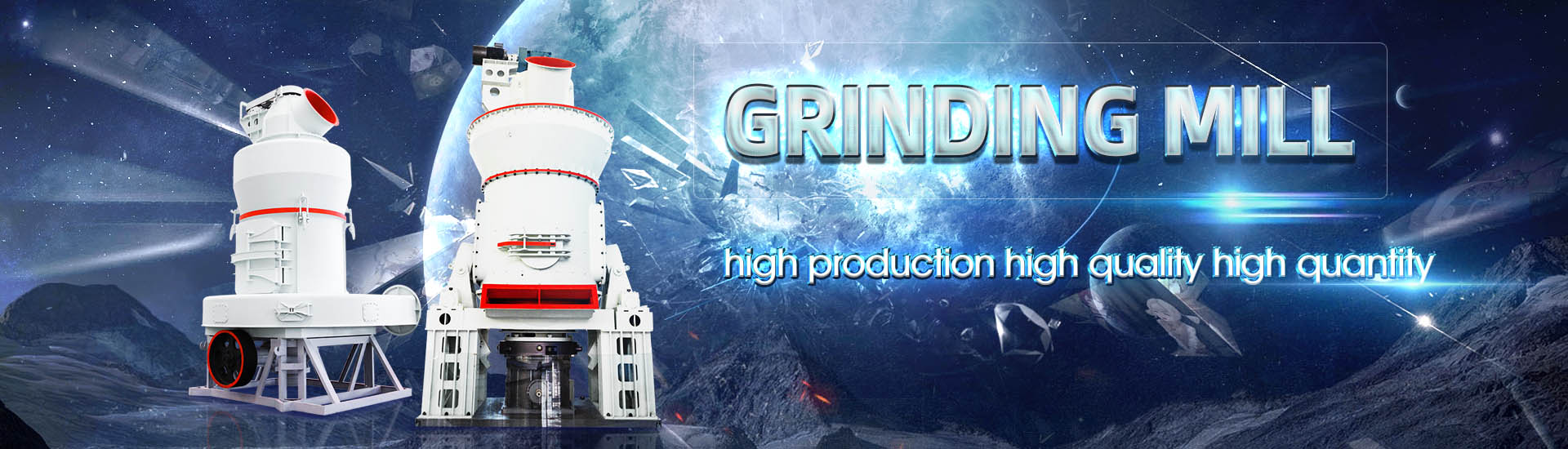
Grinding mill can crush particle size
.jpg)
Solids Choose the Right Grinding Mill Chemical
By continuously classifying out fines and returning oversize material to the mill, such systems can very efficiently provide sharp particlesizedistribution grinds As a rule of thumb, dry grinding generally will achieve particle sizes of 3–5 2019年1月1日 This effect is well illustrated by a series of experiments on the grinding of coal in a small mill, carried out by Heywood 1 The results are shown in Fig 51, in which the Particle Size Reduction and Enlargement ScienceDirectdesired particle size is achieved Wet milling enables fine particle size results, uniform size distribution, and certain desirable morphological (shape) characteristics in the outcome — MILLING METHODS COMPARISON GUIDE Custom Processing Williams Crushers has a variety of machines that can perform crushing size reduction like our Roll Crushers and Impact Crushers Grinding is generally considered reduction to table salt size, or about 5 to 25 mesh Williams Impact Particle Size Conversion Chart Williams Patent Crusher
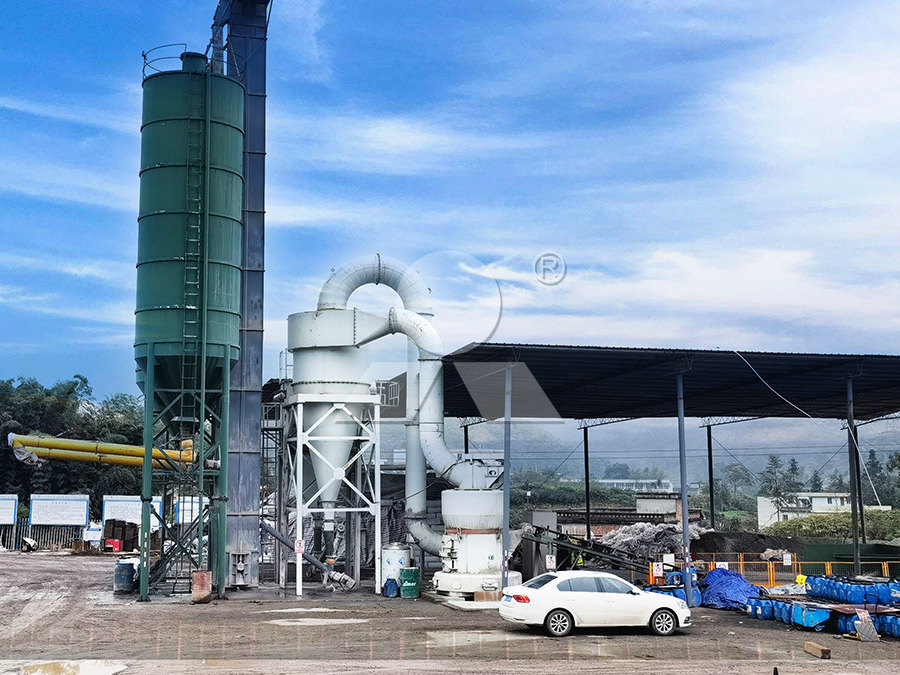
Principles of Sample Preparation by Grinding or Comminution
Grinding samples has many benefits for sample preparation since it increases homogeneity, increases surface area and decreases particle size which can improve extraction eficiencyTo achieve a uniform final particle size with minimal fines, the roller mill must have the right roll surface, roll speed ratio, and roll gap for your applicationRoller mills: Precisely reducing particle size with greater efficiency2023年10月27日 From the study, the optimal media size was 40 mm for a feed size of −2 + 045 mm and 30 mm for a feed size of −045 + 015 mm Cayirli also agrees with the fact that larger A Review of the Grinding Media in Ball Mills for Mineral Processing 2017年9月1日 Particle shape characteristics compared after grinding in ball mill or stirred mill Differences observed at laboratory scale but not at plant scale Particle shape and liberation Fine grinding: How mill type affects particle shape characteristics
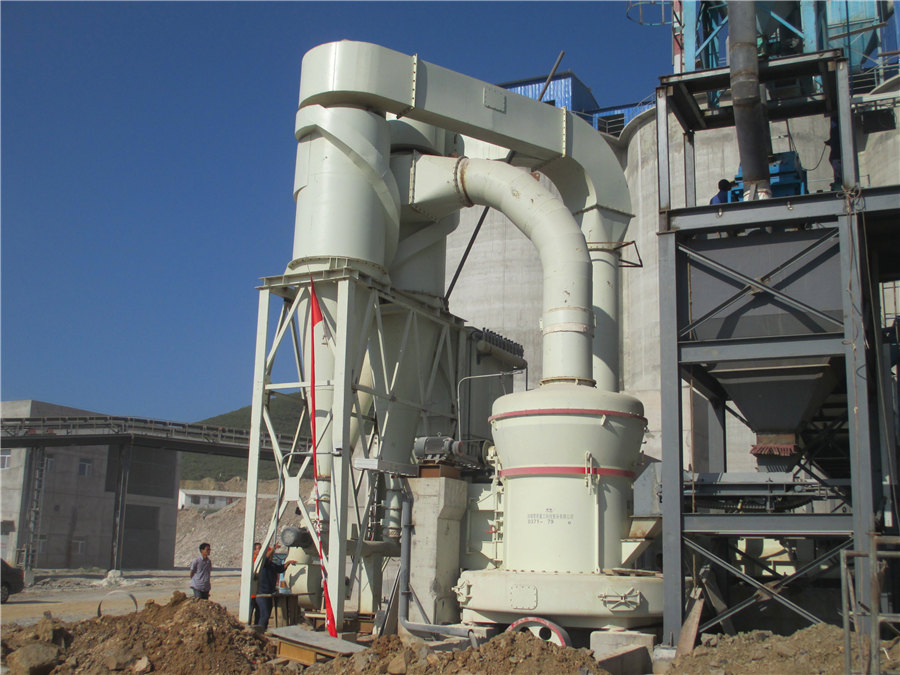
Disc Mills: Important Tools for Efficient Sample
2024年3月28日 Disc Mills, commonly known as grinding mills or disc mill crusher, are specifically designed to crush, grind, or pulverize solid materials These powerful machines employ rotating steel discs to exert intense grinding Grinding Mills Barry A Wills, James A Finch FRSC, FCIM, PEng, in Wills' Mineral Processing Technology (Eighth Edition), 2016 71 Introduction Grinding is the last stage in the comminution process where particles are reduced in size by a combination of impact and abrasion, either dry, or more commonly, in suspension in waterGrinding Mill an overview ScienceDirect Topicsrelative grindability and grinding kinetic analysis are used to elucidate the particle size distribution characteristics, and rules for achieving the ground product's particle size at lowspeed grinding Further, discussions are made on the grinding characteristics of the mill when the grinding medium is in the cascading motionResearch on the characteristics of particles size for grinding 2018年4月18日 Table 1 presents the results of two laboratory batch grinding tests, both performed at the same conditions (mill type, ball charge, pulp percent solids, feed size, etc) except for the total grinding times It can be observed that, in spite of the lower power consumption, the product D80 of test b is slightly finer than that of test aCrushing SAG Mill Critical Size Material 911Metallurgist
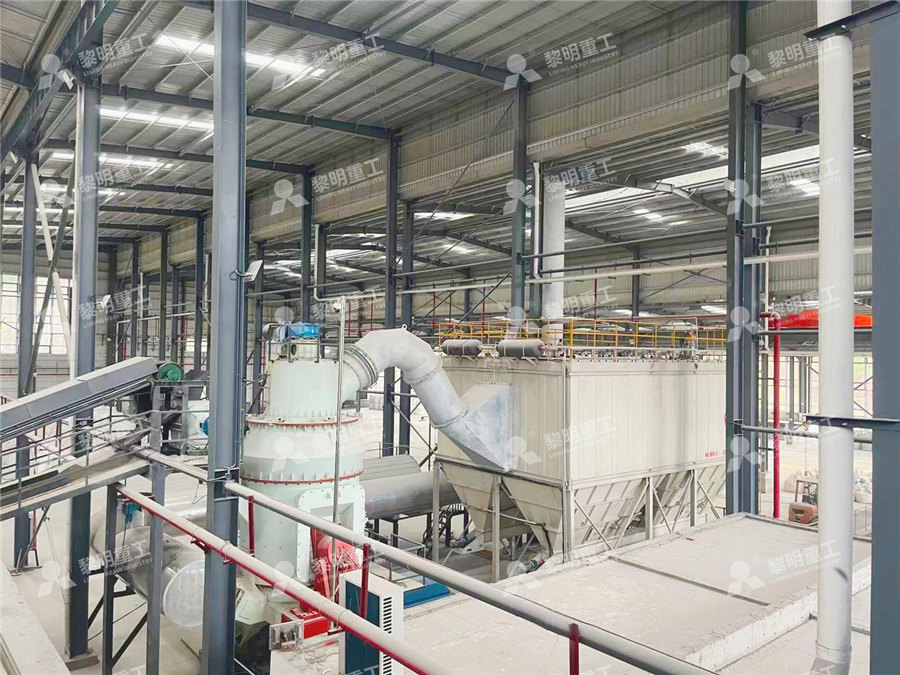
Singleparticle crush test for ultrafine particles and direct numerical
2021年5月1日 The singleparticle crush tests were performed under the conditions of a maximum loading speed of 2074 mN/s; to derive the loaddisplacement curve and determine the breakage force, F c, pressure was applied until the particles were crushedPortnikov et al reported on the effects of the loading speed on the singleparticle crush test results for glass 2017年3月4日 SIZE REDUCTION BY GRINDING METHODS ball mill can be either wet or dry grinding material at smaller particle sizes, and can be used after ball mills in a grin ding processSIZE REDUCTION BY GRINDING METHODS ResearchGatethe particle size distribution functions of a mill product Figure 112 provides the particle size distribution of a mixture of two plastic waste products After grinding, the particle size distribution changed to that shown in Figure 113 Clearly, the two different types of plastic displayed different behaviour during crushing Both were crushed:11 Crushing and classification2024年8月8日 Different materials, sizes, and densities of grinding media can significantly affect the energy transfer during milling, impacting the rate and uniformity of particle size reduction Consequently, this choice directly influences product quality, affecting characteristics such as purity, particle size distribution, and surface areaBall Mill Success: A StepbyStep Guide to Choosing the Right Grinding
.jpg)
AA04 Bauxite Particle Size Requirements for the Bayer
ball calculators and JKSimMet modelling Mill models can predict the size distribution of the mill product with reasonable accuracy Incremental improvements can also come from maintenance of key equipment which effects particle size, notably: lifter bar wear, grate hole wear, trommel wear, hydrocyclone and screen wear2019年1月1日 After some time, there seems to be little change in particle size if grinding is continued, though the particles may show some irreversible plastic What would be the consumption of energy needed to crush the same material of an average size of 75 The required operating conditions and size of mill can only be found by Particle Size Reduction and Enlargement ScienceDirectscale crushers to finer impact mills Table 2 gives the relative reduction of particle size from original material and the equipment needed Table 2 Particle size reduction comparison table Particle Size Reduction from Original Type of Equipment Large 25 x Crusher Medium 510 x Crusher Fine 1050 x Crusher or Mill Microfine 50100 x MillPrinciples of Sample Preparation by Grinding or Comminution2023年10月27日 From the study, the optimal media size was 40 mm for a feed size of −2 + 045 mm and 30 mm for a feed size of −045 + 015 mm Cayirli also agrees with the fact that larger balls can crush large particles better but at a lower grinding rate whilst smaller balls are unable to break large ore particles but grind smaller particles at a higher grinding rateA Review of the Grinding Media in Ball Mills for Mineral
.jpg)
Particle Size Conversion Chart Williams Patent Crusher
Mesh size refers to the number of openings in one inch of screen For example, a 4mesh screen means that there are four squares within one inch of the screen As the mesh size increases, the particle size decreases to create a finer 2024年7月2日 Operating conditions of the mill, power consumption of SAG mills, and different charge load actions also play a very significant role in this regard Also, the size and type of the grinding media used in the mill can also Choosing the Right Grinding Mill: SAG Mill vs Ball For sample preparation, Retsch's innovative and reliable grinding solutions can accommodate a broad spectrum of materials and applications When selecting a grinding mill, it's essential to define the intended use, the type of material to be processed, and the desired final particle size to ensure optimal resultsGrinding Mills for reliable size reduction tasks RETSCH2024年7月17日 They can crush low to medium hardness materials such as limestone and coal, as well as materials with moisture content below 15%, suitable for both dry and wet crushing Hammer crushers have a reduction ratio of up to 50, a feed size of up to 1,000 mm, and a maximum output capacity of 3,000 t/hTypes of Crushers: Choosing the Right One for Each Stage
.jpg)
Development of Size Reduction Equations for Calculating Energy
2013年1月1日 Grindability of pellets is defined as the resistance of a material to be ground into a certain size The grinding of raw white biomass pellets has extensively been investigated in several research 2017年9月1日 The first stirred mill was installed in the platinum industry in 2002, and by the year 2010, forty stirred mills had been installed at various platinum operations in South Africa, and these led to a step change in flotation recoveries (Rule, 2011, Rule, 2010)Over the last decade, approximately 200 Automated Scanning Electron Microscopy (AutoSEMEDS) systems have Fine grinding: How mill type affects particle shape characteristics 2016年6月6日 Also, precrush can lead to an increase in midsized material, overloading of pebble circuits, and challenges in controlling recycle loads In certain circuits, the loss of topsize material can lead to decreased throughput It is now widespread enough to be a standard circuit variant and is often considered as an option in tradeoff studiesSAG Mill Grinding Circuit Design 911MetallurgistHarder ores require more energy and longer grinding times, which can impact the mill's performance and operational costs 2 Media andliner Wear: The condition of the grinding media and liners affects the mill's efficiency Wear and tear can lead to a decrease in ball size and a corresponding decrease in mill performance 3Understanding the operation of grinding mills in the mining and
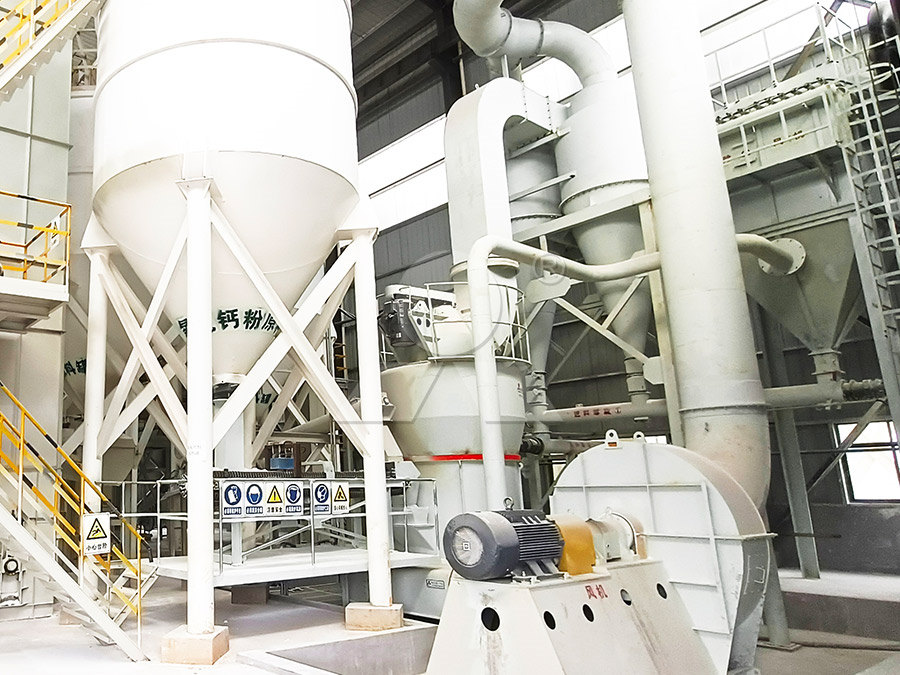
Size Reduction1: Grinding – Unit Operations in Food Processing
In a large ball mill the diameter of shell may be 3 m and 425m in length The balls are 15 to 125 mm in diameter; the pebbles in a pebble mill are 50 to 175 mm in size A tube mill is a continuous mill contain a long cylindrical shell2024年6月24日 Air classifying mill: Combining air classification with a dualstage grinding mill, Prater’s air classifying mill provides a singleunit design that uses space and energy more efficiently GSeries fullscreen hammer mill : Able to Particle Size Reduction: A Comprehensive Guide Prater2024年6月11日 In this study, the evolution behavior of the particle size distribution during the grinding process was examined with fractal theory According to the distribution index k of the Rosin–Rammler–Benne model, the Effect of Solid Concentration on Particle Size 2018年2月1日 Feed size was divided into two fractions of (+238 −4) and (+2 −238) millimeters, from which different feeds with different weight and size percent values were fed to mill at three feeds of Effect of ball and feed particle size distribution on the milling
.jpg)
What is Limestone Grinding Mill SBM Mill Crusher
2023年5月15日 Particle Size Requirements Particle sizes needed for various industries’ finished goods vary We should be able to achieve the necessary particle size distribution using the grinding mill we select Energy Efficiency A grinding mill’s energy use represents a considerable running expense, thus choosing one that is energy efficient is crucial2024年6月17日 You can use this hammer mill for dry chemicals, sugar and cement 2 Full Circle Screen A full circle hammer mill features a rotating screen to improve particle evacuation This hammer mill can be used to reduce the size of lightweight components that do not require any initial grinding, such as grasses, grain, sawdust, corn and spicesHammer Mill Types Explained Pulva Corporation2019年10月31日 In this study, we investigate the effect of the ball size in a highenergy ball mill on the comminution rate and particle size reduction The distribution pattern of particle sizes also varies upon grinding The particle size of asreceived talc shows a monomodal distribution ranging from ~3 to ~50 μm with a center at ~10 μmEffects of Ball Size on the Grinding Behavior of Talc Using a 2012年11月8日 wasted as heat and sound That makes particle size reduction perhaps the most inefficient process in modern society The amount of energy used for size reduction is evident across industries Notable examples include: agricultural (flour, grain mill products, rice milling, wet corn milling, etc), mineralBreakthrough in Clinker Grinding Massachusetts Institute of
.jpg)
Experiment 8 Size Reduction and Particle Size Measurement by Screen
Experiment8SizeReductionandParticleSizeMeasurementbyScreenAnalysis (1)pdf Free download as PDF File (pdf), Text File (txt) or read online for free This document describes an experiment conducted by students in the Chemical Engineering Department to measure particle size reduction through screen analysis It lists the student participants and instructor for 2021年8月26日 Consequently, jet mills can continue milling particles of glass until they reach the desired size, resulting in a glass powder with very little variation in particle size 5 Like ball mills, jet mills are capable of grinding glass powder down to submicron particle sizesGlass Milling Equipment and Techniques — MoSci Blog2024年8月12日 Time in Residence: Particle size reduction is also affected by the residence time of the material inside the grinding mill, which is influenced by the size and speed of rotation of it More thorough grinding and a smaller reduction in particle size Are Grinding Balls the Secret to Consistent Particle Size According to literature data, the above expression (Eq 5) can adequately describe the particle size reduction in between the interval 20100 μm [26,27] At a particle size of less than 20 μm, milling studies exhibit a progressive departure from a linear energysurface dependence This divergence is attributed to a decrease inPowder Ball Milling: An energy balance approach to particle size
.jpg)
Grinding: benefits of particle size modification Feed Strategy
2019年10月11日 The d 50 value is the average particle size of this particle size distribution This means that 50% of the particles are finer and 50% are coarser than d 50 (see figure 1, marked with a red line) Bulk materials with the same d 50 value 2023年6月22日 Figure 3: The particle size distribution from a roll crusher is more concentrated than the particle size distribution from a hammermill The main areas to consider with roll crushers are roll size, corrugations, roll speed differential, roll parallel and roll tramHammermill and roll crusher maintenance and operation2021年8月16日 As the particle size decreases with the grinding process Sun, Y; Ni, C; Xie, G Wet and dry grinding of coal in a laboratoryscale ball mill: Particlesize distributions Powder Technol 2019, 359, 305–313 [Google Scholar] Schuhmann, R, Jr Energy input and size distribution in comminution TransParticle Size Distribution Models for Metallurgical Coke Grinding 2024年6月17日 Time and energy savings: A custom hammer mill can crush or grind materials more efficiently than standard equipment, saving your company time and energy Cost savings: Investing in a custom hammer mill can also save money over time compared to the cost of using toll grinding services to have materials crushed by a third partyUnderstanding Hammer Mill Operation Pulva
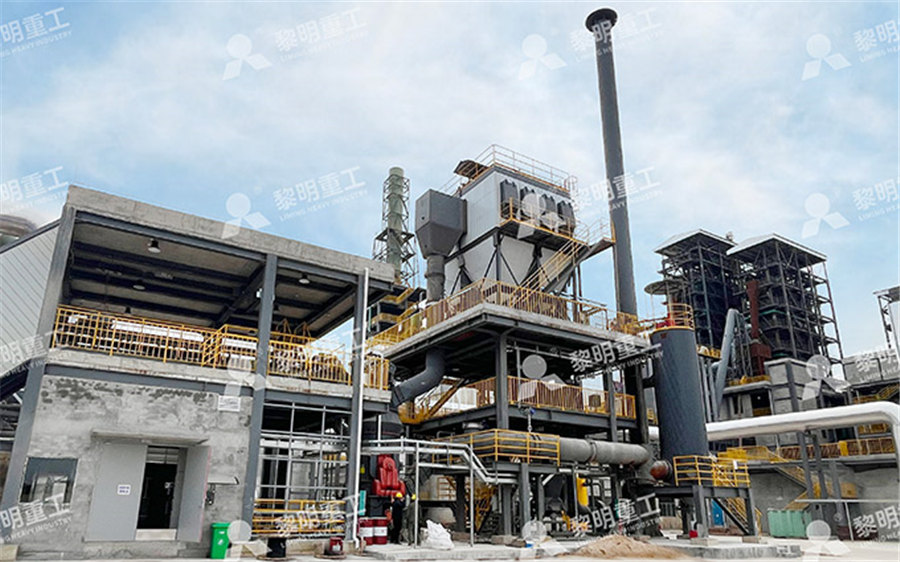
Bond Work Index FormulaEquation 911Metallurgist
2013年7月15日 What is the Bond Work Index FormulaEquation? In case you had forgotten, here is a classic: You can read all the details of this now “Biblical” grinding power requirement calculation formula in Fred Bond’s original paper You can also review the stepbystep Bond Work Index Test Procedure I posted here See this useful summary Table of Bond Work 2024年8月26日 The Extraction Process and Its Impact on Particle Size With all cannabis extraction methods, grinding your cannabis plant material to the ideal particle size is crucial to producing a highquality extract, combining flavor and potency, and reducing the number of undesirable compounds such as plant waxes and chlorophyll Each extraction method has its How to Grind Cannabis for Extraction Mobius2018年6月1日 The aim of the study was evaluate the influence of quinoa seed moisture content (10, 12, 14, 16 and 18%) and temperature (20, 3, 20 and 40°C, with the initial grain moisture content of 105%) on Effect of Moisture Content on the Grinding Process and Powder