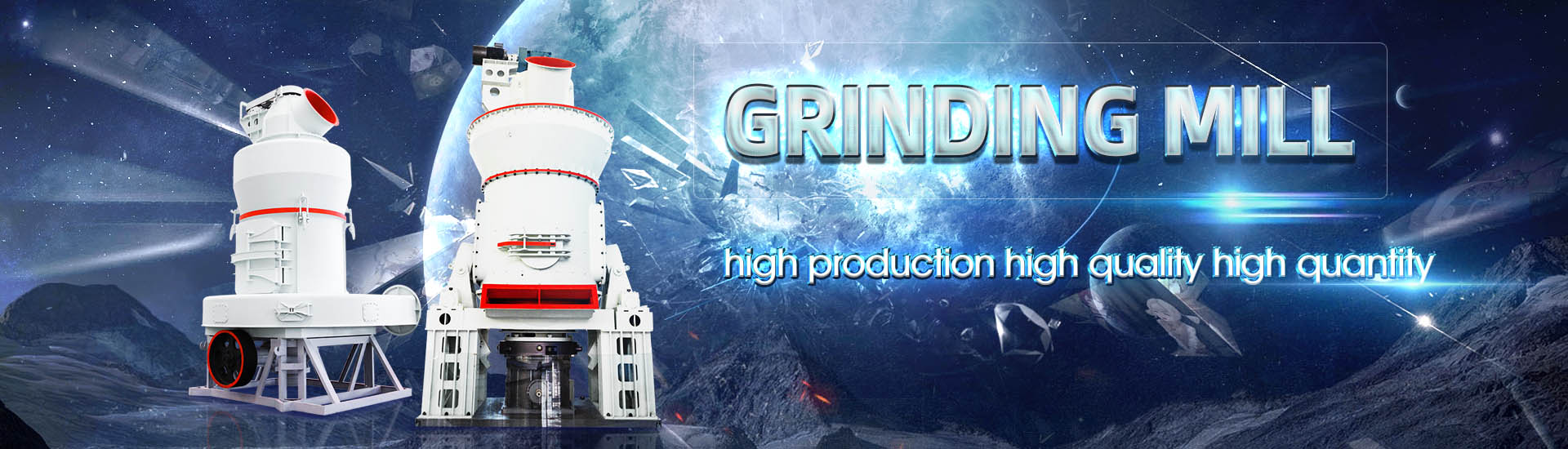
Ore powder making process
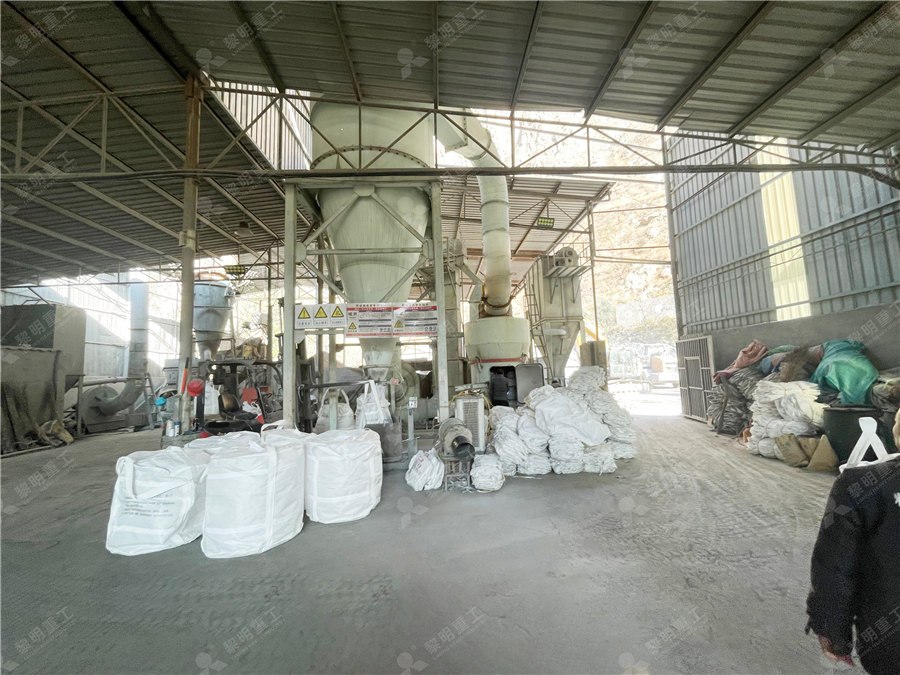
Making Metal Powder MPIF
In this process, molten metal is separated into small droplets and frozen rapidly before the drops come into contact with each other or with a solid surface Typically, a thin stream of molten metal is disintegrated by subjecting it to the impact of highenergy jets of gas or liquid In principle, the technique is applicable to 展开Virtually all iron powders are produced by one of two processes The longest established of these processes is the sponge iron process, the leading example of a family of processes involving solid state reduction of an oxide In the Powder production technologies Powder Metallurgy There are many ways in which metals may be produced in powder form, comminution of solid metal precipitation from solution of a salt; thermal decomposition of a chemical compound; Powder Metallurgy – Powder Processes (Solid State Reduction 2023年10月9日 Fluidized bed technology has become a crucial method used to process iron ore powder in nonblast furnace ironmaking, such as smelting reduction and direct reduction This Development and Problems of Fluidized Bed Ironmaking Process:
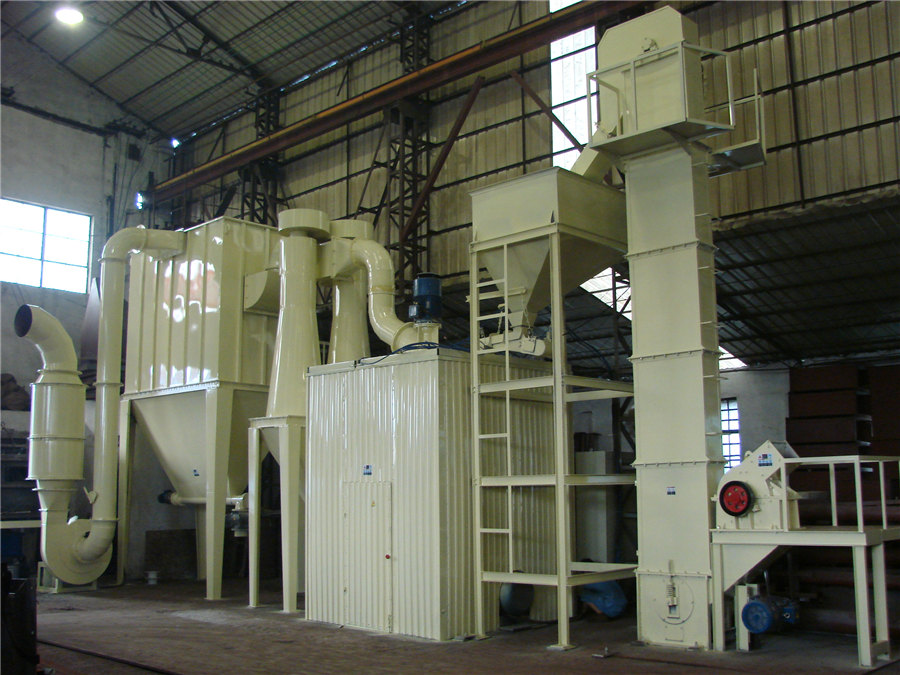
From Ore to Finished Product Copper
Copper ore is extracted using two basic methods of mining open pit or underground mining 3 Processing of Copper Ore The first step in processing the ore removed from the mine is to Iron ore powder agglomeration is the basis for blast furnace ironmaking and is the processing work in between ore crushing, ore grinding separation, and steelmaking Its purpose is to Agglomeration of Iron Ores SpringerLinkDirect reduction refers to solidstate processes which reduce iron oxides to metallic iron at temperatures below the melting point of iron Reduced iron derives its name from these processes, one example being heating iron ore in a Direct reduced iron Wikipedia2023年3月14日 Direct electrolysis of iron ore powder will introduce electrolyte impurities The iron ore needs to be purified and screened first to get the appropriate alkaline system of iron Research progress in the preparation of iron by electrochemical
.jpg)
Iron Ore Pelletizing Process: An Overview ResearchGate
2018年7月11日 Induration processes were initially developed for ores composed of magnetite, since they are oxidized, producing hematite, and generating heat ( 4824 kJ/mol of Fe 3Iron processing, use of a smelting process to turn the ore into a form from which products can be fashioned Included in this article also is a discussion of the mining of iron and of its preparation for smelting Iron (Fe) is a relatively dense Iron processing Definition, History, Steps, Uses,The first step in the overall powder metallurgy (PM) process is making metal powders There are four main processes used in powder production: solidstate reduction, atomization, electrolysis, and chemical SolidState Reduction In Making Metal Powder MPIF2014年11月26日 Iron Ore Pellets and Pelletization Process satyendra; November 26, 2014; 0 Comments ; bentonite, binder, Grate kiln, induration, Pelletization Pellets, straight grate,; Iron Ore Pellets and Pelletization Process Pelletizing of iron ore was started in the 1950s to facilitate the utilization of finely ground iron ore concentrates in steel productionIron Ore Pellets and Pelletization Process IspatGuru
.jpg)
The Process of Making Iron: From Ore to Product
2024年8月2日 The ore is passed through crushers, which break it down into smaller chunks These chunks are then screened to separate the ore from waste material Grinding The crushed ore is then ground into a fine powder This step is crucial as it increases the ore's surface area, making it easier to extract the iron during subsequent processes2019年6月11日 World resources are estimated to be greater than 800 billion tons of crude ore containing more than 230 billion tons of iron The only source of primary iron is iron ore, but before all that iron ore can be turned into steel, it must go through the sintering process Sinter is the primary feed material for making iron and steel in a blast furnaceSintering: A Step Between Mining Iron Ore and Steelmaking2024年4月26日 The crushed ore obtained from the crushing stage is typically in larger size fractions and needs to be further processed through screening 2 Screening Screening is the process of separating the crushed ore into various size fractions It involves passing the crushed ore through a series of screens with differentsized openingsIron Ore Processing: From Extraction to Manufacturing2023年3月14日 The schematic of the MOE process is shown in Fig 3Wang et al [] used the MOE method to treat the raw materials of iron concentrate powder used in blast furnace smelting and analyzed the energy consumption of the MOE ironmaking processSibille et al [] produced metal iron and oxygen by performing electrolytic melting on a floating soil analog at 1600 °CResearch progress in the preparation of iron by electrochemical
.jpg)
Chapter 2 Production and Processing of Aluminum The Minerals,
the 19th century, is by far the most important process used in the production of aluminum oxide from bauxite The process has been refined and improved since its inception Fig 22 shows that the production of alumina is a complex chemical process The alumina content of bauxite ores varies from one deposit to another, and methods of treat2020年6月3日 A new route for making steel from iron ore based on the use of hydrogen to reduce iron oxides is presented, detailed and analyzed The main advantage of this steelmaking route is the dramatic reduction (90% off) in CO2 emissions compared to those of the current standard blastfurnace route The first process of the route is the production of hydrogen by Hydrogen Ironmaking: How It Works MDPI2017年3月22日 Powder injection: This process is similar to HMD injection processes CaO, CaC 2 and CaSi (sometimes in combination with Al) are used as reagents Most likely the biggest changes will involve the ironmaking process (coke making, ore agglomeration and BF), Sulphur removal in ironmaking and oxygen steelmakingPowdery iron ore includes the concentrate and natural rich ore produced by fine grinding separation Iron ore powder agglomeration is the basis for blast furnace ironmaking and is the processing work in between ore crushing, ore grinding separation, and steelmaking Its purpose is to provide highquality furnace burden for steelmakingAgglomeration of Iron Ores SpringerLink
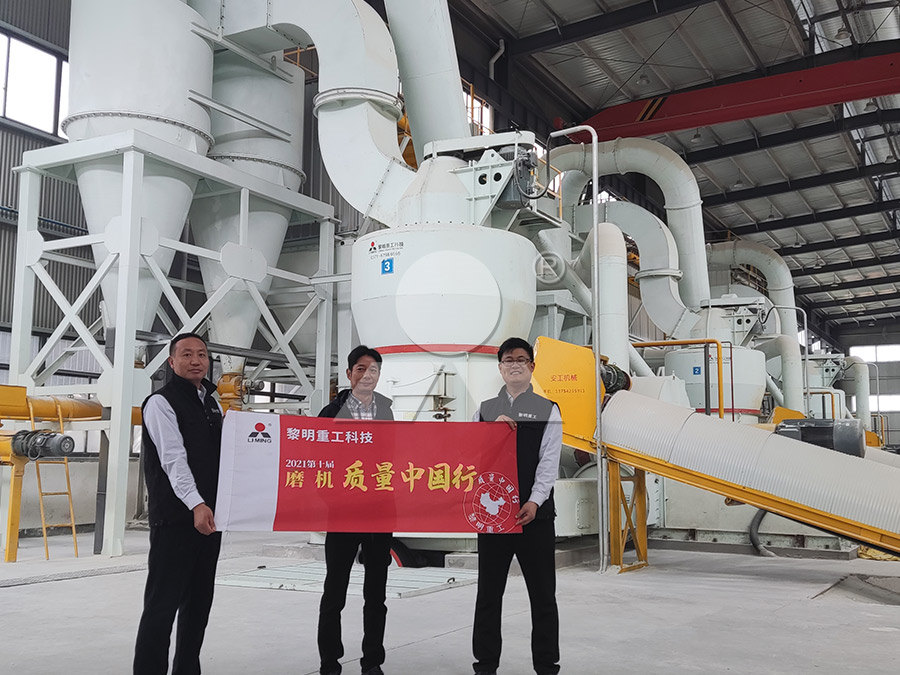
Raw materials Sinter plant ArcelorMittal
The sinter plant turns iron ore into sinter, which is the optimal product for the blast furnace Sinter is made by burning a mix of iron ore powder, fluxes and recycled substances from the steel plant to create an opengrained, consistent substance The sinter is then crushed, cooled and screened for dust Sometimes, iron ore is supplied in the form of iron ore pellets2013年2月23日 Fig 2 Flowsheet of straight travelling grate process Grate kiln process The grate kiln process was developed by former Allis Chalmer and the first plant on this technology was constructed in 1960 In the grate kiln process (Fig 3) the traveling grate is used to dry and preheat the pelletsIntroduction to Iron ore Pellets and Pelletizing processes2023年2月15日 Talc chemical formula: Mg 3 Si 4 O 10 (OH) 2 Talc hardness: 1 on Mohs scale Color of talc: Talc minerals are colorless, white, green, brown or gray Talc powders are white or gray Transparency: Translucent Talc luster: Vitreous and pearly Morphology: Euhedral crystals are extremely rare, usually found in platy, foliated to finegrained compact masses, sometimes How to Process Talc (the Softest Mineral)? FTM Machinery2024年1月7日 The Transformation: The first step in this transformation is crushing and grinding the ore into a fine powder finetuning the process and making adjustments based on the unique characteristics of each batch of ore Their expertise ensures that the final product meets the specific requirements of various applicationsHow is Tungsten made: From Ore to HighTech Metal
.jpg)
Copper Mining and Processing: Processing Copper Ores
Copper processing is a complicated process that begins with mining of the ore (less than 1% copper) and ends with sheets of 9999% pure copper called cathodes, which will ultimately be made into products for everyday useThe most common types of ore, copper oxide and copper sulfide, undergo two different processes, hydrometallurgy and pyrometallurgy, respectively, Manganese ore powder agglomeration method mainly comprises the group of pressure, sintering and three kinds of techniques of pelletizingAt present, sintering process is adopted in the manganese ore agglomeration more in the worldIn these several main methods, the group's of pressure method technique is simple, production cost low and environment is good, but Sintering process of manganese ore powder Google PatentsThe iron used in the steelmaking process is currently chemically reduced from iron ore through the use of fossil resources – natural gas or coal This process is known as Direct Reduced Ironmaking (DRI) Carbon combines with the oxygen in the iron ore, producing metallic iron and a carbonrich process gas, according to theFact sheet Hydrogen (H2)based ironmakingFrom its original home buried underground in a mine to its use in a finished product such as wire or pipe, copper passes through a number of stages When it is recycled it can pass through some over and over againFrom Ore to Finished Product Copper
.jpg)
The Direct Reduction of Iron Ore with Hydrogen
2021年8月8日 The steel industry represents about 7% of the world’s anthropogenic CO2 emissions due to the high use of fossil fuels The CO2lean direct reduction of iron ore with hydrogen is considered to offer a high 2024年7月30日 The smaller pieces are ground into a fine powder in a ball or rod mill This process increases the surface area of the ore, allowing for better copper extraction The grinding mills use steel balls or rods to crush the ore into a fine consistency, similar to The Process of Making Copper From Ore to ProductIron ore must go through a lengthy preprocessing stage before it can be pelletized – a series of steps that work to beneficiate and concentrate lowgrade ores This process varies depending on the ore source, but typically involves Iron Ore Pelletization FEECO International IncThe possibility of directly using powder, granular ore, and coal was confirmed, and necessary equipment specifications were determined 2 CO2 emissions in the iron making process decreased by 4 to 5% Ta ble 1 Research and development progress 1988 1991 1992 1993 1990 1995 Core technology study3A3 Direct Iron Ore Smelting Reduction Process (DIOS)

Study on the Basic Characteristics of Iron Ore Powder with MDPI
2022年7月30日 In order to study in depth the differences in basic characteristics between iron ore fines commonly used by a steel company, and guide the sintering performance plant to choose the best ore allocation method, experimental studies on the basic characteristics of seven iron ore powders of three sizes were carried out using microsintering equipment, mainly 2023年2月15日 Hematite, also spelled haematite, is a weakly magnetic iron ore with better floatability than magnetite and wide distributionIt is one of the most important raw materials for the extraction of iron Its composition is complex In addition to containing a small amount of magnetite, the impurity embedding of haematite has uneven particle size and high content of How to Extract Iron from Hematite: Methods and Plants4 天之前 Copper industrial minerals include: natural copper, chalcopyrite, chalcocite, tetrahedrite, azurite, malachite, etc Chalcopyrite (a compound of copper, sulfur, and iron) is mined mainly, followed by chalcocite and bornite If copper ore wants to be fully utilized, it must be processed by flotation Flotation separation is an important copper ore beneficiation process in Copper Ore Processing Plants, Flow And EquipmentThe last stage of making cement is the final grinding process In the cement plant, there are rotating drums fitted with steel balls Clinker, after being cooled, is transferred to these rotating drums and ground into such a fine powder that each pound of it contains 150 billion grains This powder is the final product, cementHow Cement is Made Cement Manufacturing Process
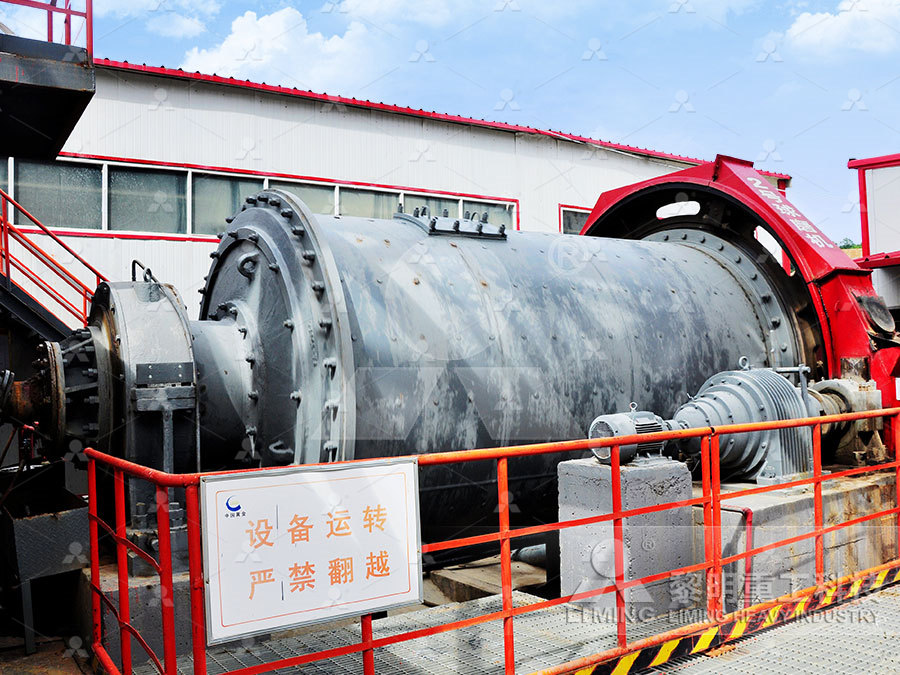
Want To Grind Gold Ore Into Powder? Here’S How! Stone
Grinding gold ore into a fine powder is a crucial step in the extraction and processing of gold This process not only increases the surface area of the ore, making it more amenable to chemical extraction methods, but it also enhances the efficiency of subsequent processing stagesExtraction of Aluminium (Aluminium Ore) To generate aluminium oxide from aluminium ore called bauxite is purified, a white powder form which aluminium can be extracted Occurrence and uses of Aluminium Hallheroult process for the production of aluminiumExtraction of Aluminium (Aluminium Ore) HallHeroults Process 2024年1月1日 Iron ore sintering is the iron ore powder agglomeration process that changes fine iron ore powder into the lumpy ironbearing raw material used for blast furnace ironmaking (2013) Ferrous metallurgy: ironmaking Metallurgical Industry Press, Beijing Google Scholar Download references Author information Authors and AffiliationsIron Ore Sintering SpringerLink2021年12月16日 For several decades, the metallurgical industry and the research community worldwide have been challenged to develop energyefficient and lowcost titanium production processes The expensive and energy Titanium: An Overview of Resources and
.jpg)
Copper Metallurgy SpringerLink
2023年6月8日 The main raw material is copper sulfide ore, and highgrade copper oxide ore can also be smelted in the pyrometallurgical process The mining grade of copper sulfide is 03–2%, and the average mining grade is approximately 081% The mined ore is crushed and pulverized Then flotation will separate the copper sulfide concentrate2019年1月15日 The pelletizing process has lower energy consumption and less pollution emission compared with iron ore sintering process Its superiority made it a significant way for the cleaner production of iron making Usually, the highgrade iron ore is The degradation rate of dioxins was improved from 9303% (fly ash powder added Improvement on the thermal cracking performance of pellets prepared Hematite, the main iron ore found in Brazilian mines Stockpiles of iron ore pellets like this one are used in steel production An illustration of iron ore being unloaded at docks in Toledo, Ohio Iron ores [1] are rocks and minerals from which metallic iron can be economically extracted The ores are usually rich in iron oxides and vary in color from dark grey, bright yellow, or deep purple Iron ore Wikipedia2016年1月8日 The first commercial production of phosphate rock began in England in 1847 A wide variety of techniques and equipment is used to mine and process phosphate rocks in order to beneficiate lowgrade ores and remove impurities The eighth chapter of this book deals with mining and beneficiation of phosphate ore The principle and operating conditions of important Mining and Beneficiation of Phosphate Ore IntechOpen
.jpg)
Iron ore pellets for blast furnace a technical guide MAXTON
2023年1月28日 What is iron ore pellet Iron ore pellets are made by adding a small amount of additives to the fine ore powder (200 mesh, that is, the ore powder with a particle size of less than 0074mm accounts for more than 80%, and the specific surface area is more than 1500cm2/g), adding water to the pelletizer, relying on capillary force and mechanical force of Extraction and refining Ammonium paratungstate Tungsten ores frequently occur in association with sulfides and arsenides, which can be removed by roasting in air for two to four hours at 800° C (1,450° F) In order to produce ammonium paratungstate (APT), an intermediate compound in production of the pure metal, ores may be decomposed by acid leaching or by the autoclave Tungsten processing Extraction, Refining Applications2021年9月1日 Tumble Strength (TS) of iron ore sinter, affected by numerous factors, is considered as a vital performance to assess sinter quality for blast furnace (BF) ironmaking For the sake of providing a credible manipulative strategy of TS in sinter production, we built a mathematical model using artificial neural network, the socalled ANN technology, to predict A forecast model of the sinter tumble strength in iron ore fines 2024年5月9日 The strong magnets will attract the fine iron ore powder Iron particles are drawn to and taken by the magnets This magnetic separation technique is effective for highquality ores, such as magnetite A magnet is used to attract magnetic iron particles and the waste rock is discarded Through this process, we get concentrated iron ore powderIron Ore Mining Essentials: Key to Steel Production JXSC