stage of a stream turbine, another part is superheated by the Recovery of Waste Heat By Cement Plant for Power Generation *Ravikant Rai, **Chandra Prakash Sonkar *Research scolar, **Assistant Professor Heat power engineering (Department of Mechanical Engineering) Ojaswini Institute of Management Technology, Damoh Abstract —The Waste heat is heat, which is produce in a process where fuel combustion orRecovery of Waste Heat By Cement Plant for Power Generationfrom the central station power plant to the user result in reduced primary energy use and lower greenhouse gas emissions The most common CHP configuration is known as a topping cycle, where fuel is first used in a heat engine to generate power, and the waste heat from the power generation equipment is then recovered to provide usefulWASTE HEAT TO POWER SYSTEMS US Environmental 2018年3月1日 Fig 1 shows the schematic diagram of the waste heat power generation system for a cement plant The system contains a suspension preheater (SP) boiler, an air quenching cooler (AQC) boiler, a steam turbine, a generator, a condenser, a feed water pump and a heat recovery system with nine heat recovery exchangersOptimization design of waste heat power generation systems for cement
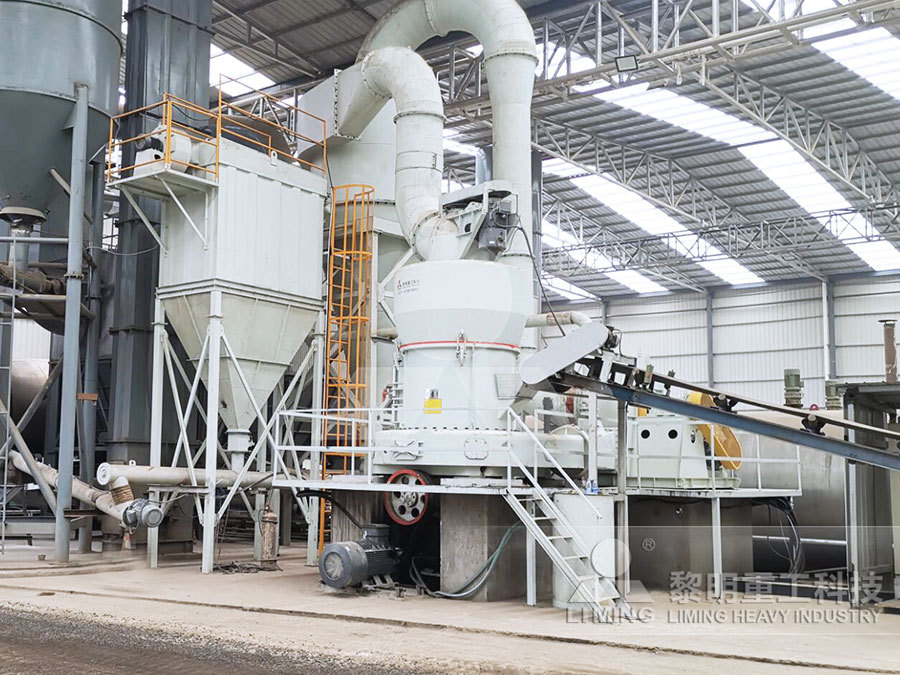
The thermoelectric generators use for waste heat utilization
Therefore, the electricity generation in a cement plant from waste heat from the rotary kiln can be achieved by: than 30% of the electric power demand by the cement plant In recent years, Summary: The generation of power from waste heat in cement plants was for a long time the subject of controversial discussion Today, hardly anyone remains unconvinced by the concept Depending on the system used, 30–45 kWh/t clinker can be generated, which is up to 30 % of the electrical power requirement of a cement plant The benefits of this technology are clearTrends in power generation from waste heat in cement plantsAs shown in Figure 1, the hot, dustladen exhaust gases from the cement plant can be tapped from two sources — namely, clinker cooler and preheater cyclones The hot gases are passed through the waste heat recovery boiler (WHRB) to generate mediumpressure superheated steam to drive the steam Rankine cyclebased power plantWaste Heat Recovery Systems and Power Projects for Cement PlantsSemen Indonesia, who is the parent company of Thang Long Cement JSC, at its Tuban Plant located in East Java under “Facilities Subsidy Scheme 2014 for Project Using the Joint Crediting Mechanism: Facilities Subsidy Project of Power Generation by Waste Heat Recovery Power Generation at Cement Factory in
.jpg)
Waste Heat Power Generation System of Cement Calcination Plant
In a cement burning plant waste heat power generation system, an AQC boiler comprises an economizer, an evaporator and a superheater, and a PH boiler comprises a first evaporator and a superheater A part of hot water heated by the economizer of the AQC boiler is fed through a flasher to the low pressure stage of a stream turbine, another part is superheated by the Power Generation by Waste Heat Recovery in Cement Industry Gen TAKAHASHI General Manager, Global Business Development Seminar on the Joint Crediting Mechanism Counterpart PT Semen Indonesia Site Tuban Plant, East Jawa Power Generation 28MW GHG Emission Reduction 122,000tCO2 /year Surabaya Tuban appx100km Surabaya Jakarta PJ Power Generation by Waste Heat Recovery in Cement IndustryJournal Preproof Power generation in white cement plants from waste heat recovery using steamorganic combined Rankin cycle AM Khater, A Soliman, Tamer S Ahmed, Ibrahim M IsmailPower generation in white cement plants from waste heat Power generation Generally the waste heat recovery efficiency is 227%The total heat available for power generation is 992Mcal/hr Gross power generation = Total heat available for power generation *WHR efficiency*1000 = 992 * 0227 * 1000/860 Assuming 80 00h usage, we find Energy saved = power generated * Hour usage = 2620 * 8000 Waste Heat Recovery in Cement plant International Journal of
.jpg)
Cement Plant Power Solutions GE Vernova
Steam produced from these two waste gases during the cement waste heat recovery process powers the steam turbine, creating an electrical power source for the plant Because the cement plant is using waste in this way, it can reduce its dependence on costly fuel 2020年2月10日 The 8MW system will recover waste heat during the calcining stage of cement production and use it for power generation and energysaving measures at the plant The KHI system is scheduled to Kawasaki Heavy Industries to supply 8MW waste heat power generation In a cement plant, 26% of heat input is lost through the kiln, preheater surfaces, convection from the kiln, and preheaters This article reports on waste heat recovery from a typical cement plant in Egypt Measurements and analyses have been performed to determine the waste heat from different stages of the cement manufacturing linesINVESTIGATION OF USING KALINA CYCLE FOR WASTE HEAT RECOVERY IN A CEMENT 2014年7月16日 Waste heat generated in cement manufacture has proven to be amenable to conversion into electrical energy, provided it is tapped in adequate measure and the temperature is sufficiently high to make the project viable In a typical Indian cement plant, the potential generation of power from waste heat is estimated at roughly 20 – 25 kWh/t of Waste Heat Recovery in India – Part 2 World Cement
.jpg)
Waste heat recovery and power generation in cement works
2009年12月1日 In cement plant, about 90% of total energy is used as heat energy in the clinker calcination process Out of total heat consumed in the clinker calcination process, more than 35% of heat is discharged as waste heat to the surroundings without utilization Therefore, a great deal of energy is wasted, and the heat pollution in the workplace is serious In this study, a waste Waste Heat Power Generation Capacities as a Function of Kiln Capacity 17 Figure 9 WHR System Installed Costs will vary in each specific cement plant, the general enabling factors are favorable in East and South Asian countries and in Latin AmericaWaste Heat Recovery for the Cement Sector» In this process it was observed that in house power generation is feasible if the waste heat from various areas in the industries is utilized This technology is already proven in steel industries » In case of Cement industries, it was observed that there are few areas from where the waste heat can be utilized for steam Power generationDecarbonization In Cement Plants With Waste Heat Recovery 2021年12月1日 Waste heat is mainly liberated from kiln preheater system, clinker cooler, and combustion exhaust gases The amount of heat liberated from a cement plant to the surrounding may reach 40% of the energy consumed in the production process [12] Power generation from waste heat recovery may provide about 20% of energy consumption in a cement plantPower generation in white cement plants from waste heat
.jpg)
Optimization of Organic Rankine Cycle Waste Heat Recovery for Power
2015年12月30日 A cement plant that produces 8,300 tons per day releases 265,000 Nm3/h of flue gas at 360°C from its Suspension Preheater (SP) and 400,000 Nm3/h of hot air at 310°C from its air quenching cooler (AQC) It is imperative to recover the waste heat emitted by the plant for power generation, ie, Waste Heat Recovery Power Generation (WHRPG)Waste Heat Power Generation Capacities as a Function of Kiln Capacity 17 Figure 9 WHR System Installed Costs will vary in each specific cement plant, the general enabling factors are favorable in East and South Asian countries and in Latin AmericaWaste Heat Recovery for the Cement SectorExergoeconomic Analyses of a Cement Plant Waste Heat Recovery in a Novel Combined Power and Refrigeration Cycle Bourhan Tashtoush1*, Karima Megdouli2, Towhid Gholizadeh3, Elhadi Dekam4 1 Mechanical Engineering Department, Jordan University of Science and Technology, Irbid 22110, Jordan 2 Unité de Recherche Energétique et Environnent, Ecole National Exergoeconomic Analyses of a Cement Plant Waste Heat 2022年5月1日 The waste heat recovery of cement plants has been extensively studied in the past few years Wang et al [16] evaluated an ORCbased WHRS for a typical cement production line, while hexane, isohexane, R601, R123, or R245fa was selected as the working fluidThe results showed that the scheme using R601 had the best economic and environmental Performance evaluation of a novel design for the waste heat
.jpg)
Waste Heat Recovery Power Generation Systems for Cement Factory
2021年1月18日 A case study has been done at a cement factory having two units, 1600 TPD and 5500 TPD, identified three waste heat rejections at 176 °C, 330 °C and 420 °C and designed a suitable power plant 2014年7月14日 Waste heat recovery plants offer a reliable supplement to captive power generation in an energyintensive industry like cement, particularly in an energydeficient country such as India ACC Limited, part of the Holcim group, recently launched its first Waste Heat Recovery (WHR) system at the Gagal cement plant in the north Indian state of Himachal Waste heat recovery at ACC’s Gagal cement plant2018年4月30日 New technologies from FLSmidth are helping to maximise waste heat recovery for today’s cement producers – without compromising recuperation efficiency As cement producers are continually looking to improve the performance of their existing assets, many are seeing the upsides of bringing waste heat recovery into the production process In particular, “Waste Heat Recovery” maximisation in clinker cooler systemswasteheattoelectricity efficiency of 303% for a net power output of 8 MWe and a turbine inlet temperature of 550 °C • Simple Brayton sCO2 power cycle • The cement plant heat source can be used for many different cycle layouts and with a combination of Hydrogen systems can lead to the highefficiency green cement plantGREENING A CEMENT PLANT USING sCO POWER CYCLE
.jpg)
A CASE STUDY: THE WASTE HEAT RECOVERY AND UTILIZATION FOR POWER
commercial applications in cement plant The aim of this case study was generating power by utilizing waste heat from the dual sources using Steam Rankine Cycle In the present work a WHRPG system is designed to recover waste heat for power generation purpose in the cement manufacturing process