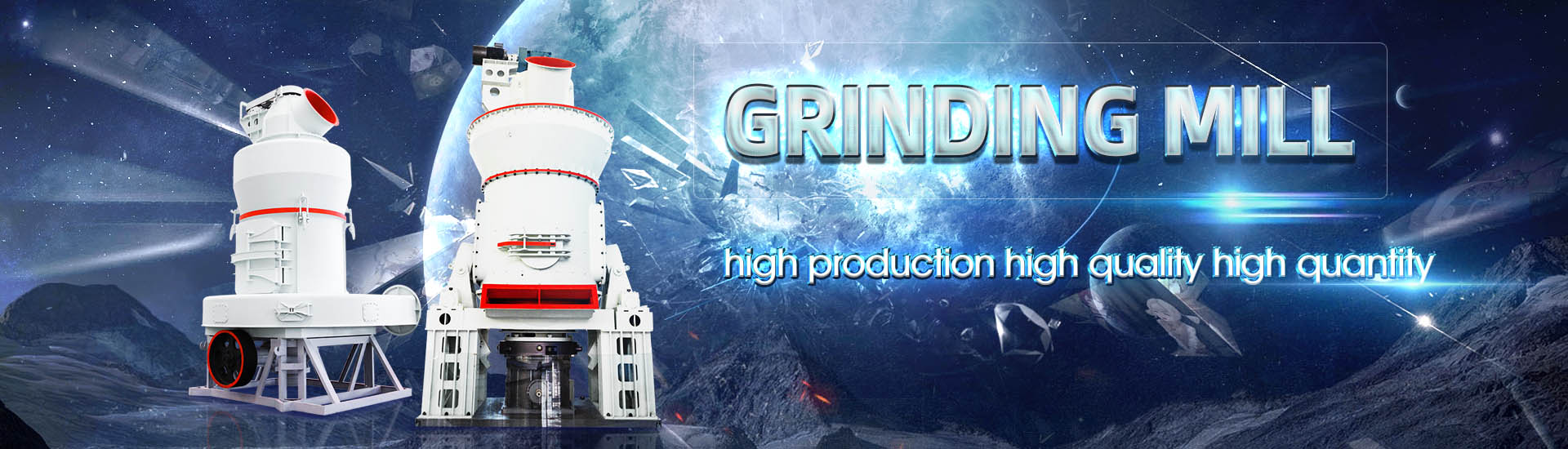
UM464 raw material mill installed power
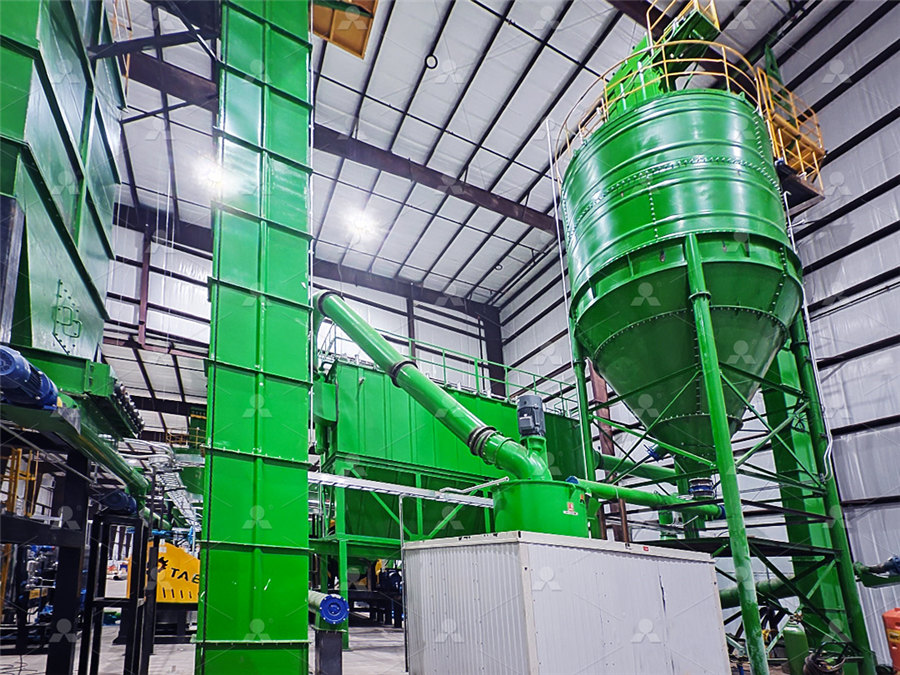
(PDF) Drives for large vertical roller mills ResearchGate
2017年1月1日 A new drive room was built to allow all drives to be installed, powered up, and checked out prior to shutdown An added advantage was that all drives were in one room on 2015年6月19日 Use this online calculators for Motor Sizing and Mill sizing as well as mill capacity determinators In extracting from Nordberg Process Machinery Reference Manual I Ball Mill Design/Power Calculation 911MetallurgistHighest availability, optimal redundancy, maximum throughput: These are the features of the quadropol® roller mill, which is based on a modular system of 2, 4 or 6 rollers Thanks to its Industrial Solutions quadropol QMR² myPolysiusServiceFor over 40 years, the MPS mills for power stations have been manufactured under license of Hitachi Power Europe GmbH (formerly Babcock Borsig AG), headquartered in Oberhausen, Reprint from ZKG 3 Gebr Pfeiffer
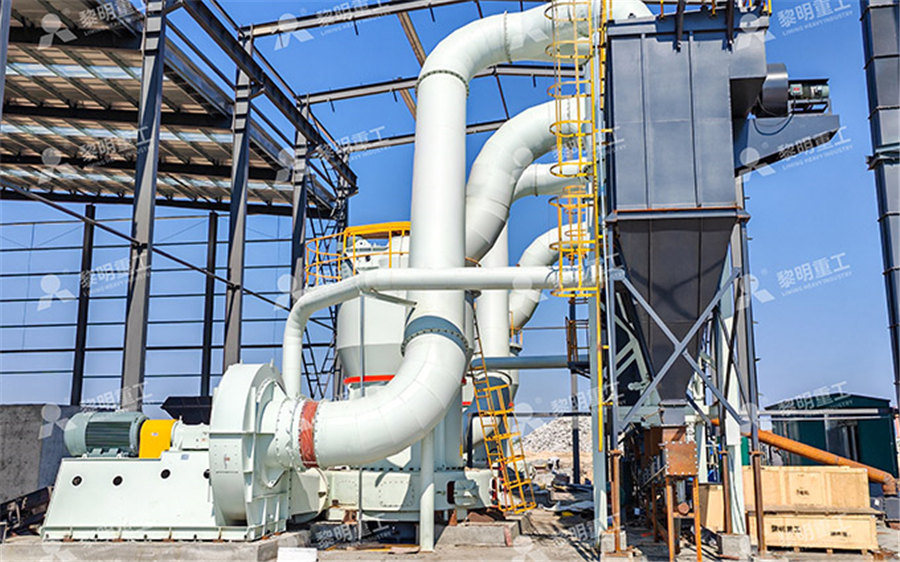
BALL MILLS Ball mill optimisation Holzinger Consulting
common solution to grind raw materials and cement Roller presses are used mainly in combination with a ball mill for cement grinding applications and as finished product grinding Vertical roller mills are adopted in 20 cement plants (44 mills) in Japan In the vertical roller mill which is widely used in the raw material grinding process, raw materials input grinding table Vertical roller mill for raw Application p rocess materials2014年4月1日 The newly developed modular roller mill for grinding cement raw material, cement clinker, and additives with an installed power of up to 12,000 kW was specifically designed to (PDF) The latest innovative technology for vertical roller mills roller mill designs for throughput rates of up to and exceeding 600 tph and drive powers of up to 6,000 kW, but also the optimisation of existing grinding plants and a broad range of customer Polysius Roller Mills For grinding
.jpg)
QUADROPOL® roller mill
This mill system from Polysius thus fulfils the prerequisites for ”online operation“ in the cement factory with a practically uninterrupted flow of material from the mill to the kiln High grinding vertical roller grinding mills for grinding: • Coal • Cement raw material • Clinker / granulated slag • Industrial minerals, and • Ores The core elements of these plants are the Loesche vertical PROCESS OPTIMISATION FOR LOESCHE GRINDING PLANTSin combination with a ball mill for cement grinding applications and as finished product grinding units, as well as raw ingredient grinding equipment in mineral applications This paper will focus on the ball mill grinding process, its tools and optimisation possibilities (see Figure 1) The ball mill comminution process has a high electricalBALL MILLS Ball mill optimisation Holzinger Consulting2019年6月22日 Specific power consumption of a raw mill is primarily dependent upon raw materials hardness and harder the material more will be the power required to grind the material to the desired fineness Optimizing Raw Mills Performance ; the Materials
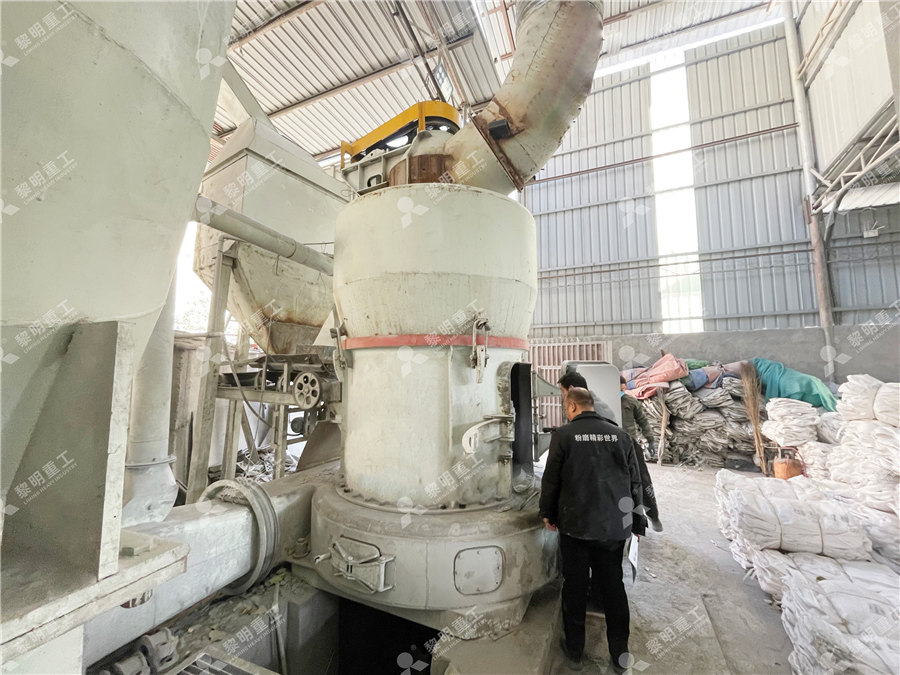
Raw Material Vertical Roller Mill
6External circulation reduce power consumption of fan 7Feed sluice ensures air flow and steady feed flow for minimum power consumption and optimum mill production 8The raw mill is easily adaptable to grind wet materials Specifications Note: mill spectral pattern benchmark 1Material medium friction (MF)=09~10; 2Material moisture max 7%;of material from the mill to the kiln High grinding plant availability has two beneficial results: it permits the use of a smaller mill and, provided that the factory is equipped with suitable raw material and raw meal analysis systems, allows the blending and storage silos to be downsized Roller unit with hydraulic systemQUADROPOL® roller millThe new mill system from Krupp Polysius thus fulfils the prerequisites for »online operation« in the cement factory with a practically uninterrupted flow of material from the mill to the kiln High raw material grinding plant availability has two beneficial results: it permits the use of a smaller mill and, provided that the factoryThe QUADROPOL roller millavailable for raw grinding, ensure the ability to meet all possible capacity requirements in a single mill even for the hardest materials The wellknown reputation of the OK mill as a reliable machine that is easy to operate and maintain continues with the OK raw mill In addition to the roller design features, the OK mill retains the abilityOK RAW AND CEMENT MILL
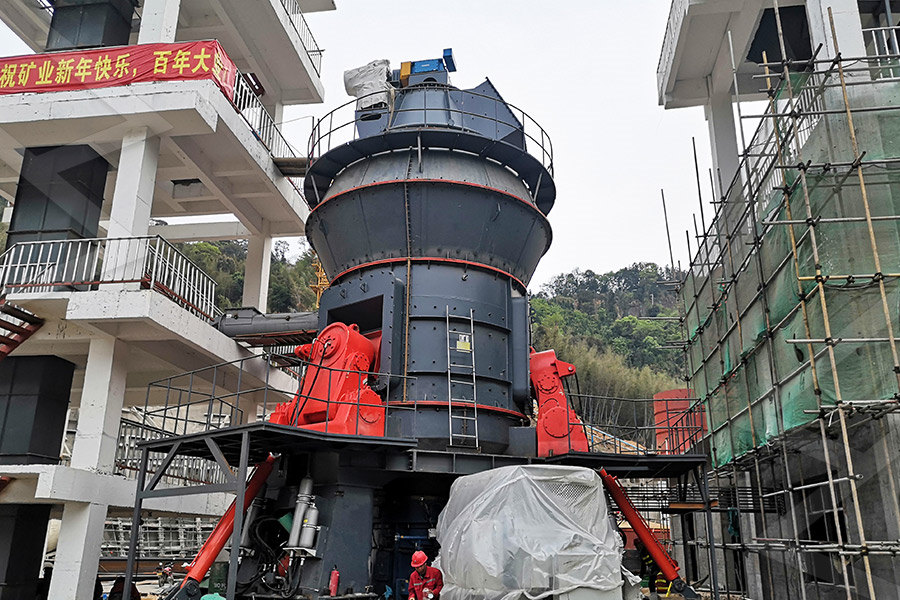
VERTICAL ROLLER MILLS AMCL
The mill consists of the lower casing, upper casing, table mounted on the vertical planetary gear reducer and grinding rollers supported by the swing levers The separator is installed at the upper parts of the mill The raw material fed through the air lock gate is ground between the rollers and table with the grinding force added byRoller mill for cement raw material grinding in China Roller mill for cement clinker grinding in Mexico Coal grinding plant in Poland 4 Advantages of Polysius roller mills at a glance: Installed power kW Throughput (Raw material of average grindability, 12 % R Polysius Roller Mills For grindingRaw Material Homogenization and Storage step in the line of the raw mix preparation processes installed with the aim to reduce the residual (relatively shortterm, high frequent) compositional variations observed for the raw meal produced in the raw mill (fig521) The raw meal reclaimed from such blending or homogenization silos will Raw Material Homogenization and Storage INFINITY FOR 2016年10月5日 A raw material moisture of up to 8 % can be dried when utilizing the preheater exit gases only If hot air from an air heater is also supplied, then a raw material moisture of up to 18 % can be handled The power requirement is 10–20 % lower than a ball mill, depending upon the grindability and moisture content of the raw material EnergyEfficient Technologies in Cement Grinding IntechOpen

Optimisation of Pfeiffer raw mill for cement plant PPT
2024年3月4日 Grinding bed is the material layer between the roller and the table It transmits the entire roller force and mill power It is the key issue to successful operating of a VRM !!! Determined by: •Feed Material size •Feed Material 2010年1月1日 Pfeiffer AG for grinding cement raw material, cement clinker, and additives with an installed power of up to 12 000 kW does in fact fulfill these customer requirements perfectlyThe modular design The new PFEIFFER roller mill MVR: Reliable grinding2015年1月30日 The generation of mill scale represents about 2% of steel produced and that is available as a secondary raw material, due to its richness in iron (about 70 to 72 % total Fe)Mill Scale: A Potential Raw Material for Iron and 2017年1月1日 7 CEM 6000 kW drive for a raw material mill FLSmidth Maag Gear 8 MultiDrive with four drive units GPSE mill with an installed power of 12 000 kW and fea(PDF) Drives for large vertical roller mills ResearchGate
.jpg)
Ball Mill Design/Power Calculation 911Metallurgist
2015年6月19日 The basic parameters used in ball mill design (power calculations), rod mill or any tumbling mill sizing are; material to be ground, characteristics, Bond Work Index, bulk density, specific density, desired mill tonnage capacity DTPH, operating % solids or pulp density, feed size as F80 and maximum ‘chunk size’, product size as P80 and maximum and finally the type of Usually each raw component is stored and fed separately to the mill, from which product is sampled and chemically analysed to determine adjustment of feed proportions by addition of corrective components tG maintain the target clinker compositionOlder mills may have silos for raw material storage, but the occurrence of feed problems with moist materialhas led to a Raw milling and blending INFINITY FOR CEMENT EQUIPMENT2017年5月1日 roller mill 5000 – 4 roller raw material mill in operation in North America and detailed operational data of s everal other 4 an d 6 Installed drive power 3,300 kW (PDF) Grinding process optimization — Featuring case studies and 2010年11月1日 Pfeiffer AG for grinding cement raw material and also cement clinker or granulated blastfurnace slag, with an installed power of up to 12000 kW does in fact fulfil these requirementsThe new pfeiffer MVRR vertical roller mill for producing raw meal
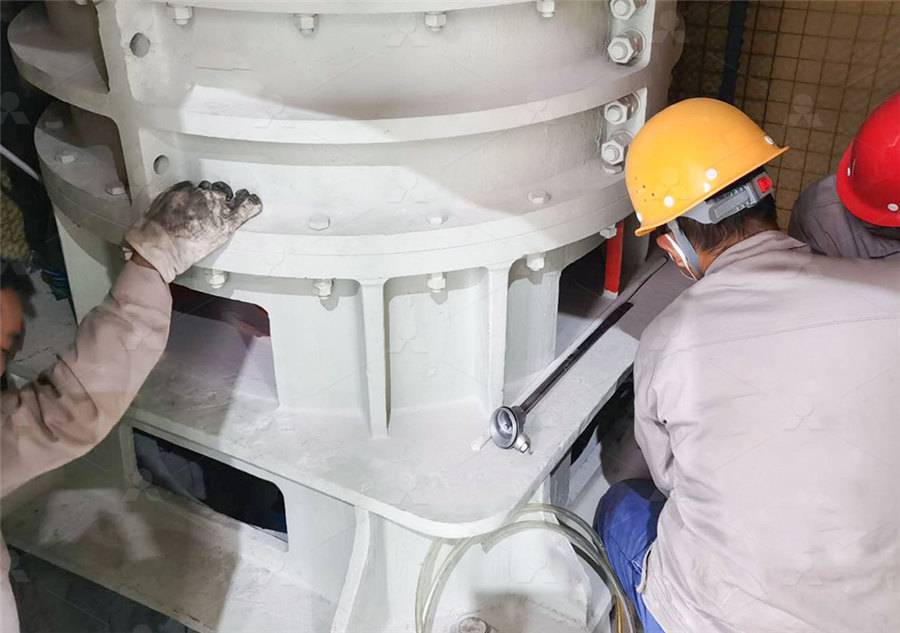
Polysius Roller Mills For grinding
Roller mill for cement raw material grinding in China Roller mill for cement clinker grinding in Mexico Coal grinding plant in Poland 4 Advantages of Polysius roller mills at a glance: Installed power kW Throughput (Raw material of average grindability, 12 % R Clinker grinding / Raw Material Grinding VRPM can be integrate with existing Cement Mill circuit to have substantial saving in specific power consumption and increase in production capacity We have experience of system engineering layout engineering which allows us to install the VRPM circuit within limited space in existing plantVRPM – AMCL Machinery LimitedPart Three: Raw Mill Process of Raw Mill The proportioned raw material is feed first to a grinding mill In the mill, particles ground in to very fine sizes In the grinding unit, drying, grinding and mixing takes place simultaneously Hot gas Cement Manufacturing Process INFINITY FOR 2023年5月19日 Did you know that 29% of plants spend 5 to 10% of their annual budget on maintenance, and 44% spend more than 40 hours a week performing maintenance? Considering this, crusher and mill efficiency must be one of the Tactics for Optimizing Crusher and Mill Efficiency: A
.jpg)
Raw Mill – Kiln Application in Cement Industry
THE CUSTOMER PROFILE M/s Chettinad Cement Corporation Limited (CCCL), An Indian Rs 85 Billion business group is into Manufacturing (Cement, Silica, Quartz, Grits) Services (Construction, Transports, Ship Management, 2007年11月1日 An MPS 5600 BC (Figure 5) with an installed power of 5300kW started production at the end of 2006 in China It is guaranteed for 120t/h of GBFS at a fineness of 5000cm 2 /g or 170t/h with a fineness of 4000cm 2 /g The same mill size MPS 5600 BC with 5400kW installed power was sold in 2006 to India for 145t/h slag at a fineness of 4200 BlaineMPS vertical roller mills for slag and slag cementsDepending on how much power you need, you may choose the suitable MultiDrive® with 3 to 6 identical drive units reaching a power rating of as much as 18,000 kW » Reduced space and costs The MultiDrive® has the lowest construction height of PFEIFFER VERTICAL MILL WITH MULTIDRIVE MORE POWER2022年5月23日 IDENTIFIKASI MASALAH PADA MESIN RAW MILL MENGGUNAKAN METODE FMEA DAN RPN Transport Raw Material Produksi material dan peralatan tidak l ancar 50 11 Power Panel dosimat off 2 20(PDF) IDENTIFIKASI MASALAH PADA MESIN RAW MILL
.jpg)
The Ultimate Guide to Ball Mills Miningpedia
2019年8月14日 After rising to a certain height, it will hit the raw material under the action of gravity, and then rises with the wall of the cylinder again and again to grind the raw material Working principle of ball mill back to top The ball mill is usually composed of a horizontal cylinder, a hollow shaft and a grinding headRaw mill is also called cement raw mill, similar to cement ball mill, it is an important cement milling equipment used in the cement production process Raw mill is mainly used for grinding cement raw meal in the cement factory production process It is also suitable for metallurgical, chemical, electric power and other industrial mining enterprises to grind various ores and other grindable Cement Raw Mill in Cement Plant for Cement Raw Meal GrindingDepending on how much power you need, you may choose the suitable MultiDrive® with 3 to 6 identical drive units reaching a power rating of as much as 18,000 kW » Reduced space and costs The MultiDrive® has the lowest construction height of PFEIFFER VERTICAL MILL WITH MULTIDRIVE MORE POWER2023年5月12日 In position a (Fig 1a) the length l 1 of the lower part of the chamber 1 is minimal, the grinding bodies 2 in it are located at the maximum level h 1Center of masses (CM 1) of grinding bodies (GB) in chamber 1 is located at the minimum distance a 1 from the filling bottom and at the distance b 1 from the crushing cylinder body The length l 2 of the lower part of the Power Calculation of BallTube Mill Drives in the Construction
.jpg)
QUADROPOL QMC Roller mill for the grinding of cement and
Throughput [t/h] Installed power [kW] Construction sizes Throughput [t/h] Installed power [kW] Innovative process technology assures Cement grinding Throughput rates up to 550 t/h Drive power up to 8600 kW Product fineness up to 550 m2/kg Numerous options to use hot gases for the drying process Material feeding and circulation in The raw material mill consists of feeding part, discharging part, gyre part, transmission part, which has the advantages of lower consumption and higher production capacity refractory material plants, chemical industry, electric Raw Material Mill with Excellent Performance Fote The vertical raw mill has high grinding efficiency Due to innovative materialgrinding principle, it reduces power consumption by 2030% as compared with ball mills The higher the feeding material moisture content, the more energy Vertical Raw Mill PENGFEI GroupIn this region, agricultural residue as the basic raw material is abundantly available Bindals use Kolhu bagasse, mill bagasse, wheat straw, we further installed TG of 5 MW; hence the total power generation was 20 MW We also started power export What is the overall outlook on the availability of raw material for your mill?Bindal Papers Mills: Reaching New Heights Papermart
.jpg)
Evaluasi Kinerja alat Vertical Raw Mill Melalui Perhitungan Neraca
2021年7月27日 Evaluasi Kinerja alat Vertical Raw Mill Melalui Perhitungan Neraca Massa dan Neraca Panas Di PT Semen Baturaja (Persero) Tbk2017年1月1日 The MVR vertical roller mill with an installed power of up to 18 000 kW offered by the Operational results of the MVR 6000 R6 mill for raw material grinding THE MOST COMPETITIVE WAY Of (PDF) Case studies and operational results of modern MVR MVR vertical roller mill solutions for grinding cement raw material, clinker and granulated blast furnace slag The MPS technology, however, is also applied in numerous installations simultaneously grinding and drying coal for use in cement plants, power stations and in the steel industry In these plants very differentCOAL GRINDING IMPS: more than meets the eye Gebr PfeifferOptimizing the raw materials selection and properties can significantly improve raw mill performance and capacity Reducing the raw material size from 70mm to 30mm increased one mill's output by 14%, far exceeding theoretical predictions Maintaining an optimal raw meal residue around 1015% and moisture level of 02510% also enhances performance Optimizing Raw Mills Performance PDF Mill (Grinding) Cement
.jpg)
TowerMill Eirich
Suitable molding material – trendsetting quality; Metallurgy Preparation of Vertical agitated media mill for energy efficient fine grinding The Eirich Reduced operating costs; Features The Eirich TowerMill product family ranges in installed power from 10 hp to 1,500 hp / 75 kW to 1,120 kW with throughputs from 05 up to 400 metric OptimizationofVerticalRawMillOperationpdf Free download as PDF File (pdf), Text File (txt) or view presentation slides online The document discusses optimization and operation of vertical roller mills (VRMs) Key points include: 1) Continuously monitor and adjust process parameters to find the optimum operating conditions of highest capacity and lowest power consumptionOptimization of Vertical Raw Mill Operation PDF