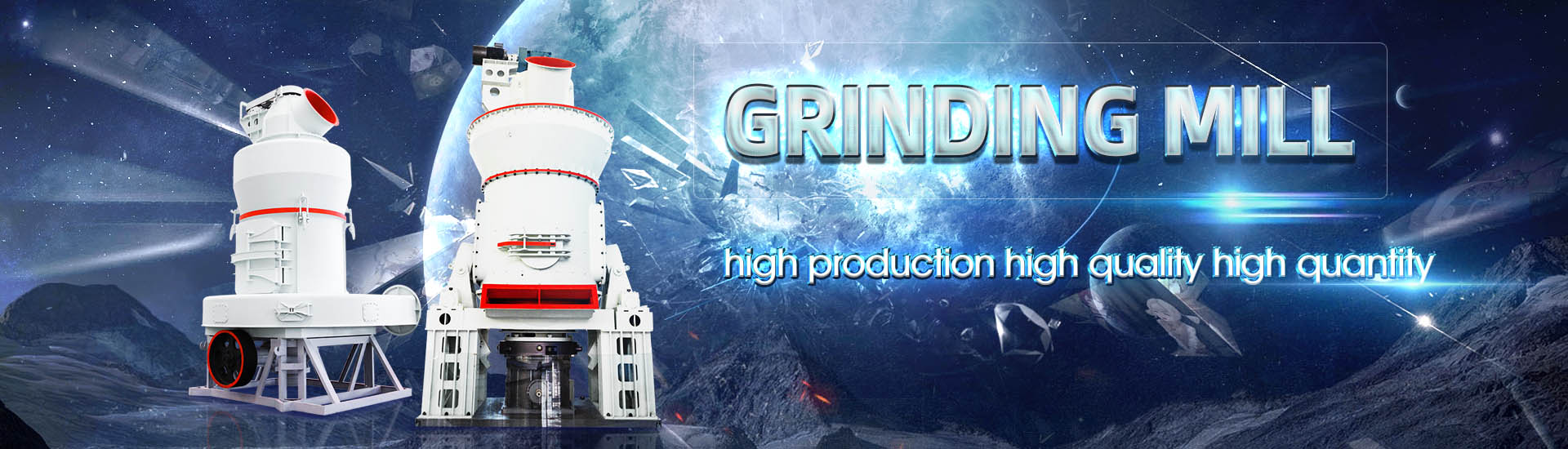
Manganese ore powder making process
.jpg)
Sintering process of manganese ore powder Google Patents
The invention discloses a sintering process of manganese ore powder The process comprises the following steps of: adding water to mix manganese ore powder, a binding agent, fuel, a2024年11月15日 The process diagram in Figure 1 shows a generic flow sheet with the conventional steps needed to produce a manganese sulfate solution suitable for final refining Almost all refined manganese processing, including HPMSM Processing 101 Canadian ManganeseThe innovative hydrometallurgical processing technique for industrial zinc and manganese process residues generally conventional roastreduction is adopted for the manufacture of electrolytic manganese dioxide (EMD)/ chemical Hydrometallurgical Processing of Manganese Ores: A 2024年2月26日 In this paper, the process mineralogy of Chongqing Chengkou lowgrade manganese ore will be studied in order to determine the mineral types and beneficiation methods of Chongqing Chengkou manganese ore In Comprehensive Study on Mineral Processing Methods
.jpg)
Hydrometallurgical Processing of Manganese Ores: A
2011年1月1日 A detailed review of the various steps involved in the hydrometallurgical processing of manganese, concentration and purification processes and newer processes of extraction of manganese2019年7月15日 Manganese ore smelting is reviewed in terms of processing parameters such as feed material particle sizes, energy input methods, heat transfer modes, smelting mechanisms, experimentalA Review of Ore Smelting in High Carbon 2022年2月23日 Manganese carbonate and oxide ores are two primary resources for extracting Mn Manganese carbonate ore is valuable because Mn(II) is soluble in acid solutions, making the extraction process extremely Novel Process of Reduction Roasting Manganese Ore 2020年8月21日 As South Africa accounts for 74% of the world’s identified manganese resources and 32% of the world’s reserves,4 the paper presented here describes in more detail the From Ore Body to High Temperature Processing of Complex Ores:
.jpg)
Ferromanganese Production Process: From Ore to Alloy
2023年12月5日 Globally sourced manganese ore serves as the primary manganese source, while iron ore provides the essential iron component Moreover, carbonaceous materials play a vital role as reducing agents, aiding Manganese ore powder agglomeration method mainly comprises the group of pressure, sintering and three kinds of techniques of pelletizingAt present, sintering process is adopted in the manganese ore agglomeration more in the worldIn these several main methods, the group's of pressure method technique is simple, production cost low and environment is good, but Sintering process of manganese ore powder Google Patents2022年2月23日 Manganese carbonate and oxide ores are two primary resources for extracting Mn Manganese carbonate ore is valuable because Mn(II) is soluble in acid solutions, making the extraction process extremely Novel Process of Reduction Roasting Manganese Ore 2016年4月27日 The problem involved in Manganese Ore Processing deals with the production of acceptable specification grades of manganese concentrates at a maximum recovery of the total manganese from ores having variable characteristics The flowsheet provides for both gravity and flotation with a maximum recovery of the manganese values in a coarse size in the most Manganese Ore Processing 911Metallurgist
.jpg)
(PDF) Novel Process of Reduction Roasting Manganese Ore with
2022年2月23日 Novel Process of Reduction Roasting Manganese Ore with Sulfur W aste and Extraction of Mn by Acid Leaching Yongjie Liu 1 , Fupeng He 1 , Donglai Ma 1 , Qingqing Hu 1 and Zhixiong Y ou 1,2 , *2019年7月15日 Manganese ore smelting is reviewed in terms of processing parameters such as feed material particle sizes, energy input methods, heat transfer modes, smelting mechanisms, experimental findings on A Review of Ore Smelting in High Carbon Ferromanganese Production2023年4月23日 Manganese is a chemical element with the symbol Mn and atomic number 25 It is a hard, brittle, silverygray metal that is commonly found in the Earth's crust Manganese is an essential trace element that plays a crucial role in many biological processes, including metabolism, bone formation, and antioxidant function It is also used in various industrial Manganese (Mn) Ore Minerals, Occurrence, Deposits Geology Manganese carbonate and oxide ores are two primary resources for extracting Mn Manganese carbonate ore is valuable because Mn(II) is soluble in acid solutions, making the extraction process extremely simple However, globally, its availability is limited Manganese oxide ores are extensively employed for manganese production [4–6]Novel Process of Reduction Roasting Manganese Ore with Sulfur
.jpg)
A Review of Low Grade Manganese Ore Upgradation Processes
2019年7月29日 The process of extraction of manganese from ferruginous manganese ore using reduction roasting and magnetic separation, beneficiation technology of poorgrade manganese ore to improve the ratio of Ferrous Metallurgical Process Industry Santanu Chakraborty, in Treatise on Process Metallurgy: Industrial Processes, 2014 537 Manganese Ore Manganese ore is required in iron making to control the manganese content of the hot metal in the desired range Unlike other plants, where manganese ore lump is used directly in blast furnace, in VSP, it was proposed to use Manganese Ore an overview ScienceDirect Topics2014年5月7日 Chemical studies of manganese during the 16th through 19th centuries led to the realization that the addition of manganese to iron orebased steel made it even harder In today’s world, manganese is often used for Manganese Mining and Processing: Everything you 43 Reduction of Manganese Ore Powder estimated based on a common ore and assumed process yields of 95% (HC FeMn), 75% (MC minus the ore cost 13 Figure 24: Global annual production of manganese alloys for steel making for 2013 Production is normalized based on contained Reduction of Manganese Ore by Methane University of Toronto
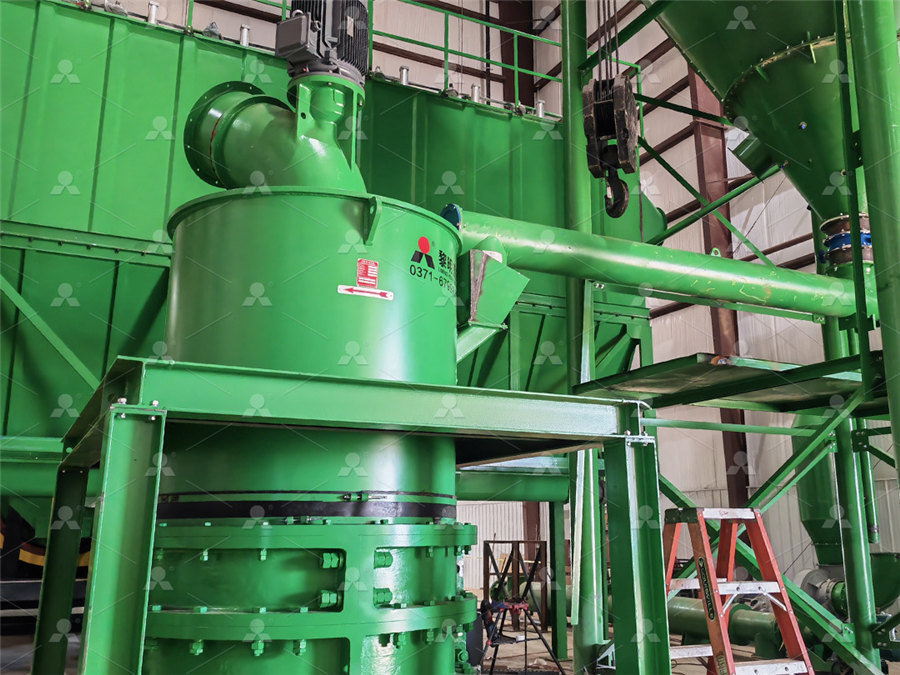
A Process for Extraction of Manganese from Manganese Oxide Ores
2023年5月30日 Manganese ores are commonly used as a raw material in many fields, such as the steel and iron industry, food additive industry, agriculture, and preparation of cells and fine chemicals 1,2 Among them, the steel and iron industry is the biggest consumer of manganese ores, and manganese for steel production comprises 80% of total manganese production 3,4 in manganese ore on the melting behavior of the ore were also investigated 2 Experimental Procedure 21 Manganese Ore Table 1 shows the compositions of the manganese ores used in this study A is a raw manganese ore, B is a sintered manganese ore and C is a heattreated sintered manganese ore The oxygen contents of ores A, B and C are 348%,Fundamental Investigation of High Temperature Reduction and 2017年3月22日 Manganese should be high Wire feeder: This process is comparable with powder injection Most likely the biggest changes will involve the ironmaking process (coke making, ore agglomeration and BF), since it is the largest producer of CO and CO 2 Sulphur removal in ironmaking and oxygen steelmaking2020年12月1日 Making a fine powder for the insitu XRD analysis may increase the interfacial contacts between the ore components compared with the case of calcining the large particles Optimizing manganese ore sinter plants: process parameters and design implications INFACON X, 1 (2004), pp 281290Characterization and calcination behavior of a lowgrade manganese ore
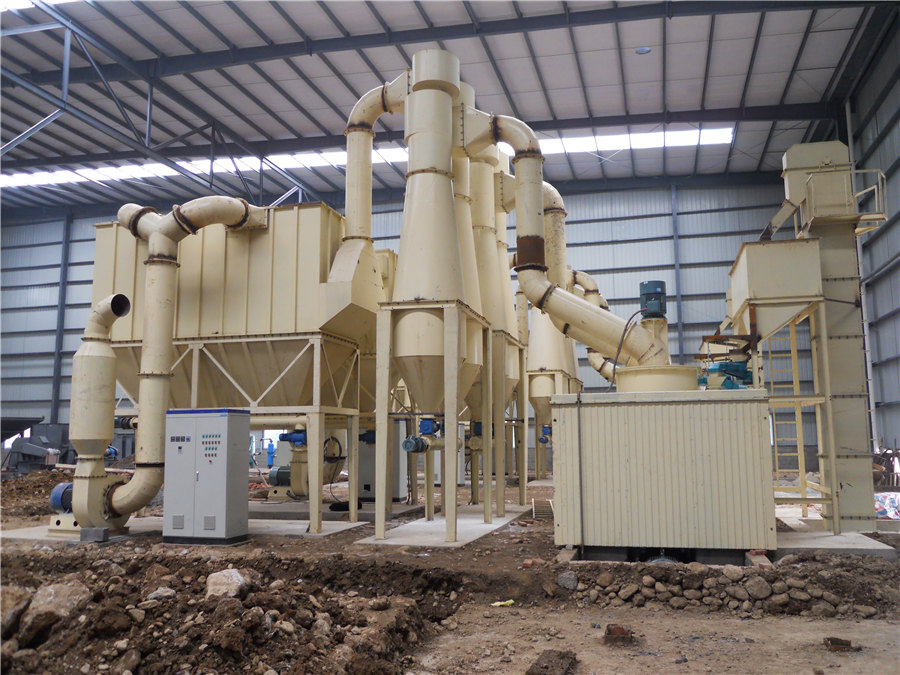
Assessing the environmental footprints of the manganese
2023年3月8日 Increasing demand for manganese and rapid depletion of highgrade manganese ores grow attention to other resources However, environmental impacts and technoeconomic issues are the main challenges regarding manganese extraction from lowgrade ores This study investigated the environmental impacts of manganese recovery from lowgrade ores and the ture of manganese ore powder,wder and anthracite powder using a cored wire macTt mass of the mixed powder in the finished manganese ore cored wire is 12/Tanese ore cored wire is composed of manganese or,hrAter dr,ushed and gr,he three types of raw materials are pressed to spheres or fabricated to cored wires by high pressurTReaction kinetics during direct alloying of manganese ore cored Manganese (Mn) is the twelfth most abundant element in the Earth’s crust Amongst some 300 minerals containing manganese, only about a dozen are of economic significance Manganese is a silverygray metal that resembles ironIt is hard and very brittle, difficult to Manganese Ore Process Plant JXSC Mineral2024年11月15日 Ore is leached, and impurities are removed to produce a purified manganese sulfate solution using a process like that shown in Figure 1 Purified manganese sulfate solution serves as the electrolyte to produce standardgrade electrolytic manganese (EMM) or electrochemical manganese dioxide (EMD)HPMSM Processing 101 Canadian Manganese
.jpg)
Equipment Required To Build A Manganese Ore
2024年11月21日 Manganese ore processing plants typically include crushers, ball mills, where the manganese ore is refined into a fine powder using specialized equipment such as ball mills or vertical roller mills To achieve this, Iron processing, use of a smelting process to turn the ore into a form from which products can be fashioned Included in this article also is a discussion of the mining of iron and of its preparation for smelting Iron (Fe) is a relatively dense Iron processing Definition, History, Steps, Uses,2024年1月10日 Chromite ore processing tailings and lowgrade manganese ores are typically considered waste due to their limited or negligible utility, leading to environmental and storage concerns Researchers globally have explored various methods to utilize or upgrade these wastes, particularly because dumping chromite ore has been linked to severe health issues Valorization From Waste: Combined Reduction of Chromite Ore2017年2月16日 PDF Sintering is a thermal agglomeration process that is applied to a mixture of iron ore fines, recycled ironmaking products, fluxes, slagforming Find, read and cite all the research you (PDF) Iron Ore Sintering: Process ResearchGate
.jpg)
Gaseous Reduction of Manganese Ores: A Review and Theoretical Insight
2019年8月8日 Gaseous reduction of manganese ores has been studied as it is beneficial for both understanding the common ferromanganese production process and the development of new processes2019年8月1日 Abstract In this study, the use of XRF, XRD and other instruments found that the manganese content in the ore was 1453%, and the main forms were carbonate, iron manganese oxide and manganese oxide Because of the special magnetic susceptibility of these minerals, the magnetic separation method was chosen to improve the grade of manganese ore, and the Insight into Mineralogy of a LowGrade Manganese Ore for2024年11月21日 Manganese carbonate ore is a mixed primary manganese ore with high manganese, high sulfur, high silver, high lead and high zinc, and has a high comprehensive recovery value Manganese carbonate is an inorganic compound with the chemical formula MnCO3, which exists in nature in the form of rhodochrositeWhat Processes For Beneficiation Of Manganese Carbonate OreManganese carbonate and oxide ores are two primary resources for extracting Mn Manganese carbonate ore is valuable because Mn(II) is soluble in acid solutions, making the extraction process extremelyNovel Process of Reduction Roasting Manganese Ore with Sulfur
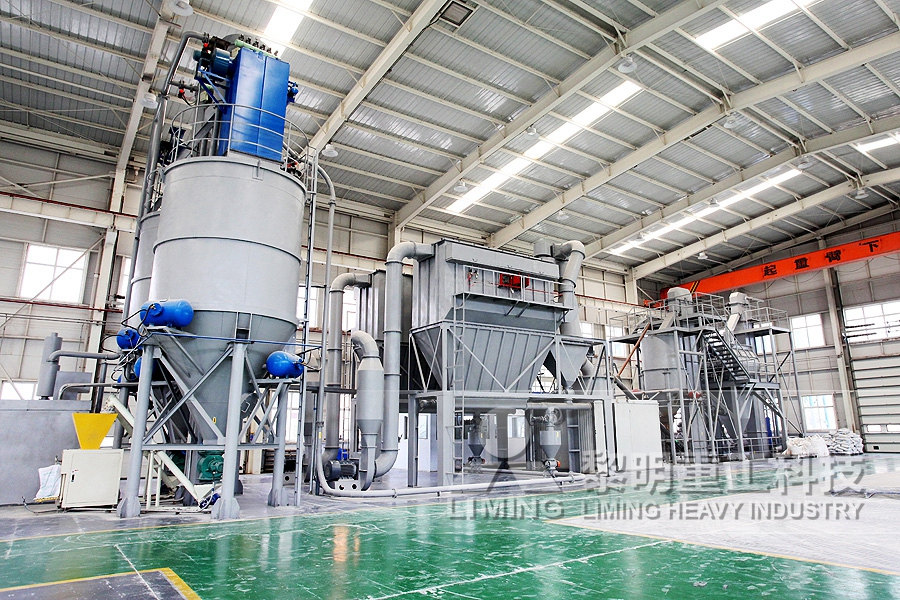
A Sustainable Process to Produce Manganese and Its Alloys
2021年12月24日 Hydrogen and aluminum were used to produce manganese, aluminum–manganese (AlMn) and ferromanganese (FeMn) alloys through experimental work, and mass and energy balances Oxide pellets were made from Mn oxide and CaO powder, followed by prereduction by hydrogen The reduced MnO pellets were then smelted and 2022年12月28日 The transformations of lowgrade manganese ore were investigated during roasting in the air at different temperatures up to 1200°C The transformations were followed up by XRD and TGADTA(PDF) Investigation of transformations of lowgrade manganese ore The iron ore production has significantly expanded in recent years, owing to increasing steel demands in developing countries However, the content of iron in ore deposits has deteriorated and lowgrade iron ore has been processed Iron Ore Pelletizing Process: An Overview2020年8月3日 Manganese alloys are important raw materials for steelmaking However, selective mining of highgrade manganese ore resources has resulted in a scarcity of these highgrade Mn ores (Mn: >42; Mn/Fe: >5) The present research work is carried out to explore a new smelting reduction process to produce highMn/Fe synthetic Mn ore from lowgrade Development of a Smelting Reduction Process for LowGrade
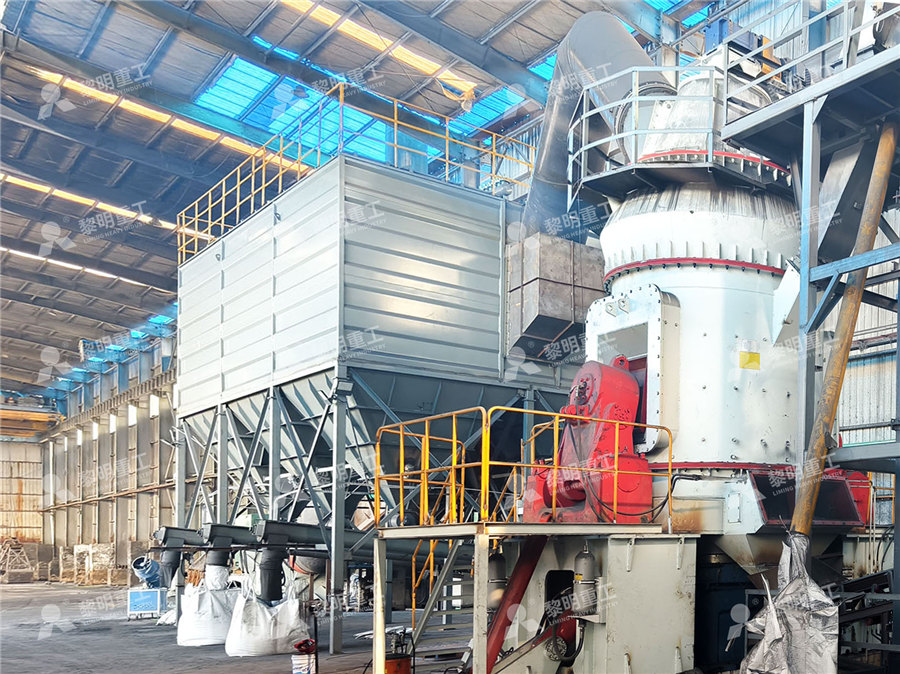
Manganese ore for Ferro Studies on Aluminothermic Reduction of
production in steel melting stage Alurninothermic process produces carbon free ferroalloys In this paper, details of investigations onferromanganese making are given Influence ofprereduction of manganese ore to Mn7O3 and Mn ,stage, excess aluminium overstoichiometric requirement, addition of fluxes etc, on metal yield is discussediron and/or silicon and modifying the process Manganese ore is the primary source of manganese used in the manufacture of manganese ferroalloys To be used in this way, asmined manganese ores normally undergo bene˜ciation to increase the manganese content and remove impurities Following crushing, milling and subsequentMANGANESE VALUE CHAIN RAW MATERIAL OUTLOOKManganese is an essential component of steelmaking process because it improves certain properties that steel by itself doesn´t have To name a few, Manganese allows to avoid a phenomenon called “hot shortness”, which causes a surface cracking process at high temperatures, it has an important ability to combine with Sulphur (an unwanted element in MANGANESE DISCOVERY, HEALTH SAFETY International Manganese Manganese ore is reduced and then leached with sulfuric acid The solution is purified, and manganous dioxide is obtained by electrolysis It can also be obtained by the oxidation of manganese compounds of lower valance or by the thermal decomposition of manganese nitrate Potassium permanganate (KMnO 4) finds wide use as an oxidizing agentManganese processing Alloy, Extraction, Smelting Britannica
.jpg)
Merioneth Manganese: Uses of manganese Hendrecoed
Spiegeleisen can be used in the Bessemer process of steel making to provide a known quantity of carbon at the end of the conversion process In the 1880s Welsh ore was calcined at the ironworks before being added to the blast furnace together with richer manganese ores2022年5月27日 Manganese minerals are weakly magnetic minerals [specific magnetic coefficient X = 10 × 106~600 × 106cm3 / g] can be recovered in the high magnetic field magnetic separator with magnetic field strength ho = 800 ~ 1600kA / M (10000 ~ 20000oe), which can generally increase the manganese grade by 4% ~ 10% Due to the simple operation, Manganese Beneficiation Processing Technology in China2019年5月1日 From the MnOre, manganese oxide (Mn3O4) was extracted and the powdered manganese oxide (Mn3O4) was then combined with lithium hydroxide monohydrate (LiOHH2O) to produce lithium manganese oxide Reducing agents in the leaching of manganese ores: A comprehensive 2020年6月4日 Lowcarbon ferromanganese (LCFeMn) is an essential ingredient for making highstrength lowalloy steel and stainless steel The conventional industrialscale silicothermic method for the production of LCFeMn comprises several energy intensive complex steps consuming about 2000 kWh/ton We have attempted an improved silicothermic process, which An Improved Process for the Production of LowCarbon Springer