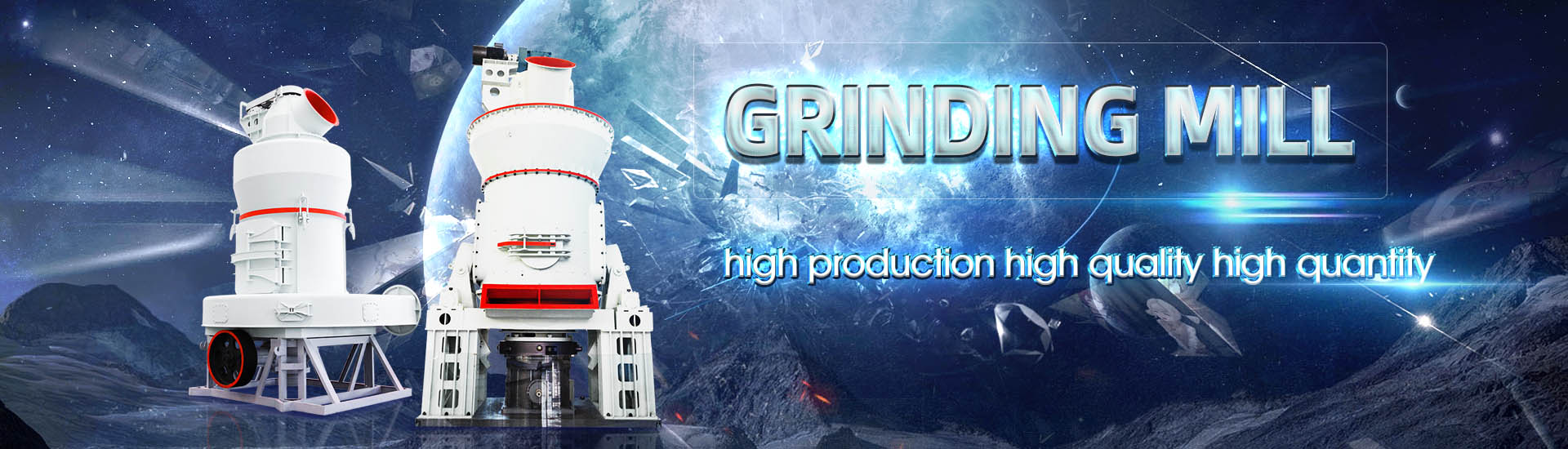
Method for grinding polymer materials into fine particles

Producing Fine Particles for Multiple Applications AZoM
With the increase in demand for higher performance plastics, the industry has been searching for more efficient, hightech grinding solutions that can produce even finer polymer particles that are distributed more evenly All this needs to be achieved whilst also maximising throughputs For example, the food packaging 展开Ball milling is a mechanical technique widely used to grind powders into fine particles and blend materials18 Being an environmentallyfriendly, costeffective technique, it has found wide application in industry all over the worldBall milling: a green technology for the preparation and 2015年7月1日 Milling involves the application of mechanical energy to physically break down coarse particles to finer ones and is regarded as a “top–down” approach in the production of Overview of milling techniques for improving the solubility of Ball milling is a mechanical technique that involves grinding solid materials using hard balls like stainless steel or tungsten to prepare nanosized metal particles with desired properties in a Ball Milling an overview ScienceDirect Topics
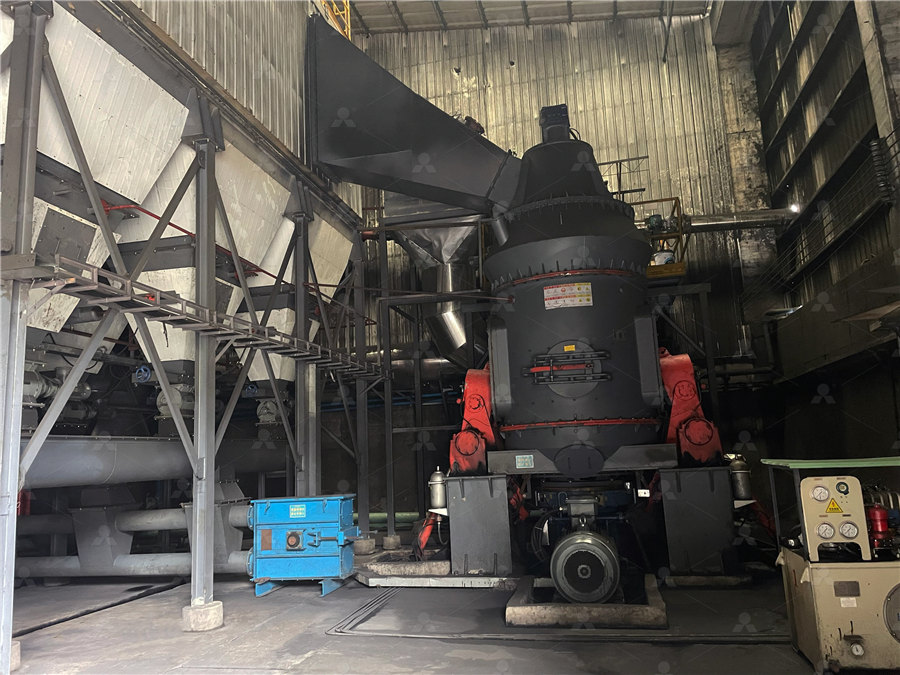
Ball milling: a green technology for the preparation and
Nano bers can be obtained by mechanical shearing actions such as highpressure homogenization, cryocrushing, micro uidization, high intensity ultrasonic treatments and 2023年6月29日 Shear force is in favor of exfoliating layered compounds, and impact force can efficiently grind the powders into fine particles As for highenergy ball milling, the heat generated by friction can be used to induce the Facile Ball Milling Preparation of FlameRetardant 2012年9月1日 It is shown that wet grinding of polymers in a stirred media mill and organic solvents (ethanol, hexane) at reduced temperatures down to − 80 °C is a suitable method to Production of polymer particles below 5 μm by wet grindingHosokawa’s attrition plates are uniquely engineered to finely grind heat sensitive materials, and in many cases, without cooling gas or liquid nitrogen The serrated teeth of the rotating and FINE GRINDING OF POLYMERIC HEAT SENSITIVE MATERIALS
.jpg)
New Cryogrinding System for fine grinding of Plastics
Hosokawa Micron Powder Systems has designed and installed a new system specifically for the size reduction of heat sensitive polymeric materials The system incorporates stateoftheart milling and classification equipment and Cryogenic grinding is a specialized process that involves cooling materials to extremely low temperatures, typically using liquid nitrogen at 196°C, before reducing them to fine particles This method is particularly effective for grinding materials that are sensitive to heat, such as plant and animal tissues, substances prone to oxidation, and volatile compounds like spices and Faqs Liquid Nitrogen Cryogenic Grinding Machine For Plastic When plane grinding, abrasive particles can become embedded in soft materials Continue with a somewhat finer grit surface (ie MD/DPPan with DiaPro Pan 15 um) as a second plane grinding step and MDLargo for fine grinding Metallographic grinding and polishing insight2021年12月24日 The materials obtained from the solgel method are used in various optical, electronic, Figure 4 shows a diagram of the loading of secondary particles into the nanoporous material 100 nanometers, they Nanomaterial by SolGel Method: Synthesis and
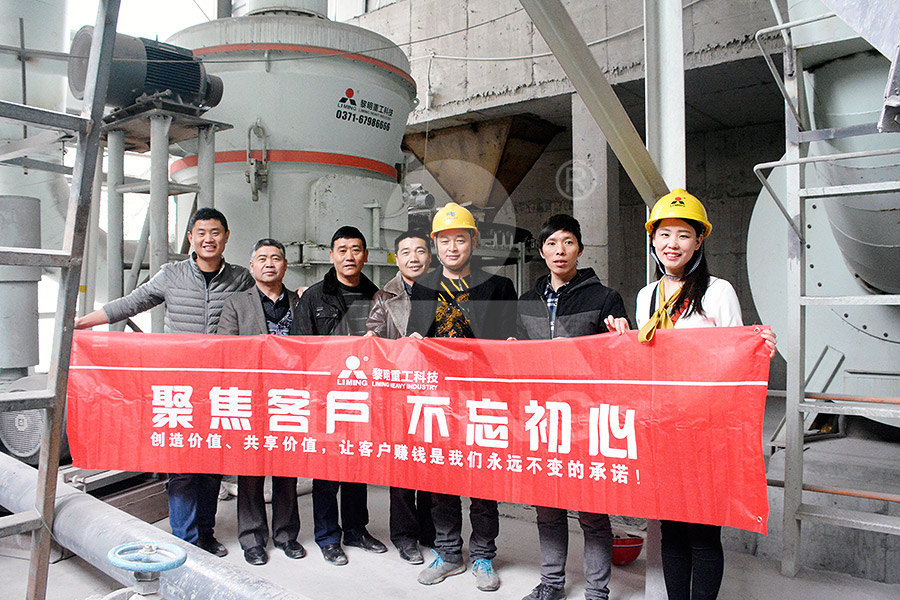
EnergyEfficient Advanced Ultrafine Grinding of Particles Using
2023年7月10日 The present literature review explores the energyefficient ultrafine grinding of particles using stirred mills The review provides an overview of the different techniques for size reduction and the impact of energy requirements on the choice of stirred mills It also discusses the factors, including the design, operating parameters, and feed material properties, 2022年9月16日 Nanomaterials are materials with one or more nanoscale dimensions (internal or external) (ie, 1 to 100 nm) The nanomaterial shape, size, porosity, surface chemistry, and composition are controlled at the nanoscale, and this offers interesting properties compared with bulk materials This review describes how nanomaterials are classified, their fabrication, Nanoparticle and Nanostructure Synthesis and Controlled Growth MethodsIntroduction to Supercritical Fluids Richard Smith, Cor Peters, in Supercritical Fluid Science and Technology, 2013 413 Particle Formation Fine particles are needed in many technological fields [PF1]In pharmaceutical fields, fine particles are used into tablets and capsules to provide reliable and stabilized drug delivery drug formulation processesFine Particle an overview ScienceDirect Topics2021年1月1日 [Show full abstract] demonstrate that wet grinding of polymers is a feasible approach for production of fine polymer particles that eg may be used as a starting material in a process chain for Shredding of polyethylene terephthalate waste ResearchGate
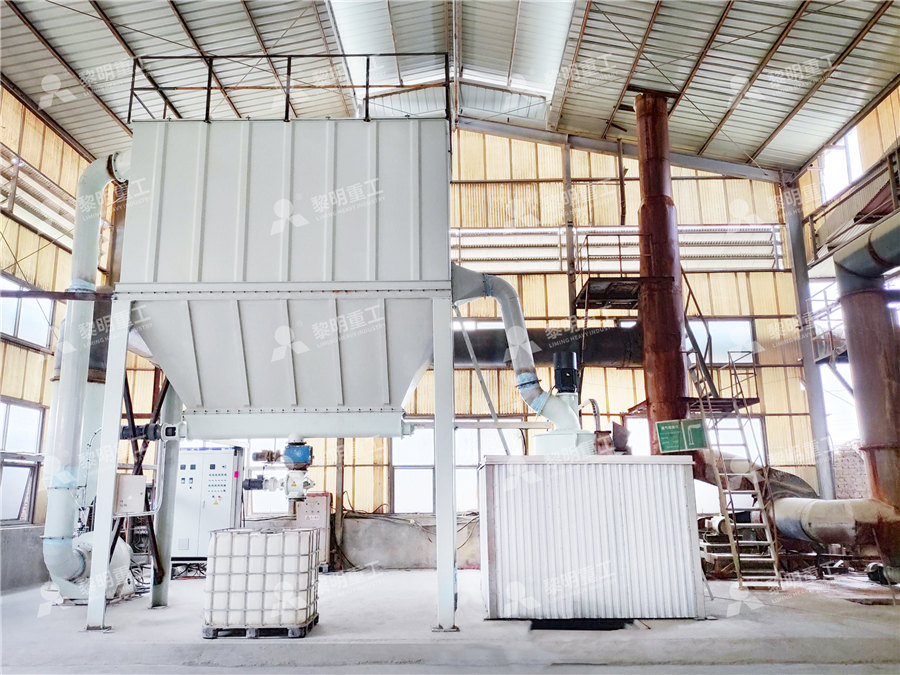
Recent Developments on the Synthesis of Nanocomposite Materials
2022年9月16日 This review is focused on the topical developments in the synthesis of nanocomposites using the simplest topdown approach, mechanochemical milling, and the related aspects of the interfacial interactions Milling constraints include time duration of milling, ball size, the balltosample content proportion, rotation speed, and energy that took part in a vital part 2012年9月1日 Polymeric microparticles that may be used in rapid prototyping processes typically are produced by either polymerization processes or cryogenic grinding in impact mills at liquid nitrogen temperature (− 196 °C) or by dry grinding at solid carbon dioxide temperature (− 78 °C) Within this account an alternative approach for the production of polymer particles is Production of polymer particles below 5 μm by wet grindingof grinding polymer waste is several times higher than for most brittle mineral materials Cutting and impact equipment is often used to shred plastic waste To obtain micronsized polymer particles, the technologies of cryogenic grinding and wet grinding in solvents are used, which is followed by high operating costsShredding of polyethylene terephthalate waste e3s 2015年12月31日 It is shown that wet grinding of polymers in a stirred media mill and organic solvents (ethanol, hexane) at reduced temperatures down to − 80 °C is a suitable method to produce polymer Rounding of Irregular Polymer Particles in a Downer Reactor
.jpg)
Fine Grinding an overview ScienceDirect Topics
Autonomous grinding algorithms with future prospect towards SMART manufacturing: A comparative survey Md Riaz Pervez, Paolo Dario, in Journal of Manufacturing Systems, 2022 21 Grinding operation Grinding is a metal removal process with the help of bonded, coated or free abrasive grain tools Apart from all other machining operations, the ‘Grinding’ is the last Fine Particle Technologies makes possible the use of beads with diameters down to 50 m The new design prevents damage to nanoparticles through the use of a novel revolving screen that facilitates adequate product throughput at slow, low energy motor speeds while providing practical methods for handling fine grinding mediaEffectively Grinding And Dispersing Nanoparticles Using A Fine 2019年11月1日 In this study, to provide a general understanding on rubber toughening, we first briefly introduce the classification of polymer materials that require toughening (Section 2), common strategies to improve the interfacial adhesion between rubber and polymer matrices (Section 3), and homogeneous rubber microparticle toughening (Section 4)Advances in toughened polymer materials by structured rubber particles2012年9月1日 Polystyrene (PS) (Carl Roth) of a particle size fraction of 250 μm to 500 μm (x 50,3 = 363 μm) and PEEK Vicote 705 (Victrex, x 50,3 = 215 μm) have been used as starting materials (particle size distributions see Fig 1)The aforementioned PS particle fraction has been obtained by comminution of PS granules of 3 mm in diameter using a rotor mill Production of polymer particles below 5 μm by wet grinding
.jpg)
An assessment of methods used for the generation and
2023年9月4日 Surface analysis FTIR Fouriertransform infrared (FTIR) spectroscopy was used to verify polymer chemistry before and after the cryomilling process using a Bruker VERTEX 70v FTIR Spectrometer with a platinum diamond attenuated total reflectance (ATR) crystal in the wavenumber range from 4000 cm −1 to 400 cm −1Data was collected at a spectral resolution more widespread This concerns, among others , polymer materials The annual volume of polymer materials manufactured all over the world reaches nearly 260 million Mg, out of which about 60 million Mg in Europe [18] Taking into account short life (which particularlySize Reduction by Grinding as an Important Stage in Recycling2022年5月20日 Particlesize reduction is a result of particle–particle and particle–wall collisions upon feeding of solids into the air stream (Fig 46) Normally, gas velocities are such that a sonic flow is achieved, and only particles that reach a predetermined particle size will be able to leave the vortex through the exitMechanical ParticleSize Reduction Techniques SpringerLinkThe drug material is grinded into fine powder, and then placed inside a clean container The extraction solvent hot or cold is then poured on top of the drug material, soaked, and kept for a short period of time[ 1 , 2 , 3 , 11 ] This method is suitable for extraction bioactive constituents that are readily solublePreparation of Medicinal Plants: Basic Extraction and Fractionation
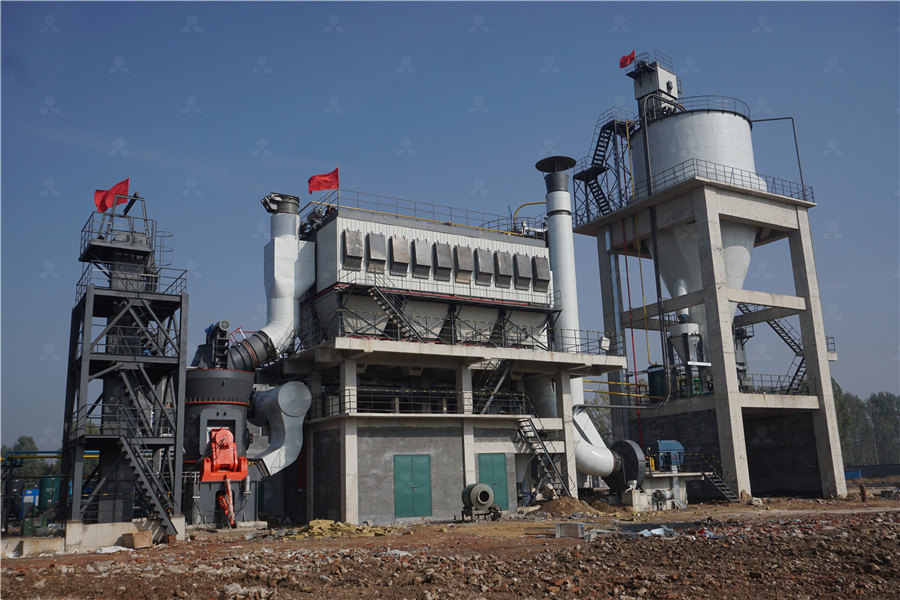
Amey Engineers Plastic Fine Grinding
Plastic Fine Grinding play a key role in plastic recycling plants and production facilities It offers several benefits in addition to processing plastics that are used as raw materials for other products like storage containers, toys, packaging bags, and consumer electronics2021年10月15日 We comprehensively summarize stateoftheart 3D printing in polymer/particle composite processing in this review First, section 2 will briefly overview a few critical structural features contributing to the material properties (ie, material types, nanoparticle morphologies, and interfacial interactions) Then, section 3 will introduce the reviewed 3D printing and give 3D printing for polymer/particlebased processing: A reviewProduction of polymer particles below 5μm by wet grinding × Close Log In Log in used as surrogates Cryogenic grinding, or cryomilling, was successfully utilized to transform polystyrene (PS) bulk material into heterogenous micro and 3895–3902 [8] S MolinaBoisseau, N Le Bolay, Fine grinding of polymers in a vibrated bead mill Production of polymer particles below 5μm by wet grinding2020年1月1日 The structure of γAl 2 O 3 regarded as a defect spinel with a deficit of cations, and characterized by cubic closepacked oxygen lattices The aluminum ions in the octa and tetrahedral interstices form particles with a small and narrow size distribution and possessed a high surface area: ~300 m 2 /g Upon the thermal treatment of γAl 2 O 3, it transforms to Recent processes for the production of alumina nanoparticles

Pulverization 1: Definition and purpose THINKY MIXER
2019年10月31日 The particle is broken up into several pieces, and this process continues until the particle gradually turns into fine particles Volume grinding is dominant in compression pulverization and impact pulverization(*3)(*4)。 Mechanism of pulverization The external force applied to particles can be roughly divided into four types, “compression 2022年3月11日 During the granulation process, small fine or coarse particles are converted into larger agglomerates called granules Granules enhance the un iformity of the AP I, increase the d ensity of the b (PDF) GRANULATION TECHNIQUES: AN OVERVIEW ResearchGate2023年5月15日 The main goal of ball milling method is to reduce particle size to a target range It has been widely used for transforming powders into fine particles (also known as comminution), inhibiting the aggregation of fine particles, deagglomerating powdered materials and blending materials by using impact and friction forcesMixing methods for solid state electrodes: Techniques, Ball milling is a mechanical technique that is broadly used to grind powders into fine particles [134–141] The reactants are generally broken apart using solvent molecules in the traditional method; but in ball milling, reactants are broken by using mechanical forces The term mechanochemistry has been introduced very recently [142]Ball Milling an overview ScienceDirect Topics
.jpg)
New Cryogrinding System for fine grinding of Plastics
One of the largest materials markets in the world is Plastics and these applications require the use of a wide variety of Polymers The global polymer market was valued at $5336 Billion USD in 2019 and is projected to have a compound annual growth rate of 51% to 2030 Currently the size reduction of polymerstwo particles Shear refers to cutting of particles resulting in fracture The particles are broken into fine particles by squeezing action in compression force type Main objective of milling: Particle size reduction (main purpose), Particle size growth, shape change, agglomeration (joining of particles together), solid state alloying,Powder metallurgy – basics applications IIT Guwahati2018年6月1日 Fine grinding mills can be categorized into five groups [48]: impact mills, ball media mills, air jet mills, The globular particles in fine powdered wood tend to aggregate This can be explained by the different grinding methods and material properties including the moisture and operating parameters used in the experimentsFine grinding of wood – Overview from wood breakage to 2024年4月3日 As discussed, the awareness of grinding raw materials into fine particulates to achieve desired performance came remarkably early in human civilization, but the specific usage of particles within a comparably uniform A review on applications of fine particles integrated
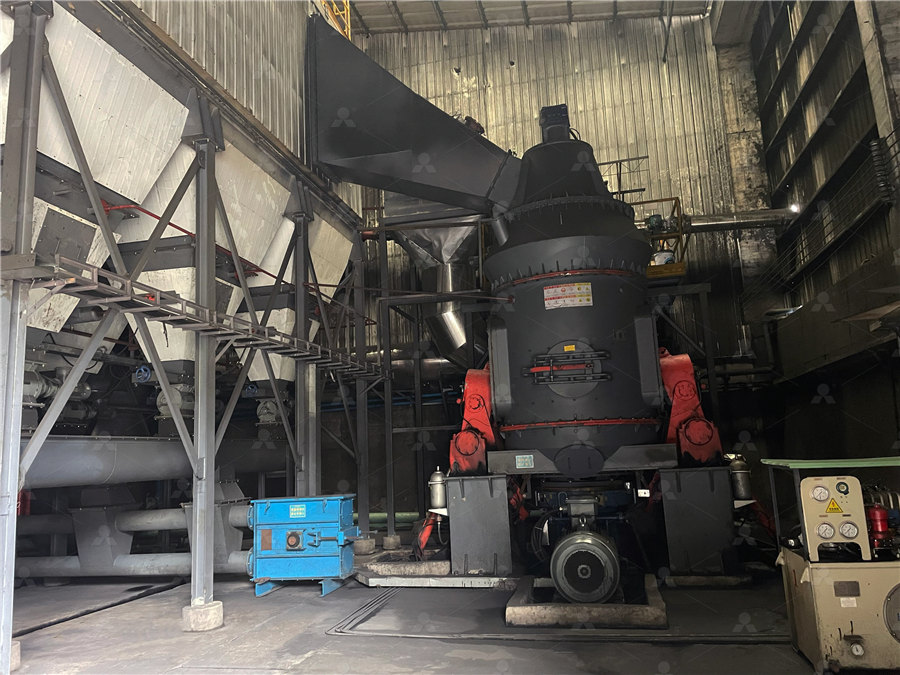
What is the easiest way to grind polymer pellets into
The key is to do the grinding below the glass temperature of the polymer to convert it into a powder as you mention, if material heats on grinding it can make it more difficult particularly if 2022年6月10日 The problem of fine grinding of materials is voiced and it is shown that for a number of characteristics the existing equipment does not meet modern requirements, and a new development trend is FIBER GRINDING METHOD OF MATERIALS AND ISSUES OF ITS From precrushers for the comminution of coarse materials to jet and ball mills for ultrafine grinding: Hosokawa Alpine offers mills for a wide range of fineness levels The mill type that is best suited to your application depends not only on the desired fineness level, but also on which raw material is to be ground and for what purposeGrinding Hosokawa Alpine2017年3月4日 grinding material at smaller particle sizes, and can be used after ball mills in a grin ding process Like ball mills, grinding (steel) balls or pebbles are often added to stirred mills to help SIZE REDUCTION BY GRINDING METHODS ResearchGate
.jpg)
The Development of Efficient Contaminated Polymer Materials
2021年2月26日 Usually, selfpropelled machines are used to crush and break polymer materials into fairly large particles [48] In energy re covery processes in the context of inci neration, shredding is carried out2020年7月24日 Cryogenic grinding, namely freezer grinding or cryomilling [36], is among the advanced grinding methods that allows finer particle size via grinding operation at extremely low temperature, often (PDF) A Review on Cryogenic Grinding ResearchGate2017年12月15日 We demonstrate that wet grinding of polymers is a feasible approach for production of fine polymer particles that eg may be used as a starting material in a process chain for production of Production of PBT/PC particle systems by wet grinding2023年1月27日 Recycling Today Magazine Hosokawa Micron Group “Ask the Experts” – Fine Grinding of Plastics July Issue focusing on Plastics Recycling Five questions and answers about fine grinding of plastics, totaling 400450 words What limitations does the plastic industry face when it comes to size reduction and fine grinding of polymers? The manufacture of polymer Ask the Expert: 5 Questions about Fine Grinding of Plastics
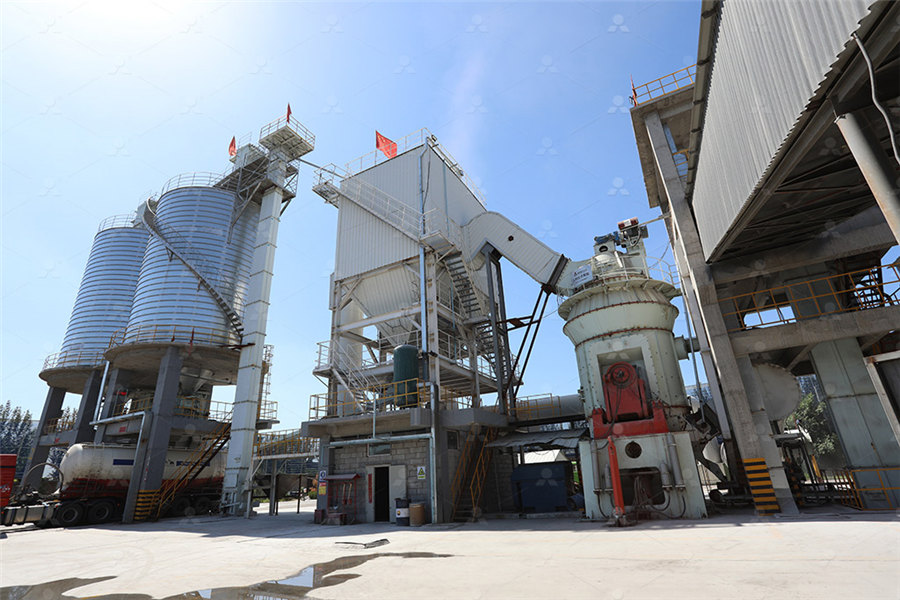
Aggregating fine hydrophilic materials in froth flotation to
2024年3月1日 Among the influencing factors shown in Fig 1, particle size is the most important [[9], [10], [11]]Froth flotation works best when minerals are in an intermediate particle size range, typically from 20 to 150 μm, but varies with the types of minerals [[10], [11], [12]]When particles are smaller than about 20 μm, value mineral recovery and separation selectivity drop quickly