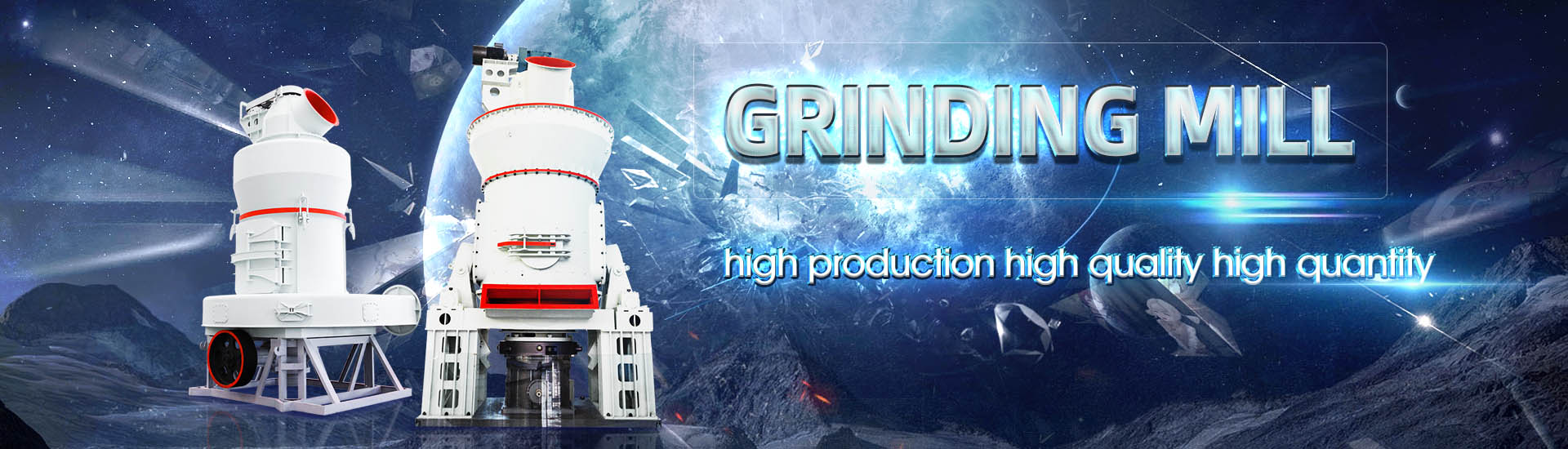
The unit capacity consumption of MMD1000 ore mill
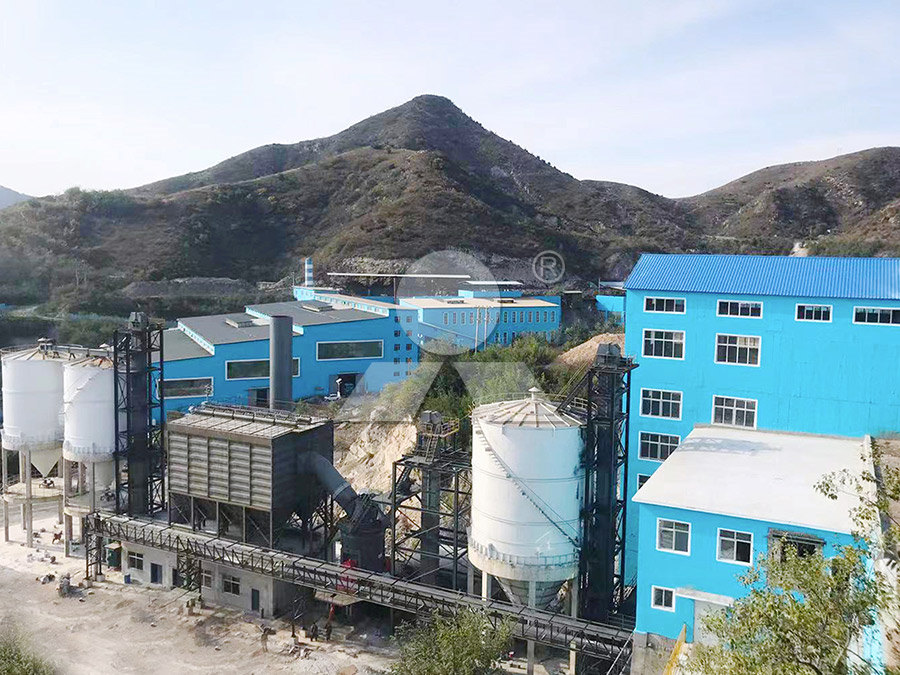
Ball Mill Design/Power Calculation 911Metallurgist
2015年6月19日 Use this online calculators for Motor Sizing and Mill sizing as well as mill capacity determinators In extracting from Nordberg Process Machinery Reference Manual I will also provide 2 Ball Mill Sizing (Design) example done ‘byhand’ from tables and charts2015年2月1日 A model of specific energy consumption (kW h/tonne milled) versus throughput (% design capacity) was developed for a base metal milling facility, from hourly electricity and The link between operational practices and specific energy 2017年7月26日 We will consider an ore with a ball mill work index varying between 16 and 13, feeding into a single stage ball mill operation with one million kilowatts per day consumed How Ball Mill Ore Feed Size Affects Tonnage Capacity2020年5月1日 Taking a Φ549 × 883 m ball mill as the research object, the reason for the low processing capacity of the ball mill was explored via process mineralogy, physicochemical Enhancing the capacity of largescale ball mill through process
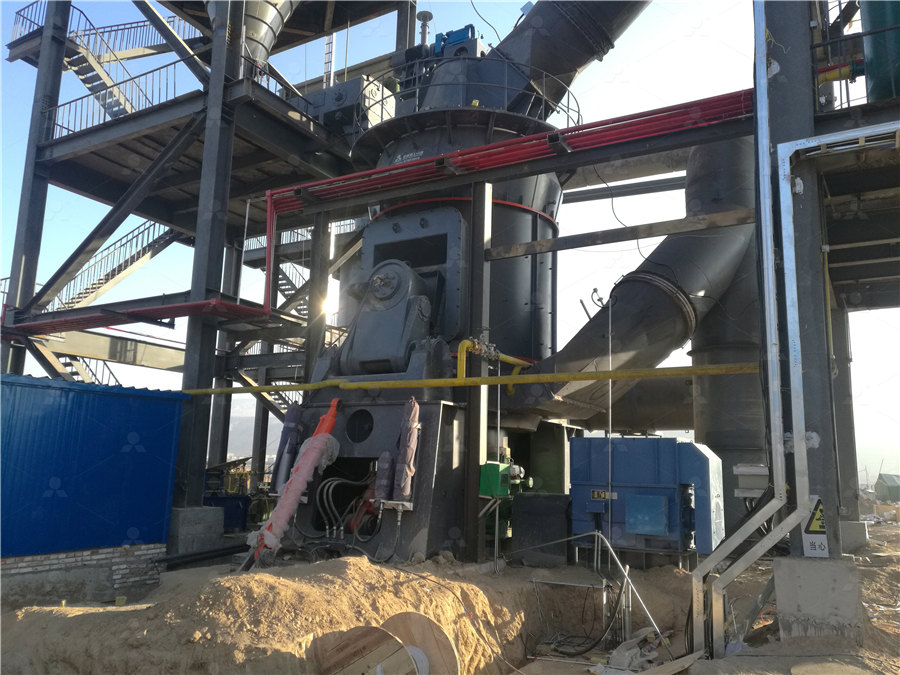
Energy conservation and consumption reduction in grinding
2023年11月1日 Grinding efficiency is the unit energy consumption rate of the mill, which represents the amount of material with a particle size of −0043 mm newly generated for every 2023年7月20日 (3) Hourly production capacity of the mill, which is the amount of raw ore processed by the mill per unit time under certain conditions of ore feeding and product particle Ore Grinding SpringerLinkTwo features specific to the IsaMill that make it attractive for coarser grinds are : the large unit size (currently up to 26 MW) suitable for large scale applications Installations at Lonmin Fine Grinding as Enabling Technology – The IsaMillIn this paper we focus on an approach to overcome the problem of inconsistent mill throughput related to variability in mill feed size and rock competency The focus is on ores containing AUTOGENOUS MILL FEED PREPARATION TO REDUCE UNIT
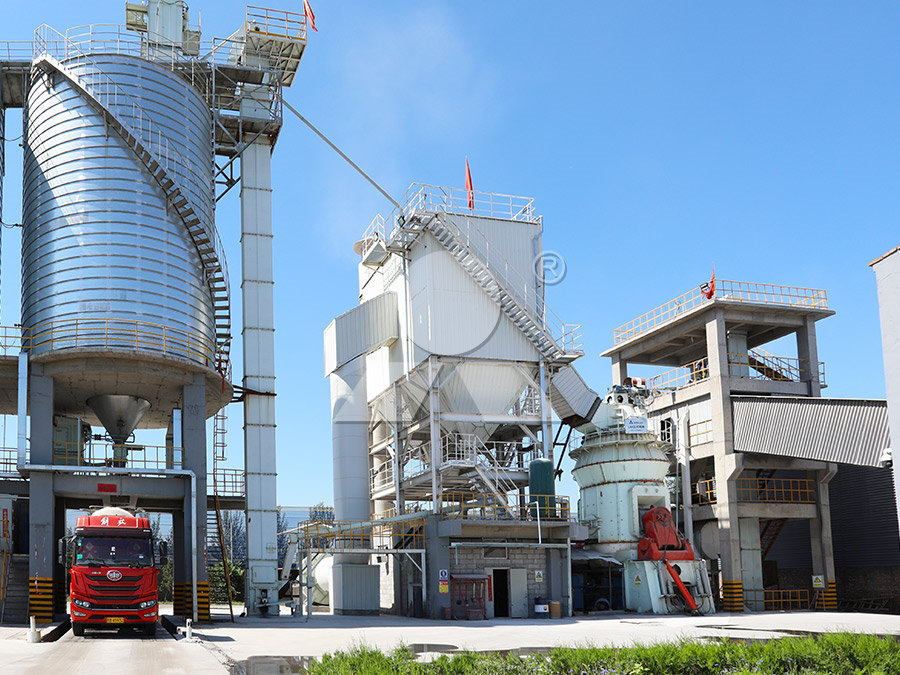
Implementing strategies to improve mill capacity and efficiency,
Recent advances in fine screening technology allow for the efficient classification of mill products by means of particle size separation only The advantages are numerous, including improved 2018年8月17日 The concept of ore blending is a very relevant notion in modern high tonnage production mines It is not only essential for the prolongation of the mine life of the concerned mine but as well as a The effects of ore blending on comminution 2013年8月1日 However, the mill exposes certain defects, including high power consumption per unit, huge steel consumption, severe overgrinding of products, and loud noise, etc (Aldrich, 2013)Consumption of steel grinding media in mills – A review2016年1月1日 In wet grinding practice, highstress abrasion occurs over a small region when ore particles are trapped between the grinding balls and the mill liner, and the load is sufficient to fracture A comparison of wear rates of ball mill grinding
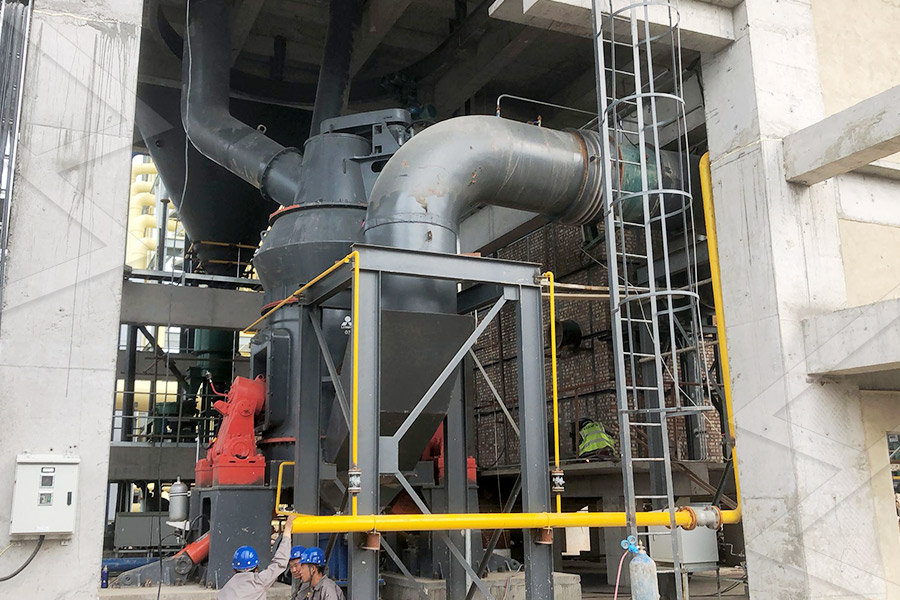
Consumption of steel grinding media in mills – A review
2013年8月1日 Apart from these cost factors, one of the major unsolved problems in the optimal design of ball mills concerns the equilibrium media size distribution in the mill, which is determined by the rate at which makeup media is added to the mill, as well as the rate at which these grinding media are consumed (Austin and Klimpel, 1985)Reliable prediction of grinding media 2021年2月26日 Milling is among the most energyconsuming technological stages of copper ore processing It is performed in mills, which are machines of high rotational masses The start of a mill filled to capacity requires appropriate solutions that mitigate the overloading One method for increasing the energy efficiency of ball mills is to optimize their drive systems This article Energy Efficiency Analysis of Copper Ore Ball Mill Drive PDF On Apr 29, 2021, Assad Yousif Khudher and others published Effect of number , thickness of the blades and feed rate on the capacity and power consumption of the hammer mill Find, read and Effect of number , thickness of the blades and feed rate on the This paper will focus on the ball mill grinding process, its tools and optimisation possibilities (see Figure 1) The ball mill comminution process has a high electrical energy consumption, especially when those systems are in combination with first or secondgeneration classifiers This is particularly relevant in terms of theBALL MILLS Ball mill optimisation Holzinger Consulting
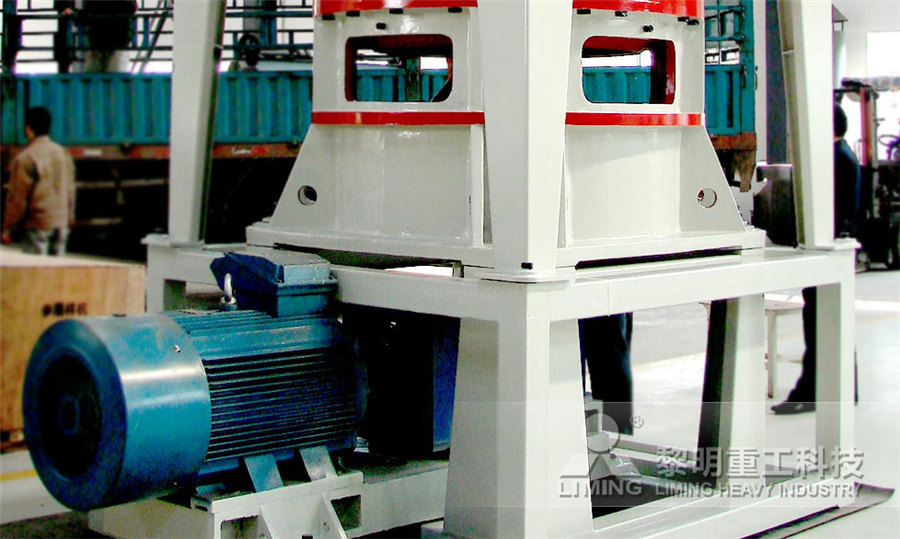
Energy consumption characteristics of turnmill machining
2016年12月29日 Reducing the energy consumption of manufacturing processes and machine tools can considerably affect the environmental and economic impact of industrial activities Since the 2008 global financial crisis, many scholars have focused on modeling the energy consumption of basic machining processes such as turning, milling or grinding, etc, and investigated the 2020年10月9日 Changsha , China; qyxie168@163 (QX); fuqiang0812@163 (QF);Operation Analysis of a SAG Mill under Different Conditions Based on Both of these effects would allow the mill feed rate to increase and the unit power consumption (kWh/t) would decrease The concept includes sizing of the primarycrushed rock from the mine with a grizzly at a coarse size (150 to 200 mm, for example) Ore that is larger than the grizzly opening is sent to a separate stockpile as “media rock”AUTOGENOUS MILL FEED PREPARATION TO REDUCE UNIT ENERGY CONSUMPTION2013年7月15日 The ball mill in closed circuit with hydrocyclones is an industry standard, and well known methodologies exist for equipment sizing, selection and design(PDF) Energy Efficient Ball Mill Circuit – Equipment
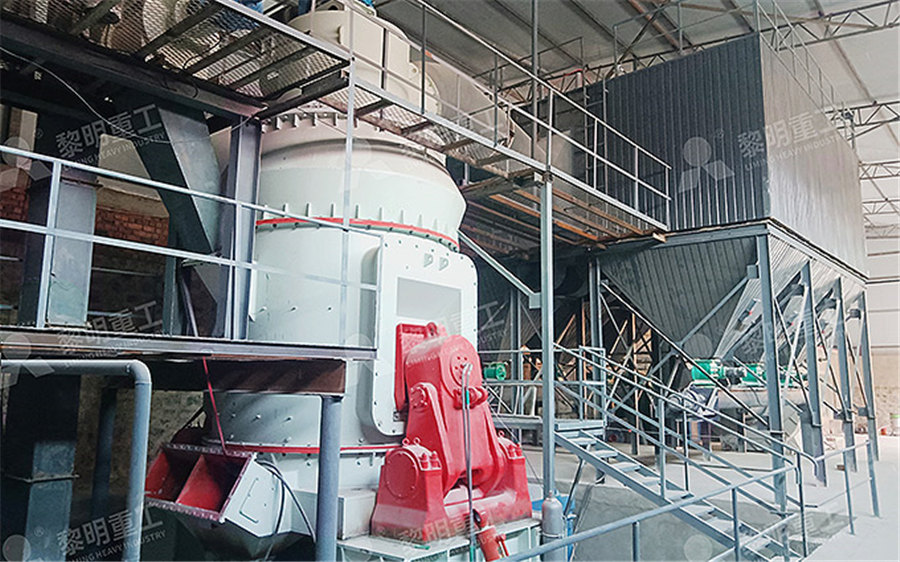
The future of SAG mills North American Mining
2024年6月5日 Improving the wear life of mill liners is one way to tackle indirect energy consumption; it also improves mill productivity as downtime for liner replacement is reduced Sam Hearn, global sales director at Multotec, 2017年7月31日 Electrical energy consumption in the milling process of white rice mill and parboiled rice mill are approximately 110 MJ/ton paddy and 134 MJ/ton paddy, respectively(PDF) Electrical Energy Consumption and Energy Conservation of Understanding Mine to Mill is presented in five parts Part A – Setting the Scene provides some definitions of Mine to Mill (M2M) and the historical background A chronology of Mine to Mill developments is followed by brief descriptions of the very wide range of Mine to Mill applications which have been implemented over the last 15 yearsUNDErsTaNDINg MINE TO MILL 911 Metallurgist2020年7月24日 In grinding processes, energy consumption is a very important profitability criterion for the applied particular size reduction technology The energy consumption of grinding is the subject of Determination of granulometrical composition of the clinker
)D`ERF`389RMI4.jpg)
Fine Grinding as Enabling Technology – The IsaMill
Mill Diameter Mill Length Installed Power Mill Volume Power Intensity (m) (m) (kW) m3 (kW/m3) Autogenous Mill 10 45 6400 353 18 Ball Mill 5 64 2600 126 21 Regrind Ball Mill 32 48 740 39 19 Tower Mill 25 25 520 12 42 IsaMill 13 3 1120 3 280 3 3) 23/m) Ball Mill Tower Mill IsaMill (m Power Intensity Media Size No Balls / m Surface Area 2014年10月20日 The ball mill is the most common ore grinding technology today, and probably more than 50% of the total world energy consumption for ore grinding is consumed in ball millsEffect of circulating load and classification efficiency on HPGR 2020年5月1日 The ball mill capacity Q is obtained from the ratio of the power of the pinion required by the ball mill to the unit power consumption of the grinding product, as shown in Eq (8) [20] The grinding kinetic formula is presented in Eq (9) [20] Eq (10) is obtained after logarithmic processing [20]Enhancing the capacity of largescale ball mill through process 2020年5月1日 The main aim of this study is to improve the processing capacity of the largescale ball mill Taking a Φ549 × 883 m ball mill as the research object, the reason for the low processing capacity of the ball mill was explored via process mineralogy, physicochemical analysis, workshop process investigation, and the power consumption methodEnhancing the capacity of largescale ball mill through process
.jpg)
Benchmarking comminution energy consumption for the
2014年10月1日 Summary of calculated percentage of mine utilised energy attributable to comminution (Ballantyne et al, 2012; DOE, 1981, 2002, 2007; Dorai, 2006; Marsden, 2008 1992年3月1日 Batch grinding parameters a T 063 min −1 γ 080 α 137 Λ 47 β 62 Φ 0 060 δ 01 a T 112 mm Table 2 Average input values for the fullscale mill and their corresponding interval ranges Optimization of the makeup ball charge in a 2023年4月23日 Comminution is a very important and resultdetermining step in mineral processing This is because further downstream processes in the beneficiation chain depend entirely on it(PDF) Grinding Media in Ball MillsA Review2016年9月1日 Furthermore, VRM separator speed (rpm) is one of the key operational parameters that determines product particle size Increasing the classi er rotor speed from 60 to 80 rpm decreases the particle Operational parameters affecting the vertical roller mill
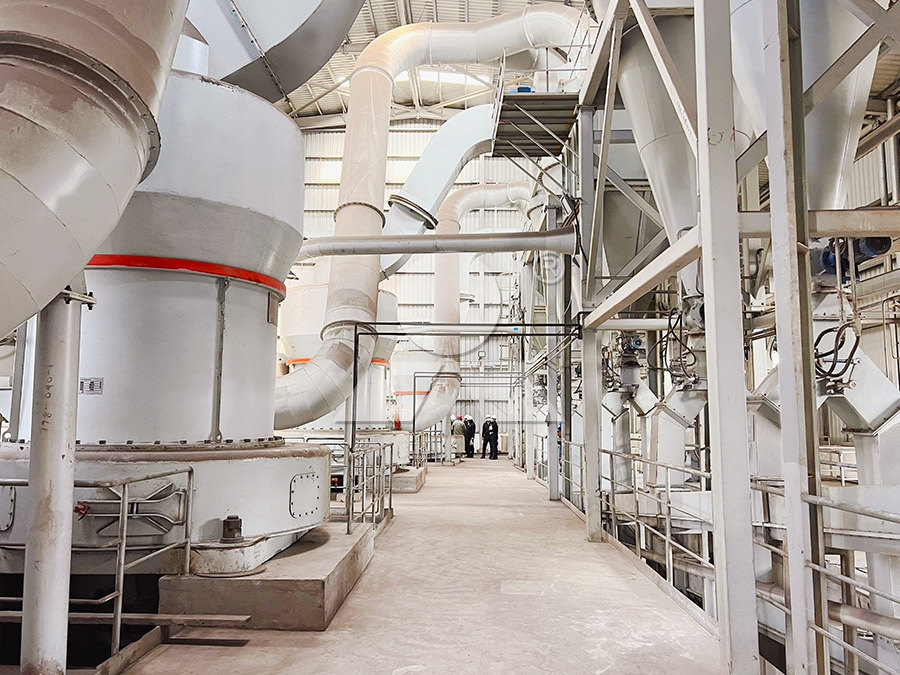
PreProcessing to Increase the Capacity of SAG Mill Circuits
2022年6月6日 This paper describes the adopted approach for increasing the capacity of an existing industrial grinding circuit by adapting the respective configuration to process the ore from a new mine Accordingly, due to Sossego mine exhaustion, Vale S A decided to use the existing industrial facilities and infrastructure for processing the Cristalino ore deposit located in Para Operating cost including iron ore, coke, energy, labour, and services, is around 415 €/ton for a conventional steel mill, and the share of a reducing agent (coal) is around 84 €/ton (Mayer et Unit costs of different iron and steel production technologies 2016年4月25日 In this study, certain measures are implemented in an existing raw mill in a cement factory and the specific energy consumption of the unit is calculated to be 2552 kWh/ton farineDetermination of correlation between specific energy consumption crusher unit, hammer shape, the size of the gap between the unit walls and the hammer edges, the feeding technique of the crusher unit, the technique of unloading the product, the screen area, the impact plate etc) have been investigated how such factors affect energy consumption in hammer mills Key words: hammer mill, specific energy FACTORS AFFECTING ENERGY CONSUMPTION IN HAMMER MILLS
.jpg)
Reducing energy consumption of a raw mill in cement industry
2012年6月1日 The cement industry one of the worst pollutant industries [4]The collection and evaluation of periodical data concerning industry and other final energy consuming sectors are primary conditions in the determination of targets for the studies on energy saving [5]Since 1970, the primary physical energy intensity for cement production has dropped by 30%, from 79 It has been recognized that the grindability of an ore in a ball mill is a function of both feed and mill parameters: is a function of mill capacity and diameter, ie,P M = Mill Constant * (Mill Diameter ) n where n = 03 to 05 Mill Power Consumption Example Ball AMIT 135: Lesson 7 Ball Mills Circuits – Mining Mill Operator 2020年7月2日 At all mill fillings, changing mill speed has the greatest influence on power consumption when the mills charge comprising 60% of small balls and 40% of big balls When the mill charge is more(PDF) Effects of Ball Size Distribution and Mill Speed and Their Several key factors need to be considered when designing a mill: 1 Mill Size and Capacity: The size and capacity of the mill depend on various factors, including the ore deposit characteristics, desired throughput, and economic considerations The mill should be sized adequately to handle the expected feed rate and accommodate future expansionUnlocking the Secrets of Gold Ore Mill: A Comprehensive Guide
.jpg)
Implementing strategies to improve mill capacity and efficiency,
BARKHUYSEN, NJ Implementing strategies to improve mill capacity and efficiency, with platinum references and case studies The 4th International Platinum Conference, Platinum in transition ‘Boom or Bust’, The Southern African Institute of Mining and Metallurgy, 2010 Implementing strategies to improve mill capacity and2016年3月21日 where R represents the ratio: % Pb in crude ore/% Cu in crude ore Formula (32) is very convenient for milling calculations on ores of this type Example: An ore contains 5% lead and 1% copper The ratio of perfect Common Basic Formulas for Mineral Processing 2012年6月1日 The industry is producing only the 20 tex and 30 tex cotton yarns It is observed from the study that the 8% of the total energy consumed by the mill has been reduced by applying different (PDF) Investigation of Specific Energy Consumption and 12 roller mill 33 42 47 52 15 roller mill 32 41 47 52 55 18 roller mill 32 40 47 53 50 60 • Wt of bagasse after each mill w = TCHxfbx1000 kg q • Assume bagasse density(d) after each mill 1200 1210 1220 1230 kg/m³MILL DESIGN MILL OPERATION
.jpg)
Energy Efficiency Analysis of Copper Ore Ball Mill Drive Systems
drive system to be overloaded when the mill filled with copper ore is started For this reason, the mill is stopped only in the case of a failure or planned maintenance work The aim is to minimize the potential number of startups, as the mill at a standstill must be later started under full load In the case of a prolonged downtime, the 2015年9月20日 Low capacity for highly c ompetent ores: When fed with extremely competent ores, havi ng JK drop we ight test values of A*b under 25, SA G mills lack the spe cific input energy t o rapidly break (PDF) FULL PRECRUSH TO SAG MILLS ResearchGateFind your ore mill easily amongst the 42 products from the leading brands (Fritsch GmbH, Retsch, Eriez, with the continuous consumption of highgrade ores, The Taskmaster® Titan® Duplex combines powerful channel grinding capability with high flow capacity and low headlossOre mill, Ore grinding mill All industrial manufacturers2012年10月19日 The production and consumption of iron ore is Capacity Volume (unit for over 50 plants worldwide on both Magnetic and Hematite ores, with a total installed capacity of over 115 (PDF) Technoeconomic Evaluation of Iron Ore Pellet
.jpg)
Comminution a Heart of Mineral Processing ResearchGate
2021年7月6日 unit mass (Drzymala, J, 2007) The capacity of comminution Ore deposit is the gathering of ore where ore is defined as a rock or sediment unit or the dry ball mill at essentially the same