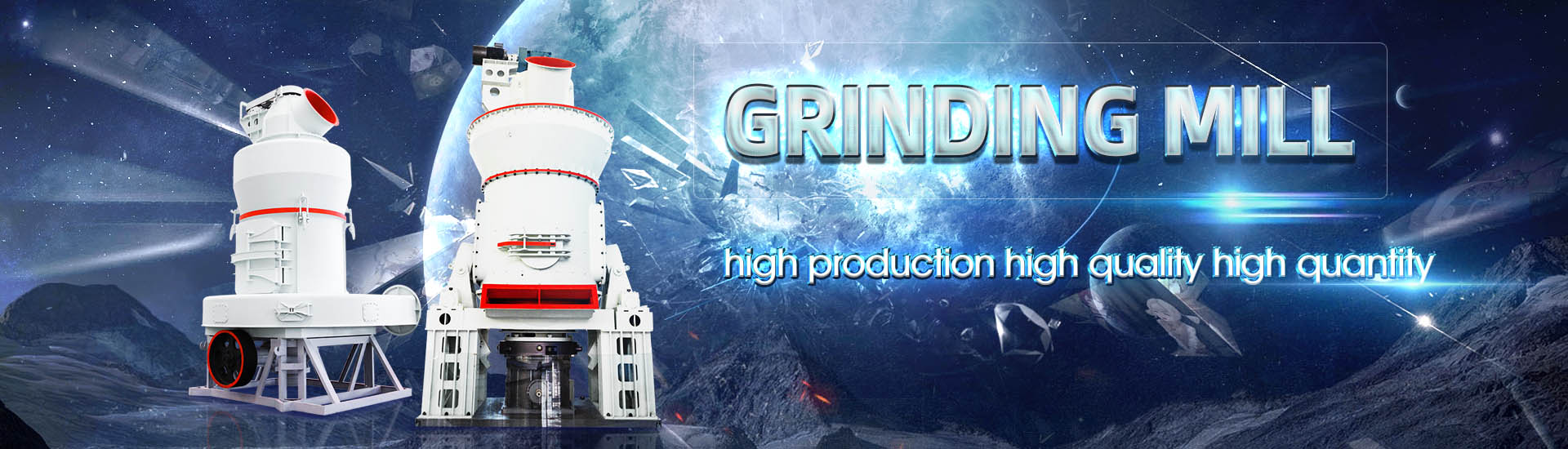
Which ore mill is good for cement
.jpg)
3 Necessary Cement Milling Comparison
Before the invention of the cement ball mill, cement grinding is completed by cement crushers, which has disadvantages of complicated process, pollution, and more area occupied Cement ball mill started in the 1960s, after the ball mill has been enlarged, the conditions have been created for reducing construction investment 展开2019年8月20日 Common examples of sedimentary rocks include limestone, sandstone, coal, iron ore, etc These rocks are the most relevant ones for cement manufacture Metamorphic rocks are derived from previously formed rocks of Basics of mineral resources for cement productionCement ball mill and cement vertical mill are two raw mills commonly used in cement plants As the main cement equipment in the cement production line, the two cement raw mills have different characteristicsRaw Mill – Raw Mill In Cement Plant AGICO Cement For cement raw material preparation, our renowned raw mills with the proven MVR technology are perfectly suited and always adapted to the customer's particular requirementsRaw mills for all requirements Gebr Pfeiffer
.jpg)
How cement is made Heidelberg Materials
The desired raw mix of crushed raw material and the additional components required for the type of cement, eg silica sand and iron ore, is prepared using metering devices Roller grinding mills and ball mills grind the mixture to a fine 2024年8月20日 5 Iron Ore Iron ore contains 30–70% iron oxides like hematite (Fe₂O₃) and magnetite (Fe₃O₄) It gives color and strength to the final product of cement The iron ore is like a rock or mineral from which the iron can be easily Understanding the Raw Materials for Manufacturing Iron Ore: It is used to add iron oxide to the mix to enrich the cement’s colour while contributing to the fusion of raw materials for cement production and the strength of the final product Gypsum: It regulates the cement’s setting timeExplore Raw Material Used For Cement Production JK 2023年1月1日 The utilization of coal in the cement and concrete industries takes three basic forms: (1) as a fuel in the production of cement clinker; (2) ash produced by burning coal in Coal utilization in the cement and concrete industries
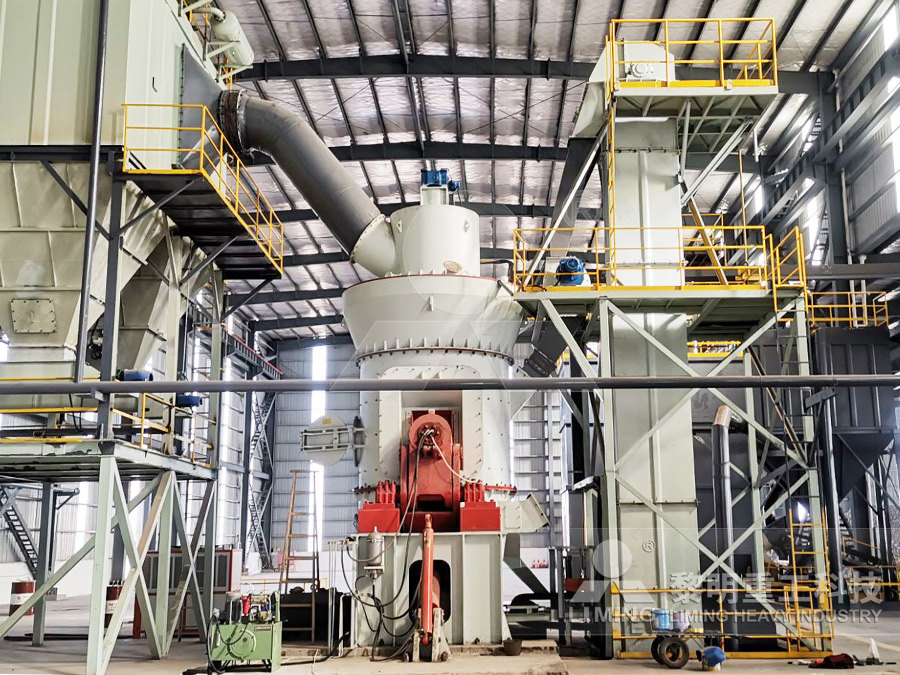
From raw materials to cement
components required for the type of cement, eg silica sand and iron ore, is prepared using metering devices Roller grinding mills and ball mills grind the mixture to a fine powder at the 5) Portland Slag Cement Grade Cement Portland Slag Cement (PSC) is created by blending OPC clinker with granulated blast furnace slag, a process that enhances cement in terms of strength, durability, and workability One notable advantage of PSC is its reduced heat of hydration, allowing for the execution of largescale concrete pours6 Types of Cement Grades Grades and Uses Explained UltraTech CementStage of Cement Manufacture There are six main stages of the cement manufacturing process Stage 1: Raw Material Extraction/Quarry The raw cement ingredients needed for cement production are limestone (calcium), sand and clay (silicon, aluminum, iron), shale, fly ash, mill scale, and bauxite The ore rocks are quarried and crushed into smaller pieces of about 6 inchesHow Cement is Made Cement Manufacturing ProcessLime Component Limestone: Common forms of calcium carbonate used as raw material for cement manufacturing are limestone and chalkLimestone is of predominantly fine grained crystalline structure, its hardness is between 18 to 30 of the Mohs scale of hardness and specific gravity 2 To 28 Limestone usually contains admixtures of clay substance or iron compounds, Raw materials for cement manufacturing Cement Plant
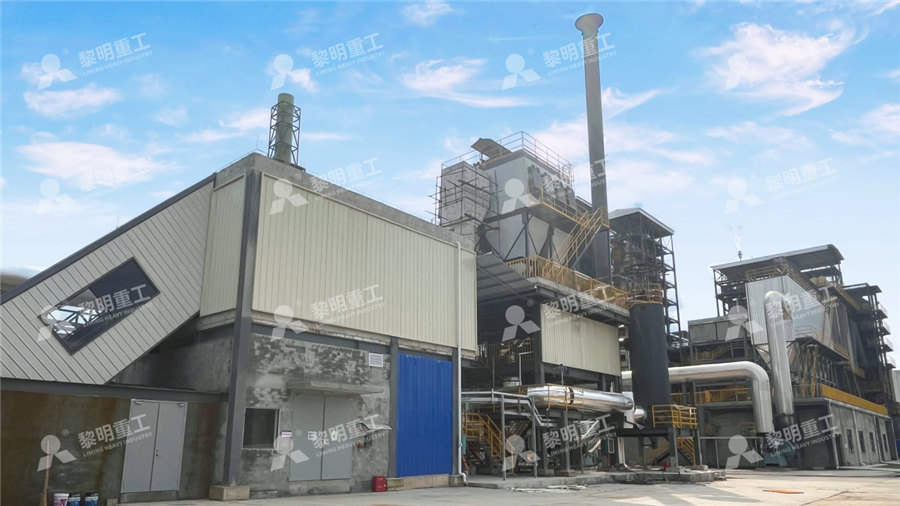
How to Make Cement From BlastFurnace Slag 911Metallurgist
2017年4月23日 Slag cements fall below highgrade Portland cements in tensile strength, but good American slag cement develops sufficient strength to pass many American specifications for Portland cement Tested neat, they do not approach Portland cements so nearly as tested in 2 to 1 and 3 to 1 mortarsOther materials used to manufacture cement include: shells, chalk, shale, slate, silica sand, iron ore, and blast furnace slag The Cement Manufacturing Process While each cement plant may differ in layout, equipment, and appearance, the general process of manufacturing portland cement is the same: crushed limestone and sand are mixed with ground clay, shale, iron ore, How Cement is Made Portland Cement AssociationA cement mill (or finish mill in North American usage [1]) is the equipment used to grind the hard, nodular clinker from the cement kiln into the fine grey powder that is cement Most cement is currently ground in ball mills and also vertical roller mills which are more effective than ball millsCement mill WikipediaProcess Training Ball Mill To Download this post + all manuals and books and Excel sheets and all notes I collected over my 23 years of experience in Cement industry click here now INTRODUCTION Comminution is a major unit operation in a cement plant, accounting for about 50 75 % of the total plant energy consumptionProcess Training Ball Mill INFINITY FOR CEMENT EQUIPMENT
R)8OC`6F[ZIB.jpg)
Everything you need to know about Blended Cements
Blended cement (center) surrounded by (bottom and clockwise) portland cement, fly ash, blastfurnace slag, silica fume, calcined (burnt) clay, “Operating Experience With the Production of Slag Cements in a Roller Mill,” ZementKalkGips, 52(3), pages 136146, 19996 The mill hot air inlet temperature should not exceed 315°C on systems using ambient air 7 The mill outlet temperature should not exceed 95°C on direct fired systems; the maximum outlet temperature on indirect systems is generally lower than that for direct fired systems using the same solid fuel 8 If a fire occurs in the mill:Everything you need to know about Kiln System Operations in Cement 2023年5月27日 Then feed the mixture into a cement mill for fine grinding Portlandlimestone cement (PLC) Type IL is governed by ASTM C595 or AASHTO M 240 Standard Specification for Blended Hydraulic Cements It is a blended cement manufactured with a limestone content between 5% and 15% Necessary matters about limestone grinding Conclusion2 Major Roles of Limestone in Cement Manufacturing2013年2月26日 However, topping up the mill with additional media is a simple task and most cement manufacturers will regrade their cement mill media on an annual basis The other major repairs that take place on ball mills are to replace the liners and diaphragms and on a VRM to replace (or turn) the rollers and replace the paring ball mills and VRMS for cement grinding
.jpg)
Ball Mill For Cement Grinding – Cement Ball Mill Ball
Ball mill for cement grinding is a kind of important cement equipment in cement plants IRON ORE PELLETIZING Pelletizing Disc Annular Cooler Grate Kiln Damp Mill Rotary Drum Mixer Iron Ore Dryer Traveling Grate CONTACT An overview is given of the principal types and materials of construction of mill liners Examples of good and bad liner design are given, economically unbeatable for highly abrasive ores in small to medium size mills (Powell 1991b) They are light in weight and make use of the grinding media hardness to provide anThe Selection and Design of Mill Liners 911 MetallurgistMill production is determined by the grinding power available and feed grindability, but for high moisture feed, the system drying capacity may bethe limitingfactorTypically,thetarget moisturelevel exmill is below one per cent to assure good flowability of Raw milling and blending INFINITY FOR CEMENT EQUIPMENTMill capacity decreases as the demand in fineness increases Mill Air flow : Normally Flow across Mill is kept as 2 to 30 m/sec for raw materials grinding 1 to 15 m/sec for close circuit of cement grinding 1 to 12 m/sec for open circuit of cement grindingNotes on Tube mills INFINITY FOR CEMENT EQUIPMENT
.jpg)
Cement Mill Optimization: Practical Strategies for Enhanced
Adjusting mill parameters: Finetuning mill parameters such as mill speed, ball charge, filling ratio, and grinding media size can have a substantial impact on the grinding efficiency of the mill For example, a 10% increase in mill speed can result in up to 10% higher production rate, while optimizing the ball charge can lead to a 510% reduction in energy consumption2021年5月24日 When clinker cooler air is used for coal mill heating, the fine carryover dust can add large amounts of inert ‘ash’ to the ground coal This can interfere with combustion and limit kiln output The abrasive dust also accelerates equipment wear and makes burner pipe and snowmen buildups more likelyBetter and cheaper cement: Optimising the right clinker propertiesThe choice between a vertical roller mill and a ball mill for cement grinding ultimately depends on the specific needs and constraints of the cement plant VRMs offer significant energy savings, finer product control, and reduced maintenance costs, making them an attractive option for modern cement plants focused on efficiency and sustainabilityVertical roller mill vs ball mill for cement grinding: Comparison Suited mainly for Portland cement and with limitations for composite cement; the ground and dried additive is fed to the tube mill or mill outlet In the first stage (press with separator) the cement is ground 1’000 – 1’500 [cm2/g] below desired product fineness and in CEMENT GRINDING SYSTEMS INFINITY FOR CEMENT EQUIPMENT
.jpg)
Coal utilization in the cement and concrete industries
2023年1月1日 The utilization of coal in the cement and concrete industries takes three basic forms: (1) as a fuel in the production of cement clinker; (2) ash produced by burning coal in power stations is used as a component in cement rotary kiln feeds; (3) ash produced by burning coal in power stations is used as a mineral additive in concrete mixesBall race mill (Petersmill of the Claudius Peters Joint Stock Company, Hamburg, Germany) The cement industry employs the Petersmill (pre viously called FullerPetersmill) mostly for coal grinding It is a few years now that the shockproof Roller mills INFINITY FOR CEMENT EQUIPMENT2024年9月5日 Tricalcium silicate (C₃S): this compound gives strength to the cement and hardening properties Dicalcium silicate (C₂S): Strengthens cement hardening over time (C₃A) Tricalcium aluminate: regulates cement setting A Comprehensive Guide to the Cement Manufacturing Cement manufacturing brief description of a cement mill Cement clinker is usually ground using a ball mill This is essentially a large rotating drum containing grinding media normally steel balls As the drum rotates, the The cement mill

Process technology for efficient and sustainable cement production
2015年12月1日 The reason for the very limited additional potential savings of thermal energy is the necessary heat for the clinker production process Fig 1 shows the heat flows, the thermal input, the use for clinkering and drying, and the remaining waste heat flows that might be utilised However, the remaining waste heat is already used to a high degree, indicated by the already 2022年7月1日 The bulk of the cement industry's environmental burden is from the calcareous source Calcium is mostly available naturally as limestone (CaCO 3), where almost half of the mass is eventually released as CO 2 during clinker manufacture Iron (Fe) is the fourth most common element in the Earth's crust surpassed only by oxygen, silicon, and aluminium; Sustainable ironrich cements: Raw material sources and binder Cement ball mill and cement vertical mill are two raw mills commonly used in cement plants IRON ORE PELLETIZING Pelletizing Disc Annular Cooler Grate Kiln Damp Mill Rotary Drum Mixer Iron Ore Dryer Traveling Grate CONTACT US : info@cementplantequipment PHONE: +86 Raw Mill – Raw Mill In Cement Plant AGICO Cement Raw MillFor a cement mill: intermediate or outlet diaphragm For the case of; cement mills with a drying chamber see raw mills Mill working conditions: ventilation air speed through the mill Bigger or smaller than 12 [m/s] Material abrasivity The [%] of slag or pouzzolana content on the fresh mill feed for cement grindingEverything you need to know about clinker/cement Grinding
.jpg)
Understanding the Raw Materials for Manufacturing Cement
2024年8月20日 Step 4: Cement grinding and storageThe cooled clinker with gypsum is finely ground in a cement mill to form the hard cement This contributes to 05–6% of the cement raw material The iron ore helps lower the melting temperature of the raw mix 6 Gypsum Gypsum contains 70–90% calcium sulfate dihydrate The vertical roller mill (VRM) is a type of grinding machine for raw material processing and cement grinding in the cement manufacturing processIn recent years, the VRM cement mill has been equipped in more and more cement plants around the world because of its features like high energy efficiency, low pollutant generation, small floor area, etc The VRM cement mill has a Vertical Roller Mill Operation in Cement PlantMECHANICAL ELEMENTS OF TUBE MILLS this is a part of ASEC Academy training Courses SUMMARY the mechanical elements of a tube mill could be separated into elements which have a direct function with the grinding process (ie grinding media, liners, diaphragms) and into elements which can be considered as individual units which are connected to each other to a MECHANICAL ELEMENTS INFINITY FOR CEMENT EQUIPMENTThis is done by a mixture of both aircooling and watercooling, including spraying water inside the mill Cement milling and gypsum dehydration Because the cement gets hot due to the heat generated by grinding, gypsum can be partly Cement Milling
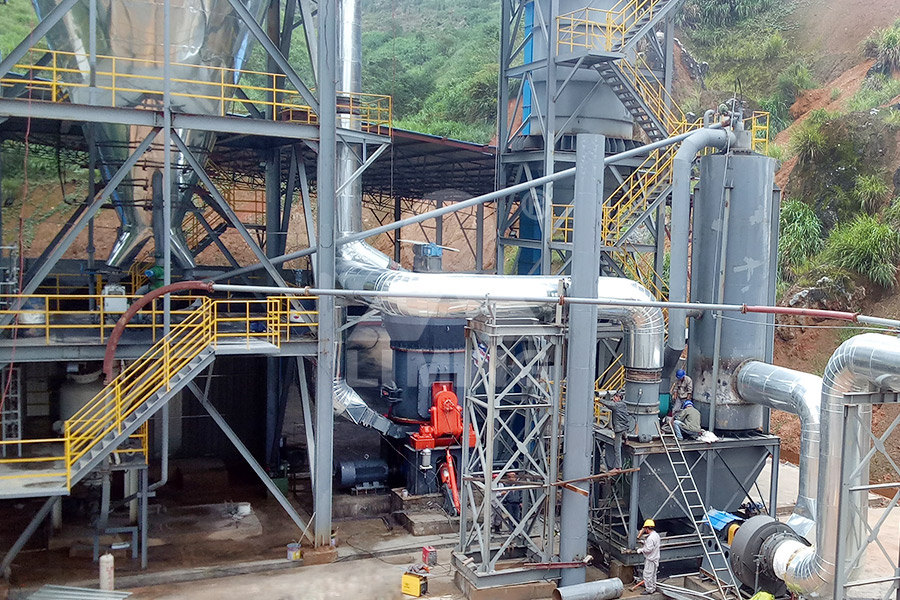
Cement Mill for Sale Buy Cement Ball Mill Vertical
Cement mills are the milling machines used in cement plants to grind hard clinker into fine cement powders Cement ball mill and vertical roller mill are two most widely used cement mills in today’s cement grinding plants and are also the Learn about the raw mill in cement plants and the basic raw materials used in cement manufacturing Discover our efficient cement manufacturing process Contact us for more info! Amrit Support About Amrit Support; Services; Raw Mill in Cement Plant Cement Manufacturing Varieties of cement is prepared by mixing clinker with the other requisite materials in the cement mill For example, clinker and gypsum are mixed for Ordinary Portland Cement, fly ash for Portland Pozzolana Cement, and slag for slag cement These are extracted from their respective hoppers and fed to the cement millsMaking of Cement CMA IndiaCoal mill is the main equipment in the pulverized coal preparation processBecause calcining topgrade cement clinker requires a stable supply of coal powder as the fuel of cement kiln, and more than 85% of pulverized coal should be finer than 200 mesh, water content less than 2%, and calorific value more than 6000Kcal/kg, therefore the pulverized coal preparation system is one Cement Mill Cement Grinding Machine AGICO Cement Grinding Mill
.jpg)
Which Cement Is Best For House Construction?Best Cement For
Several cement brands offer different types of cement in the market, which generally confuses the buyer to choose the best one for their house Today in this article, we will discuss which cement is best for house construction and which brand of cement should you use for constructing your dream house Commonly Used Cement In India Two types of cement are most commonly 2023年1月29日 In a cement mill, the clinker, gypsum, and other additives are ground into a fine powder which is then mixed into a slurry surrounded by rotating rollers This slurry is discharged through an opening at the bottom of the mill where it is collected in silos or tanks before being sent to a kiln for further processingWhat Is Cement Milling? Difference Between Raw Mill And Cement MillIn cement plants, proper specification and supply of AC induction motors is critical to project schedules and providing efficient production This paper focuses on the selection of AC induction motors for cement mill applications, with reference to fan, kiln and vertical mill applications The criteria for motor selection includes:Selection of AC Induction Motors for Cement Plant ApplicationsBall mill is the cement crushing equipment in the cement plant Compared with open circuit ball mill, the closedcircuit ball mill has high efficiency, high output, low cement temperature, and good comprehensive benefit It is the best choice for a cement plant Skip to IRON ORE PELLETIZING Pelletizing Disc Annular Cooler Grate Kiln Ball Mill In Cement Plant Cement Ball Mill AGICO Cement
.jpg)
Drying of raw materials INFINITY FOR CEMENT EQUIPMENT
The PolysiusAerofallmill as a dryinggrinding plant The PolysiusAerofallmill which is predominantly used for autogenous grinding in the preparation or ores, is now increasingly employed in the cement industry, particularly for dryinggrinding of cement raw material The PolysiusAerofallmill is a short tube mill with a large diameter