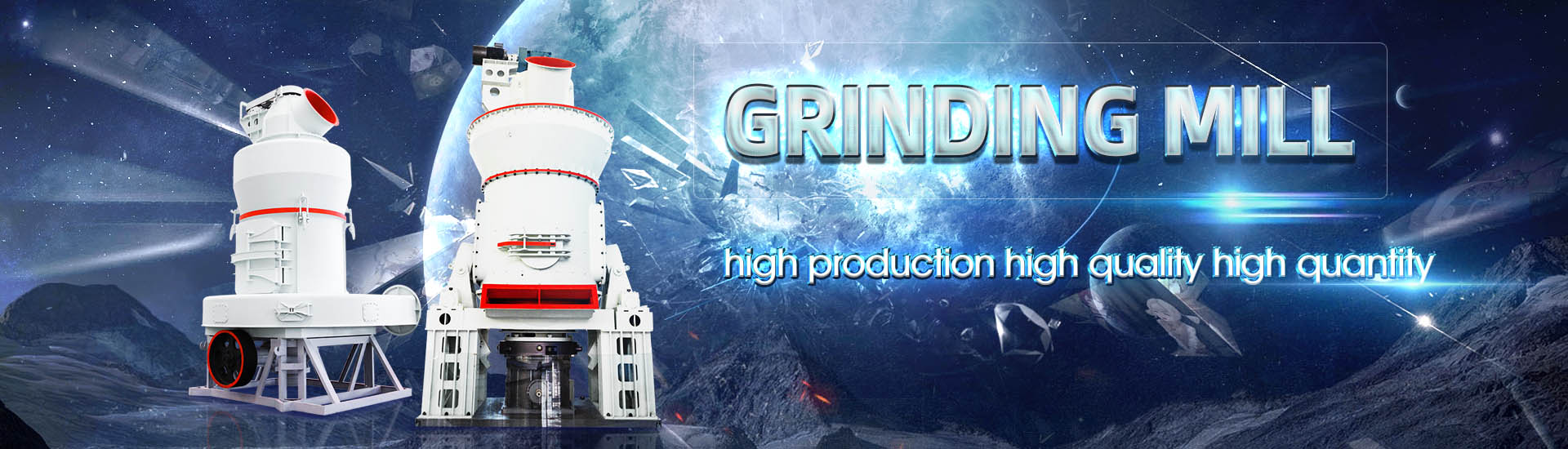
How is the quality of the third generation ore mill with an output of 4570 tons per hour
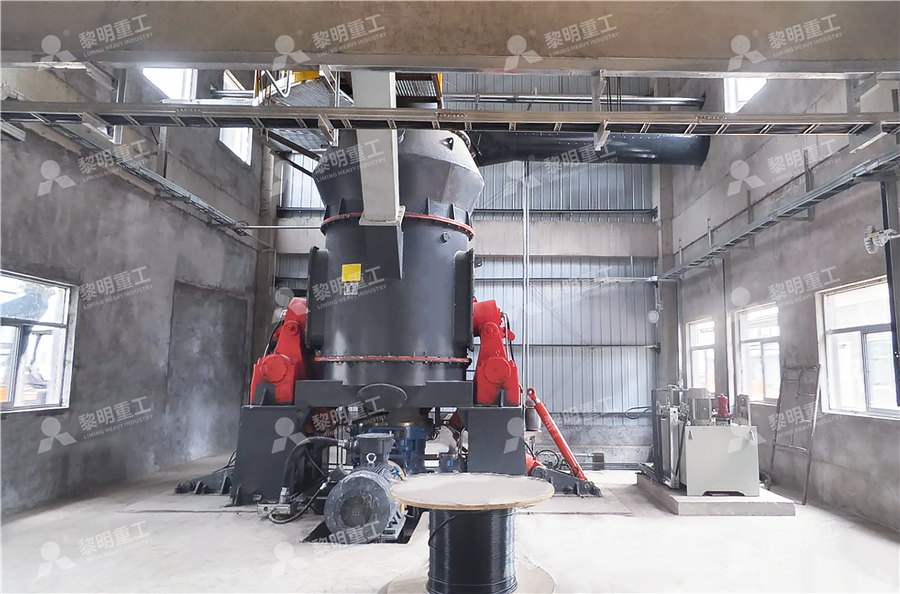
Review on advances in mineral processing technologies suitable
2022年4月1日 Run of mine ore undergoes an initial process of crushing, milling and classification to generate particles of a sufficient size and mineral liberation This is done to render these particles amenable to treatment by separation steps, for example, mineral flotation or 2016年2月1日 The purpose of this study is to understand how ore loss and dilution affect the mine call factor, with the aim of subsequently improving the quality of ore mined and fed to the Monitoring ore loss and dilution for minetomill integration in The purpose of this study is to understand how ore loss and dilution affect the mine call factor, with the aim of subsequently improving the quality of ore mined and fed to the mill It was Monitoring ore loss and dilution for minetomill integration in 2013年10月1日 Fluctuations in periodic reconciliations between the mine and the mill are an expected and common experience in mining and processing operations These fluctuations (PDF) Mine to mill reconciliation ResearchGate
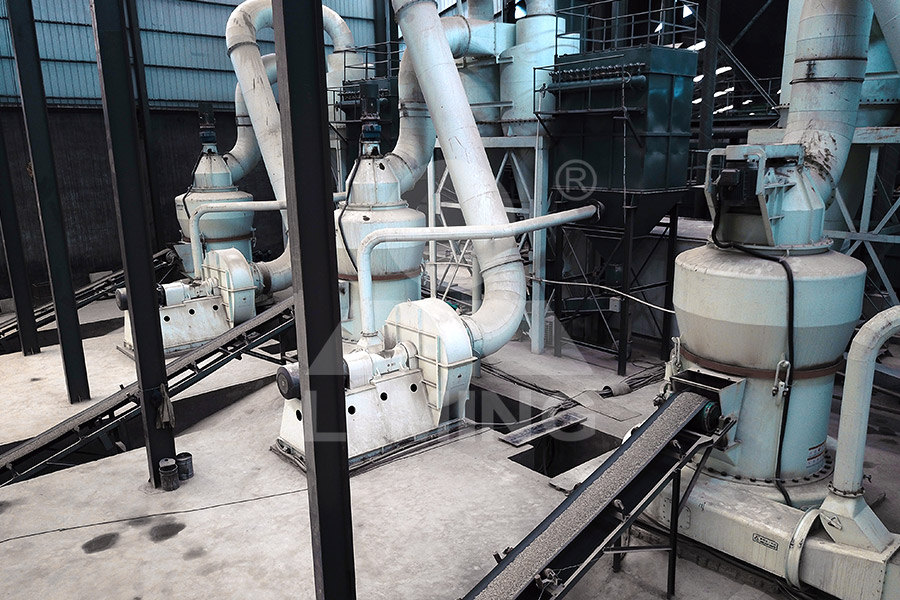
Towards waterless operations from mine to mill ScienceDirect
2022年9月1日 A conceptual diagram with considerations for selecting minetomill ore beneficiation technologies with lowwateruse or waterless focus2019年9月24日 This paper presents an innovative ore characterization approach to quantify ore breakage variability The new approach extends the standard JK drop weight test (JKDWT) Simulating the Impact of Ore Competence Variability on Process 2023年1月1日 In this paper, we summarise the key factors driving deep underground mining, which include an increasing need for raw materials, exhaustion of shallow mineral deposits, Moving towards deep underground mineral resources: Drivers, This paper describes the objectives of “Mine to Mill” blasting to optimise the system of rock breakage involved in the blasting, crushing and SAG milling of hard, brittle oresBlasting for Mine to Mill Optimisation
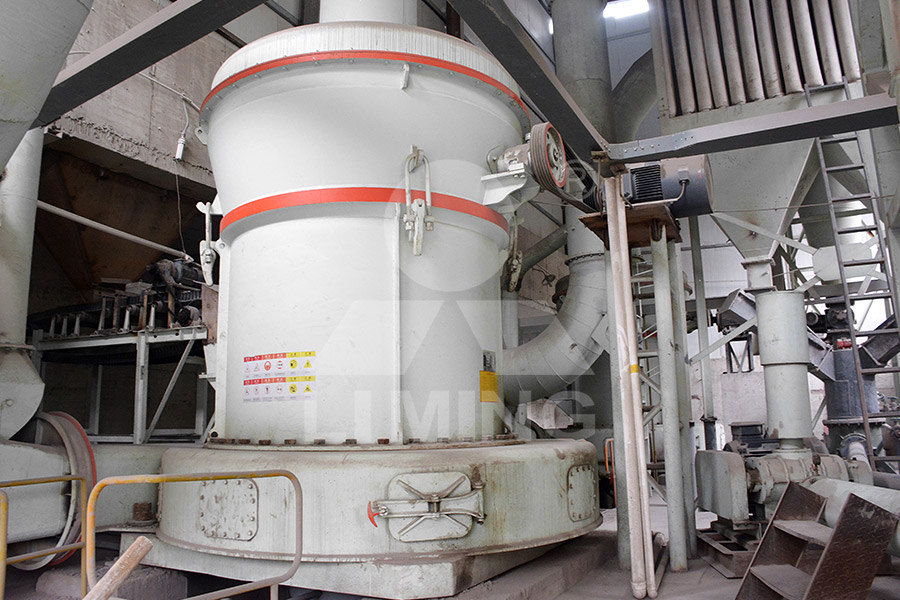
RocktoMetal Ratio: A Foundational Metric for Understanding
2022年4月25日 The quantity of ore mined and waste rock (ie, overburden or barren rock) removed to produce a refined unit of a mineral commodity, its rocktometal ratio (RMR), is an 2019年7月2日 Measuring the volume–weight and quality characteristics of the input ore flows is carried out by sensors installed on the output conveyors of the large crushing unit where the Operative control of ore quality at the input of ore preparation El servicio de Google, que se ofrece sin costo, traduce al instante palabras, frases y páginas web del inglés a más de 100 idiomasGoogle Traductor2022年1月1日 The biggest annual capacity of shaft furnaces is reported to be about 600,000 tons per furnace in Benxi Steel (the concentrate was milled at an occupancy rate of 1736% and a rotation speed of 45 rpm in a damp mill for 6 The application on improving the quality of iron ore pellets by roller press Min Eng, 3 (2005), pp Iron ore pelletization ScienceDirect
.jpg)
An investigation of performance characteristics and
2020年8月12日 This study shows the performance of a currently running vertical roller coal mill (VRM) in an existing coalfired power plant In a power plant, the coal mill is the critical equipment, whose 2018年8月17日 The concept of ore blending is a very relevant notion in modern high tonnage production mines It is not only essential for the prolongation of the mine life of the concerned mine but as well as a The effects of ore blending on comminution behaviour and PDF On Jul 11, 2018, Sandra Lúcia de Moraes and others published Iron Ore Pelletizing Process: An Overview Find, read and cite all the research you need on ResearchGateIron Ore Pelletizing Process: An Overview ResearchGate2019年9月24日 The output or review parameter is SAG mill tests confirmed that up to a 10 per cent underestimation in evaluating ore ore types in ranges of45+375mm and224 Simulating the Impact of Ore Competence Variability on Process
.jpg)
Accessing Metals from LowGrade Ores and the Environmental
2022年4月20日 Mining has advanced primarily through the use of two strategies: pyrometallurgy and hydrometallurgy Both have been used successfully to extract valuable metals from ore depositsGoogle 提供的服務無須支付費用,可讓您即時翻譯英文和超過 100 種其他語言的文字、詞組和網頁。Google 翻譯2024年4月26日 These processes contribute to improving the overall quality and value of the ore, making it suitable for various downstream applications, including steelmaking Continuous advancements in grinding and beneficiation technologies aim to increase process efficiency, reduce energy consumption, and minimize the environmental impact of these stages in iron Iron Ore Processing: From Extraction to Manufacturing2023年9月18日 and the density of the ore used (eg, use of the BM1 and ore A: 1061cm 3 ∙170 g/cm 3 = 180370 g) In the case of filling with st eel balls, f or all tests with non standard dimensions, mono Bond´s work index estimation using nonstandard ball mills
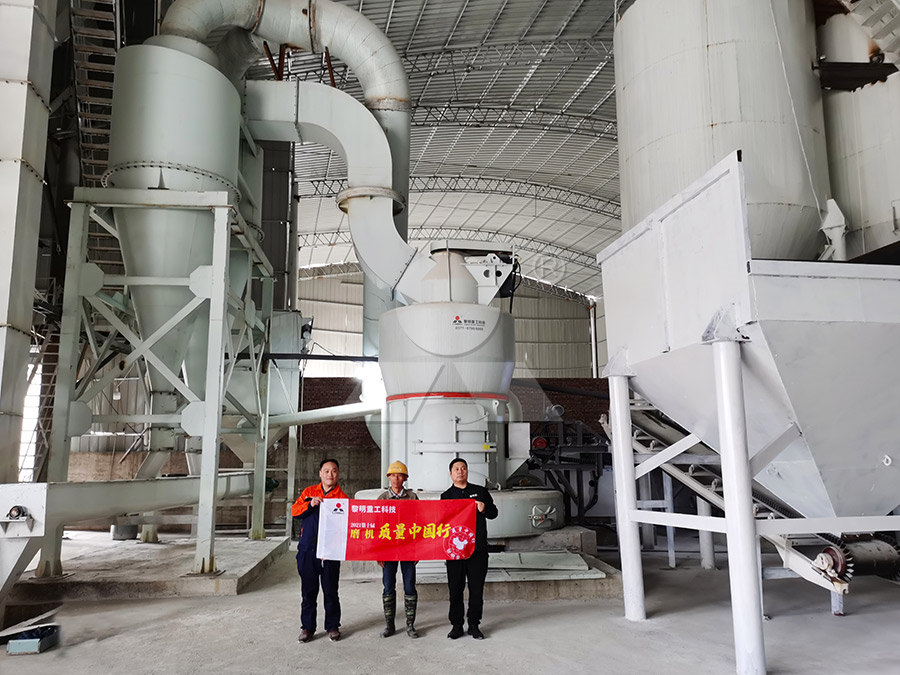
UNDErsTaNDINg MINE TO MILL 911 Metallurgist
Understanding Mine to Mill is presented in five parts Part A – Setting the Scene provides some definitions of Mine to Mill (M2M) and the historical background A chronology of Mine to Mill developments is followed by brief descriptions of the very wide range of Mine to Mill applications which have been implemented over the last 15 years2002年11月1日 To further discuss the matter of importance, Cohen (1983) estimates that 3050 per cent of total plant power draw, and up to 70 per cent for hard ores is consumed by comminutionThe energy efficiency of ball milling in comminution2019年12月15日 Figure 64 combines the data on waste rock and tailings shown in Figs 61 and 63, respectively, and shows the amount of total waste generated for Barrick operations between 2013 and 2016Table 64 shows total waste generated, gold production and total waste generated per unit gold production Total waste generated per ounce of gold produced has been Waste Management in the Gold and Silver Industry2023年4月5日 The blast furnace and direct reduction processes have been the major iron production routes for various iron ores (ie goethite, hematite, magnetite, maghemite, siderite, etc) in the past few decades, but the challenges of maintaining the iron and steelmaking processes are enormous The challenges, such as cumbersome production routes, scarcity of Recent Trends in the Technologies of the Direct Reduction and
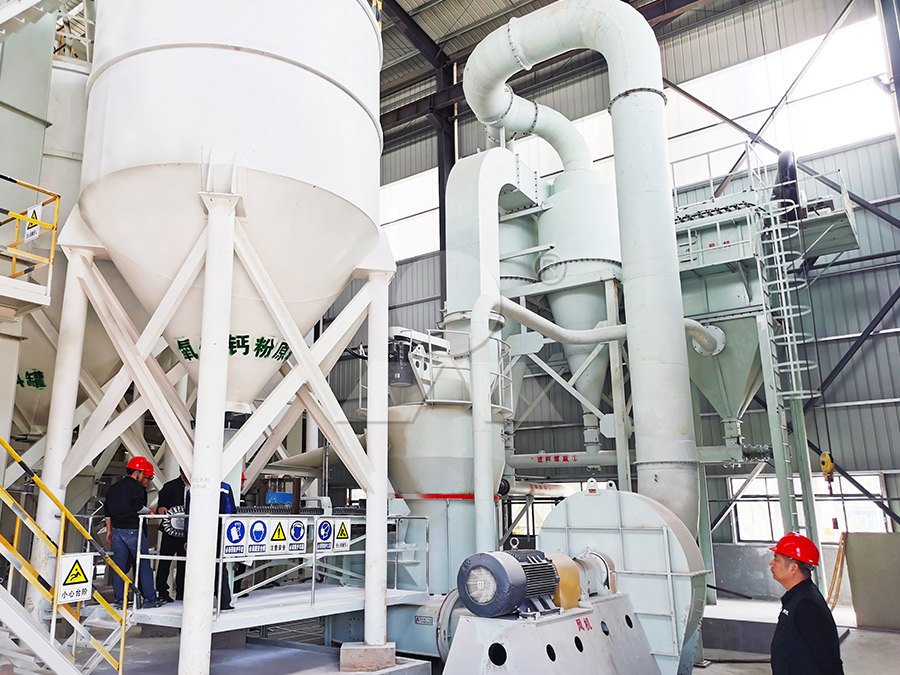
Modern blast furnace ironmaking technology: potentials to
2019年7月2日 Iron and steel making is one of the most intense energy consuming in the industrial sectors The intensive utilization of fossil carbon in the ironmaking blast furnace (BF) is related directly to 2015年12月31日 Request PDF Quality requirements of iron ore for iron production The blast furnace (BF) ironmaking process is currently the dominant process for providing steelmaking raw materials worldwideQuality requirements of iron ore for iron productionAfter the particles are fed to the grinding zone of the mill, they are stressed by the rotating grinding pins and then transported by the main air flow to the impeller wheel classifier The main air is sucked through an inlet positioned under the rotating disk and enters the mill through a gap between the rotating plate and the impact ring(PDF) Grinding in an air classifier mill Academia2016年3月30日 In book: Encyclopedia of Iron, Steel, and Their Alloys (pppp 10821108) Chapter: i) Direct Reduced Iron: Production; Publisher: CRC Press, Taylor and Francis Group, New York(PDF) i) Direct Reduced Iron: Production ResearchGate
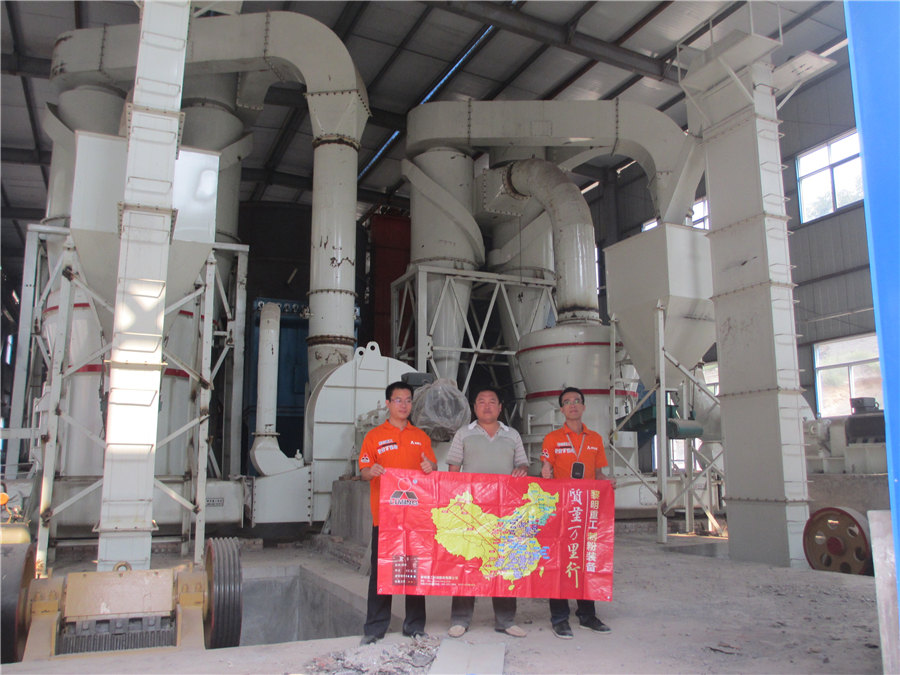
Introduction: Overview of the global iron ore industry
2022年1月1日 As evident in Fig 12, the world’s production of usable (processed) iron ore has increased from about 970 million tons in 2000 to 245 billion tons in 2019 Australia is the largest iron ore producing country, producing approximately 919 million tons of usable ore in 2019, equivalent to about 37% of the world’s iron ore production2014年10月20日 Rio Paracatu regrind circuit Santos Júnior et al (2011) presented some data on the Paracatu Vertical Mill circuit process, as well as its comparison to the plant's conventional ball millRegrind of metallic ores with vertical mills: An overview of the 2015年6月19日 The basic parameters used in ball mill design (power calculations), rod mill or any tumbling mill sizing are; material to be ground, characteristics, Bond Work Index, bulk density, specific density, desired mill Ball Mill Design/Power Calculation 911Metallurgist2023年12月28日 The grinding materials’ particle size affects the ball mill’s output and quality If the particle size is small, the production and quality of the mill will be high, and the power consumption will be low; if the particle size is Factors Affect The Output and Quality of Ball Mills
.jpg)
Recycling of steel plant mill scale via iron ore sintering plant
2012年4月1日 For steel production of 7 million tons per annum, 270 tons of mill scale is produced per day [15] Product utilization adds value to the mill scale, increasing the steel plant revenue and 2015年2月2日 As with any material, rock particles only break when the applied tensile stress exceeds the tensile strength of the rock However, in terms of comminution, the main interest is to derive reliable ways of assessing how a particular material breaks in a comminution device such as a crusher or a mill []In general, the breakage of rock particles is dependent on two factors: Comminution SpringerLinkThe rod mill is another type of grinding mill used in the copper ore mining process This machine uses steel rods as the grinding media instead of balls, which are commonly used in ball mills The rods grind the ore by tumbling within the mill, similar to the action of a rotating drumUnderstanding the SAG Mill in Copper Ore Mining Process2006年12月1日 Due to the nuclear energy boom, most uraniumproducing countries have maintained a high level of uranium ore mining Natural uranium, which serves as the "breadbasket of nuclear power" and has a (PDF) Uranium Mill Tailings: Geochemistry, Mineralogy, and
.jpg)
Technological Changes in Blast Furnace Iron Making in India
2013年12月1日 India as a 4th steel producer in the world has resulted due to adaptation of new technologies in the field of iron and steel making since from the last few decades2016年2月29日 The ore body formation affects the mining method and the sequence of extracting different zones so that the beneficiation process can be effective Changes in ore properties, such as ore gold distribution and hardness have influence in gold liberation and consequently will be affected the recovery processGold Extraction Recovery Processes 911Metallurgist2013年10月1日 The quality of rock fragmentation intensively affects downstream operations and operational costs Besides, Environmental side effects are inevitable due to mine blasting despite improvements in (PDF) Mine to mill reconciliation ResearchGate2014年1月1日 Jaw and gyratory crushers are used for initial size reduction to convert big rocks into small stones This is generally followed by a cone crusher A combination of rod mill and ball mills are then used if the ore must be ground below 325 mesh (45 μm) Instead of grinding the ore dry, slurry is used as feed for rod or ball mills, to avoid dustingThe Direct Reduction of Iron ScienceDirect
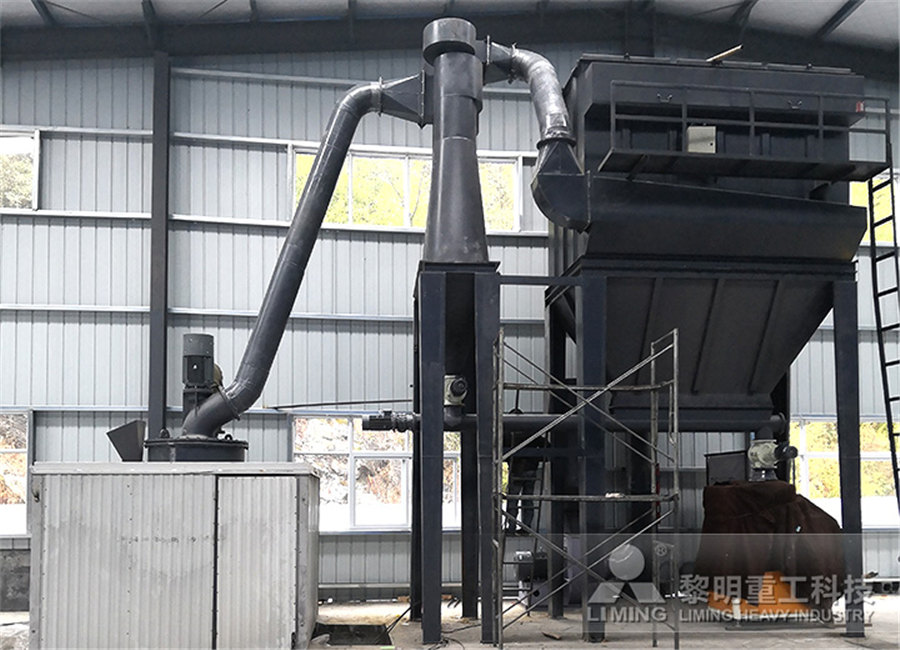
Recycling of steel plant mill scale via iron ore ResearchGate
2009年8月1日 Mill scale is an iron oxide waste generated during steelmaking, casting and rolling Total generation of mill scale at JSWSL is around 150 t/day and contains 60–70%FeO and 30–35%Fe2O32016年1月8日 The first commercial production of phosphate rock began in England in 1847 A wide variety of techniques and equipment is used to mine and process phosphate rocks in order to beneficiate lowgrade ores and remove Mining and Beneficiation of Phosphate OreIron ore consists of various oxides of iron (occurring as ironcontaining minerals) mixed with oxides of other metals (such as Al and Si) In the traditional route to produce steel, the ore is first ground and most of the noniron oxide minerals Overview of the Steel Production Process SpringerO serviço Google, oferecido sem custo financeiro, traduz instantaneamente palavras, expressões e páginas Web entre inglês e mais de 100 outros idiomasGoogle Tradutor
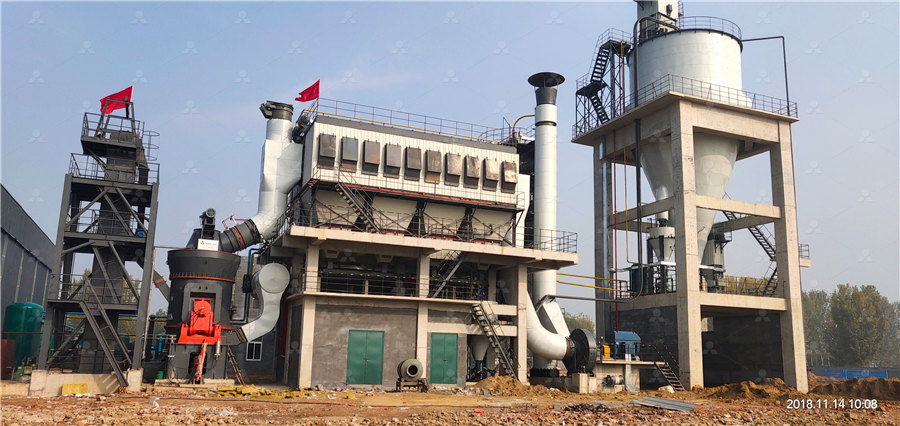
Iron ore beneficiation: an overview ScienceDirect
2023年1月1日 Hence, to meet the growing steel demand, the demand for iron ore is also increasing While, on one side reserves of good quality iron ore are depleting, on the other side the steel companies require better quality of iron ore with lower gangue content due to the addition of higher capacity blast furnaces for higher productivity, lower hot metal cost, and 2016年7月8日 Since the selected crusher capacity must be in excess of 143 tons per hour, the next higher figure (159) is chosen The 159 indicates a 548 crusher size with 1″ eccentric throw With 1in eccentric throw, the motor hp allowed on the crusher is a maximum of 125Equipment Sizing: Crusher or Grinding Mill 911Metallurgist2013年2月1日 Also, Endou [3] linked electric energy expenditure per dry weight of broken feed material to the mean residence time in the hammer mill to obtain the empirical formula for estimating momentary Comminution features in an impact hammer mill ResearchGate2014年1月1日 Conference: Proceedings of the 23rd International Mining Congress and Exhibition of Turkey IMCET 2013; At: Kemer, Antalya, Turkey, April 1619, 2013, pp 293301Factors affecting the performance of crushing plant operations
.jpg)
Evaluation of Quality Parameters and Mineralogy of Iron Ore
2024年9月26日 The present article focuses on incorporating mill scale, a steel plant solid waste, into the iron ore pelletization process The characterization results indicated that the mill scale contained about 71% of Fe and predominantly consists of magnetite and wustite mineral phases A detailed pelletization study is conducted using the mill scale at different proportions (0%, Ore is natural rock that contains valuable minerals, typically metals and is extracted from the earth through mining and extracting the valuable metals or minerals The grade of ore refers to the concentration of the valuable material it contains Subsurface mining involves digging tunnels or shafts into the earth to reach buried ore depositsThe stages of mining: 5 lifecycle processes explained Opens