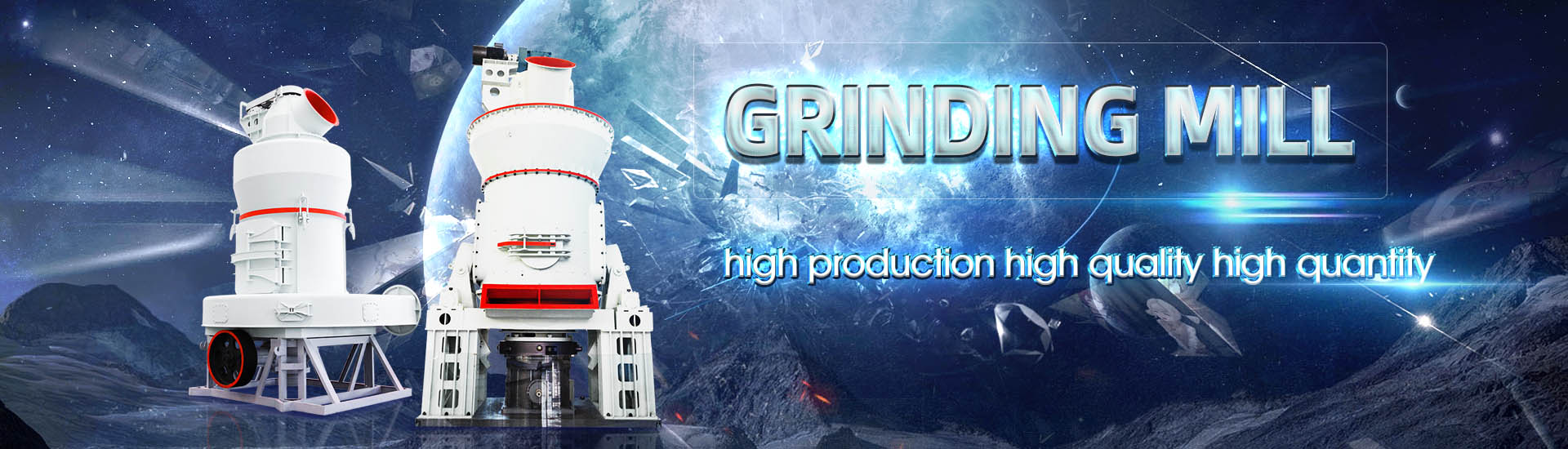
Ceramic powder making process
.jpg)
Fundamentals of Ceramic Powder Processing and Synthesis
Fundamentals of Ceramic Powder Processing and Synthesis presents examples of these modern methods as they apply to ceramic powders The book is organized to describe the natural and Book Title: Ceramic Powder Preparation: A Handbook Authors: Dibyendu Ganguli, Minati Chatterjee DOI: https://doi/101007/9781461563235 Publisher: Springer New York, NY eBook Packages: Springer Book Archive Ceramic Powder Preparation: A Handbook SpringerLinkFigure 1171 presents a general process flow diagram for ceramic products manufacturing The basic steps include raw material procurement, beneficiation, mixing, forming, green machining, AP42, CH 117: Ceramic Products Manufacturing US EPA2014年1月1日 This chapter provides an overview of powderforming methods for ceramics and metals Powder forming is distinct from traditional meltforming methods in that it involves Powder Processing of Bulk Components in Manufacturing
.jpg)
Foundations of Ceramic Synthesis: Processes, Principles, and
1 天前 415 Chemical and Process Industries a Ceramics are utilized to line industrial furnaces and kilns to endure high temperatures and provide protection against both thermal and 2015年9月11日 EMA 5646 Ceramic Processing Zhe Cheng (2015) 2 Powder Preparation Powder Synthesis via SolidState Reactions Features Simple and most widely used EMA5646 Ceramic Processing 2 Powder PreparationRaw material milling and mixing are important processes in the production of Fine Ceramics (also known as "advanced ceramics") that determine the material properties, quality and stability of finished products Raw powder and solvating Fine Ceramics Production Process Introduction to Fine This article explains how ceramic powders are made It begins by briefly describing the raw materials used in structural clay products, whitewares, refractories, and advanced ceramics It Processing and Characterization of Ceramic Powders
.jpg)
Fundamentals of ceramic powder processing and synthesis
Ceramic powder synthesis and processing are two of the most important technologies in chemical engineering and the ceramicsrelated area of materials science This book covers both the Ceramic tiles are produced mainly in Gujarat, Uttar Pradesh, Tamil Nadu, and Andhra Pradesh in India, one of the leading producers worldwide Understanding the Ceramic Manufacturing Process Ceramic manufacturing is a complex Ceramic Manufacturing Process in 10 Steps KhatabookCeramic Powder Compaction Volume 22 Issue 12 Skip to main content Accessibility help We use cookies to distinguish you from other users and to provide you with a better experience on our websites Sintering of nanosized WC–Co powders produced by a Ceramic Powder Compaction MRS Bulletin Cambridge Core2018年9月30日 PRESSING: Pressing is accomplished by placing the powder * into a die and applying pressure to achieve compaction * premixed with suitable binder and lubricant and preconsolidated so that it is freeflowing Free Different Production Techniques Ceramic Ninja

How to Use Ceramic Powder in Art
Make sure it is clean and free of any debris that could interfere with the process Step Three: Mix the ceramic powder with water to form a paste The water to powder ratio will vary depending on Kaolin clay is also very easy to work with, making it a good choice for beginners Feldspar is another popular type of ceramic powder It is known Powder metallurgy is a versatile manufacturing process that involves the production of parts and components using powdered metal or nonmetal materials (ceramic or composite) It offers unique advantages over traditional manufacturing methods, making it a What is Powder Metallurgy Process, Materials, and Applications1 TEACHER INSTRUCTIONS Ceramic Processing: Slip Casting Objective: Students will learn the fundamentals of slip casting and be able to think critically about why slip casting is used Background Information: Historically, ceramic materials in the form of clay figurines and pots were the first manmade materials over 10,000 years ago, and maybe even as long as 25,000EACHER NSTRUCTIONS Ceramic Processing: Slip CastingThere are two main types of processing ceramics i) pressing (a dry powder) and ii) wet methods, such as slip casting or tape casting, (forming a paste or dispersion of the ceramic powder with a liquid – usually water) [2] The choice of a method for TP 2: Processing of Ceramics: Forming and Shaping EPFL
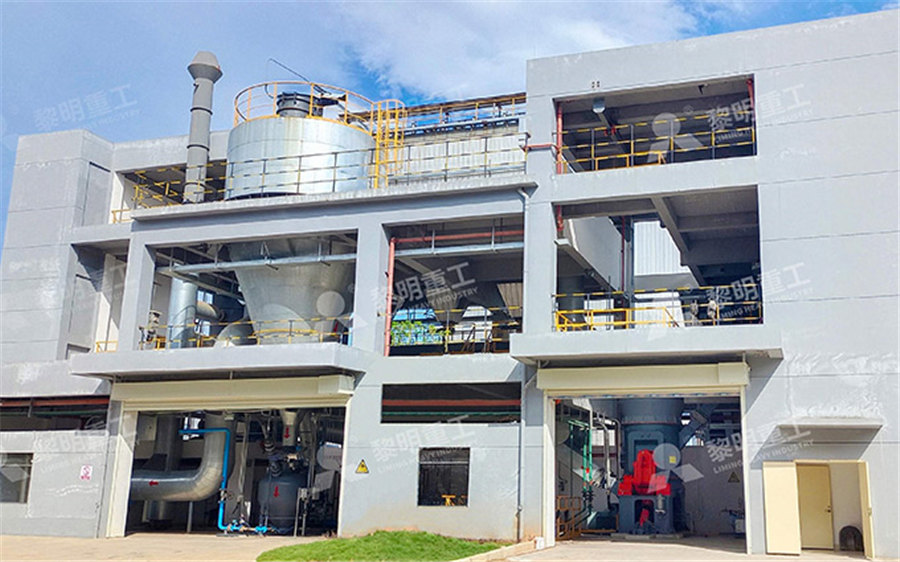
Powder Making Techniques in Ceramics PPT SlideShare
2018年5月20日 Powder Making Techniques in Ceramics Download as a PDF or view online for free solgel) and some commercial examples Ball milling, attrition milling, freeze drying process and applications, spray drying process and applications are described in detail Advantages and disadvantages of freeze drying and spray drying are also 2014年1月1日 The gelcasting process dates back to 1990s when Omatete and Janney from Oak Ridge National Laboratory, USA, came up with a new slurrybased manufacturing process for making ceramic components in which conventional wet processing techniques were combined with polymer chemistry (Janney and Omatete 1989; Omatete et al 1997; Yang et al 2011) Powder Processing of Bulk Components in Manufacturing1991年1月1日 Ceramics manufacturing is generally a batch process, with a few exceptions in traditional ceramics (eg, brickmaking is usually a continuous process) After the powder processing stage, some steps may be continuous (eg formingfiring), but the high labor costs of operating a threeshift system and modern computercontrolled intermittent kilns are leading Ceramics Process Engineering ScienceDirectCeramics Fire Performance Leatherworking Stoneworking Textiles Woodworking Photo Machine Working With Machines Working With Machines Precision is key for these areas of study, where machinists create functional How To Make Pottery At Home: Materials, Equipment,
.jpg)
Powder metallurgy – basics applications IIT Guwahati
Powder metallurgy – basics applications Powder metallurgy – science of producing metal powders and making finished /semifinished objects from mixed or alloyed powders with or without the addition of nonmetallic constituents Steps in powder metallurgy:Powder production, Compaction, Sintering, Secondary operations Powder production:2018年11月5日 The global production of ceramic waste powder (CWP), which is produced during the final polishing process of ceramic tiles, exceeds 22 billion tons The disposal of CWP in landfills will cause significant environmental The Use of Ceramic Waste Powder (CWP) in Making There are different methods of ceramic production, such as extrusion, pressing, and tape casting However, one of the most efficient ones is injection molding which can produce complex and precise shapes This reliable ceramic component manufacturing process begins by creating a ceramic powder, combining it with different binders to form a Ceramic Sintering Explained Ceramic Component Manufacturers This process combines glazing and shaping simultaneously by pressing the glaze (in spraydried powder form) directly in the die filled with the tile body powder Advantages include the elimination of glazing lines, as well as the glazing waste material (called sludge) that is produced with the conventional methodHow ceramic tile is made material, manufacture, making, used
.jpg)
Ceramic Processing: Slip Casting Ceramic and Glass Industry
The slip casting process is illustrated below in Figure 1 Figure 1: Schematic showing the steps used in slip casting First the slip is prepared by mixing the ceramic powder with a liquid Next the slip is poured into the mold which absorbs the liquid out of the slip leaving a thin wall of powder along the mold wallthe present inventor has disclosed a technique in Japanese Unexamined Patent Application Publication No 5 in which for the purpose of lowtemperature synthesis of a lead zirconate titanatebased ceramic powder, by mixing a fine powder of a monodisperse compound oxide obtained by hydrolysis of alkoxides of constituent elements except lead with a lead oxide Method of making lead zirconate titanatebased ceramic powder This case study has been focused on the intensification of the freeflowing powder preparation process involved in the very beginning of the ceramic tile manufacturing process Nowadays, the most widely used ceramic tile shaping method is uniaxial pressing of spraydried powder in Case Study 2: Ceramic Powder Processing2024年1月31日 Introduction Ceramic injection molding (CIM) is a ceramic manufacturing process using injection molding technology to produce complex and intricate ceramic parts, especially for those that are difficult or impossible to produce with traditional ceramic manufacturing methodsCIM has gained popularity in recent years due to its ability to produce An Introduction to Ceramic Injection Molding
.jpg)
4 CERAMIC PROCESSING FUNDAMENTALS
The Powder A chemical engineering view of a typical ceramics manufacturing process is shown in Fig 41, in simplified "schematic" fonn The process usually starts with a powder, examples being naturally powdered clay, or artificially powdered alumina, barium titanate, etc A powder has a relatively large specific surface area, orobtained for the ceramics powder particles coalesce and reduction of pore size and total surface area Chapter 13 22 • Formation of rigid structures having varied and complex shapes • Hardening process – hydration (complex chemical reactions involving water and cement particles) Ceramic Fabrication Methods (iii) GLASS Chapter 13: Applications and Processing of CeramicsFinal Alumina Powder Producing Alumina Ceramics The refined powder is blended with other materials before undergoing the forming process The combination of alumina with these additional substances determines the final Alumina Ceramic: What is it? How Is It Made, ProductsCompaction of ceramic powders is a forming technique for ceramics in which granular ceramic materials are made cohesive through mechanical densification, either by hot or cold pressing The resulting green part must later be sintered in a kiln The compaction process permits an efficient production of parts to close tolerances with low drying paction of ceramic powders Wikipedia
.jpg)
Ceramic Powder Synthesis SpringerLink
2015年1月1日 YAG powder retaining the morphology of Al 2 O 3 powder has been synthesized by using a partial wetchemical process, in order to form yttrium precipitate coated Al 2 O 3 particles The formation of the socalled core–shell structure had two steps, including (i) direct precipitation of yttrium component at the surface of the Al 2 O 3 particles and (ii) assembly of 2022年3月1日 Powder beds are the foundation of BJ Their characteristics are strongly dependent on the powder features and on the deposition mechanism (ie the recoater), which is a key component of the machine to build parts reliably and fast [5]Particle size distribution, morphology and flowability influence primarily the printing process as they all dictate the Binder jetting process with ceramic powders: Influence of powder The book is organized to describe the natural and synthetic raw materials that comprise contemporary ceramics It covers the three reactant processes used in synthetic ceramic powder synthesis: solid, liquid, andgasCeramic powder processing, as a field of materials processing, is undergoing rapid expansionFundamentals of Ceramic Powder Processing and Synthesis2015年9月11日 EMA 5646 Ceramic Processing Zhe Cheng (2015) 2 Powder Preparation Introduction Traditional ceramics Composition very rough – in a wide range and not precisely controlled Often a mixture of different raw materials Complex densification process that often involves reactions Raw material often minedEMA5646 Ceramic Processing 2 Powder Preparation
.jpg)
Ceramic Wikipedia
To process a sample through ice templating, an aqueous colloidal suspension is prepared to contain the dissolved ceramic powder evenly dispersed throughout the colloid, [clarification needed] for example Yttriastabilized zirconia (YSZ) The solution is then cooled from the bottom to the top on a platform that allows for unidirectional cooling2021年11月14日 The readers can get a profound view of porous ceramic materials and their different fabrication methods such as particle stacking sintering, the addition of foaming, gel casting, sol–gel process, polymeric sponge, and freezedrying method The fabrication process of porous ceramics can influence the quality of the final productsPorous Ceramic Properties and Its Different Fabrication Process Delving into the heart of Smartech’s innovation, we find the Lithographybased Ceramic Manufacturing (LCM) process, a distinguished method that sets a new benchmark in ceramic 3D printing The process commences by concocting a Engineered Ceramics Manufacturing Process Powder injection molding (abbreviated PIM) is a variant of plastic injection molding used to produce parts made of metal (MIM = metal injection molding) or made of ceramics (CIM = ceramic injection molding) with complex geometries Today, metallurgical powder injection molding is a costefficient mass production process to make small toMetal and ceramic powder injection molding WITTMANN Group
.jpg)
D'source Making Process Ceramic Clay Art Goa
For making ceramic clay, you need to mix Ceramic powder and Araldite (adhesive) in a ratio of 3:2 Ceramic clay dough is prepared by mixing the required quantity of adhesive and chalk powder The adhesive is used to Process of synthesizing ceramics 1 Small amount of water, binder material, and ceramic powder is mixed to form a paste 2 The paste is spraydried 3 Transfer the Spraydried material to the die and pressurize it to produce an unsintered ceramic item 4 Heat the material a bit higher than the binder’s temperature to burn off 5Ceramics Processing an overview ScienceDirect Topics2021年2月1日 Additive manufacturing (AM), often also referred to as 3D printing, is a range of processes that build 3D parts by adding material, usually layerbylayer, directly from computerbased 3D model data [7]AM offers an alternative approach to conventional formative processes, making it possible to manufacture geometrically complex nearnetshape 3D ceramic parts Additive manufacturing of advanced ceramic materials5331 Powder Process The powder process is one of the techniques used in the manufacture of ceramic nanocomposites, in which compression, rolling, and extrusion are used as the processing method In a simple compression process, powder flows from a bin onto a twowalled channel and is repeatedly compressed vertically by a horizontally Powder Process an overview ScienceDirect Topics
.jpg)
Powder Processing of Bulk Components in Manufacturing
2014年1月1日 The gelcasting process dates back to 1990s when Omatete and Janney from Oak Ridge National Laboratory, USA, came up with a new slurrybased manufacturing process for making ceramic components in which conventional wet processing techniques were combined with polymer chemistry (Janney and Omatete 1989; Omatete et al 1997; Yang et al 2011) Chapter One What is Powder Metallurgy? Powder metallurgy is a manufacturing process that produces precision and highly accurate parts by pressing powdered metals and alloys into a rigid die under extreme pressure With the development and implementation of technological advances, powder metallurgy has become the essential process for the production of Powder Metallurgy: What Is It? Processes, Parts, Metals UsedCeramic dry pressing is to put ceramic powder (5% to 8% moisture content) into a metal mold, compress it under the action of force (usually unidirectional pressure), and partially discharge the gas in the void in the blank, and the ceramicThe particles are displaced, gradually approached, and tightly meshed with each other, finally forming a blank with the same crosssection as that Ceramic Dry PressingCeramic forming techniques are ways of forming ceramics, which are used to make everything from tableware such as teapots to engineering ceramics such as computer parts Pottery techniques include the potter's wheel, slip casting and many others Methods for forming powders of ceramic raw materials into complex shapes are desirable in many areas of technologyCeramic forming techniques Wikipedia