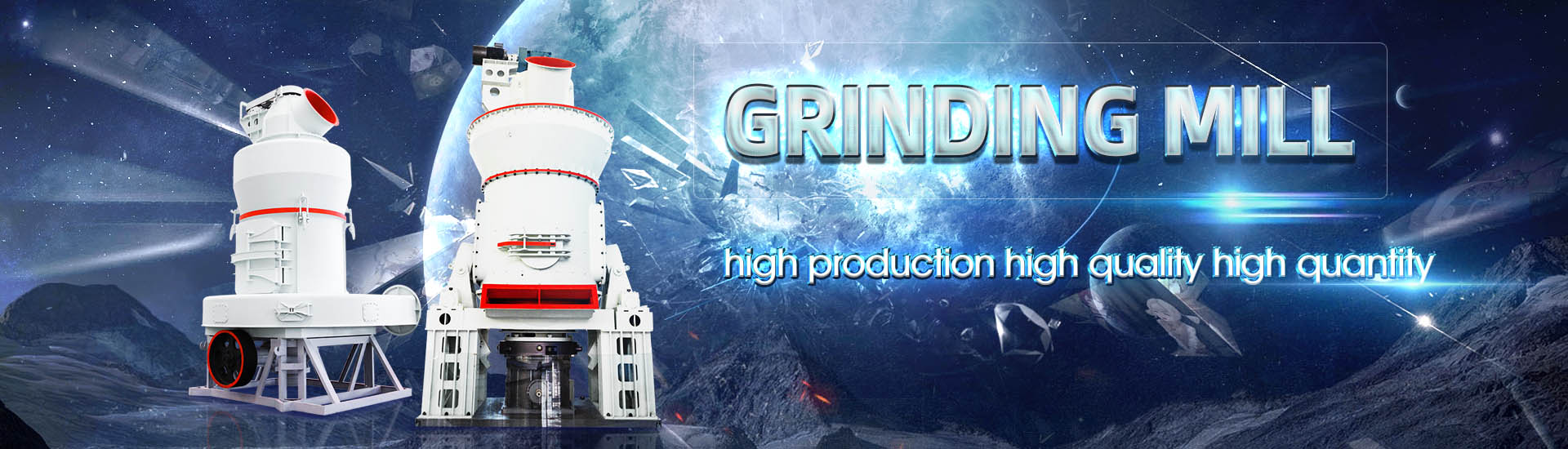
NdFeB waste mill sample
.jpg)
Study of an Impact MillBased Mechanical Method for
2023年6月12日 On the other hand, the high cost and the dangerous standard recovery methods that apply to NdFeB magnets limits options for traditional recycling A new mechanical method is proposed, not requiring hydrogen, high 2016年9月20日 Firdaus et al indicated a number of challenges for REE recovery from NdFeB magnet scrap: (1) the different mix of wastes produced—the complexity of magnet waste composition; (2) the effects of REE Recovery from EndofLife NdFeB Permanent 2023年5月8日 The most important challenge in magnettomagnet recycling of NdFeB magnets by hydrogenation is the recovery rate of the magnetic properties of the final products rather than the yield weight, since the efficiency of the Review on the Parameters of Recycling NdFeB Magnets 2024年4月1日 This paper extensively reviews the properties, recycling potential, and critical raw material stateoftheart recycling technologies of waste permanent NdFeB magnets An overview of NdFeB magnets recycling technologies
2FD{P}PC]854]XQ.jpg)
NdFeB Magnets Recycling via HighPressure Selective Leaching
2024年6月26日 Scrap NdFeB Magnet and Oxidized Powder Characterization Waste NdFeB magnet samples were dissembled from an endoflife motor and supplied in bulk form Then 2018年1月31日 A proof of principle for electrochemical approach was developed to effectively recover valuable elements from NdFeB magnet waste The speciation of iron in solution is An environmentally friendly electrooxidative approach to recover 2022年4月1日 Recovery processes must respond to several criteria in order to make recycling the NdFeB magnetbased waste sustainable These processes must be: (1) highly efficient on Recovery of rare earth elements from NdFeB magnet by mono2024年2月2日 In this study, the nearzerowaste valorization concept for EoLNdFeB magnets is developed, and highpurity REEs are achieved with a twostep process, including leaching and adsorption using alginate beadsDevelopment of a NearZeroWaste Valorization

Neodymium recovery from NdFeB magnets: a sustainable,
a realtime application, we demonstrate Nd recovery from a NdFeB magnet present in waste electronic equipment The removal using CFNC is speedy, efficient, and selective Solar 2018年1月29日 NdFeB magnet waste is one of the important secondary resources from which rareearth elements (REEs) can be recovered Herein we present an electrochemical route to selectively extract REEs from Selective electrochemical extraction of REEs from 2022年5月1日 NdFeB wastes are generated from magnet manufacturing and endoflife products The NdFeB wastes include 27 wt%–35 wt% rareearth elements, and represent an important secondary resource of rare earth 3 Currently, less than 1% of rare earth elements are recycled from rareearth wastes 4 In the wastes, rare earth elements are usually present in Recycling rare earth from ultrafine NdFeB waste by capturing 2023年3月1日 Rare earth elements are a nonrenewable strategic resource [1]However, undirected development in recent years has caused a serious waste of rare earth resources and irreversible damage to such resources, the supply gap of some rare earth elements is widening year by year [2]Recycling rare earth elements from urban or industrial waste is crucial to Recovery of highvalue rare earth elements from waste NdFeB by

An environmentally friendly electrooxidative approach to recover
An environmentally friendly electrooxidative approach to recover valuable elements from NdFeB magnet waste but enhances the leaching efficiency also The leaching of the roasted sample with 05 M hydrochloric The ball milling was performed at Umicore (Olen, Belgium) using Retsch RS100 ball mill for two hours to mill the solid sintered 2023年11月13日 A solvometallurgical process was developed to recover rareearth elements and cobalt from endoflife NdFeB magnets, using the ionic liquid (IL) trihexyltetradecylphosphonium trichloride ([P666,14 Recycling NdFeB Magnets and Rare Earth Fluorescent2017年9月1日 In this manuscript, we demonstrate a room temperature electrochemical process for efficiently recycling NdFeB magnet waste First, the magnet waste was completely leached with HCl and then, in An environmentally friendly electrooxidative approach to 2022年12月1日 Reported recycling technology of NdFeB waste: preferential dissolution by HCl [8], oxidation [9], [10], [11], chlorination [12], [13], and electrochemical method [14]Among them, the hydrochloric acid preferential dissolution method is to form Fe 2 O 3 and REO after roasting and to leach RE elements by HCl The method is attributed to its high purity production, New insight into oxidative roasting and leaching for NdFeB waste
.jpg)
REE Recovery from EndofLife NdFeB Permanent Magnet Scrap
2016年9月20日 NdFeB permanent magnets have different life cycles, depending on the applications: from as short as 2–3 years in consumer electronics to 20–30 years in wind turbines The size of the magnets ranges from less than 1 g in small consumer electronics to about 1 kg in electric vehicles (EVs) and hybrid and electric vehicles (HEVs), and can be as large as NdFeB magnets, which were an indispensable part of many hightech devices (Lixandru et al, 2017) At the same time, the REE content in NdFeB magnets was particularly high (up to 30%) (Moore et al 2015; Önal et al 2017), so the discarded NdFeB magnets have progressively became the focus of recycling materialsEfficient recovery of rare earth elements from discarded NdFeB 2021年11月29日 Due to the increasing demands and supply shortages for rare earth elements (REEs), the recovery of REEs from discarded NdFeB with high REE content has become extremely important In this paper, a hydrometallurgical coupling process involving mechanical activation and selective acid leaching was proposed for the recovery of REEs from discarded Efficient recovery of rare earth elements from discarded NdFeB 2021年3月1日 The annual output of NdFeB magnetic materials in 2016 is 35% higher than that in 2010, reaching t, and is expected to increase at an annual rate of 10% 2, 3 Meanwhile, more than 10000 t of NdFeB scrap are expected to be disassembled from waste electrical appliances annually 4 NdFeB waste contains not only 20%–30% rare earth elements but also Highefficiency simultaneous extraction of rare earth elements and
.jpg)
An environmentally friendly electrooxidative approach to
1 An environmentally friendly electrooxidative approach to recover valuable elements from NdFeB magnet waste aPrakash Venkatesan *, ZHI Sunb*, Jilt Sietsmaa, Yongxiang Yanga aDepartment of Materials Science and Engineering, TU Delft, 2628 CD Delft, the Netherlands b National Engineering Laboratory for Hydrometallurgical Cleaner Production Technology, 2018年1月31日 In this manuscript, we demonstrate a room temperature electrochemical process for efficiently recycling NdFeB magnet waste First, the magnet waste was completely leached with HCl and then, insitu electrochemical oxidation was performed to selectively oxidize Fe(II) in the leachate to Fe(III) Finally, oxalic acid was added directly to the electrooxidized leachate An environmentally friendly electrooxidative approach to To effectively recover valuable elements from the acidsoluble residue, scientific and technological workers have also conducted a series of studies, as shown in Table 1However, the majority of studies on acidsoluble residue from NdFeB waste have only utilized single elements such as rare earth or iron, and have not achieved the maximization of the benefits of acidsoluble residueRecovery of valuable metals in acidsoluble residue from NdFeB waste 2023年6月12日 Study of an Impact MillBased Mechanical Method for NdFeB Magnet Recycling June 2023; Metals Open Access Metallurgy Journal 13(6) an Italian Company working in the field of waste recovery (PDF) Study of an Impact MillBased Mechanical Method for NdFeB
.jpg)
Recovery of rare earth elements from NdFeB magnet by mono
2022年4月1日 Rare earth elements (REEs) such as Nd 3+ and Dy 3+ were recovered from simulated and real leaching solution of the NdFeB magnet via solid phase extraction (SPE) Extraction of REEs from simulated solutions was investigated using silica functionalized with NH 2, EDTA and/or phosphonic groupsThe effects of several experimental factors (pH, efficiency 16 waste NdFeB magnets by supergravity technology was investigated and the separating 18 conditions of G = 800 and t = 15min, the total oxygen of the sample decreased from 19 410 ppm to 28 ppmRecycling of waste NdFeB magnets by supergravity2024年6月26日 Scrap NdFeB Magnet and Oxidized Powder Characterization Waste NdFeB magnet samples were dissembled from an endoflife motor and supplied in bulk form Then they were demagnetized (Magnetizer, Horizon Instruments, UK) and crushed by using a vibrating disc mill machine (ScheibenschwingTS 750, SIEBTECHNIK TEMA, Netherlands)NdFeB Magnets Recycling via HighPressure Selective Leaching ewaste is collected correctly and recycled5 The ewaste is a concentrated source of many transition and rare earth metals6 The content of these metals is significantly higher in the ewaste than in natural minerals7 Recycling of Nd (or any REE) from ewaste will lead to active use of the valuable metal and result in overall economic benefitsNeodymium recovery from NdFeB magnets: a sustainable,
.jpg)
Recovery of Neodymium and Dysprosium from Waste Hard Disk
2021年5月24日 We demonstrate an endtoend protocol for the recovery of Dy and Nd from used NdFeB magnets by following steps crushing, roasting, grinding, leaching, liquid–liquid extraction and striping The magnets were roasted over a temperature range of 923–1273 K The influence of roasting temperature was studied by leaching the roasted samples with HCl NdFeB magnet is prone to oxidize in the air even at room temperature, so usually coated with a metal of Ni or Zn First, the plating layer was peeled off using cyanide solution And they were crushed and ground to powders under 200um in size using a jaw crusher, roll mill, and vibration mill in sequence (Fig 2)KIGAM Technology for the Recovery of NdFeB Waste Magnet and 2018年9月15日 A large number of waste sintered NdFeB magnets are generated in the machining and electroplating process and the waste magnet in the machining process accounts for 35% [1]To deal with the waste magnet, the usual recycling method is to resmelt as raw materials or partially joining the quicksetting flakes into the jet mill [2], and crush it into single Efficient reuse of the waste sintered NdFeB magnet with Dy2O3 2023年6月12日 For verification, the NdFeB standard lattice parameters (PDF 000361296, measured as bulk sample) are Michailidis, N Sustainable Recovery, Recycle of Critical Metals and Rare Earth Elements from Waste Study of an Impact MillBased Mechanical Method for
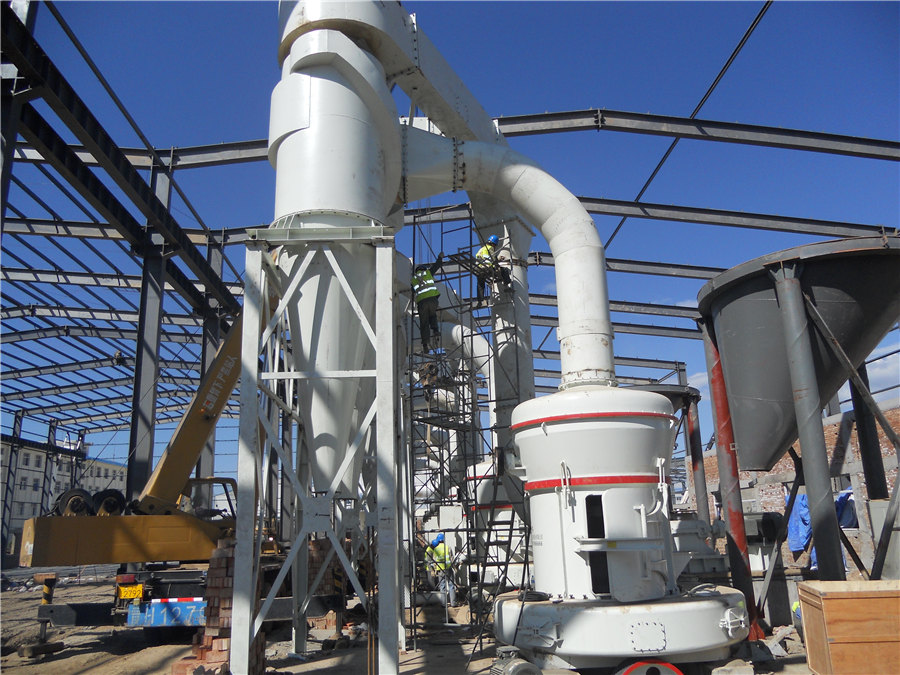
(PDF) Hydrogen Decrepitation PressLess Process recycling of NdFeB
Hydrogen Decrepitation PressLess Process recycling of NdFeB The powder was milled under argon for 3 hours at 650 rpm in a Fritch P6 ball mill The samples prepared from Trans Magn 20, 1584– 1589 (1984) [2] K Habib, P K Schibye, AP Vestbø, O Dall H Wenzel, “Comprehensive Waste Flow Sampling and Analysis 2024年2月2日 Waste NdFeB magnets were supplied in bulk form, as rectangles, from various companies The supplied waste magnets were crushed by a jaw The sample concentration was prepared with a 10% DMSO solution at 125 μg/mL and the 10% DMSO solution was used as the negative control 180 μL of the samples was added to each well in a 96 Development of a NearZeroWaste Valorization Concept for Waste NdFeB Breakage and Surface Oxidation Characteristics of Waste NdFeB Magnet In ball mill grinding test, it was found that the grinding process was not performed properly Fig 1 Waste rare earth magnet sample used in this study (123 mm(d) × 145 mm(h)) Table 2Breakage and Surface Oxidation Characteristics of Waste NdFeB Selective electrochemical extraction of REEs from NdFeB magnet waste at room the powder samples were directly divided into 3 gram subsamples and stored in a plastic vial to offset the effect of oxidation on the extraction efficiency calculations read more 15 What was the process used to mill the bulk sintered magnets? Ballmilling was Selective electrochemical extraction of REEs from NdFeB magnet waste
.jpg)
Separation and Recovery of Rare Earths and Iron from NdFeB
2023年9月30日 PDF NdFeB magnet scraps contain large amounts of iron, which poses challenges in recycling and greatly hinders the recovery of rare earths through Find, read and cite all the research you 2024年4月25日 The secondary waste produced by NdFeB waste after rare earth recycling, with an annual output of more than tens of thousands of tons, is the largest solid waste emission source in the rare earth industry, and longterm storage causes land resource occupation and environmental pollution Arseniccontaining mine wastewater has serious harm, wide Study on Properties of MicroNano Magnetic Composite Prepared 2022年3月1日 Specifically, NdFeB waste magnets as well as mixtures of Ln 2 O 3 obtained by preliminary separative treatments can be dissolved by HNO 3 solutions before being concentrated and separatedRecovery of rare earth elements from NdFeB magnet by mono2015年7月7日 These samples were then fed in a planetary ball mill (Retsch PM4000, 5 mm stainless steel balls) for further grinding to obtain \ 40, \ 125, and \ 200 l m samples(PDF) Recycling of NdFeB Magnets Using Sulfation
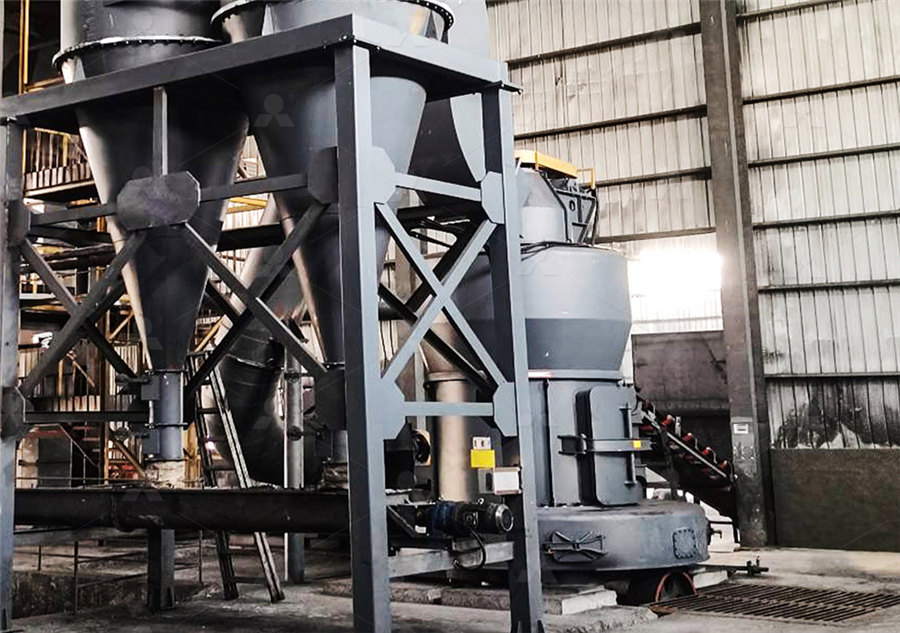
NdFeB: From sludge waste to powders via purification and modified
2022年2月1日 The oilbased NdFeB sludge waste was directly recycled to singlephase Nd 2 Fe 14 B powders via the combination of purification and modified Careduction reaction method The impurities and organics in the purified NdFeB sludge waste were greatly reduced, reducing calcium consumption in the subsequent reduction and diffusion (RD) process, thereby 2021年2月1日 The weight of NdFeB magnets, which have a life cycle of 1015 years in electric/hybrid cars and 2030 years in wind turbines, can reach 3040 g in electric/hybrid cars and 12 t in wind turbines Energy efficient process for recovery of rare earths from spent NdFeB 2023年2月11日 In the benchscale milling setup, a total of 200–400 mg sample of magnetic scraps, at ~ 10 microns, and sodium hydroxide solution were loaded into a 15 mL zirconia jar (FormTech Scientific) together with two 7 mm zirconia balls and milled for the respective period of time at 21 Hz in a Retsch MM300 mixer millLiquidassisted grinding (LAG) was utilized due Leaching of Neodymium from Recycled NdFeB Magnet Powders 2023年4月1日 This study proposes an advanced leaching method using organic acids to recover rare earth elements (REEs) from NdFeB permanent magnets from endoflife computers hard disk drives (HDDs) The endoflife HDDs were first dismantled in order to recover NdFeB magnets, which were then thermally demagnetized at 350 °C during 30 min before crushing in a ball mill Evaluating organic acids as alternative leaching reagents for rare
.jpg)
(PDF) Recycling of Waste NdFeB Magnets by Supergravity
2023年5月16日 NdFeB magnets are the most widely used rare earth permanent magnet materials at present The increasing number of the waste NdFeB magnets and their high rare earth content motivate a search for 2020年5月1日 Download Citation Highefficiency simultaneous extraction of rare earth elements and iron from NdFeB waste by oxalic acid leaching Iron can not be recovered at high value because only rare Highefficiency simultaneous extraction of rare earth2019年11月1日 Leaching efficiencies of Nd, Pr, Fe and Co after baking at 200 °C with a) 25 and b) 40 wt/vol% NaOH concentration (fixed conditions: t Baking = 2 h, t Leaching = 1 h and L/S = 20 mL g −1 )Alkali baking and solvometallurgical leaching of NdFeB magnets2022年9月27日 China's dominance in rare earth production and supply along with an increase in the available NdFeB magnets in the market [1], strongly motivates the recovery of rare earth elements from secondary (PDF) Recovery of Rare Earth Elements from Spent NdFeB
.jpg)
(PDF) The use of thermal hydrogen decrepitation to recycle NdFeB
2020年1月1日 Initial, demagnetized and disintegrated magnets; dark grey captions indicates those samples which are indicated as fully disintegrated The results from the hydrogen sorption analyzer (Tables 2 and