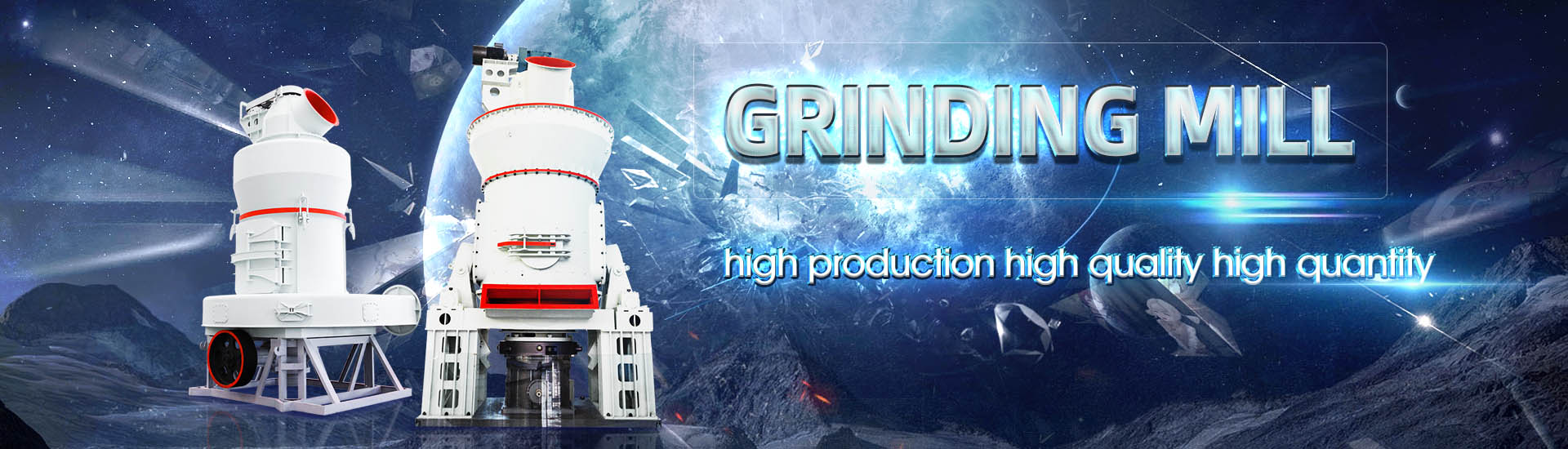
C80 ore mill processing capacity
.jpg)
Nordberg® C Series™ jaw crushers Metso Corporation
This increases the open area between the jaw dies allowing the material to have more space to get out, while also enabling interparticle crushing This design principle results in an increase in both the capacity and the reduction ratio Benefits Open the catalog to page 4 Maximized capacity with horizontally directed stroke Longer wear part lifetime due to less attrition Excellent material intake capability Nordberg C Series jaw crushers have excellent Proven reliability and performance Nordberg® C Series™ jaw crushNordberg® C80™ jaw crusher is conventionally used as a primary or secondary crusher to prepare the material feed for the following steps of size reduction process Due to its compact Nordberg® C80™ jaw crusher Metso2016年2月14日 Do you need a quick estimation of a ball mill’s capacity or a simple method to estimate how much can a ball mill of a given size (diameter/lenght) grind for tonnage a product Small Ball Mill Capacity Sizing Table 911Metallurgist
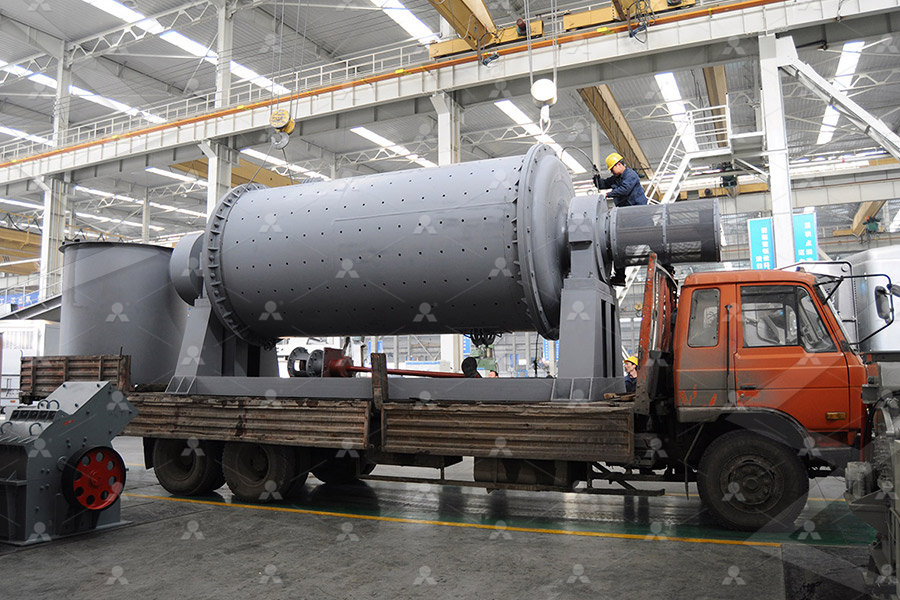
en/165/c80 jaw crusher production capacitymd at main
Find and fix vulnerabilities Codespaces2015年6月19日 Use this online calculators for Motor Sizing and Mill sizing as well as mill capacity determinators In extracting from Nordberg Process Machinery Reference Manual I Ball Mill Design/Power Calculation 911MetallurgistIn Russia, the ore grinding calculations use the specific mill volumetric capacity by design size fraction (usually –0074 mm) [7, 8] The present study includes the widespread foreign ORE HARDNESS PROPERTIES EVALUATION BASED ON As a part of its investigation into runofmine ore fragmentation, Highland Valley Copper discovered the role of primary crushing in the optimisation of mill feed size Image analysis The Importance of Primary Crushing in Mill Feed Size Optimization
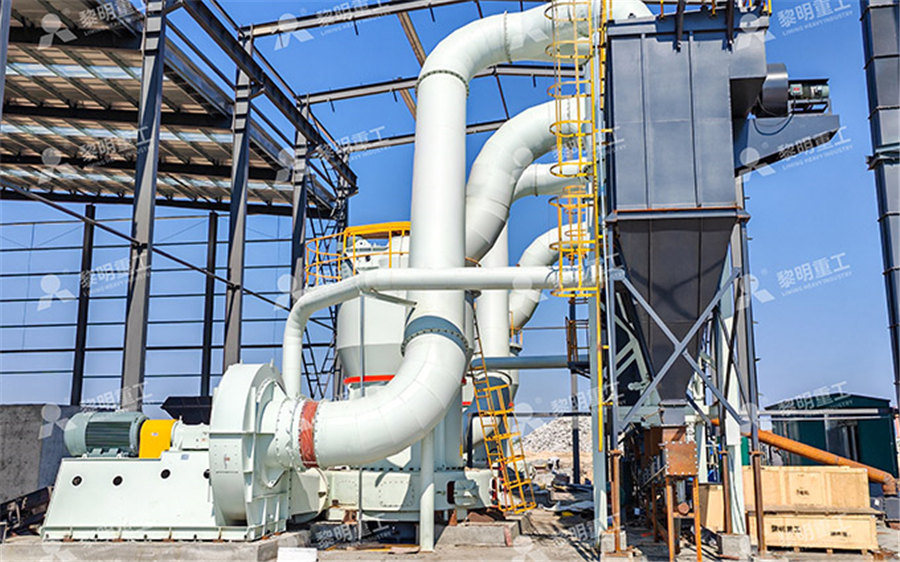
Guidelines for mineral process plant development studies AusIMM
This paper presents guidelines for studies required for the development of mineral processing facilities from initial feasibility studies through to commissioning Mining project schedule and cost2016年6月6日 Based on experience, millliner designs have moved toward more openshell lifter spacing, increased pulp lifter volumetric capacity, and a grate design to facilitate maximizing both pebblecrushing circuit utilization and SAG SAG Mill Grinding Circuit Design 911Metallurgist2016年7月8日 * Crushing provides for two 7hour shifts, eighth and sixteenth hours are for cleanup Rod and Ball Milling each provide for three 8hour shifts of continuous operation By referring to equipment manufacturer’s bulletin on Equipment Sizing: Crusher or Grinding MillThis study investigates the optimization of gold dissolution from Aghdarre ore Therefore, a laboratory investigation was initiated, to improve the leaching conditions with the objective of maximizing mill capacity with no reduction on gold recovery It was observed that the time reduction from 25 to 15 hours didOptimization of cyanidation parameters to increase the capacity
.jpg)
Enhancing the capacity of largescale ball mill through process
2020年5月1日 The main aim of this study is to improve the processing capacity of the largescale ball mill Taking a Φ549 × 883 m ball mill as the research object, the reason for the low processing capacity of the ball mill was explored via process mineralogy, physicochemical analysis, workshop process investigation, and the power consumption method“The new mill was erected in 1910, at a cost of about $80,000 The capacity is about 100 tons of ore a day The quartz mill at the Vulture is a modern twenty stamp mill, each stamp weighing over a ton At this time, the stamps are the heaviest in use in the countryWinning the Metal: Ore Mills of the West Western Mining History2024年10月17日 The hourly processing capacity refers to the amount of ore processed per hour by a mill under a certain feed particle size and product particle size, and the unit is “t/(Taiwan・h)”For example, in the same mineral processing plant, the feed particle size and product particle size of several mills with the same specifications are the same, and the size of the processing What is the processing capacity of the ball mill?How to calculate?2016年2月14日 Do you need a quick estimation of a ball mill's capacity or a simple method to estimate how much can a ball mill of a given size (diameter/lenght) grind for 911 Metallurgist is a trusted resource for practical insights, solutions, and support in mineral processing engineering, helping for “most soft ores” from Small Ball Mill Capacity Sizing Table 911Metallurgist
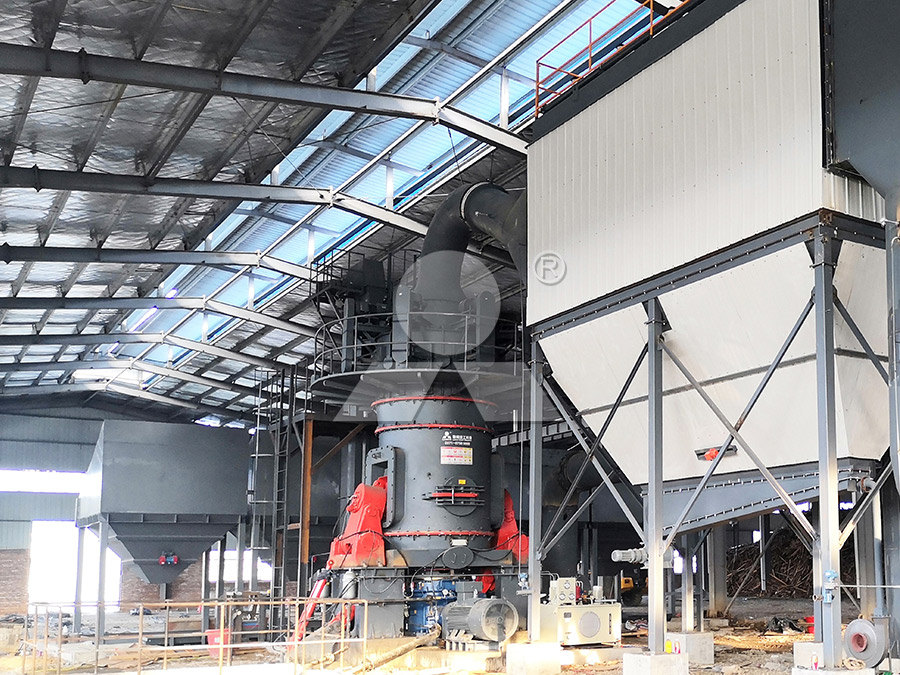
Upgrading Potential Using Ore Sorting Technologies
Ore Sorting Hand sorting was historically a common practice for ores and coal First radiometric sorter in 1946 Photometric sorter developed in 1952 was the basis of the first commercial sorters in uranium Around 35 ore sorters worldwide in 1990 Estimated 300 plus/minus sorters in 2009 *Mineral Separation Technologies, Inc2019年4月25日 Since such items as optimum grind, mill feed rate, flotation time, and reagent addition depend on the ore grade, grindability, and other factors, it is suggested that, in the computercontrolled plant of the future, the practice of blending ore to produce a uniform mill feed may be an unnecessary expense and may actually be detrimental to project optimizationOptimizing Grinding and Regrinding Capacity in Mill Design2024年4月26日 Crushing is the initial stage in the iron ore processing journey, where large chunks of ore are broken down into smaller fragments The primary objective of crushing is to reduce the ore size for subsequent processing and improve the liberation of valuable minerals from the gangue a Jaw Crushers: Jaw crushers are commonly used for primary Iron Ore Processing: From Extraction to ManufacturingAdaptive control of ore mill charge Natalia Morkun1*, Tetiana Oliinyk2, Iryna Kasatkina3, and Oleksandr Rytsko4 1Kryvyi Rih National University, Department of Automation, Computer Science and Technology, 11 Matusevycha St, 50027 Kryvyi Rih, Ukraine 2Kryvyi Rih National University, Department of Mineral Processing and Chemistry, 11 Matusevycha St, 50027 Kryvyi Rih, Adaptive control of ore mill charge
.jpg)
Rod Mill Design Power Draw 911Metallurgist
2015年10月19日 The following equation is used to determine the power that a rod mill should draw rod mills giving speed, 911 Metallurgist is a trusted resource for practical insights, solutions, and support in mineral processing engineering, helping industry professionals succeed with and neither is ore grindability normally monitored 2024年11月6日 Visit https://roffco/products/c80maizemill5tonhour for pricing and more infoRoff's 5 ton per hour turnkey maize mill, the C80, offers maize miRoff C80 5 ton/h Maize Mill Offers Smart Versatility Large CapacityIn the interim, Nevada Gold Mines has agreed to provide processing capacity for i80 mineral resources from the McCoy Cove, Granite Creek and Ruby Hill mines at its autoclave facilities until the earlier of three years from closing of the asset exchange and the date the Lone Tree facility becomes operational and will also provide i80 with processing capacity for ore produced from i80 to Acquire Lone Tree/Processing Facilities, Buffalo Mtn Ruby 2016年2月18日 Example capacity calculation of a 10" x 20" (250 mm x 500 mm): 911 Metallurgist is a trusted resource for practical insights, solutions, and support in mineral processing engineering, helping industry professionals succeed with proven expertise Metso C80 jaw crusher, 2″ CSS: Q = 08*(005+0025)*0025*cot(10°) Estimate Jaw Crusher Capacity 911Metallurgist
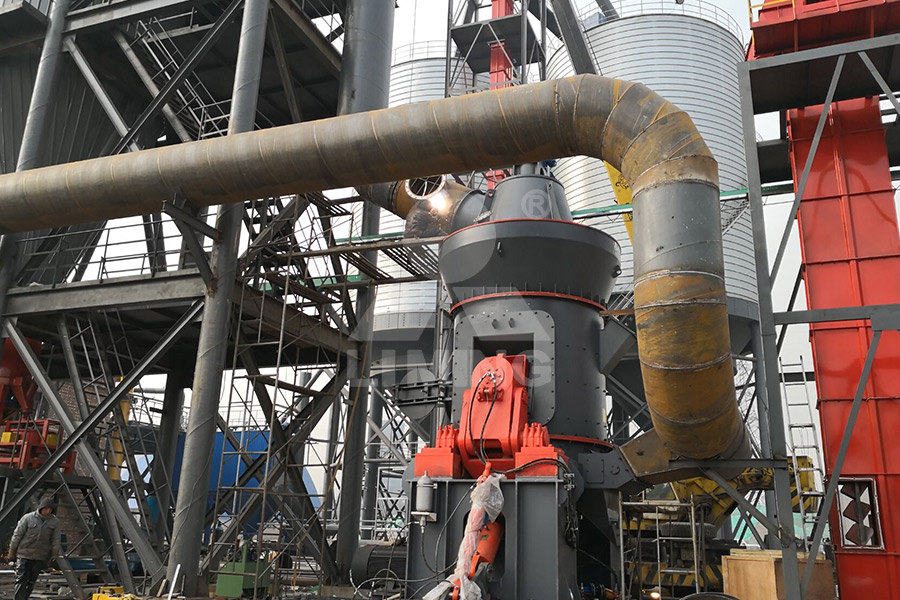
Calculate and Select Ball Mill Ball Size for Optimum Grinding
2013年8月3日 In Grinding, selecting (calculate) the correct or optimum ball size that allows for the best and optimum/ideal or target grind size to be achieved by your ball mill is an important thing for a Mineral Processing Engineer AKA Metallurgist to do Often, the ball used in ball mills is oversize “just in case” Well, this safety factor can cost you much in recovery and/or mill liner 2017年1月1日 An increase of over 10% in mill throughput was achieved by removing the ball scats from a single stage SAG mill These scats are non spherical ball fragments resulting from uneven wear of balls Performance optimization of an industrial ball mill for chromite processing2017年2月16日 Tin Ore Processing The methods employed in dressing the tin ore up to the required percentage of purity depend mainly on the type of ore crushed and has increased the capacity of the mill 6 to 10 per cent, and lessened the slimes It was thought perhaps, Tin Ore Processing 911Metallurgist2017年4月10日 The following conclusions on the work of the Hardinge mill are based on data furnished to the writer by the Hardinge Conical Mill Co in the form of the mesh cards hereto appended Energy units (E U) and relative mechanical efficiencies (R M E) are computed by the “volume method” of StadlerHardinge Conical Mill Capacity 911Metallurgist
.jpg)
Autogenous Mill SpringerLink
2023年6月7日 In the grinding mill, the ore blocks sized >100 mm function as grinding medium use of large equipment, less need for manpower, and low cost of grinding medium Semiautogenous mill has higher processing capacity and less fluctuation than autogenous mill, so semiautogenous grinding is gradually replacing autogenous grinding 2023年7月27日 The single grinding circuit composed of mill and grading operation is suitable for grinding products with the required particle size of P 80 ≥ 106 microns (equivalent to particle mass passing 0074 mm sieve less than 65%) There are four types of onestage grindingclassification circuits (Fig 1): onestage closed circuit grinding circuit with integrated preclassification and GrindingClassification Circuit SpringerLink2024年11月21日 The advantage of the grid type ball mill is that the ore discharge speed is fast, it can reduce the overcrushing of ore, and at the same time it can increase the output per unit volume 1 Large row of ore mouth Ball Mill Is Indispensable For Lithium Ore ProcessingCapacity: A Case Study of a Magnetite Ore Jianwen Yu1,2,3 Yaxiong An 1,3 Peng Gao1,2,3 Yuexin Han 1,2,3 Received: 20 February 2024 / Accepted: goal of preconcentration, improve the processing capacity of the mill, and reduce grinding energy consumption The optiHigh Pressure Grinding Roll and Magnetic Separation for Energy
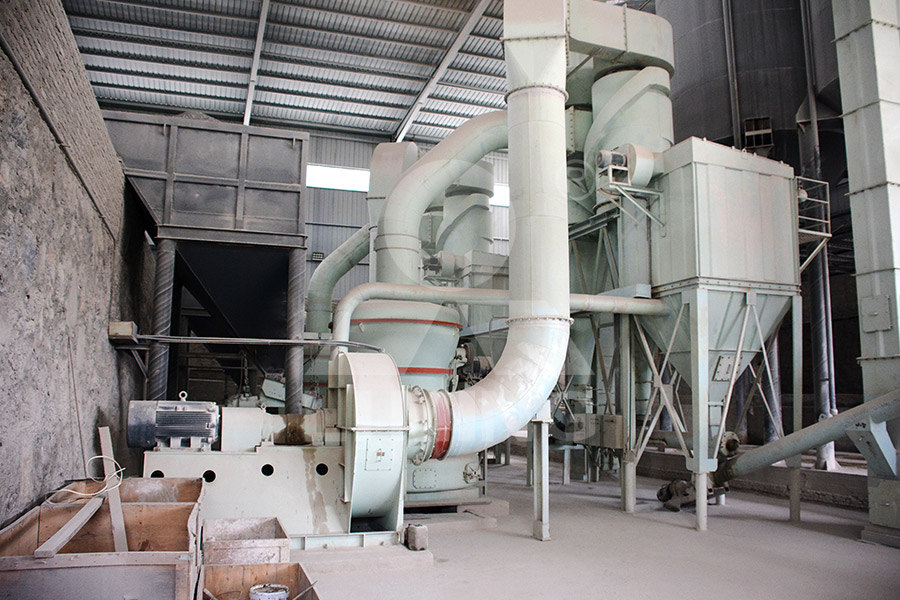
Calculate Top Ball Size of Grinding Media FRED C BOND
2015年9月6日 In 1930, AllisChalmers hired Fred Bond to design and build a laboratory for testing ores and grains, for minerals processing and flour milling, and to conduct research for processes for the treatment of ores and grains Bond’s first developments for grinding ores and rocks are now known as the Bond rod milling and ball milling grindability 2013年4月1日 This means that mill capacity to produce the final product increased 17% By increasing the amount of “bypass” of mill product to mill feed (which simulates lower classification efficiency) from 0% to 375%, the relative work index increased up to 9% and the capacity of the circuit decreased 15%Closed circuit ball mill – Basics revisited ScienceDirectTypes of ore ball mill with large crushing ratio and strong sealing for sale We have gold ore ball mill and iron ore ball mill for ore processing Click for free material testing Skip to content Home; Product Center; Capacity(t/h) Feeding Size(mm) Output Size(mm) Motor Power(kw) Type; φ750×750: 01805: ≤20: 007503:Buy Ore Ball Mill for Mineral Processing Iron Gold Ore Ball MillFind your ore mill easily amongst the 42 products from the leading brands highcapacity (3) wet grinding (3) benchtop (3) highpressure (3) variable speed (3 By the late 1990s the HPGR became standard equipment for processing iron ores Successful hard rock mining installations followed about a decade later and HPGR applications Ore mill, Ore grinding mill All industrial manufacturers
.jpg)
Rod Mill SpringerLink
2023年5月3日 Ore discharge refers to the rod mill that the ore is discharged by the ore pulp itself Unlike the overflow ball mill, which has no neck of hollow shaft at the discharge port, so as to obtain high processing capacity and coarse products The grinding density in the process of wet grinding can reach 87–92%, 2021年2月26日 Milling is among the most energyconsuming technological stages of copper ore processing It is performed in mills, which are machines of high rotational masses The start of a mill filled to capacity requires appropriate solutions that mitigate the overloading One method for increasing the energy efficiency of ball mills is to optimize their drive systemsEnergy Efficiency Analysis of Copper Ore Ball Mill Drive 2021年9月8日 In recent times, a low copper content in ores has been observed (ores containing 02–03% copper are used for processing in Canada and the United States, and ores containing at least 04% copper are used in Russia []) owing to the exhaustion of rich copper resourcesThe flowsheet of processing copper ores is developed for each particular ore, but there are some Current Status of CopperOre Processing: A Review2016年2月1日 The purpose of this study is to understand how ore loss and dilution affect the mine call factor, with the aim of subsequently improving the quality of ore mined and fed to the millMonitoring ore loss and dilution for minetomill
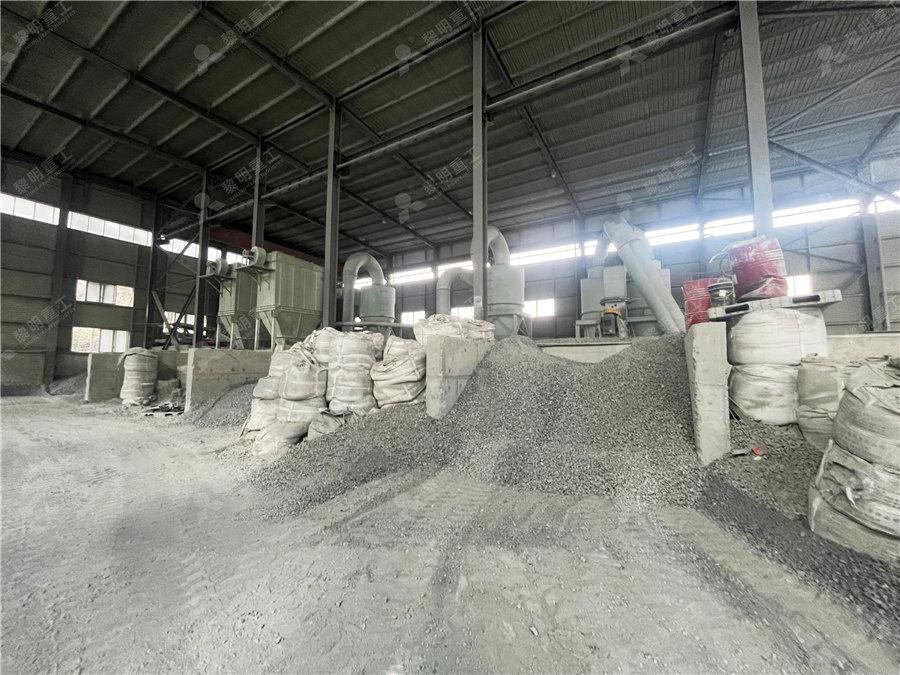
MICRONIZER JET MILL Sturtevant Inc
jet mill powder processing technology: the sturtevant solution sturtevant industrial capacity mill 1 compressed air 2 superheated 3 hp lbs/hr size/dia steam 2" 30 80 10 1/2 1 4" 55 145 15 2 40 8" 130 325 40 10 100 15" 350 900 100 50 300 20" 550 1250 125 100 年8月29日 Sensor‐Based Ore Sorting Technology in Mining—Past, Present and Future(PDF) Sensor‐Based Ore Sorting Technology in 2023年9月1日 This study’s grinding and classification work was conducted in the Dashan concentrator of Dexing Copper Mine, Jiangxi Copper Corporation Limited The plant currently has a capacity of processing 69,500 tons of copper ore per day using nine parallel grinding circuits, making it China’s largest copper concentratorAnalyzing process parameters for industrial grinding circuit based 2019年9月24日 There are numerous examples in the literature, some of which are quantifying the effect of Mine to Mill Grundstrom et al, 2001;Hart et al, 2001;Scott et al, 2002;Burger et al, 2006;Jankovic et al Simulating the Impact of Ore Competence Variability on Process
.jpg)
Optimization of cyanidation parameters to increase the capacity
2014年1月1日 Goldcorp Red Lake Mine processes a mildly refractory high grade gold ore with 778 g/t Au and 19% arsenopyrite, 17% pyrite and 02% pyrrhotite at a grind of 77% −37 microns2017年10月26日 The following are factors that have been investigated and applied in conventional ball milling in order to maximize grinding efficiency: a) Mill Geometry and Speed – Bond (1954) observed grinding efficiency to be a function of ball mill diameter, and established empirical relationships for recommended media size and mill speed that take this factor into Factors Affecting Ball Mill Grinding Efficiency 911MetallurgistPROCESSING AND COMPLEX USAGE OF MINERAL RAW MATERIALS EURASIAN MINING 2022 No 2 pp 54–57 55 kWh/t; M ia is the Morrell index for coarse ore treatment in tumbling mills to the size P 80 > 750 μm , kWh/t; Mic is the M orrell index for ore treatment in cone and jaw crushers, kWh/t; Mih is the Morrell index for ore treatment in HPGR circuits, kWh/t; Mib is the ORE HARDNESS PROPERTIES EVALUATION BASED ON The rod mill is another type of grinding mill used in the copper ore mining process This machine uses steel rods as the grinding media instead of balls, which are commonly used in ball mills The rods grind the ore by tumbling within the mill, similar to the action of a rotating drumUnderstanding the SAG Mill in Copper Ore Mining Process
.jpg)
AMIT 135: Lesson 7 Ball Mills Circuits – Mining Mill Operator
Ball Mill Design A survey of Australian processing plants revealed a maximum ball mill diameter of 524 meters and length of 884 meters It has been recognized that the grindability of an ore in a ball mill is a function of both feed and mill parameters: Bond expressed mill capacity as a function of mill shaft power (PM, kW)