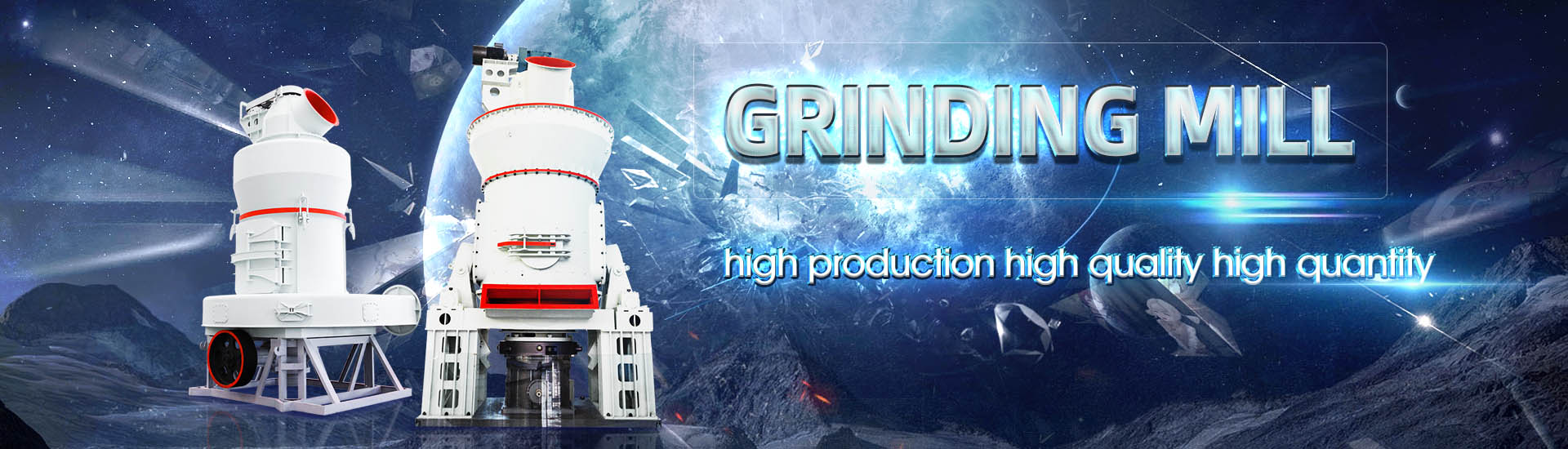
Efficient EnergySaving Cement Breaking Equipment

IMPROVING THERMAL AND ELECTRIC ENERGY EFFICIENCY AT
Association of Portland Cement (ABCP), the International Energy Agency (IEA), the Cement Sustainability Initiative (CSI) of the World Business Council for Sustainable Development (WBCSD), and IFC This report, and an accompanying report on alternative fuels, provide a 2013年3月1日 In this paper, energy saving measures in the cement industry, such as energyefficiency measures for the preparation of raw materials, production of clinker, and the An overview of energy savings measures for cement industries2021年3月30日 Improving production technology is a good strategy to reduce the energy needs of a cement plant The market offers a wide variety of alternative solutions; besides, the Technological Energy Efficiency Improvements in Cement Industries2020年3月1日 In the literature, technical characteristics like process specification, capacity enhancement, energy savings, CO2 emission reduction and quality enhancement have been A decision support tool for cement industry to select energy
.jpg)
A critical review on energy use and savings in the cement industries
2011年5月1日 It has been identified that sizeable amount of energy can be saved and emission can be reduced in raw materials preparation, clinker production, finish grinding, general areas, This report provides a summary of international best practice experience in the cement sector and focuses on specific technical measures that could be implemented by cement plants to reduce Improving thermal and electric energy efficiency at cement plants 2010年10月1日 Joint grinding system is the preferred cement grinding system of current cement process design, the advantages are high productivity, low energy consumption of system and Applications of Efficient EnergySaving Cement GrindingTables 2 through 8 provide the following information for each technology: fuel and electricity savings per tonne of cement; annual operating and capital costs per tonne of cement or Energy Efficiency Improvement Opportunities for the Cement
.jpg)
Towards Leveraging Artificial Intelligence for
2024年6月5日 By combining the equipment modeling approach with advanced machine learning techniques, the study demonstrated intelligent energy management strategies that can optimize electrical energy consumption and 2023年7月31日 The sustainable development and intelligent transformation of the manufacturing industry have become inevitable trends As a typical example of the intelligent transformation, the networked manufacturing mode has been A framework for energysaving selection and 2021年3月30日 ing cement production equipment, excluding managerial energy ‐ saving measures and measures related, for example, to the us e of waste fuels Moreover, the discussion excludesTechnological Energy Efficiency Improvements in Cement IndustriesThis efficiency reflects the power consumption of the mill only and does not include any auxiliary equipment like conveyors and dust collectors nor the separator 3 Conclusions Comparisons between different energyefficient grinding technologies and applications were presented for production of cement with energy savingsEnergyEfficient Technologies in Cement Grinding Academia
.jpg)
A New Design for Energy Saving in the Rotary Kilns of Cements
Therefore, improved energy efficiency can reduce cement production costs that can be achieved through energy management, by using more efficient processing equipment, replacing old facilities with new ones or by new types of cement production processes, carrying out the research and development needed to develop new cement plants An energy Where possible, for each technology or measure, costs and energy savings per tonne of cement produced are estimated and then carbon dioxide emissions reductions are calculated Savings (kgC/t) Efficient Transport System 34 > 10 (1) 078 Raw Meal Blending 1743 NA (1) 0410Energy Efficiency Improvement Opportunities for the Cement 2010年10月1日 Joint grinding system is the preferred cement grinding system of current cement process design, the advantages are high productivity, low energy consumption of system and low noise, etc It meets the industrial policy of domestic energysaving and reduction emission, so the development prospects is broadApplications of Efficient EnergySaving Cement Semantic PDF On Aug 1, 2013, Ernst Worrell and others published Energy Efficiency Improvement and Cost Saving Opportunities for Cement Making An ENERGY STAR® Guide for Energy and Plant Managers Find Energy Efficiency Improvement and Cost Saving Opportunities for Cement
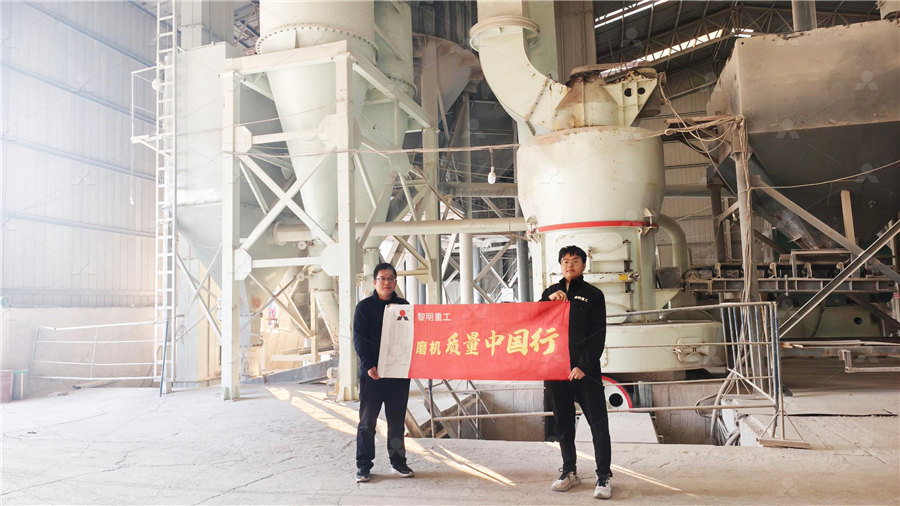
Energy Efficiency Improvement and Cost Saving Opportunities for Cement
Energy Efficiency Improvement and Cost Saving Opportunities for Cement Making An ENERGY STAR® Guide for Energy and Plant Managers Ernst Worrell and Christina Galitsky Energy Analysis Department Environmental Energy Technologies Division Ernest Orlando Lawrence Berkeley National Laboratory University of California Berkeley, California 94720Joint grinding system is the preferred cement grinding system of current cement process design, the advantages are high productivity, low energy consumption of system and low noise, etc It meets the industrial policy of domestic energysaving and reduction emission, so the development prospects is broadApplications of Efficient EnergySaving Cement Grinding 2019年3月8日 Savings in the Cement Industries,” Renewable and Sustainable Energy Reviews 15, no 4 (2011): 2,042–60 Figure 2 : Rotary Cement Kiln (Dry Process with Cyclonic Preheaters)IMPROVING THERMAL AND ELECTRIC ENERGY EFFICIENCY AT CEMENT 2020年1月4日 The article deals with the energy conservation achieved by adapting various energyefficient technologies and incorporating energyefficient operation Energy is one of the major inputs for the economic development of Energy conservation through energy efficient tech
.jpg)
EnergyEfficient Comminution: Best Practices and Future
2017年11月2日 The mining energy value chain starts at the face and extends to smelting and refining The main component of this value chain is comminution, which accounts for 53% of all energy used in the mining industry []For large openpit mines, comminution has been reported to account for up to 70% of all electrical energy consumed at a mine []2014年7月17日 How to account for VAT if you’re a contractor or subcontractor installing energysaving materials and grantfunded heating equipmentEnergysaving materials and heating equipment (VAT Notice offer significant potential for electrical and thermal energy saving in Indian cement industry today Total loss of latest generation coolers stands at less than 100 kCal/ kg clinker and has recuperation efficiency in excess of 75% Benefits: Thermal Savings : 30 kCal / kg Clinker Electrical Savings : 05 kWh / MT clinkerEverything you need to know about Thermal Energy Efficiency in Cement 2024年11月15日 As one of the largest energy consuming sectors in the world, the construction industry accounts for about 30 % of the world's total energy consumption, and the resulting carbon emission problem is becoming increasingly serious [1]In 2020, the total carbon emissions from the whole process of China's buildings were 508 billion tCO 2, accounting for 509 % of Thermophysical properties and energysaving efficiency of phase
.jpg)
8 main factors to save cost of cement manufacturing
There are several ways in which a cement manufacturer can save costs: Energy efficiency: Cement manufacturing is a energyintensive process Implementing energysaving measures such as using energyefficient equipment and optimizing the use of Great Wall Machinery provides energy saving and efficient equipment for the cement industry, including vertical roller mills, ball mills, and rotary kilns Vertical roller mills offer high grinding efficiency and lower energy consumption compared to ball mills Ball mills are widely used for grinding but can have high temperatures during operation Great Wall's double slipper ball mill Saving and Efficient Equipment For Cement Industry ScribdMaking investments in more energyefficient equipment and facilities to target significant energy loads across the value chain has the potential to deliver the most material reductions in energy use, albeit with longer payback periods than workforce engagement and smart control initiativesBecause the upgrading and replacement of energyconsuming equipment and Upgrading and replacing equipment and assets to improve energy 2013年10月17日 The old adage, “You can’t control what you can’t measure,” can truly be applied to energy management In the Rohrdorf cement works, energy consumption is measured by the Simatic S7 automation system, and stored in an SQL database This can then be evaluated, and displayed in Excel in either graphic or tabular formSaving Energy in a Cement Plant
.jpg)
Cement Kiln Thermal Efficiency: Strategies for Cost Savings and
Energy Storage Solutions: Integration of energy storage systems to capture and reuse excess heat generated during kiln operation Conclusion Optimizing thermal efficiency in cement kilns is not only a key performance indicator but also a significant driver of cost savings and environmental sustainability2 REVIEW FOR ENERGY SAVING IN CEMENT KILN 21 Modeling Balance of Cement Kiln The share of energy consumed in a cement clinker kiln plant attains 7078% of the overall energy consumed in the process of cement production as a whole The residual (2230%) is the share of electrical energy On the other hand,Different Possible Ways for Saving Energy in the Cement The effective use of these technologies will allow an energy and carbon manager to, among other things, monitor energy consumption and detect avoidable energy waste, provide realtime control adjustment, quantify the energy savings and reduce energy costsWhat is the role of energyefficient equipment and smart While the most direct influence factor is the choice of cement equipment In the past, people first used earth kilns to calcine clinker In 1877, the cement rotary kiln obtained a patent for calcining cement clinker, more and more efficient, Cement Manufacturing Machine Cement Making
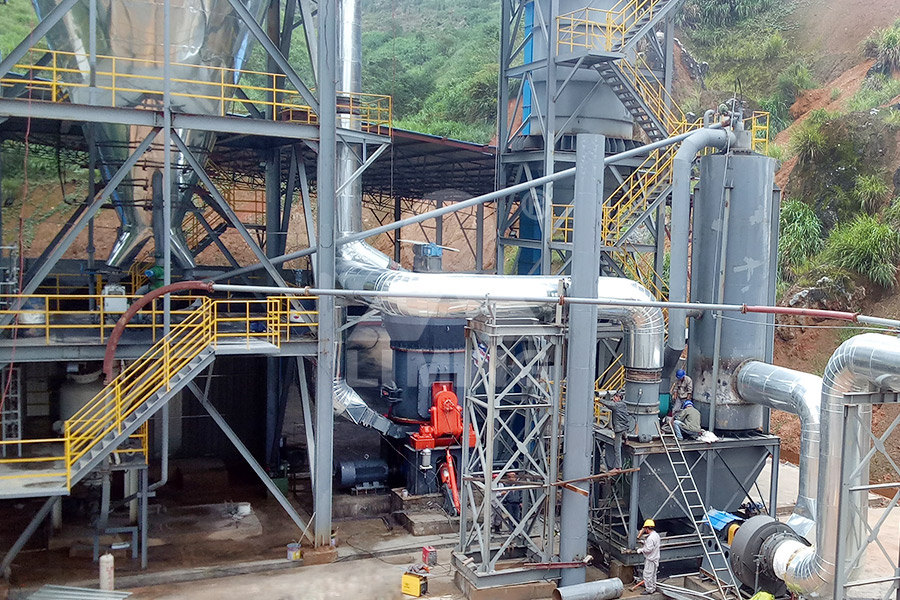
Energy Efficiency Improvement Opportunities for Cement Making An ENERGY
2004年1月1日 We examined over 40 energy efficient technologies and measures and estimated energy savings, carbon dioxide savings, investment costs, and operation and maintenance costs for each of the measuresMany people work from home at least one day per week Working from home saves energy and time by cutting out the commute, but it may increase your home energy bills unless you use energysaving office equipment ENERGY STARlabeled office equipment is widely available It can provide dramatic energy savings—as much as 75% savings for some Energy Efficient Computers, Home Office Equipment, and Energy efficiency is called the “first fuel” in clean energy transitions, as it provides some of the quickest and most costeffective CO2 mitigation options while lowering energy bills and strengthening energy security Together, efficiency, electrificatiEnergy Efficiency Energy System IEA International Energy 2022年7月18日 Decarbonization strategies for the cement and concrete sector have relied heavily on supplyside technologies, including carbon capture and storage (CCS), masking opportunities for demandside Efficient use of cement and concrete to reduce reliance on
.jpg)
Comprehensive Guide to Cement Kilns: Processes, Types,
Equipment used in this stage Word count: 1000; Section 2: Types of Cement Kilns Energy Savings: Both processes require less energy for drying compared to the wet process The efficient operation of a cement kiln relies on the precise control of various operational parameters Key Parameters2024年4月8日 Mechanical and Thermal Properties of an EnergyEfficient Cement Composite Incorporating equipment to maintain comfortable indoor climate parameters Energysaving technologies, materials Mechanical and Thermal Properties of an EnergyEfficient Cement 2021年4月20日 They use less energy, perform faster and have been proven to be comparatively easy to operate Investing in similar powersaving equipment used in cement manufacturing units can reduce electricity consumption and wastage of resources, while also boosting productivity EnergyEfficient Process ControlsSaving Energy in Cement Plants: 3 Ideas Worth ConsideringDownload Citation On Oct 5, 2016, Ömürden Genç published EnergyEfficient Technologies in Cement Grinding Find, read and cite all the research you need on ResearchGateEnergyEfficient Technologies in Cement Grinding ResearchGate
.jpg)
A Case for EnergyEfficient Motors Indian Cement Review
2017年4月30日 Financial constraints: The cost of implementing green technology is high, creating economic challenges, particularly for smaller cement manufacturers Equipment upgrades, energyefficient kilns, and carbon capture facilities require considerable investment, which many companies find difficult to justify without strong financial incentivesThe cement industry in Uganda is not a major emitter However, demand is growing, and production is projected to increase significantly over the next 20 years Investing in key energy efficiency management strategies such as switching to lowercarbon fuels and promoting material efficiency presents economic and energysavingPolicy Brief: Prospects for Energy Efficiency in Uganda Cement 2017年1月17日 For new applications, t aking advantage of more energy efficient processing equipment (eg high pressure grinding rolls , crushers ) ( Morrell, 2009 ; Nordel l et al, 2016 ; Van Der Meer and Breaking down energy consumption in industrial grinding mills2021年10月14日 The major cost factor in a cement factory is no longer the primary fuel but electric energy, due to the increasing use of secondary fuels, Although many energysaving measures have already been considered and implemented, the search for further solutions continues to counter increasing power costs Siemens suggests some areas to consider New Saving Electrical Energy Indian Cement Review
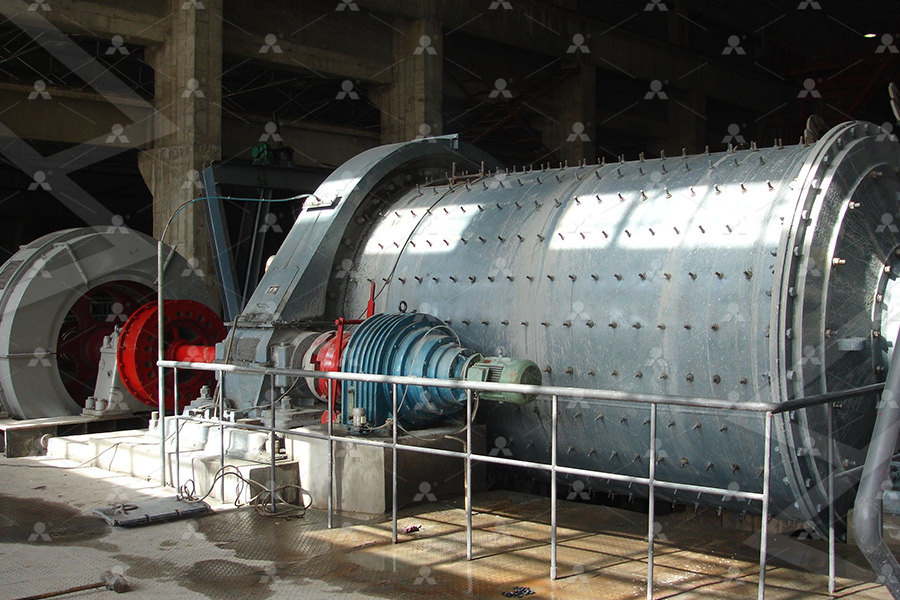
A critical review on energy use and savings in the cement industries
2011年5月1日 The cement subsector consumes approximately 12–15% of total industrial energy use Therefore, a state of art review on the energy use and savings is necessary to identify energy wastage so that necessary measures could be implemented to reduce energy consumption in this subsector2007年5月1日 null THE ENVIRONMENTAL IMPERATIVE Given the energyintensive nature of the cementmanufacturing process, it is perhaps not surprising that a twentieth of the world’s manmade CO 2 emissions can be traced to a single industry: cement About half of these emissions are a necessary byproduct of the chemical reaction essential in transforming the raw material Concrete energy savings – onsite power for the world’s cement In our experience, 10% of the energy savings can be achieved with small investments that will pay back within 1 year Another 10% savings can be achieved with medium levels of investments and with payback periods of less than 2 years Higher cost investments can achieve a further 10%20% energy savings with typical paybacks of less than 4 yearsENERGY EFFICIENCY – CEMENT 2024年6月27日 Score: 94/100 Energy consumption over an hour: 078kwh Cost to run per hour: £017 Energy rating: A+ Miele’s 71litre capacity oven achieved a perfect score for ease of use in the GHI lab Best energy efficient appliances 2024 UK Good Housekeeping
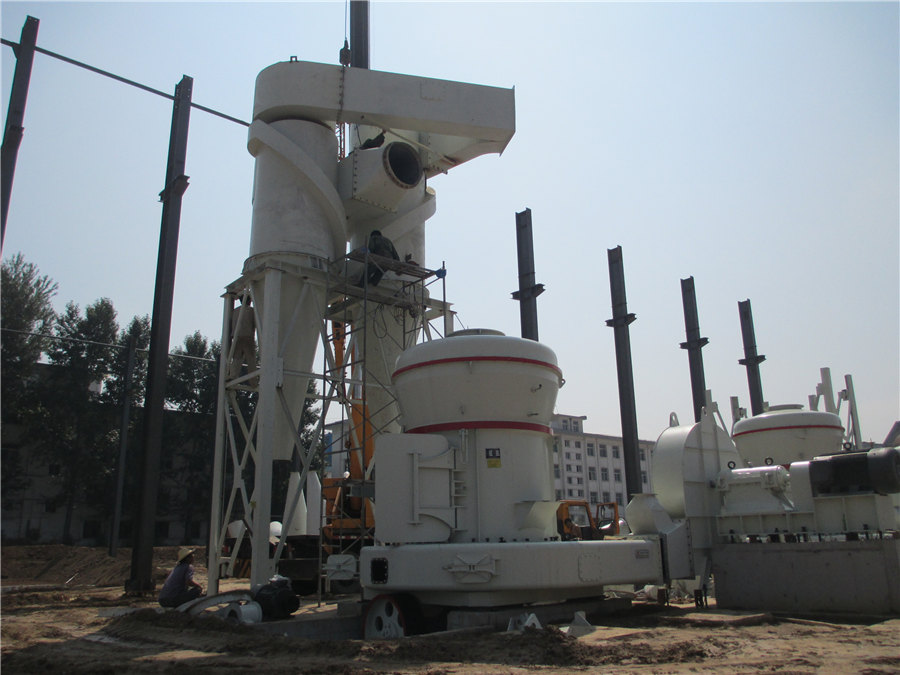
Modern Processing Techniques to minimize cost in Cement
The mill can be used for pregrinding and finish grinding This millsystem claims to have advantages of ball mill, roller mill and roller press in terms of reliability and energy savings The energy saving is claimed to be similar to roller press, around 20 % less compared to ball mill, but with a moderate circulating load and grinding pressure