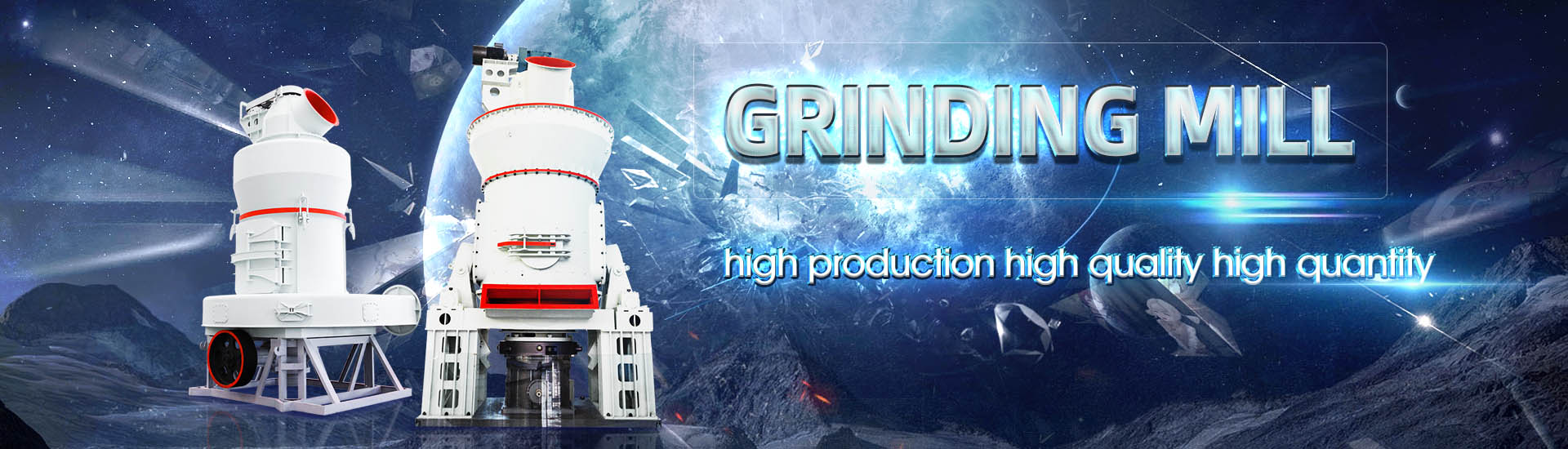
Cement mill iron removal technology
.jpg)
ENERGYEFFICIENT TECHNOLOGY OPTIONS FOR DIRECT
Direct reduction of iron (DRI) forms an important subsector of the Indian steel sector, accounting for about 33% of the total steel production, which is about 3415 million tonne of steel produced in2021年10月12日 We assess the potential for decarbonization in the cement, metals (including steel and aluminium) and chemicals manufacturing industries, including the potential to reduce Innovations to decarbonize materials industries Nature2018年9月26日 Membranebased systems can capture 80% of the CO 2 emitted from cement or steel production processes at costs of $40 to $50/tonne of CO 2 captured Lower costs are CO2 Capture from Cement Plants and Steel Mills Using Membranes2023年1月7日 There is scope for various technologies to be used in the cement manufacturing process for reducing emissions and energy consumption This paper presents an analysis of Emission reduction through process integration and exploration of
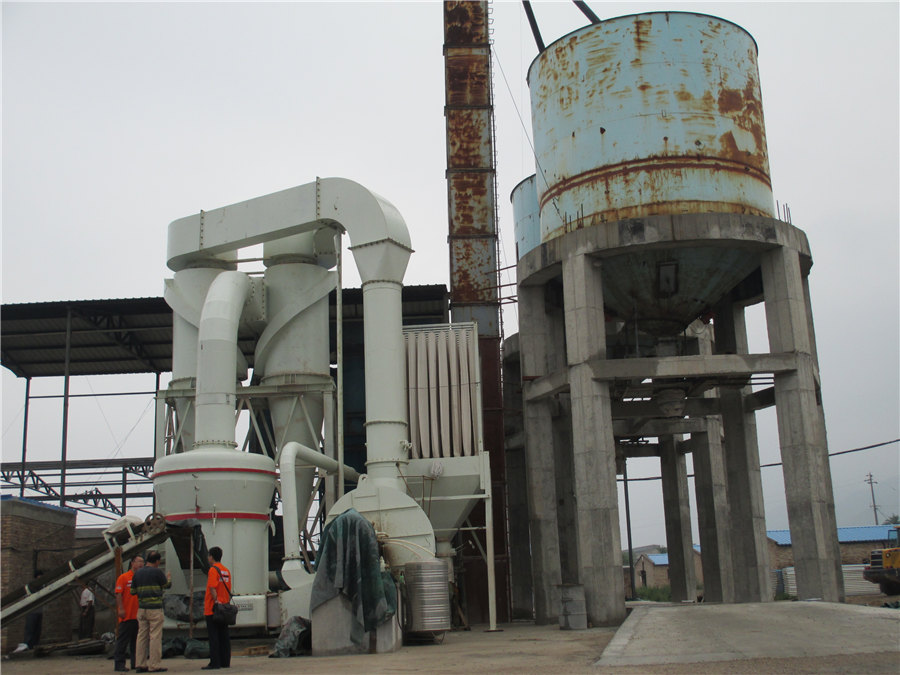
Air Pollution Control in Cement: Solutions Impact
2023年9月22日 Electrostatic Precipitators (ESPs) are formidable weapons in the battle against air pollution ESP are used in Raw Material Crusher, Cement Mill, Coal Mill, Rotary Kiln in Cyclone Preheater Tower ESPs utilize electrostatic 2022年4月4日 In this study, greenhouse gas (GHG) emissions related to two cement production systems with CaL carbon capture are evaluated: the tailend CaL carbon capture and the integrated CaL carbon capture The carbon Evaluating the Carbon Footprint of Cement Plants 2019年1月21日 Reduction in energy consumption and carbon emissions during cement manufacturing can be achieved by introducing alternative cements The potential of alternative cements as a replacement of conventional OPC can Recent Progress in Green Cement Technology Utilizing To fully decarbonise the sector, process emissions from the clinkermaking process need to be addressed, regardless of the heat source Part of the solution will need to be CO2 capture – Deep decarbonisation of industry: The cement sector Europa
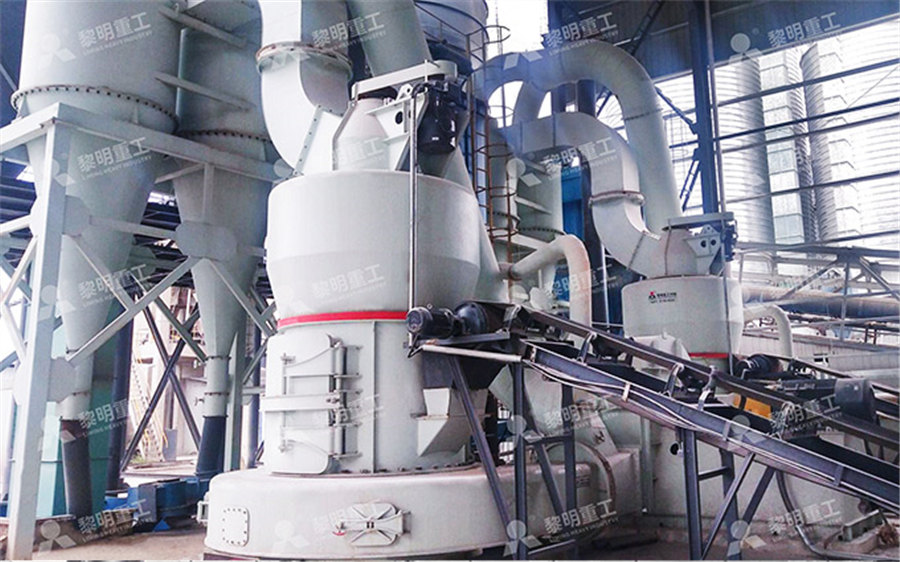
Cement and steel — nine steps to net zero Nature
2022年3月23日 Infrastructure, technology transfer and mechanisms for reducing financial risks must be established to allow lowemissions heavy industry to flourish Here, we highlight nine priorities forSemifinishing grinding system: after ground by cement roller press, materials are divided into three parts through an air classifier: coarse, medium and fine, in which the coarse material is returned to the roller press for regrinding, the Cement Roller Press Roller Press In Cement Plant2016年10月5日 In this chapter an introduction of widely applied energyefficient grinding technologies in cement grinding and description of the operating principles of the related equipments and comparisons over each other in EnergyEfficient Technologies in Cement Grinding2019年1月21日 The cement industry is facing numerous challenges in the 21st century due to depleting natural fuel resources, shortage of raw materials, exponentially increasing cement demand and climate linked environmental Recent Progress in Green Cement Technology
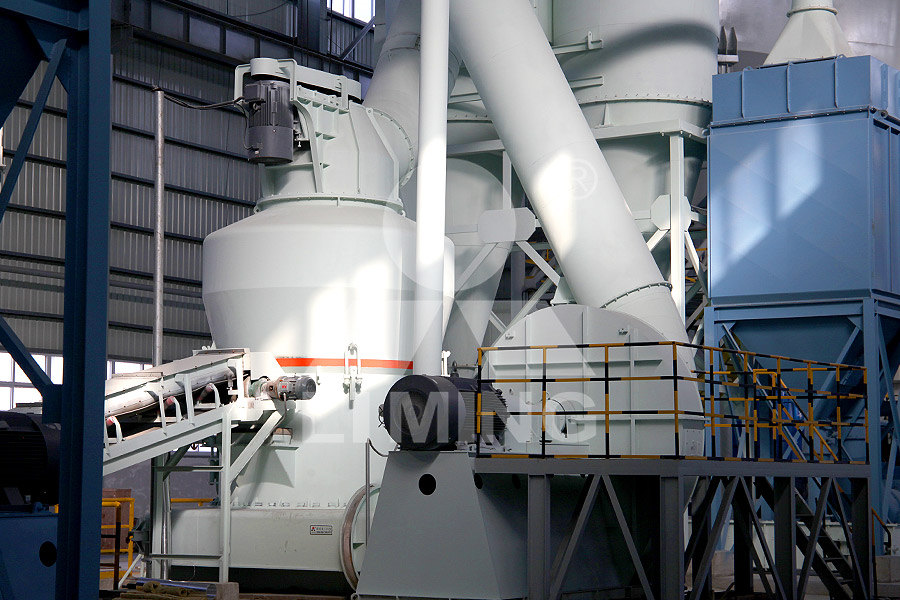
Cement and Clay Products Technology SpringerLink
2021年8月10日 In practice, it is the presence and relative amounts of the compounds tricalcium silicate (C 3 S), dicalcium silicate (C 2 S), tricalcium aluminate (C 3 A) and tetracalcium aluminoferrite (C 3 AF) in cement that imparts the different properties to the different types of Portland cement The probable composition of these compounds in Portland cement has the Our bestinclass OK™ Mill is a globally successful vertical roller mill solution for grinding raw material, cement and slag Its cuttingedge design features consistently deliver the highest quality products with the greatest efficiency It is affordable to install and cost effective to operate over your cement plant’s lifetimeOK™ Raw and Cement Mill2021年5月10日 Today, cement and concrete are some of the most consumed materials after water throughout the whole world About 41 billion tons of cement are fabricated annually (half a ton per person) and half of this amount is produced by China [5]In addition, >1 m 3 of concrete per person is produced with Portland cement each year [6]Today, Portland cement, Portland Steel slag and its applications in cement and concrete technology2023年7月10日 Cement manufacturing is a significant industrial activity that plays a vital role in the construction sector However, the process of cement production is associated with various environmental Cement Manufacturing Process and Its Environmental Impact
.jpg)
Magnetic Separator Manufacturer, Iron Separator, Eddy Current
Magnetic Separator Supplier, Iron Separator, Eddy Current Separator Manufacturers/ Suppliers Shandong Huate Magnet Technology Co, Ltd Menu Sign In2021年1月22日 In the whole process of cement production, the electricity consumption of a raw material mill accounts for about 24% of the total Based on the statistics of the electricity consumption of the raw material mill system of 1005 production lines in China between 2014 and 2019, it is found that the average electricity consumption of the raw material preparation A Survey and Analysis on Electricity Consumption of Raw Material Mill 6 clinker grinding and cement making 7 composition and properties of portland cements 8 advances in plantbased quality control practice 9 environmental mitigation and pollution control technologies 10 trends of research and development in cement manufacture and application 11 global and regional growth trends in cement productionCement Production Technology Principles and Practice2018年9月26日 In this paper, the feasibility of capturing CO 2 from cement and steel plants is examined using currently available membrane technology Coal power plant flue gas contains 13–15% CO 2 ; cement and steel plant flue gas contains 20–30% CO 2 ; this higher CO 2 concentration is useful for all separation technologies, but especially for membranes where CO2 Capture from Cement Plants and Steel Mills Using Membranes
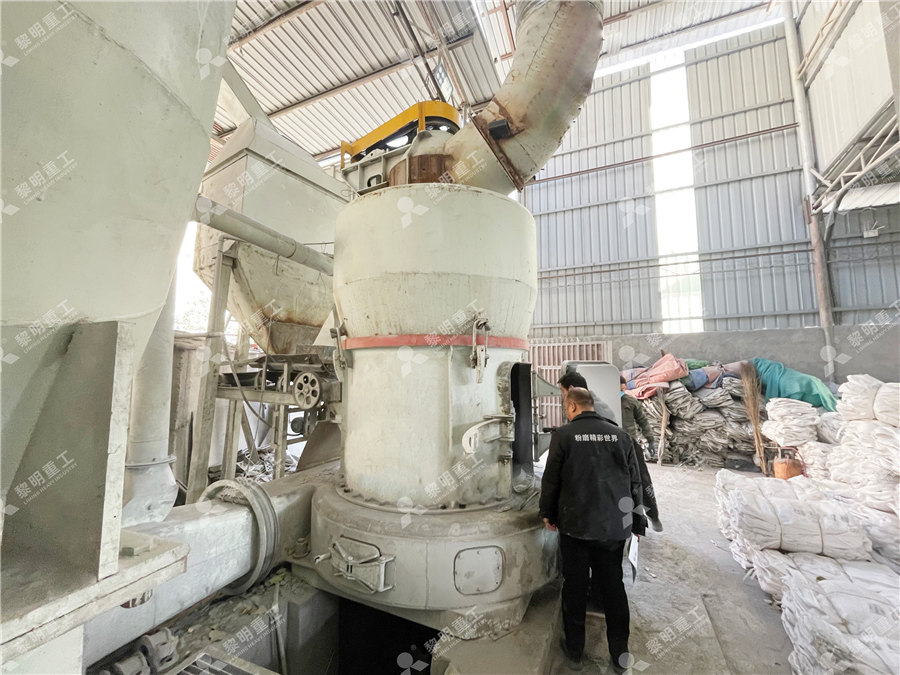
ESP Electrostatic Precipitator Electrostatic Dust
The cement industry is an industry with serious dust pollution, the dust below 10 microns that it produces accounts for about 90% As cement equipment, the ESP electric precipitator is often set behind the cement kiln and other production 2021年1月22日 In the whole process of cement production, the electricity consumption of a raw material mill accounts for about 24% of the total Based on the statistics of the electricity consumption of the raw A Survey and Analysis on Electricity Consumption of Raw Material Mill A number of cement milling simulations were carried out by Metso Minerals Process Technology group located in Brisbane, Australia These included the simulations for Argos Cement, Green Island Diaphragm between the two compartments of the twocompartment mill OK mill Ball mill OK mill Ball mill OK mill Ball mill 3 days 155 145 225 220 115 110 7 days 255 245 275 260 195 190 28 days 430 420 350 330 425 425 *50/50 clinker and slag mixture Portland cement Slag* RollerTable Table Roller Without hardfacing1 1 65 With hardfacing05 3005 25 *50/50 clinker and slag mixtureOK vertical roller mill Environmental
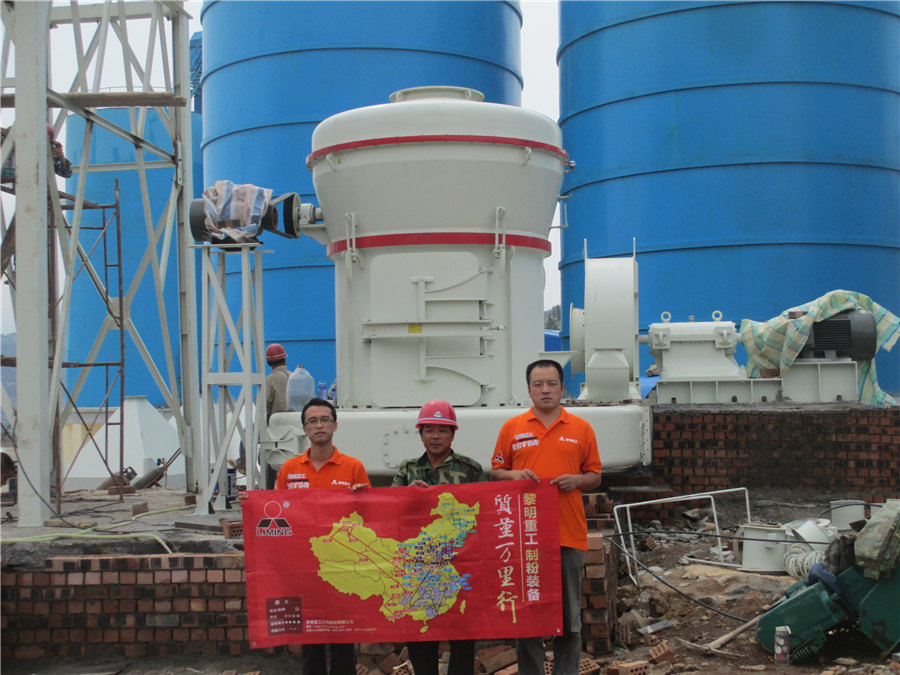
Cement ball mill DARKO
A cement ball mill has the capacity typically ranging from 10 to 300 tons per hour We are experienced in your industryTechnology leader in cement plant energysaving and environmental protection equipment manufacturing industry High Chromium Cast Iron Liners: Chromium content exceeds 11%, with a chromiumtocarbon ratio over 45Part Three: Raw Mill Process of Raw Mill The proportioned raw material is feed first to a grinding mill In the mill, particles ground in to very fine sizes In the grinding unit, drying, grinding and mixing takes place simultaneously Hot gas from clinker burning unit is passed into the grinding unit to assist the drying and grinding processCement Manufacturing Process INFINITY FOR CEMENT EQUIPMENTFCT has a proprietary solution to maintain the traditional ‘cement grey’ colour, regardless of iron content in the clay Iron compounds in the form of hematite (Fe 2 O 3) have a reddish hue and when in the form of magnetite (Fe 3 O 4) have a darkgreyish hue At higher temperatures, the iron is mostly in the form of magnetiteClay Calcining Technologies FCT CombustionCement raw material is the mixture of mainly Limestone other constituent such Iron oxide, Shale etc having different moisture contain depending on composition deposit We offer the mills with optimized process technology to evaporate the moisture by employing the hot gases and intricate mill design provides efficient grindingVRM – AMCL Machinery Limited
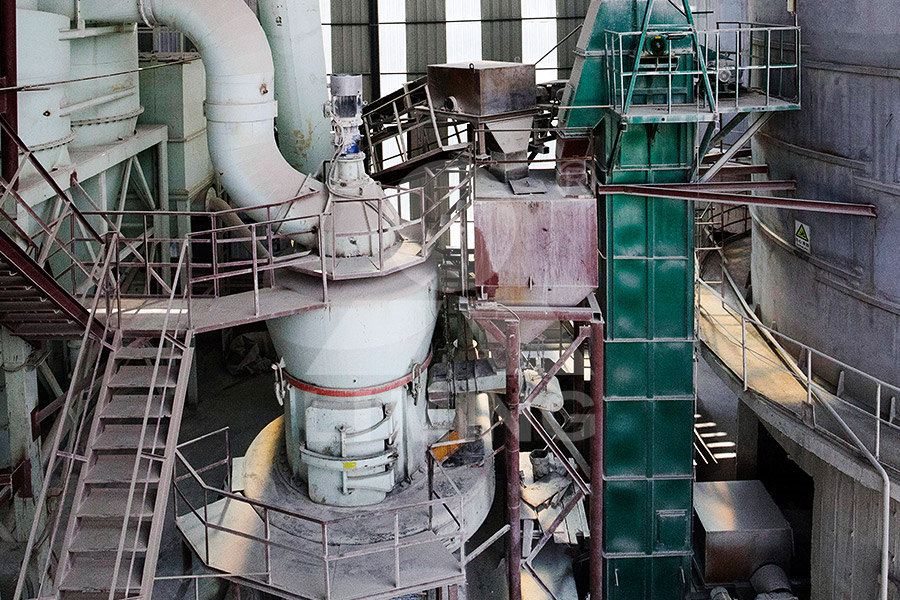
Vertical Roller Mill Operation in Cement Plant
The vertical roller mill (VRM) is a type of grinding machine for raw material processing and cement grinding in the cement manufacturing processIn recent years, the VRM cement mill has been equipped in more and more cement plants around the world because of its features like high energy efficiency, low pollutant generation, small floor area, etc The VRM cement mill has a into the cement mill hopper by means bucket elevator where 2% Gypsum will be added and fed to the ball mill for grinding operation Gypsum helps in initial setting of cement The cement (OPC) produced is stored in Cement silos and then sent for packing and final dispatchCleaner production assessment in cement plant using vertical 2024年1月16日 Problems with breathing or acute lung pain caused by cement specks in the air are common, and the cement producing industry typically has a hard time keeping them under controlA Review of the System for Filtering Particulate Matter Since cement mill have interconnected processing operations the system is complex Main difficulty of cement ball mill load is large delay time which is solved using sampling control strategy of fuzzy logic control Index terms – Fuzzy logic controller, Ball mill 1 INTRODUCTION Cement is a hydraulic binder which sets andDevelopment of Fuzzy Logic Controller for Cement Mill
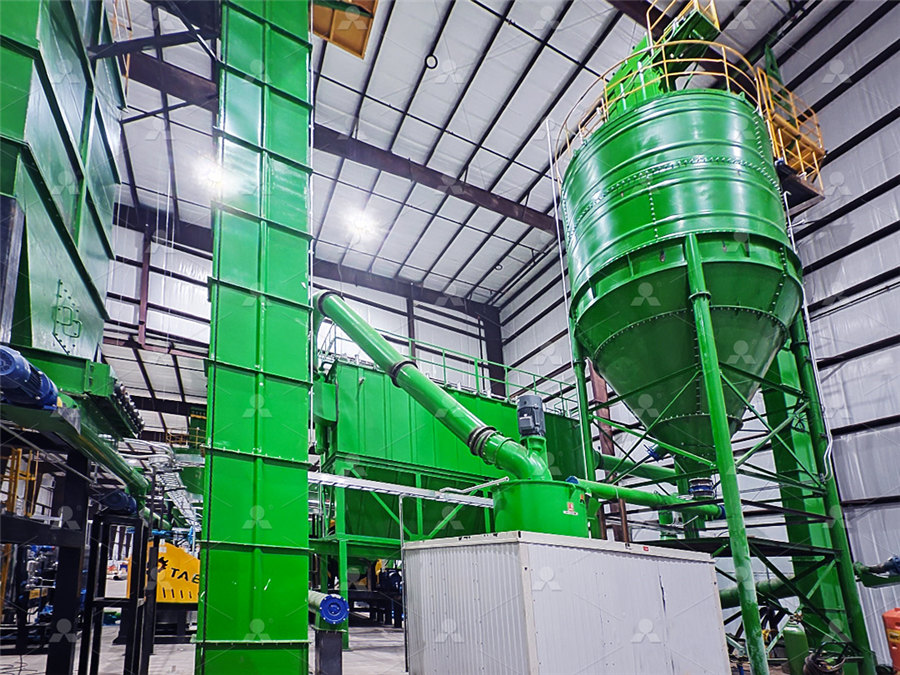
COAL PREPARATION AND FIRING INFINITY FOR CEMENT EQUIPMENT
Previous Post Next Post Contents1 COAL PREPARATION AND FIRING11 INTRODUCTION12 2COAL RESERVES13 CHARACTERISATION OF COALS BY CHEMICAL131 31 Major components132 32 Minor Components14 4CHARACTERISATION BY PHYSICAL AND MECHANICAL PROPERTIES141 41 Coal Storage142 42 Variation of Physical and For this reason, such ball mills were only used as a pregrind stage, followed by for example flat stones In 1904, Krupp produced a selfcontained cement mill using a ball mill and their version of the Askham separator in closed circuit, but I think this was never used in BritainCement Kilns: Size Reduction and Grinding2019年7月1日 Raw iron ore is characterized by the most abundant ironcontaining mineral found in the ore: magnetite (Fe 3 O 4), hematite (Fe 2 O 3), siderites (FeCO 3), and limonites (2Fe 2 O 3 3H 2 O) (Walker, 1986)All the impurities in iron ore (silica, alumina, titania, sulfur, and phosphorus) are collectively known as gangueAll iron ore that is mined has to be crushed, The recycling and reuse of steelmaking slags — A reviewBasic Cement Technology IF YOU WORK IN A CEMENT PLANT AND YOU NEED COURSES AND MANUALS LIKE THIS MANUAL AND BOOKS AND EXCEL SHEETS AND NOTES I SPENT 23 YEARS COLLECTING THEM YOU SHOULD sand and clay contain the four essential elements required to make cement: calcium, silicon, aluminium and iron How do you Basic Cement Technology INFINITY FOR CEMENT EQUIPMENT

OPTIMIZATION OF CEMENT GRINDING OPERATION IN BALL MILLS
The consumption of energy by the cement grinding operation amounts to one third of the total electrical energy used for the production of cement The optimization of this process would yield substantial benefits in terms of energy savings and capacity increase Optimization of the Cement Ball Mill OperationWhat Is A Cement Ball Mill The cement ball mill is a kind of cement grinding millIt is mainly used for grinding the clinker and raw materials of the cement plant, and also for grinding various ores in metallurgical, chemical, and electric power enterprisesIt has the characteristics of strong adaptability to materials, continuous production, a large crushing ratio, and easytoadjust the Cement Ball Mill Cement Grinding Machine Cement Mill2020年11月22日 Three sets of samples (unreinforced iron, 4 wt% micrometersize (∼5–15 μm) WCreinforced iron and 4 wt% nanosize (∼30 nm) WCreinforced iron were prepared using a powder metallurgy route to Wear Resistance Improvement for Grinding Balls of Horizontal Cement AGICO Cement Vertical Mill AGICO Cement Ball Mill Cement Vertical Mill Grinding System Cement vertical mill, also called roller mill, is another raw mill commonly used in cement pared with the cement ball mill, it has a Raw Mill – Raw Mill In Cement Plant AGICO Cement
.jpg)
Everything you need to know about Crushers in Cement industry
In the cement industry, which uses chiefly mediumhard to hard limestone as its principal raw materials, singlestage crushing plants equipped with hammer crushers are the commonly preferred type Feed Hoppers The feed hopper, feeding equipment, crusher and product removal conveyors are the main component units of the plant2023年12月23日 The raw mill fan is usually connected to the preheater by a duct The raw mill fan is a highspeed rotating machine It is important to ensure the safety of the raw mill fan The raw mill fan should be regularly inspected Powering Progress: Unveiling the Technology Behind 2021年7月12日 Iron is a key detrimental impurity in silica sands that determines their contribution to hightechnology industries Herein, a simple ecologically sound approach is investigated for iron removal The Modeling and Optimization of Iron Removal from Silica Sand 2019年1月8日 One of the major concerns faced by the iron and steel industry, other than the abundant emission of carbon dioxide into the atmosphere, is the huge quantity of slag that is generated during the manufacturing of iron and steel A comprehensive understanding of the iron and steel slag properties has diverted them away from stockpiling or landfilling to useful Critical review of applications of iron and steel slags for carbon
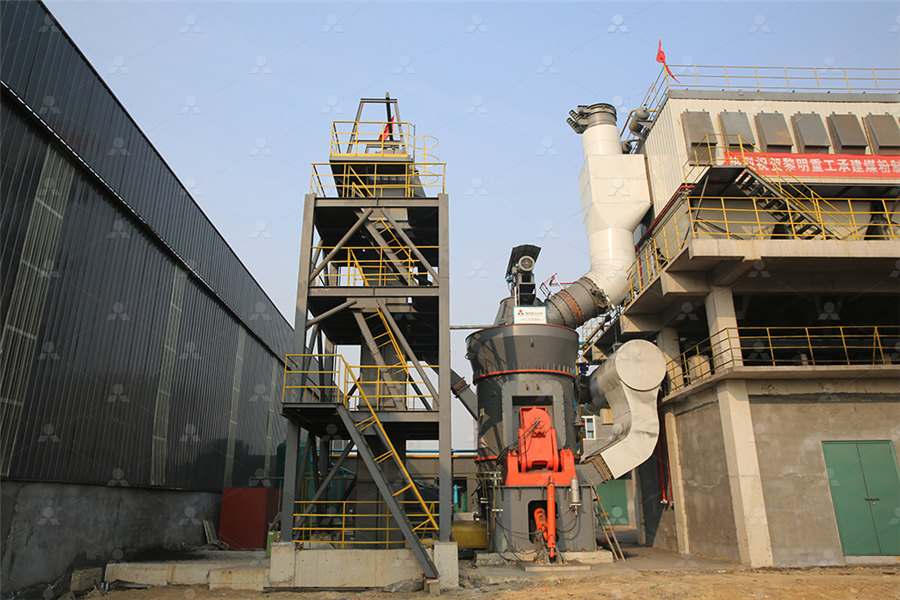
Cement Plant Equipment Cement Crusher, Cement Mill, Cement
2019年11月21日 Cement ball mill Cement ball mill is core equipment for cement grinding It has own advantages in operation, application, and structure, at present, cement ball mill has widest applications High working efficiency, the cement ball mill produce uniform particles, increases the production capacity by 25%54 Installation of VFD for Line2 Cement Mill Bag Filer Fan and Preheater ID Fan 58 Removal of Silencer for Cooler Fans and Arresting Leakages of Cooler Thermal Power Plant, Chlor Alkali, Cement, Pulp and Paper and Iron and Steel This manual is expected to serve as reference manual for • Identifying sources of GHG emissionsGood Practices Manualremoval in the slag chute Objective To change the chute design for remove the slag coating Observation The raw material needed for cement production are lime stone (calcium carbonate) and clay (silicon, Aluminium and iron ore) The additive material used in cement production are slag, fly ash and gypsumMODIFIED CHUTE DESIGN FOR SLAG REMOVAL IN CEMENT MAKINBag Filters AGICO Operation Effect Economic Benefit The dust removal efficiency of the blowback bag filter and pulse jet bag filter can reach more than 99%, the air leakage rate is less than 3%, and their dust emission concentration is far below the emission limit of 150 mg/ m 3 Compared with the cyclone dust collector, settling chamber, and electrostatic precipitator, the Bag Filter In Cement Plant Pulse Jet Bag Filter Cement Equipment
.jpg)
Closed and Open Circuits Ball Mill for Cement, Limestone, Iron ore
We bring forth a highly advanced Ball Mill, specifically engineered for both wet as well as dry cement grinding applications Classified depending on the circuit design, bearing, grinding type and drive, the selection is made on the basis of the product fineness, quality, and nature of raw material, site conditions and specific requirements