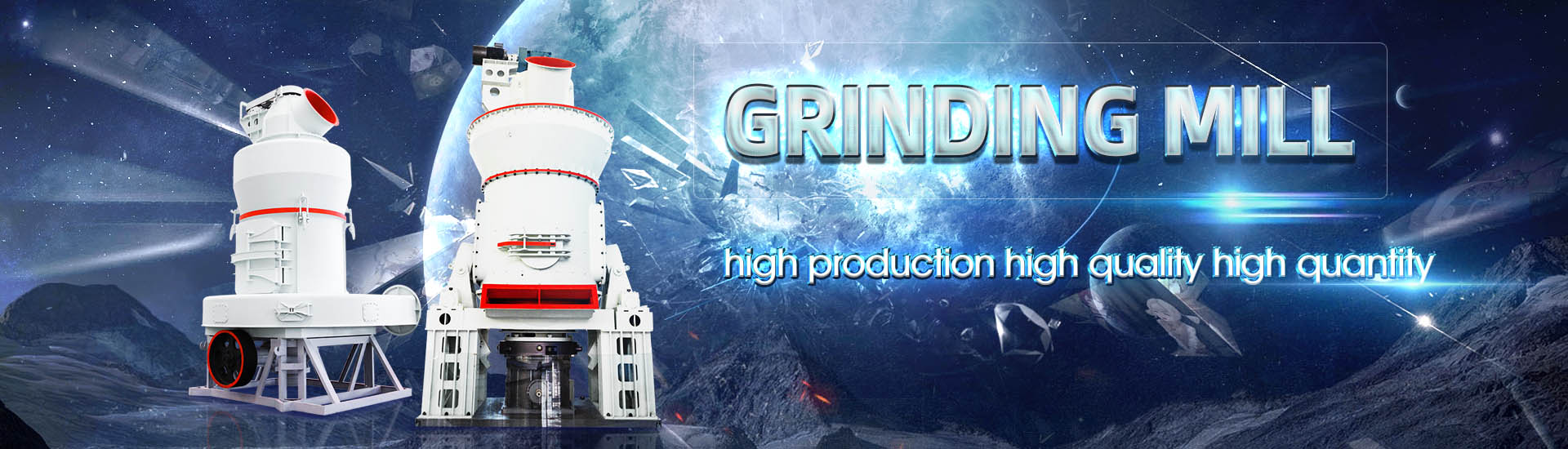
What is the ball consumption of calcite ore ball mill
.jpg)
Ball Mill Design/Power Calculation 911Metallurgist
2015年6月19日 Ball Mill Power Calculation Example #1 A wet grinding ball mill in closed circuit is to be fed 100 TPH of a material with a work index of 15 and As a result of this work, the optimum grinding test conditions were found to be 840 rpm for stirrer speed, 070 for ball filling ratio, 0100 for powder filling ratio, 50% for solid ratio and 20 min for grinding timeOptimization of Wet Grinding Parameters of Calcite Ore in Stirred 2013年8月3日 In Grinding, selecting (calculate) the correct or optimum ball size that allows for the best and optimum/ideal or target grind size to be achieved by your ball mill is an important thing for a Mineral Processing Engineer AKA Calculate and Select Ball Mill Ball Size for Optimum 2015年7月4日 An experimental practice on the ultrafine wet grinding of calcite ore in a conventional batch ball mill is reported In this study, the effect of wet grinding conditions on the production of fine particles was researchedWet Grindability of Calcite to UltraFine Sizes in Conventional Ball
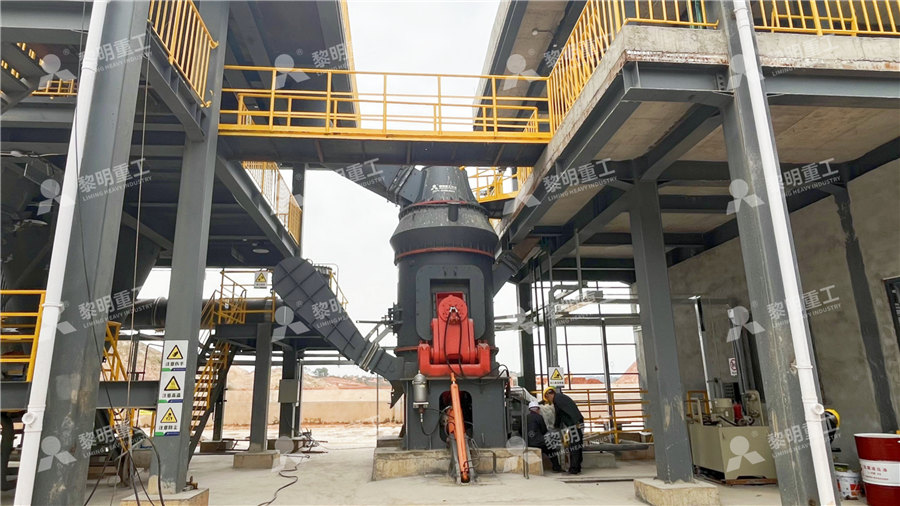
BALL MILLS Ball mill optimisation Holzinger Consulting
the ball mill had an average production rate of 190tph with a specific electrical energy consumption of 355kWh/t Its operational issues included: • oversized limestone • wornout lifting liners with liner thickness decreasing from 80 to 20mm • lowquality media Following 2014年10月27日 It was found that the ball mill consumed 5467 kWh/t energy to reduce the F 80 feed size of 7222 lm to P 80 product size of 2754 lm while stirred mill consumed 3245 kWh/t of energy toWet Grindability of Calcite to UltraFine Sizes in Conventional Ball 2015年7月29日 The outcomes indicate that the wet grinding technique in conventional ball mill for calcite ore is effective to obtain ultrafine size productsWet Grindability of Calcite to UltraFine Sizes in Conventional Ball A ball mill is a type of grinder used to grind and blend materials, and the ball milling method can be applied in mineral dressing, paints, ceramics etc The ball milling owns the strengths of simple raw materials and high efficiency, and it can be used in large scale productionBall Mill an overview ScienceDirect Topics
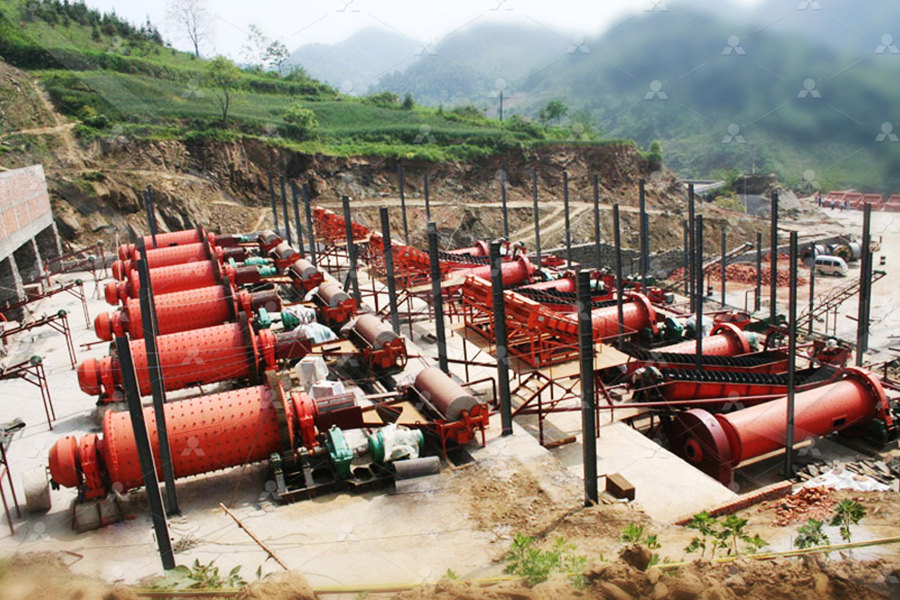
Influences of operating parameters on dry ball mill performance
2018年1月1日 The paper is aimed to investigate the influence of operating parameters on dry fine grinding of calcite in a laboratory scale conventional ball mill Within the context, the influence of2017年2月13日 In all ore dressing and milling Operations, including flotation, cyanidation, gravity concentration, and amalgamation, the Working Principle is to crush and grind, often with rod mill or ball mill, the ore in order to liberate the Ball Mills 911Metallurgist2023年6月6日 Attrition mill is a type of grinding mill by kinds of media to crush lump to powderlike substances The impact can be rock on rock such as in an Autogenous Grinding (AG) mill, rock and a small ball charge (~10%), used in What’s the difference of Ball mill, SAG mill, AG mill?1 Ball Mill: The grinding medium of the ball mill is mainly steel balls or steel sections, and it is widely used 2 Rod Mill: The grinding medium is mainly steel rod, the diameter of steel rod is mostly between 50100mm, and the grinding Ball Mill Working Principle Ball Mill Types MC
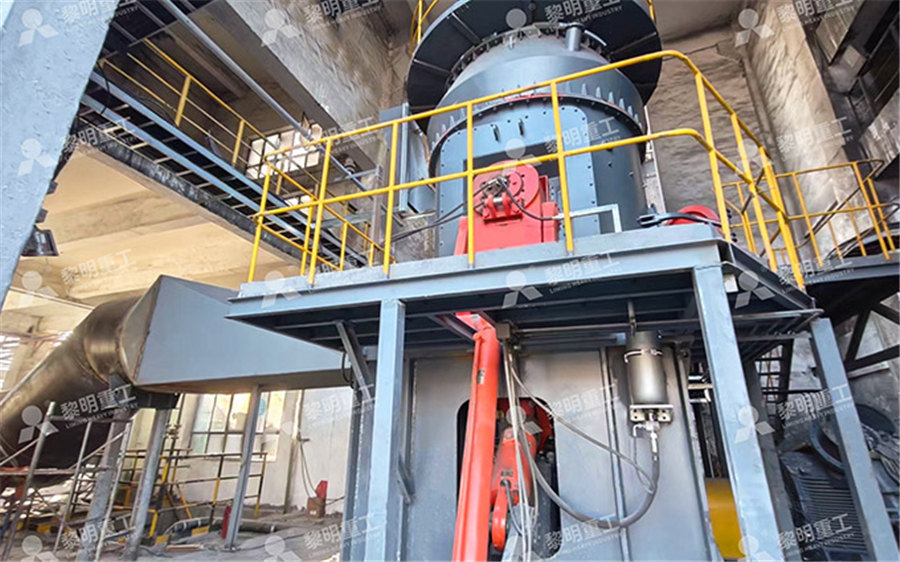
Effect of grinding aids on the grinding energy consumed during
DOI: 101016/JMINENG200909011 Corpus ID: ; Effect of grinding aids on the grinding energy consumed during grinding of calcite in a stirred ball mill @article{Choi2010EffectOG, title={Effect of grinding aids on the grinding energy consumed during grinding of calcite in a stirred ball mill}, author={H I Choi and W Lee and D Kim and 2017年4月29日 In the previous discussion the fact was established that the work done by a ball when it strikes at the end of its parabolic path is proportional to its weight and velocity; then, since the velocity may be considered as constant for all the balls in the mill, the work done by a ball is proportional to its weight Since the amount of ore crushed varies as the work done upon it, it Grinding Media Wear Rate Calculation in Ball Mill2002年11月1日 Single magnetite, single calcite, and blended magnetitecalcite mixture at three weight ratios in four particle sizes were ground in a laboratory wet conical ball mill at four grinding time periodsThe energy efficiency of ball milling in comminution2013年12月18日 Fine grinding, to P80 sizes as low as 7 μm, is becoming increasingly important as mines treat ores with smaller liberation sizes This grinding is typically done using stirred mills such as the Isamill or Stirred Media Detritor While fine grinding consumes less energy than primary grinding, it can still account for a substantial part of a mill’s energy budget Overall Energy Use of Fine Grinding in Mineral Processing
.jpg)
Small Ball Mill Capacity Sizing Table 911Metallurgist
2016年2月14日 Do you need a quick estimation of a ball mill's capacity or a simple method to estimate how much can a ball mill of a No BWi Bond Work Index required here BUT be aware it is only a crude approximation for “most soft ores” from F80 1 cm to P80 700um Ball mill design power example calculation Calculate Ball Mill Grinding 2023年2月15日 After fully understanding the differences between ball mill and rod mill, it also lays the foundation for purchasing equipment and you can choose from the following: 1 By raw material Select a ball mill Ball mill is suitable for grinding hard materials, such as What Are the Differences between Ball Mill and Rod Mill?where Ω E is the energycorrected ball wear rate, g per kWh, d R is the diameter of the largest balls in the mill (the recharge size), mm, K d E is the linear wear rate of balls, µm per kWh t −1, Ai is the Bond abrasion index determined in a laboratory test (unitless), F 80 is the feed 80% passing size of the ore, µm, and pH is the water acid/base measurement of the mill pulpBall Mill an overview ScienceDirect Topics2017年7月26日 We will consider an ore with a ball mill work index varying between 16 and 13, feeding into a single stage ball mill operation with one million kilowatts per day consumed power For the particular mill configuration, a performance graph, Fig (21), has been constructed according to Bond’s methodsHow Ball Mill Ore Feed Size Affects Tonnage Capacity
.jpg)
Ball Mill Success: A StepbyStep Guide to Choosing
2024年8月8日 In mining, it's used for ore processing, enabling the extraction of valuable minerals The pharmaceutical industry relies on it to create uniform particle sizes, enhancing drug solubility and absorption Ceramics benefit from 2016年3月21日 Pulp Densities Pulp densities indicate by means of a tabulation the percentages of solids (or liquidtosolid ratio) in a sample of pulp This figure is valuable in two ways—directly, because for each unit process and operation in Common Basic Formulas for Mineral Processing 2020年2月26日 Measurement results of two ball mills in a real ceramic manufacturing plant showed that the proposed calculation models could achieve an accuracy of more than 96% for predicting the ball mill Calculation method and its application for energy consumption of ball In the world of ore processing, ball mills are a common and essential tool The size of the steel balls used in these mills plays a crucial role in their effectiveness Ball mills are machines used in the mineral processing industry to grind materials into smaller particles These machines come in different sizes and shapes, but all have a cylindrical shell that contains the grinding media What is the size of balls used in ball mills?
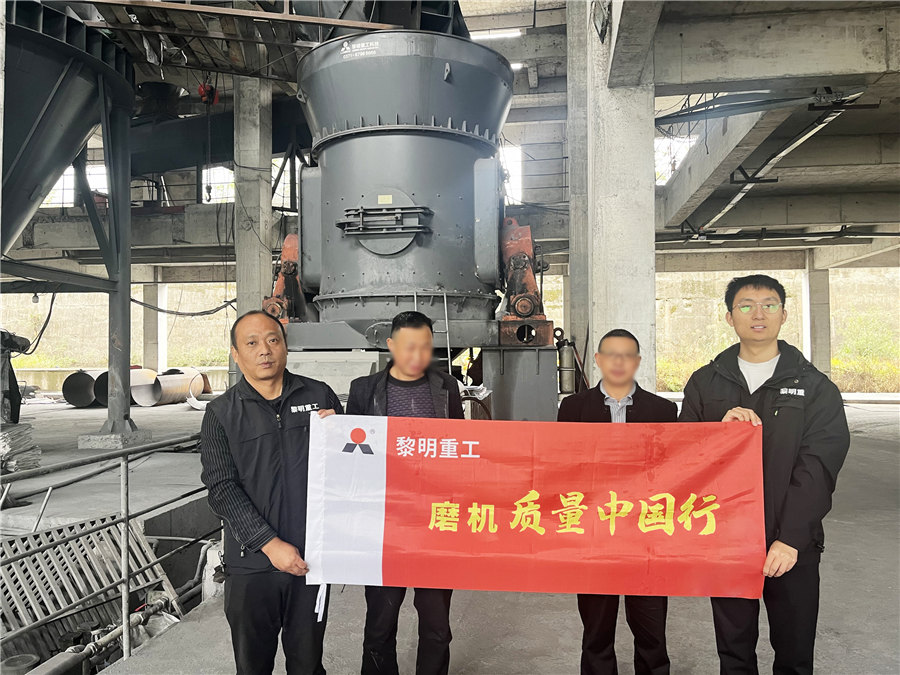
THE OPTIMAL BALL DIAMETER IN A MILL 911 Metallurgist
The ball impact energy on grain is proportional to the ball diameter to the third power: 3 E K 1 d b (3) The coefficient of proportionality K 1 directly depends on the mill diameter, ball mill loading, milling rate and the type of grinding (wet/dry) None of the characteristics of the material being ground have any influence on K 12010年1月1日 The structure and granularity of calcite were measured during dry grinding in a ball mill by Xray diffraction, Fourier transform infrared spectroscopy and laser diffraction, and its morphology was observed by a scanning electron microscopeEffect of grinding aids on the grinding energy consumed during grinding 2023年12月12日 In addition, the ore properties are one of the important parameters for the optimal utilizing of the ball mill Ore can have various properties, such as hardness, density, moisture content, etc (PDF) Control of ball mill operation depending on ball load and ore Advantages of Ball Mill Ball mill grinding machine offer several advantages, including: Versatility: Ball mills can perform various types of grinding, such as dry grinding ball mill or wet grid ball mill, batch or continuous grinding, and fine or ultrafine grinding, making them Ball Mill Grinding Machines: Working Principle, Types, Parts
.jpg)
What Is a Ball Mill and How Does It Work? Certified MTP Blog
2024年7月12日 A conical ball mill, known for its efficiency in grinding, operates with changes in ball size and kinetic energy as the discharge outlet is approached While they may differ in design and operation, all of these ball mills share the same 2020年7月2日 A comprehensive investigation was conducted to delineate the effect of ball size distribution, mill speed, and their interactions on power draw, charge motion, and balls segregation in a (PDF) Effects of Ball Size Distribution and Mill Speed and Their 2023年10月27日 The ball mill is a rotating cylindrical vessel with grinding media inside, which is responsible for breaking the ore particles Grinding media play an important role in the comminution of mineral ores in these mills This work reviews the application of balls in mineral processing as a function of the materials used to manufacture them and the mass loss, as A Review of the Grinding Media in Ball Mills for Mineral 2015年12月1日 Download Citation An experimental study on the ultrafine grinding of gypsum ore in a dry ball mill Gypsum is a crystalline form of hydrated calcium sulfate (CaSO42H20) generally used in An experimental study on the ultrafine grinding of gypsum ore in
.jpg)
Influences of operating parameters on dry ball mill performance
2018年1月1日 In an experiment to determine the effect of ball loading ratio on a calcite ore, Cayirli [81] found out that as the ball charge increases, the mill's energy input also increases and gets to a 2023年1月8日 Since the particle size, shape, specific surface area, and purity of the ground calcium carbonate (GCC) decide its usability in the paper, paint, and plastic industries, the effect of grinding is important However, the effect of stirred and ball mill grinding on the particle shape of GCC by dynamic image analysis (DIA) is still lacking in the literature Therefore, the aim of Comparison of Particle Shape, Surface Area, and Color Properties 2012年12月1日 The inmill load volume and slurry solids concentration have significant influence on the ball mill product size and energy expenditure Hence, better energy efficiency and quality grind can only (PDF) Optimization of inmill ball loading and slurry solids 2021年4月21日 The purpose of this study was to investigate the dry grindability of calcite powders in a vertically and horizontally orientable laboratory batch type stirred mill The experimental results were evaluated using stress intensity analysis The performance was also compared in terms of mill orientation The results showed that the d50 values decreased with The Influence of Stirred Mill Orientation on Calcite Grinding
.jpg)
Understanding the SAG Mill in Copper Ore Mining Process
The rod mill is another type of grinding mill used in the copper ore mining process This machine uses steel rods as the grinding media instead of balls, which are commonly used in ball mills The rods grind the ore by tumbling within the mill, similar to the action of a rotating drum2017年1月1日 Thus, the performance of an industrial ball mill can be adequately described using the orespecific breakage distribution function together with the systematic variation of the material transport (PDF) Performance optimization of an industrial ball mill for Ball mill optimisation As grinding accounts for a sizeable share in a cement plant’s power consumption, optimisation of grinding equipment such as ball mills can provide significant cost and CO 2 emission benefits to the cement producer n by Thomas Holzinger, Holzinger Consulting, SwitzerlandBALL MILLS Ball mill optimisation Holzinger Consulting2013年9月8日 SAG Ball consumption is “average” at 400 g/t while Ball Mill grinding media (3″ balls) usage in 550 g/t Yet, you add steel and nothing seems to happen, tonnage is not noticeably improved You need more tonnage and could actually use a larger/coarser transfer size from the SAG to Ball MillSAG Mill Ball Size Evaluator Evaluation Factors Calculate
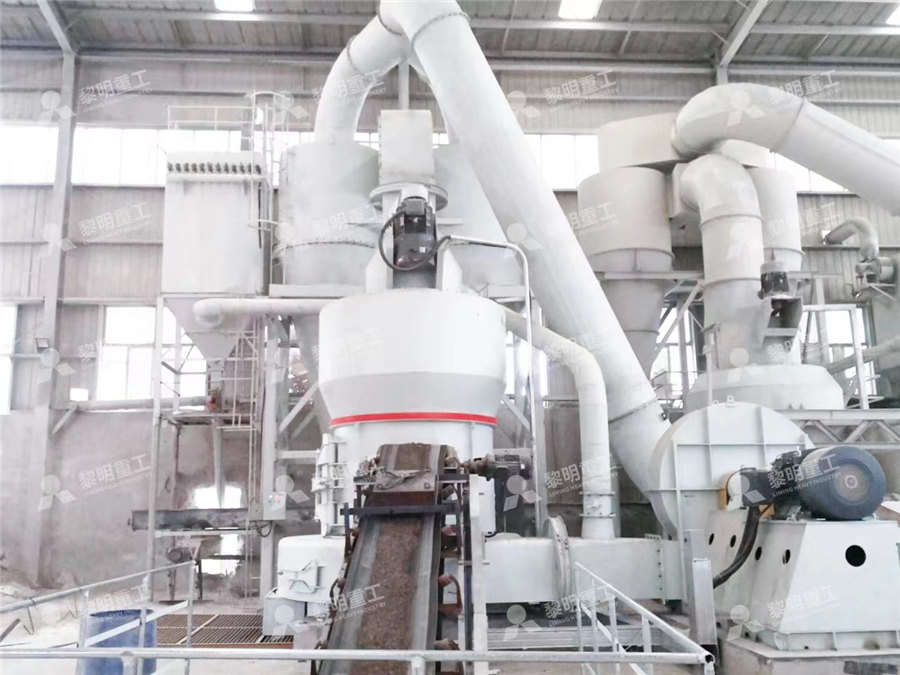
Calcium Carbonate Ball Mill Plant DASWELL
The calcium carbonate ball mill plant has the lowest energy consumption and the best particle size distribution, which is most suitable for market demand The calcium carbonate ball mill plant has the lowest energy consumption and the 2020年1月11日 Here the structure means the ratio of ball mill length to its diameter According to the industrial tests, the capacity varies with the ball mill types; Even from the same type of ball mill, the energy consumption and 5 Ways to Improve the Ball Mill Efficiency FTMIt has been recognized that the grindability of an ore in a ball mill is a function of both feed and mill parameters: Work index, W i; Largest particle size and size distribution; Mill Power Consumption Example Ball mill = 35 m x 35 m; Rubber lining = 75 mm % Mill volume charge = 40%; Grinding balls diameter = 70 mm;AMIT 135: Lesson 7 Ball Mills Circuits – Mining Mill Operator 2015年10月15日 A) Total Apparent Volumetric Charge Filling – including balls and excess slurry on top of the ball charge, plus the interstitial voids in between the balls – expressed as a percentage of the net internal mill volume (inside liners) B) Overflow Discharge Mills operating at low ball fillings – slurry may accumulate on top of the ball charge; causing, the Total Charge Calculate Ball Mill Grinding Capacity 911Metallurgist
.jpg)
Ball mill characteristics and test conditions Download Table
This paper presents the kinetics study of dry ball milling of calcite and barite minerals The experimental mill used was a laboratory size of 209 mm diameter, 175 mm length, providing a total 2011年1月1日 The digital energy meter was previously tested and evaluated in Bond ball mill Work Index testing where direct measured comminution energy of ores processed in the Bond ball mill were compared Measurement of electrical energy consumption in a Bond ball mill2020年7月24日 The energy consumption of grinding is the subject of many studies, especially in the case of ball mills for grinding clinkers [8, 9], fuels [10], iron ore [11], hematite ore [12], sulfide ore [13 Determination of granulometrical composition of the clinker 2018年2月1日 In another study to investigate ball size distribution on ball mill efficiency by Hlabangana et al [50] using the attainable region technique on a silica ore by dry milling, a threeball mix of Effect of ball and feed particle size distribution on the milling

What is a Ball Mill?
2023年6月12日 A ball mill is a type of grinder that uses metal balls or other grinding mediums to reduce the size of various materials The material to be ground is placed in a cylindrical container that spins on its axis The metal balls or grinding media inside the container hits the material and breaks it down into smaller particles