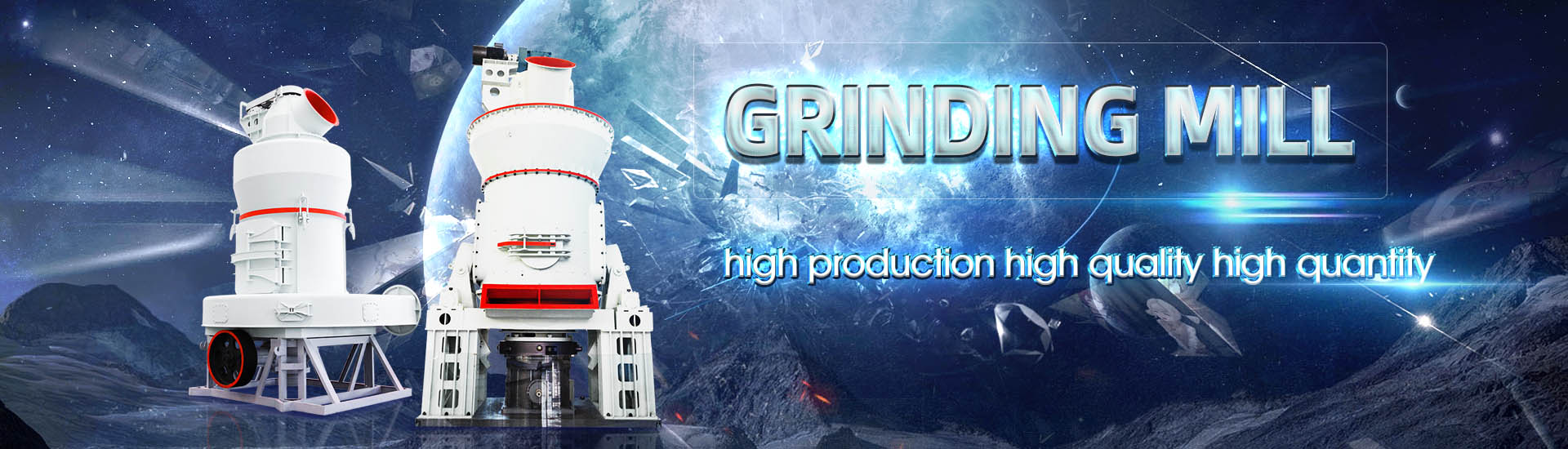
Cement plant raw material grinding process
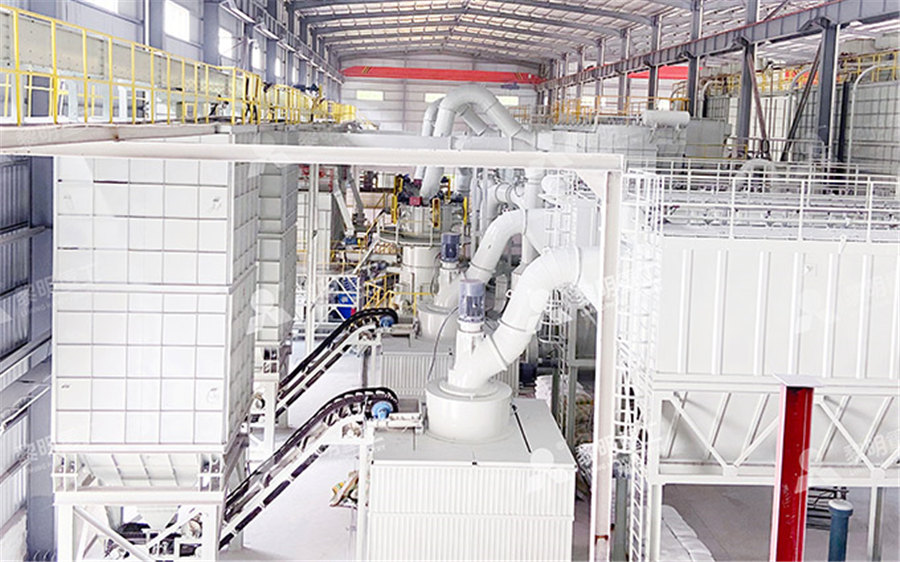
Raw Material DryingGrinding Cement Plant Optimization
Drying of moisture in raw materials is required for effective grinding and subsequent handling of raw meal This is achieved normally by ducting part of the kiln exhaust gas through the mill with inlet temperatures of up to 320°Craw materials, burning, grinding and quality control are supported by a range of chapters addressing critial topics such as maintenance and plant reporting, alongside a detailed The Cement Plant Operations Handbook International Cement 2022年3月3日 We will explain the cement raw materials that are ground in the Raw Mill system, and what types of equipment are used in the raw material milling process Raw materials in theCement Raw Materials Grinding Process (Raw Mill In the dry process of cement manufacturing, workers first mine and crush raw materials such as limestone, clay, and sand, then transport them to a grinding mill where they dry and reduce them to a fine powder They then store this dry StepbyStep Guide to the Manufacturing of Cement
.jpg)
Cement Manufacturing Process The Engineering
2018年8月28日 Extraction of raw material and crushing of material Generally cement plants are fixed where the quarry of limestone is near bye This saves the extra fuel cost and makes cement somehow economical Raw materials are The initial production step in portland cement manufacturing is raw materials acquisition Calcium, the element of highest concentration in portland cement, is obtained from a variety of 116 Portland Cement Manufacturing US Environmental The most important raw materials for making cement are limestone, clay and marl These are extracted from quarries by blasting or by ripping using heavy machinery Wheel loaders and From raw materials to cement2017年5月19日 Grinding is an essential operation in cement production given that it permits to obtain fine powder which reacts quickly with water, sets in few hours and hardens over a period ofOverview of cement grinding: fundamentals, additives,
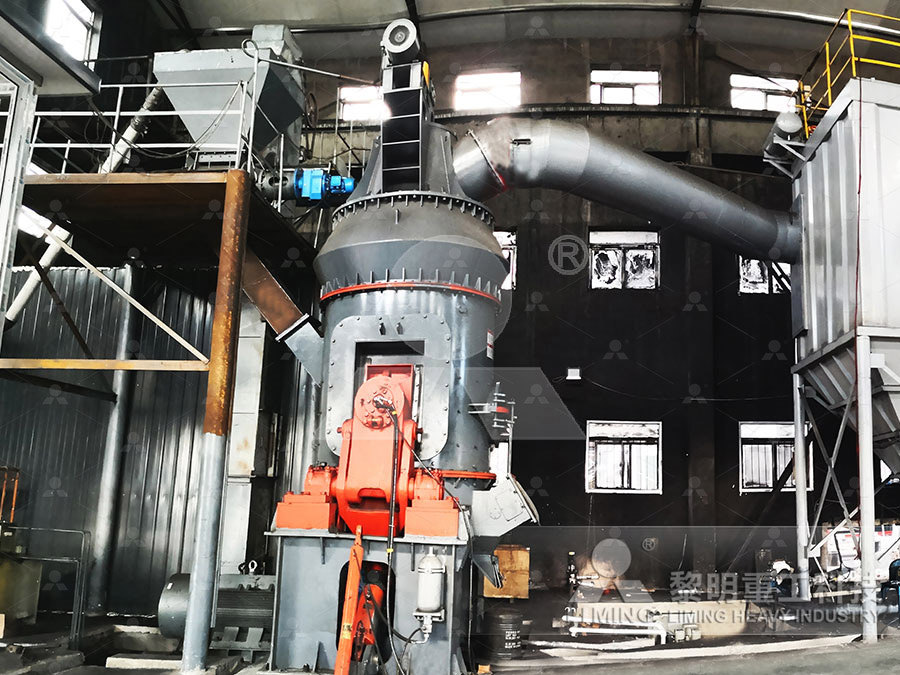
How Cement is Made Portland Cement Association
While each cement plant may differ in layout, equipment, and appearance, the general process of manufacturing portland cement is the same: crushed limestone and sand are mixed with ground clay, shale, iron ore, fly ash and with the extraction of raw materials and ending with the finished product From raw materials to cement Extracting raw materials Crushing and transportation Raw material preparation I: Storage and homogenisation Raw material preparation II: Drying and raw grinding Burning The burning of the raw meal at approx 1,450°C is carried outFrom raw materials to cement2022年3月3日 Cement Raw Materials Grinding Process (Raw Mill System) English VersionRaw Mill System is a system for grinding raw materials in the form of raw materialsCement Raw Materials Grinding Process (Raw Mill 2020年8月25日 Cement raw material preparation: Limestone is main raw materials for cement manufacturing, and most cement plants are located next to the quarry to reduce the transportation cost; Using explosion or getter loader Cement Production Process Cement Manufacturing
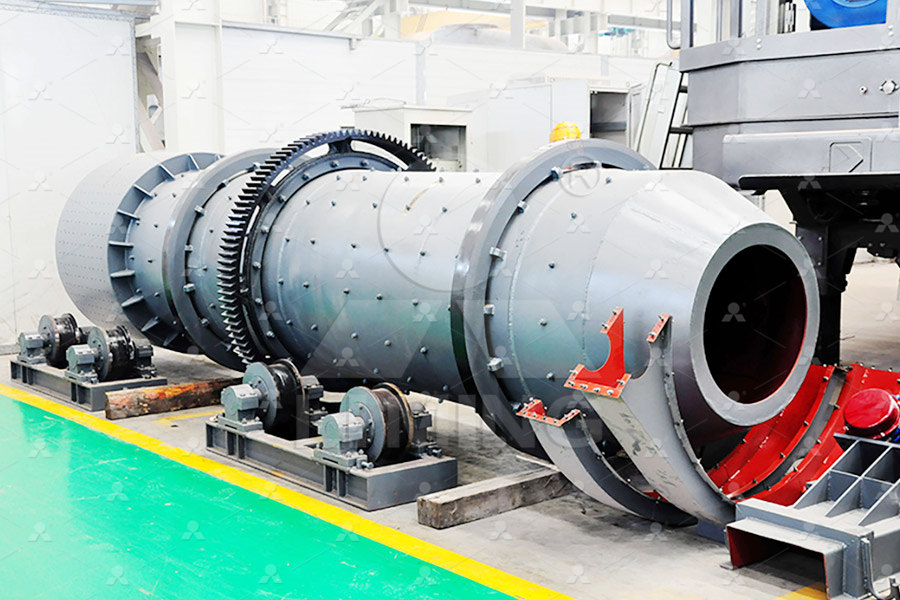
Manufacture of Cement Materials and Manufacturing Process of
Manufacture Process of Cement The manufacture procedures of Portland cement is described below Mixing of raw material; Burning; Grinding; Storage and packaging; 1 Mixing of raw material The major raw materials used in the manufacture of 2012年8月30日 Raw mix is stored in a prehomogenization pile after grinding raw mix to fine powder Cement Manufacturing Process Phase III: Preheating Raw Material After final grinding, the material is ready to face the preheating chamber Preheater chamber consists of series of vertical cyclone from where the raw material passes before facing the kilnCement Manufacturing Process Engineering IntroEVERYTHING YOU NEED TO KNOW ABOUT ESTABLISHING CEMENT GRINDING PLANT 1MTY These will include loading and unloading of raw materials and cement into trucks/tippers, my attention when you said that cement from silos is being extracted through a series of air slides to the packer plant during the process of cement packingEVERYTHING YOU NEED TO KNOW ABOUT ESTABLISHING CEMENT GRINDING PLANT In recent years, the tube mill has gradually been replaced by roller mill and other equipment, became the main equipment of cement grinding in cement cement manufacturing plant While in raw meal grinding, with the mature use of vertical mill and roller mill, the power consumption of grinding one ton raw meal has been reduced from 20 to 10 kWh Raw Material Preparation in Cement Manufacturing Plant AGICO
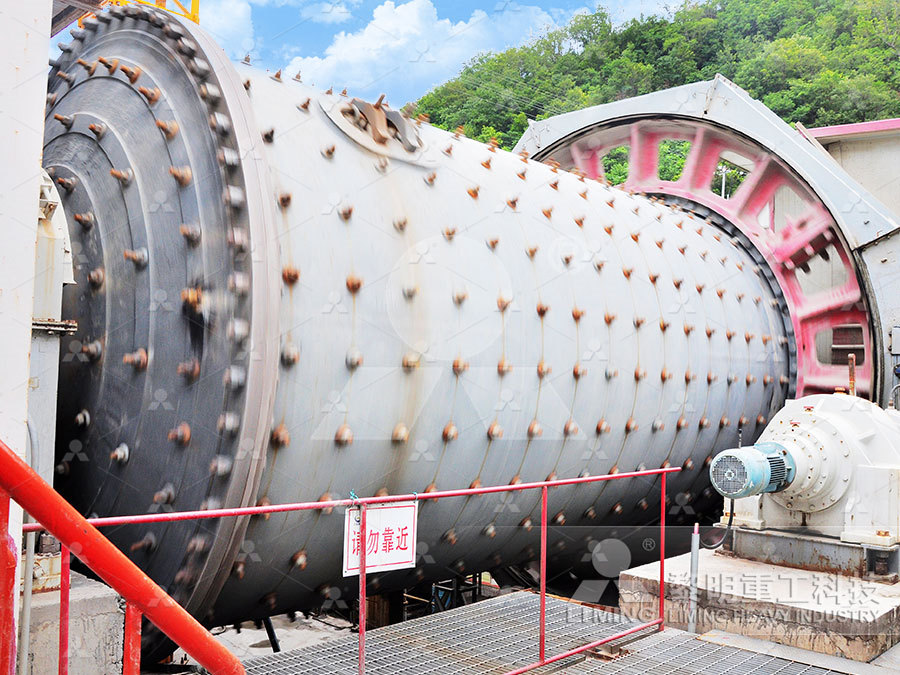
Vertical Roller Mill Operation in Cement Plant
The vertical roller mill (VRM) is a type of grinding machine for raw material processing and cement grinding in the cement manufacturing processIn recent years, the VRM cement mill has been equipped in more and more cement plants around the world because of its features like high energy efficiency, low pollutant generation, small floor area, etc The VRM cement mill has a In raw grinding, a ball mill with a high efficiency separator is used to achieve uniform particle size in raw mix for the next stages of the manufacturing process At the Cement Grinding Stage, 90 – 95% of the clinker is mixed with gypsum and ground in a Cement Ball Mill to produce quality cement OPC 43 and OPC 53Cement Grinding Unit Process High Quality Cement Grinding Plant2015年10月23日 Multicompartment ball mills and air separators have been the main process equipments in clinker grinding circuits in the last 100 years They are used in grinding of cement raw materials (raw meal) (ie limestone, clay, iron ore), cement clinker and cement additive materials (ie limestone, slag, pozzolan) and coalEnergyEfficient Technologies in Cement Grinding IntechOpen2014年6月10日 Evolution of the cement Process • Wet process easiest to control chemistry better for moist raw materials • Wet process high fuel requirements fuel needed to evaporate 30+% slurry water • Dry process Cement manufacturing process PPT Free Download
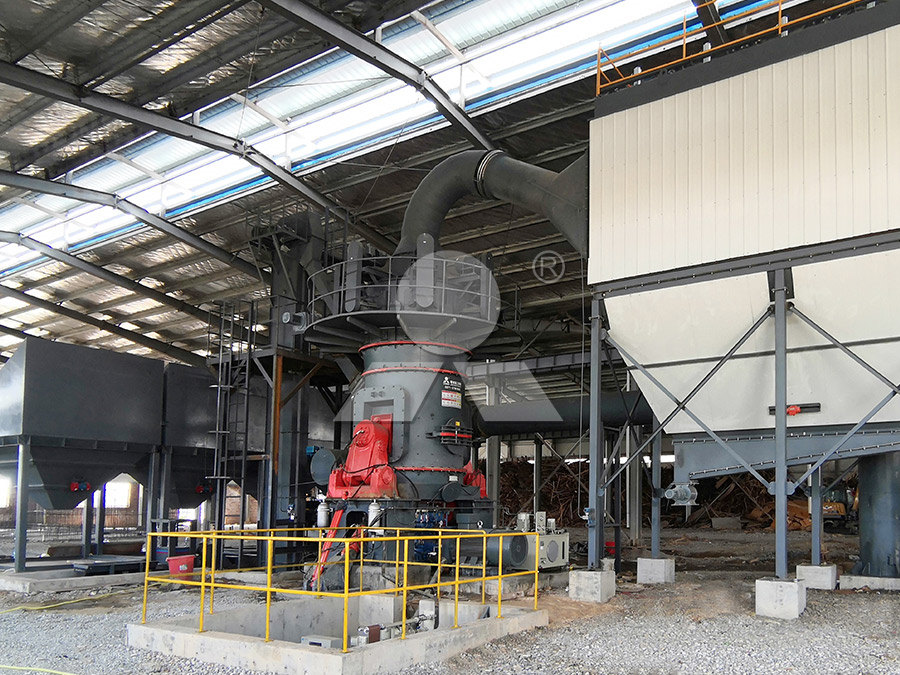
Raw mill Cement Plant
Raw mill is generally called cement raw mill, raw mill in cement plant, it refers to a common type of cement equipment in the cement plantIn the cement manufacturing process, raw mill in cement plant grind cement raw materials kiln feed preparation, pyroprocessing, and finished cement grinding Each of these process components is described briefly below The primary focus of this discussion is on pyroprocessing operations, which constitute the core of a portland cement plant The initial production step in portland cement manufacturing is raw materials acquisition116 Portland Cement Manufacturing US Environmental Today we are going to start here one very important topic ie Process technology of cement manufacturing: Raw grinding plant We will understand the various terminologies and engineering concepts used in cement technology with the help of this categoryCEMENT MANUFACTURING PROCESS: RAW GRINDING PLANT2024年9月5日 2 Raw material grinding After crushing, the raw materials are carried to a grinding mill and made into a fine powder This is done using equipment such as ball mills or vertical roller mills The grinding process ensures the correct particle size of raw material and its homogeneous constitution, which is so critical for product quality 3 A Comprehensive Guide to the Cement Manufacturing Process
.jpg)
Preparation Of Cement Raw Material Cement Mill, Cement
The cement raw materials is formed with calcareous materials, clayey materials and slight corrective material in appropriate proportion, and grinded into certain fineness The raw material production of cement plant can be classified into four steps: crushing, grinding, mixing and 2023年11月1日 The design of the raw material grinding system should focus on the energysaving, vertical mill grinding system because of its powersaving, simple process to become a large cement plant, the use of a ball mill grinding system is no more than two reasons: first, the raw material is difficult to grind, such as high quartz sandstone content, the second is the 8 Tips For Cement Plant Design Cement Manufacturing Process2023年7月10日 The cement manufacturing process involves the extraction and processing of raw materials, such as limestone, clay, and shale, which are then heated in a kiln at high temperatures to form clinkerCement Manufacturing Process and Its Environmental ImpactAGICO Cement is a cement equipment manufacturer supplies EPC projects for cement grinding station with a simple process, easy operation, low investment Get a FREE quote now! Skip to content +86 the following seven methods can effectively reduce the energy consumption of cement grinding plant 1 Improve raw materials and cement grinding Unit
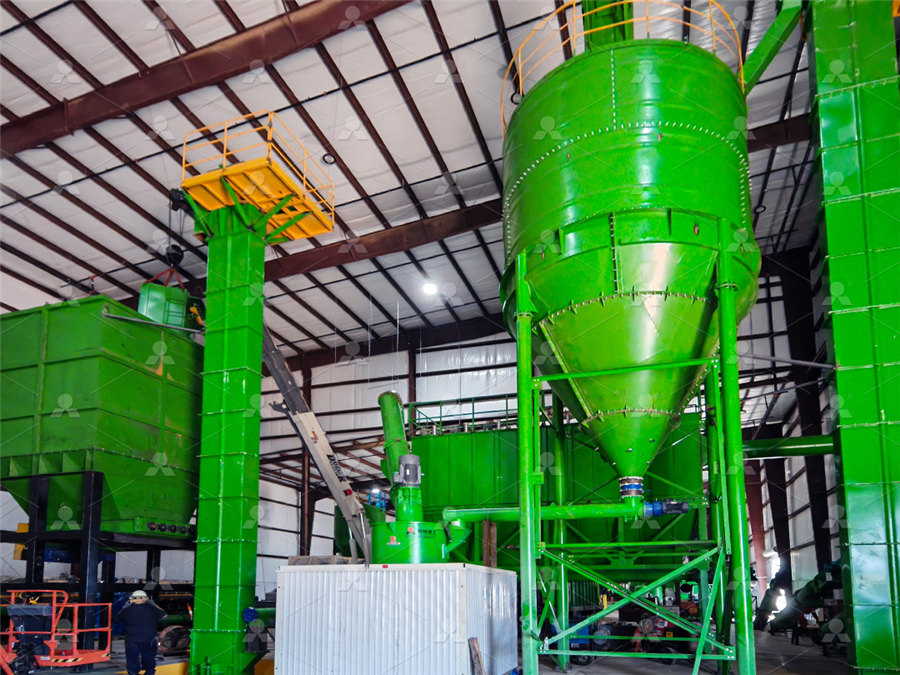
Raw Mill – Raw Mill In Cement Plant AGICO Cement Raw Mill
AGICO Cement Vertical Mill AGICO Cement Ball Mill Cement Vertical Mill Grinding System Cement vertical mill, also called roller mill, is another raw mill commonly used in cement pared with the cement ball mill, it has a great difference in structure, grinding principle, process layout, automatic control, and energy consumption, which play an important role in the Continuous high temperature process in the cement industry: Calcination and cement clinker burning Calcination of raw material CaCO 3 => CaO + CO 2 Process emissions of raw material: = 054 t CO 2 /t clinker Endotherm reaction at 950 °C ca 1700 MJ/t clinker ≈ 50% of energy Cement clinker burning at 1450 °C formation of hydraulicProcess characteristics of clinker and cement production SINTEFProportioning of raw materials Grinding Storing and Blending Burning of raw mix Clinker grinding along with gypsum These operations are controlled from Central Control Room (CCR) which is the nerve center for plant Discover the detailed steps of the cement manufacturing process in IndiaKnow All About Cement Manufacturing Process in India mycem cement2023年12月20日 Cement manufacturing is a complex process that begins with mining and then grinding raw materials that include limestone and clay, to a fine powder, called raw meal, which is then heated to a sintering temperature as The Cement Manufacturing Process Thermo Fisher
.jpg)
PROCESS TRAINING for operators of Vertical RAW Mills
For drying the wet raw material it is necessary that prior to the mill start up the grinding plant isheated for some timeOtherwise the cold grinding plant would take away too much heat from the drying process and the finish product would not be dry – handling problems in the meal transport and silo extraction would followRaw material blending is an important process affecting cement quality The aim of this process is to mix a variety of materials such as limestone, shale (clay), sandstone and iron to produce The cement raw material blending process and its control systemA mediumsized dry process roller mill A raw mill is the equipment used to grind raw materials into "rawmix" during the manufacture of cement Rawmix is then fed to a cement kiln, which transforms it into clinker, which is then ground to make cement in the cement millThe raw milling stage of the process effectively defines the chemistry (and therefore physical properties) of the Rawmill WikipediaAn intermediary storage of the raw material is necessary since the material flow has to be divided up after the primary crusher and the secondary crushers should be loaded The jaw crusher should be mentioned as alternative to the primary gyratory crusher However, its use for cement raw materials is advantageous only under very special conditionsEverything you need to know about Crushers in Cement industry
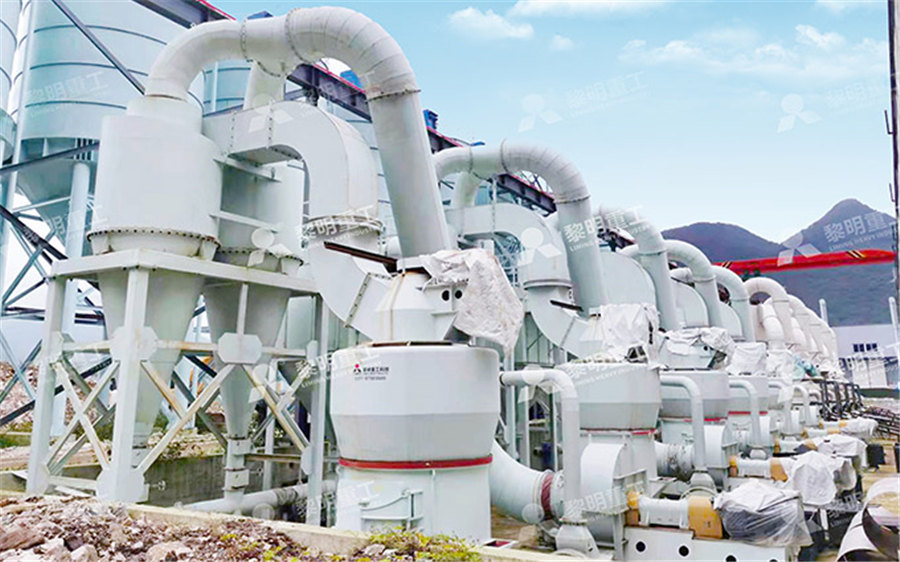
Analysis of material flow and consumption in cement production process
2015年8月1日 The results show that approximately 248t, 469t, and 341t of materials are required to produce a ton of the product in raw material preparation, clinker production, and cement grinding stages All over the world, cement is one of the most important building materials Whether for houses, bridges or tunnels, we cannot imagine our modern world without it Join us for a short tour to experience how cement is made: starting with the extraction of raw materials and ending with the finished productHow cement is made Heidelberg Materials2023年10月19日 Clinker grinders are an important part of the cement manufacturing process They are used to grind clinker into a fine powder and are typically located at the end of the cooler in a cement plant Clinker is a nodular material produced during the cement manufacturing process and is the primary raw material for making cementClinker Grinding Techniques in Cement Manufacturing JM 2024年8月20日 Step 4: Cement grinding and storageThe cooled clinker with gypsum is finely ground in a cement mill to form the hard cement The other raw materials are added during the grinding process The raw material added Understanding the Raw Materials for Manufacturing
.jpg)
EnergyEfficient Technologies in Cement Grinding
2016年10月5日 In this chapter an introduction of widely applied energyefficient grinding technologies in cement grinding and description of the operating principles of the related equip‐ ments and comparisons over each other in The production of raw cement involves the extraction and procurement of raw materials like limestone and clay or iron ore These materials are then crushed and finely ground to form the raw mix The raw mix is then subjected to high Explore Raw Material Used For Cement Production2015年1月1日 Vertical cement mill (vertical mill) is a machine that plays an important role in the raw meal production process of the newtype dry cement, and it is a set breakage, drying, grinding, transport in one []Raw material grinding process is a vital and energy consumption link in the cement productionModeling Based on the Extreme Learning Machine for Raw Cement The raw mix is fed into a circular storage unit called a raw mix storage Then, the mix is extracted transversely from the stockpile by reclaimers and conveyed to a raw mill bin called the raw mix bin for grinding The other raw materials that are used in cement manufacturing, called additives, are high purity limestone, sand and iron oreManufacturing process Lafarge
.jpg)
Everything you need to know about cement Materials Preparation and Raw
Brundick, H, “Drying and grinding of extremely moist cement raw materials in the Loesche mill,” ZKG International, No2, 1998, pages 6471Brundick, Horst, and Schäfer, HeinzUllrich, “Loesche mills for clinker grinding,” Asian Cement and Construction Discover our efficient cement manufacturing process Learn about the raw mill in cement plants and the basic raw materials used in cement manufacturing Discover our efficient cement Limestone from mines are brought to plant site and stored in the yard then fed to dump hopper of primary crusher by mixing highgrade and lowgrade Raw Mill in Cement Plant Cement Manufacturing Raw Materials1971年8月17日 116 Portland Cement Manufacturing 1161 Process Description17 Portland cement is a fine powder, gray or white in color, that consists of a mixture of hydraulic cement materials comprising primarily calcium silicates, aluminates and aluminoferrites More than 30 raw materials are known to be used in the manufacture of portland cement, and these116 Portland Cement Manufacturing US EPA2024年9月10日 Steps of Cement Manufacturing The steps involved in cement manufacturing are as follows: Quarrying: Raw materials such as limestone and clay are extracted from quarries or mines; Crushing and Grinding: The extracted raw materials are crushed and ground into a fine powder; Blending: The crushed and ground raw materials are blended in specific proportions Cement Manufacturing Process: Know Extraction, Processing
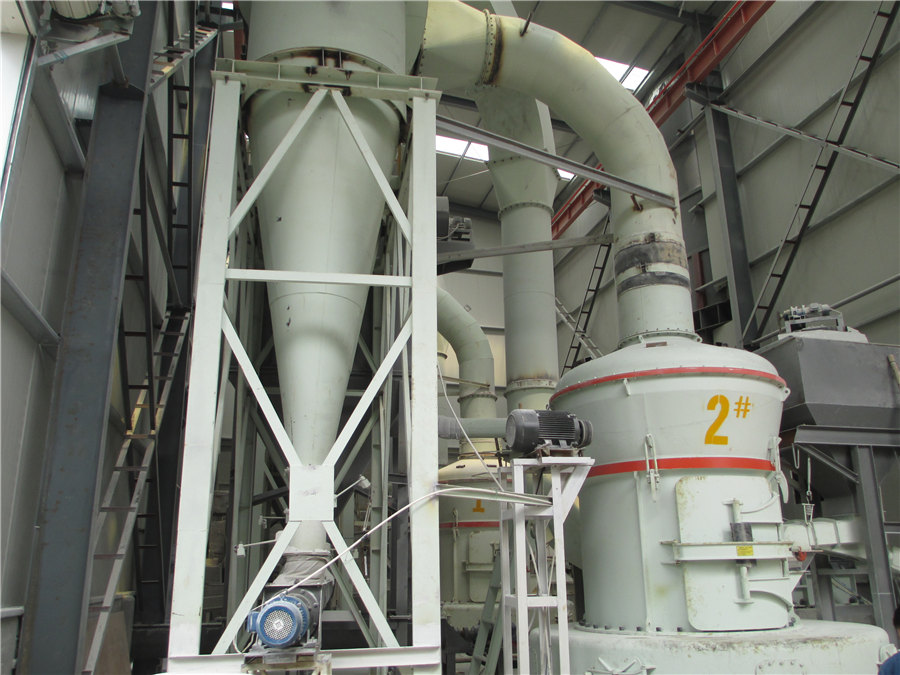
Everything you need to know about clinker/cement Grinding
The plant used 2 very similar classifying liners of the same dimensions and wear the process parameters of the grinding circuit will help to decide if a finer global net wear rate of 11 [g/kWh] (Stephane) Gross wear rate 15 g/kWh (my estimate) Wear rate is the same for raw material and cement Different for slurry grinding