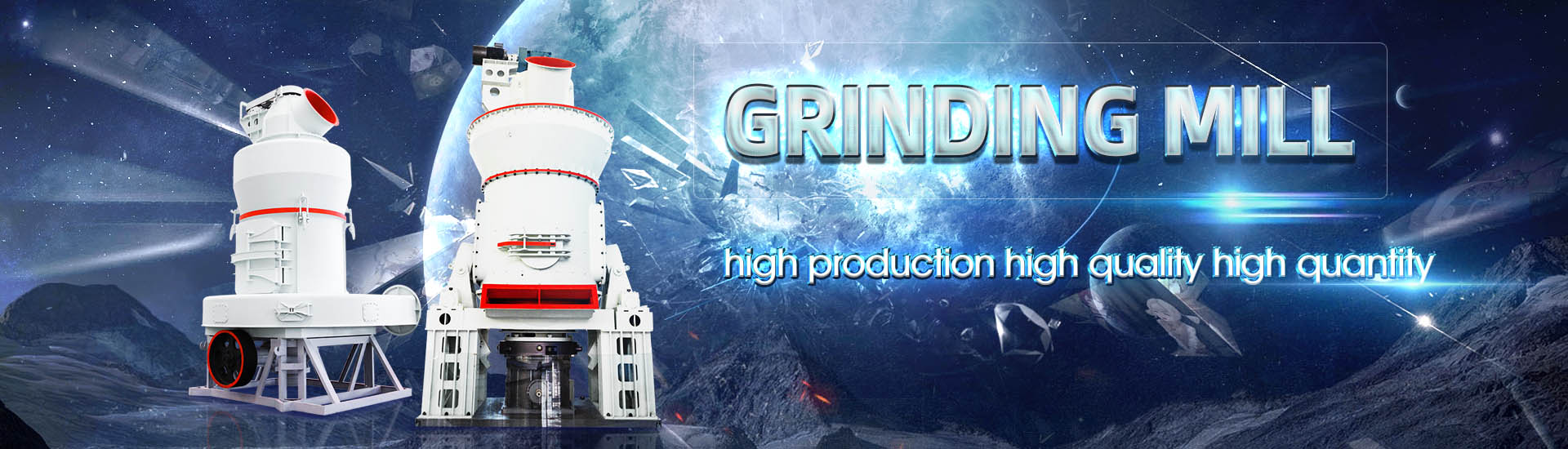
Coke coking plant (production line)
.jpg)
Coking factory Wikipedia
A coking factory or a coking plant is where coke and manufactured gas are synthesized from coal using a dry distillation process The volatile components of the pyrolyzed coal, released by heating to a temperature of between 900°C and 1,400 °C, are generally drawn off and recovered There are also coking plants 展开Using the most modern environmentallyfriendly technologies and the highest possible level of automation, the Schwelgern cokeoven plant achieves a production capacity of 264 million The new Schwelgern coke plant ThyssenKruppThyssenKrupp Industrial Solutions has been designing and building coke oven plants for more than 130 years, making it the longest established coke plant engineering company in the worldCoke Plant Technologies ThyssenKruppEngineering, delivery, installation and commissioning of a pushing emissions control system including optimised sequence planning to avoid lengthy plant stoppage times Construction of a new coke oven battery; basic engineering, Coke plant technologies thyssenkrupp Uhde
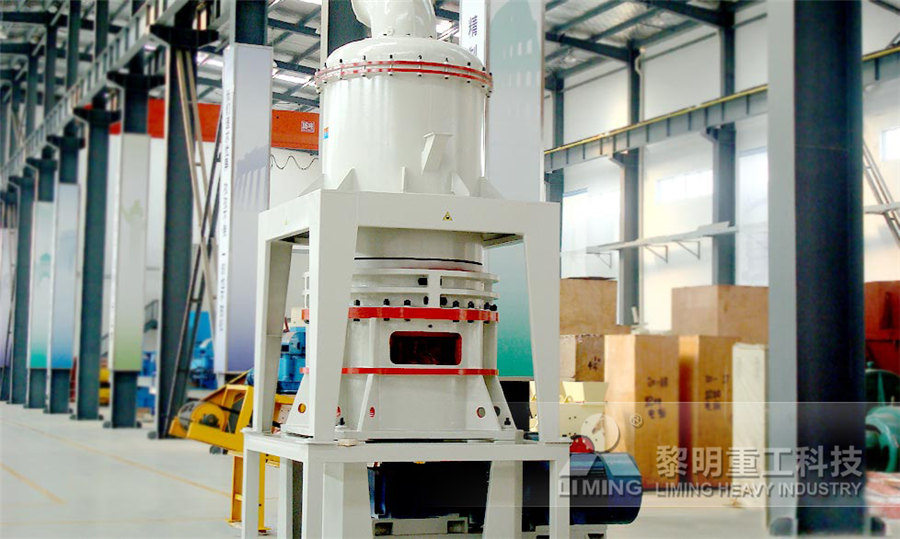
TKISAIST2015PaperUsing modern coke oven technology
Under normal production with 283 hours gross coking time and an average heating flue temperature of 1245 degC, the Coke Oven Plant (abbrev: COP) of Phase 1 and Phase 2 are Coking plant Coke’s role in steelmaking is to provide the heat needed to melt the ore, whose natural state is iron oxide, the rust you see on iron after it has been exposed to the Coking plant ArcelorMittal2019年1月1日 Metallurgical coke is produced in coke ovens and is mainly used for the iron ore reduction in blast furnaces (BFs) It is also consumed in blast and electric furnaces for ferroalloy production and for the reduction of other metal Coke in the iron and steel industry ScienceDirect2019年7月19日 In COG route, methanol production stage presents the highest contribution, while coke production stage is responsible for less than 10% due to mass allocation among Coke Making: Most Efficient Technologies for Greenhouse
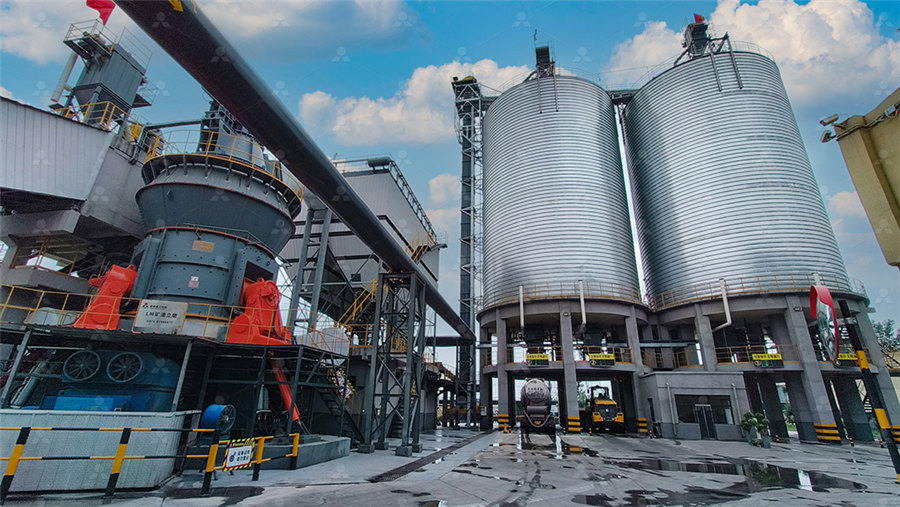
How is Coke Oven Gas produced? IFRF
2003年9月8日 In the present combustion file the production processes of COG are described A coke plant consists of a coal supply system, one or more coke batteries, a coke quenching system and a coke oven byproduct plant These 122 Coke Production 1221 General Metallurgical coke is produced by destructive distillation of coal in coke ovens Prepared coal and 1224 give sizespecific emission factors for coking operations A few domestic plants preheat the coal to about 260°C (500°F) before charging, using a 122 Coke ProductionThe bulk of the worldwide coke production in 2011 was effected in conventional coking plants including a recovery of gas and coal chemicals These plants are very often called byproduct coking plants, too Approx 5 % of the total coke production originate from the nonrecovery technology, which does not recover gas and coal chemicalsEnvironmental Control and Emission Reduction for Coking Plants 2024年11月1日 On July 22, 2024, ArcelorMittal Poland (AMP) announced the permanent closure of its remaining coke battery at the Krakow plant This decision follows an anticipated rebound in steel demand that did not materialize The coke battery was idled last November due to weak demand and a narrowed price differential between coke and coking coalArcelorMittal Poland Permanently Closes Krakow Coke Production
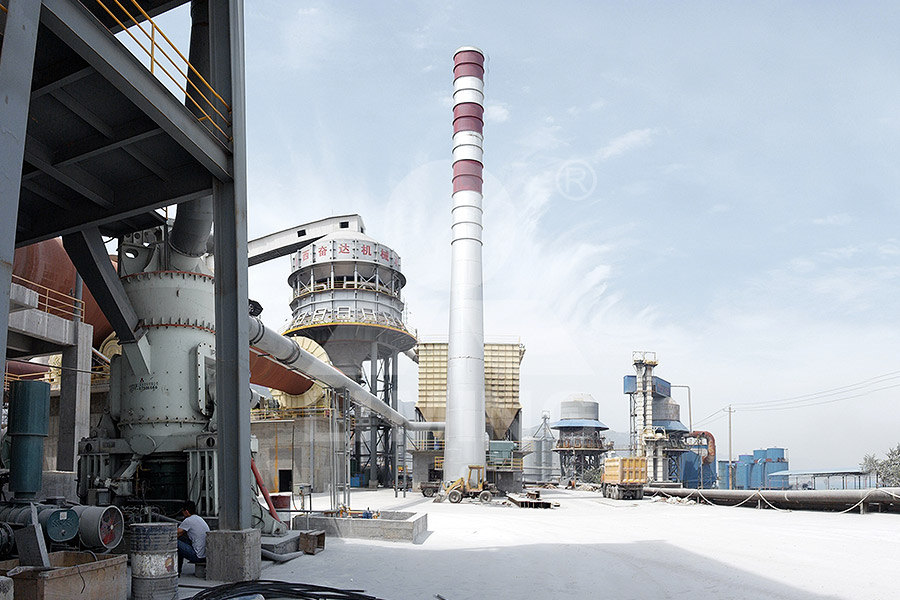
Coke production in Ukraine fell by 59% in 2022 Dnipropetrovsk
2023年2月21日 The hostilities led to the shutdown of the largest coking plant located in the city of Avdiivka, next to the front line In 2022, Ukrainian Coke Plants reduced the production of 6% moisture gross coke by 59% compared to the previous year – to 391 million tons In 2022, the output of gross coke decr2017年12月15日 As the penetration of CDQ technology in China is 36% in 2014 [2], the coke production process mainly uses CWQ technology and is characterized by significant heat waste due to the flue gas and the quenched water used for cooling the incandescent coke and raw COGAbout 37–48% of thermal energy is lost from the incandescent coke at temperature of Modeling, thermodynamic and technoeconomic analysis of coke production 2021年3月6日 11 Introduction to Coke Plant, TATA STEEL LTD Tata steel Jamshedpur (Fig 2) has three stamp charge coke plants and operates as Battery#10, 11, Battery#8, 9 and Battery#5, 6, 7 to cater to the coke requirement of 5 blast furnaces of Tata steelCoke Plant Battery#10, 11 accounts for an annual production of 14 MTPA and has 88 ovens in each battery []Prediction of coke CSR using time series model in Coke PlantConsidering the coke plant operator’s objective to achieve reductions in OPEX, the increasing coal blend price and the ever lower quality of coking coal, stamp charging technology offers substantial benefits for cost effective coke production Paul Wurth’s coke oven batteries of COKEMAKING TECHNOLOGY Paul Wurth
.jpg)
The scheme of coke production at a coke oven plant
Although the time for operating mines and coking plants in many They are generated in extreme quantities such as 120–150 m³/h in a plant with annual coke production of 42 Mt Both the production of metallurgical coke as well as the purification of gas, is executed completely automated The metallurgical coke is utilised as fuel in our blast furnace It furthermore plays an important part in the chemical processes taking place in the blast furnaceCoking plant ArcelorMittal in Belgium2013年11月1日 Coke is a very strong macroporous carbonaceous material produced by the carbonization of a specific coal grade or of different coal blends at temperatures ⩾1400 K Approximately 90% of coke produced from blends of coking coals is used to maintain the iron production process in a blast furnace (BF) [9]Coke oven gas: Availability, properties, purification, and utilization 2016年6月22日 When coke is consumed it generates intense heat but little smoke, making it ideal for smelting iron and steel Prior to the 1880’s, steel was produced using charcoal By 1920, nearly 90% of US steel was produced How does coke and coal play into steel making?
.jpg)
Coke in the iron and steel industry ScienceDirect
2019年1月1日 Download: Download fullsize image Figure 132 Flow sheet of an integrated steel plant: 1, area of raw material delivery and handling; 2, sinter plant (agglomeration of fine iron ore); 3, coking plant (coke making from coal); A coking plant is a production line to manufacturer coke and the raw material is coal In a coking plant, belt conveyors play a crucial role in the handling and transportation of various materials associated with the coke production process Coking plants are Coal Handling Conveyor In Coking Plant SKE Industries2002年3月1日 However, these mechanisms are often reactorrelated and contradictory to each other since laboratory scale reactors do not simulate the practical cracking operation in ethylene plants Therefore, analyzing coke deposits produced in such reactors may not necessarily give results similar to those of coke produced in industrial plantsCoke formation in steam crackers for ethylene productionCapacity: 2,600,000 t/year of coke, 155,000 Nm3/h of coke oven gas, 2 batteries, 70 ovens each, chamber height 84 m World‘s largest coke oven batteries; TWINFLUE, Compound, Gun flue, PROven, ControlpressCoke plant technologies thyssenkrupp Uhde
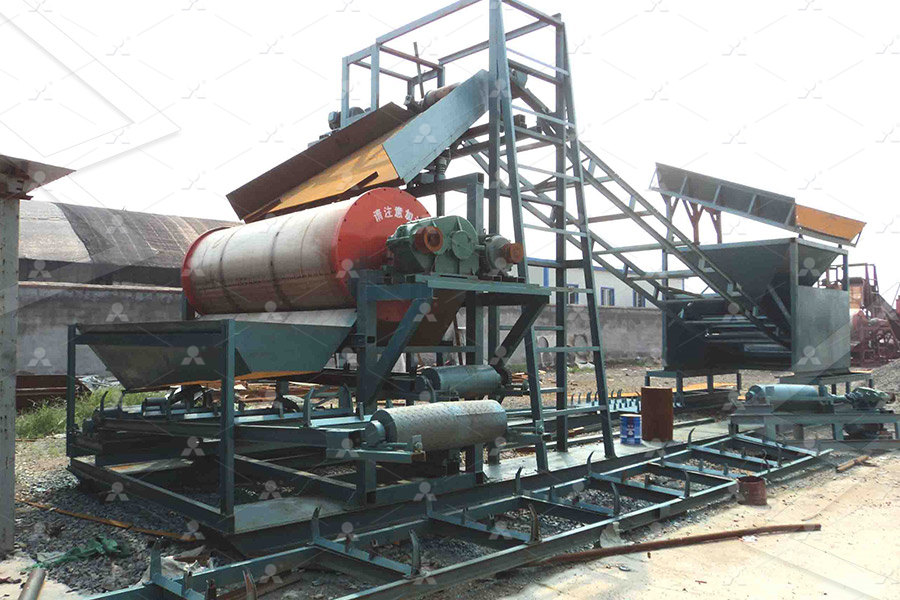
coking plant French translation – Linguee
Many translated example sentences containing "coking plant" – FrenchEnglish dictionary and search between 1 240 °C and 1 250 °C in order to obtain coke, which is needed for the production of pig iron eurlexropa eurlexropa D the refrigeration of coking gas: these lines were completely renovated in 1991 eurlex 2019年11月14日 Coking is a complex process It features a large time constant, strong nonlinearities, and timevarying characteristics To achieve good control performance, it is important to obtain a precise COT in a realtime fashion; but this is difficult owing to restrictions imposed by the structure of a cokeoven and operating costsIntelligent Optimization and Control of Coking Process2022年8月5日 Petroleum coke is one of the coking products that is divided into three types: shot coke, sponge coke and needle coke, depending on the feed properties and operating conditions of the process Needle coke is used as a valuable product in the production of graphite electrodes used in electric arc furnace (EAF) for melting scrap metal and producing steelCoking IntechOpenThe plant’s coke oven batteries will be located on a southwest to northeast line within approximately 100 feet of the eastern property line of the Project Site Coke oven waste gases generated by the coking process are routed to refractory lined tunnels for complete combustion and generation of excess waste heatNonRecovery Coking FDS Coke Plant
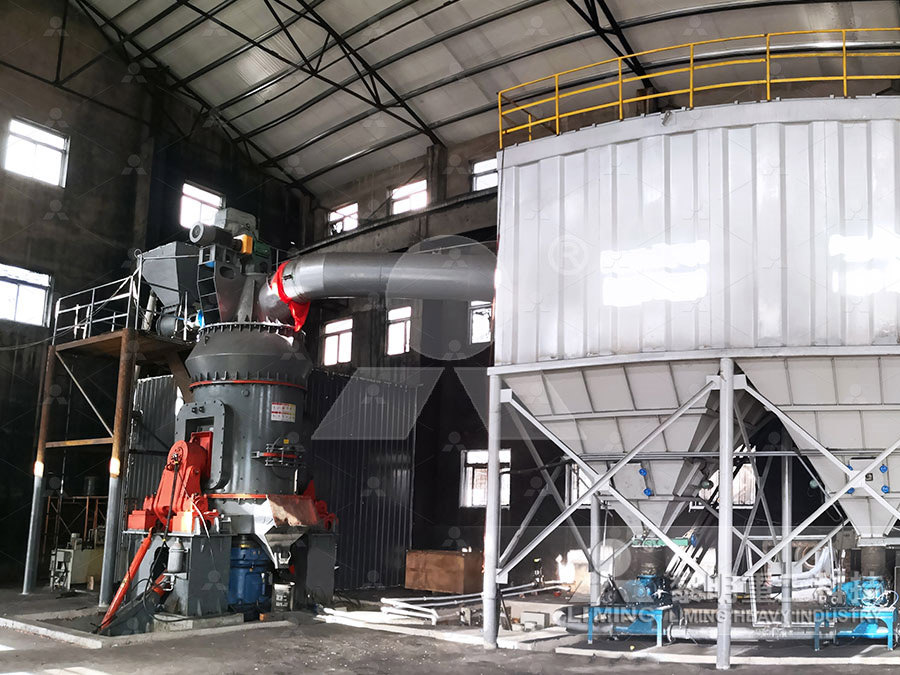
Production of Hydrogen from Coke Oven Gas in JSW Group
taking place in coking plants, related to coke oven battery firing, operation of existing power units, gas compression systems and taking into account the securing of external consumers' needs for 2020年3月17日 The Fifth Russian Coking Conference was held in Moscow on October 10–11, 2019 In all, 80 specialists and executives from 33 organizations in ten countries attended, with expertise in coal delivery, coke production, cokeplant equipment, refractories, and cokeplant design, as well as engineering and consulting servicesFifth Russian Coking Conference: A Report Coke and ChemistryAs coal and coke production grew steadily at Walston, the officers of the RPCI formulated plans for the opening of another mew mining and coking plant in Young Township, two miles from Punxsutawney The mines at the site appropriately named, "Adrian" in honor of chief investor Adrian Iselin, made its first shipment in January, 1887History of Coke IUP122 Coke Production 1221 General Metallurgical coke is produced by destructive distillation of coal in coke ovens Prepared coal and 1224 give sizespecific emission factors for coking operations A few domestic plants preheat the coal to about 260°C (500°F) before charging, using a 122 Coke Production
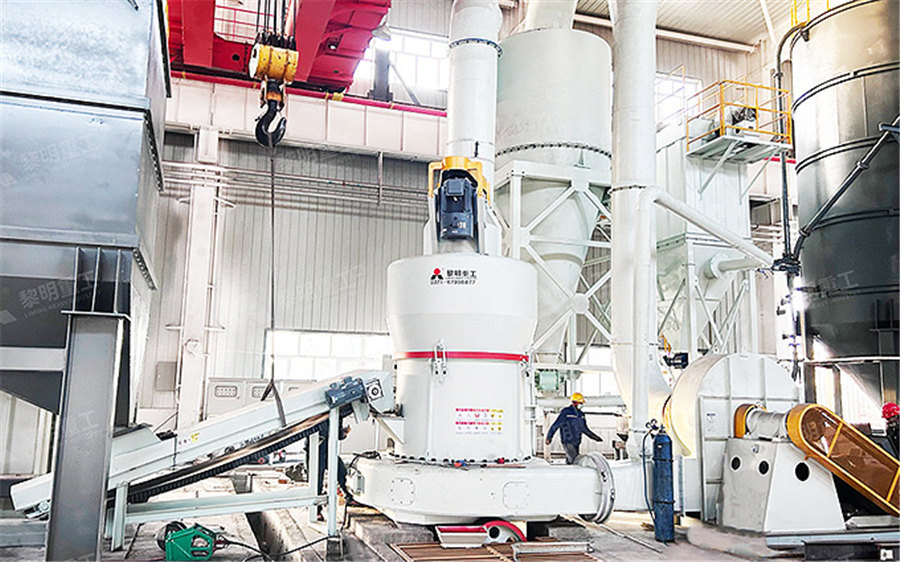
Biological treatment of coke plant effluents: from a microbiological
2020年8月20日 During coke production, large volume of effluent is generated, which has a very complex chemical composition and contains several toxic and carcinogenic substances, mainly aromatic compounds, cyanide, thiocyanate and ammonium The composition of these highstrength effluents is very diverse and depends on the quality of coals used and the operating The first coking battery started production in July, 2023, and we will have 4 coking batteries of 32 million mt in production by the first quarter of 2024 start of professional career with coke plant technology company Thyssen Still Otto (which in 1999 became Thyssen Krupp EnCoke and in 2004 was integrated in the company thyssenkrupp Uhde)EUROCOKE Where the global coke, coal, and steel industry 2020年12月7日 criteria adopted by other coking plants is presented below in table4,5 6 Table 4: Production and use of high CSR coke at Inland Steel" ISS 1990 5972; H S Valia; D D Kaegi;BLENDING CONSIDERATION IN COKE MAKING TOWARDS OPTIMUM COKE QUALITYFor outsiders the Hansa coking plant was a forbidden city for more than 60 years Its roads and bridges were permeated with the smell of tar, its buildings and towers covered with layers of coal dust, day and night Every ten minutes the endless batteries of coking ovens had to be emptied and refilled with coalHansa Coking Plant ERIH
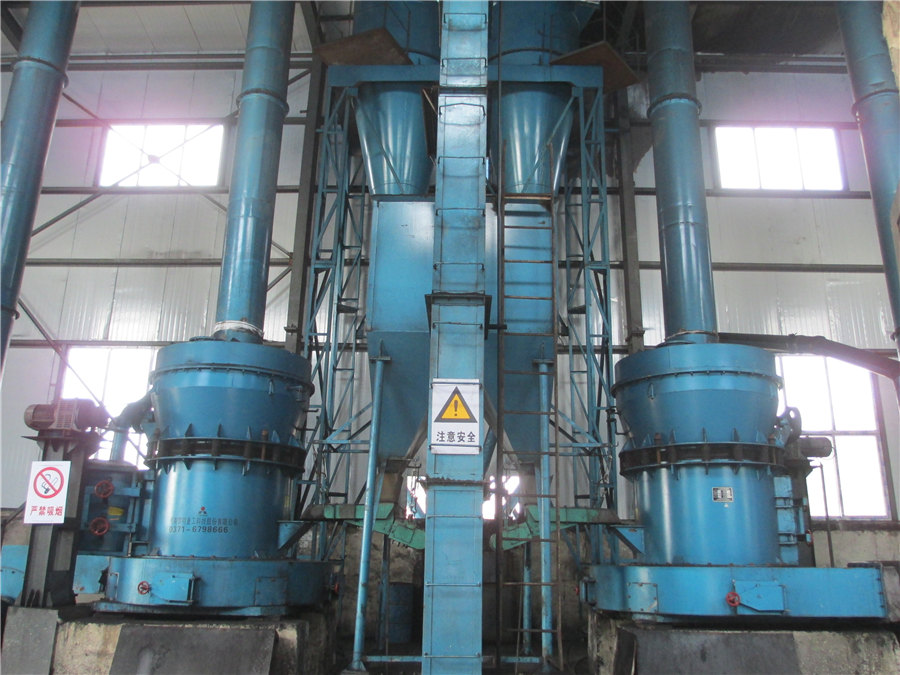
Formulating Coal Batch for Coking: A Review Coke and Chemistry
2021年7月2日 In turn, coke quality is largely determined by the coal employed in the coking batch [2–5]The properties of the coal employed in coking determine 70% of the value of CSR for the coke produced and 80% of the CRI value, according to data in [3, 5]Although deficiencies in the coal may be somewhat compensated by adjusting the coking conditions—such as the The large amount gas generated due to the vapourization of VM in the coal during the production of coke in the byproduct coke oven battery is treated in an adjacent byproduct plant During the cycle of coking, (iii) remove ammonia (NH3) to prevent gas line corrosion, (iv) remove benzol oil for recovery and sale of benzene, toluene and Coke Oven Gas Generation and Usage IspatGuru2019年5月21日 The coking industry is an important VOCs emission source in China Due to the complex production process, the VOCs emission characterization is lack, so a typical mechanized coking plant was selected to study Samples were collected from coke oven chimney, coke pushing, coal charging and coke oven top GC/MS was used to analyze the samples, and Characteristic Analysis of VOCs Emitted from a Typical Coking Plant2012年7月15日 settler , production facility of ammonium sulfate and crude benzol and asphalt conveyor belt of this coking plant are se verely polluted . The contents of detected total cyanide , TP Hs and (PDF) Vertical distribution of typical contaminants
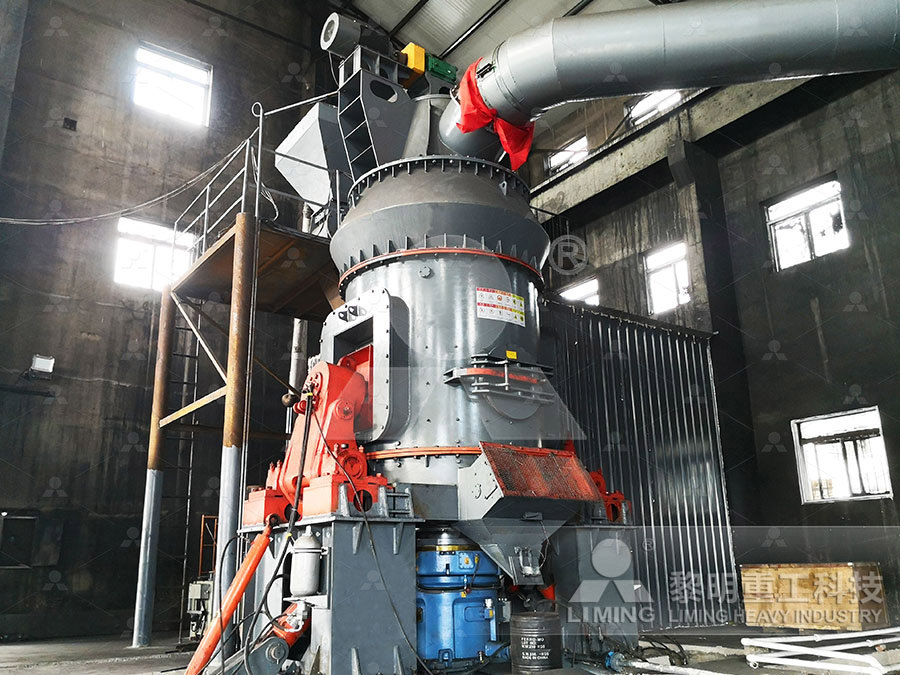
Stateoftheart of Coke Formation during Steam Cracking: AntiCoking
2018年10月24日 Although steam cracking is a mature technology, mitigation of coke formation remains one of the main challenges in the petrochemical industry To increase the olefin output of existing plants, coil materials that can withstand higher temperatures are desired This work reviews material technologies that were developed and tested in the past three decades to To make steel in a blast furnace, coal must first be turned into coke Coke has a dual role in the steelmaking process First, it provides the heat needed to melt the ore, and second, when it is burnt, it has the effect of ‘stealing’ the oxygen from the iron ore, leaving only the pure iron behind In the coking plant, coal is heated in the absence of oxygen to 1250cRaw materials Coking plant ArcelorMittal2023年7月15日 Coking chemistry is the subject of relative theories, technologies, processes, and equipment of process where main material coal in the condition of isolating air is researched, and coal is transformed into coke (or semicoke) and raw gas after physicochemical action like thermolysis and coking, and the raw gas is purified and separated to obtain coal tar and Coking Chemistry SpringerLinkA coking plant is used to produce coke (coking coal) from metallurgical coal Coking plants consist of coke ovens (aka coking ovens, coke furnaces, coking furnaces) Coal is used to reduced iron ore to produce pig iron (aka hot metal) in the blast furnace (BF)However, it cannot be burned directly in the furnace because it contains numerous harmful byproducts that gets generatedCoking plant Global Energy Monitor
.jpg)
A Life Cycle Analysis of Deploying Coking Technology to Utilize
2020年6月15日 At present, the excess capacity in China’s coke industry can be deployed to utilize some lowrank coal, replacing coking coal with potential economic gains, energy efficiency, and environmental benefits This study presents a life cycle analysis to model these potential benefits by comparing a metallurgical coke technical pathway with technical pathways of %PDF16 %âãÏÓ 133 0 obj > endobj xref 133 96 00000 n 00000 n 00000 n 00000 n 00000 n 00000 n 00000 n 00000 n 00000 n 00000 n 00000 n 00000 n 00000 n 00000 n 122 Coke Production US Environmental Protection Agency2019年1月26日 Recovery of Ammonia during Production of Coke from Coking Coal Ammonia (NH3) is a byproduct produced during the production of coke from coking coal in the byproduct coke ovens It is a constituent of the coke oven gas (COG) leaving the coke ovens, with a typical concentration in raw COG of 6 grams per normal cubic meters (g/N cum)Recovery of Ammonia during Production of Coke from Coking 2019年7月3日 It integrates fluid coking and air gasification to eliminate petroleum coke production Instead of withdrawing unburned coke as in fluid coking, coke is gasified at 1500–1800 °F in an integrated steam/air gasifier to produce Coking and Visbreaking SpringerLink