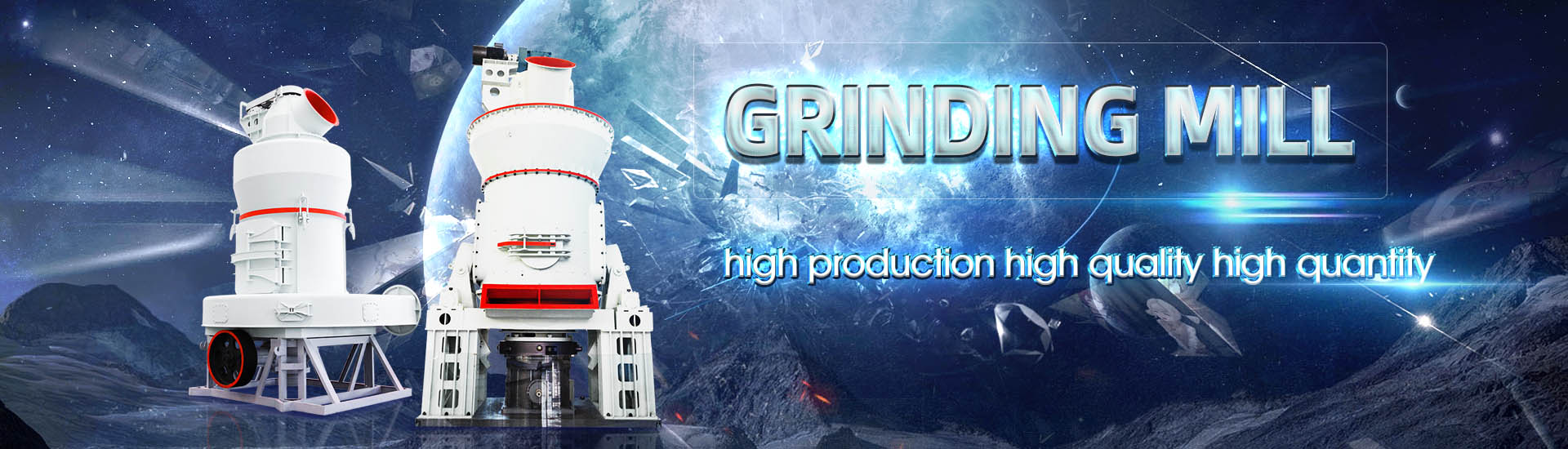
Working principle of cement processing equipment
.jpg)
Cement Manufacturing Process INFINITY FOR
2018年4月26日 Working principle Raw mills uses pressure and shear generated between the rollers and rotating table to crush and grind limestone, Cement manufacturing process information source: IECA (Instituto Español del Cemento y sus Aplicaciones) The systems for the monitoring and control of the cement manufacturing CEMENT MANUFACTURING PROCESS VisionTIRConcrete is made by mixing cement with aggregate (sand, gravel, and water), which forms a paste that hardens over time Cement is necessary to give the concrete its binding properties, How Cement is Made Cement Manufacturing ProcessThe Cement Plant Operations Handbook is a concise, practical guide to cement manufacturing and is the standard reference used by plant operations personnel worldwide Providing a The Cement Plant Operations Handbook International Cement
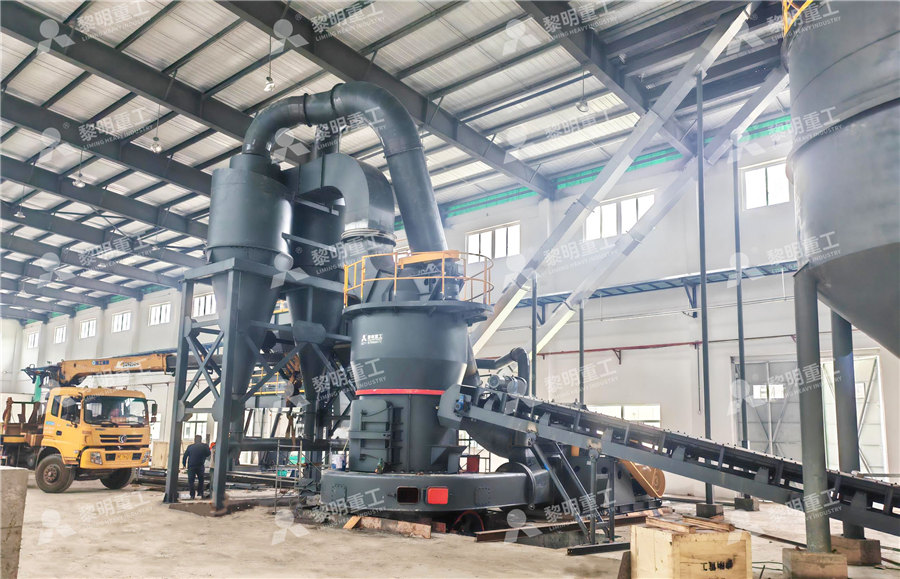
Cement manufacturing: components of a cement plant
Cement manufacturing: components of a cement plant This page and the linked pages below summarize the cement manufacturing process from the perspective of the individual components of a cement plant the kiln, the cement mill etc Cement kilns are an essential component of the cement manufacturing process, playing a crucial role in producing the clinker that is ground into cement These massive, rotating cylindrical vessels are designed to withstand extreme Comprehensive Guide to Cement Kilns: Processes, 2023年12月20日 Cement manufacturing is a complex process that begins with mining and then grinding raw materials that include limestone and clay, to a fine powder, called raw meal, which is then heated to a sintering temperature as The Cement Manufacturing Process Thermo Fisher The cement production process 1 The Quarry: The cement production process begins with the extraction of limestone and clay from the quarry 2 Crusher and PreBlending: The material is A practical guide to improving cement manufacturing processes
.jpg)
Chapter 4 Cement Manufacturing and Process Control
The most common way to manufacture Portland cement is through a dry process The first step is to quarry the principal raw materials, mainly limestone, clay, and other materialsPrevious Post Next Post Contents1 KILN STARTUP PROCEDURES11 KILN STARTUP PROCEDURES2 11 Parameters to be tracked during preheat3 111 Preheater/Precalciner4 112 Long Wet/Long Dry Kilns5 ¨ Thermal KILN STARTUP PROCEDURES INFINITY FOR 2023年2月28日 Learn everything you need to know about primary crushing, secondary crushing, and tertiary crushing in this comprehensive guide Discover the types of crushers used in each stage, their working principles, and the The Complete Guide to Primary Crushing, Secondary The working principle of the DICONT 031 is based on the differentiation method Conveying rate per mea sured unit has to be equal to the “time” set value The system components are the weigh hopper with adjustable flow control gate Pneumatic homogenization of raw mix INFINITY
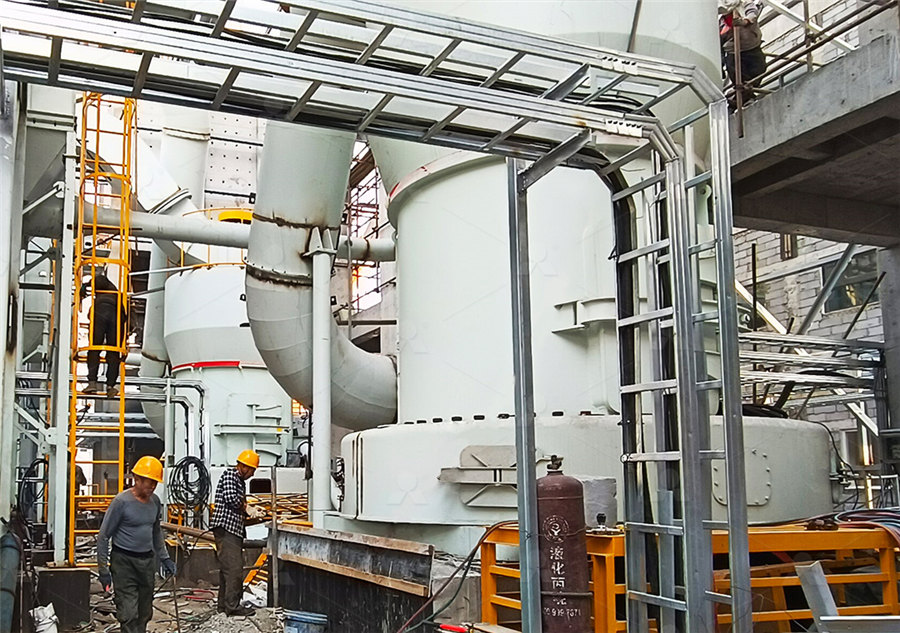
Everything you need to know about Crushers in Cement industry
In the cement industry, which uses chiefly mediumhard to hard limestone as its principal raw materials, singlestage crushing plants equipped with hammer crushers are the commonly preferred type Feed Hoppers The feed hopper, feeding equipment, crusher and product removal conveyors are the main component units of the plantExshaw FM2 successfully uses this idea to make the mill sweep dust fine enough for finish cement However the box is extremely large to accomplish this As a rule of thumb for cement mills, the air velocity around the discharge trunnion and hood must be less than 4 m/s In Exshaw’s dropout box they strive for about 2 m/sAIR SEPARATORS INFINITY FOR CEMENT EQUIPMENTWorking Principle Of Cement Grinding In Ball Mill read about history description parts construction working principle types and ball mill is one type of milling machine which is used to mill or grind the the ball mill is a key equipment to grind the chilli powder processing equipments in india; manganese sulphate production line; jai kaila Vibratory Feeder Principle For Production Process Of Cement2014年6月10日 This document discusses Portland cement and the cement manufacturing process It begins with an overview of what cement is and how it is used to make concrete It then describes the industrial process for manufacturing cement, involving grinding raw materials like limestone and clay at high temperatures in a kiln to form clinker, which is then pulverized with Cement manufacturing process PPT Free Download SlideShare
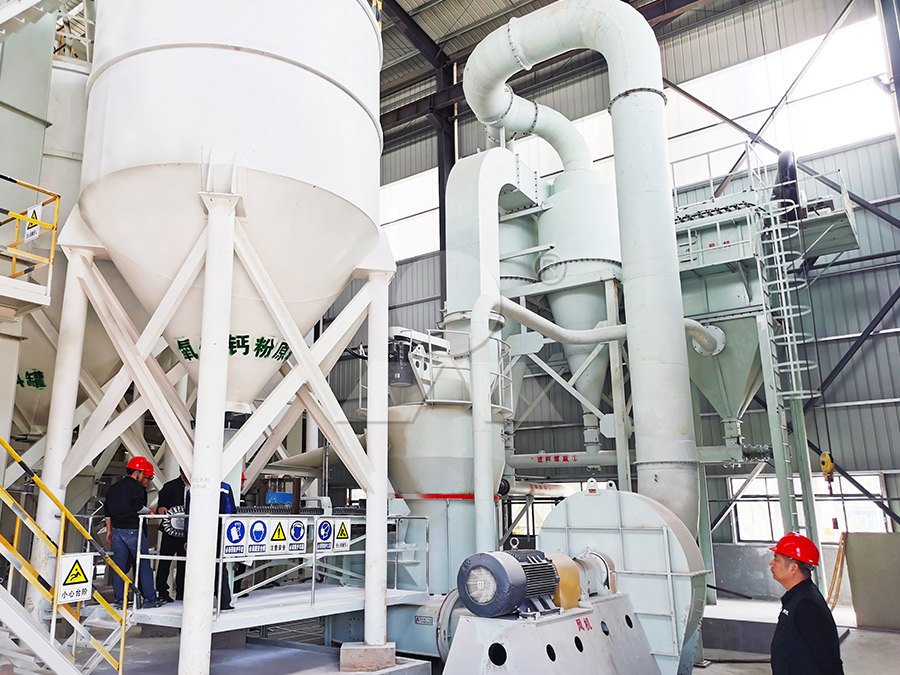
Ball Mill PPT SlideShare
2015年11月30日 PRINCIPLE: A ball mill works on the principle of impact and attrition size reduction is done by impact as the balls drop from near the top of the shell 8 CONSTRUCTION: Wet or dry ball mill grinding machine consists of following parts: 1Working Principle: Feeding: Raw materials (cement clinker, fuel, and auxiliary materials) enter the rotary kiln from the feeding port, forming a material layer; Rotary Motion: The rotary kiln begins to rotate, and the material gradually slides down and moves forward under the action of gravity and centrifugal force; Drying, Preheating, Calcination, and Cooling: Fuel is sprayed from the kiln Cement Rotary Kiln Structure Working Features MCpassivation – 13 Cement quality – 14 Setting time – 15 ASTM cement types and specifications – 16 European EN 197 cement specification – 17 Composite cements (intergrinds and blends) – 18 Supersulphated cement – 19 Calcium aluminate cement (CAC) – 20 Shrinkagecompensating cements (SCC) – 21 ISO 9001:2000 Quality 8The Cement Plant Operations Handbook International Cement Electrochemical machining (ECM) is a machining process in which electrochemical process is used to remove materials from the workpiece In the process, workpiece is taken as anode and tool is taken as cathode The two Electrochemical Machining (ECM) Working
.jpg)
Roller Press In Cement Plant Roller Press Cement Mill CNBM
Working principle of cement roller press Two horizontally positioned, simultaneously revolving extrusion rollers are the primary source of highpressure material crushing in the roller press Through forced downward movement, the closed material layer is gradually raised to a sufficient extrusion pressure until it is crushed, extruded into a dense cake, and released from the machine3 Construction, Working and Maintenance of Crushers for Crushing Bulk Materials practicalmaintenance Crushers for Bulk Materials Crushers and breakers are used to reduce size of mined and quarried material for further processing or to size suitable for the intended end use The goal of a crusher is to crush theConstruction, Working and Maintenance of Crushers for Crushing 2012年6月1日 processing and mining industry, metallurgy, cement production, chemical industry, pharmaceutics and cosmetics, this paper we provide a brief survey of the basic principles in modeling of the Grinding in Ball Mills: Modeling and Process Control2022年7月11日 The FBE (Fluid Bed Equipment) technique introduces to improve the product quality, reduce the processing time, and reduce the cost of the manufacturing process A fluid bed processor is an advanced technique if talking about the past like FBD and RMG used to perform the same function which is involved the long time process, hence new technique is a very Fluid Bed Processor (FBP), Principle, and Working

Cement Processing Equipment Rotary Feeders Meyer Industrial
Bulk material handling equipment, such as a rotary feeder in a cement plant, is used to transfer these raw materials and mix them between points in the production process Because of the abrasiveness of the material and the extremely high temperatures of the process, slide gates, flap gates, and other cement equipment must be of exceptional durability2016年6月1日 For evaporating moisture from concentrates or other products from plant operations, Rotary Dryers are designed and constructed for high efficiency and economy in fuel consumption Whenever possible to apply heat direct to the material to be dried, Rotary Dryers of the Direct Heating Design are used If it is not possible to apply heat direct to the material to Rotary Dryer Design Working Principle 911MetallurgistApplication: In cement industry production, in order to improve the efficiency of the grinding system and reduce the energy consumption of the product, a circulating grinding system is now widely used As an important part of the system, the advanced performance of the classifier directly affects the efficiency of the system Therefore, the research and development of the Cement Seperator for Cement Grinding SystemWorking Principle of Cyclone Preheater: It utilizes the hightemperature airflow accumulated in the kiln and adopts multistage circulating suspension preheating method to make the raw material powder and the hot air flow exchange heat well, complete the suspension preheating and partial raw material decomposition, and prepare for the raw material into the kiln calcinationCyclone Preheater Provided for Cement Plant
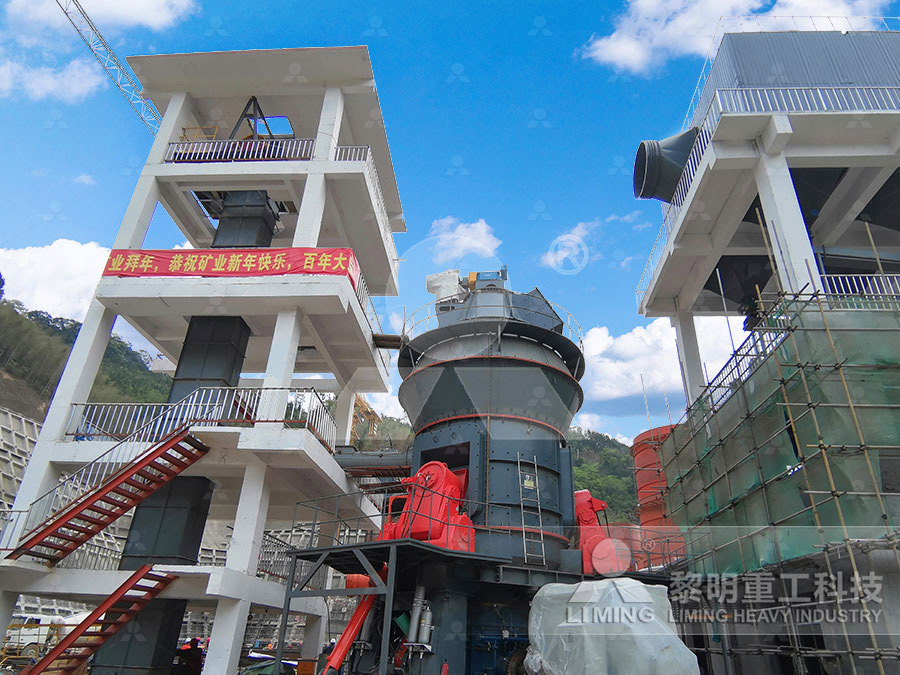
Rod Mill Ball Mill Cement Milll AGICO Cement Equipment
Rod Mill Working Principle The working principle of the rod mill is that the main motor is connected with the pinion through a reducer to drive the large gear ring, thus rotating the cylinder There are some steel rods in the machine chamberThe vertical roller mill (VRM) is a type of grinding machine for raw material processing and cement grinding in the cement manufacturing processIn recent years, the VRM cement mill has been equipped in more and more cement Vertical Roller Mill Operation in Cement PlantPrevious Post Next Post Contents1 Principles of Rock Drilling11 Objectives12 Contents13 Drilling Blasting14 Importance of Drilling and Blasting15 General Drilling Requirements16 Mechanism of rock Drilling17 Components of Drill Machine18 Dynamics of surface blasthole drill19 Systems of Rock Drilling:191 Mechanical192 Thermal193 Chemical110 Types of Principles of Rock Drilling INFINITY FOR CEMENT EQUIPMENTVertical cement mill is applied for the processing of nonflammable and nonexplosive mineral materials with mohs hardness below grade 8 and humidity less Vertical cement mill working principle AGICO CEMENT supplies EPC Vertical Cement Mill
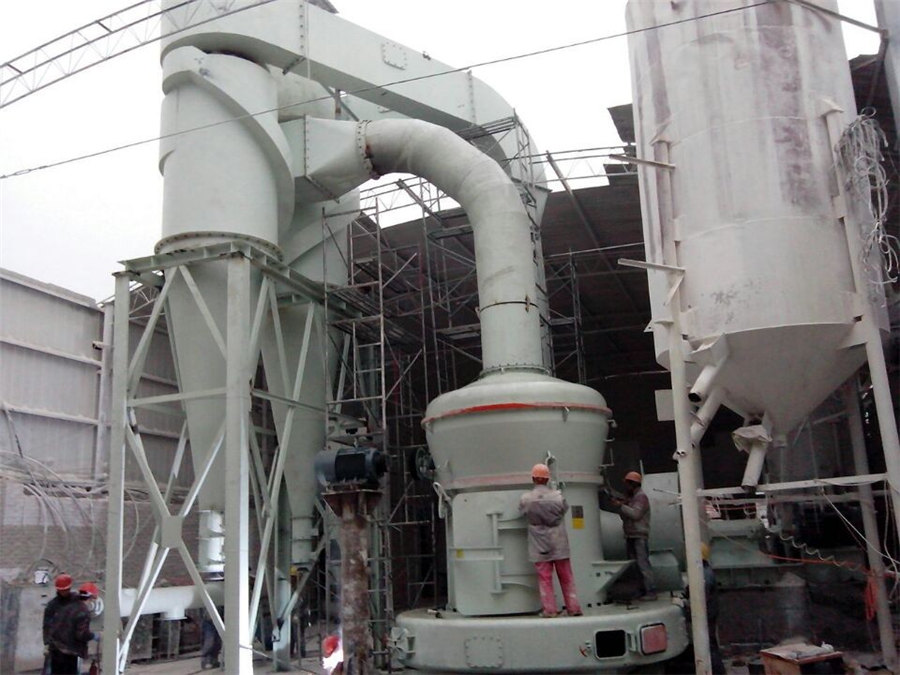
Different Working Principles of Crushing Equipment
How to divide the range of coarse, medium and fine According to the size of the broken material: Crushed: the feed size is 300900mm, and the discharge granularity is 100550mm; Medium crush: the feed size is 100350mm, and the discharge granularity is 20100mm; Finely divided: the feed size is 50 to 100 mm, and the discharge size is 5 to 15 mm What is granularity, what is 2022年6月17日 The working principle of a concrete batching plant is to mix, transport, and pour concrete into forms Some types of plants can also mix and compress the mixture before it enters the form A typical batching plant c onsists of a mixer, hopper, silo, storage bin or bins, truck or conveyor belt system, discharge pipe or nozzle, and control system, which includes an on/off How does the concrete batching plant work? PoyatosPrevious Post Next Post Contents1 Coarse size reduction of raw materials in Cement Industry11 Size reduction machinery and methods111 A Machinery for size reduction in the coarse range (crushers) by application of compression:112 B Crushers for size reduction by impact:113 C For comminution in the fines range (grinding mills) by application of impact:114 D Mills where Complete Lecture about Crushers in Cement Industryclick here to Download the Most Important 13 Books in Cement Industry PROCESS TRAINING for operators of Vertical RAW Mills Heating of mill and grinding plant In fact there are three processes going on in the MPS mill namely grinding, drying and clas sifying, and only when all three processes are working well the operation is smoothPROCESS TRAINING for operators of Vertical RAW Mills
.jpg)
What Role Does Cement Mill Play In Production?
2024年10月14日 In today's construction industry, the demand for cement as a basic material continues to grow, and cement mills, as key equipment in the cement production process, play a vital role The production process of cement mills involves a variety of technical links, from the grinding of raw materials to the manufacture of finished cement, and each step affects the Cement Ball Mill Structure When Ball Mill is working, raw material enters the mill cylinder through the hollow shaft of the feed The inside of the cylinder is filled with grinding media of various diameters (steel balls, steel segments, etc); when the cylinder rotates around the horizontal axis at a certain speed, Under the action of centrifugal force and friction force, the medium and the Ball Mill for Cement Grinding ProcessBag Filters types ,working principles daily maintenance INFINITY FOR CEMENT EQUIPMENTpdf Free download as PDF File (pdf), Text File (txt) or read online for free Bag filters operate by separating dust particles from gas using filtration material like mesh cloth As dustladen gas passes through the filter bag, particles larger than the mesh size are trapped Bag Filters Types, Working Principles Daily Maintenance ScribdIn principle, the standard deviation is reduced by stacking the material in a large number of layers and subsequently reclaiming these layers Theoretically – without taking the particulate nature of the material into account – the blending Everything you need to know about Stacker and
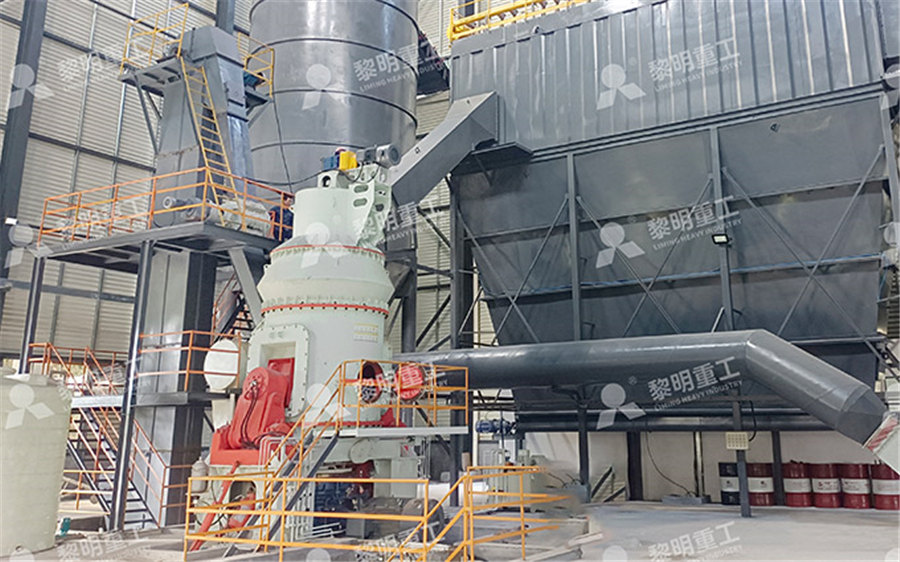
Everything you need to know about Clinker Coolers
The efficient sealing between the compartments permits operation at high and different pressures in the various compartments With a normal clinker bed thickness of 600 mm, the pressure drop at a constant air flow per unit area will Stage of Cement Manufacture There are six main stages of the cement manufacturing process Stage 1: Raw Material Extraction/Quarry The raw cement ingredients needed for cement production are limestone (calcium), sand and clay (silicon, aluminum, iron), shale, fly ash, mill scale, and bauxite The ore rocks are quarried and crushed into smaller pieces of about 6 inchesHow Cement is Made Cement Manufacturing Processkey Equipment Working Principles , types , Daily maintenance Cement Grinding system, key Cement Ball Mill Maintenance admin / Everything you need to know about Cement Mill Maintenance TO DOWNLOAD THIS POST AND MOST IMPORTANT MATERIAL IN CEMENT Daily maintenance, Raw Materials Processing Select your Favorite Type of 7 Different key Equipment Working Principles , types , Daily maintenanceHow can I start a cement manufacturing plant? Starting a cement factory involves several crucial steps: Determine the scale of production and type of cement to be produced Choose an optimal location for the cement plant Design the layout of the cement factory Acquire the necessary equipment Construct the factory and install the equipmentStepbyStep Guide to the Manufacturing of Cement
.jpg)
Understanding the Cone Crusher Working Principle: How It
2023年2月23日 In this article, we'll explore the cone crusher working principle, including the eccentric motion of the main shaft, the crushing process, and the importance of proper maintenance Whether you're a seasoned industry professional or simply curious about heavy machinery, this article will provide valuable insights into the workings of the cone crusherA cement separator, also known as a cement pulverizer or cement cyclone separator, is a kind of equipment used to separate ground cement clinker and ground cement powder in a cement mill system Cement Mill Separator is usually installed at the end of the cement mill to receive the material from the mill and separate it from clinker and cement powderCement Separator HighEfficiency Cement Mill SeparatorResidence Time ac Conscant Bed Depth As mentioned previously, it is not desirable to maintain a constant undergrate pressure under all kiln out put ratesThis, of course, requires a constant bed depth, which means that the clinker residence EVERYTHING YOU NEED TO KNOW ABOUT OPERATION AND Basic working principle of cement classifier While different cement classifiers have different working principles The basic working principle is similar To separate coarse and fine particles, a cement classifier uses physical forces such as gravity, centrifugal force, inertia force, air drag force, and mechanical forceCement Mill Separator High Efficiency Cement Separator
.jpg)
How Is Cement Produced in Cement Plants Cement Making
This type of cement was invented in the early 19th century by Joseph Aspdin It is named ‘portland cement’ because its property is similar to the stone quarried on the Ise of Portland, England The making process of portland cement in the modern industry can be divided into the wet process, dry process, and semidry process