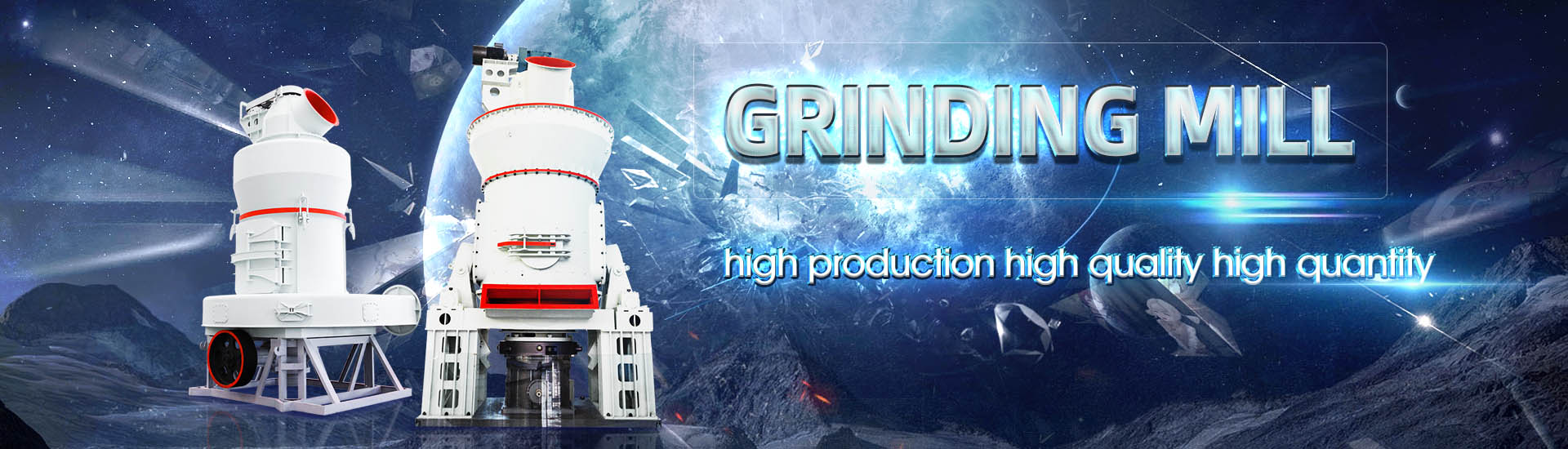
Ore mill rotation direction Ore mill rotation direction Ore mill rotation direction
.jpg)
Directional Milling Guide: Which Direction to Mill?
2024年1月3日 Choosing the correct milling direction is paramount in achieving precise cuts and exceptional surface finishes By carefully considering factors such as feed rate, workpiece orientation, and cutter selection, operators can The speed of rotation of the mill determines three basic types of operation modes: slow rotation (cascading), fast rotation (cataracting) and very fast rotation (centrifugation) Each type is Grinding in Ball Mills: Modeling and Process Control Sciendo2003年7月14日 Runs an ordinary 5C collet right in the spindle Regular rotation (forward on the stick) has the spindle turning CCW as viewed from the front which means regular end mills Proper rotation direction for a horizontal mill? Practical MachinistAbstract – The present paper aims to investigate the key points of kinematic of contents inside the mill (load orientation), namely the shoulder, toe, impact, and pool angles The kinematic of the Experimental observations of mill operation parameters on
.jpg)
Basics of End Mills UNION TOOL
Direction of rotation Feeding Direction The amount of feed per tooth fz [mm/t] is calculated by dividing the amount of feed per rotation by number of tooth (flutes) which contributes for millingsimple and novel nonlinear model of a runofmine ore grinding mill circuit, developed for process control and estimation purposes, is validated The model makes use of the minimum number Analysis and validation of a runofmine ore grinding mill circuit 2013年4月1日 A simple and novel nonlinear model of a runofmine ore grinding mill circuit, developed for process control and estimation purposes, is validated The model makes use of Analysis and validation of a runofmine ore grinding mill circuit 2004年12月1日 The PBM process is most effective when the milling conditions, such as rotational speed, milling time, balltomaterial ratio, number, size, and material of the grinding Optimum revolution and rotational directions and their speeds in
.jpg)
ENERGY EFFICIENT GRINDING MILLS ABM Proceedings
When grinding mill rotates in clockwise direction, the pulp lifter essentially has the possibility to discharge its contents starting from 9’O clock and complete latest by 3’O clock position If the Climb vs Conventional Milling When milling, one should be aware of the difference between conventional, and climb milling In conventional milling, the workpiece is fed into the rotation of Introduction to the Mill MIT OpenCourseWareThe history and necessity of mechanical alloying M Sherif ElEskandarany, in Mechanical Alloying (Second Edition), 2015 2515 Planetary ball mills The Planetary ball mills are the most popular mills used in MM, MA, and MD scientific researches for synthesizing almost all of the materials presented in Figure 11 In this type of mill, the milling media have considerably high Ball Mill an overview ScienceDirect Topics2002年7月1日 Download Citation Effects of rotational direction and rotationtorevolution speed ratio in planetary ball milling The rotational direction of a pot in a planetary ball mill and its speed Effects of rotational direction and rotationtorevolution speed

UNDErsTaNDINg MINE TO MILL 911 Metallurgist
Understanding Mine to Mill is presented in five parts Part A – Setting the Scene provides some definitions of Mine to Mill (M2M) and the historical background A chronology of Mine to Mill developments is followed by brief descriptions of the very wide range of Mine to Mill applications which have been implemented over the last 15 years2002年7月1日 Threedimensional motion of the media balls in the mill was simulated by the DEM method proposed in previous works [21]Young's modulus and Poisson's ratio of the ball in the simulation of the present work are 210 GPa and 030, respectivelyEffects of rotational direction and rotationtorevolution speed content is uniform and thoroughly mixed by the rotation of the mill and the movement of the grinding media [44] In this case the model is known as a perfectly mixed model In some cases the mill’s charge is considered to be perfectly mixed in the radial direction and only partially mixed in the axial direction AnotherGrinding in Ball Mills: Modeling and Process Control Sciendo2017年6月15日 Request PDF Friction and wear of liner and grinding ball in iron ore ball mill roller rotation rate, steel ball or steel rod, and so on [16] [17][18][19 Friction and wear of liner and grinding ball in iron ore ball mill
.jpg)
Research of iron ore grinding in a verticalrollermill
2015年3月15日 VRM has been widely researched in processing of cement (Ito et al 1997;Jorgensen 2005;Wang et al 2009, Ghalandari et al 2021), coal (Tontu 2020), iron ore (Reichert et al 2015), zinc ore (van 2023年1月1日 DOI: 101016/japt2022 Corpus ID: ; Size reduction performance evaluation of HPGR/ball mill and HPGR/stirred mill for PGE bearing chromite ore @article{Santosh2023SizeRP, title={Size reduction performance evaluation of HPGR/ball mill and HPGR/stirred mill for PGE bearing chromite ore}, author={T Santosh and Chinna M Size reduction performance evaluation of HPGR/ball mill and 2011年2月1日 In contrast, for SAG mills which were first modelled by Rajamani and Mishra (1996) and subsequently by others (Cleary, 2001a, Cleary, 2001c, Herbst and Nordell, 2001, Morrison et al, 2001, Morrison and Cleary, 2008) at least some fraction of the rock ore has been included Cleary (2004) showed that modelling the complete mill with 95% of the rock size Understanding fine ore breakage in a laboratory scale ball mill using 2016年6月6日 A Mill Charge Charge Weight/Volume/Percent Filling Ore Specific Gravity Percent Rock or Ore Charge Percent Ball Charge (if semiautogenous) Percent Solids – in the mill B Mill Power Mill Speed: Percent Critical/Peripheral; Direction of Rotation; Power Draft Design Drive PowerSAG Mill Grinding Circuit Design 911Metallurgist
.jpg)
SAG Mill Liner Design 911Metallurgist
2016年6月6日 Once the process metallurgist has thoroughly tested the ore body and determined the optimum method of mineral recovery; and the plant designer has efficiently and economically laid out the circuit, instrumentation, 2004年11月1日 A representative SAG mill charge was used, with a rock top size of 122 mm and the bottom size resolved in the DEM model chosen to be 6 mm, so that >90% of the charge was correctly represented in the model The fill level was 39% with a ball load of 5% giving around 425,000 particles The mill rotation rate was 24 rpm corresponding to 76% criticalUsing DEM to model ore breakage within a pilot scale SAG mill2013年4月1日 Two types of mills commonly found in the minerals processing industry are ball and semiautogenous (SAG) mills, which use both ore and steel balls as grinding media (Wei and Craig, 2009b)In the case of a ball mill the ore is crushed before it enters the mill, whereas a SAG mill receives runofmine (ROM) ore directly (Stanley, 1987)A SAG mill in a singlestage Analysis and validation of a runofmine ore grinding mill circuit A section cutthrough of ball mills A ball mill is a type of grinder filled with grinding balls, used to grind or blend materials for use in mineral dressing processes, paints, pyrotechnics, ceramics, and selective laser sinteringIt works on the principle of impact and attrition: size reduction is done by impact as the balls drop from near the top of the shellBall mill Wikipedia
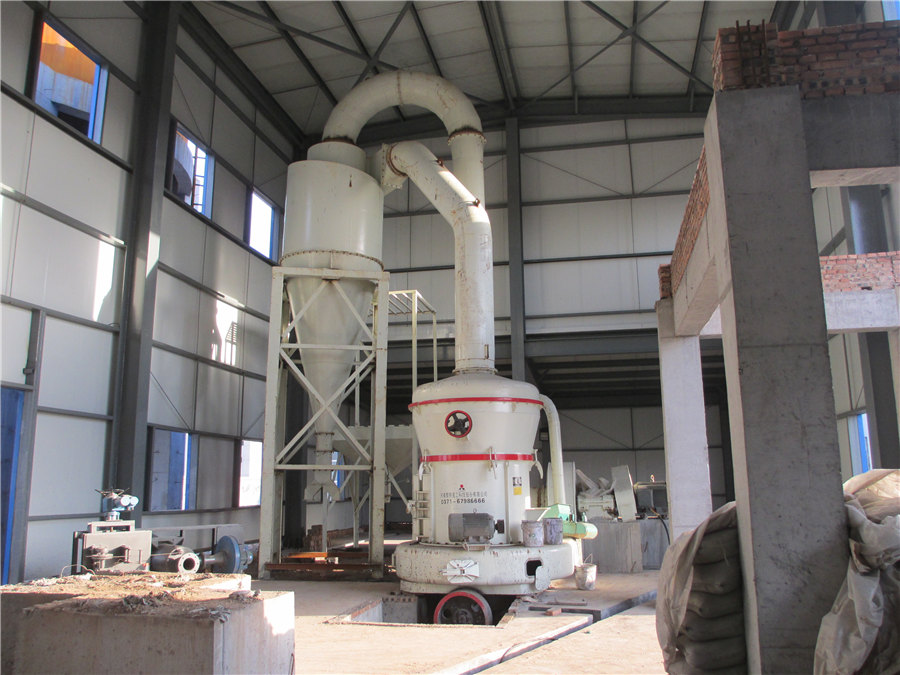
Acoustic emissions monitoring of SAG mill performance
1999年2月1日 Polar contour plot of the natural logarithm of the number of vibrational events ( 5 0 e number intervals) as a function of amplitude (volts) in the radial direction and mill rotation phase angle Keywords: ball mill; rotation body; dropping motion; crushing medium; steel ball; Abstract: When ANSYS finite element analysis of the ball mill body is conductedrotation , the force of the ball mill rotation body should be analyzed first The force of the rotation body is closely related to the grinding action of the ball millResearch on Mechanical Problems of Rotation Body Motion of 2020年7月23日 The depletion of highgrade ores has forced the utilization of lowgrade ores The small liberation sizes in the lowgrade ores require fine grinding which is an energy intensive operationOptimization of stirred mill parameters for fine grinding of PGE 2000年7月23日 motions: rotation around the mill axis and vertical motion (See Figure 1) It was observed that the media motion in the radial direction is not significant and thereforeScale up of tower mill performance using modelling and simulation
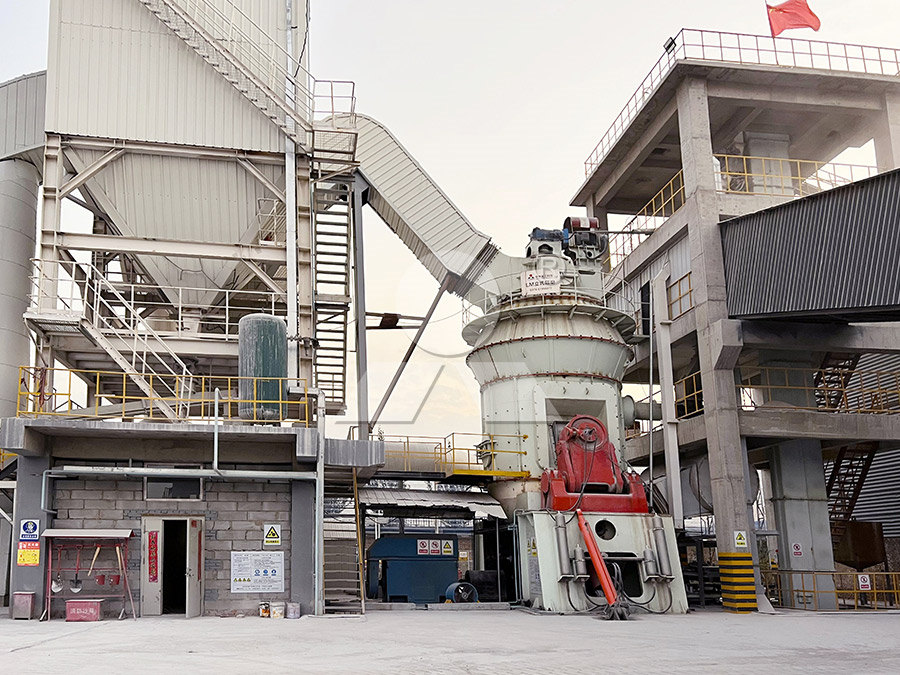
Buy Ore Ball Mill for Mineral Processing Iron Gold Ore Ball Mill
Ore ball mill sometimes called ore grinding mill, is generally used in mineral processing concentrator, processing materials include iron ore, copper ore, gold ore, molybdenum ore and all kinds of nonferrous metal oreThe core function of the ore ball mill is to grind the materials, and also to separate and screen different mineral materials, and to separate the tailings, which is 2020年10月20日 Tracking the mill performance showed that the mill power consumption decreased from 949 to 663 kWh/t (a nearly 30% reduction), P 80 of the mill product decreased from 611 to 355 μm, and the mill fresh feed flow rate increased from 511 to 521 t/h by decreasing the feed ore hardness from 112 min to 58 min based on SAG power index (SPI)The performance improvement of a fullscale autogenous mill by setting 2016年2月26日 Operational Characteristics: The method of operation has a considerable effect upon the nature of the productWhen minimum fines are a requirement, the hammer mill should always he operated in closed circuit with a screen, or screens; the circulating load should be fairly high; speed should be as low as is consistent with physical structure of the material; and Hammer Mill Operating Principle 911Metallurgist2023年6月19日 According to different ore discharge methods, ball mill types can be divided into the grid ball mill and the overflow ball mill there is the spiral blade with a spiral direction opposite to the mill rotation direction The purpose Battle of the Mill Grid Ball Mill VS Overflow Ball Mill
.jpg)
OPTIMIZATION OF LATERITE ORE GRINDING PROCESS
2022年12月31日 OPTIMIZATION OF LATERITE ORE GRINDING PROCESS USING BALL MILL WITH RESPONSE SURFACE METHOD and the rotation speed of th e ball mill the direction of the ball being lifted by the lifters2002年7月1日 The rotational direction of a pot in a planetary ball mill and its speed ratio against revolution of a disk were studied in terms of their effects on the specific impact energy of balls calculated from the simulation on the basis of the Discrete Element Method (DEM) and structural change of talc during milling The specific impact energy of balls is measured as a significantly Effects of rotational direction and rotationtorevolution speed The profile can be better customised to suit mill speed and filling and therefore optimise performance, and it allows more material in the lifter for a given base width, but the mill must only run in one direction 7 High–low double wave ball mill The Selection and Design of Mill Liners 911 MetallurgistTo access One way Machining in the Mill Multiaxis Wizard: When climb milling is set, the tool movement and the spindle rotation have to be in the same direction The tool always machines on the left side When side tilt angle is less than 45 degreesDirection for One way Machining Bobcad
.jpg)
Operation Analysis of a SAG Mill under Different Conditions Based on
2020年10月9日 Changsha , China; qyxie168@163 (QX); fuqiang0812@163 (QF);2003年7月14日 My circa 1904 LeBlond is made to run CCW looking from the front, with the table feeding from right to left for normal milling The power feed gearbox has a big arrow showing direction of rotation However, I remember seeing some illustrations of setups in the catalogs of other LeBlonds, which were going the other wayProper rotation direction for a horizontal mill? Practical MachinistEFFECTS OF MILL ROTATIONAL SPEED ON THE BATCH GRINDING KINETICS OF A UG2 PLATINUM ORE By DINEO MOKGANYETJI MAKGOALE Submitted in accordance with the requirements for the degree of MAGISTER TECHNOLOGIAE in the subject ENGINEERING: CHEMICAL at the UNIVERSITY OF SOUTH AFRICA SUPERVISOR: Prof FRANCOIS EFFECTS OF MILL ROTATIONAL SPEED ON THE BATCH GRINDING KINETICS OF content is uniform and thoroughly mixed by the rotation of the mill and the movement of the grinding media [44] In this case the model is known as a perfectly mixed model In some cases the mill’s charge is considered to be perfectly mixed in the radial direction and only partially mixed in the axial direction AnotherGrinding in Ball Mills: Modeling and Process Control Sciendo
.jpg)
Some aspects of slurry flows in a mill DiVA
slurry flow through a mill with focus on macroscopic resistance mechanisms The axial flow of slurry in a mill is affected by two opposing effects related to the resistance to flow The mill rotation in perpendicular direction increases the resistance to axial flow On the other hand, the charge in motion has a larger porosity, which promotes2022年1月1日 Mio et al [24, 25] investigated the influence of rotation direction, rotationrevolution speed ratio, and revolution radius on the wear rate of the steel balls in a planetary ball mill The results showed that the counter direction could provide immense impact energy of balls during milling than that of the normal directionInvestigation of the ball wear in a planetary mill by DEM simulation 2021年7月1日 The direction of the normal force at point p always points to the center of SP1, we compared the motion behavior of polyhedral and spherical particles in a labscale rotation mill Parameters of the mill: Rotation speed Ω/rpm: 105: Ore filling level: 20%: Media filling level: 15%: 5 Results and discussionDEM investigation of SAG mill with spherical grinding media The rolling ball mill and the stirring ball mill use the multidimensional cyclic rotation motion of the grinding ball and the material so that the upper, lower, left and right positions in the Location of the vibration sensors on the mill's shell (A) and time
.jpg)
Tubular Ball Mills ScienceDirect
2016年1月1日 Figure 72 B indicates a mill where a diaphragm or grate is placed before the exit end so that particles greater than the openings of the diaphragm are not discharged but held back for further grinding Grate discharge mills give less excessive grinding compared to overflow mills and are best suited to grinds to 150–250 μm In Figure 72 C, the discharge opening is at the 2013年4月1日 However, a lot of academic applications have been developed using Matlab/Simulink R le Roux et al (2013) proposed and validated a novel and simple nonlinear model, Sbárbaro (2010), Liu and Analysis and validation of a runofmine ore grinding mill circuit SAG Mill ore hardness kWh/t: Energy required to grind an ore from F80 of 152 mm to T80 of 17 mm It is a resulting value from the SAGDesign test No other test accurately reports SAG hardness in kWh/t The required SAG energy is calculated using the Bond Wi to adjustDesign SAG mill production when you need it most: In day 1 and 2024年4月26日 Learn about the key stages in iron ore processing, including crushing, screening, and beneficiation techniques for optimal resource utilization +86 ; xlyin@ The choice of grinding mill depends on factors such as the desired product size, capacity requirements, and energy consumption b Autogenous and Semi Iron Ore Processing: From Extraction to Manufacturing
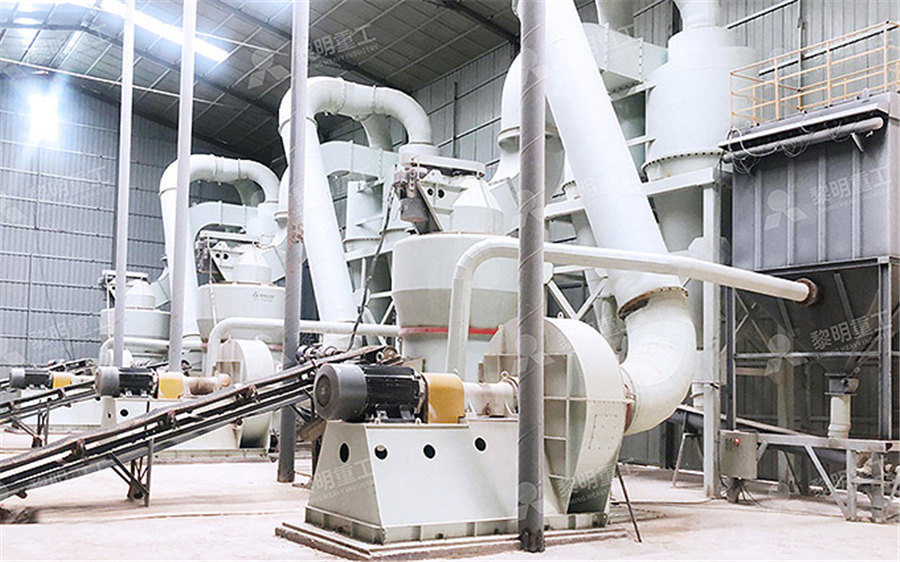
Analysis and validation of a runofmine ore grinding mill circuit
which use both ore and steel balls as grinding media (Wei and Craig, 2009b) In the case of a ball mill the ore is crushed before it enters the mill, whereas a SAG mill receives runofmine (ROM) ore directly (Stanley, 1987) A SAG mill in a singlestage closed circuit con guration, as shown in Fig 1, is considered for this study A description2021年1月11日 viewed through the open end of the SAG mill, it was evident that maximum throughput occurred when the cascading material (for clockwise mill rotation), was hitting the shell at 30o to the right of the vertical diameter (or 5 o’clock) This impact point was normal to the mill shell tangent at that pointChoosing a SAG Mill to Achieve Design Performance