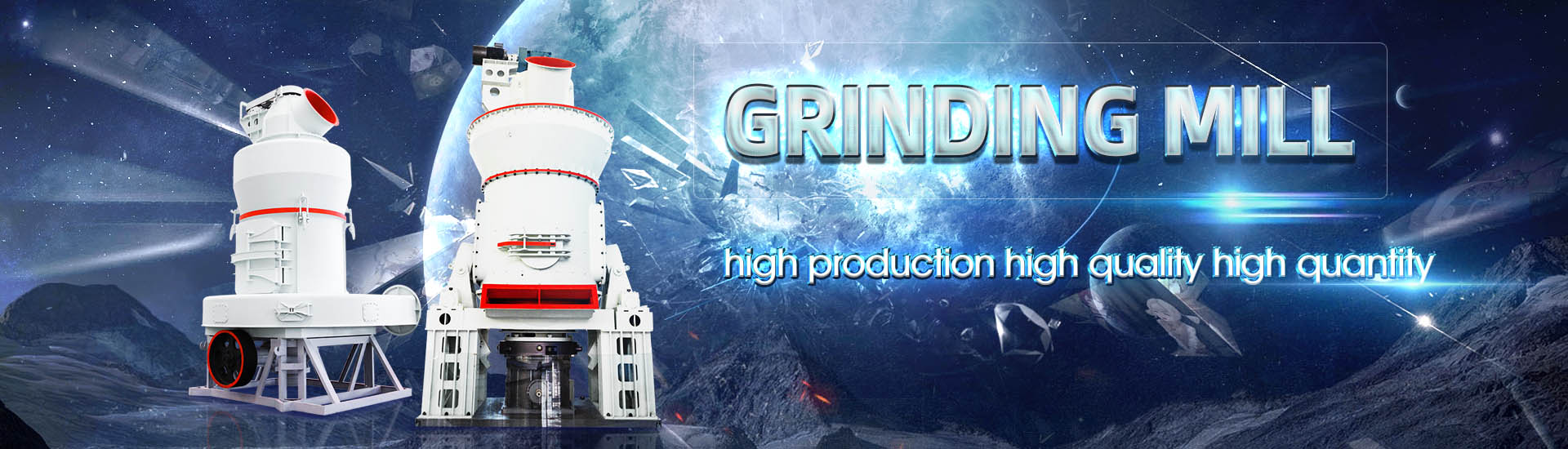
In order to make the grinding system effect of high fine vertical mill
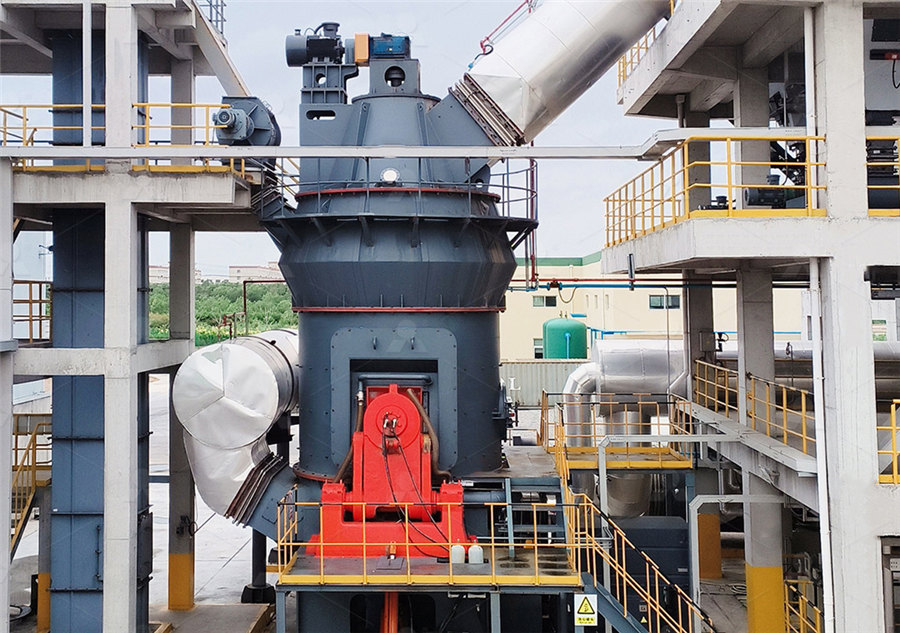
Operational parameters affecting the vertical roller mill
2016年9月1日 In vertical roller mills there are several factors that influence the performance of the grinding process [22] which are moisture content (mc), grinding table rotation speed (s), 2024年1月15日 An industrialscale vertical roller mill (M600) was analysed for air flow in this study This led to proposed modifications, which were implemented in a new mill design Optimisation of the performance of a new vertical roller mill by 2024年1月17日 Based on energysize reduction models proposed in the literature, equations were derived to estimate the grinding energy of the vertical roller mill by using the size and pistondie test dataParameters for the Grinding Process in Vertical Mills 2022年1月23日 For design of experiments (DOE), the response surface method (RSM) was employed with the VRM experiments to systematically investigate the influence of operating parameters on the energyAnalysis and Optimization of Grinding Performance of
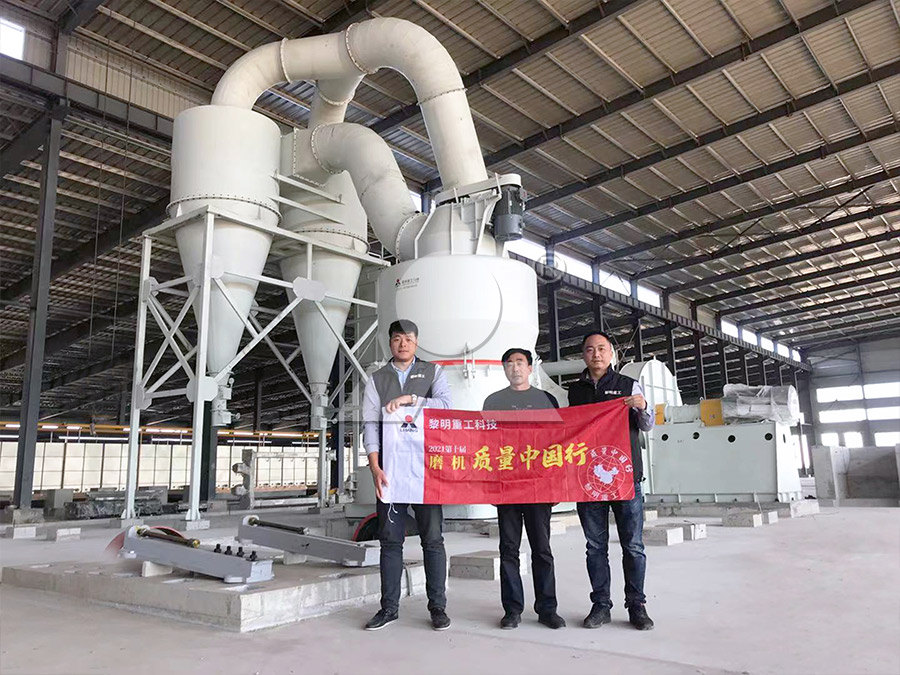
Vertical roller mill for raw Application p rocess materials
Recently, the vertical roller mill having great grinding performance is widely applied to the raw material grinding process However, tube mill, which has about 30% poor grinding 2021年7月12日 This paper introduces an expert system based on the NSGAII algorithm The established system is able to suggest the grinding and dressing parameters to produce a Development of an expert system for optimal design of the A high content of very fine particles on the grinding track usually troubles the stability of the grinding bed Fine particles lower the interparticle friction, which reduces the grinding SikaGrind® for vertical roller mills2024年6月14日 The obtained research results indicate that the type of grinding media used significantly affects the grain size of the milling product—especially in fine and very fine grinding (below 10 µm) − Analysis of the percentage share The Influence of the Grinding Media Diameter on
.jpg)
A Review of the Grinding Media in Ball Mills for Mineral
2023年10月27日 The ball mill is a rotating cylindrical vessel with grinding media inside, which is responsible for breaking the ore particles Grinding media play an important role in the comminution of mineral ores in these mills This work reviews the application of balls in mineral processing as a function of the materials used to manufacture them and the mass loss, as 2018年2月1日 The crushed product of HPGR was subjected to grinding in the second stage in a ball mill and stirred mill The effect of mill speed, grinding time, and ball size on the performance of the ball Effect of ball and feed particle size distribution on 2023年3月9日 In order to make a cut, the grinding wheel is moved across the workpiece by the crossfeed handwheel Crossfeed moves the wheel head up and down or left and right It is another crucial component of this machine #7 Grinding Machine: Parts, Types, Operations, More 2021年1月1日 Grinding Mill Vertical Roller Mill or Ball Mill: The reclaimed raw mix fed to Raw Mills, for drying and fine grinding of Raw meal for kiln feed: 4: Coal Grinding: Grinding Mill Vertical Roller Mill or Ball Mill: Coal is ground in Coal mill, which is a fuel for use in Kiln firing: 5: Pyro Section, Clikerization: In line calciner six stage Review on vertical roller mill in cement industry its
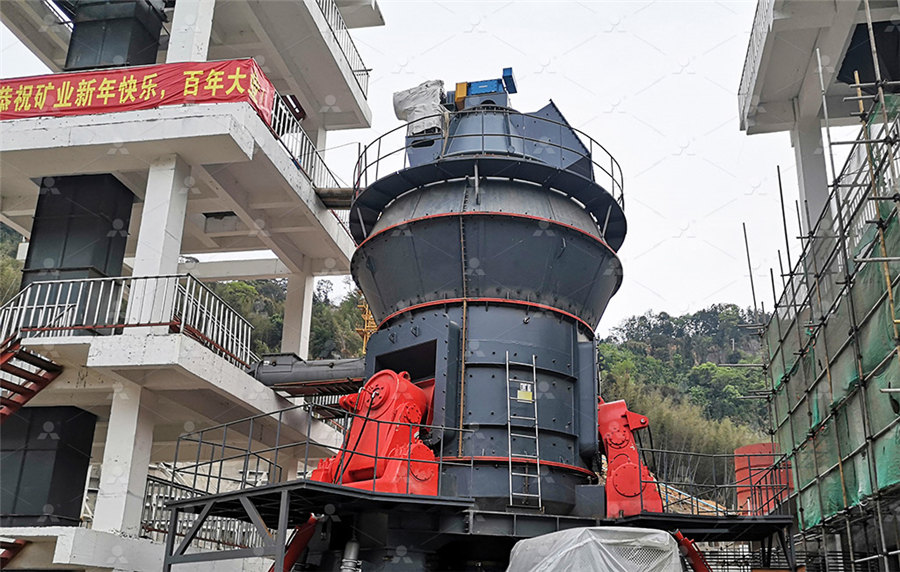
(PDF) Analysis of the efficiency of the grinding process in closed
2016年1月1日 For open circuit grinding [34,35], there is no disagreement with the calculation of the circulating load and classification efficiency, both of which 2 can be characterized relatively accurately2022年5月27日 The main chemical component of highsilicon iron tailings (HSITs) is SiO2; HSITs also include some oxides such as Al2O3 and CaO Mechanical activation can reduce the particle size of HSITs and enhance their pozzolanic activity such that they can be used as a type of mineral admixture for cementbased materials (CBMs) This study aims to investigate the On the grinding effects of highsilicon iron tailings2023年7月10日 The present literature review explores the energyefficient ultrafine grinding of particles using stirred mills The review provides an overview of the different techniques for size reduction and the impact of energy requirements on the choice of stirred mills It also discusses the factors, including the design, operating parameters, and feed material properties, EnergyEfficient Advanced Ultrafine Grinding of Particles Using2017年9月1日 With the continual depletion of high grade simple ore bodies, more complex, finely disseminated ore bodies are being processed, which has led to an increase in the prevalence of fine grinding (Sinnott et al, 2006)This has been evident in the platinum group element (PGE) industry in South Africa, where the Bushveld Complex hosts 70% of global Fine grinding: How mill type affects particle shape characteristics
.jpg)
The liberation effect of magnetite fine ground by vertical stirred mill
2012年7月1日 A magnetite middling was used to compare the liberation effect of the magnetite fine ground by a vertical stirred mill and a ball mill The magnetite middling contained a high content of magnetite intergrowth with the particle size mainly distributed in the range of 40–150 μmThe new generated −38 μm products were concentrated by magnetic separation2013年12月18日 Fine grinding, to P80 sizes as low as 7 μm, is becoming increasingly important as mines treat ores with smaller liberation sizes This grinding is typically done using stirred mills such as the Isamill or Stirred Media Detritor While fine grinding consumes less energy than primary grinding, it can still account for a substantial part of a mill’s energy budget Overall Energy Use of Fine Grinding in Mineral Processing2018年4月28日 Grinding is a staple sizereduction process to produce food powders in which the powdered form is chemically and microbiologically stable and convenient to use as end products or intermediate products The moisture Effect of Moisture Content on the Grinding Process 2017年1月17日 Grinding mills are infamous for their extremely low energy efficiency It is generally accepted that the energy required to produce new mineral surfaces is less than 1% of the electricity consumed Breaking down energy consumption in industrial
.jpg)
Analysis and Optimization of Grinding Performance of
2022年1月23日 This work concentrates on the energy consumption and grinding energy efficiency of a laboratory vertical roller mill (VRM) under various operating parameters2023年10月27日 Although considerable work has been carried out in that area, the influence of grinding media shape on the liberation of minerals, as well as the effect of various mill conditions on the A Review of the Grinding Media in Ball Mills for Mineral Processing2014年1月1日 However there is a trend towards ball mill grinding for product sizes below the traditional ball mill cutoff of 45 mThe effect of ball size on the feed and product size distributions in a fine The investigation of operating parameters in a vertical stirred mill2015年8月6日 There are basically two groups of Grinding Mill Liners Ones with a HIGH PROFILE and Grinding Mill Rubber Liners This system combined rubber plates with cast manganese lifter bars which “assures that the major portion of the The base of the metal lifter must also be a flat smooth surface in order to properly seat Grinding Mill Liners 911Metallurgist

Ceramic Grinding Kinetics of Fine Magnetite Ores in the Batch Ball Mill
2023年9月10日 Aiming to reveal the kinetic characteristics of ceramic ball grinding of fine magnetite comprehensively, two types of ceramic balls ground with the same filling rate and total weight as steel balls were researched The results show that the breakage rate of ceramic ball grinding is only half of that of steel ball grinding with the same media filling rate With the same 2023年9月29日 In order to control grinding heat, Toshiyuki Enomoto et al [117] made grinding wheels with submicron and titanium dioxide particles on the surface by electroplating (as shown in Fig 13 (c)(d)), he found that these diamond grinding wheels have high hydrophilicity, these two treatments had a significant effect on the reduction of grinding heatMechanical behavior and modeling of grinding force: A 2024年1月31日 Ceramic ball milling has demonstrated remarkable energysaving efficiency in industrial applications However, there is a pressing need to enhance the grinding efficiency for coarse particles This paper introduces a novel method of combining media primarily using ceramic balls supplemented with an appropriate proportion of steel balls Three grinding media Enhancing the Grinding Efficiency of a Magnetite SecondStage Mill 2024年1月18日 This study investigated the effect of grinding media on the finegrinding performance in the wet tumbling mill Comparative experiments between cylpebs and ceramic balls were conducted in a laboratory wet ball mill under various conditions, such as different total masses, total surface areas, and total numbers The results indicated that ceramic balls A Comparison of the FineGrinding Performance between
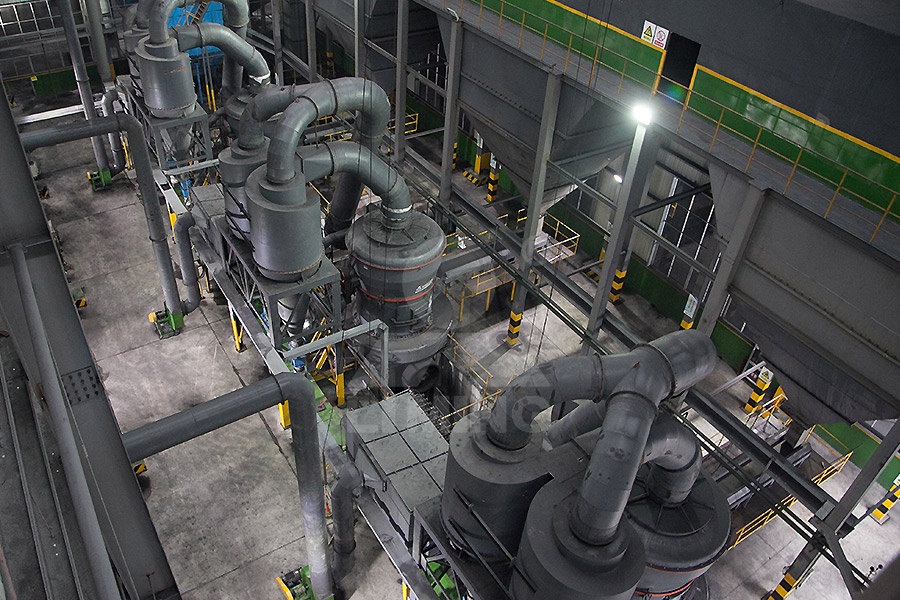
Development of an expert system for optimal design of the grinding
2021年7月12日 The physical or empirical modeling of the grinding process and the effects of its parameters on the workpiece quality is sophisticated This is due to the extreme complexity of the process So far, no remarkable success could be made by the proposed models to achieve a reliable and effective design and control of the process This article introduces an expert 2022年11月30日 Highspeed rail grinding is a unique passive grinding maintenance strategy that differs from conventional grinding techniques Its grinding behavior is dependent on the relative motion between the grinding Investigating the Effect of Grinding Time on High 2017年1月1日 A dry operated, horizontal stirred media mill was used for the fine grinding of limestone and compared in open and closed circuit modes It was found that the choice of grinding aids as well as The Effect of Stirred Mill Orientation on Calcite 2021年7月1日 Vertical stirred mills may be classified according to the speed of the stirrer in two groups: gravityinduced or fluidized mills [[1], [2], [3]]In the gravityinduced mills, the stirrer, generally of the screw type, turns so that the grinding charge exhibits an ascending convective motion at the center, descending from the edges of the screw and close to the mill shell, owing Predicting the effect of operating and design variables in grinding
.jpg)
(PDF) A comprehensive review on the grinding process:
June 2022; ARCHIVE Proceedings of the Institution of Mechanical Engineers Part C Journal of Mechanical Engineering Science 19891996 (vols 203210) 236(2):年10月18日 The aim of this work was to observe the impact of the milling technique employed by the DESI 11 disintegrator on the properties of fly ash This type of mill is a highspeed pin mill with two (PDF) The effect of highspeed grinding technology on the properties 2024年10月5日 Highspeed grinding (HSG) is an advanced technology for precision machining of difficulttocut materials in aerospace and other fields, which could solve surface burns, defects and improve surface integrity by increasing the linear speed of the grinding wheel The advantages of HSG have been preliminarily confirmed and the equipment has been built for Highspeed grinding: from mechanism to machine tool2021年4月30日 Passive grinding is a new rail grinding strategy In this work, the influence of grinding pressure on the removal behaviors of rail material in passive grinding was investigated by using a selfdesigned passive grinding simulator Meanwhile, the surface morphology of the rail and grinding wheel were observed, and the grinding force and temperature were measured Study on the Effect of Grinding Pressure on Material Removal
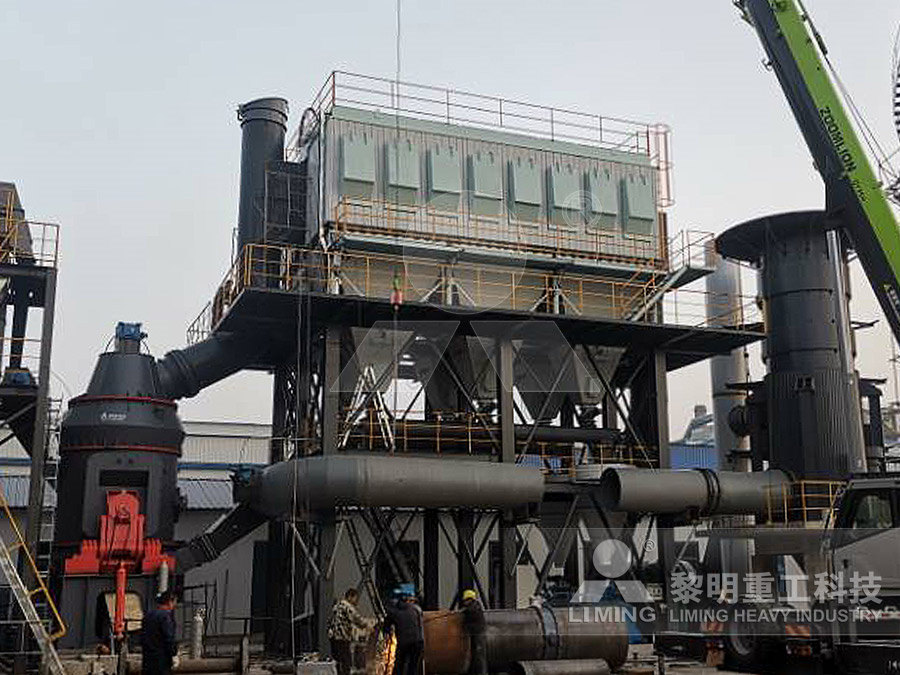
The Influence of the Grinding Media Diameter on Grinding
2024年6月14日 The grinding process plays a crucial role in industry, allowing for the reduction of particle sizes of raw materials and substances to the required fineness—either as a finished product or for further technological processes The high demand for micro and nanopowders or suspensions is associated with the high energy consumption of the milling process Therefore, 2024年1月20日 Compared with the parameters of surface grinding, those of the curved surface abrasive belt grinding are more diverse, and the material removal mechanism is more complicated This makes the selection of the parameters of the curved surface grinding process extremely difficult This study investigates the effects of different parameters on the grinding Comprehensive analysis of the effects of different parameters on 2022年1月1日 The size of grinding media is the primary factor that affects the overall milling efficiency of a ball mill (eg power consumption and particle size breakage)Effect of grinding media on the milling efficiency of a ball millimprovement of this tube mill grinding system is highly expected Descriptions The tube mill comminutes raw materials by impact and friction between grinding balls, which hit raw materials as well as between grinding ball and mill lining Many of this type mills have two grinding chambers for coarse and fine grinding Grinding ball sizeVertical roller mill for raw Application p rocess materials
.jpg)
Sustainable techniques in grinding: State of the art review
2020年10月1日 Grinding is a frequently used manufacturing process to produce finished components of desired shape, size, and accuracy This uses multiple point cutting tools to remove the unwanted materials from the stock in the form of chips (Komanduri, 1993)Earlier researchers have classified grinding as FormFinish Grinding (FFG) and Stock Removal Grinding (SRG)2024年2月28日 Hard materials have found extensive applications in the fields of electronics, optics, and semiconductors Parallel grinding is a common method for fabricating highquality surfaces on hard materials with high efficiency However, the surface generation mechanism has not been fully understood, resulting in a lack of an optimization approach for parallel grinding A Novel Approach to Optimizing Grinding Parameters in the2013年1月1日 One of these, "Circuit Classification System Efficiency" (CSE), is the fraction of "coarse" material inside the ball mill upon which grinding energy is deliberately expended, versus the remaining THE BENEFITS OF HIGH CLASSIFICATION EFFICIENCY IN CLOSED BALL MILL 2019年4月22日 High grinding density, the material is easy to stick around the steel ball, so the impact and grinding effect of steel ball on materials is good, but the pulp flows slow, which is not conducive to Ten Ways to Improve the Grinding Efficiency of Your Ball Mill
.jpg)
Cement grinding Vertical roller mills VS ball mills
The grinding efficiency of the vertical roller mill combined with an ability to grind, classify and – if required – dry within a single unit gives the vertical roller mill system a decided advantage over a ball mill system However, the grinding process applied in a vertical roller mill has the effect that the vertical roller mill is more 2020年8月12日 This study shows the performance of a currently running vertical roller coal mill (VRM) in an existing coalfired power plant In a power plant, the coal mill is the critical equipment, whose An investigation of performance characteristics and energetic 2016年10月5日 In this chapter an introduction of widely applied energyefficient grinding technologies in cement grinding and description of the operating principles of the related equipments and comparisons over each other in terms of grinding efficiency, specific energy consumption, production capacity and cement quality are given A case study performed on a EnergyEfficient Technologies in Cement Grinding IntechOpen2019年12月1日 High quartz content in clay substantially impacts the grinding of raw mix, quality of clinker and final cement produced The presence of quartz requires very fine grinding and a long sintering Comparative study of the grinding aid effects for dry fine grinding