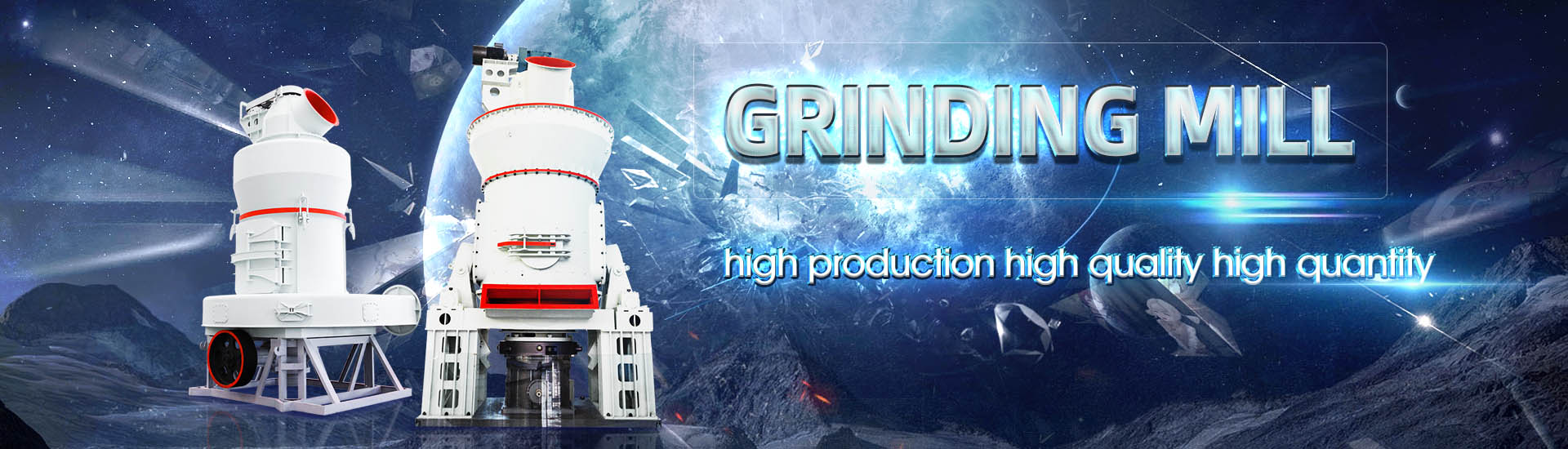
Coal mill maintenance work report Face up to the challenge
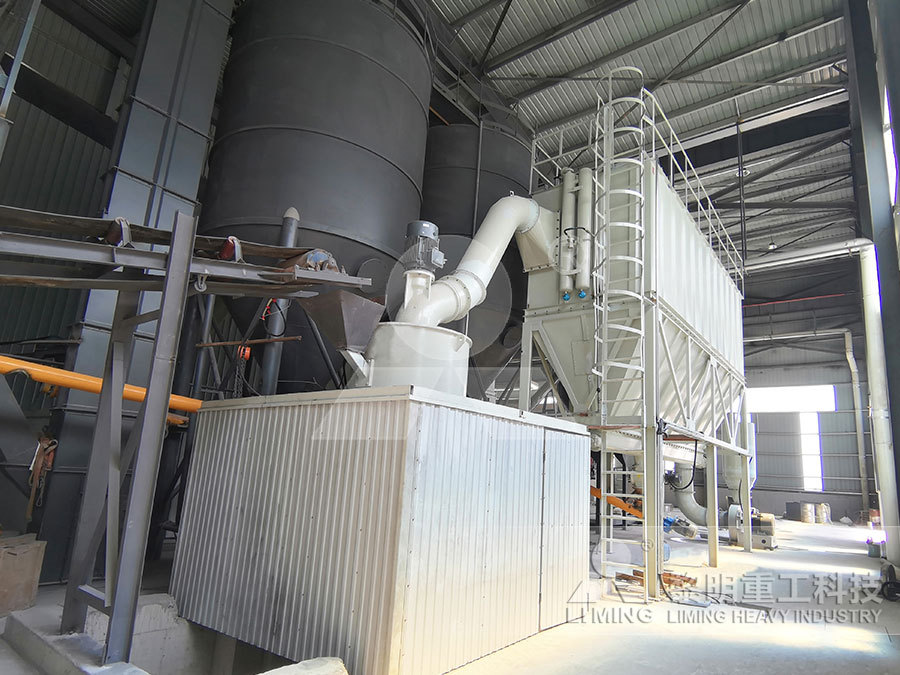
Operation and Maintenance of Coal Handling System in Thermal
2011年1月1日 Analyze technical characteristics of coal handling system and operating characteristics of the relevant machinery and equipment Then, the safe operation of coal 2011年12月31日 Analyze technical characteristics of coal handling system and operating characteristics of the relevant machinery and equipment Then, the safe operation of coal handling system and the proper(PDF) Operation and Maintenance of Coal Handling The maintenance to keep these mills in shape is influenced significantly by the results of the fineness testing At a time when many plants are reducing their mill maintenance budget to Coping with Coal Quality Impacts on Power Plant Operation and Maintenance of coal handling plants (CHP) of thermal power stations has traditionally as the processes related to the performance of routine, unscheduled and emergency maintenance It Quality Assured Maintenance Management For Coal Handling Plant
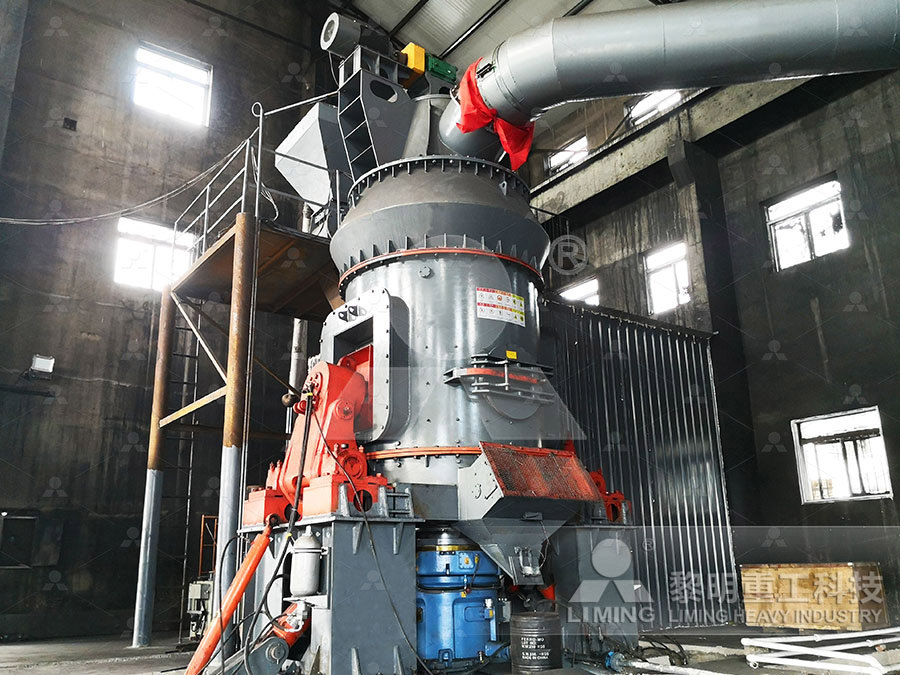
Coal mill pulverizer in thermal power plants PPT SlideShare
2012年11月17日 The document discusses coal mill/pulverizers used in thermal power plants It describes how pulverized coal is dried, ground, circulated, and classified within the mill to THE DESIGN EVALUATION AND OPERATION OF COAL MILL DUST COLLECTORS FACING THE CHALLENGE Introduction Today’s regulatory climate has cement plants worldwide facing CHALLENGE Parker Hannifin Corporation2015年8月1日 Power plant performance and reliability is highly influenced by coal mills that grind, dry, and transport coal to the furnace This paper presents a review of the current state Review of control and fault diagnosis methods applied to coal 2020年4月2日 The results show, the highest mill in service not affected to the boiler parameters such as reheater metal temperature, main steam temperature and boiler flue gas outlet and Analysis of the Coal Milling Operations to the Boiler Parameters
.jpg)
Increasing the flexibility of coalfired power plants
A recent report from the IEA Clean Coal Centre discussed the growing capacity of renewable energy plants around the world and the effects of their intermittent and highly variable output Substantial savings, owing to reduced maintenance costs and production losses, can be achieved through fewer mill choking incidents, fewer mill runbacks, optimal mill operation, and rapid Coal Mill an overview ScienceDirect Topics2036 Lihua ZHAO and YLihua ZHAO / Procedia Engineering 00 (in LIN / Procedia Engineering 26 (2011) 2032 – ) 000–000 5 222 b Application and maintenance of Ring hammer coal crusher hammerOperation and Maintenance of Coal Handling System inOur ATOX® Coal Mill has large rollers with great grinding capability of virtually all types of raw coal The rollers work harmoniously with a highlyefficient separator and feed sluice to consistently and reliably deliver coal meal The three ATOX® Coal Mill FLSmidth Cement
.jpg)
Life at the coal face: Who are the UK's 21st Century
2012年2月29日 The UK's biggest mining firm UK Coal has been fined a total of £450,000 for safety failings which led to the deaths of four men underground It follows the deaths of a further five men at Raw coal enters the top of the pulverizer through the raw coal feed pipe The raw coal is then pulverized between the roll and rotating ring Hot air is forced in through the bottom of the pulverizing chamber to remove unwanted moisture and transport the coal dust up through the top of the pulverizer and out the exhaust pipe directly to the burnerCoal Pulverizer – Power Plant Pall Corporation2021年8月1日 HP type medium speed coal pulverizer produced by Shanghai heavy machinery works has been widely used in recent years, with common faults in operation, short maintenance cycle and heavy task(PDF) Fault analysis and optimization technology of HP2021年9月9日 Rapid changes in electricity power markets have increased the production costs of coalfired power plants and pushed their production to the limits of profitability For power plants currently in operation, a possible approach to cope with this issue is to introduce novel methods that increase the plant’s reliability and availability Coal mills are a subsystem that should Impact of RemediationBased Maintenance on the Reliability of a Coal
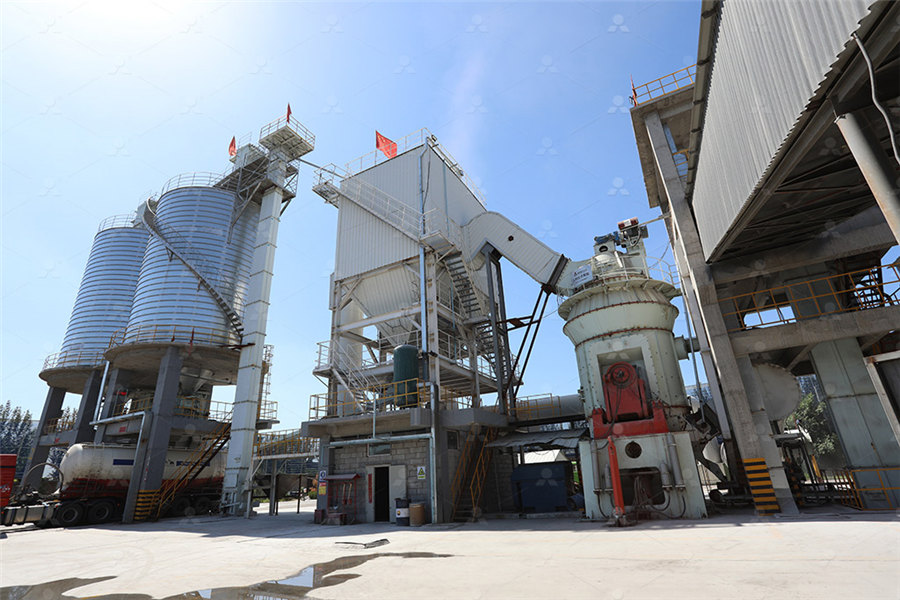
An investigation of performance characteristics and energetic
2020年8月12日 This study shows the performance of a currently running vertical roller coal mill (VRM) in an existing coalfired power plant In a power plant, the coal mill is the critical equipment, whose Report boundary and scope This Report covers all of Centennial's whollyowned operations, and assets that operate as joint ventures, for the period 1 January 2017 to 31 December 2017 Centennial has elected to produce a Global Reporting Initiative (GRI) referenced sustainability report for 2017 (GRI Report), to detail specific informationCentennial Coal Sustainability Report 2017The work presented in this paper, is based on a Babcock MPS 212 coal mill used at Elsam’s Nordjyllandsværktet Unit 3 However, the methods proposed in the paper are so generic hence they can be applied to other coal mill types The coal mill is illustrated in principle in Fig 1 The coal is fed to the coal mill through the central inlet pipeCoal Mill an overview ScienceDirect Topics5 VERTICAL ROLLER MILL KTM Main data Type Min motor power Max motor power Min capacity Max capacity [kW] [kW] [t/h] [t/h] KTM 400 11 18,5 0,1 0,8 KTM 800 37 55 2 5 KTM 1000 55 90 4 8 KTM 1200 90 132 6 12 KTM 1400 132 200 9 18 KTM 1600 200 315 12 24 KTM 1800 315 400 20 38 KTM 2000 400 500 29 50 KTM 2200 500 630 39 64 KTM 2400 630 800 GRINDING AND SEPARATING TECHNOLOGY SYSTEMS
.jpg)
Mill Inerting and Pulverizer/Mill Explosion Mitigation
• Smoldering coal inside an idle mill can evolve into a big problem when the mill is started, agitating these accumulation combined with a high air to fuel ratio environment • PRB is one of the most difficult coals with respect to mill fires and explosions • Mill internal temperatures are generally high enough somewhere to ignite any type of2020年8月12日 To understand the performance of a vertical roller coal mill, the real operational tests have been performed considering three different coal sources Obtained results indicate that grinding pressure, primary air (PA) temperature and mill motor current have a tendency to rise by increasing coal feeding mass flow rates for all used coalAn investigation of performance characteristics and energetic COAL MILL Derek Stuart, AMETEK Land, and Todd Collins PE, Hoosier Energy, US, discuss available the abrasion shield to face the flow of maintenance Commissioning took place during an outage in May 2011 The main practical challenge inCOAL MILL Land Instruments International2023年10月12日 The present Indian annual demand of 120 Mt is expected to go up to 310 Mt by the end of this century Although the major share of this is expected to come from opencast mines, underground coal (PDF) INSTALLATION OF HIGH CAPACITY BELT CONVEYOR
.jpg)
Overhaul Procedure For Coal Mill PDF Scribd
Overhaul Procedure for Coal Mill Free download as Powerpoint Presentation (ppt / pptx), PDF File (pdf), Text File (txt) or view presentation slides online The document outlines the steps for an overhaul procedure of a coal mill It involves 21 steps to remove, inspect, replace, and reinstall components Key steps include removing the mill cover, inspecting and replacing grinding 2019年4月29日 Capital Cost Estimating Methodology for Coal Washing PlantCoal Preparation PlantCHPP Heng Huang 8y After the coal preparation plant goes into operation,the main design issues are exposed 6 Keys to Successful Coal Preparation Plant Maintenance2014年1月1日 The emission factors of kiln end, kiln head, coal mill, crushing and cement mill was 0156 clinker g/t, 3914 clinker g/t, 1538 coal g/t, 0016 stone g/t and 0056 cement g/t respectively, the (PDF) MPS mills for coal grinding ResearchGate2009年1月1日 Most plants that burn PRB coal were not designed to deal with the fuel's propensity to ignite in bunkers, silos, and hoppers Recognizing this, the PRB Coal Users' Group has come up with a set of Selection of coal mill reject handling system for ResearchGate
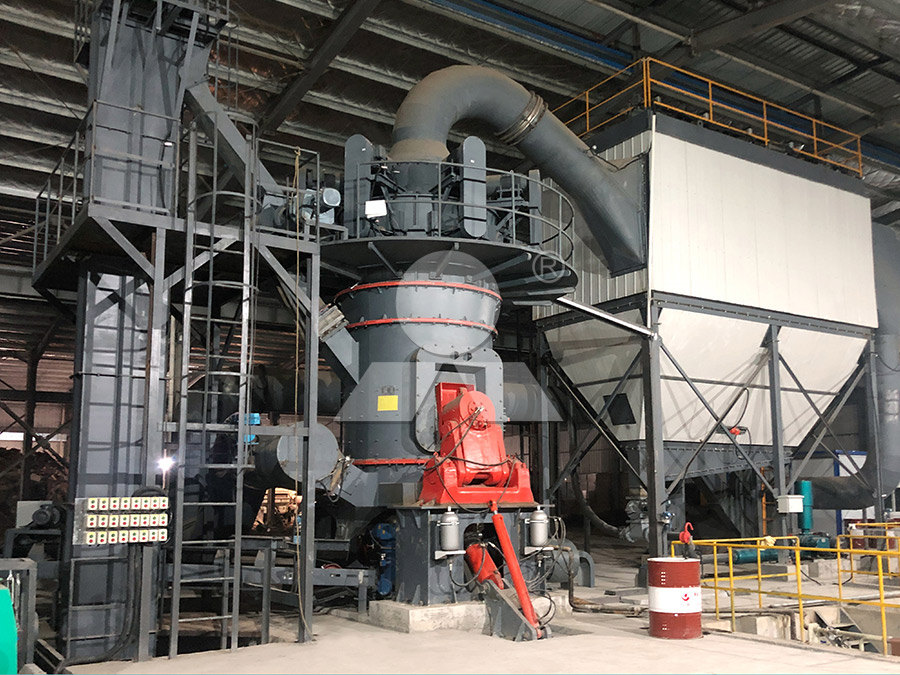
Example COAL MINING RISK ASSESSMENT CMRa
47 The Coal Authority report confirms the absence of proven or unrecorded mine workings 48 The local geology consists of deep superficial deposits up to 80m thick, underlain by the Pennine Lower Coal Measures Formation 49 There is an ambiguity between geological mapping and Coal Authority mining records for the site2016年10月20日 General Ball Mill Maintenance After the mill is erected, in order to avoid overlooking both obvious and obscure installation details, we recommend the use of a check list This is particularly recommended for Ball Mill Maintenance Installation Procedure2021年5月14日 The mill operates 24hours a day and is responsible for the grinding, drying, transporting and classification of the coal Babcock’s mill maintenance specialist says that the reliability of the mill is essential to ensure correct coal fineness, dryness and throughput, with the performance of the milling plant significantly impacting on plant Babcock wins coal milling maintenance contractHard coal is a sedimentary rock which was formed by deposition and carbonization of plant remains It is hard and resistant More than 50% of its weight is made up by carbon Therefore it is classified as highrank coal Coal mills for all requirements Gebr Pfeiffer
.jpg)
COAL
1 Fuel handling and storage – raw coal receiving, storage and handling 2 Fuel preparation – raw coal grinding 3 Fuel conveying – fine coal storage and conveying for an indirect firing system 4 Fuel conveying – fine coal conveying for a direct firing system 5Spillage and unsafe conditions at coal mill Kiln burner (firing system)2020年4月7日 Monitoring and diagnosis of coal mill systems are critical to the security operation of power plants The traditional datadriven fault diagnosis methods often result in low fault recognition rate or even misjudgment due to the imbalance between fault data samples and normal data samples In order to obtain massive fault sample data effectively, based on the Modeling of Coal Mill System Used for Fault Simulation MDPI2023年12月14日 Indian Railways’ plan to raise the quantum of coal to be transported by rail by at least 400 million tonne in the next eight years face congestion and logistical challenges, the Institute for ‘Ambitious coaltransportation plans set to challenge Indian 2021年9月30日 While these coalbased units are meeting the stability challenge, they are operating mostly at offdesign conditions, with increased wear and tear of plant components that brings new challenges As more intermittent renewable sources are added to the grid worldwide, the need for flexible operation will increase (Kumar and Hillemann 2018 )Flexible Operation of High Efficiency Coal Power Plants to
.jpg)
How To Maintain a Coal Pulverizer? (All You Need To Know)
The work carried out by the coal mill is relatively heavy, so it will suffer more losses If these faults are not solved in time, they may cause some more serious problems It is very vital to do a good job in the maintenance of the coal mill Common Faults methane ignition that could result in a coal dust explosion is probably the most feared event of all by coal mine workers and mine management Effective ventilation remains one of the primary means of controlling methane in the face and for preventing methane buildup inside the cutting zone of the Continuous Miner headingPREVENTING CUTTING HEAD METHANE IGNITIONS ON Maintenance practices enhancement shall require shortterm interventions in the form of establishing and strengthening the maintenance planning function through establishment of a Maintenance Planning Cell along with preparation of a Plant Asset Database and a Condition Monitoring Plan Longer term interventions could be towardsStrengthening Operations and Maintenance Practices In StateSector Coal amount of pulverised fuel inside a hot mill The large surface area of the pulverised coal and the high temperature inside the mill lead to rapid oxidation of the coal This results in further heat buildup and the potential for a fire If the mill is restarted without first COAL HANDLING SAFETY Land Instruments International
.jpg)
Modeling and Parameter Identification of Coal Mill
2009年9月20日 A control oriented model was then developed by Fan (1994) and Fan and Rees (1994) In 2009, coal flow and outlet temperature of mill were modelled using mass and heat balance equations for startup 2018年5月8日 3 Repair: The detected fault is evaluated according to working schedule of the mill and necessary repair works are done LABORFORCE FOR MAINTENANCE ACTIVITIES Engineers in charge of production and maintenance have to be aware of all aspects of maintenance work Maintenance team is not only responsible for fixing and repairing Mill Maintenance Methods Miller MagazineSection of coal bowl mill Table 1 Guaranteed coal conditions for mill performance evaluation Coal Moisture % 20 Coal HGI 55 Mill Outlet Temperarure °C 80 Mill Air Flow T/hr 102 Coal Fineness (% passing trough 200 mesh) 70% passing through 200 mesh and 90% passing through 50 mesh Differental Pressure 300 mmwc Coal Output from Mill 609 t/hrA Study on 500 MW Coal Fired Boiler Unit’s Bowl Mill 2011年12月31日 Then, the safe operation of coal handling system and the proper method of the equipment maintenance are summed up Belt Conveyor Dual drums head actuations Fig3(PDF) Operation and Maintenance of Coal Handling System in
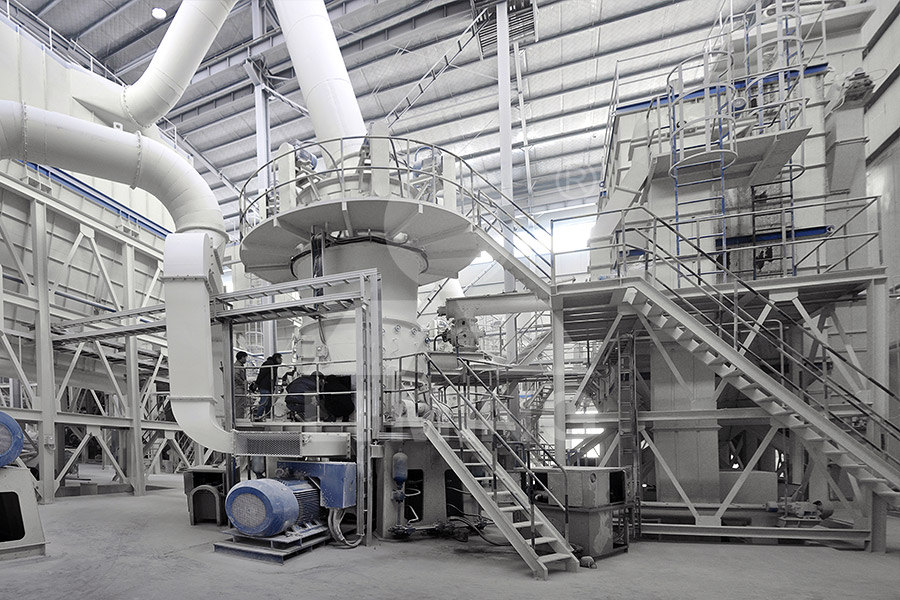
Coal Mill Manual PDF Furnace Combustion
Coal Mill Manual Free download as PDF File (pdf), Text File (txt) or read online for free This document provides an overview of the operation and maintenance of a pulverized coal system used for direct coal firing in power plants It describes the key components of the system including bowl mills that pulverize coal, windboxes that inject coal into the furnace, feeders that supply coal chain, with virtually all transport systems and most coal producers and consumers making use of stockpiles Stockpiling is carried out at coal mines, coal preparation plants, transhipment facilities (including export/import facilities) and end user sites such as power plants, coking plants and cement works With mounting pressure toManagement of coal stockpiles ICSC1927 First Loesche coal mill delivered for the Klingenberg power station in Berlin 1953 500th coal mill plant sold worldwide 1961 Introduction of hydraulic spring assembly system 1965 Construction of first pressure mill (LM 122 D) 1980 Delivery of first modular coal mill (LM 263 D) 1985 Delivery of first selfinerting coal grinding plant (LM 212 D) for the steel industry (PCI LOESCHEMILLS6 Construction and Maintenance of Belt Conveyors for Coal and Bulk Material Handling Plants practicalmaintenance also oscillating horizontally This phenomenon results in internal agitation to the material on belt and therefore the material’s external faces assume inclination at surcharge angle TheConstruction and Maintenance of Belt Conveyors for Coal and
.jpg)
Review of control and fault diagnosis methods applied to coal
2015年8月1日 Mill problems originate mainly due to poor controls or faults occurring within the milling system As discussed by GQ Fan and NW Rees [3], the control of mills remains very simple in most of the power plants due to the fact that the mill system is highly nonlinear with strong coupling among the variables and it is very difficult to measure some important