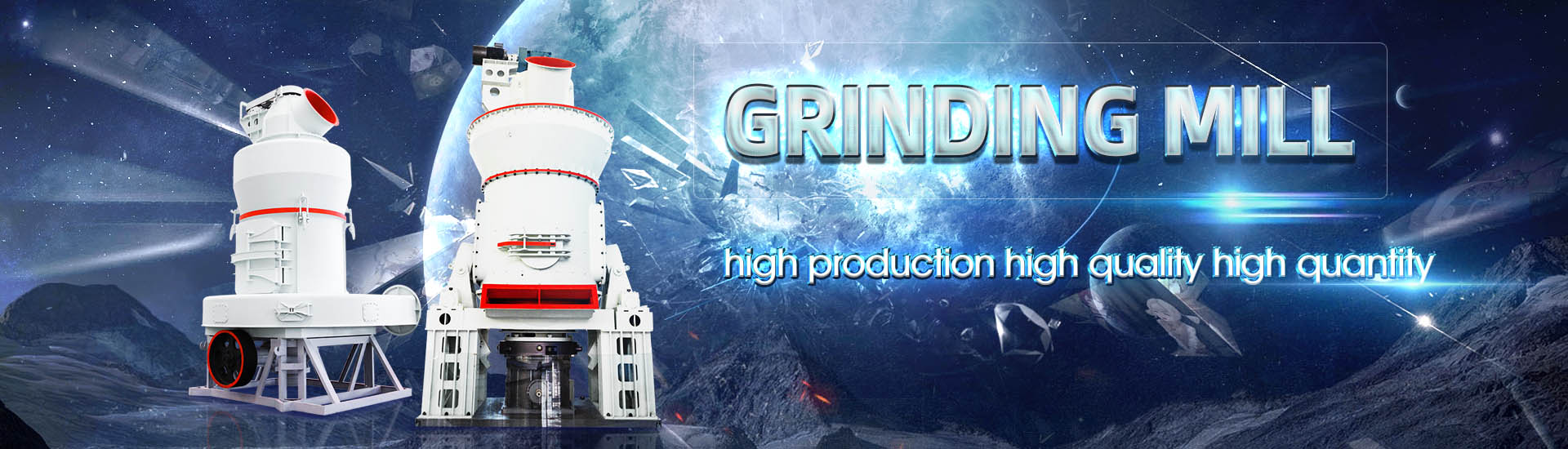
The quality of secondary ore mills in quicklime coal plants
.jpg)
Efforts to Improve the Quality of Quicklime in Handling
2023年11月2日 Utilizing Pareto and Ishikawa diagrams to discern the root causes and subsequently validating these findings through linear regression, the research assessed Quicklime's efficacy in the process2024年2月27日 The results show that from a quicklime quality perspective, with respect to CaO (s), limestone should be processed below a maximum temperature of 1300 °C, which likely corresponds well to many current lime Impact of Limestone Surface Impurities on Quicklime Experimental research and practice show that quicklime powder is an essential additive in sintering production And high active quicklime powder can significantly improve the output The Influence Analysis of Quicklime Quality on Output and Quality 2022年10月1日 In this review, the current state of the lime industry and its processing configurations is visualised This is followed by a detailed description of the current status of Decarbonising the lime industry: Stateoftheart ScienceDirect
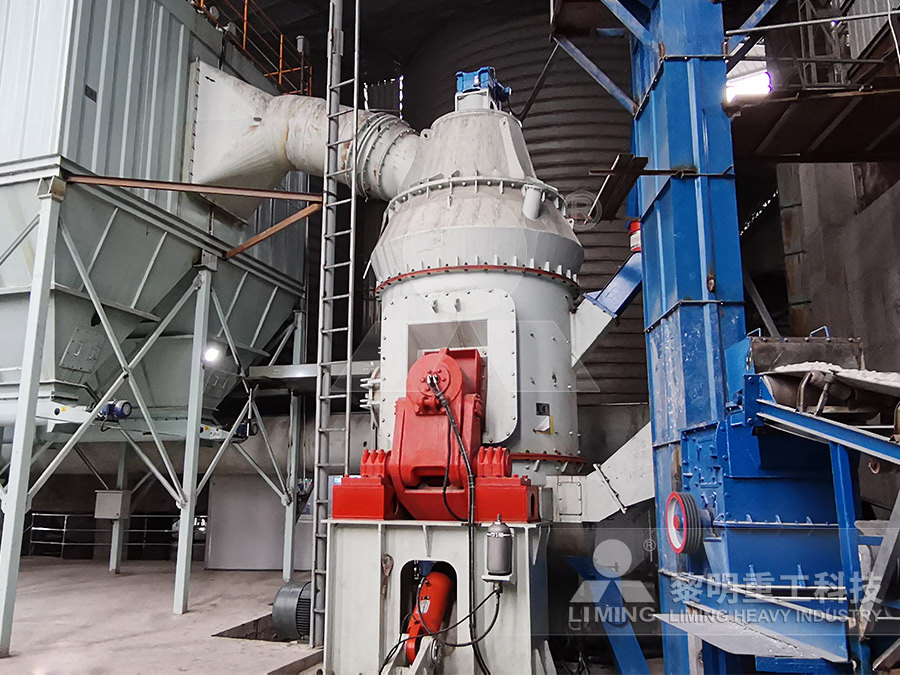
CFD Analysis of Cofiring of Coke and Biomass in a Parallel Flow
2022年6月24日 In this paper, a numerical tool is presented, which simulates a largescale Parallel Flow Regenerative (PFR) kiln that currently uses coke as main fuel The developed The primary objective of this study was to understand how ore loss and dilution affect the MCF and to subsequently improve the quality of ore mined and fed to the mill On the basis of this Monitoring ore loss and dilution for minetomill integration in The high moisture and viscosity characteristics of oily cold rolling mill (CRM) sludge led to limitations in its recycling In this paper, the results of using quicklime as a conditioning agent Enhancing the Dewaterability of Oily Cold Rolling Mill Sludge The quality of quicklime is affected by several factors related to the limestone feed and the calcination process These include the chemical composition and crystalline structure of the Factors Affecting The Quality of Quicklime
.jpg)
Oily cold rolling mill sludge conditioned by quicklime to improve
2023年7月20日 Dewatering is critical to oily cold rolling mill (CRM) sludge treatment Therefore, finding an efficient, energysaving, and applicable dewatering technology for oily CRM sludge The 6th International Seminar on Business, Economics, Social Science, and Technology (ISBEST) 2023 eISSN 29870461 Vol 3 (2023) 254 PT TCM, a coal mining company in East Kalimantan, Indonesia EFFORTS TO IMPROVE THE QUALITY OF QUICKLIME IN 2006年4月1日 Conventional floatsink testing is considered the standard test method for generating coal washability data (Temel, Majumder, and Bakır 2015, Galvin 2006, Callen et al 2002, Callen et al 2008 (PDF) Coal preparation plant optimization: A critical 2012年11月17日 20 131Fineness Fineness is an indicator of the quality of the pulverizer action Specifically, fineness is a measurement of the percentage of a coal sample that passes through a set of test sieves usually designated at 50, Coal mill pulverizer in thermal power plants PPT
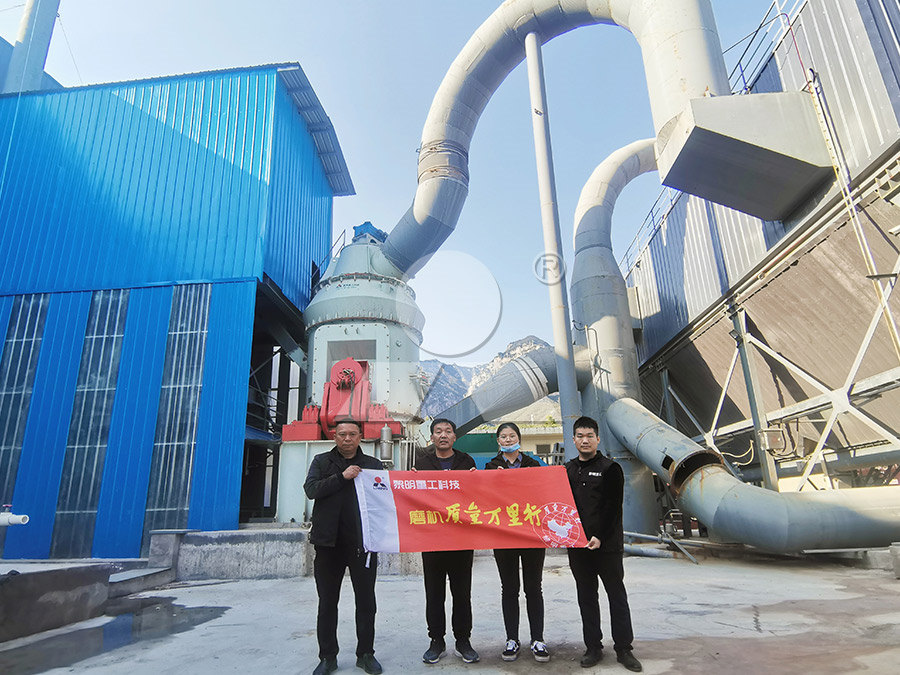
The Effect of Calcination Temperature on The Quality of Quicklime
2022年2月28日 The industrially produced quicklime showed intrusion by extraneous elements, mainly Al and Si, up to 800 µm into the quicklime, in accordance with expected ash composition, based on the ash 2016年3月30日 In book: Encyclopedia of Iron, Steel, and Their Alloys (pppp 10821108) Chapter: i) Direct Reduced Iron: Production; Publisher: CRC Press, Taylor and Francis Group, New York(PDF) i) Direct Reduced Iron: Production ResearchGateTHE EFFECTS OF IMPURITIES ON LIME QUALITY “Lime” is a very general term used to describe virtually all finely divided types of limestone and burned forms of lime However, by definition, lime is only calcined limestone known as quicklime, calcium oxide, and a secondary product namely hydrated lime (calcium hydroxide) orTHE EFFECTS OF IMPURITIES ON LIME QUALITY Penta 2020年8月12日 As the significant ancillary equipment of coalfired power plants, coal mills are the key to ensuring the steady operation of boilers In this study, a fault diagnosis model was proposed on the An investigation of performance characteristics and energetic
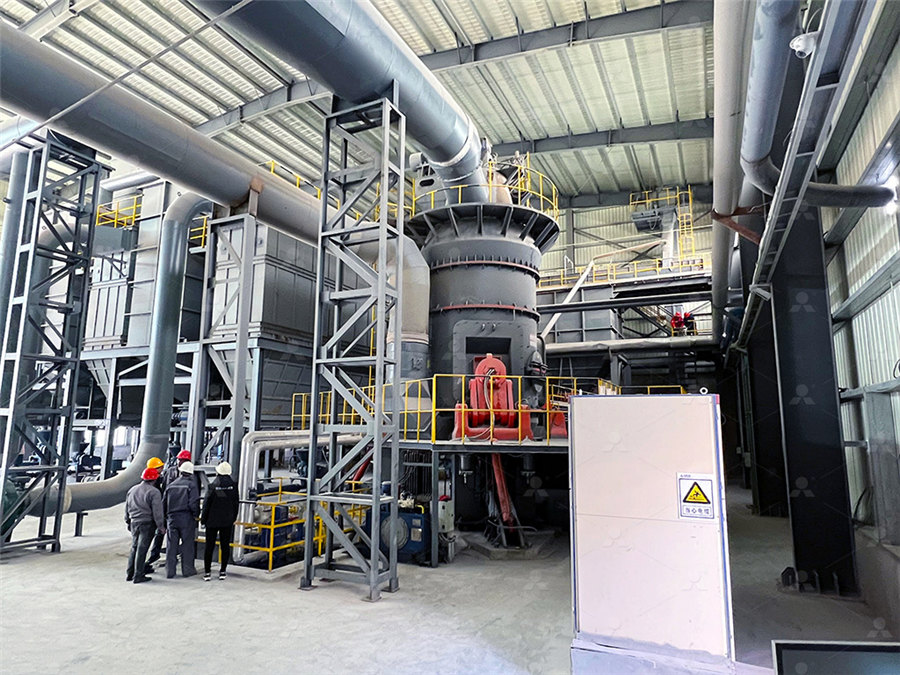
(PDF) Utilising of the oiled rolling mills scale in iron ore sintering
2013 Sintering is a process by which a mixture of iron ores, fl uxes and coke is agglomerated in a sinter plant to manufacture a sinter product of a suitable composition, quality and granulometry to be used as burden material in the blast furnacecoal (36%) followed by different types of waste (10%), fuel oil (7%), lignite (6%) and gas (2%) In 1995 there were 252 installations producing cement clinker and finished cement in the European Union and a total of 437 kilns, but not all of them in operation In addition there were a further 68 grinding plants (mills) without kilnsIntegrated Pollution Prevention and Control (IPPC) Reference2021年3月31日 3 COAL QUALITY –IMPACT COMPLEX • Pulverizer capacity, fineness wear • Slagging fouling in boiler • Corrosion erosion in boiler • Ash characteristics affect efficient collection in ESP • Affects furnace convective pass heat absorption boiler availability • Quantification of impact is complex 31Mar2021 total output power solutions 3Effect of Coal Quality and Performance of Coal pulverisers / MillsRaw Material Handling Plant VSP annually requires quality raw materials viz Iron Ore, fluxes (Lime stone, Dolomite), coking and non coking coals etc to the tune of 1213 Million Tonnes for producing 3 Million Tonnes of Liquid Steel To handle such a large volume of incoming raw materials received from differentFUNCTIONS OF VARIOUS DEPARTMENTS OF RINL/VSP
.jpg)
IT IS QUALITY THAT MATTERS TO US RATHER THAN
We execute lime Processing plant manufacturers and suppliers including hydrated lime plants, quick lime plants, primary secondary crushers and other conveying/loading systems We have supplied more than 200 ball mills 2013年7月20日 The ore deposits obtained from Dunoka, Amankwo and Umuakpo in Lejja Nsukka were found to be iron silicate in nature They were analysedby XRD, XRF, AAS and the ores were found to contain 6059% Fe The Challenge of Domestic Iron and Steel 2024年3月31日 Pregrobbing is a phenomenon in which minerals retain gold, especially due to the presence of species like carbonaceous matter and silicates in the mineral This study demonstrates the impact of quicklime, used to adjust the pH of a gold cyanidation solution, on the retention of gold contained in pregnant cyanidation solutions and sorption mechanismsStudy of PregRobbing with Quicklime in Gold Cyanide Solutions silica from bauxite ore and for causticization in the manufacturing of alumina Dolomitic quicklime is used to produce metallic magnesium by thermal reduction which reduces magnesium oxide Lime is also used in the processing of ores and the subsequent smelting and refining of copper, zinc, lead, and other nonferrous ores EnvironmentalQUICK LIME AND BYPRODUCTS PEC Consulting Group
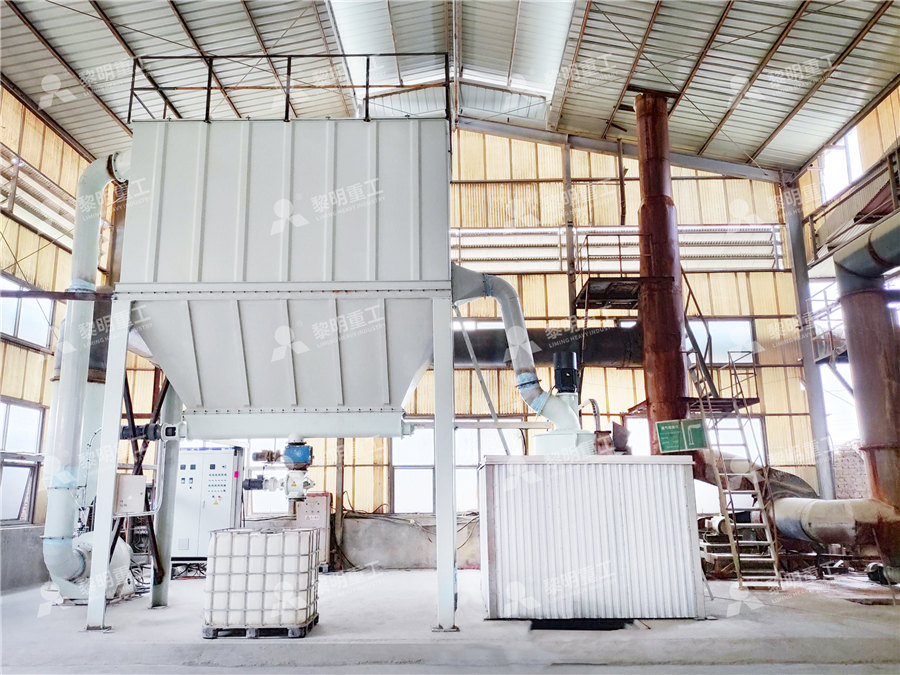
Lime Plant Graymont
Secondary menu Customer Portal; Main menu Products Chemical the Bedford plant remains a quality supplier of pulverized limestone used in roof shingles, fertilizers, animal feed, agricultural liming and the glass industry highcalcium hydrated lime, dolomitic quicklime and PCC quicklimeThe newest addition to the plant is kiln #5, In modern thermal power plants coal grinding mills are an important and very frequent subsystem As time passes the grinders in the mills become depleted and the functionality of these mills decreases Because of that the mills need to be stopped periodically, every 1500 hours, so they can be checked and, if necessary, repaired During this maintenance check the production of ANALYSIS OF THE CONDITION OF COAL GRINDING MILLS IN In the case of lump ore, this increases to 18 to 2 tonnes of lump ore Apart from this effect of pellets and lump ore on coal consumption, the quality of coal also plays an important role When a mix of imported and domestic coal is used with lump ore, consumption ranges from 14 tonnes/tDRI to 16 tonnes/tDRIHow can India Decarbonise Coalbased DRI Plants in Steel Making?2022年11月1日 Pulverizedcoal combustion is the most widely used means of burning coal A century ago, the Keystone Coal Catalog (1922, p 231; later the Keystone Coal Industry Manual) could say that “ the quality of coal is not of great importance” Now it is universally acknowledged that coal quality is of prime importance in the modern coal industryUnderstanding coal quality and the critical importance of
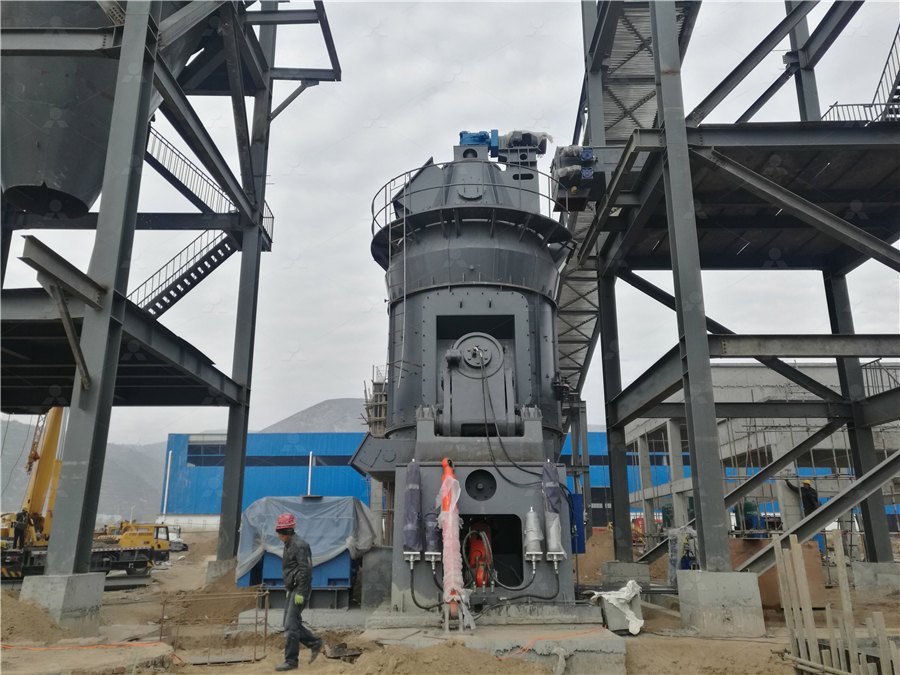
Coal ash and limestone interactions in quicklime production
2021年9月1日 This paper reports on results from detailed studies on coal ash and limestone interactions during calcination Industrially produced quicklime from a coalfired rotary kiln was analyzed and 2011年1月1日 The effects of ore type and bed depth on sinter production and quality, in Proceedings Iron Ore 2007 Conference, pp 301309 (The Australasian Institute of Mining and Metallurgy: Melbourne) Show Calculating the value of iron ores in ironmaking 2014年12月23日 Coal washing plants also use lime to neutralize the acidic waste or process water to reduce corrosion on steel equipment and to recover the water for reuse The quality of lime is dependent on the calcination method, the fuel used for calcination, type of limestone, and weather conditionsLime and Calcined Dolomite for Use in Steel Plant IspatGuru2023年8月22日 Industrial emissions, in particular from energy intensive sectors, have been identified as key sources of greenhouse gas (GHG) and particulate matter (PM) emissions, which both represent the two Global sitespecific health impacts of fossil energy, steel mills, oil
.jpg)
Fact sheet Energy use in the steel industry
than the production of secondary steel using scrap (see Figure 2) due to the chemical energy required to reduce iron ore to iron using carbonbased reducing agents Because reduction does not take place at room temperature, reducing agents such as coal, coke and natural gas also supply energy for the heat needed2014年10月20日 PDF At the regrind or secondary grinding stages of metal ores, Regrind of metallic ores with vertical mills: An overview of the existing plants in Brazil October 2014;Regrind of metallic ores with vertical mills: An overview of the 2023年4月23日 A comparison of the grinding media is given together with the knowledge gaps that still need to be bridged to improve the quality and performance of grinding media used in ball mills(PDF) Grinding Media in Ball MillsA Review ResearchGate2018年8月17日 The concept of ore blending is a very relevant notion in modern high tonnage production mines It is not only essential for the prolongation of the mine life of the concerned mine but as well as a The effects of ore blending on comminution behaviour and
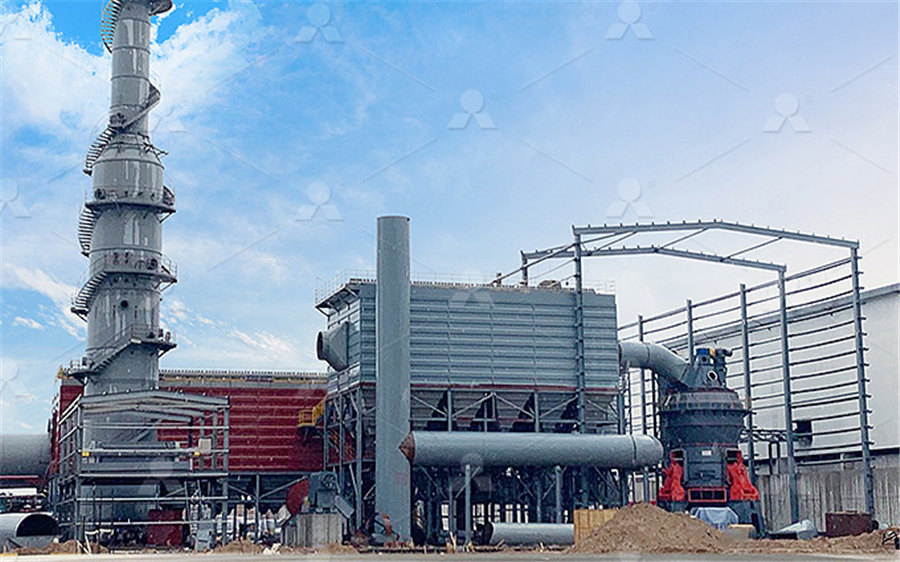
Mineral Beneficiation and Processing of Coal SpringerLink
2021年5月11日 The modernday coal processing plants can be categorized into four different circuits, depending upon the size of the coal particles to be treated: (a) coarse coal processing circuit treating particles coarser than 10 mm, (b) small coal circuit for washing particles in the size range of 110 mm, (c) fine coal circuit for cleaning particles in size range of 015–1 mm, and 2023年1月1日 Secondary raw materials (materials in the kiln “raw feed” other than limestone) depend on the purity of the limestone Some of the second raw materials used are clay, shale, sand, iron ore, bauxite, fly ash, and slag Coal used to fire the rotary kiln should also be considered a secondary raw material as it contributes its ash to the mixCoal utilization in the cement and concrete industriesSinter plants account for more than 10, 40 and 70% of the total emission of CO2, NO and SO2 in steelworks, respectively It is necessary to reduce the fuel ratio in the sinter mix to decrease the Characterization of the studied iron ores with TG analysis Basic 2015年4月1日 Lime is one of the most versatile chemicals in the world with numerous industrial, environmental and chemical uses It is a white alkaline substance consisting of calcium oxide (CaO), which is obtained by heating limestone; it is also used in the production of hydrated lime [Ca(OH) 2]Due to its different geological origins and the various circumstances surrounding its Lime in the limelight ScienceDirect
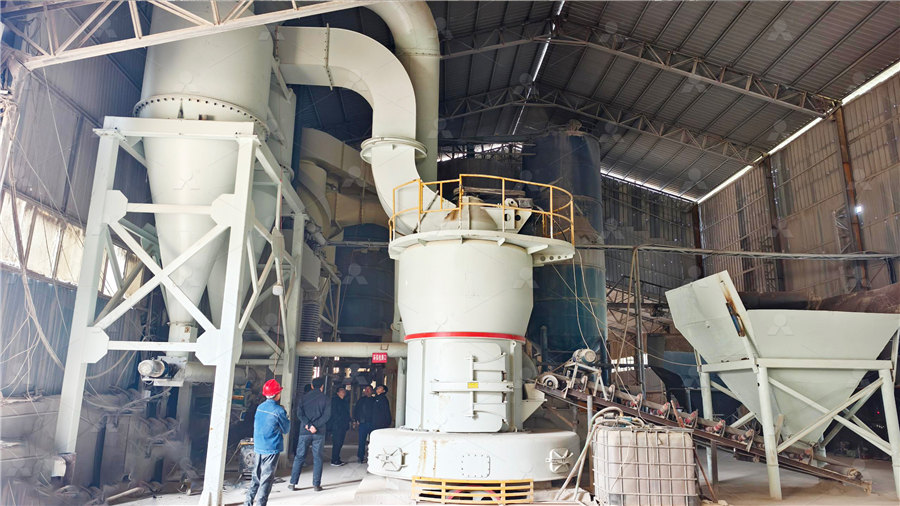
Scrap use in the steel industry
consumption of 14 tonnes of iron ore, 740kg of coal and 120 kg of limestone3 How much scrap is used? All the scrap that is available to the steel industry is used repeatedly to create new steel Recycled steel maintains the inherent properties of the original steel and the quality can also be improved on recycling2021年11月4日 Test methods for grindability and abrasion testing: Full scale ring and ball mill, Hardgrove mill [30,31], BCURAroll mill, Rotating electrode ball wear tester [32], Dropweight test machine [28 Technique to Investigate Pulverizing and Abrasive Performance of Coals Download Table Limestone and the resulting quicklime chemical analysis after calcination in a kiln from publication: Management of Lime in Steel The EU28 total lime demand in 2017 was Limestone and the resulting quicklime chemical analysis after %PDF16 %âãÏÓ 4215 0 obj > endobj 4235 0 obj >/Encrypt 4216 0 R/Filter/FlateDecode/ID[87C03FABF6FB2246BC4F9AB649B4B217>]/Index[4215 26]/Info 4214 0 R/Length 101 AusIMM – Leading the way for people in resources

The Complete Guide to Primary Crushing, Secondary Crushing,
2023年2月28日 Learn everything you need to know about primary crushing, secondary crushing, and tertiary crushing in this comprehensive guide Discover the types of crushers used in each stage, their working principles, and the advantages and disadvantages of each process Get answers to frequently asked questions and improve your understanding of the comminution irrespective of limitations in the availability and quality of iron ore and coking coal In India, the average primary specific energy consumption (SEC) from selected major steel plants was 273 GJ/tcs The globally, the Best Available Technology (BAT) has a benchmark of primary SEC ofA Study of Energy Efficiency in the Indian Iron and Steel IndustryHence, efficiency ore management mine necessitates the need to measure accurately, firstly the fragment size distribution, then ore loss and dilution, and thereafter track ore movement after blasting from the stope face to the concentration plantMonitoring ore loss and dilution for minetomill integration in 2015年1月1日 Iron ore sintering is a material preparation process employed worldwide in the production of iron and steel According to statistical data on pollution, sintering plants rank second in terms of toxic emissions, after the incineration of municipal solid waste (Menad et al, 2006, Remus et al, 2013)Of the eight CORINAIR (Core Inventory of Air Emissions (environment)) Sintering emissions and their mitigation technologies