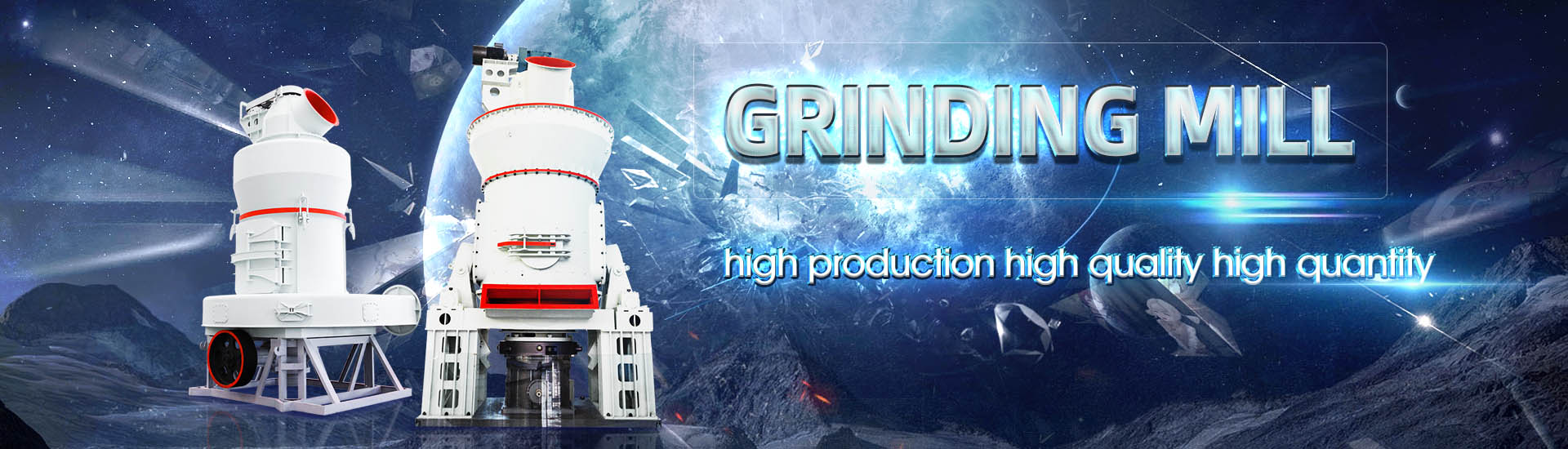
Ultrafine grinding of semicoal
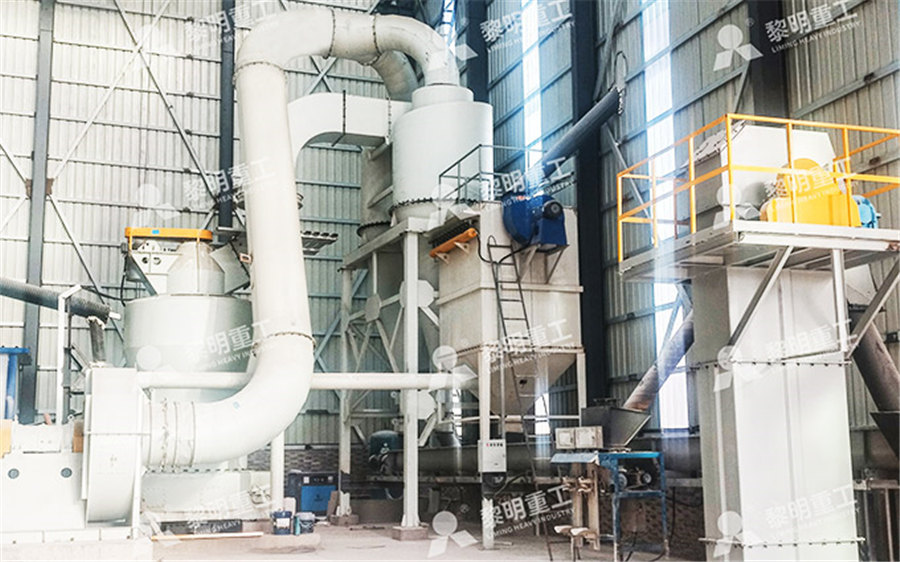
Mechanistic study of the effects of ultrafine grinding on the
2024年9月1日 This study advances our knowledge on the mechanism by which ultrafine grinding alters the physicochemical properties of anthracite coal particles and affects the flotation 通过扫描电镜和X射线衍射仪进行微观理化特性表征,使用哈氏可磨仪和振动磨分别进行输入有限和过量能量条件下的破碎实验,采用激光粒度仪分析粒度分布规律,并结合分形理论研究破碎 低阶煤及其热解半焦的超细粉碎特性2022年12月1日 In this paper, the fractal characteristics of the coal particle size distribution are expected to be taken as the starting point to establish the ultrafine grinding model of coal Study on microenergy consumption model of ultrafine grinding 2023年7月10日 The present literature review explores the energyefficient ultrafine grinding of particles using stirred mills The review provides an overview of the different techniques for (PDF) EnergyEfficient Advanced Ultrafine Grinding of Particles
[GYQ0R)ZQ]ESS4NJ.jpg)
Optimization of operating conditions on ultrafine coal grinding
2022年5月1日 This study investigated ultrafine coal grinding performance of four low to moderatecost grinding media in a laboratory stirred mill Kinetic grinding tests showed that 2021年7月30日 An ultrafine grinding scheme assessed by the authors as being the most costeffective option for grinding extrahard materials and materials having high surface energy was TwoStage Grinding as the Most CostEffective Option for 2022年4月1日 The present literature review explores the energyefficient ultrafine grinding of particles using stirred mills The review provides an overview of the different techniques for Optimization of operating conditions on ultrafine coal grinding Exploratory investigation on the use of lowcost alternative media for ultrafine grinding of coal Qingqing Huang A Noble Deniz TalanOptimization of Operating Conditions and Design Parameters on
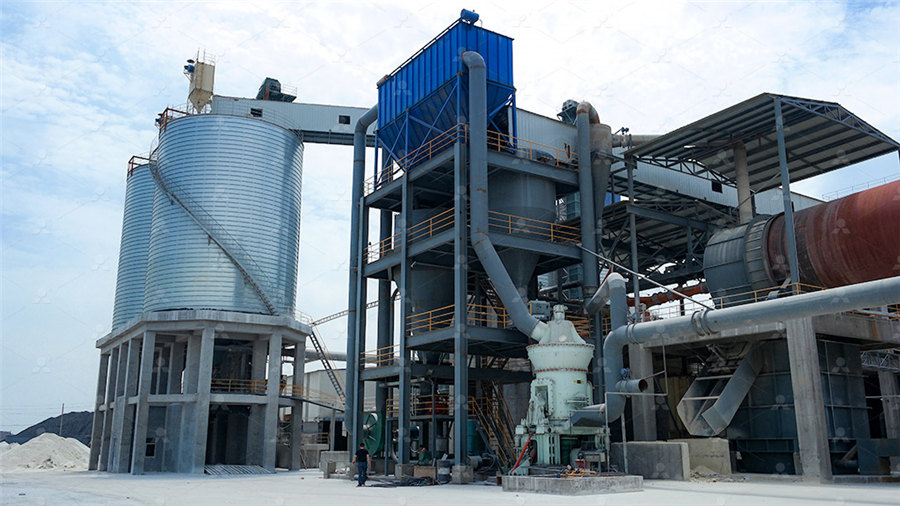
Exploratory investigation on the use of lowcost alternative media
2020年8月20日 In this study, the energy efficiency of three alternative grinding media including, coarse silica beads, fine silica beads, and granular sand, were evaluated and compared 2019年6月1日 PDF The ultrafine grinding kinetic model for pulverized coal based on the mechanism of grinding process can be used to predict the particle size Find, read and cite all the research you (PDF) Investigation on the ultrafine grinding of Americas, Corporate Headquarters Air Products and Chemicals, Inc 7201 Hamilton Boulevard Allentown, PA 181951501 T 8006544567 or 6107064730PolarFit™ UltraFineGrinding Mill Air Products Chemicals2005年4月1日 Download Citation Ultrafine coal grinding and ultraclean coal preparation Six coals of different rank were analyzed and investigated regarding to their constituent and size of embedded Ultrafine coal grinding and ultraclean coal preparation

Sustainability of coal mines: Separation of clean coal from the fine
2021年5月1日 Ultrafine grinding and decanter centrifugation to recover clean coal from [47] observed the phenomenon of reagent adsorption by ultrafine coals in the flotation process, which shows a detrimental effect on clean coal separation Column flotation seems to be an attractive option, however, dewatering of clean coal slurry (60 2023年7月10日 The present literature review explores the energyefficient ultrafine grinding of particles using stirred mills The review provides an overview of the different techniques for size reduction and (PDF) EnergyEfficient Advanced Ultrafine Grinding of Particles 2022年2月28日 Comparing dry and wet grinding curves in a ball mill in the same condition (an equal amount of materials and grinding media has been used on each pair of wetdry experiments) (Fig 17) indicated two significant differences at higher power values of wet grinding, specifically when speed exceeded 06 critical speed and for higher ω Pmax in the Grinding SpringerLinkOPTIMIZATION OF OPERATING CONDITIONS AND DESIGN PARAMETERS ON COAL ULTRAFINE GRINDING THROUGH KINETIC STIRRED MILL TESTS AND NUMERICAL MODELING Skip to search form Skip to main content Skip to account menu Exploratory investigation on the use of lowcost alternative media for ultrafine grinding of coalOptimization of Operating Conditions and Design Parameters on Coal
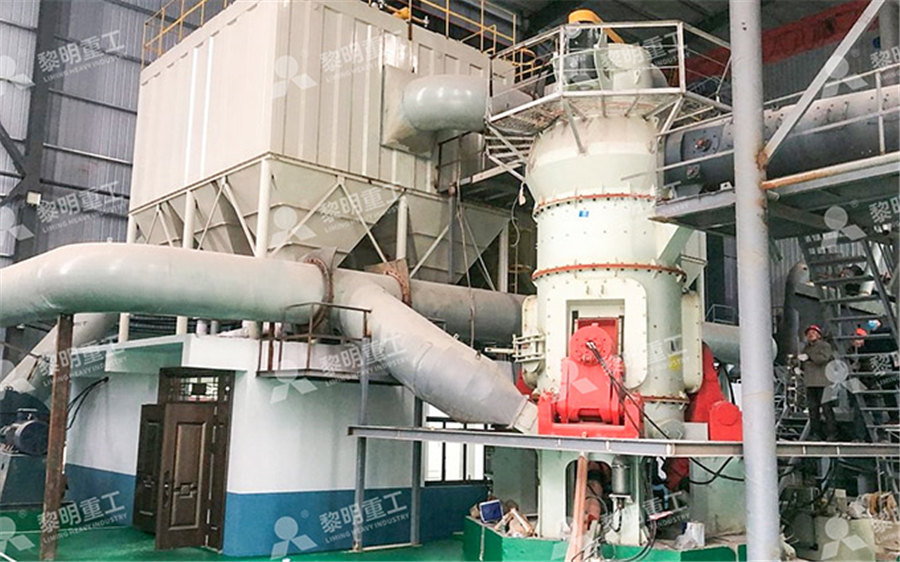
Influence of grinding methods on the preparation of ultraclean coal
DOI: 1037190/ppmp/ Corpus ID: ; Influence of grinding methods on the preparation of ultraclean coal from slime @article{wang2022InfluenceOG, title={Influence of grinding methods on the preparation of ultraclean coal from slime}, author={Ruiyang wang and Liang Gao Gao and Wenli Liu and Qiming Zhuo}, journal={Physicochemical Problems of 2022年12月1日 To obtain lowash coal by physical or chemical methods, we process coal samples into ultrafine coal particles [1], [2], [3]Ultrafine particles refer to particles with a size less than 30 μm, and some literature stipulates a particle size below 10 μm [4]With the increasing demand for ultrafine coal particles, coupled with stringent quality requirements, efficient Study on microenergy consumption model of ultrafine grinding coal 2020年7月1日 Based on the particle size distribution and surface physicochemical characteristics of coal particles, a microenergy consumption model of coal particles in the ultrafine grinding process was Recent developments in beneficiation of fine and ultrafine coal 2022年4月16日 This study investigated ultrafine coal grinding performance of four low to moderatecost grinding media in a laboratory stirred mill Kinetic grinding tests showed that silica beads generated Optimization of operating conditions on ultrafine coal grinding
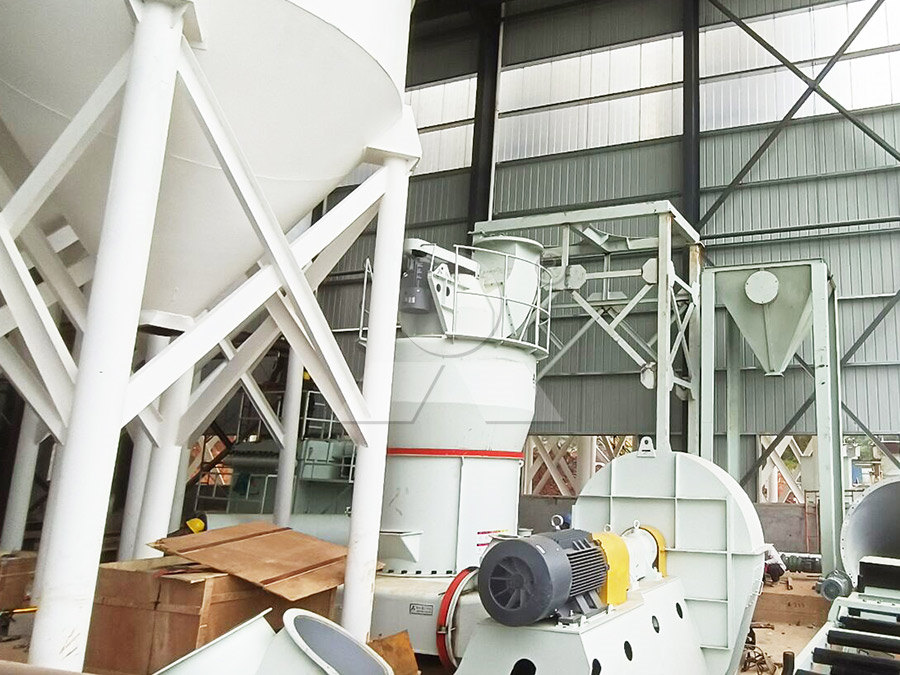
Preparation of clean coal by flotation following ultra fine liberation
2003年3月1日 Fig 2 illustrates the relationships of the flotationrate constant obtained for the individual vitrinite; the vitrinite and exinite group; and the exinite and inertinite group versus consumption of BKI reagent Comparison of the floatabilities shown in this diagram concludes in the following floatability order of the petrographic components: V>E>I>Inorganic groupA defined particle size distribution and a high throughput rate are essential success factors in powder production To ensure that you and your customers benefit from high endproduct quality, Grenzebach’s whirlwind mill offers you Whirlwind mill – fine and ultrafine grinding2020年8月20日 PDF Ultrafine grinding is a technology, which can be used to process inorganic nonmetallic materials High quality surfaces with a low roughness, Find, read and cite all the research you (PDF) Ultrafine grinding of inorganic nonmetallic materials using 2024年9月1日 Additionally, ultrafine coal particles are prone to agglomeration and surface oxidation during ultrafine grinding [10], [11] Consequently, not only achieving finer material granularity, but also considering how to adequately liberate inorganic minerals from coarser particles is important, which can influence both the energy consumption of crushing and Mechanistic study of the effects of ultrafine grinding on the
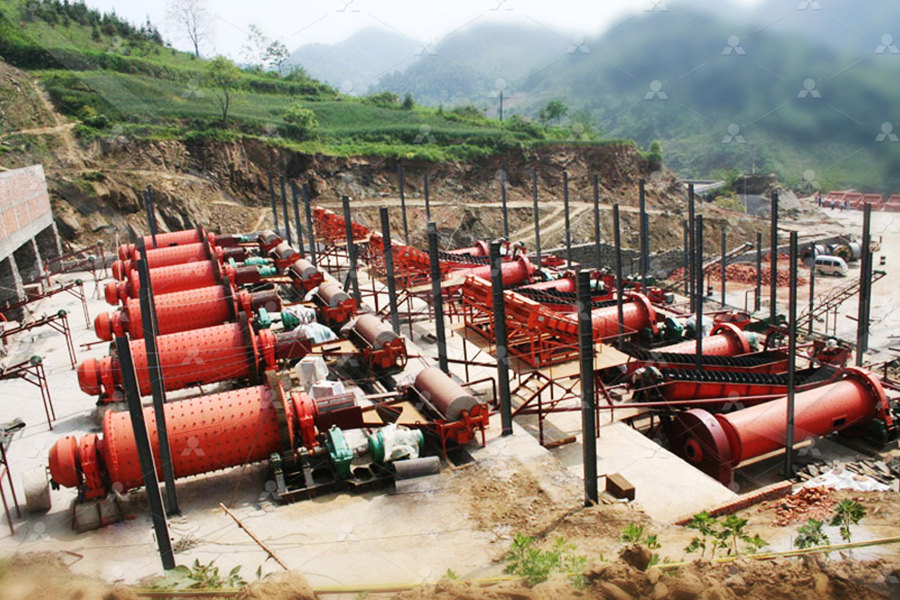
Optimization of operating conditions on ultrafine coal grinding
This study investigated ultrafine coal grinding performance of four lowto moderatecost grinding media in a laboratory stirred mill Kinetic grinding tests showed that silica beads generated the finest product size with a P80 of 59 pm from a feed size of 244 pm while having a specific energy (SE) input of 309 kWh/ton2021年9月30日 Beneficiation of coal is a water intensive process, and the water is recovered in downstream operations in the high rate thickener (HRT) and vacuum belt filtration (VBF) Clean coal particles entering the HRT have an inherent tendency to enter the overflow because they are extremely fine and hydrophobic Hence, flocculants (polymers) are used to floc the ultrafine New Process for Recovery of Ultra Fine Coal by PreTreatment DOI: 101016/jpartic202407022 Corpus ID: ; Liquidsolid grinding system: Grinding kinetics of coal fly ash as ultrafine supplementary cementitious materials @article{Yang2024LiquidsolidGS, title={Liquidsolid grinding system: Grinding kinetics of coal fly ash as ultrafine supplementary cementitious materials}, author={Jin Yang and Yong Huang Liquidsolid grinding system: Grinding kinetics of coal fly ash as 2018年9月1日 In a commercial setting, coal preparation plants often discard ultrafine coal because of the high clay and high ash content These ultrafine coal particles are classified as waste and discarded since the coal cannot be efficiently and economically separated from gangue material [8]The problem of discarding ultrafine coal to numerous impoundments worldwide Recent advances in the beneficiation of ultrafine coal particles
.jpg)
Optimization of operating conditions on ultrafine coal grinding
This study investigated ultrafine coal grinding performance of four lowto moderatecost grinding media in a laboratory stirred mill Kinetic grinding tests showed that silica beads generated the finest product size with a P80 of 59 pm from a feed size of 244 pm while having a specific energy (SE) input of 309 kWh/tonVertical Coal Mill is specially used for ultrafine grinding of raw coal and bituminous coal materials in cement, power plants, iron and steel plants and other fields The GRMC coal vertical mill produced by CHAENG adopts special structural design and production process, which is energysaving and environmentally friendlycoal grinding machine CHAENGsimultaneous ultrafine grinding and drying of lowrank coals in a fluidenergy mill was undertaken Two different lignites and a subbituminous coal were used in the study Ultrafine grinding tests were conducted with air nominally at ambient conditions and with steam at temperatures ranging from 225°F to 488°FPOWER REQUIREMENTS FOR ULTRAFINE GRINDING AND DRYING OF LOWRANK COALS 2022年4月1日 Semantic Scholar extracted view of "Optimization of operating conditions on ultrafine coal grinding through kinetic stirred milling and numerical modeling" by F Patiño et al The present literature review explores the energyefficient ultrafine grinding of particles using stirred mills The review provides an overview of the Optimization of operating conditions on ultrafine coal grinding

Optimization of some parameters of stirred mill for ultrafine grinding
Modeling and multiobjective optimization of operating parameters in semi autogenous grinding Stirred mills are primarily used for ultrafine grinding applications in the mining (1996) 141–152 [18] MJ Mankosa, GT Adel, RH Yoon, Effect of media size in stirred ball mill grinding of coal, Powder Technology 49 (1986) 75–82 Wet ultrafine grinding has been increasingly used for production of The study was conducted for the mill on a semitechnical (1974) 397 – 420 [19] RR Klimpel, Slurry rheology influence on the performance of mineral/coal grinding circuit, Part 1, Mining Engineering 34 (1982) 1665 – 1668 [20] RR Klimpel, Slurry (PDF) Slurry rheology in wet ultrafine grinding of industrial 2021年5月11日 The modernday coal processing plants can be categorized into four different circuits, depending upon the size of the coal particles to be treated: (a) coarse coal processing circuit treating particles coarser than 10 mm, (b) small coal circuit for washing particles in the size range of 110 mm, (c) fine coal circuit for cleaning particles in size range of 015–1 mm, and Mineral Beneficiation and Processing of Coal SpringerLink2022年5月1日 Even though many studies have explored the ultrafine grinding behavior of various minerals using stirred mills [14,55,62,80,83], the studies on coal ultrafine grinding are limited In addition, there are still many areas, including modeling and simulation, that need to be studied to understand the grinding mechanism in depthOptimization of operating conditions on ultrafine coal grinding
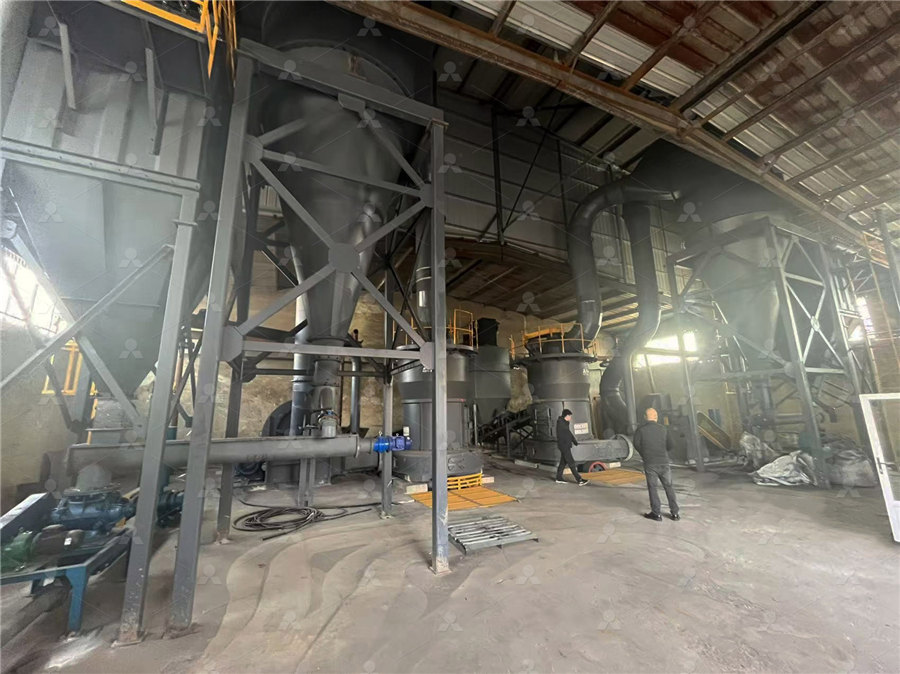
Breakage mechanisms and mill performance in ultrafine grinding
1999年11月1日 With the increasing time, the dry grinding breakage rate increased, while it decreased for wet grinding (solid concentration of 70 vol%) The differences in shape factor and surface roughness of the wet and dryground samples were attributed to different breakage mechanisms and grinding energy amounts generated by those two types of procedures2023年5月25日 Impacts of Blending Semicoke in PCI coal on Grinding Efficiency and Bl ast Furnace Operation Chong ZOU 1), Nan YU 1), Dong LIANG 2), Jiangyong HE 1), Ruimeng SHI 1), and Mengmeng REN 1) * 2Impacts of Blending Semicoke in PCI Coal on Grinding Efficiency 2022年1月4日 This study investigated the ultrafine coal grinding performance of four low to moderatecost grinding media: ceramic balls, granular sand, alumina beads, and silica beads The kinetic grinding tests were conducted using a stirred mill, while different operating conditions, including the media size, solids concentration, and the addition of viscosity modifiers, were Optimization of Operating Conditions and Design Parameters on Coal 1997年5月1日 Investigations were performed on fine grinding of bituminous coal in a laboratoryscale pulverizer The results indicated that the breakage behavior at relatively coarse sizes (ie, greater than Reagglomeration phenomena in fine dry grinding of coal
.jpg)
Ultrafine Grinding an overview ScienceDirect Topics
Grinding R Hogg, H Cho, in Encyclopedia of Materials: Science and Technology, 2001 (d) Vibratory mills Vibratory mills use oscillatory motion of the mill shell to agitate the media As for the stirred mills, the active grinding zone encompasses the entire mill volumeWhat Is Ultra Fine Grinding Mill The ultrafine powder grinding system is a new product independently developed by our company, mainly used to grind and classify various nonmetallic ores in cement plants, such as the grinding of Ultra Fine Grinding Mill Ultra Fine Powder GrinderFig 1 Section drawing of stirred mill used in ultrafine grinding tests [8] (1—Motor for moving of grinding chamber; 2—Motor of stirring shaft; 3—Connection of motor and shaft; 4—Stirring pins; 5—Grinding chamber; 6—Moving table of stirred grinding chamber; 7—Stability table; 8—Control panel) 23 Experimental designUltra fine grinding of silver plant tailings of refractory ore using 2020年8月20日 This study investigated ultrafine coal grinding performance of four low to moderatecost grinding media in a laboratory stirred mill Kinetic grinding tests showed that silica beads generated Exploratory investigation on the use of lowcost ResearchGate
.jpg)
Study on MicroEnergy Consumption Model of Ultrafine Grinding Coal
2022年1月1日 The effect of ultrafine dry grinding for up to 1920 min in a planetary ball mill at 300 rpm on size distribution, particle agglomeration and bulk structural changes in a dolomiterich (CaMg(CO3)2 Fig 1 Section drawing of stirred mill used in ultrafine grinding tests [8] (1—Motor for moving of grinding chamber; 2—Motor of stirring shaft; 3—Connection of motor and shaft; 4—Stirring pins; 5—Grinding chamber; 6—Moving table of stirred grinding chamber; 7—Stability table; 8—Control panel) 23 Experimental designUltra fine grinding of silver plant tailings of refractory ore using 2013年4月16日 Ultrafine grinding involves a large number of parameters in its operation In this paper, four important parameters of the Drais stirred ball mill, ie, the bead density, slurry density, mill Investigation of some parameters affecting the Ultrafine grinding Ultrafine Grinding The Emax is an entirely new ball mill designed for high energy grinding The maximum speed of 2000 rpm, so far unrivaled in a ball mill, and the innovative jar design produce highly effective size reduction by impact and friction The grinding jar geometry in combination with the circularTHE REVOLUTION IN ULTRAFINE GRINDING RETSCH

Effect of ultrafine grinding on coal surface properties and ultra
In order to understand the effect of ultrafine grinding on the coal surface properties and super clean coal separation,Huainan gas coal (HN) and Taixi anthracite (TX) were investigated in this study Fourier transform infra red spectroscopy (FTIR),ζ potential meter,microcalorimeter and specific surface analyzer were used to analyze the variation of surface functional